Ensuring Compliance and Safety with Belt Conveyor Hood Covers
In the diverse landscape of industrial operations, belt conveyor hood covers stand as a crucial component across various sectors, including mining, agriculture, and manufacturing. These innovative solutions play a pivotal role in safeguarding conveyor belt systems, which are the lifelines of material handling and processing activities. The primary purpose of belt conveyor hood covers is to offer unmatched protection to the conveyor belt materials and ensure uninterrupted operation under various environmental conditions. By shielding the conveyor belts from the detrimental effects of weather elements such as rain, wind, and excessive sunlight, as well as from dust and debris, these covers significantly extend the lifespan of the conveyor systems. Additionally, they help in maintaining the quality of the transported materials, preventing contamination and loss during transit. This introduction underscores the indispensable role of belt conveyor hood covers in enhancing the efficiency, safety, and sustainability of industrial conveyor operations.
What is Belt Conveyor Hood Covers
Belt conveyor hood covers are an essential component in the material handling industry, designed to protect the conveyor system and the materials being transported from external elements. These covers not only safeguard the conveyor belt, materials, and system components from damaging weather conditions but also help in maintaining the quality of the materials being conveyed. This detailed exploration delves into the definition of belt conveyor hood covers and the ten pivotal roles they play in enhancing and safeguarding the lifespan of conveyor systems.
Definition of Belt Conveyor Hood Covers
Belt conveyor hood covers are protective enclosures made from metal, plastic, or other durable materials, designed to span over the conveyor belts. These covers serve as a shield for the conveyor system, protecting it from rain, wind, sunlight, and other environmental factors that could potentially harm the conveyor belt, the materials being transported, or the conveyor’s structural integrity. By doing so, they significantly reduce downtime and maintenance costs associated with conveyor systems.
The Ten Roles of Belt Conveyor Hood Covers in Safeguarding and Enhancing Conveyor Systems
- Weather Protection: The primary function of belt conveyor hood covers is to offer protection against weather elements such as rain, snow, wind, and extreme sunlight, which can damage both the conveyor belt and the materials being transported.
- Material Quality Maintenance: By protecting the conveyor system from the elements, these covers help in maintaining the quality of the materials being transported, preventing contamination and moisture accumulation that could lead to spoilage or degradation.
- Reduced Maintenance and Operational Costs: Hood covers minimize the exposure of conveyor components to damaging conditions, thereby reducing the frequency of maintenance and the associated costs.
- Increased Safety: By enclosing the moving parts of the conveyor system, hood covers reduce the risk of accidents and injuries to workers operating near the conveyor.
- Enhanced System Longevity: Protecting the conveyor belt and components from environmental damage and reducing maintenance needs directly contribute to extending the lifespan of the entire conveyor system.
- Prevention of Material Loss: Hood covers help in preventing the loss of materials being transported, especially in outdoor installations where strong winds and other factors could lead to material spillage.
- Compliance with Environmental Regulations: In some cases, conveyor hood covers can help facilities comply with environmental regulations by preventing dust and particulate matter from escaping into the atmosphere.
- Noise Reduction: Certain types of hood covers can also provide a degree of noise reduction, contributing to a more pleasant and compliant working environment.
- Improved Efficiency: By reducing downtime and maintenance requirements, hood covers can improve the overall efficiency of the conveyor system, ensuring a smoother and more continuous operation.
- Aesthetic Integration: Modern hood covers are designed not only for functionality but also to aesthetically complement the industrial environment, contributing to a cleaner and more organized appearance of the operation area.
Belt conveyor hood covers play a crucial role in the efficient and safe operation of conveyor systems. They offer a multitude of benefits that extend beyond mere protection from the weather, including maintaining material quality, enhancing safety, reducing operational costs, and contributing to environmental compliance. By understanding the importance and functionality of these covers, businesses can make informed decisions to safeguard their conveyor systems, thereby ensuring their longevity and reliability.

Belt Conveyor Hood Covers
Types of Belt Conveyor Hood Covers
Belt conveyor hood covers are essential components in the efficient and safe operation of conveyor systems across various industries. They not only protect the conveyor belt and the materials being transported from environmental elements but also enhance the longevity and performance of the conveyor system itself. Below, we delve into the different types of conveyor belt cover thickness, each designed to meet specific operational needs and environmental conditions.
Heavy-duty Belt Conveyor Hood Covers
Heavy-duty belt conveyor hood covers are engineered to withstand extreme environmental conditions, including high winds, heavy rainfall, and significant temperature fluctuations. These covers are typically made from durable materials such as galvanized steel, stainless steel, or aluminum, offering robust protection against wear and tear. They are ideal for industries like mining and construction, where the conveyor systems are exposed to harsh outdoor elements. The primary application of these heavy-duty covers is to ensure the uninterrupted flow of operations by preventing the accumulation of debris and water on the conveyor belt, which could lead to material spillage, belt slippage, or even system breakdown.
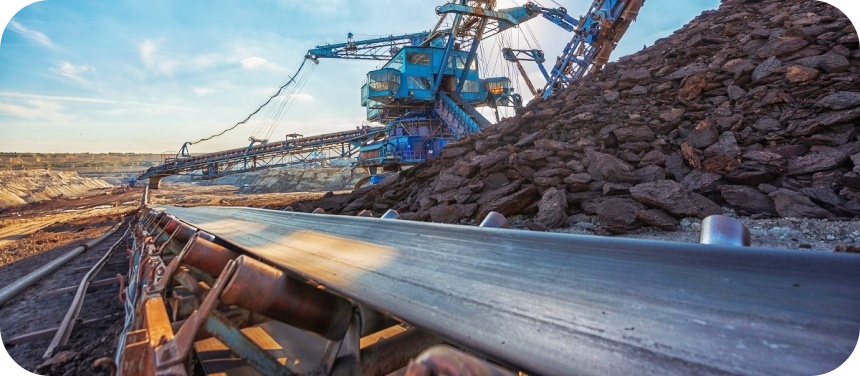
Conveyor Covers Plastic
Plastic belt conveyor hood covers offer a lightweight and corrosion-resistant alternative to their metal counterparts. These covers are particularly advantageous in the following seven aspects:
- Corrosion Resistance: Plastic covers do not rust, making them suitable for applications in corrosive environments or those involving the transport of corrosive materials.
- Lightweight: The reduced weight of plastic covers eases the installation process and puts less structural strain on the conveyor system.
- Cost-Effectiveness: Generally less expensive than metal covers, plastic covers provide an economical solution without compromising on protection.
- Transparency: Some plastic covers are transparent, allowing for visual inspection of the conveyor belt and the materials being conveyed without removing the covers.
- Durability: Modern plastics are highly durable and resistant to impacts, ensuring a long service life under normal conditions.
- Maintenance: Plastic covers are easy to clean and maintain, requiring no special treatments to prevent corrosion.
- Flexibility: They can be easily customized to fit specific conveyor configurations and requirements.
PPI Conveyor Covers
Precision Pulley and Idler (PPI) belt conveyor hood covers are renowned for their quality, durability, and the added value they bring to conveyor systems. PPI covers are designed with the following features and benefits:
- Enhanced Protection: PPI covers provide superior protection against environmental hazards, ensuring the longevity of the conveyor belt and the quality of the materials being transported.
- Aerodynamic Design: Some models feature aerodynamic designs that minimize wind resistance, making them ideal for locations prone to high winds.
- Easy Access: PPI designs often include hinged or removable sections, allowing for easy access to the conveyor for inspection and maintenance without compromising safety or protection.
- Customization: PPI offers customization options to meet specific operational needs, including varying levels of protection, materials, and configurations.
- Durability: Made from high-quality materials, PPI covers are built to last, providing a reliable solution that enhances the overall efficiency of the conveyor system.

The selection of belt conveyor hood covers should be based on the specific needs of the operation, taking into account factors such as environmental conditions, material characteristics, and maintenance requirements. Whether opting for heavy-duty, plastic, or PPI conveyor covers, the right choice will significantly contribute to the conveyor system’s performance, safety, and longevity.
Materials and Design of Belt Conveyor Hood Covers
The materials and design of belt conveyor hood covers are critical to their effectiveness in protecting conveyor systems and the materials they transport. These components are not only pivotal for safeguarding against environmental hazards but also contribute significantly to the longevity and efficiency of conveyor operations. This section delves into the variety of material options available for hood covers and the essential design considerations that enhance their functionality and user safety.
Material Options
A wide range of materials can be used in the manufacturing of belt conveyor hood covers, each offering unique benefits and suited to different environmental conditions and operational requirements:
- Galvanized Steel: Known for its durability and resistance to rust and corrosion, galvanized steel is a popular choice for hood covers in environments prone to moisture and harsh weather conditions. Its longevity and strength make it a cost-effective option for long-term use.
- Aluminum: Aluminum stands out for its lightweight nature, making it easy to install and handle. Despite its lightness, it offers excellent durability and resistance to corrosion, making it suitable for various environments, especially those requiring frequent removal or access to the conveyor.
- Stainless Steel: For environments where corrosion resistance is paramount, such as in chemical processing plants or areas with high salt exposure, stainless steel is the material of choice. It combines strength with superior corrosion resistance, albeit at a higher cost.
- Fiberglass: Fiberglass offers an excellent strength-to-weight ratio and is resistant to corrosion, making it ideal for use in corrosive environments or where weight considerations are critical. Its non-conductive nature also makes it safe for use in electrical hazard areas.
- Painted Steel: Painted steel provides an economical option that combines the strength of steel with additional protection from paint coatings. This option allows for customization in terms of colors, enhancing the aesthetic appeal of the installation.
- Plastic: Plastic hood covers are lightweight, corrosion-resistant, and often more cost-effective than metal options. They are suitable for less demanding environments and offer the advantage of being easy to fabricate and install.
Design Considerations
The design of belt conveyor hood covers goes beyond material selection, incorporating features that enhance their strength, safety, and convenience:
- Corrugated Design: The corrugated design is widely adopted for its ability to provide additional strength and rigidity to the hood covers. This design helps in withstanding environmental loads such as wind, snow, and accumulation of debris, ensuring the covers remain intact and functional over time.
- Safety Features: Safety is a paramount consideration in the design of hood covers. Features such as folded edges minimize the risk of cuts or injuries to personnel during installation or maintenance. This attention to detail is crucial for creating a safe working environment.
- Convenience Features: To facilitate easy access for inspection, maintenance, and repair of the conveyor system, belt conveyor hood covers often include convenience features like easy-to-open latches and access doors. These features ensure that the covers can be quickly and easily removed or opened, minimizing downtime and enhancing the efficiency of operations.
- Integration with Conveyor Structure: The design also considers the seamless integration of hood covers with the existing conveyor structure. This includes considerations for mounting options, ensuring a secure fit, and accommodating various conveyor profiles and configurations.
The materials and design of belt conveyor hood covers are integral to their performance and the protection they offer. By carefully selecting the appropriate materials and incorporating key design features, these covers effectively safeguard conveyor systems from environmental challenges while ensuring safety and convenience in maintenance and operation.
Specifications of Belt Conveyor Hood Covers
When delving into the specifications of belt conveyor hood covers, one crucial aspect that stands out is the “Conveyor Belt Cover Thickness.” This particular feature plays a pivotal role in determining both the durability and the level of protection that the cover offers to the conveyor system and the materials it transports.
Conveyor Belt Cover Thickness
The thickness of belt conveyor hood covers is not just a measure of the material used in its construction; it’s a critical factor that impacts several key attributes of the cover’s performance:
- Durability: Thicker covers generally offer greater durability. They are more resistant to physical damage from external impacts, such as falling debris in industrial settings or harsh environmental conditions. A thicker cover can absorb more force without sustaining damage, thereby ensuring that it remains functional over a longer period. This resilience is particularly important in industries where conveyor systems are exposed to heavy loads and potentially abrasive materials that could compromise the integrity of the cover.
- Protection: The primary purpose of conveyor belt cover thickness is to protect the conveyor belt and the materials being conveyed from environmental elements, such as rain, wind, dust, and direct sunlight. A thicker cover provides a better barrier against these elements, more effectively preventing moisture from seeping in and ensuring that materials like dust and sand are kept at bay. This level of protection is essential for maintaining the quality of the materials being transported and for preventing any damage or wear to the conveyor belt itself.
- Weather Resistance: Thicker covers are inherently more resistant to weather-related wear and tear. They can better withstand the effects of UV radiation, which can cause lesser materials to become brittle and crack over time. They are also better equipped to handle temperature fluctuations, maintaining their structural integrity in both extreme heat and cold. This is particularly important for outdoor conveyor systems, which must operate reliably in varying weather conditions.
- Sound Insulation: An often overlooked advantage of thicker belt conveyor hood covers is their ability to provide sound insulation. This can be particularly beneficial in operations where noise reduction is a priority, either for the comfort and safety of workers or to comply with local noise regulations. A thicker cover can help dampen the sound of materials being transported, as well as the mechanical noise generated by the conveyor system itself.
The thickness of belt conveyor hood covers is a vital specification that significantly influences their effectiveness. It is a key determinant of the cover’s durability, its capacity to protect the conveyor system and the materials being conveyed, its resistance to weather and environmental conditions, and its ability to reduce operational noise. When selecting covered conveyor belt, it’s important to consider the specific demands of the environment and the application to choose a cover thickness that will provide the optimal balance of protection, durability, and performance.
Benefits of Using Belt Conveyor Hood Covers
Belt conveyor hood covers offer a multitude of advantages that extend far beyond simple protection from the elements. These covers not only enhance the operational efficiency and longevity of conveyor systems but also play a crucial role in environmental compliance, worker safety, and the preservation of material quality. Additionally, their design and material options allow for aesthetic considerations, enabling them to blend seamlessly into various environments. Let’s delve deeper into each of these benefits.
Protection from Weather Conditions
One of the primary benefits of using hood cover for belt conveyors is their ability to protect the conveyor system and the materials being transported from harsh weather conditions. Whether it’s rain, snow, wind, or extreme sunlight, these covers provide a shield that prevents weather-induced damage and degradation. This protection is crucial for maintaining continuous operation, especially in outdoor or exposed environments where weather conditions can be unpredictable and potentially harmful to both the conveyor system and the materials being conveyed.
Environmental Compliance
Belt conveyor hood covers also play a significant role in ensuring environmental compliance. In industries where dust and particulate matter can pose a significant environmental hazard, these covers help to contain and minimize the release of such materials into the atmosphere. By doing so, they assist in complying with environmental regulations and standards, reducing the risk of fines and sanctions while promoting a cleaner, healthier environment. This aspect is particularly important in sectors like mining, construction, and agriculture, where the potential for environmental impact is high.
Ensuring Worker Safety
The safety of workers is paramount in any industrial setting. Belt conveyor hood covers contribute to a safer work environment by enclosing moving parts and reducing the risk of accidents. They prevent contact with potentially hazardous materials and protect workers from the elements, reducing the likelihood of injury. Moreover, certain design features, such as non-slip surfaces and safety latches, further enhance worker safety during maintenance and operation.
Preserving the Quality of Conveyed Materials
Maintaining the quality of the materials being transported is essential for operational efficiency and customer satisfaction. Belt conveyor hood covers protect these materials from contamination by dust, moisture, and other environmental factors. This protection is vital for sensitive materials that could be compromised by exposure to the elements, ensuring that the quality and integrity of the products are maintained from start to finish.
Aesthetic Considerations
Aesthetic considerations are increasingly becoming a factor in the selection and implementation of industrial equipment. Belt conveyor hood covers are designed with the flexibility to blend into natural and built environments, offering options in materials and finishes that can match or complement surrounding structures. This aspect is especially beneficial in scenic or residential areas, where the visual impact of industrial operations may be a concern. By choosing covers with the right aesthetic qualities, businesses can minimize the visual disruption caused by their operations, fostering a more harmonious relationship with the community and the environment.
The benefits of using covered conveyor belt extend well beyond mere protection from the elements. They are an integral component of any conveyor system, contributing to environmental compliance, worker safety, the preservation of material quality, and even aesthetic considerations. By incorporating these covers into their operations, businesses can achieve a balance between efficiency, safety, and environmental responsibility, all while maintaining a positive image in their respective industries.
Choosing the Right Hood Cover
Selecting the appropriate belt conveyor hood covers is a critical decision that significantly impacts the efficiency, safety, and longevity of a conveyor system. To ensure the optimal selection, several key factors must be carefully considered. These factors are based on the conveyor’s size, the type of materials being transported, the prevailing environmental conditions, and the applicable regulatory standards. Moreover, the availability of custom sizes and designs plays a crucial role in meeting specific operational needs.
Factors to Consider
- Conveyor Size: The size of the conveyor system directly influences the type and size of belt conveyor hood covers needed. It’s essential to accurately measure the length and width of the conveyor to ensure the covers provide complete protection without obstructing the system’s operation. Larger conveyors may require more robust or segmented covers for ease of installation and maintenance.
- Material Type: The nature of the materials being transported has a significant impact on the selection of hood covers. For instance, materials that are highly abrasive or corrosive may necessitate covers made from more durable or resistant materials to prevent wear and tear. Conversely, for light, non-abrasive materials, lighter and potentially less costly cover options might suffice.
- Environmental Conditions: Environmental factors play a pivotal role in determining the right belt conveyor hood covers. For outdoor conveyors exposed to harsh weather conditions, such as rain, snow, or extreme temperatures, choosing covers with high durability and weather resistance is crucial. Covers made from materials that offer UV protection, waterproofing, and temperature resistance will ensure the conveyor’s longevity and reliability.
- Regulatory Standards: Compliance with local and international safety and environmental regulations is a critical consideration. Certain industries may have specific standards that hood cover for belt conveyors must meet, such as fire resistance, noise reduction, or emission controls. Ensuring compliance not only safeguards operations but also helps avoid potential legal and financial penalties.
Custom Sizes and Designs
The unique operational needs of different conveyor systems often necessitate custom-sized and designed belt conveyor hood covers. Manufacturers and suppliers of these covers usually offer customization options to accommodate specific requirements, including:
- Custom Fit: Tailored to perfectly match the dimensions of your conveyor system, ensuring comprehensive protection and a seamless integration without impeding the system’s functionality.
- Special Materials: Depending on the operational environment and the materials being conveyed, custom covers can be fabricated from specialized materials to enhance durability, resist corrosion, or meet specific regulatory standards.
- Design Features: Custom designs can include features such as easy-access panels for maintenance, transparent sections for monitoring the conveyor’s operation, and aerodynamic shapes to reduce wind resistance.
Opting for custom belt conveyor hood covers ensures that every aspect of the conveyor’s operation and environmental exposure is considered, leading to enhanced protection, efficiency, and compliance with regulatory standards. When choosing the right hood cover, working closely with manufacturers to specify the exact requirements can significantly impact the success and longevity of the conveyor system.
Get expert advice on Belt Conveyor Hood Covers by filling out our inquiry form.
FAQs about Belt Conveyor Hood Covers
A belt conveyor system comprises several key components, each playing a vital role in its operation and efficiency. The primary parts include:
Conveyor Belt: The central component that transports materials from one location to another. It’s made from various materials, depending on the application, including rubber, plastic, or metal.
Pulleys: These are used to drive the belt, maintain its tension, and change its direction. The main pulleys in a belt conveyor system are the drive pulley (which powers the belt) and the idler pulley (which supports the belt).
Rollers: Positioned along the conveyor frame, rollers support the conveyor belt and the materials being transported. They help reduce friction and facilitate smooth belt movement.
Frame: The structure that supports the conveyor components and maintains the system’s integrity and alignment.
Motor: The power source for the conveyor, which drives the pulley and, in turn, moves the belt.
Belt Conveyor Hood Covers: Protective covers that shield the conveyor belt and the materials from environmental elements.
Skirt Board: Positioned along the loading zone of the conveyor to contain materials and reduce spillage.
Understanding these components and their functions is crucial for operating and maintaining a belt conveyor system effectively.
Protecting your conveyor belt is essential for prolonging its lifespan and maintaining operational efficiency. Here are several strategies for conveyor belt protection:
Use Belt Conveyor Hood Covers: Installing covers over your conveyor belt protects it from weather conditions, dust, debris, and other external elements that could cause damage or contamination.
Regular Maintenance and Inspection: Routine checks can identify and address issues such as misalignment, wear, and tear, or lubrication needs before they lead to significant damage.
Proper Loading: Ensuring materials are evenly distributed and loaded onto the conveyor can prevent undue stress and wear on the belt.
Install Skirt Boards: Skirt boards help contain the material at the loading point, reducing spillage and minimizing the risk of belt damage.
Use Impact Beds: Placing impact beds beneath the loading zone can absorb the shock and distribute the force of falling materials, protecting the belt from damage.
Adopting these protective measures can significantly enhance the durability and functionality of your conveyor belt, reducing downtime and maintenance costs.
A skirt board in a belt conveyor system is a critical component designed to enhance operational efficiency and safety. Positioned along the sides of the conveyor at the loading zone, the skirt board serves multiple functions:
Containment of Materials: It helps to contain the materials being loaded onto the conveyor belt, preventing spillage over the sides. This is particularly important for maintaining a clean environment and reducing material wastage.
Reduced Dust Emission: By containing the materials, skirt boards also help to minimize dust emissions, contributing to a safer and healthier working environment.
Protection of the Conveyor Belt: Skirt boards help to protect the conveyor belt from the impact and abrasion of materials at the loading zone, thereby extending the belt’s lifespan.
Enhanced Material Flow: Skirt boards assist in directing the flow of materials onto the center of the conveyor belt, promoting efficient transport and reducing the risk of belt misalignment.
Skirt boards are adjustable to accommodate different material volumes and types, making them an adaptable solution for improving conveyor belt performance and protection.
A conveyor belt cover, commonly known as a belt conveyor hood cover or simply a conveyor hood, is designed to shield the conveyor belt, along with the materials it carries, from external elements and environmental conditions. These covers play a crucial role in preserving the longevity and efficiency of the conveyor system by protecting it against rain, wind, sunlight, and debris, which could otherwise lead to damage, contamination, or operational interruptions. Conveyor belt covers are essential for maintaining the quality of the materials being transported, preventing spillage, and ensuring compliance with safety and environmental regulations. Made from various materials such as metal, plastic, or specialized fabrics, these covers can be customized to suit different conveyor sizes, environmental conditions, and industry-specific requirements, ensuring optimal protection and performance.
Last Updated on August 1, 2024 by Jordan Smith
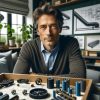
Jordan Smith, a seasoned professional with over 20 years of experience in the conveyor system industry. Jordan’s expertise lies in providing comprehensive solutions for conveyor rollers, belts, and accessories, catering to a wide range of industrial needs. From initial design and configuration to installation and meticulous troubleshooting, Jordan is adept at handling all aspects of conveyor system management. Whether you’re looking to upgrade your production line with efficient conveyor belts, require custom conveyor rollers for specific operations, or need expert advice on selecting the right conveyor accessories for your facility, Jordan is your reliable consultant. For any inquiries or assistance with conveyor system optimization, Jordan is available to share his wealth of knowledge and experience. Feel free to reach out at any time for professional guidance on all matters related to conveyor rollers, belts, and accessories.