Belt Conveyor System for Coal Handling in a Thermal Power Plant
Coal handling plays a pivotal role in the efficiency and sustainability of various industries, most notably in thermal power plants and coal mining operations. belt conveyor system for coal handling transport large volumes of coal over long distances efficiently, reducing operational costs.The process of moving coal from point A to point B must be seamless, efficient, and environmentally responsible. This is where the belt conveyor system for coal handling comes into play, serving as the backbone of coal transportation within these sectors. Belt conveyor systems are engineered to transport coal over long distances, through complex routes, and often across challenging terrains. Their ability to handle large volumes of coal continuously and reliably makes them an indispensable component in the coal handling processes of today’s industrial landscape. By integrating advanced technologies and robust materials, these conveyor systems ensure that coal is moved in the most efficient, safe, and cost-effective manner possible, underpinning the operational success of power generation and mining activities.
What are Belt Conveyor Systems for Coal Handling
Definition and Basic Operation
A belt conveyor system for coal handling is an essential mechanism designed for the continuous transport of bulk materials, specifically coal, over long distances. It consists of a loop of a durable material, typically rubber, that moves over a series of rollers or idlers. This system is particularly crucial in settings where coal needs to be moved efficiently from mines or plants to processing locations or storage facilities.
The basic operation of a belt conveyor system for coal handling involves several key steps: the loading of coal onto the belt, the transportation of coal along the conveyor path, the maintenance of belt tension to prevent slippage, the unloading of coal at the destination, the return of the belt to the loading point, and the control of dust and spillage throughout the process.
Key Components
The belt conveyor system is made up of nine key components:
- Conveyor Belt: The heart of the system, this is the moving surface that carries the coal from one point to another. It must be durable and resistant to the abrasive nature of coal.
- Idlers: These rollers support the conveyor belt and the coal on it. They are spaced along the length of the conveyor to ensure smooth belt movement.
- Pulleys: Located at the ends of the conveyor system, pulleys drive the belt and can also be used to change its direction.
- Drive Unit: Comprising motors and gearboxes, the drive unit provides the necessary power to move the conveyor belt loaded with coal.
- Take-Up System: This component adjusts the tension of the conveyor belt to prevent slippage on the drive pulley.
- Belt Cleaners: These are installed to clean the belt, especially at the discharge end, to ensure that coal does not stick to the belt and carry back.
- Skirt Boards: Used at the loading points, skirt boards prevent coal spillage and ensure that the coal is loaded onto the center of the belt.
- Conveyor Frame: This is the structure that supports all the components of the conveyor system.
- Safety Devices: These include emergency stop cords, belt misalignment switches, and speed monitors to ensure the safe operation of the belt conveyor system for coal handling.
Understanding these components and their functions is crucial for optimizing the efficiency and safety of a belt conveyor system for coal handling, making it an indispensable part of modern coal transportation infrastructure.
Coal Conveyor Belt Specifications for Belt Conveyor System for Coal Handling
Specific Requirements
The belt conveyor system for coal handling relies heavily on the quality and specifications of the conveyor belts used. These belts must meet specific requirements to ensure efficient and reliable coal transport. Here are ten critical specifications for conveyor belts in coal handling:
- Material Composition: The belt material must be resistant to the abrasive nature of coal and the associated dust. Common materials include rubber compounds, PVC, and synthetic fabrics designed for durability and resistance to wear and tear.
- Tensile Strength: High conveyor belt tensile strength is crucial to withstand the weight of the coal and the stress of continuous operation.
- Belt Width: The width of the belt determines the capacity of the conveyor system. Wider belts can carry more coal, increasing the system’s throughput.
- Thickness: The thickness of the belt contributes to its durability and lifespan. Thicker belts can resist punctures and tears better.
- Top Cover Thickness: The top cover protects the belt from the abrasive action of the coal and external elements. Its thickness should be chosen based on the application’s severity.
- Bottom Cover Thickness: This provides protection against wear from the conveyor structure and should be durable enough to withstand friction.
- Belt Speed: The speed of the belt must be optimized for coal handling, ensuring efficient transport without causing spillage or excessive wear.
- Troughability: The ability of the belt to form a trough shape is essential for carrying coal efficiently and preventing spillage.
- Impact Resistance: The belt should be capable of absorbing impacts at loading points to prevent damage.
- Temperature Resistance: Belts must withstand the temperatures of the environment and the material, especially in thermal power plants where coal may be hot.
Importance of Selecting the Right Belt Material
Selecting the right belt material for a belt conveyor system for coal handling is crucial due to several reasons:
- Durability: The right material can withstand the abrasive nature of coal, reducing wear and tear and extending the belt’s lifespan.
- Efficiency: Proper belt material ensures that the conveyor system operates smoothly, with minimal downtime for maintenance and repairs.
- Safety: High-quality belt materials reduce the risk of belt failure, which can lead to accidents and operational disruptions.
- Cost-effectiveness: While high-quality belts may have a higher initial cost, their durability and reliability can lead to lower overall operational costs.
- Environmental Resistance: Belts must resist environmental conditions such as moisture, temperature variations, and exposure to chemicals or UV light.
- Compliance: The right belt material ensures compliance with safety and environmental regulations, avoiding potential fines and legal issues.
The specifications of conveyor belts in a belt conveyor system for coal handling are critical for the system’s performance, safety, and cost-efficiency. Careful selection of belt materials and specifications tailored to the specific demands of coal handling can significantly enhance the effectiveness of the conveyor system.
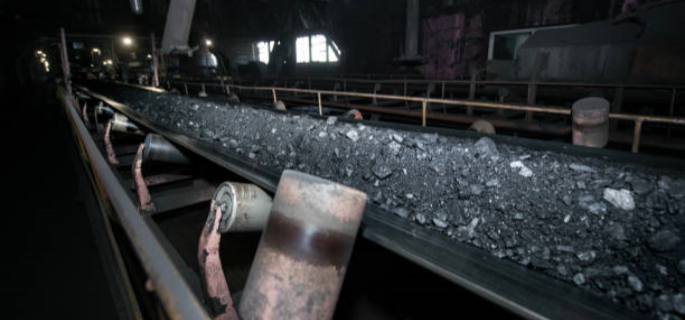
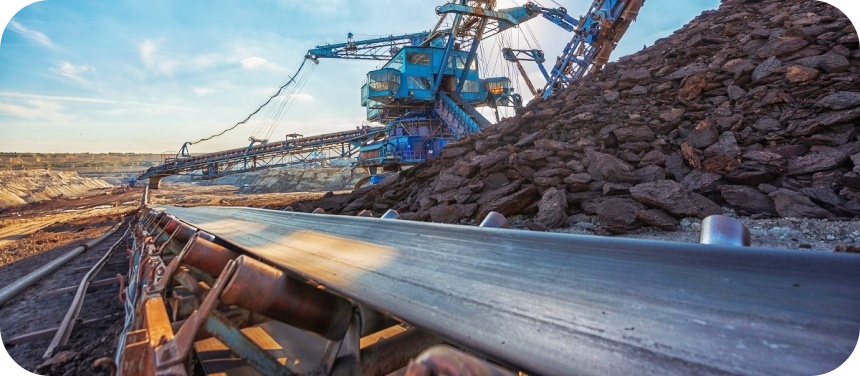
Advantages of Belt Conveyor System for Coal Handling
The use of belt conveyor systems for coal handling in thermal power plants offers several significant advantages. These advantages enhance operational efficiency, safety, and cost-effectiveness. Here are some key benefits:
Energy Efficiency
- Lower Energy Consumption: Belt conveyors generally consume less energy compared to other transport methods like trucks or railways, especially over long distances. This efficiency reduces overall operational costs and energy consumption.
Modular Design
- Scalability: Belt conveyors can be easily expanded or reconfigured to accommodate changes in production capacity or layout modifications, providing flexibility in system design.
- Ease of Installation: The modular nature of belt conveyors simplifies installation and maintenance, leading to reduced downtime and lower setup costs.
High Degree of Automation
- Automated Control: Modern belt conveyor systems often feature advanced automation technology, allowing for precise speed and load control, which enhances efficiency and productivity.
- Monitoring and Diagnostics: Equipped with sensors and monitoring devices, these systems can continuously monitor operational status, quickly diagnose issues, and implement corrective actions, improving reliability and safety.
Reduced Noise and Vibration
- Quiet Operation: Belt conveyors typically generate less noise and vibration compared to other mechanical transportation systems, improving the working environment and reducing the impact on surrounding areas.
- Lower Equipment Wear: Reduced vibration contributes to less wear and tear on the equipment, extending its operational life.
Adaptability to Harsh Environments
- Durability: Belt conveyors are designed to operate efficiently in harsh conditions, such as extreme temperatures, high humidity, and dusty environments, making them suitable for coal handling.
- Corrosion Resistance: Options are available for conveyors made with corrosion-resistant materials, enhancing durability in challenging environments.
Minimized Material Loss
- Gentle Handling: Belt conveyors transport materials smoothly, reducing the risk of material loss or damage, which is particularly important for handling fine or granular coal.
Long-Term Investment
- High ROI: While the initial investment in belt conveyors can be substantial, their long-term benefits include lower maintenance and operating costs, making them a cost-effective solution over time.
These additional advantages further illustrate why belt conveyor systems are highly valued in coal handling, combining operational efficiency, safety, and cost-effectiveness to support the demanding needs of thermal power plants.
Design and Selection Criteria for Coal Handling Belt Conveyors
The design and selection of a belt conveyor system for coal handling involve a comprehensive understanding of the operational requirements and environmental conditions.
Factors Influencing the Design and Selection
Here are nine crucial factors that influence the design and selection of these systems:
- Load Capacity: The system must be capable of handling the maximum expected load of coal, both in terms of volume and weight, to ensure efficient operation.
- Belt Speed: The speed of the belt must be optimized to balance the throughput requirements with the risk of spillage or excessive wear.
- Conveyor Length: The length of the conveyor must be determined based on the distance between the coal supply point and the destination, considering any necessary route deviations.
- Incline Angles: The system must be designed to handle the incline angles required to transport coal from lower to higher elevations or vice versa.
- Material Characteristics: The abrasive and dusty nature of coal requires a conveyor design that minimizes wear and tear and contains dust.
- Operational Environment: The conveyor system must be designed to operate reliably under the specific environmental conditions of the site, including temperature, humidity, and exposure to elements.
- Energy Efficiency: The design should consider energy consumption, selecting components and configurations that minimize power usage while maintaining performance.
- Maintenance and Accessibility: The system should be designed for ease of maintenance, with accessible components and modular designs that allow for quick repairs and replacements.
- Safety and Compliance: The conveyor must incorporate safety features and comply with relevant regulations, including measures to prevent fires and explosions in coal handling environments.
Need durable conveyor belts? Inquire now for top-quality solutions!
Considerations for Choosing Conveyor Belt Specifications
When choosing conveyor belt specifications for a belt conveyor system for coal handling, the following considerations are critical:
- Belt Material: The material must be durable enough to withstand the abrasive nature of coal and resistant to environmental factors like moisture and temperature.
- Belt Width and Thickness: These dimensions should be selected based on the required load capacity and the belt’s ability to withstand wear and tear.
- Tensile Strength: The belt must have sufficient tensile strength to handle the tension generated by the load and the drive system without stretching or breaking.
- Cover Grade: The cover of the belt should be chosen based on the abrasiveness of the coal and the presence of potentially damaging materials in the coal.
- Splice Method: The method used to splice the belt ends together must ensure a strong, reliable joint that can withstand the operational stresses.
- Roller and Idler Specifications: Rollers and idlers must be selected to support the belt and load adequately, with materials and designs that minimize friction and wear.
By carefully considering these factors and criteria, engineers can design a belt conveyor system for coal handling that meets the specific needs of the operation, ensuring efficient, reliable, and safe coal transportation.
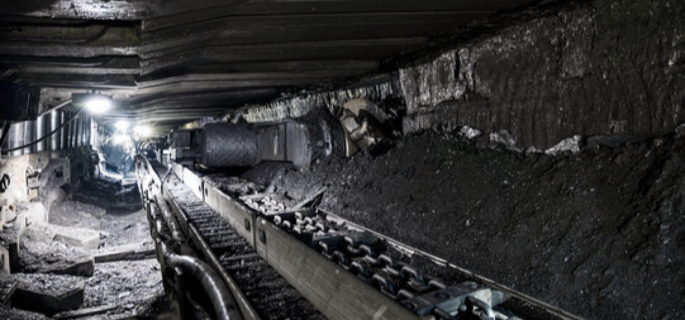
Cost Considerations of Belt Conveyor Systems for Coal Handling
When implementing a belt conveyor system for coal handling, understanding the financial aspects is crucial for making informed decisions. This includes both the initial installation costs and the ongoing operational expenses. Initial costs encompass the purchase of materials, such as the conveyor belt, rollers, idlers, and the drive system, as well as the expenses related to engineering, installation, and commissioning of the system. Operational expenses cover maintenance, repairs, energy consumption, and potential downtime costs.
Investing in high-quality belt conveyor systems for coal handling can offer significant long-term cost benefits, which include:
- Reduced Maintenance Costs: High-quality systems are designed for durability and reliability, requiring less frequent and less costly maintenance.
- Extended Equipment Lifespan: Premium materials and components can withstand the harsh conditions of coal handling, extending the lifespan of the conveyor system and reducing the need for replacements.
- Increased Operational Efficiency: Efficient systems minimize energy consumption and maximize throughput, leading to lower operational costs per ton of coal handled.
- Improved Safety: Enhanced safety features and reliability reduce the risk of accidents and associated costs, including potential fines and downtime.
- Lower Downtime: Reliable systems experience fewer breakdowns, minimizing costly downtime and ensuring continuous coal supply.
- Enhanced Environmental Compliance: Systems designed with dust control and spillage prevention in mind can help avoid environmental fines and remediation costs.
- Scalability: High-quality conveyor systems can be more easily adapted or expanded to meet future needs, avoiding the costs of a complete system overhaul.
- Resale Value: Well-maintained, high-quality conveyor systems can retain a higher resale value, providing financial return at the end of their service life.
- Reduced Spillage and Waste: Precision-engineered systems reduce coal spillage, minimizing waste and the costs associated with cleanup and lost material.
- Predictable Budgeting: The reliability and efficiency of a high-quality system allow for more predictable budgeting for operational and maintenance costs.
By carefully considering these cost factors and benefits, organizations can make strategic investments in belt conveyor systems for coal handling that not only meet their immediate needs but also provide long-term financial advantages.
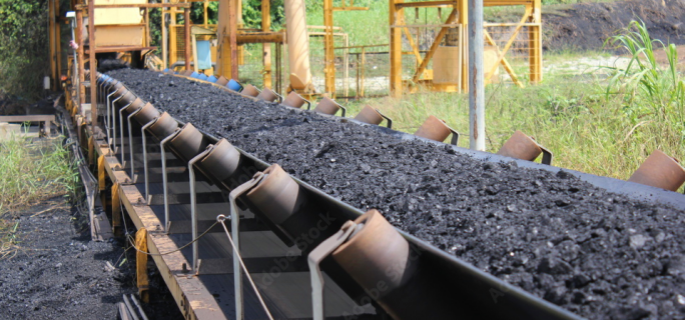
Manufacturers of Belt Conveyor System for Coal Handling
Leading Manufacturers
When selecting a belt conveyor system for coal handling, the choice of the conveyor belt manufacturer is critical. Here are eight leading manufacturers known for producing conveyor belts that are suitable for coal handling:
- GRAM Conveyor: GRAM Conveyor is a company that specializes in the design, manufacturing, and installation of conveyor systems. These systems are used in various industries to transport materials and products efficiently and safely from one point to another within a facility. The company’s offerings might include a wide range of conveyor types, such as belt conveyors, roller conveyors, among others.
- ContiTech: A global leader in conveyor belt manufacturing, ContiTech offers a wide range of durable and high-performance conveyor belts specifically designed for the mining and power generation industries.
- Fenner Dunlop: Specializing in the production of heavy-duty conveyor belting, Fenner Dunlop’s products are engineered to meet the demanding conditions of coal handling applications.
- Bridgestone: Known for its innovative and high-quality conveyor belts, Bridgestone provides solutions that enhance the efficiency and safety of coal transportation.
- Yokohama Rubber: Offers high-quality, durable conveyor belts with advanced technology for coal mining and handling, ensuring operational reliability.
- Sempertrans: A leading name in the conveyor belt sector, Sempertrans offers belts that are specifically designed to withstand the harsh environments of coal handling.
- Bando: With a strong focus on research and development, Bando’s conveyor belts are known for their high durability and efficiency in coal handling.
- Phoenix Conveyor Belt Systems: Phoenix provides custom-designed conveyor belts for complex coal handling applications, ensuring high performance and reliability.
- Zhejiang Double Arrow: Specializes in producing conveyor belts that are resistant to wear, tear, and fire, making them suitable for coal handling in mines and power plants.
Importance of Partnering With Reputable Manufacturers
Partnering with reputable manufacturers is crucial for several reasons:
- Quality Assurance: Established manufacturers adhere to strict quality standards, ensuring that the conveyor belts are durable and reliable.
- Innovation: Leading manufacturers invest in research and development to provide innovative solutions that improve the efficiency and safety of coal handling.
- Customization: Reputable manufacturers can offer customized conveyor belt solutions tailored to the specific needs of a coal handling operation.
- Technical Support: Top manufacturers provide excellent technical support, from the initial design phase through installation and operational troubleshooting.
- Warranty and Service: Reliable manufacturers stand behind their products with warranties and offer comprehensive after-sales service and support.
- Compliance: Conveyor belts from reputable manufacturers are more likely to comply with international safety and environmental standards, reducing the risk of non-compliance issues.
- Long-Term Partnership: Working with a trusted manufacturer ensures a long-term partnership that can provide ongoing support, updates, and improvements to the belt conveyor system for coal handling.
Selecting the right manufacturer for the conveyor belt is a critical decision that can significantly impact the efficiency, safety, and longevity of a belt conveyor system for coal handling.
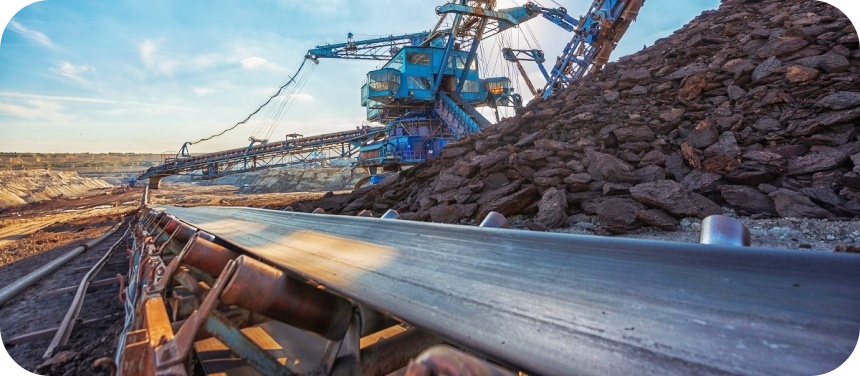
Underground Conveyor Belt Systems for Belt Conveyor System for Coal Handling
Special Considerations in Underground Mining Operations
Underground conveyor belt systems for coal handling require specialized design and safety measures due to the unique challenges of the subterranean environment. Here are six special considerations for designing and implementing these systems:
- Space Limitations: Underground tunnels have limited space, requiring compact conveyor designs that can efficiently operate in confined areas.
- Moisture and Corrosion: High humidity levels underground can lead to corrosion, necessitating the use of corrosion-resistant materials and protective coatings for all conveyor components.
- Ventilation and Dust Control: Adequate ventilation is crucial to disperse harmful gases and dust. Conveyor systems must include effective dust suppression technologies to minimize airborne particles.
- Material Accumulation: Preventing coal and debris accumulation in underground conveyors is vital to avoid blockages and ensure continuous operation.
- Incline and Decline Handling: Conveyor systems must be adept at managing steep inclines and declines, common in underground mining, without compromising coal stability on the belt.
- Integration with Other Systems: Underground conveyors need to be seamlessly integrated with other coal handling and extraction systems for efficient operation.
Safety Measures and Requirement
Safety measures and explosion-proof requirements are paramount for underground conveyor belt systems in coal handling due to the potential for hazardous conditions:
- Explosion-Proof Design: All electrical components must be designed to prevent ignition of explosive gases and dust present in coal mines.
- Fire-Resistant Belts: Conveyor belts must be made from fire-resistant materials to reduce the risk of fire, which can be devastating in an underground environment.
- Emergency Stop Systems: Easily accessible emergency stop controls along the conveyor belt are essential for immediate shutdown in case of an emergency.
- Regular Maintenance and Inspections: Scheduled maintenance and routine conveyor belt inspections are crucial to identify and rectify potential hazards like frayed belts, malfunctioning rollers, and electrical issues.
- Monitoring Systems: Continuous monitoring of conveyor operation, including belt speed, temperature, and alignment, helps in early detection of potential problems.
- Training for Personnel: Workers should be thoroughly trained in the safe operation of conveyor systems and in emergency response procedures.
- Ventilation Systems: Adequate ventilation is necessary to remove potentially explosive gases and dust, ensuring a safer working environment.
- Dust Suppression Systems: Implementing dust control measures, such as water spray systems or dust collectors, minimizes the risk of dust explosions.
Designing and implementing an underground belt conveyor system for coal handling requires careful consideration of these special considerations and safety measures to ensure efficient, safe, and reliable operation in the challenging underground mining environment.
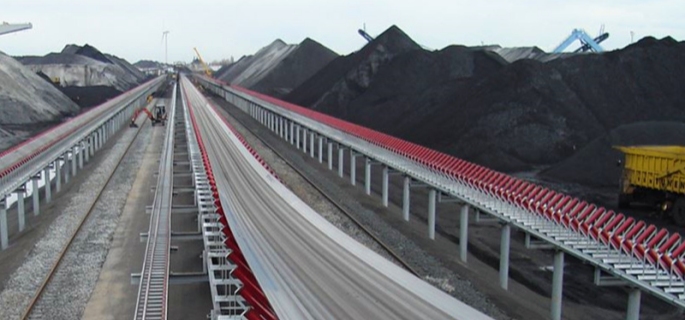
Belt Conveyor System in Thermal Power Plants for Coal Handling
The belt conveyor system for coal handling plays a pivotal role in thermal power plants by ensuring the continuous, efficient, and reliable transport of coal from storage areas to the boilers where it is used for power generation.
Types of Conveyors in a Thermal Power Plant
In a thermal power plant, various types of conveyors are used to transport materials efficiently and reliably. Here are the main types of conveyors typically found in these facilities:
Belt Conveyors
- Description: These conveyors consist of endless belts that pass over drums or pulleys. The belts are usually made of rubber or fabric.
- Usage: Commonly used for transporting coal, ash, and other bulk materials over long distances.
- Advantages: High efficiency, large capacity, and the ability to handle various materials.
Screw Conveyors
- Description: These conveyors consist of a helical screw blade, or auger, that rotates inside a tube or trough.
- Usage: Ideal for moving fine-grained or powdered materials like fly ash.
- Advantages: Compact design, ability to control the material flow rate, and easy to enclose to prevent dust.
Bucket Elevators
- Description: Comprise a series of buckets attached to a belt or chain that moves vertically.
- Usage: Used to lift bulk materials vertically, such as coal or ash, from one level to another.
- Advantages: Efficient vertical transport and minimal ground space requirement.
Drag Chain Conveyors
- Description: Utilize chains to drag bulk materials through a trough.
- Usage: Suitable for moving heavy, abrasive materials like coal and ash.
- Advantages: Robust design and ability to handle high-temperature materials.
Pneumatic Conveyors
- Description: Use air pressure or vacuum to transport materials through pipes or tubes.
- Usage: Often used for moving fine, dry materials like fly ash.
- Advantages: Flexible routing, minimal spillage, and enclosed system to reduce dust.
Vibrating Conveyors
- Description: Use vibration to move materials along a trough or tube.
- Usage: Effective for short distances and for materials that need to be spread evenly, such as ash.
- Advantages: Gentle handling of materials and can be used to convey, screen, and cool materials simultaneously.
Apron Conveyors
- Description: Consist of overlapping metal plates or aprons mounted on chains.
- Usage: Designed for heavy-duty applications, such as moving large, hot, or abrasive materials.
- Advantages: Durable and can handle heavy loads and high temperatures.
Overland Conveyors
- Description: Long-distance belt conveyors that transport materials across large distances.
- Usage: Used to move coal and other bulk materials from mines or stockyards to the plant.
- Advantages: Cost-effective for long-distance transport and can cross difficult terrains.
Role of Belt Conveyors in Thermal Power Plants
Here are ten critical roles that these conveyor systems fulfill in thermal power plants:
- Continuous Coal Supply: Belt conveyors provide a continuous and consistent supply of coal to the boilers, ensuring uninterrupted power generation.
- Efficient Material Transport: These systems are designed for efficient transport of bulk coal, minimizing energy consumption and operational costs.
- Flexibility in Operation: Belt conveyors can be easily adjusted for changes in the rate of coal supply, accommodating fluctuations in power demand.
- Reduced Labor Requirements: Automated conveyor systems reduce the need for manual labor in coal handling, decreasing operational costs and enhancing safety.
- Minimized Coal Losses: Enclosed belt conveyor designs help in minimizing coal spillage and losses during transport.
- Environmental Protection: Conveyor systems can be equipped with dust control measures, reducing the environmental impact of coal handling.
- Space Efficiency: Belt conveyors can be designed to fit the specific layout of a thermal power plant, optimizing the use of space.
- Safety Enhancements: Modern conveyor systems include safety features such as emergency stop controls and monitoring systems to enhance operational safety.
- Scalability: Conveyor systems can be expanded or modified to meet the changing needs of a thermal power plant.
- Integration with Coal Processing: Belt conveyors seamlessly integrate with crushing, screening, and washing equipment, ensuring the coal is the correct size and quality for power generation.
Challenges Faced in Thermal Power Plant Coal Handling System
However, implementing a belt conveyor system for coal handling in thermal power plants comes with its set of challenges:
- High Volume Handling: Thermal power plants require the handling of large volumes of coal, demanding robust and high-capacity conveyor systems.
- Abrasive Nature of Coal: Coal can be highly abrasive, leading to increased tear and wear on conveyor belts and components.
- Dust Generation: Coal handling generates significant amounts of dust, posing challenges for environmental compliance and worker health.
- Varying Coal Properties: Coal properties can vary widely, requiring adaptable conveyor systems that can handle different types of coal efficiently.
- Operational Reliability: Conveyor systems must be highly reliable to prevent unscheduled downtime, which can lead to power generation losses.
- Maintenance Accessibility: Maintaining conveyor systems in the confined and complex environment of a thermal power plant can be challenging.
- Safety Risks: Coal handling poses fire and explosion risks, necessitating stringent safety measures in conveyor system design and operation.
Belt conveyors address these challenges through advanced design features such as wear-resistant materials, dust suppression systems, and safety devices. They are engineered to withstand the harsh conditions of thermal power plants while ensuring the safe, efficient, and reliable transport of coal, making them an indispensable component of modern power generation infrastructure.
FAQs about Belt Conveyor System for Coal Handling
In coal mining, the most commonly used type of conveyor is the belt conveyor. Belt conveyors are particularly prevalent due to their ability to handle large volumes of coal, their efficiency, and their adaptability to various terrains and routes. These conveyors consist of a long, continuous belt made of a durable material like rubber, PVC, or fabric, which is mounted on rollers and driven by pulleys. They are favored in mining operations for their ability to transport coal over long distances, through inclines and declines, and their capability to be configured in various layouts to suit the specific needs of a mining operation. Belt conveyors in coal mining are also appreciated for their relatively low operational costs and their contribution to reducing labor requirements by automating the coal transportation process.
A coal conveyor belt is a specialized type of conveyor belt designed specifically for transporting coal in mining operations, power plants, and other areas where coal handling is necessary. These belts are constructed to withstand the abrasive nature of coal and the associated heavy loads. They are made from durable materials that can resist wear and tear, such as heavy-duty rubber, reinforced with materials like steel cords for added strength and durability. Coal conveyor belts are also designed to be fire-resistant and may include features to minimize dust generation and spillage, which are common challenges in coal handling. The design and material choice for coal conveyor belts are critical to ensure safety, efficiency, and longevity in the harsh conditions of coal handling and transportation.
The belt conveyor is the type of conveyor most widely used to move coal in various stages of handling and processing, from mining to power generation. Belt conveyors are favored for their ability to transport large quantities of coal efficiently and reliably over both short and long distances. They can be designed to accommodate different terrains and layouts, making them highly versatile for coal transportation needs. Belt conveyors for coal handling are equipped with features like dust suppression and control systems to minimize environmental impact and ensure compliance with safety regulations. Their widespread use in coal handling is attributed to their proven performance, cost-effectiveness, and the ability to be customized to meet the specific requirements of a coal handling operation.
A coal handling system encompasses the various structures, equipment, and procedures used to manage and transport coal from the point of extraction or receipt to its final usage point, such as a power plant or industrial furnace. This system includes processes such as receiving, unloading, storing, conveying, crushing, and possibly washing the coal to prepare it for combustion or other uses. The coal handling system is designed to ensure that coal is handled efficiently, safely, and with minimal environmental impact. Key components of a coal handling system include conveyors, crushers, screens, feeders, storage facilities, and dust suppression units. The design and operation of a coal handling system are critical to the overall efficiency and safety of mining operations, power generation facilities, and any industrial process that requires coal as a fuel or raw material.
Last Updated on July 30, 2024 by Jordan Smith
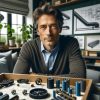
Jordan Smith, a seasoned professional with over 20 years of experience in the conveyor system industry. Jordan’s expertise lies in providing comprehensive solutions for conveyor rollers, belts, and accessories, catering to a wide range of industrial needs. From initial design and configuration to installation and meticulous troubleshooting, Jordan is adept at handling all aspects of conveyor system management. Whether you’re looking to upgrade your production line with efficient conveyor belts, require custom conveyor rollers for specific operations, or need expert advice on selecting the right conveyor accessories for your facility, Jordan is your reliable consultant. For any inquiries or assistance with conveyor system optimization, Jordan is available to share his wealth of knowledge and experience. Feel free to reach out at any time for professional guidance on all matters related to conveyor rollers, belts, and accessories.