Conveyor Belt Scale Weighing System
A belt scale weighing system is an essential component in various industrial applications, where precise measurement of bulk material flow is critical. This system plays a crucial role in industries such as mining, agriculture, construction, and manufacturing, where accurate weighing is necessary for operational efficiency, inventory management, and cost control.
Belt Weigh Scale Working Principle
Understanding the working principle of a belt weigh scale is fundamental to appreciating its functionality and accuracy. A belt weigh scale operates by measuring the weight of the material on a conveyor belt while it is in motion. This process involves several key components:
- Load Cells: These are sensors that measure the weight of the material on the belt. They are installed at specific points under the conveyor belt to detect the weight and convert it into an electrical signal.
- Speed Sensor: This device measures the speed of the conveyor belt. It is typically mounted on the tail pulley or the belt itself and provides real-time data on the belt’s speed, which is crucial for calculating the flow rate.
- Integrator: The integrator is the brain of the belt scale weighing system. It processes the signals from the load cells and speed sensor to calculate the flow rate and total weight of the material conveyed. It also allows for data logging, alarm settings, and interfacing with other control systems.
Accuracy in a belt weigh scale is achieved through several means. Firstly, the load cells are designed to be highly sensitive and durable, ensuring precise weight measurements. Secondly, the speed sensor provides accurate belt speed data, which is essential for flow rate calculations. Finally, the integrator uses advanced algorithms to process the data, compensate for any variations, and provide reliable results.
Belt Scale Weighing System Price Factors
In the realm of industrial operations, investing in a belt scale weighing system entails considerations beyond just functionality. Price plays a pivotal role in the decision-making process, influenced by a myriad of factors. Understanding these price determinants and evaluating them judiciously is essential for making informed investment decisions.
Factors Influencing the Price of a Belt Scale Weighing System
The price of a belt scale weighing system is contingent upon a multitude of factors, each exerting varying degrees of influence. Some of the key determinants include:
- System Capacity: The maximum throughput capacity of the conveyor belt system directly impacts the complexity and cost of the weighing solution. Higher capacity systems necessitate robust load cells, sophisticated signal processing algorithms, and reinforced structural components, thereby escalating the overall cost.
- Accuracy Requirements: Stringent accuracy requirements demand precision-engineered components and advanced calibration methodologies, contributing to higher system costs. Conversely, applications with less stringent accuracy tolerances may opt for cost-effective solutions without compromising performance.
- Environmental Conditions: Harsh operating environments, characterized by extremes of temperature, humidity, or corrosive elements, necessitate specialized materials and protective enclosures to ensure longevity and reliability. These additional features incur supplementary costs, reflecting in the overall price of the system.
- Integration Complexity: The degree of integration with existing control systems, data acquisition platforms, and enterprise resource planning (ERP) systems influences the complexity of the installation process. Seamless integration entails additional engineering efforts and customization, thereby impacting the overall cost.
- Customization Requirements: Tailoring the belt scale weighing system to specific application requirements often involves custom engineering, software development, and system integration. While customization enhances suitability and performance, it also entails additional costs associated with engineering resources and development efforts.
Typical Price Ranges for Various Belt Scale Systems
The price range for belt scale weighing systems varies significantly based on the aforementioned factors and the specific requirements of each application. At the lower end of the spectrum, basic belt scale systems with modest throughput capacities and moderate accuracy levels are available at relatively affordable prices, typically ranging from a few thousand to tens of thousands of dollars.
Conversely, high-end belt scale systems catering to heavy-duty industrial applications with stringent accuracy requirements command premium prices, often exceeding six figures. These sophisticated systems boast advanced features such as multi-point calibration, digital signal processing, and real-time data analytics, warranting substantial investment but delivering unparalleled performance and reliability.
Value Considerations When Investing in a Belt Scale Weighing System
While price is undeniably a critical consideration, it’s imperative to assess the value proposition offered by a belt scale weighing system holistically. Beyond the upfront cost, factors such as long-term reliability, scalability, after-sales support, and return on investment (ROI) should be carefully evaluated.
Investing in a high-quality belt scale system may entail a higher initial outlay but can yield significant dividends in terms of improved process efficiency, accurate inventory management, regulatory compliance, and enhanced profitability. Moreover, reputable manufacturers offering comprehensive warranty coverage, timely technical support, and maintenance services can mitigate operational risks and enhance the overall value proposition.
Ultimately, striking the right balance between price and value is essential for optimizing the return on investment and achieving sustainable operational excellence with a belt scale weighing system. By conducting thorough due diligence, leveraging industry expertise, and prioritizing long-term performance over short-term cost considerations, stakeholders can make informed decisions that drive business success and prosperity.

Feature of Belt Scale Weighing System
Belt scale weighing systems are designed with various features to ensure accurate and efficient measurement of bulk materials conveyed on a belt. Here are some key features and their benefits:
1. High Accuracy
- Advanced load cell technology and precise calibration ensure accurate weight measurements.
- Capable of high-precision measurements even in dynamic conditions.
- Provides reliable data for inventory management and production control.
- Reduces material wastage and improves process efficiency.
2. Robust Construction
- Built with durable materials to withstand harsh industrial environments.
- Designed to resist corrosion, dust, moisture, and extreme temperatures.
- Long-lasting performance with minimal maintenance.
- Suitable for use in demanding applications such as mining, cement, and steel industries.
3. Multiple Idler Configurations
- Available in single, dual, triple, and four-idler configurations.
- Configurations can be customized based on application needs and accuracy requirements.
- Flexibility to choose the appropriate setup for specific applications.
- Enhanced accuracy and belt support for higher precision requirements.
4. Integration Capabilities
- Can be easily integrated with existing control systems and data management platforms.
- Compatible with PLCs, SCADA systems, and other industrial automation systems.
- Seamless integration into current workflows and processes.
- Facilitates real-time monitoring and control of material flow.
5. Digital Display and User Interface
- Equipped with digital displays showing real-time weight, flow rate, and totalized weight.
- User-friendly interfaces with touchscreens and programmable settings.
- Easy to read and interpret data for operators.
- Simplifies system setup, calibration, and operation.
6. Advanced Data Logging and Reporting
- Capable of logging historical data for analysis and reporting.
- Options for data export in various formats (e.g., CSV, XML).
- Facilitates detailed analysis of production trends and material usage.
- Supports compliance with regulatory and quality standards.
7. Remote Monitoring and Diagnostics
- Options for remote access and monitoring via internet or network connections.
- Diagnostic tools for troubleshooting and maintenance alerts.
- Enables remote support and management of the weighing system.
- Reduces downtime by allowing proactive maintenance and quick issue resolution.
8. Dynamic Zero Tracking and Auto Calibration
- Dynamic zero tracking compensates for belt and environmental changes.
- Automatic calibration features ensure consistent accuracy.
- Maintains accurate measurements without manual intervention.
- Reduces the need for frequent manual recalibration.
9. Variable Speed Compensation
- Adjusts measurements to account for changes in conveyor belt speed.
- Ensures accuracy regardless of belt speed fluctuations.
- Provides consistent and reliable data in variable operating conditions.
- Enhances the flexibility of the system for different production scenarios.
10. Modular Design
- Modular components allow for easy expansion and customization.
- Simplifies installation and maintenance processes.
- Adaptable to changing needs and future upgrades.
- Reduces installation time and effort.
Belt scale weighing systems are equipped with a range of features designed to ensure accurate, reliable, and efficient measurement of bulk materials. These features contribute to improved process control, enhanced productivity, and reduced operational costs. When selecting a belt scale weighing system, consider the specific requirements of your application to choose a system with the most suitable features.

Applications of Belt Scale Weighing System
Belt scale weighing systems are essential tools in various industries for measuring the flow rate and total weight of bulk materials conveyed on a belt. Here are some key applications:
1. Mining and Quarrying
Application:
- Material: Coal, ore, minerals, aggregates.
- Purpose: Monitor production output, control material flow, inventory management.
- Benefits: Helps in optimizing production processes, ensuring efficient material handling, and reducing material wastage.
2. Cement and Construction
Application:
- Material: Cement, sand, gravel, aggregates.
- Purpose: Ensure the correct mix of raw materials, monitor production rates, manage inventory.
- Benefits: Maintains product quality, supports accurate batching processes, enhances operational efficiency.
3. Agriculture
Application:
- Material: Grains, seeds, fertilizers.
- Purpose: Measure and control the flow of materials during processing, storage, and distribution.
- Benefits: Ensures accurate delivery of materials, optimizes processing operations, aids in inventory control.
4. Food and Beverage
Application:
- Material: Raw ingredients, finished products.
- Purpose: Monitor the flow of materials in production lines, ensure proper ingredient mixing, track product output.
- Benefits: Enhances product consistency, supports quality control, reduces material waste.
5. Power Generation
Application:
- Material: Coal, biomass, other fuels.
- Purpose: Measure fuel consumption, control feed rates, monitor inventory.
- Benefits: Improves fuel management, ensures efficient energy production, helps in regulatory compliance.
6. Steel and Metal Processing
Application:
- Material: Iron ore, scrap metal, additives.
- Purpose: Measure and control raw material input, monitor production rates.
- Benefits: Optimizes material usage, ensures consistent product quality, supports efficient production processes.
7.Chemical and Pharmaceutical
Application:
- Material: Raw chemicals, powders, granules.
- Purpose: Ensure precise dosing of materials, monitor production flow, manage inventory.
- Benefits: Enhances product quality, supports compliance with industry standards, improves process efficiency.
8. Waste Management and Recycling
Application:
- Material: Waste materials, recyclable materials.
- Purpose: Measure the amount of waste processed, monitor recycling rates, manage material flow.
- Benefits: Supports efficient waste management, enhances recycling processes, ensures regulatory compliance.
9. Paper and Pulp Industry
Application:
- Material: Wood chips, pulp, recycled paper.
- Purpose: Monitor material flow, control production processes, manage inventory.
- Benefits: Ensures efficient production, maintains product quality, optimizes material usage.
Belt scale weighing systems are versatile and essential in many industries. They provide accurate and reliable measurements, helping to optimize production processes, manage inventory, ensure product quality, and support regulatory compliance. Choosing the right belt scale system tailored to the specific needs of your industry can lead to significant improvements in operational efficiency and cost savings.

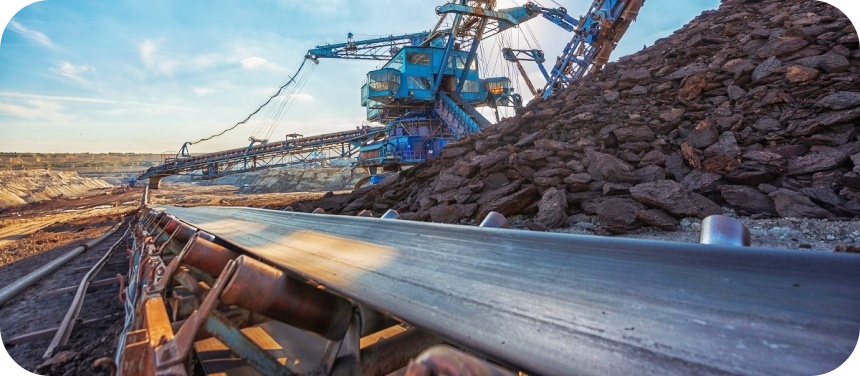
Inline Conveyor Scale Applications in Belt Scale Weighing System
Inline conveyor scales are integral components of a belt scale weighing system, designed to measure the weight of materials as they are transported on a conveyor belt. These scales are strategically placed within the conveyor system to provide continuous and real-time weight data, ensuring accurate and efficient material handling. Unlike traditional static weighing systems, inline conveyor scales allow for the measurement of bulk materials without interrupting the flow, making them ideal for high-speed and high-volume operations.
Inline conveyor scales are equipped with advanced sensors and load cells that detect the weight of the materials on the belt. This data is then transmitted to an integrator, which processes the information and provides real-time weight readings. The seamless integration of inline conveyor scales into a belt scale weighing system enhances the overall accuracy and efficiency of the weighing process.
Benefits and Applications of Using Inline Conveyor Scales
The use of inline conveyor scales in a belt scale weighing system offers numerous benefits, making them essential for various industrial applications. Here are some of the key benefits:
- Continuous Weighing: Inline conveyor scales provide continuous weight measurements, eliminating the need for manual weighing and reducing downtime. This feature is particularly beneficial in high-speed production environments where uninterrupted material flow is crucial.
- Real-Time Data: The real-time data provided by inline conveyor scales allows for immediate adjustments in the production process, ensuring optimal efficiency and reducing waste. Operators can monitor the weight of materials in real-time and make necessary changes to maintain product quality and consistency.
- Increased Accuracy: Advanced sensors and load cells in inline conveyor scales ensure high accuracy in weight measurements. This accuracy is essential for maintaining product quality, complying with industry regulations, and optimizing production processes.
- Versatility: Inline conveyor scales are versatile and can be used in various industries, including mining, agriculture, manufacturing, and food processing. They are capable of handling different types of materials, from fine powders to large aggregates, making them suitable for a wide range of applications.
Applications of Inline Conveyor Scales:
- Mining Industry: Inline conveyor scales are used to measure the weight of mined materials, ensuring accurate inventory management and optimizing the extraction process.
- Agriculture: In agriculture, inline conveyor scales help in weighing bulk commodities such as grains, seeds, and fertilizers, facilitating efficient storage and distribution.
- Manufacturing: Manufacturing industries use inline conveyor scales to monitor the weight of raw materials and finished products, ensuring quality control and efficient production.
- Food Processing: In food processing, inline conveyor scales are used to weigh ingredients and final products, maintaining consistency and compliance with food safety standards.
How Inline Conveyor Scales Enhance Operational Efficiency
Inline conveyor scales significantly enhance operational efficiency by providing accurate and continuous weight measurements, reducing manual labor, and minimizing production downtime. Here’s how they contribute to operational efficiency:
- Automated Weighing: The automation of the weighing process reduces the need for manual intervention, allowing operators to focus on other critical tasks. This automation leads to increased productivity and efficiency in the production line.
- Real-Time Monitoring: Real-time monitoring of material weight enables quick adjustments in the production process, preventing overloading or underloading of materials. This capability ensures optimal use of resources and minimizes material wastage.
- Data Integration: Inline conveyor scales can be integrated with other control systems and software, providing valuable data for process optimization and decision-making. This integration helps in identifying bottlenecks, improving workflow, and enhancing overall productivity.
- Reduced Downtime: By providing continuous weight measurements, inline conveyor scales eliminate the need for stopping the conveyor belt for weighing purposes. This reduction in downtime leads to smoother operations and higher throughput.
Belt Scale Weighing System Frames
Belt scale weighing system frames are critical components that support and stabilize the belt scale, ensuring accurate weight measurements. Here are some common types of belt scale weighing system frames and their features:
Types of Belt Scale Weighing System Frames
1. Single-Idler Frames
- Description: Consist of a single idler roller that supports the conveyor belt.
- Applications: Suitable for light to moderate duty applications.
- Advantages: Simple design, easy to install, cost-effective.
- Disadvantages: May not be suitable for high precision or heavy-duty applications.
2. Dual-Idler Frames
- Description: Incorporate two idler rollers, providing additional support to the belt.
- Applications: Used in moderate to heavy-duty applications.
- Advantages: Improved accuracy over single-idler systems, better belt support.
- Disadvantages: More complex design, higher cost compared to single-idler frames.
3. Triple-Idler Frames
- Description: Feature three idler rollers, offering enhanced support and stability.
- Applications: Ideal for heavy-duty applications and high precision requirements.
- Advantages: High accuracy, excellent belt support, suitable for harsh environments.
- Disadvantages: Complex installation, higher cost.
4. Four-Idler Frames
- Description: Utilize four idler rollers for maximum support and stability.
- Applications: Used in very heavy-duty applications where high accuracy is crucial.
- Advantages: Superior accuracy, excellent support for the conveyor belt, minimizes belt sagging.
- Disadvantages: Most complex design, highest cost, challenging installation.
5. Modular Frames
- Description: Composed of multiple sections that can be configured to fit various applications.
- Applications: Versatile, suitable for a wide range of industries and applications.
- Advantages: Customizable, easy to transport and assemble, adaptable to different conveyor systems.
- Disadvantages: Can be expensive depending on the configuration.
Choosing the Right Frame
- Load and Capacity: Select a frame that can handle the load and capacity of your conveyor system.
- Environmental Conditions: Consider frames designed for the specific environmental conditions (e.g., temperature, moisture, dust).
- Accuracy Requirements: Higher accuracy requirements typically necessitate more complex frames with multiple idlers.
- Budget: Balance the cost of the frame with the features and accuracy needed for your application.
- Ease of Installation and Maintenance: Ensure the frame can be easily installed and maintained to minimize downtime.
Recommended Frame Systems
Siemens Milltronics MSI
- Frame Types: Single-idler, dual-idler, and triple-idler frames available.
- Features: Robust construction, suitable for various industrial applications.
- Best For: High precision and heavy-duty applications.
Thermo Fisher Ramsey Series 20
- Frame Types: Single-idler and dual-idler frames.
- Features: Cost-effective, easy to install and maintain.
- Best For: General industrial use.
Rice Lake Weighing Systems
- Frame Types: Single-idler, dual-idler, triple-idler, and four-idler frames.
- Features: High accuracy, customizable options.
- Best For: Versatile applications, high accuracy needs.
Merrick Model 475
- Frame Types: Dual-idler and triple-idler frames.
- Features: Advanced load cell technology, durable design.
- Best For: Harsh environments, high flow rate applications.
Choosing the right belt scale weighing system frame involves understanding your specific application requirements, including load capacity, environmental conditions, accuracy needs, and budget. By considering these factors and reviewing the recommended frame systems, you can select the most suitable frame to ensure accurate and reliable weight measurements in your belt scale weighing system.
Roller Conveyor Scale Features and Uses in Belt Scale Weighing System
Key Features of Roller Conveyor Scales
Roller conveyor scales are another critical component of a belt scale weighing system, designed to measure the weight of items as they move along a roller conveyor. These scales are equipped with precision load cells and sensors that provide accurate weight data, making them ideal for various industrial applications. Here are some of the key features of roller conveyor scales:
- High Precision: Roller conveyor scales are designed with high-precision load cells that ensure accurate weight measurements. This precision is crucial for maintaining product quality and compliance with industry standards.
- Durability: Built to withstand harsh industrial environments, roller conveyor scales are made from robust materials that ensure long-term durability and reliability. They are capable of handling heavy loads and resisting wear and tear.
- Easy Integration: Roller conveyor scales can be easily integrated into existing conveyor systems, providing seamless operation and minimal disruption. They can be customized to fit specific conveyor configurations and requirements.
- Versatility: These scales are versatile and can handle a wide range of materials and products, from small packages to large industrial components. This versatility makes them suitable for various industries and applications.
- User-Friendly Interface: Equipped with user-friendly interfaces, roller conveyor scales allow operators to easily monitor and manage weight data. This feature enhances ease of use and operational efficiency.
Common Applications in Various Industries
Roller conveyor scales are used in a variety of industries for different applications, thanks to their accuracy, durability, and versatility. Here are some common applications:
- Logistics and Distribution: Roller conveyor scales are used in warehouses and distribution centers to weigh packages and pallets, ensuring accurate shipping and inventory management.
- Manufacturing: In manufacturing, roller conveyor scales help in weighing raw materials, components, and finished products, ensuring quality control and efficient production processes.
- Food and Beverage: The food and beverage industry uses roller conveyor scales to weigh ingredients and products, maintaining consistency and compliance with safety regulations.
- Automotive: In the automotive industry, roller conveyor scales are used to weigh parts and assemblies, ensuring accurate weight distribution and quality control.
How Roller Conveyor Scales Improve Material Handling Processes
Roller conveyor scales enhance material handling processes by providing accurate and real-time weight measurements, reducing manual labor, and improving overall efficiency. Here’s how they contribute to improved material handling:
- Accurate Weighing: The high precision of roller conveyor scales ensures accurate weight measurements, which are essential for maintaining product quality and compliance with industry standards. This accuracy reduces errors and minimizes material wastage.
- Streamlined Operations: By automating the weighing process, roller conveyor scales streamline operations and reduce the need for manual weighing. This automation leads to increased productivity and efficiency in material handling processes.
- Real-Time Data: Real-time weight data provided by roller conveyor scales allows for immediate adjustments in the handling process, optimizing resource use and reducing downtime. This capability ensures smooth and efficient material flow.
- Enhanced Workflow: The integration of roller conveyor scales into existing conveyor systems enhances workflow by providing continuous weight measurements and reducing interruptions. This integration leads to improved operational efficiency and higher throughput.
Both inline and roller conveyor scales are vital components of a belt scale weighing system, offering numerous benefits and applications in various industries. By understanding their features, benefits, and applications, businesses can select the right conveyor scales to enhance their operational efficiency and achieve accurate and reliable weight measurements.
Best Belt Scale Weighing System for Your Needs
Selecting the best belt scale weighing system for your needs involves considering several criteria to ensure it meets your operational requirements. Here are some key factors to consider:
- Accuracy: The primary criterion for any weighing system is its accuracy. Look for systems with high-precision load cells and advanced integrators that can provide accurate and consistent measurements.
- Durability: In industrial environments, the belt scale must withstand harsh conditions, including dust, moisture, and heavy loads. Choose systems made from robust materials and designed for durability.
- Ease of Maintenance: Regular maintenance is crucial for the longevity and accuracy of the belt scale weighing system. Opt for systems that are easy to maintain, with accessible components and clear maintenance guidelines.
- Compatibility: Ensure the belt scale system is compatible with your existing conveyor system and can be integrated with other control systems for seamless operation.
- Features: Look for additional features such as data logging, remote monitoring, alarm systems, and user-friendly interfaces that enhance the functionality and ease of use of the belt scale weighing system.
- Environment:Industrial Use: Systems should be robust and durable for heavy-duty environments.Harsh Conditions: Consider systems designed to withstand extreme temperatures, dust, moisture, and other harsh conditions.
- Material Being Weighed:Type of Material: Different materials (e.g., aggregates, grains, coal) may require different types of belt scales.Flow Rate: High flow rates might need specialized systems to maintain accuracy.
- Budget:Cost-Effective: Balance between cost and features based on your budget.
Advantages of using a top-rated belt scale weighing system include improved operational efficiency, accurate inventory management, cost savings, and compliance with industry standards. A reliable system ensures that you get precise measurements, which are crucial for optimizing production processes, reducing waste, and maximizing profits.
A belt scale weighing system is an indispensable tool in various industries, providing accurate and real-time data on material flow. By understanding its working principle and selecting the right system for your needs, you can ensure efficient and cost-effective operations.
Belt Conveyor Weighing System PDF Resources
In the realm of industrial operations, the efficacy of a belt scale weighing system is pivotal for accurate measurement and control. To delve deeper into understanding and optimizing these systems, accessing comprehensive resources becomes indispensable. Fortunately, a plethora of PDF documents are available, offering insights into various aspects of belt conveyor weighing systems.
Availability of PDF Resources on Belt Conveyor Weighing Systems
The digital landscape is abundant with resources elucidating the intricacies of belt scale weighing systems. Manufacturers, industry experts, and research institutions contribute significantly to this pool of knowledge. These PDF resources encompass a wide array of topics, ranging from the fundamentals of conveyor belt scales to advanced troubleshooting techniques.
How to Access and Utilize These Resources Effectively
Navigating through the multitude of PDF resources necessitates a strategic approach to extract maximum value. Various avenues facilitate access to these documents, including manufacturer websites, industry forums, and academic repositories. Moreover, subscribing to newsletters and industry publications can provide regular updates on the latest advancements and research findings in the realm of belt conveyor weighing systems.
To utilize these resources effectively, it’s imperative to adopt a systematic approach. Start by identifying specific areas of interest or challenges encountered in your operational setup. Next, scour through the available PDFs to find relevant information pertaining to your requirements. Pay close attention to case studies, best practices, and technical specifications outlined in these documents. Furthermore, leveraging search functionalities within PDF readers can expedite the process of locating pertinent information.
Key Topics Covered in Belt Conveyor Weighing System PDFs
The breadth of topics covered in belt conveyor weighing system PDFs is vast, catering to the diverse needs of industry stakeholders. Some of the key areas addressed include:
- Principles of Operation: Detailed explanations of how belt conveyor weighing systems function, including the role of load cells, signal processing algorithms, and calibration procedures.
- Installation and Calibration: Step-by-step guides for the installation, calibration, and commissioning of belt scale systems, ensuring optimal performance and accuracy.
- Troubleshooting and Maintenance: Insights into common challenges encountered during operation, along with troubleshooting strategies and preventive maintenance protocols to minimize downtime.
- Integration with Control Systems: Strategies for seamless integration of belt conveyor weighing systems with existing control and automation frameworks, enhancing process efficiency and data integrity.
- Regulatory Compliance: Compliance guidelines and standards pertaining to the installation and operation of belt scale systems, ensuring adherence to regulatory requirements and industry best practices.
By delving into these resources, stakeholders can enhance their understanding of belt scale weighing systems and leverage this knowledge to optimize their operational processes, improve efficiency, and drive business growth.
FAQs about Belt Scale Weighing System
A belt scale, also known as a belt weigh scale, is an essential component in material handling systems, used to measure the mass flow rate of bulk materials as they move along a conveyor belt. The working principle of a belt scale involves load cells, which are sensors that measure the weight of the material on the conveyor. These load cells are typically installed under the conveyor belt at specific points. As the material passes over the load cells, the weight is recorded, and the speed of the belt is measured using a speed sensor. The data from the load cells and the speed sensor are combined by a digital integrator to calculate the flow rate and total weight of the material. This real-time information helps in process control, inventory management, and ensuring compliance with industry standards.
Calibrating a belt scale is crucial to ensure its accuracy and reliability. The calibration process typically involves several steps. First, ensure the conveyor belt is empty and set the zero calibration by adjusting the scale to read zero weight. This step ensures that any residual material or mechanical influences are accounted for. Next, place a known test weight or calibration chain on the belt and run the conveyor at the normal operating speed. Record the weight measured by the belt scale and compare it to the known weight. Adjust the scale settings to correct any discrepancies between the measured and actual weights. Repeat this process multiple times to verify the accuracy. Regular calibration checks are recommended, especially after significant maintenance activities or changes in operational conditions, to maintain the precision of the belt weigh scale.
A weighing belt, also known as a belt weigh scale or conveyor belt scale, is a specialized conveyor belt system equipped with integrated weighing capabilities. It is designed to measure the weight of bulk materials being transported on the belt in real-time. The weighing belt typically includes load cells positioned at strategic points along the conveyor to detect the weight of the material passing over them. Additionally, a speed sensor is used to measure the belt’s velocity. The combination of weight and speed data allows for precise calculation of the mass flow rate and total weight of the transported material. Weighing belts are widely used in various industries, including mining, agriculture, food processing, and manufacturing, to monitor material flow, optimize production processes, and ensure accurate inventory management. The integration of a weighing system into the conveyor belt enhances operational efficiency and provides critical data for quality control and compliance with industry standards.
Belt weigh scales typically have an accuracy range of 1/10 to 1/2%, depending on the model and application. High-quality models, like Rice Lake’s BCi belt scale, are designed for high precision and reliability in demanding environments.
To ensure your scale is accurate:
Calibration: Regularly calibrate your scale using certified test weights.
Consistency: Check for consistent readings by weighing the same item multiple times.
Comparison: Compare the scale’s readings with another reliable scale.
Zeroing: Ensure the scale zeroes correctly before each use.
Yes, digital weight scales can be wrong due to factors such as:
Calibration Errors: Scales need regular calibration to maintain accuracy.
Battery Issues: Low or faulty batteries can affect performance.
Environmental Factors: Temperature, humidity, and placement on uneven surfaces can impact accuracy.
Scales weigh differently on carpet because the soft surface can cause the scale to tilt or sink, leading to inaccurate readings. Hard, flat surfaces provide a stable base, ensuring more accurate measurements.
Body fat scales use bioelectrical impedance analysis (BIA). They send a small, harmless electrical current through your body and measure the resistance to the current. Fat tissue has higher resistance compared to muscle, and the scale uses this data along with your weight, height, age, and gender to estimate body fat percentage.
At home, you can calibrate your scale using known weights such as:
Dumbbells or Free Weights: Ensure they have a known and accurate weight.
Household Items: Use items with a known weight (e.g., a gallon of water weighs approximately 8.34 pounds).
Calibration Weights: Purchase calibration weights specifically designed for this purpose.
Request a quote for our high-quality conveyor belts today.
Last Updated on August 5, 2024 by Jordan Smith
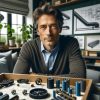
Jordan Smith, a seasoned professional with over 20 years of experience in the conveyor system industry. Jordan’s expertise lies in providing comprehensive solutions for conveyor rollers, belts, and accessories, catering to a wide range of industrial needs. From initial design and configuration to installation and meticulous troubleshooting, Jordan is adept at handling all aspects of conveyor system management. Whether you’re looking to upgrade your production line with efficient conveyor belts, require custom conveyor rollers for specific operations, or need expert advice on selecting the right conveyor accessories for your facility, Jordan is your reliable consultant. For any inquiries or assistance with conveyor system optimization, Jordan is available to share his wealth of knowledge and experience. Feel free to reach out at any time for professional guidance on all matters related to conveyor rollers, belts, and accessories.