Belt Weigh Scale: Essential for Conveyor Systems
A belt weigh scale system is an essential component in many industrial processes, providing accurate and reliable measurement of material flow on a conveyor belt. This system integrates various technologies to ensure precise weight readings, which are critical for maintaining operational efficiency and ensuring product quality.
Belt Weigh Scale Working Principle
Detailed Explanation of the Working Principle of a Belt Weigh Scale
The belt weigh scale operates on a straightforward yet highly effective principle, integrating both mechanical and electronic components to achieve precise material measurement. The core concept revolves around measuring the weight of material passing over a section of the conveyor belt and calculating the flow rate based on this weight and the belt speed.
When material moves along the conveyor belt, it passes over one or more load cells embedded in the belt weigh scale. These load cells are sensors that convert the mechanical force of the material’s weight into an electrical signal. The strength of this signal is directly proportional to the weight of the material. This signal is then transmitted to the scale’s integrator, an electronic device that processes the signal and converts it into a readable weight measurement.
In addition to the load cells, the belt weigh scale includes a speed sensor that measures the conveyor belt’s velocity. This sensor is usually mounted on a non-driven pulley of the conveyor system and detects the rotational speed, which is then translated into belt speed. The combination of weight data from the load cells and speed data from the sensor allows the integrator to calculate the material flow rate.
The basic equation used by the belt weigh scale system is:
Flow Rate (Q) = Belt Speed (v) multiplied by Load (L)
Where:
- Flow Rate (Q) is the rate at which material is being conveyed.
- Belt Speed (v) is the speed of the conveyor belt.
- Load (L) is the weight of the material per unit length of the belt.
This calculated flow rate provides a continuous and real-time measure of the material being transported, which is crucial for process control and inventory management.
Key Components Involved in the Weighing Process
Several key components work in tandem to ensure the effective operation of a belt weigh scale system:
- Load Cells: These are the primary sensors that detect the weight of the material on the conveyor belt. They are strategically placed under the belt at specific intervals to capture the weight data accurately. Load cells are designed to withstand the harsh industrial environments and provide reliable readings.
- Speed Sensor: This device measures the speed of the conveyor belt. It is usually installed on a pulley that rotates with the belt, ensuring accurate speed measurement. The speed sensor plays a crucial role in calculating the flow rate by providing real-time velocity data.
- Integrator: The integrator is the electronic unit that processes the signals from the load cells and the speed sensor. It calculates the flow rate by combining the weight and speed data, and then displays the result on a digital readout. The integrator can also send the data to a central control system for further analysis and process control.
- Weigh Frame: This is the structural frame that houses the load cells and provides support for the conveyor belt section where weighing occurs. The weigh frame must be rigid and stable to ensure accurate measurements.
- Calibration Mechanism: Regular calibration of the belt weigh scale is essential for maintaining accuracy. Calibration involves placing known weights on the belt and adjusting the system to ensure it reads correctly. Some systems include automatic calibration features for convenience and accuracy.
- Data Communication Interfaces: Modern belt weigh scales often come equipped with various communication interfaces such as RS-232, RS-485, Ethernet, and wireless options. These interfaces allow the system to transmit data to external devices or control systems for monitoring and analysis.
How the Belt Weigh Scale Ensures Accuracy and Reliability
Ensuring accuracy and reliability in a belt weigh scale system involves several factors and best practices:
- Proper Installation: The installation of the belt weigh scale must be carried out meticulously, ensuring that the load cells are positioned correctly and the speed sensor is aligned accurately. Any misalignment or improper installation can lead to erroneous readings.
- Regular Calibration: Regular calibration is crucial for maintaining the accuracy of the belt weigh scale. Calibration should be performed at intervals recommended by the manufacturer or whenever there is a significant change in the material type or conveyor belt conditions.
- Environmental Considerations: The belt weigh scale should be protected from environmental factors such as dust, moisture, and temperature fluctuations, which can affect the accuracy of the sensors. Enclosures and covers can help shield the sensitive components from harsh conditions.
- Maintenance: Routine maintenance of the belt weigh scale, including checking the load cells, speed sensor, and integrator for any signs of wear or damage, ensures the system remains in optimal working condition. Regular maintenance helps in identifying and addressing potential issues before they affect the system’s performance.
- Operator Training: Proper training of the personnel operating and maintaining the belt weigh scale is essential. Operators should be knowledgeable about the system’s components, calibration procedures, and troubleshooting techniques to ensure smooth and accurate operation.
- Software Updates: Keeping the integrator’s software up to date with the latest versions can improve the performance and accuracy of the belt weigh scale. Manufacturers often release updates that include enhancements and bug fixes.
By understanding and implementing these practices, users can ensure that their belt weigh scale provides consistent and reliable measurements, contributing to the efficiency and productivity of their operations.
Belt Weigh Scale: Conveyor Belt Scale Price Considerations
Factors Affecting the Price of a Conveyor Belt Scale
When considering the purchase of a conveyor belt scale, it’s important to understand the various factors that influence its price. Several key elements determine the cost, including:
- Quality and Durability: High-quality materials and robust construction increase the cost of a conveyor belt scale but also ensure longer lifespan and reliability. Durable scales are essential in harsh industrial environments where equipment is subjected to wear and tear.
- Accuracy and Precision: The level of accuracy required can significantly affect the price. Scales with higher precision and advanced calibration capabilities tend to be more expensive due to the sophisticated technology used.
- Load Cell Technology: The type and number of load cells used in the belt weigh scale impact its price. Advanced load cells with higher sensitivity and reliability come at a higher cost.
- Speed Sensors: Accurate speed sensors are crucial for calculating the mass flow rate. High-precision speed sensors that can operate reliably under various conditions will add to the overall cost.
- Integration and Connectivity: Conveyor belt scales with advanced integration capabilities, such as connection to SCADA systems, remote monitoring, and data logging features, tend to be more expensive due to the additional electronics and software involved.
- Installation and Calibration: Professional installation and calibration services are often required to ensure optimal performance. These services can add to the initial cost but are essential for accurate measurements and longevity of the scale.
- Brand and Manufacturer: Established brands with a reputation for quality and reliability may charge a premium for their products. However, these brands often provide better support, warranties, and after-sales services.
Typical Price Ranges for Different Types of Conveyor Belt Scales
The price of conveyor belt scales can vary widely based on the type, features, and capabilities. Here are some typical price ranges for different types of scales:
- Basic Belt Scales: Basic models designed for light-duty applications and general material handling can range from $2,000 to $10,000. These scales offer standard accuracy and minimal features, suitable for less demanding environments.
- Standard Industrial Belt Scales: For medium-duty applications in industries like agriculture, mining, and manufacturing, prices typically range from $10,000 to $30,000. These scales offer better accuracy, durability, and additional features such as more advanced load cells and speed sensors.
- High-Precision Belt Scales: For industries requiring high accuracy, such as pharmaceuticals, food processing, and chemical production, high-precision belt scales can cost between $30,000 and $100,000. These models come with sophisticated load cells, advanced electronics, and integration capabilities.
- Custom and Specialized Belt Scales: Custom-designed scales tailored for specific applications or unique operational requirements can exceed $100,000. These scales often include specialized sensors, customized integration, and enhanced durability features.
Value Considerations When Investing in a Conveyor Belt Scale
Investing in a conveyor belt scale involves more than just the initial purchase price. It’s crucial to consider the long-term value and return on investment (ROI). Here are some factors to keep in mind:
- Operational Efficiency: A high-quality belt weigh scale enhances operational efficiency by providing accurate and reliable measurements. This helps in optimizing production processes, reducing waste, and improving inventory management.
- Reduced Downtime: Investing in a durable and reliable scale minimizes downtime due to maintenance and repairs. This ensures continuous operation and reduces the risk of costly interruptions.
- Improved Product Quality: Accurate weighing is essential for maintaining product quality and consistency. This is particularly important in industries like food processing and pharmaceuticals, where precise measurements are critical.
- Regulatory Compliance: Many industries are subject to strict regulations regarding material handling and measurement accuracy. A reliable belt weigh scale helps ensure compliance with these standards, avoiding potential fines and legal issues.
- Data and Analytics: Advanced conveyor belt scales provide valuable data and analytics that can be used for process optimization and decision-making. The ability to monitor and analyze material flow in real-time leads to more informed and effective management practices.
- Support and Warranty: Consider the support and warranty offered by the manufacturer. Investing in a belt weigh scale from a reputable company with strong after-sales support ensures that any issues can be promptly addressed, minimizing operational disruptions.
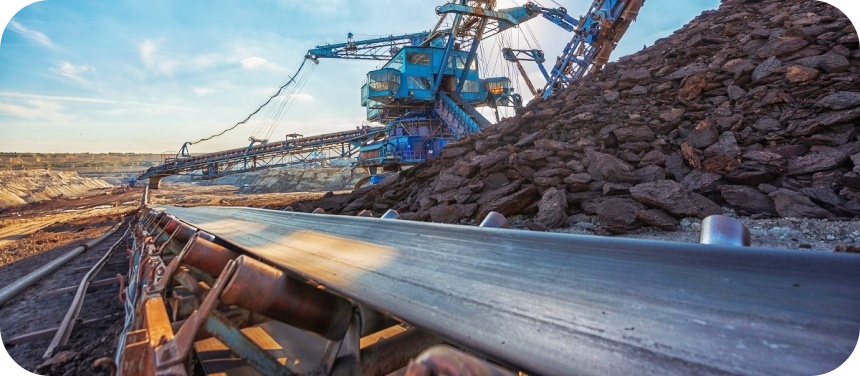
Belt Weigh Scale: Overview of Conveyor Belt Scales
Different Types of Conveyor Belt Scales Available in the Market
Conveyor belt scales come in various types, each designed to meet specific operational needs. Understanding the different types can help in selecting the right scale for your application:
- Single-Idler Belt Scales: These are the most basic type of belt scales, using a single idler to measure the load. They are suitable for light to medium-duty applications and offer a balance between cost and accuracy.
- Multi-Idler Belt Scales: Multi-idler scales use multiple idlers to distribute the load, providing higher accuracy and stability. They are ideal for applications requiring precise measurements and are commonly used in heavy-duty industries like mining and bulk material handling.
- Dual-Belt Scales: These scales use two parallel belts to measure the load. They are used in applications where high accuracy is critical, such as in chemical and food processing industries.
- Portable Belt Scales: Designed for flexibility and ease of use, portable belt scales can be moved and installed quickly. They are ideal for temporary or mobile operations, such as construction sites and remote mining locations.
- In-Motion Belt Scales: In-motion belt scales are designed to measure materials on moving conveyors without the need for stopping. They are used in high-speed applications where continuous measurement is essential.
Key Features and Benefits of Various Conveyor Belt Scales
Each type of conveyor belt scale offers unique features and benefits:
- Single-Idler Belt Scales:
- Features: Simple design, easy installation, and lower cost.
- Benefits: Suitable for general material handling, providing a cost-effective solution for basic weighing needs.
- Multi-Idler Belt Scales:
- Features: Multiple idlers for increased stability and accuracy, suitable for high-capacity applications.
- Benefits: Enhanced accuracy and reliability, ideal for demanding environments where precise measurement is crucial.
- Dual-Belt Scales:
- Features: Two belts for parallel measurement, high accuracy, and redundancy.
- Benefits: Ensures accurate measurements even in critical applications, reducing the risk of errors.
- Portable Belt Scales:
- Features: Lightweight, easy to transport and install, adaptable to various conveyor systems.
- Benefits: Flexibility for temporary or changing operations, reducing the need for permanent installations.
- In-Motion Belt Scales:
- Features: Capable of measuring materials on moving conveyors, high-speed operation.
- Benefits: Continuous measurement without interrupting the process, ideal for high-speed production lines.
Applications Where Conveyor Belt Scales are Most Effective
Conveyor belt scales are used across various industries to improve operational efficiency and accuracy. Some of the most effective applications include:
- Mining and Quarrying: Belt scales are used to measure and control the flow of extracted materials, ensuring efficient loading and transportation. Accurate measurement is essential for inventory management and optimizing the extraction process.
- Agriculture: In agricultural operations, conveyor belt scales help in weighing and distributing bulk materials such as grains, fertilizers, and feed. They ensure accurate blending and prevent wastage.
- Food Processing: Belt scales are crucial in food processing plants for measuring ingredients, ensuring consistent product quality, and maintaining compliance with regulatory standards.
- Pharmaceuticals: In pharmaceutical manufacturing, precise measurement is critical for maintaining the accuracy of dosages and formulations. Conveyor belt scales help ensure that each batch meets the required specifications.
- Recycling and Waste Management: Belt scales are used to monitor and control the flow of recyclable materials and waste, improving sorting efficiency and material recovery rates.
- Construction: In construction sites, portable belt scales are used to measure and distribute materials such as sand, gravel, and cement. They provide flexibility and accuracy in material handling.
By understanding the different types of conveyor belt scales, their features, benefits, and applications, you can make an informed decision that meets your operational needs and enhances productivity.
Comprehensive Guide on Belt Weigh Scale
Belt Conveyor Weighing System PDF Resources
Available PDF Resources on Belt Conveyor Weighing Systems
Belt conveyor weighing systems are integral components in industries where accurate measurement of bulk material is essential. These systems, often encapsulated in detailed PDF resources, provide in-depth knowledge about their design, functionality, and applications. Understanding and utilizing these resources can significantly enhance one’s ability to implement and maintain effective weighing systems in conveyor operations.
How to Access and Utilize These Resources for Better Understanding and Implementation
Accessing PDF resources on belt conveyor weighing systems is relatively straightforward. Many manufacturers and industry experts offer these documents through their official websites, technical forums, and industry-specific portals. Some common ways to access these resources include:
- Manufacturer Websites: Many companies that design and produce belt conveyor weighing systems provide comprehensive PDF manuals and guides. These documents can usually be found in the “Resources” or “Support” sections of their websites.
- Industry Portals: Websites dedicated to the material handling and processing industries often host a variety of technical papers, user manuals, and case studies in PDF format. These portals can be an excellent source for learning about different systems and technologies.
- Technical Forums and Communities: Online forums and professional networks like LinkedIn often have groups and discussions where experts share valuable PDF resources. Engaging in these communities can provide access to shared documents and firsthand advice from experienced professionals.
- Academic and Research Institutions: Universities and research organizations frequently publish studies and reports on conveyor weighing systems. These documents are typically available through academic journals, institutional repositories, or upon request from the authors.
Key Topics Covered in Belt Conveyor Weighing System PDFs
PDF resources on belt conveyor weighing systems typically cover a broad range of topics to cater to both beginners and experienced professionals. Some of the key topics include:
- System Overview: An introduction to the components and working principles of belt conveyor weighing systems. This section usually describes the different types of scales, sensors, and data processing units involved.
- Installation Guidelines: Detailed instructions on how to properly install the weighing system on a conveyor belt. This includes information on selecting the right location, mounting the hardware, and ensuring accurate alignment.
- Calibration Procedures: Step-by-step procedures for calibrating the weighing system to ensure accurate measurements. This section often includes troubleshooting tips and common calibration errors to avoid.
- Operational Best Practices: Recommendations for maintaining and operating the weighing system efficiently. Topics might cover regular maintenance schedules, software updates, and performance optimization.
- Case Studies: Real-world examples demonstrating the application of belt conveyor weighing systems in various industries. These case studies highlight the benefits, challenges, and solutions implemented in actual scenarios.
- Technical Specifications: Detailed specifications of the weighing system components, including load cells, integrators, and display units. This information helps users understand the capabilities and limitations of their systems.
Belt Weigh Scale: Beltway Scales Manual and Usage
Overview of the Beltway Scales Manual
The Beltway Scales manual is an essential document for anyone involved in the installation, operation, and maintenance of Beltway Scales. This manual provides comprehensive instructions and detailed information to ensure the scales are used correctly and effectively. It is designed to guide users through every step, from initial setup to routine maintenance, ensuring optimal performance and longevity of the equipment.
How to Use the Beltway Scales Manual for Installation and Maintenance
Using the Beltway Scales manual effectively involves several key steps:
- Familiarization with the Manual: Begin by thoroughly reading the manual to understand its structure and contents. The manual is typically divided into sections that cover different aspects of the scale’s operation and maintenance.
- Installation Instructions: Follow the step-by-step installation guidelines provided in the manual. This includes selecting the appropriate location for the scale, mounting it securely, and connecting it to the necessary power and data systems.
- Calibration Procedures: The manual provides detailed calibration instructions to ensure the scale measures accurately. This involves setting the zero point, performing test weighings, and making necessary adjustments.
- Routine Maintenance: Regular maintenance is crucial for the longevity and accuracy of Beltway Scales. The manual outlines maintenance schedules and procedures, including cleaning, inspection, and component replacement.
- Troubleshooting: The troubleshooting section helps diagnose and resolve common issues. This part of the manual is particularly useful for identifying symptoms of malfunctions and implementing corrective actions.
- Software Updates: The manual may include instructions for updating the scale’s software to the latest version, ensuring it benefits from the newest features and performance improvements.
Key Sections and Tips from the Beltway Scales Manual
- Safety Precautions: This section emphasizes the importance of safety during installation and maintenance. It provides guidelines on handling the equipment, using personal protective gear, and avoiding potential hazards.
- Component Descriptions: Detailed descriptions of each component, including load cells, digital displays, and power supplies, help users understand the functionality and interconnections of the system.
- Installation Diagrams: Visual aids such as diagrams and photographs illustrate the installation process, making it easier to follow and implement.
- Calibration Logs: Keeping a log of calibration activities is recommended. The manual may include templates for recording calibration data, which can be useful for tracking performance over time.
- Maintenance Checklists: Checklists for routine and periodic maintenance activities ensure that no important steps are overlooked. These checklists help maintain the scale in optimal working condition.
- Technical Support Contacts: Contact information for technical support is provided for situations where further assistance is needed. This can include phone numbers, email addresses, and website links for customer service.
Exploring Conveyor Scales
Conveyor scales are essential tools used across various industries for measuring the weight of materials as they move along a conveyor belt. These scales are designed to provide continuous, real-time data on material flow, which is critical for process control and inventory management. Conveyor scales come in different types and configurations, each suited to specific applications and material types.
Benefits and Applications of Using Conveyor Scales in Various Industries
- Accuracy and Efficiency: Conveyor scales offer high accuracy in measuring material weight, which is crucial for maintaining product quality and consistency. By providing real-time data, these scales help optimize production processes and reduce waste.
- Inventory Management: Accurate weight measurements are essential for effective inventory management. Conveyor scales help track the amount of material being processed, ensuring that inventory levels are maintained accurately.
- Cost Savings: By improving process efficiency and reducing material waste, conveyor scales can lead to significant cost savings. They help minimize overfilling or underfilling of products, which can be costly and affect profitability.
- Regulatory Compliance: Many industries are subject to strict regulations regarding material handling and processing. Conveyor scales ensure compliance with these regulations by providing precise and reliable weight data.
- Versatility: Conveyor scales are used in a wide range of industries, including mining, agriculture, food processing, and manufacturing. Their versatility makes them suitable for measuring various types of materials, from bulk solids to packaged goods.
How Conveyor Scales Contribute to Operational Efficiency
- Real-Time Monitoring: Conveyor scales provide continuous, real-time monitoring of material flow, allowing operators to make immediate adjustments to the production process. This helps maintain optimal operating conditions and prevents downtime.
- Automated Control Systems: Many conveyor scales are integrated with automated control systems that adjust the conveyor speed and material feed based on weight measurements. This automation enhances operational efficiency and reduces the need for manual intervention.
- Data Integration: Conveyor scales can be connected to data management systems, enabling the collection and analysis of weight data. This integration supports data-driven decision-making and helps identify areas for process improvement.
- Quality Control: By ensuring accurate weight measurements, conveyor scales contribute to consistent product quality. This is particularly important in industries where precise material proportions are critical, such as food processing and pharmaceuticals.
- Process Optimization: Conveyor scales help optimize the entire production process by providing insights into material usage and flow rates. This information can be used to streamline operations, reduce bottlenecks, and improve overall productivity.
Belt weigh scale and conveyor scales play a vital role in modern industrial operations. By leveraging available PDF resources, utilizing comprehensive manuals, and understanding the benefits and applications of these scales, industries can achieve greater accuracy, efficiency, and cost savings in their material handling processes.
Optimize your production with our expert conveyor belt solutions.
FAQs about Belt Weigh Scale
The accuracy of a belt weigh scale, also known as a conveyor belt scale, can vary depending on several factors, including the quality of the equipment, installation, maintenance, and calibration. High-quality belt scales can achieve an accuracy of ±0.25% to ±1% of the totalized weight under ideal conditions. To maintain this level of accuracy, it is essential to ensure proper alignment, tensioning, and regular calibration of the scale. Environmental factors such as temperature changes, vibration, and belt speed can also impact the accuracy, so it is crucial to monitor these variables and make adjustments as necessary.
A belt scale, or conveyor belt scale, is a device used to measure the mass of bulk material being transported on a conveyor belt. The system typically consists of load cells that measure the weight of the material on the belt, a speed sensor to determine the belt’s speed, and an integrator that calculates the total weight by combining the weight and speed data. Belt scales are widely used in various industries, including mining, agriculture, and manufacturing, to monitor and control the flow of materials, ensuring accurate inventory management, process control, and product quality.
The equation for the belt scale, often used to measure the flow rate of material on a conveyor belt, can be expressed in plain text as:
Flow Rate (Q) = Belt Speed (v) multiplied by Load (L)
Where:
Flow Rate (Q) is the rate at which material is being conveyed, typically measured in units such as kilograms per hour (kg/h) or tons per hour (t/h).
Belt Speed (v) is the speed of the conveyor belt, typically measured in meters per second (m/s) or feet per minute (ft/min).
Load (L) is the weight of the material per unit length of the belt, typically measured in kilograms per meter (kg/m) or pounds per foot (lb/ft).
So, the equation can be written as:
Q = v * L
Calibrating a belt scale involves several steps to ensure accurate measurements:
Zero Calibration: Ensure the conveyor belt is empty and run it to set the zero reference point. This step accounts for the weight of the belt and any residual materials.
Span Calibration: Use a known test weight or a chain calibration method to simulate the weight of the material. Place the test weight or chain on the belt and run the conveyor to compare the measured weight with the known weight.
Adjust the Scale: If there is a discrepancy between the measured and known weights, adjust the scale factor or calibration settings to align the measurements.
Verification: Repeat the span calibration with different weights or materials to verify the accuracy across the operating range. Make additional adjustments if necessary.
Documentation: Record the calibration settings, test weights, and results for future reference and compliance with regulatory standards.
Last Updated on July 29, 2024 by Jordan Smith
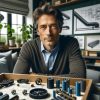
Jordan Smith, a seasoned professional with over 20 years of experience in the conveyor system industry. Jordan’s expertise lies in providing comprehensive solutions for conveyor rollers, belts, and accessories, catering to a wide range of industrial needs. From initial design and configuration to installation and meticulous troubleshooting, Jordan is adept at handling all aspects of conveyor system management. Whether you’re looking to upgrade your production line with efficient conveyor belts, require custom conveyor rollers for specific operations, or need expert advice on selecting the right conveyor accessories for your facility, Jordan is your reliable consultant. For any inquiries or assistance with conveyor system optimization, Jordan is available to share his wealth of knowledge and experience. Feel free to reach out at any time for professional guidance on all matters related to conveyor rollers, belts, and accessories.