The Best Belt Conveyor Manufacturer
Welcome to our in-depth exploration of the best belt conveyor systems, essential in modern industrial operations. Since their introduction, belt conveyors have dramatically transformed the movement of materials in factories, warehouses, and large-scale mining operations. Serving as the backbone of material handling, these systems have evolved significantly, meeting the dynamic needs of various industries. From the early 20th century’s simple designs to today’s advanced, sensor-laden models, belt conveyors reflect the technological progress in the industrial sector.
In this article, we explore the world of top belt conveyor systems, highlighting their vital role in boosting efficiency, safety, and productivity across different sectors. We will navigate through various types of belt conveyors, including Econo Pac 120, Grip Tex, GP 210M, WU 210 A/S, and Slip Top. Each type is designed for particular applications and challenges, and understanding their distinct features is crucial for selecting the ideal belt conveyor for any task, from light-duty packaging to heavy-duty mining.
Additionally, we will offer insights into the latest market trends, cutting-edge innovations, and leading manufacturers driving the evolution of conveyor technology. Integrating expert opinions and real-world case studies, this guide is designed to equip you with the knowledge needed to make well-informed choices about the best belt conveyor systems for your industrial applications. Join us on this informative journey to understand how these critical systems facilitate seamless operations in various industries, steering them towards greater efficiency and technological advancement.
Types and Applications of The Best Belt Conveyor Systems
When it comes to optimizing industrial operations, selecting the best belt conveyor system is crucial. Let’s explore the diverse types of belt conveyors, each designed to address specific material handling needs and challenges.
Exploring the best belt conveyor systems involves understanding the different types and their applications. Here are the primary types of belt conveyor systems and their uses:
Flat Belt Conveyors:
- Description: Flat belt conveyors are the most common type, consisting of a continuous belt that runs over pulleys or rollers.
- Applications: They are used in manufacturing, warehousing, and distribution for transporting products or materials over long distances. They are suitable for a variety of industries, including automotive, food processing, and packaging.
Modular Belt Conveyors:
- Description: These conveyors use interlocking plastic pieces to form the belt, providing flexibility and easy maintenance.
- Applications: Ideal for food processing, packaging, and pharmaceuticals, modular belt conveyors are used in environments that require frequent cleaning and easy belt replacement. They can handle complex paths, including curves and inclines.
Cleated Belt Conveyors:
- Description: Cleated belt conveyors have vertical cleats or barriers attached to the belt surface.
- Applications: They are used for transporting bulk materials, such as grains, minerals, and powders, up steep inclines. The cleats prevent materials from slipping and falling back. Industries such as agriculture, mining, and construction frequently utilize these conveyors.
Applications in Different Industries:
- Manufacturing: Flat belt conveyors are commonly used to move parts and products through assembly lines.
- Food Processing: Modular belt conveyors are essential for handling food items due to their sanitary design and ease of cleaning.
- Agriculture: Cleated belt conveyors are crucial for moving crops and grains, particularly in vertical farming and storage operations.
- Pharmaceuticals: Precision and cleanliness are paramount, making modular belt conveyors the preferred choice.
Understanding these types and their applications helps in selecting the best belt conveyor system to enhance productivity and efficiency in various industries.
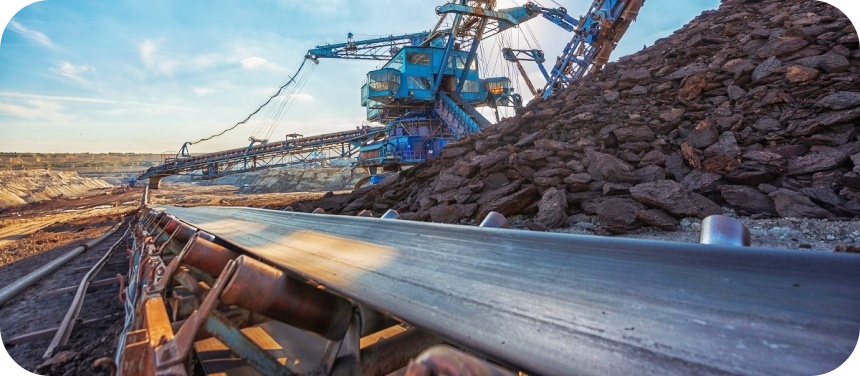
The Best Belt Conveyor Manufacturer
Determining the “best” belt conveyor manufacturer can depend on various factors such as industry needs, specific application requirements, budget, and location. Here are some globally recognized belt conveyor manufacturers known for their quality, innovation, and reliability:
- GRAM Conveyor: Renowned for their high-quality rollers and extensive industry experience, GRAM Conveyor offers a wide range of products suitable for various applications. They emphasize durability and efficiency in their designs.
- Dorner: Known for its innovative and customizable conveyor solutions, Dorner offers a wide range of conveyors, including low-profile and sanitary conveyors.
- Hytrol: Renowned for its comprehensive conveyor systems and solutions, Hytrol is a leader in the material handling industry with a focus on innovation and customer support.
- Interroll: This company is a leading global provider of material handling solutions, including conveyors and sortation systems, with a reputation for high quality and reliability.
- Siemens Logistics: Known for advanced technology and reliable conveyor systems, Siemens Logistics specializes in providing solutions for airports, parcel, and mail logistics.
Given that you are a manufacturer of conveyor belts under the brand name GRAM Conveyor and supplier of various conveyor accessories, positioning your company alongside these industry leaders by highlighting unique selling points, quality, and customer service can help establish your brand as one of the best in the industry.

Key Features of the Best Belt Conveyor Systems for Advanced Industrial Needs
In the realm of material handling, the best belt conveyor systems are distinguished not just by their ability to transport goods but also by their advanced features, which enhance efficiency, safety, and adaptability in various industrial settings.
Product Overview
- The hallmark of the best belt conveyor systems is their ability to seamlessly integrate with existing operations. A prime example is the extension from permanent conveyors into trailers, a feature that significantly eases the loading and unloading processes. This extendibility not only improves operational flexibility but also reduces manual labor and the associated risks.
Construction and Capacity
- The foundation of the best belt conveyor systems lies in their construction. A structural channel base forms a sturdy and stable framework, essential for handling significant loads. This robust construction ensures longevity and reliability in various industrial environments.
- The load capacity of these systems is a critical factor, defining their suitability for different operational scales. High load capacities are synonymous with efficiency, as they enable the handling of substantial volumes of goods, thereby optimizing throughput.
Key Features
- Ergonomic controls are a standout feature of the best belt conveyor systems. User-friendly interfaces allow for easy operation, reducing the learning curve and enhancing safety. These controls often include intuitive elements like joysticks for steering, which simplify navigation and maneuverability.
- A guide track is another essential feature, ensuring smooth extension and retraction of the conveyor, thus facilitating seamless integration with various transport vehicles and storage systems.
- Large solid tires are a notable addition, designed to ensure stability and ease of movement, especially over uneven surfaces. These durable tires are typically designed to resist wear and flatting, ensuring uninterrupted operation.
Standard Specifications
- The best belt conveyor systems boast impressive specifications that cater to a range of industrial needs. Key among these are:
- Load capacity per foot, which determines the volume of material that can be handled efficiently.
- Standard belt speed, crucial for maintaining a consistent flow of goods.
- Motor details, including power and efficiency, which play a significant role in the system’s overall performance.
- Conveyor dimensions, including width and length, which should be chosen based on the specific requirements of the operational environment.
Accessories
- The best belt conveyor systems offer a variety of accessories for customization. These may include options like Herringbone Transition for smoother material flow, Wheel Guards for added safety, Fans and Lights for better working conditions, Fused Electrical Disconnects for electrical safety, Tall Guard Rails for enhanced security during operation, and Indexing Kits with Transition Photo Eye & Switch for precision and control.
The best belt conveyor systems are characterized by their advanced features, which include efficient design, robust construction, ergonomic controls, and customizable options. These features collectively enhance the operational efficiency, safety, and adaptability of conveyor systems in various industrial settings.
Maintenance and Warranty of the Best Belt Conveyor Systems
The maintenance and warranty aspects are pivotal in the lifecycle of the best belt conveyor systems, ensuring they continue to operate at peak efficiency while offering peace of mind to the users.
Upgrade your systems with our conveyor belts. Contact us for details.
Overview of Warranty Terms for Mechanical and Electrical Components
- A key factor that defines the best belt conveyor systems is the robustness of their warranty terms, especially for mechanical and electrical components. These warranties typically cover a range of potential issues, from manufacturing defects to performance irregularities.
- Mechanical components, being the backbone of conveyor systems, often come with extended warranty periods. For instance, a standard 24-month warranty is common, reflecting the manufacturer’s confidence in the durability and quality of these components.
- Electrical components, critical for the operation of conveyors, usually have a slightly different warranty coverage, often up to 12 months. This warranty encompasses various electrical parts, ensuring that any malfunction due to material or workmanship defects can be addressed promptly and efficiently.
Services
- Technical Support: The best belt conveyor systems are backed by comprehensive technical support, ensuring that any technical queries or issues can be resolved swiftly. This support often includes access to a team of experts who can provide guidance and troubleshooting advice, either remotely or on-site.
- Installation Services: Proper installation is crucial for optimal performance. Hence, these systems often come with professional installation services. These services ensure that the conveyor is set up correctly, adhering to all safety and operational guidelines.
- Maintenance: Regular maintenance is essential for the longevity and efficiency of conveyor systems. Maintenance services might include routine inspections, parts replacement, and performance assessments, ensuring that the conveyor continues to operate smoothly over its lifespan.
- Training Options: To ensure safe and effective operation, manufacturers of the best belt conveyor systems often offer comprehensive training for operators and maintenance personnel. This training covers various aspects, including operational techniques, safety protocols, and routine maintenance procedures.
The maintenance and warranty offerings are integral to the value proposition of the best belt conveyor systems. These aspects not only ensure the smooth and efficient operation of the conveyors but also significantly contribute to their longevity and reliability, ultimately supporting the operational goals of various industries.

Global Conveyor Belt Market Overview in the Context of Best Belt Conveyor Systems
The global conveyor belt market, a critical segment in industrial automation and material handling, is undergoing significant transformations. Understanding these changes is essential when considering the best belt conveyor systems for any application.
Market Size and Forecast
- The current valuation of the global conveyor belt market stands at a substantial figure, reflecting its indispensable role in various industries. As of 2023, the market reached a value of US$ 6.8 billion, underscoring its vast scale.
- Looking ahead, the market is forecasted to grow steadily. By 2032, it’s expected to reach around US$ 8.7 billion, growing at a Compound Annual Growth Rate (CAGR) of 2.7% from 2024 to 2032. This growth trajectory highlights the increasing reliance on conveyor systems in various sectors, from manufacturing to logistics.
Innovations and Growth Drivers
- One of the key growth drivers in the market is the development of smart conveyor belts. These advanced systems, equipped with sensors, cameras, and machine learning algorithms, represent the cutting edge in conveyor technology, offering unprecedented efficiency and monitoring capabilities.
- Magnetic conveyor belts are another innovative development, particularly beneficial for handling fragile materials with utmost care. Their unique design reduces material damage, a crucial factor in industries like pharmaceuticals and electronics.
- The shift towards eco-friendly materials in conveyor belt manufacturing is not only a response to environmental concerns but also a strategic move to appeal to sustainability-conscious consumers. These materials are designed to reduce the carbon footprint of industrial operations while maintaining high performance.
Challenges and Opportunities: Balancing Automation Demands with Regulatory Compliance
- The rising demand for automation across various industries is a significant driver for the conveyor belt market. As industries strive for greater efficiency and reduced labor costs, the best belt conveyor systems are increasingly seen as a solution to these needs.
- However, this surge in automation comes with its own set of challenges, particularly in terms of safety regulations. Compliance with stringent safety standards is paramount, especially as conveyor systems become more complex and integrated into larger automated processes.
- This regulatory landscape presents both challenges and opportunities. Manufacturers who can innovate while adhering to safety regulations are likely to lead the market. This environment encourages the development of safer, more efficient, and more reliable conveyor systems, ultimately benefiting end-users.
The global conveyor belt market is a dynamic field with substantial growth potential. Innovations in technology and materials, coupled with the increasing demand for automation and the need to comply with safety regulations, are shaping the future of the best belt conveyor systems. These factors not only drive growth but also present opportunities for innovation and improvement in the industry.

Top Material Analysis in Best Belt Conveyor Systems
The best belt conveyor systems are a product of innovative engineering and quality materials. A closer look at the leading manufacturers and the materials they use reveals why these systems are essential in various industries.
Material Analysis
- Rubber
- Characteristics: Rubber is known for its durability, flexibility, and abrasion resistance, making it a popular choice in conveyor belt manufacturing.
- Applications: Ideal for general material handling, assembly lines, and incline/decline applications, rubber belts are versatile.
- Advantages: The primary advantage of rubber belts is their resilience to wear and tear, making them suitable for heavy-duty applications.
- PVC (Polyvinyl Chloride)
- Characteristics: PVC stands out for its resistance to oils and chemicals, durability in various environments, and significant tensile strength.
- Applications: PVC belts are effective in food handling and environments where physical resistance is crucial.
- Advantages: Their strength makes PVC belts less prone to breakage, offering a reliable solution in demanding conditions.
- Urethane
- Characteristics: Urethane is celebrated for its flexibility, sanitary properties, and excellent elastic memory, which allows it to maintain shape under stress.
- Applications: Urethane belts are ideal for environments requiring high standards of sanitation, such as food handling.
- Advantages: The longevity of urethane belts is a key advantage, as they typically outlast other materials in conveyor belt applications.
The best belt conveyor systems are a synergy of innovative manufacturing and high-quality materials. The leading manufacturers in this industry, such as Bando Chemical Industries, Fenner, and Intralox, continue to set the standard with their advanced and specialized solutions. The choice of material—be it rubber, PVC, or urethane—plays a pivotal role in determining the application, durability, and efficiency of the conveyor belts, making material selection a key consideration in the quest for the best conveyor system.
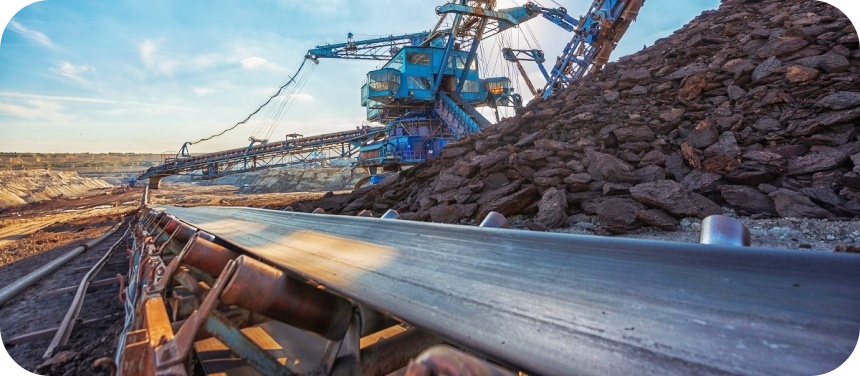
FAQs about Best Belt Conveyor
The “best” conveyor belt depends on the specific requirements of your application. For general material handling, PVC belts are popular due to their durability and versatility. For heavy-duty applications, rubber belts are preferred for their strength and resilience. For food handling or sanitary environments, urethane or food-grade PVC belts are recommended for their hygiene and maintenance ease.
Bando Chemical Industries, Ltd.: Known for a broad range of high-quality conveyor belts and chemical products.
Fenner PLC: Specializes in durable and high-performance power transmission belts and industrial hoses.
Intralox: Renowned for innovative conveying solutions, particularly in food-grade conveyor belts.
Volta Belting Technology Ltd.: Offers a variety of homogenous conveyor belts for multiple industries.
Fives: An industrial engineering group that provides advanced conveyor systems integrated with automation technologies.
The best conveyor belt companies are often those that specialize in a range of products and offer solutions for various industries. This includes companies like Bando Chemical Industries, Fenner PLC, Intralox, Volta Belting Technology Ltd., and Fives. These companies are recognized for their innovation, quality, and comprehensive product offerings.
The largest conveyor belt company can vary based on different criteria such as revenue, global presence, or production capacity. Historically, companies like Continental AG (especially after acquiring Veyance Technologies) and Bridgestone have been major players and are often cited as among the largest in the industry. However, for the most current information, especially in a rapidly evolving market, a recent industry analysis would be required.
The three main types of conveyor belts are flat belt conveyors, modular belt conveyors, and cleated belt conveyors. Flat belt conveyors are the most common and are used to transport items through irregular or flat-bottomed surfaces. They are versatile and can handle a wide range of materials, making them ideal for many industries. Modular belt conveyors are made up of interlocking plastic pieces, providing flexibility and easy maintenance. They are often used in food processing and packaging industries due to their ease of cleaning and ability to navigate curves and inclines. Cleated belt conveyors feature vertical cleats or barriers on the belt surface, which help in moving items up steep inclines and prevent materials from slipping. This type is particularly useful in industries that handle bulk materials, such as agriculture, mining, and manufacturing.
Last Updated on July 10, 2024 by Jordan Smith
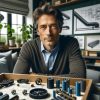
Jordan Smith, a seasoned professional with over 20 years of experience in the conveyor system industry. Jordan’s expertise lies in providing comprehensive solutions for conveyor rollers, belts, and accessories, catering to a wide range of industrial needs. From initial design and configuration to installation and meticulous troubleshooting, Jordan is adept at handling all aspects of conveyor system management. Whether you’re looking to upgrade your production line with efficient conveyor belts, require custom conveyor rollers for specific operations, or need expert advice on selecting the right conveyor accessories for your facility, Jordan is your reliable consultant. For any inquiries or assistance with conveyor system optimization, Jordan is available to share his wealth of knowledge and experience. Feel free to reach out at any time for professional guidance on all matters related to conveyor rollers, belts, and accessories.