Maximizing Efficiency with Broons Impact Roller Technology
Broons stands at the forefront of the compaction industry, renowned for its innovative engineering and commitment to delivering robust solutions for ground and soil compaction. As a leading manufacturer, Broons has carved a niche for itself by developing equipment that meets the rigorous demands of construction, mining, and agriculture. Among its esteemed lineup, the Broons impact roller emerges as a pivotal tool, designed to enhance the efficiency and effectiveness of compaction projects across a diverse array of sectors. This specialized roller is not just a piece of machinery; it represents a leap in dynamic compaction technology, offering unparalleled depth and uniformity in soil compaction. The introduction of the Broons impact roller has revolutionized how professionals approach compaction tasks, providing a versatile solution that caters to the complex requirements of modern infrastructure projects, agricultural land management, and mining operations. Its significance in these sectors underscores Broons’ role in advancing compaction techniques and equipment, setting new standards for performance and reliability.
Broons Impact Rollers: Overview
The Broons impact roller represents a significant advancement in the field of compaction technology, setting itself apart from traditional compaction equipment through its innovative design, operating principles, and unique features. At the heart of its design is the commitment to delivering deep, effective compaction across a variety of soil types and conditions, making it a versatile tool for numerous industries.
Design and Operating Principles:
The Broons impact roller is engineered with a focus on maximizing compaction efficiency and depth. Unlike conventional rollers that rely on weight and vibration, the Broons impact roller utilizes a dynamic compaction technique. This involves a non-circular, multi-sided module that imparts a high-energy impact to the ground. As the roller moves, its uniquely shaped modules lift and drop, delivering substantial kinetic energy directly into the soil. This action not only compacts the surface layer but also transmits force deeper into the subsoil, achieving compaction at depths that traditional rollers cannot reach.
Unique Features:
- Non-Circular Modules: The distinct shape of the impact roller’s modules allows for a more significant and focused impact force, enhancing deep compaction capabilities.
- High-Energy Impact: Each module strike delivers a powerful force, effectively compacting both cohesive and non-cohesive soils.
- Versatility: Suitable for a wide range of applications, from road construction and land reclamation to mining and agricultural projects.
Development of the BH-1300 Square Impact Roller:
The BH-1300 square impact roller marks a pivotal development in rolling dynamic compaction technology. Introduced by Broons, this model has played a crucial role in the evolution of compaction methods, offering a solution that is both innovative and effective. The BH-1300 is characterized by its 8-tonne, 1.3m wide module, designed to meet the diverse needs of various compaction projects. Its development was driven by the need for a compaction tool that could deliver deeper and more uniform compaction across different soil conditions and types.
Roles in Pioneering Rolling Dynamic Compaction Technology:
Deep Compaction: Achieving compaction at depths unreachable by traditional methods.
Efficiency: Reducing the time and passes needed to achieve desired compaction levels.
Versatility: Adapting to a wide range of soil types and project requirements.
Environmental Benefit: Lowering the carbon footprint by reducing the number of passes and machinery needed.
Cost-Effectiveness: Minimizing project costs through improved efficiency and reduced equipment wear.
Innovation: Introducing a new approach to compaction that challenges conventional practices.
Safety: Enhancing project safety by ensuring more stable and reliable ground conditions.
Sustainability: Contributing to more sustainable construction and mining practices through efficient resource use.
The Broons impact roller, particularly the BH-1300 model, embodies the company’s commitment to innovation, efficiency, and sustainability. Its introduction has not only provided a practical solution to the challenges of traditional compaction methods but has also set new standards in the compaction industry, reinforcing Broons’ position as a leader in the field.
Main Models and Specifications of Broons Impact Roller
Broons impact rollers are renowned for their robust design and versatility in various compaction tasks, particularly in the construction and mining industries. These rollers are designed to deliver deep compaction, effectively breaking up and compacting soil, sub-base, and other materials to create a solid foundation for roads, constructions, and mining operations. Below is an overview of the main models, including the BH-1300 and mining-specific versions, along with their specifications and intended applications.
Overview of Broons Impact Roller Models
Features and Benefits of Broons Impact Rollers
The Broons impact rollers are designed with specific features to enhance their effectiveness and versatility across different soil types and conditions. Here’s a detailed look at these features and the benefits they offer:
Broons impact rollers, particularly models like the BH-1300 and the mining-specific versions, are engineered to meet the rigorous demands of modern construction and mining projects. Their unique design and construction offer deep compaction, versatility across different soil types, and enhanced durability for long-term use. Whether for general construction, road building, or specialized mining operations, Broons impact rollers provide a reliable and effective solution for compaction needs.
Broons Impact Roller Price and Availability
The Broons impact roller stands out in the compaction industry for its innovative design and effectiveness across various applications. Understanding the pricing range and availability of the Broons impact roller is crucial for potential buyers looking to invest in high-quality compaction equipment. This section provides an in-depth look at the factors influencing the cost of Broons impact rollers and outlines the purchasing options available.
Pricing Range and Influencing Factors:
The price of a Broons impact roller can vary significantly based on several key factors, including the model, specifications, and any additional features that may be required for specific projects. The following table provides a general overview of how these factors can influence the cost of Broons impact rollers:
Purchasing Options:
Broons offers flexible purchasing options for its impact rollers, catering to a wide range of budgetary and project needs. Potential buyers can choose between new and used equipment, each with its own set of advantages:
- New Equipment Sales: Purchasing a new Broons impact roller ensures access to the latest technology and full manufacturer support, including warranty and maintenance services. Buyers can also specify custom features to meet their project’s specific requirements. Interested parties can contact Broons directly or through authorized dealers to inquire about new models, pricing, and any ongoing promotions.
- Used Equipment Sales: For those with budget constraints or looking for cost-effective solutions, Broons occasionally offers used impact rollers for sale. These units are typically refurbished to ensure they meet Broons’ quality standards, offering a balance between performance and price. Availability of used equipment can vary, so potential buyers are encouraged to check Broons’ website regularly or contact their sales team for the most current listings.
Whether opting for a new or used Broons impact roller, buyers can expect a durable, high-performance piece of equipment that delivers on the promise of efficient and effective compaction. For detailed pricing, specifications, and availability, interested parties are advised to reach out directly to Broons through their official website or authorized dealers, ensuring they receive the most accurate and up-to-date information.
Parts and Maintenance of Broons Impact Roller
The Broons impact roller is a crucial piece of equipment in the construction and mining industries, known for its robust design and effectiveness in soil compaction. Proper maintenance and understanding of its parts are essential for ensuring the longevity and efficiency of this machinery. This section provides an overview of the basic components of Broons impact rollers, their functions, and a guide to maintenance practices.
Overview of Basic Components and Their Functions
Broons impact rollers consist of several key components, each playing a vital role in the machine’s operation and effectiveness:
- Module: The core of the impact roller, typically non-circular, designed to deliver dynamic compaction energy. Its unique shape allows for effective soil breakup and compaction.
- Frame: Supports the module and connects to the towing vehicle. It’s engineered to withstand the stresses of compaction operations.
- Hydraulic System: Used for raising and lowering the module for transport and operation. It ensures precise control over the compaction process.
- Tires: Heavy-duty tires are designed to handle the weight of the roller and the rigors of compaction tasks, providing stability and mobility.
- Linkage: Connects the frame to the module and allows for the transfer of compaction energy to the ground.
Maintenance Practice Guide
To ensure the Broons impact roller remains effective and efficient, regular maintenance is crucial. Here’s a guide to best practices in maintenance, including parts availability and support from Broons:
- Regular Inspections: Conduct thorough inspections of all components, particularly before and after use. Look for signs of wear, damage, or hydraulic fluid leaks.
- Cleaning: Keep the roller clean from debris and dirt that could affect its operation. Pay special attention to the module and hydraulic system.
- Lubrication: Regularly lubricate moving parts to reduce friction and prevent wear. Use the recommended lubricants for the best results.
- Hydraulic System Maintenance: Check hydraulic fluid levels and the condition of hoses and fittings. Replace any worn or damaged parts immediately.
- Tire Inspection and Maintenance: Ensure tires are properly inflated and in good condition. Replace tires that show significant wear or damage.
- Parts Replacement: Use only genuine Broons parts for replacements to maintain the integrity and performance of the roller. Broons impact rollers are designed with parts availability in mind, ensuring that replacements are readily accessible.
- Broons Support: Take advantage of Broons’ support services, including technical assistance, maintenance advice, and parts supply. Broons offers comprehensive support to ensure your impact roller operates at peak efficiency.
Following these maintenance practices will help extend the life of your Broons impact roller and ensure it continues to perform effectively in compaction tasks. Regular maintenance not only prevents downtime but also contributes to the safety and productivity of your operations.
Practical Applications and Case Studies of Broons Impact Roller
The Broons impact roller has been instrumental in transforming the landscape of compaction tasks across a myriad of sectors. Its versatility and efficiency have made it a preferred choice for projects ranging from mining operations to agricultural improvements and large-scale infrastructure developments. This section delves into the practical applications of the Broons impact roller and presents case studies that underscore its significant contributions to project success, productivity, environmental benefits, and cost-effectiveness.
Mining Operations:
In the harsh and demanding environment of mining, the Broons impact roller has proven to be an invaluable asset. Its robust design and deep compaction capabilities have been utilized for constructing and maintaining tailings dams, preparing haul roads, and compacting waste dumps. A notable case study involves a mining site where the BH-1300 model was deployed to compact a tailings dam. The impact roller’s ability to achieve deep compaction ensured the structural integrity of the dam, significantly reducing the risk of failure and environmental contamination. Moreover, its efficiency in operation led to a reduction in project time and costs, showcasing the roller’s cost-effectiveness and contribution to sustainable mining practices.
Agricultural Land Improvement:
The Broons impact roller has also found applications in the agricultural sector, where soil compaction can influence water retention and crop yields. In one case, a farm utilized the impact roller to improve the soil structure of its fields. The compaction achieved helped in optimizing water usage and increasing the land’s productivity, demonstrating the roller’s role in enhancing agricultural efficiency and sustainability.
Infrastructure Projects:
Large-scale infrastructure projects, including road construction, airport runways, and commercial developments, have benefited from the deployment of Broons impact rollers. One case study highlights the use of the impact roller in the construction of a new highway. By ensuring a solid and compact foundation, the impact roller contributed to the longevity and durability of the road, reducing maintenance needs and future costs. The project exemplified the roller’s effectiveness in achieving uniform compaction over large areas, its productivity, and its positive impact on the project’s overall budget and timeline.
Environmental Benefits:
Beyond its direct applications in compaction tasks, the Broons impact roller offers significant environmental advantages. Its efficiency reduces the number of passes required for compaction, thereby lowering fuel consumption and emissions. Additionally, in projects such as land reclamation and landfill capping, the impact roller’s ability to compact and stabilize materials contributes to environmental protection and conservation efforts.
Cost-Effectiveness:
Across all sectors, the Broons impact roller stands out for its cost-effectiveness. By delivering high-quality compaction results in less time and with fewer resources, the impact roller reduces operational costs. Its durability and low maintenance requirements further contribute to its economic advantages, making it a wise investment for projects seeking to optimize their budgets without compromising on quality or performance.
The Broons impact roller has demonstrated its value and versatility through its applications in various industries. The case studies presented here are a testament to its role in enhancing project outcomes, contributing to environmental sustainability, and offering a cost-effective solution for compaction needs. Its continued use in diverse projects around the world underscores Broons’ commitment to innovation and excellence in compaction technology.
Broons Roller Roller Series: Beyond Impact Compaction
The Broons impact roller series is renowned for its effectiveness in deep compaction, particularly in construction and mining applications. However, Broons’ commitment to providing comprehensive compaction solutions extends beyond the impact roller. The company offers a range of specialized rollers, including the Broons Rock Buster, Multi-function Combination Roller, and Grid Roller. Each of these rollers is designed to meet specific compaction needs, offering versatility and efficiency in various scenarios. Here, we explore the applications and advantages of each roller type, including how they complement impact rollers for a complete compaction solution.
Overview of Broons Roller Range
Specific Applications and Advantages
- Broons Rock Buster: This roller is specifically designed for the challenging task of breaking and compacting oversized rock in mining and quarry operations. Its robust design allows it to tackle large rocks without the need for blasting, making it a safer and more environmentally friendly option. When used in conjunction with impact rollers, the Rock Buster prepares the ground by reducing rock size, allowing for more effective deep compaction.
- Multi-function Combination Roller: Recognizing the diverse needs of compaction projects, Broons developed the Multi-function Combination Roller to offer versatility. This roller can switch between smooth drum for fine soils, padfoot for cohesive soils, and pneumatic tires for finishing and sealing surfaces. Its adaptability makes it an excellent follow-up to impact roller compaction, ensuring a smooth and well-compacted surface across various soil types.
- Grid Roller: The Grid Roller is designed for the compaction of sub-base layers and coarse soils. Its grid pattern and weight help to crush and compact larger aggregates, making it suitable for the initial stages of road construction and site preparation. When used after an impact roller, it ensures a thoroughly compacted base, ready for subsequent construction phases.
The Broons roller series, with its range of specialized equipment, provides a comprehensive solution for compaction needs across different industries. By selecting the appropriate roller for each stage of compaction, from breaking down oversized rock with the Rock Buster to final surface preparation with the Multi-function Combination Roller or Grid Roller, project managers can achieve optimal compaction results. This strategic approach enhances the efficiency and effectiveness of compaction tasks, ensuring the longevity and stability of the constructed infrastructure.
FAQs about Broons Impact Roller
Impact rollers, also known as dynamic compaction rollers, are specialized pieces of heavy machinery designed for ground compaction tasks. Their primary use is to enhance the density and stability of soil, gravel, asphalt, and other materials in construction projects, mining operations, agricultural land improvements, and infrastructure development. Unlike traditional rollers, impact rollers utilize a unique mechanism that involves dropping heavy weights from a significant height onto the ground surface or employing non-circular, multi-sided modules that deliver high-energy impacts to the soil. This method allows for deep compaction, effectively consolidating the soil layers beneath the surface, which is crucial for creating a solid foundation for roads, buildings, and other structures. Impact rollers are particularly beneficial in projects where deep compaction is required to ensure the structural integrity and longevity of the construction, making them an invaluable tool in the compaction equipment arsenal.
The best roller for compaction depends on the specific requirements of the project, including the type of material being compacted, the depth of compaction needed, and the project’s scale. Generally, three main types of rollers are used for compaction tasks: smooth wheeled rollers, padfoot rollers, and vibratory rollers. Smooth wheeled rollers are ideal for compacting shallow layers of granular materials and finishing asphalt surfaces. Padfoot rollers, with their protruding knobs, are better suited for compacting cohesive soils at greater depths. Vibratory rollers, which generate vibrations through the drum, are highly effective in compacting a wide range of soil types and depths. For deep compaction needs, especially in unconsolidated soils or large areas requiring significant energy input, impact rollers are considered the best option due to their unique ability to deliver high-impact energy deep into the ground, ensuring a more stable and densely compacted surface.
The three primary types of rollers used in compaction tasks are:
Smooth Wheeled Rollers: These rollers have a smooth steel drum and are primarily used for compacting granular materials like sand, gravel, and asphalt. They are effective for finishing surfaces and are commonly used in road construction and repair.
Padfoot Rollers: Also known as sheepsfoot rollers, padfoot rollers feature a drum with numerous protruding pads or “feet.” These rollers are designed to compact fine-grained soils, including clay and silt, by kneading and compressing the soil to achieve higher density. They are particularly effective in compacting cohesive soils to greater depths.
Vibratory Rollers: Vibratory rollers can be smooth drum or padfoot and are equipped with an internal mechanism that generates vibrations. These vibrations enhance the compaction force applied to the soil, making vibratory rollers highly versatile and effective in compacting both cohesive and non-cohesive soils across various depths.
Each type of roller has its specific applications and is selected based on the soil type, compaction depth, and project requirements to achieve the desired compaction level efficiently.
The main difference between impact rollers and vibratory rollers lies in their compaction mechanism and the depth of compaction they can achieve. Impact rollers utilize a high-energy impact force to compact the soil. This is achieved either by dropping heavy weights from a height or using non-circular, multi-sided modules that deliver powerful impacts to the ground. This method allows impact rollers to achieve deep compaction, making them suitable for projects requiring consolidation of soil layers well below the surface.
On the other hand, vibratory rollers use a combination of weight and vibrations to compact the soil. The vibrations, generated by an internal mechanism, reduce the friction between soil particles, allowing them to move closer together and achieve compaction. Vibratory rollers are highly versatile and can be used on various soil types and compaction depths, but they are generally more effective in shallow to medium compaction depths compared to the deep compaction capabilities of impact rollers.
Last Updated on April 10, 2024 by Jordan Smith
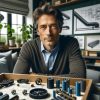
Jordan Smith, a seasoned professional with over 20 years of experience in the conveyor system industry. Jordan’s expertise lies in providing comprehensive solutions for conveyor rollers, belts, and accessories, catering to a wide range of industrial needs. From initial design and configuration to installation and meticulous troubleshooting, Jordan is adept at handling all aspects of conveyor system management. Whether you’re looking to upgrade your production line with efficient conveyor belts, require custom conveyor rollers for specific operations, or need expert advice on selecting the right conveyor accessories for your facility, Jordan is your reliable consultant. For any inquiries or assistance with conveyor system optimization, Jordan is available to share his wealth of knowledge and experience. Feel free to reach out at any time for professional guidance on all matters related to conveyor rollers, belts, and accessories.