Comprehensive Guide to Bulk Material Belt Conveyor Systems
Bulk material belt conveyors are essential systems used across various industries for the efficient transportation and handling of bulk materials. These conveyors are designed to move large quantities of materials, such as minerals, grains, and other bulk goods, with minimal effort and high efficiency. The importance of bulk material belt conveyors lies in their ability to streamline operations, reduce labor costs, and improve productivity. In this blog, we will explore the definition and significance of bulk material belt conveyors, delve into their key features and advancements, discuss how to select the right conveyor for your needs, and provide insights into top manufacturers and maintenance tips.
The Role of Bulk Material Belt Conveyors in Material Handling
Bulk material belt conveyors play a pivotal role in the material handling processes across various industries. These systems are designed to transport large volumes of bulk materials efficiently and reliably, making them fundamental to the operations of many businesses. From mining and agriculture to manufacturing and logistics, the ability to move materials seamlessly is crucial for maintaining productivity and reducing operational costs. In this section, we will explore how bulk material belt conveyors contribute to the efficient transportation and handling of bulk materials.
Efficient Transportation of Bulk Materials
One of the primary advantages of bulk material belt conveyors is their ability to transport bulk materials over long distances with minimal effort. Traditional methods of material handling, such as manual labor or the use of small vehicles, can be time-consuming, labor-intensive, and costly. Bulk material belt conveyors offer a more streamlined solution, capable of moving materials continuously and at high speeds. This efficiency is particularly beneficial in industries where large quantities of materials need to be transported regularly.
For example, in the mining industry, bulk material belt conveyors are used to transport extracted minerals from the mining site to processing plants. These conveyors can handle heavy loads and operate in harsh environments, making them ideal for mining operations. Similarly, in the agricultural sector, bulk material belt conveyors are used to move grains, seeds, and other agricultural products from storage silos to processing facilities. This not only speeds up the transportation process but also reduces the risk of product damage and loss.
Reducing Operational Costs
By automating the transportation of bulk materials, bulk material belt conveyors significantly reduce the reliance on manual labor, leading to lower operational costs. Manual handling of bulk materials often requires a large workforce, which can be expensive and prone to human error. With bulk material belt conveyors, businesses can minimize the number of employees needed for material handling tasks, allowing them to reallocate labor resources to other critical areas of operation.
In addition to labor savings, bulk material belt conveyors also contribute to cost reductions through improved energy efficiency. Modern conveyor systems are designed to operate with minimal energy consumption, using advanced technologies such as variable frequency drives (VFDs) and energy-efficient motors. These features not only lower energy costs but also reduce the environmental impact of material handling operations.
Enhancing Productivity and Throughput
The continuous and reliable operation of bulk material belt conveyors enhances productivity and throughput in material handling processes. Unlike manual handling or intermittent transportation methods, conveyors provide a constant flow of materials, ensuring that production lines remain supplied without interruptions. This continuous flow is essential for maintaining high levels of productivity, especially in industries where production schedules are tightly managed.
For instance, in manufacturing plants, bulk material belt conveyors are used to transport raw materials to various stages of production. By ensuring a steady supply of materials, conveyors help maintain the efficiency of the production process, reducing downtime and increasing output. In logistics and distribution centers, bulk material belt conveyors facilitate the rapid movement of goods, speeding up the sorting and shipping processes and improving overall efficiency.
Versatility and Customization
Bulk material belt conveyors are highly versatile and can be customized to meet the specific needs of different industries and applications. They can be designed to handle a wide range of materials, from fine powders to large, coarse aggregates. Additionally, conveyors can be configured to operate in various environments, including indoor and outdoor settings, and can be adapted to accommodate different layout requirements.
Customization options for bulk material belt conveyors include adjustable conveyor speeds, different belt materials and widths, and various loading and unloading configurations. These features allow businesses to tailor their conveyor systems to their unique operational needs, ensuring optimal performance and efficiency. For example, food processing plants may use stainless steel belt conveyors to meet hygiene standards, while construction sites might opt for heavy-duty conveyors with reinforced belts to handle abrasive materials.
Improving Safety and Reducing Risks
Safety is a critical concern in material handling operations, and bulk material belt conveyors play a significant role in improving workplace safety. Manual handling of bulk materials can pose numerous risks, including injuries from lifting heavy loads, slips and falls, and exposure to hazardous substances. By automating the transportation process, conveyors reduce the need for manual labor and minimize the associated risks.
Modern bulk material belt conveyors are equipped with safety features such as emergency stop buttons, safety guards, and automatic shut-off systems. These features help prevent accidents and ensure the safe operation of the conveyors. Additionally, regular maintenance and inspection of conveyor systems can further enhance safety by identifying and addressing potential issues before they lead to accidents.
Bulk material belt conveyors are indispensable tools in the material handling processes of various industries. Their ability to efficiently transport bulk materials, reduce operational costs, enhance productivity, and improve safety makes them fundamental to the success of many businesses. As technology continues to advance, the capabilities and applications of bulk material belt conveyors are expected to expand, offering even greater benefits to industries worldwide.
Types of Bulk Material Belt Conveyors
Bulk material belt conveyors come in various designs, each tailored to specific applications and operational requirements. Understanding the different types of bulk material belt conveyors and their unique features is crucial for selecting the right system for your needs. In this section, we will describe the various types of bulk material belt conveyors, including standard belt conveyors, heavy-duty belt conveyors, troughed belt conveyors, and closed conveyors.
Standard Belt Conveyors
Standard Belt Conveyors are the most common type of bulk material belt conveyor used across numerous industries. These conveyors are designed for the general transportation of bulk materials and are suitable for a wide range of applications. Standard belt conveyors consist of a continuous belt made from various materials, such as rubber, PVC, or fabric, which moves over pulleys and rollers to transport materials.
Common Applications and Design:
- Applications: Standard belt conveyors are used in industries like agriculture, manufacturing, and food processing. They are ideal for moving items such as grains, packaged goods, and light to medium-weight bulk materials.
- Design: These conveyors feature a simple and straightforward design, making them easy to install and maintain. The belt width, length, and speed can be customized to meet specific operational requirements. Standard belt conveyors can be used in horizontal or inclined configurations, depending on the needs of the application.
Heavy Duty Belt Conveyors
Heavy Duty Belt Conveyors are engineered to handle larger loads and operate in harsh conditions. These conveyors are built with robust materials and components to withstand the rigors of demanding environments. Heavy-duty belt conveyors are essential for industries that deal with heavy or abrasive materials, such as mining, construction, and metalworking.
Engineered for Larger Loads and Harsh Conditions:
- Applications: Heavy-duty belt conveyors are commonly used to transport materials like coal, ores, gravel, and scrap metal. They are also employed in heavy industrial processes where durability and reliability are critical.
- Design: The design of heavy-duty belt conveyors includes reinforced belts, heavy-duty rollers, and sturdy frames. These conveyors are often equipped with features like impact beds and wear-resistant liners to protect against material impact and abrasion. They can operate in extreme temperatures and challenging conditions, ensuring continuous and efficient material handling.
Troughed Belt Conveyors
Troughed Belt Conveyors are designed to form a trough shape, which helps contain and protect bulk materials during transportation. This design minimizes material spillage and environmental contact, making troughed belt conveyors ideal for handling loose or fine materials.
Usage in Bulk Goods Protection by Minimizing Environmental Contact:
- Applications: Troughed belt conveyors are used in industries such as mining, agriculture, and cement production. They are suitable for transporting materials like sand, gravel, grains, and cement.
- Design: The belt of a troughed conveyor is supported by a series of idlers arranged in a “V” or “U” shape, creating a trough that holds the material securely. The trough design reduces the risk of material spillage and helps contain dust, making it a cleaner and more efficient option for bulk material handling. Troughed belt conveyors can be used in both horizontal and inclined configurations, depending on the application requirements.
Closed Conveyors
Closed Conveyors are designed to provide enhanced protection for materials and the environment by enclosing the conveyor belt. This design prevents dust emissions, protects materials from external contaminants, and reduces the risk of material loss. Closed conveyors are essential for applications where dust control and material integrity are critical.
Enhancements for Dust Prevention and Material Protection:
- Applications: Closed conveyors are used in industries such as chemicals, pharmaceuticals, and food processing, where maintaining product purity and preventing contamination are paramount. They are also used in bulk material handling applications where dust control is a significant concern.
- Design: Closed conveyors feature an enclosed structure that surrounds the conveyor belt, providing a sealed environment for material transportation. This enclosure can be made from various materials, including metal or plastic, depending on the specific application requirements. The enclosed design helps prevent dust from escaping and protects the material from external factors such as moisture, dirt, and pests. Additionally, closed conveyors can be equipped with ventilation and dust extraction systems to further enhance dust control and air quality.
Understanding the different types of bulk material belt conveyors and their specific applications is crucial for optimizing material handling processes. Standard belt conveyors offer a versatile and cost-effective solution for general bulk material transportation. Heavy-duty belt conveyors are designed for the most demanding environments, ensuring reliable performance with heavy and abrasive materials. Troughed belt conveyors provide superior material containment and protection, making them ideal for loose or fine materials. Finally, closed conveyors offer enhanced dust prevention and material protection, making them essential for applications requiring high levels of cleanliness and environmental control.
Selecting the right type of bulk material belt conveyor for your operation requires careful consideration of the material characteristics, operational environment, and specific requirements of the application. By understanding the unique features and benefits of each conveyor type, businesses can make informed decisions that enhance efficiency, productivity, and safety in their material handling processes.
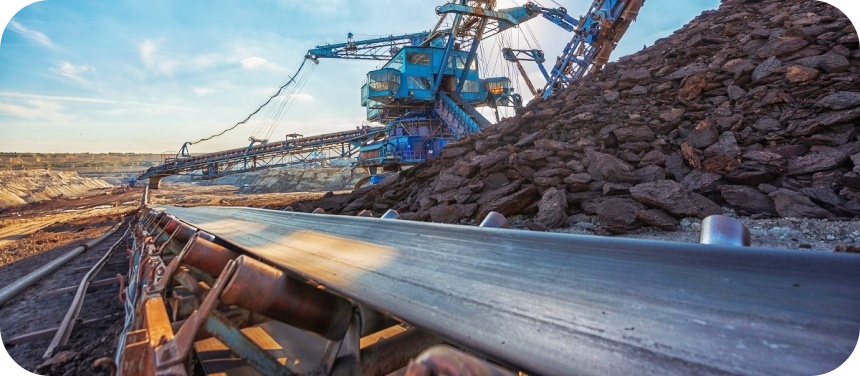
Key Features and Advancements in Bulk Material Belt Conveyors
Belt conveyors for bulk materials pdf have seen significant advancements in technology, enhancing their efficiency, reliability, and versatility. These innovations have made bulk material belt conveyors more effective for a wide range of industries and applications. In this section, we will discuss some of the latest features in conveyor technology, including long-distance covering, high-volume handling, and energy-efficient designs, providing specific examples. Additionally, we will highlight key technological advancements as outlined in sources like CEMA’s 7th edition manual.
Latest Features in Bulk Material Belt Conveyor Technology
Long-Distance Covering
- Description: Modern bulk material belt conveyors are designed to cover long distances, reducing the need for multiple transfer points and minimizing the risk of material spillage and loss.
- Example: A conveyor system used in a mining operation can extend over several kilometers, transporting ore from the extraction site to the processing plant.
High-Volume Handling
- Description: Advances in belt conveyor design now allow for the efficient handling of high volumes of bulk materials, increasing throughput and productivity.
- Example: In agricultural processing, a high-volume bulk material belt conveyor can transport several tons of grain per hour, significantly speeding up the handling process.
Energy-Efficient Designs
- Description: Energy efficiency is a critical focus in modern conveyor technology. Energy-efficient designs reduce operational costs and minimize environmental impact.
- Example: The use of variable frequency drives (VFDs) and energy-efficient motors in bulk material belt conveyors helps to optimize energy consumption, particularly during start-up and when running at partial loads.
Advanced Material Handling
- Description: Technological advancements have led to the development of conveyors capable of handling a wide range of materials, from fine powders to large, abrasive aggregates.
- Example: A bulk material belt conveyor with a specialized belt surface can handle sticky materials, such as wet clay, without clogging or excessive wear.
Automated Control Systems
- Description: Integration of automated control systems enhances the operation and monitoring of bulk material belt conveyors, improving efficiency and reducing the need for manual intervention.
- Example: Conveyor systems equipped with sensors and automated control software can adjust belt speed and tension in real-time, ensuring optimal performance and preventing overloading.
Feature Examples Table
Technological Advancements from CEMA’s 7th Edition Manual
The Conveyor Equipment Manufacturers Association (CEMA) provides comprehensive guidelines and standards for conveyor technology. The 7th edition of the CEMA manual highlights several key advancements in bulk material belt conveyor technology:
Improved Belt Construction
- Advancement: The development of stronger and more durable belt materials enhances the longevity and reliability of conveyors.
- Application: New materials and construction techniques reduce wear and tear, increasing the lifespan of the belt and reducing maintenance costs.
Enhanced Safety Features
- Advancement: The integration of advanced safety features, such as emergency stop buttons, safety guards, and automatic shut-off systems, improves workplace safety.
- Application: These features help prevent accidents and ensure the safe operation of bulk material belt conveyors.
Innovative Drive Technologies
- Advancement: Innovations in drive technology, including the use of direct drives and magnetic drives, increase efficiency and reduce maintenance requirements.
- Application: These technologies provide smoother operation and greater control over conveyor speed and performance.
Advanced Load Handling
- Advancement: The ability to handle diverse load types and sizes with improved accuracy and efficiency.
- Application: Conveyors can now be customized to handle specific materials, from delicate items to heavy, abrasive materials, without compromising performance.
Environmental Control Features
- Advancement: Enhanced environmental control features, such as dust suppression systems and enclosed conveyors, help manage environmental impact.
- Application: These features are crucial for industries where dust control and material containment are critical, such as in chemical and food processing.
The advancements in bulk material belt conveyor technology have revolutionized material handling, making it more efficient, cost-effective, and safe. By incorporating these latest features and adhering to the standards set by CEMA, industries can optimize their material handling processes, ensuring higher productivity and better environmental stewardship.
Choosing the Bulk Material Belt Conveyors for Your Needs
Selecting the appropriate bulk material belt conveyor for your specific needs is crucial to ensuring efficient and cost-effective material handling. There are several factors to consider when choosing a conveyor, including the type of material, the distance to be covered, the volume and weight of the materials, and environmental considerations. This section will provide detailed tips for selecting the right bulk material belt conveyor based on these criteria.
Material Type
The type of material you need to transport plays a significant role in determining the best bulk material belt conveyor for your application. Different materials have unique characteristics that affect how they should be handled. Here are five examples of material types and the appropriate conveyors for each:
Distance to Be Covered
The distance over which materials need to be transported is another critical factor in selecting a bulk material belt conveyor. Different conveyor systems are designed to handle varying lengths efficiently. Here are five examples based on the distance to be covered:
Volume and Weight of Materials
The volume and weight of the materials you need to transport are essential considerations when choosing a bulk material belt conveyor. High-volume and heavy-weight materials require conveyors designed to handle these loads without compromising efficiency or safety. For high-volume applications, conveyors with wide belts and high-speed capabilities are recommended. Heavy-weight materials necessitate conveyors with reinforced belts and robust support structures to prevent sagging and ensure reliable operation.
- High-Volume Materials: For applications involving the transport of large quantities of materials, consider conveyors with wide belts and high-speed capabilities to maximize throughput and efficiency.
- Heavy-Weight Materials: Conveyors designed with reinforced belts, heavy-duty rollers, and sturdy frames are necessary to handle the increased weight and prevent structural issues.
Environmental Considerations
The environment in which the bulk material belt conveyor will operate is another critical factor to consider. Different environments pose various challenges that can affect the conveyor’s performance and longevity. Here are some environmental considerations and corresponding conveyor solutions:
- Dusty Environments: Enclosed conveyors are ideal for preventing dust emissions and maintaining a clean working area. Dust suppression systems can also be integrated to further enhance dust control.
- Corrosive Environments: Conveyors constructed with corrosion-resistant materials, such as stainless steel or coated components, are essential for preventing damage and ensuring durability in corrosive settings.
- Extreme Temperatures: For environments with extreme temperatures, select conveyors designed to operate effectively in high or low-temperature conditions, with features such as heat-resistant belts and insulated components.
- Outdoor Environments: Outdoor conveyors should be built to withstand weather conditions, including rain, wind, and UV exposure. Protective covers and weather-resistant materials are crucial for outdoor installations.
- Hygienic Environments: In industries where hygiene is paramount, such as food processing or pharmaceuticals, conveyors with easy-to-clean designs and materials that meet hygiene standards are necessary to prevent contamination and ensure product safety.
Choosing the right bulk material belt conveyor involves carefully evaluating the type of material, the distance to be covered, the volume and weight of the materials, and environmental considerations. By understanding these factors and selecting a conveyor system that aligns with your specific needs, you can optimize your material handling processes, improve efficiency, and reduce operational costs. Whether you are dealing with fine powders, large aggregates, short distances, or extreme environmental conditions, there is a bulk material belt conveyor designed to meet your requirements and ensure reliable and effective material transportation.
Manufacturers and Retail Options for Bulk Material Belt Conveyors
Selecting the right manufacturer and retailer for bulk material belt conveyors is crucial for ensuring you receive a high-quality product that meets your specific needs. In this section, we will provide an overview of leading manufacturers, offer guidance on finding bulk material belt conveyor suppliers near you, and provide tips on choosing the best manufacturers to ensure product quality.
Overview of Leading Manufacturers and What They Offer
Continental Conveyor
- Overview: Continental Conveyor is a renowned manufacturer specializing in the design and production of high-quality bulk material handling systems, including belt conveyors.
- Offerings: They provide a wide range of conveyor solutions, including standard, heavy-duty, and custom-designed belt conveyors. Their products are known for durability and efficiency, suitable for various industrial applications.
Belt Technologies, Inc.
- Overview: Belt Technologies, Inc. is a leading manufacturer of stainless steel conveyor belts and systems.
- Offerings: They offer custom-engineered solutions tailored to specific industry requirements, with a focus on precision and reliability. Their conveyors are ideal for applications requiring clean, durable, and corrosion-resistant materials.
Flexco
- Overview: Flexco is a global leader in conveyor belt maintenance and manufacturing.
- Offerings: They provide a comprehensive range of belt conveyor products, including conveyor belt fasteners, belt cleaners, and belt tracking solutions. Flexco’s products are designed to enhance conveyor performance and longevity.
Dorner
- Overview: Dorner is a well-known manufacturer specializing in precision conveyor systems.
- Offerings: They offer a variety of bulk material belt conveyors designed for efficiency and flexibility. Dorner’s products include small to medium-sized conveyors suitable for various industries, from manufacturing to food processing.
Martin Engineering
- Overview: Martin Engineering is a leading provider of bulk material handling solutions, including conveyor systems.
- Offerings: They offer innovative conveyor products such as belt cleaners, transfer point solutions, and dust management systems. Martin Engineering focuses on improving efficiency and safety in bulk material handling.
Finding “Bulk Material Belt Conveyor Near Me”
Locating a reliable bulk material belt conveyor supplier near you can ensure quick delivery, better customer support, and the opportunity to visit the manufacturer or retailer if needed. Here are five examples of how to find a supplier near you:
Guidance on Choosing Manufacturers and Ensuring Product Quality
Choosing the right manufacturer for your bulk material belt conveyor is essential to ensure you receive a reliable and high-quality product.
Reputation and Experience:
- Check Reputation: Research the manufacturer’s reputation in the industry. Look for reviews, testimonials, and case studies to gauge customer satisfaction and the quality of their products.
- Experience: Choose manufacturers with extensive experience in producing bulk material belt conveyors. Experienced manufacturers are more likely to offer durable and efficient products.
Product Range and Customization:
- Product Range: Ensure the manufacturer offers a comprehensive range of conveyor products to meet your specific needs. A wide product range indicates the manufacturer’s ability to cater to various applications.
- Customization Options: Look for manufacturers that offer customization options to tailor the conveyor system to your unique requirements. Customization can include specific belt materials, sizes, and features.
Quality Assurance:
- Certifications: Verify if the manufacturer holds relevant certifications, such as ISO 9001, indicating adherence to quality management standards.
- Testing and Inspection: Inquire about the manufacturer’s quality assurance processes, including testing and inspection procedures to ensure product reliability and performance.
Customer Support and Service:
- Technical Support: Choose a manufacturer that provides excellent technical support and after-sales service. Reliable support can help address any issues quickly and ensure the smooth operation of your conveyor system.
- Installation and Maintenance: Check if the manufacturer offers installation and maintenance services. Professional installation and regular maintenance can prolong the lifespan of your conveyor system.
Innovation and Technology:
- Technological Advancements: Opt for manufacturers that invest in research and development to incorporate the latest technological advancements in their products. Innovative features can enhance the efficiency and functionality of your conveyor system.
- Sustainability: Consider manufacturers that prioritize sustainability by offering energy-efficient and environmentally-friendly conveyor solutions.
Selecting the right manufacturer and retailer for your bulk material belt conveyor involves thorough research and careful consideration of various factors. By choosing a reputable manufacturer with a proven track record, a comprehensive product range, and strong customer support, you can ensure that you receive a high-quality conveyor system tailored to your needs. Additionally, leveraging local suppliers can provide benefits such as faster delivery and personalized service, making your bulk material handling processes more efficient and reliable.
Installation and Maintenance of Bulk Material Belt Conveyors
Proper installation and regular maintenance of bulk material belt conveyors are crucial to ensuring their efficient operation and prolonging their lifespan. In this section, we will discuss the best practices for installing bulk material belt conveyors and provide essential maintenance tips to keep your system running smoothly.
Best Practices for Installation of Bulk Material Belt Conveyors
Planning and Preparation:
- Site Assessment: Conduct a thorough site assessment to determine the optimal location for the conveyor. Consider factors such as the flow of materials, space constraints, and accessibility for maintenance.
- Design Review: Review the conveyor design specifications to ensure it meets the operational requirements and site conditions. Confirm that the chosen conveyor type is suitable for the materials being transported.
Foundation and Support Structure:
- Solid Foundation: Ensure that the foundation is solid and level to support the conveyor’s weight and operational loads. Use appropriate materials and construction techniques to prevent settling or shifting.
- Support Structure: Install a robust support structure that aligns with the conveyor design. The structure should provide adequate support and stability, minimizing vibrations and potential misalignments.
Accurate Alignment:
- Alignment Checks: Carefully align the conveyor components, including pulleys, rollers, and the belt, to ensure smooth operation. Misalignment can cause belt tracking issues, increased wear, and reduced efficiency.
- Laser Alignment Tools: Utilize laser alignment tools for precise alignment of the conveyor system. These tools help achieve accurate alignment, reducing the risk of operational problems.
Belt Installation:
- Correct Tension: Install the conveyor belt with the correct tension to prevent slippage and excessive wear. Follow the manufacturer’s guidelines for tensioning procedures.
- Splicing Techniques: Use appropriate splicing techniques to join the belt ends. Proper splicing ensures a strong and reliable connection, minimizing the risk of belt failure.
Safety Measures:
- Safety Guards: Install safety guards and barriers around moving parts to protect workers from accidental contact. Ensure that emergency stop buttons are easily accessible.
- Training: Provide comprehensive training for personnel involved in the installation and operation of the conveyor. Training should cover safety protocols, operational procedures, and emergency response.
Maintenance Tips to Prolong Lifespan and Ensure Efficiency
Regular maintenance is essential to keep bulk material belt conveyors in optimal condition. Here are five maintenance tips to help prolong the lifespan of your conveyor system and ensure efficient operation:
Detailed Maintenance Tips
Regular Inspections:
- Frequency: Conduct regular inspections at scheduled intervals based on the conveyor’s operational demands. Daily visual inspections combined with more thorough monthly checks can help identify issues early.
- Checklist: Use a comprehensive inspection checklist to cover all critical components, including belts, pulleys, rollers, bearings, and support structures. Document findings and address any identified issues promptly.
Lubrication:
- Lubrication Points: Identify all lubrication points on the conveyor system, including bearings, rollers, and drive units. Ensure that each point receives the correct type and amount of lubricant.
- Schedule: Establish a lubrication schedule based on the manufacturer’s recommendations and the conveyor’s operating conditions. Over-lubrication and under-lubrication can both lead to problems, so adherence to the schedule is essential.
Belt Cleaning:
- Cleaning Devices: Install belt cleaning devices, such as scrapers and brushes, to remove material buildup from the belt surface. These devices help maintain a clean belt, reducing wear and preventing tracking issues.
- Regular Cleaning: Perform regular cleaning of the belt and other conveyor components to prevent the accumulation of dirt, dust, and debris. Cleanliness contributes to the efficient operation and longevity of the conveyor system.
Component Replacement:
- Monitoring Wear: Regularly monitor the wear and condition of critical components, such as idlers, pulleys, and the conveyor belt. Use wear indicators where available to assess the extent of wear.
- Timely Replacement: Replace worn or damaged components promptly to avoid causing further damage to other parts of the conveyor system. Timely replacement helps maintain the conveyor’s efficiency and prevents costly downtime.
Monitoring Systems:
- Sensors and Alerts: Implement monitoring systems with sensors to track key performance indicators, such as belt tension, temperature, and speed. Set up alerts to notify maintenance personnel of any deviations from normal operating parameters.
- Data Analysis: Use the data collected from monitoring systems to perform predictive maintenance. Analyze trends and patterns to predict potential issues and schedule maintenance before problems arise.
Proper installation and regular maintenance are essential for ensuring the efficient operation and longevity of bulk material belt conveyors. By following best practices during installation and implementing a comprehensive maintenance program, you can optimize your conveyor system’s performance and minimize downtime. Regular inspections, appropriate lubrication, effective belt cleaning, timely component replacement, and the use of monitoring systems are all critical elements of a successful maintenance strategy. Adhering to these guidelines will help ensure that your bulk material belt conveyor remains reliable and efficient, supporting your material handling needs for years to come.
Get in touch with us for technical specifications and pricing by filling out the inquiry form below.
FAQs About Bulk Material Belt Conveyors
Bulk material handling typically involves the use of several types of conveyors, each designed to efficiently transport various materials. The most common conveyor used for handling bulk material is the bulk material belt conveyor. These conveyors are specifically engineered to transport large quantities of bulk materials, such as ores, grains, coal, sand, and more, over long distances and through complex routes. Belt conveyors are preferred for bulk material handling due to their ability to operate continuously and handle high volumes with minimal manual intervention. Other types of conveyors used include screw conveyors, which are ideal for transporting semi-solid materials, and pneumatic conveyors, which use air to move lightweight, fine materials. Each type of conveyor is selected based on the specific properties of the material being handled, the distance to be covered, and the operational environment.
Bulk material handling refers to the process of managing and transporting large quantities of loose materials in industries such as mining, agriculture, manufacturing, and logistics. It encompasses the entire journey of materials from their point of origin, through storage and processing, to their final destination. This process involves the use of various equipment, including bulk material belt conveyors, hoppers, silos, and stackers, to move materials efficiently and safely. Bulk material handling aims to optimize the flow of materials, reduce handling costs, minimize material loss, and enhance safety. Effective bulk material handling is crucial for maintaining productivity and operational efficiency in industries where large volumes of materials are a part of daily operations.
Conveyor belts are made from a variety of materials, each selected based on the specific requirements of the application. The most common materials used include rubber, PVC (polyvinyl chloride), and fabric. Rubber belts are known for their durability and resistance to abrasion, making them ideal for heavy-duty applications like mining and quarrying. PVC belts are lightweight and resistant to chemicals, making them suitable for food processing and packaging industries. Fabric belts, often made from polyester or nylon, are flexible and offer excellent traction, suitable for light to medium-duty applications. In addition to these materials, conveyor belts can also be reinforced with steel cords or other materials to enhance their strength and longevity, particularly in high-tension applications. The choice of material depends on factors such as the type of material being transported, the environmental conditions, and the specific demands of the application.
Bulk material refers to loose, granular materials that are transported in large quantities without being packaged. These materials are usually homogenous in nature and include items such as sand, gravel, coal, grain, minerals, and powders. Bulk materials are characterized by their ability to flow freely and be moved en masse, typically by means of conveyor systems, hoppers, and other handling equipment. The term “bulk material” signifies that the material is handled in large volumes rather than in discrete units or packages. Effective handling of bulk materials is essential in industries like agriculture, mining, and manufacturing, where the efficient movement and processing of these materials are critical to operations. The ability to transport and manage bulk materials efficiently can significantly impact productivity, cost-effectiveness, and overall operational efficiency.
Last Updated on July 26, 2024 by Jordan Smith
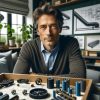
Jordan Smith, a seasoned professional with over 20 years of experience in the conveyor system industry. Jordan’s expertise lies in providing comprehensive solutions for conveyor rollers, belts, and accessories, catering to a wide range of industrial needs. From initial design and configuration to installation and meticulous troubleshooting, Jordan is adept at handling all aspects of conveyor system management. Whether you’re looking to upgrade your production line with efficient conveyor belts, require custom conveyor rollers for specific operations, or need expert advice on selecting the right conveyor accessories for your facility, Jordan is your reliable consultant. For any inquiries or assistance with conveyor system optimization, Jordan is available to share his wealth of knowledge and experience. Feel free to reach out at any time for professional guidance on all matters related to conveyor rollers, belts, and accessories.