The Versatility of Carbon Steel Roller
Carbon steel roller stands as the backbone of numerous industrial processes, embodying a blend of durability, efficiency, and versatility that few materials can match. These rollers, crafted from high-grade carbon steel, are pivotal in manufacturing, agriculture, mining, and beyond, offering unparalleled support in conveyor systems and material handling operations. The significance of carbon steel roller extends beyond their functional utility; they represent a critical investment in the operational efficiency and longevity of industrial machinery. Carbon steel rollers offer durability, efficiency, and superior wear resistance, for heavy-duty industrial and smooth material conveyance. This blog post aims to delve into the myriad benefits and applications of carbon steel roller, shedding light on why they are a preferred choice in various sectors. We will also navigate through the essential considerations one must weigh before selecting these rollers, ensuring that readers are well-equipped with the knowledge to make informed decisions. By exploring the multifaceted advantages and diverse applications, this post seeks to underscore the pivotal role of carbon steel roller in enhancing industrial productivity and innovation.
What Is Carbon Steel Roller
Carbon steel rollers, integral to the functionality of conveyor systems and bulk material handling equipment, are manufactured from carbon steel, a compound known for its robustness and versatility. The composition and construction of carbon steel roller encompass several critical attributes:
- High Carbon Content: The primary distinction of carbon steel is its high carbon content, which imparts the material with superior strength and hardness, making it ideal for the demanding environments of industrial applications.
- Manufacturing Techniques: These rollers are produced through either hot rolling or cold rolling processes. Hot rolling is performed at temperatures above the steel’s recrystallization level, while cold rolling is done at room temperature, affecting the steel’s strength and surface qualities.
- Surface Finishing: Carbon steel rollers may undergo various surface treatments, such as chrome plating or powder coating, to enhance corrosion resistance and extend their operational life.
- Customization Flexibility: They can be customized in terms of size, diameter, wall thickness, and length to meet the specific requirements of different conveyor systems.
- Enhanced Load-Bearing Capacity: The structural integrity of carbon steel allows these rollers to support heavier loads compared to rollers made from other materials, making them suitable for a wide range of industrial tasks.
- Low Maintenance: The durability of carbon steel minimizes the need for frequent maintenance, thereby reducing downtime and operational costs.
- Economic Efficiency: Carbon steel is readily available and easier to process, making rollers manufactured from this material more cost-effective than those made from alternative materials.
- Adaptability: With appropriate surface treatments, carbon steel rollers are capable of withstanding harsh environmental conditions, including exposure to chemicals, moisture, and extreme temperatures.
Comparison with Other Materials
The advantages of carbon steel roller become evident when directly compared with rollers made from rolled steel and cold rolled steel. Below is an expanded comparison to highlight these differences:
- Rolled Steel vs. Carbon Steel: While “rolled steel” is a general term that refers to steel processed through rolling to achieve various shapes and sizes, “carbon steel” specifies the steel’s composition that includes a significant amount of carbon, enhancing its mechanical properties. Carbon steel rollers, therefore, benefit from the inherent strength and durability provided by the higher carbon content, making them more resilient under heavy loads and wear conditions.
- Carbon Steel vs. Cold Rolled Steel: Cold rolled steel is distinguished by its manufacturing process, which involves rolling the steel at room temperature to achieve tighter tolerances and a smoother surface finish. Although cold rolled steel can be used to make rollers, carbon steel rollers manufactured through cold rolling benefit from the combined advantages of the material’s inherent strength and the enhanced surface finish and dimensional accuracy provided by the cold rolling process.
Here’s a detailed comparison table:
Carbon steel rollers, with their robust construction and adaptable design, stand out as the preferred choice for industrial applications requiring durability, efficiency, and cost-effectiveness. Their ability to be tailored for specific operational needs further enhances their appeal, solidifying their position as a cornerstone in the realm of material handling and conveyor systems.
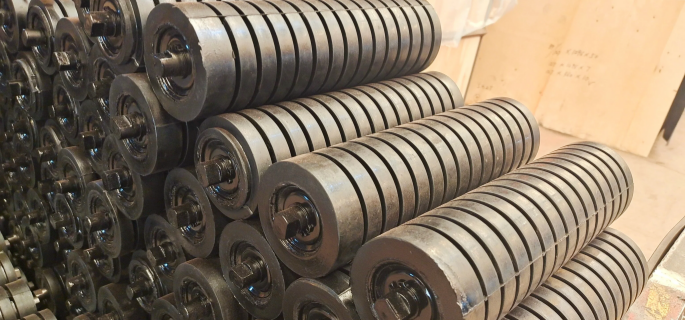
Carbon Steel Roller Dimensions
1. Diameter
- Small Diameter Rollers (20 mm – 100 mm):
- Typically used in applications requiring high precision, such as in conveyors for electronics or small packaging.
- For example, a 20 mm diameter roller might be used in lightweight conveyor systems or small-scale industrial machinery.
- Medium Diameter Rollers (100 mm – 300 mm):
- Common in a wide range of industrial applications including food processing, material handling, and manufacturing.
- A 200 mm diameter roller is often used in medium-duty conveyors or machinery where balance between load capacity and space constraints is important.
- Large Diameter Rollers (300 mm – 500 mm+):
- Used in heavy-duty applications such as mining, steel processing, or large-scale manufacturing.
- A 450 mm diameter roller might be part of a heavy-duty conveyor system handling large, bulky materials such as ores or steel beams.
2. Length
- Short Rollers (100 mm – 500 mm):
- Used in compact machinery or applications where space is limited. A 150 mm long roller might be used in small conveyor systems or assembly lines.
- Medium-Length Rollers (500 mm – 1500 mm):
- Common in standard conveyor systems, often found in packaging, food processing, and automotive assembly lines.
- A 1000 mm long roller could be part of a conveyor system in an automobile manufacturing plant, supporting and moving components along the assembly line.
- Long Rollers (1500 mm – 3000 mm+):
- These are used in large industrial systems where extended length is necessary to cover broader areas.
- For instance, a 2500 mm long roller might be used in large-scale material handling systems, such as those found in shipping or logistics centers.
3. Wall Thickness
- Thin-Wall Rollers (2 mm – 5 mm):
- Suitable for light-duty applications where load-bearing requirements are minimal. Thin walls are often found in rollers used in packaging or light material transport.
- Medium-Wall Rollers (5 mm – 10 mm):
- Used in a variety of industrial applications, balancing strength with weight. A 7 mm wall thickness might be found in rollers used in medium-duty conveyors handling items like boxed goods or smaller parts.
- Thick-Wall Rollers (10 mm – 20 mm):
- Designed for heavy-duty applications where significant strength is required. Thick-walled rollers are common in industries such as mining or metal processing.
- A 15 mm thick wall would be typical for rollers transporting heavy raw materials or in environments where durability and resistance to impact are crucial.
4. Surface Finish
- Smooth Finish:
- Ideal for applications where minimal friction is desired, such as in high-speed conveyors or precision machinery.
- Smooth rollers are often used in food processing or pharmaceutical industries where easy cleaning and hygiene are important.
- Textured Finish:
- Used in applications where greater traction is required. A textured surface helps grip materials, preventing slipping during transport.
- Rollers with a knurled or patterned surface might be used in systems handling items with slick surfaces, such as glass or polished metal.
5. Bore Diameter
- Small Bore Diameter (10 mm – 50 mm):
- Used in smaller rollers designed for light-duty applications. A 15 mm bore might be used in rollers for small conveyor systems or light industrial equipment.
- Medium Bore Diameter (50 mm – 100 mm):
- Common in medium-duty applications, balancing strength with flexibility. A 75 mm bore could be used in rollers for general industrial applications.
- Large Bore Diameter (100 mm – 200 mm+):
- Found in heavy-duty rollers, these bores are designed to accommodate larger, stronger shafts for handling significant loads.
- A 150 mm bore would be typical in rollers used in large conveyor systems or machinery designed for moving heavy industrial materials.
6. Concentricity and Tolerance
- High Precision (±0.01 mm – ±0.05 mm):
- Essential in applications requiring exact alignment and smooth operation, such as in precision machinery or high-speed conveyors.
- Rollers used in the electronics industry, for example, often need tight tolerances to ensure smooth and accurate transport of delicate components.
- Standard Precision (±0.05 mm – ±0.1 mm):
- Adequate for general industrial applications where some degree of tolerance is acceptable.
- Rollers with this level of precision might be used in standard conveyors or manufacturing systems where slight deviations won’t impact overall performance.
- Low Precision (±0.1 mm – ±0.5 mm):
- Suitable for heavy-duty applications where slight variations are permissible. This tolerance range is often found in rollers used in rugged environments, such as mining or heavy manufacturing.
- For instance, a roller with a ±0.3 mm tolerance might be used in a mining conveyor system where robustness is more critical than precision.
7. Weight
- Light Rollers (0.5 kg – 5 kg):
- Used in applications where ease of movement and low inertia are important, such as in packaging or light material handling.
- A roller weighing 2 kg might be found in small conveyor systems used in warehouses or light manufacturing.
- Medium Weight Rollers (5 kg – 50 kg):
- Common in a variety of industrial settings, balancing load capacity with manageability.
- A 20 kg roller could be used in a medium-duty conveyor system in an automotive plant or general manufacturing.
- Heavy Rollers (50 kg – 500 kg+):
- Designed for heavy-duty applications where significant strength and durability are required. These rollers are used in industries like mining, steel production, or large-scale manufacturing.
- A 200 kg roller might be part of a large conveyor system moving bulk materials or heavy industrial components.
8. End Configuration
- Flat Ends:
- Common in standard conveyor applications where the roller simply supports the load and does not require special features for guiding or positioning.
- Crowned Ends:
- Used to help center the belt or material on the roller, preventing it from drifting to one side. Crowned rollers are essential in systems where maintaining alignment is critical.
- Tapered Ends:
- Typically used in curved conveyors or systems where the material needs to change direction smoothly. The tapered design allows for smooth transitions in material handling.
These details should provide a comprehensive understanding of the various dimensions and specifications of carbon steel rollers, tailored to different industrial applications. Customization is common, so specific dimensions may vary based on the exact needs of the machinery or system in which the rollers are used.
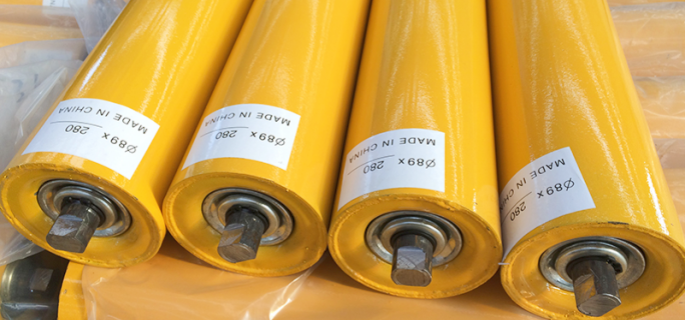
Advantages of Carbon Steel Roller
The carbon steel roller is a cornerstone in the realm of industrial machinery and conveyor systems, offering a suite of benefits that underscore its indispensability. Here are nine key advantages that highlight the superiority of carbon steel roller:
Durability and Strength: The inherent durability and strength of carbon steel roller are significantly enhanced through carburizing and heat-treating processes. These treatments infuse the outer layer of the steel with additional carbon, creating a hard, wear-resistant surface while maintaining a tough, ductile core. This dual nature ensures that carbon steel rollers can withstand high stress and impact without deformation, extending their operational lifespan even in the most demanding environments.
Efficiency and Cost-Effectiveness: Carbon steel rollers are designed to minimize friction and maximize load-bearing capacity, which translates to lower energy consumption and reduced operational costs. The smooth surface and precise manufacturing of these rollers ensure efficient material handling, reducing the power required to move goods and thus lowering energy bills. Additionally, their long service life and minimal maintenance requirements make them a cost-effective solution over time.
Versatility in Applications: The versatility of carbon steel roller is unmatched, finding utility across a broad spectrum of industries such as manufacturing, agriculture, mining, and more. Their robust construction makes them suitable for heavy-duty applications, from moving raw materials in mining operations to processing goods in manufacturing plants. This adaptability ensures that businesses in various sectors can rely on carbon steel roller for their conveyor needs.
Corrosion Resistance: With appropriate coatings or treatments, such as galvanizing or chrome plating, carbon steel rollers can resist corrosion caused by exposure to moisture, chemicals, and other corrosive elements. This resistance is crucial for applications in harsh environments, ensuring longevity and reliability.
High Load Capacity: Carbon steel’s high strength-to-weight ratio allows rollers made from this material to support heavier loads than those made from other materials. This capability is essential for industries that move large volumes of goods or heavy materials, ensuring that the conveyor system can handle the required capacity without failure.
Low Maintenance: The durability and strength of carbon steel roller result in a product that requires less maintenance. Their ability to resist wear and deformation means that replacements and repairs are less frequent, saving time and money on maintenance operations.
Temperature Tolerance: Carbon steel rollers can operate effectively in a wide range of temperatures, making them suitable for industries with high-temperature processes or those located in extreme climates. This temperature tolerance ensures consistent performance regardless of environmental conditions.
Customization: Carbon steel roller can be customized to meet specific application requirements, including size, shape, and surface treatment. This flexibility allows for optimized conveyor systems that are tailored to the unique needs of each operation.
Environmental Sustainability: Finally, carbon steel is a recyclable material, making carbon steel rollers an environmentally sustainable choice for businesses looking to minimize their ecological footprint. The ability to recycle and repurpose these rollers at the end of their life cycle contributes to a more sustainable industrial practice.
The advantages of carbon steel roller extend from their physical and mechanical properties to their operational efficiency and environmental sustainability. These benefits make them an essential component in a wide array of industrial applications, offering reliability, versatility, and cost-effectiveness that are hard to match.
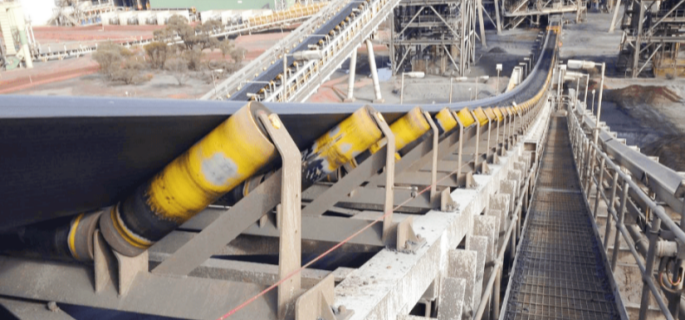
V-groove Carbon Steel Roller
A V-groove Carbon Steel Roller is a specialized type of roller commonly used in various industrial applications for guiding and supporting loads that need to move along a defined path. These rollers are named for the V-shaped groove machined into their circumference, which allows them to run smoothly along a matching V-shaped track or guide.
Design and Structure
- V-Groove: The defining feature of these rollers is the V-shaped groove that runs around their outer edge. The angle of the V-groove can vary, but it is generally designed to match the angle of the track it runs on, ensuring smooth and stable motion.
- Roller Body: The main body of the roller is usually cylindrical, with the V-groove cut into its surface. The roller can either be a solid piece or include a bore to accommodate a shaft or axle.
- Bearings: Many V-groove rollers are fitted with internal bearings to reduce friction and ensure smooth rotation. The bearings are usually sealed to protect them from dust and debris, which is important in industrial environments.
- Surface Finishing: The surface of the carbon steel roller may be treated with a protective coating, such as zinc plating or black oxide, to enhance corrosion resistance, especially if the roller is used in environments where it is exposed to moisture or chemicals.
Applications
V-groove carbon steel rollers are used in a variety of industrial settings, including:
- Material Handling: These rollers are commonly used in conveyor systems and material handling equipment, where they guide and support the movement of loads along a specific path.
- Sliding Gates and Doors: V-groove rollers are often employed in the tracks of sliding gates, doors, and windows, providing smooth and reliable movement along the guide rail.
- Automated Systems: In automated manufacturing processes, V-groove rollers help in the precise movement of components along an assembly line.
- Rail Systems: These rollers are also used in rail systems where loads need to be guided along a defined track, such as in warehouse logistics or overhead transport systems.
Advantages
- Precision Movement: The V-groove design ensures that the roller stays on track, allowing for accurate and stable movement along a defined path.
- Durability: Carbon steel’s toughness and wear resistance make these rollers suitable for applications involving heavy loads and continuous operation.
- Cost-Effective: Compared to other materials, carbon steel offers a good balance of performance and cost, making it a popular choice in industrial applications.
- Versatility: V-groove rollers can be used in a wide range of applications, from simple sliding doors to complex automated systems.
Limitations
- Corrosion Susceptibility: Although carbon steel is strong and durable, it can corrode if exposed to moisture or harsh chemicals. Protective coatings can mitigate this, but in highly corrosive environments, alternative materials like stainless steel might be preferred.
- Load Capacity: While carbon steel rollers are strong, the load capacity depends on the size and design of the roller, including the type of bearings used.
In summary, V-groove carbon steel rollers are essential components in many industrial systems, offering reliable, precise movement along defined paths. Their strength, durability, and cost-effectiveness make them a popular choice for a wide range of applications.
Find the perfect conveyor roller for your needs. Inquire here!
To Select the Best Carbon Steel Roller
Choosing the right carbon steel roller for your conveyor system is crucial for ensuring efficiency, durability, and cost-effectiveness. Here are key factors and considerations to guide you in selecting the best carbon steel roller for your needs.
Factors to Consider
When embarking on the selection process for the ideal carbon steel roller for your conveyor system, it’s imperative to approach the decision with a comprehensive understanding of the various factors that will influence both performance and longevity. The choice of a carbon steel roller is not merely about finding a component that fits; it’s about ensuring that every aspect of the roller aligns with the specific demands and operational conditions of your system. Here are several critical factors to consider that will guide you in making an informed selection, ensuring that the carbon steel roller you choose not only meets but exceeds your expectations:
- Material Quality: High-quality carbon steel ensures strength and durability. Look for rollers made from certified steel grades known for their performance in industrial applications.
- Bearing Options: Bearings are critical for smooth operation. Consider sealed and lubricated bearings for reduced maintenance, and choose between ball bearings and roller bearings based on load requirements.
- Surface Finish: A smooth finish reduces material wear and noise. Options like galvanizing or coating with polymers can also enhance corrosion resistance.
- Load Capacity: Ensure the roller can handle the maximum load of your application. This depends on both the material quality and the roller design.
- Environmental Resistance: For operations exposed to harsh conditions, consider rollers with additional corrosion protection or temperature resistance.
- Maintenance Requirements: Look for rollers designed for easy maintenance or those that offer low-maintenance solutions through their construction and material choice.
- Operational Speed: The roller’s design should accommodate the operational speed of your conveyor system without compromising efficiency or lifespan.
- Compatibility: Ensure the rollers are compatible with your conveyor system’s design, including frame and track alignment.
- Cost vs. Value: While initial cost is a consideration, focus on the total value offered by the roller, including lifespan, maintenance savings, and operational efficiency.
Customization and Specifications
Selecting the right specifications for carbon steel roller is essential for optimizing your conveyor system’s performance:
- Diameter: Match the roller diameter to the size and weight of the materials being conveyed.
- Wall Thickness: Thicker walls increase strength and load capacity but may require more power to move.
- Shaft Options: Choose the right shaft size and material to ensure durability and compatibility with the conveyor system.
- Length: The roller length should be appropriate for the width of the materials to prevent overhang and ensure balanced support.
- Bearing Type: Select bearings that suit the load and speed requirements of your application.
- Surface Treatment: Consider treatments that enhance wear resistance and reduce maintenance needs.
- Custom Features: Features like grooves or coatings can be customized to suit specific operational needs.
- Quality Assurance: Opt for rollers from manufacturers that offer warranties and quality certifications.
Is Carbon Roller Good?
Evaluating the suitability of carbon steel roller for your conveyor system involves a nuanced understanding of their capabilities and how they align with your operational demands. Carbon steel rollers are not just a component; they are a critical investment in the efficiency and longevity of your material handling processes. Let’s explore their merits and applicability in greater detail, focusing on aspects that distinguish them from other materials without reiterating previously mentioned points.
Enhanced Performance in Diverse Environments
Carbon steel rollers are engineered to excel across a broad spectrum of environments. Their robust construction enables them to operate seamlessly under substantial load capacities, which is crucial for industries that deal with heavy or bulky materials. The resilience of carbon steel to environmental stressors such as impact, abrasion, and fluctuating temperatures ensures that these rollers maintain optimal performance levels, minimizing downtime and enhancing productivity.
Longevity and Maintenance
The longevity of carbon steel rollers is a testament to their construction and material properties. Unlike other materials that may require frequent replacements or are prone to rapid wear, carbon steel offers a durable solution that stands the test of time. This durability translates into lower lifecycle costs, as the need for replacements and the associated downtime are significantly reduced. Moreover, advancements in manufacturing techniques have led to carbon steel rollers that are easier to maintain, further reducing the total cost of ownership.
Customization for Precision Applications
One of the standout features of carbon steel roller is their adaptability to customization. This allows for precision engineering to meet the exact requirements of your conveyor system, ensuring that each roller contributes to the overall efficiency and effectiveness of material handling. Whether it’s specific dimensions, surface treatments, or bearing configurations, carbon steel rollers can be tailored to provide the best fit for your operations, enhancing system performance and reliability.
Economic and Environmental Sustainability
In addition to their operational advantages, carbon steel rollers are also an economically and environmentally sustainable choice. The material’s abundance and recyclability mean that it supports a circular economy, reducing waste and promoting the reuse of resources. This aspect is increasingly important in a global context that prioritizes sustainable practices and environmental stewardship.
Assessing Suitability for Your Operations
The decision to choose carbon steel rollers should be based on a comprehensive assessment of your operational needs, including load requirements, environmental conditions, and maintenance practices. While carbon steel rollers offer numerous advantages, ensuring that they align with the specific demands of your application is crucial for maximizing their benefits.
Carbon steel rollers represent a versatile, durable, and cost-effective solution for a wide range of conveyor system applications. Their ability to perform reliably in diverse conditions, combined with the potential for customization and their contribution to sustainability, makes them a compelling choice for businesses looking to optimize their material handling processes. When evaluating whether carbon steel rollers are a good fit for your operations, consider these unique attributes and how they can enhance the efficiency and longevity of your conveyor system.
Maintenance and Longevity of Carbon Steel Roller
The maintenance and longevity of carbon steel roller are critical aspects that significantly influence the efficiency and cost-effectiveness of conveyor systems. Proper care, routine maintenance, and understanding the lifecycle costs associated with these rollers can greatly extend their service life while ensuring they continue to operate at peak performance. This section delves into essential maintenance tips and a comprehensive analysis of the lifecycle costs, providing a blueprint for maximizing the value of carbon steel roller in industrial applications.
Care and Maintenance Tips
Ensuring the durability and operational efficiency of carbon steel roller requires a proactive approach to maintenance. Here are detailed strategies designed to extend the life of these vital components:
- Regular Inspection: Implement a schedule for periodic inspections to identify and address wear, corrosion, or damage before they escalate.
- Lubrication: Adequate lubrication of bearings and moving parts is essential to minimize friction, one of the primary causes of wear.
- Cleaning: Keeping the rollers clean prevents the accumulation of debris that can lead to imbalance or increased wear over time.
- Alignment Checks: Regularly checking and correcting the alignment of rollers within the conveyor system ensures even distribution of loads and reduces wear.
- Load Monitoring: Adhering to the recommended load capacities prevents overloading, which can lead to premature roller failure.
- Environmental Protection: Use protective coatings and covers to shield the rollers from harmful substances and extreme weather conditions.
- Replacement of Worn Parts: Replacing worn components, such as bearings or seals, in a timely manner maintains the roller’s efficiency and prevents further damage.
- Use of Compatible Materials: Ensure compatibility of all parts and components with the carbon steel rollers to avoid adverse reactions or increased wear.
- Professional Servicing: Engaging professionals for maintenance checks and services guarantees that the rollers are maintained at industry standards.
Lifecycle Costs
Understanding the lifecycle costs of carbon steel rollers is crucial for effective budgeting and operational planning. Here’s an in-depth look at the financial considerations over the lifespan of these rollers:
- Initial Investment: The upfront cost is a consideration, but the long-term benefits of durability and efficiency often outweigh initial expenses.
- Reduced Downtime: Minimizing downtime through regular maintenance not only saves on direct repair costs but also avoids production losses.
- Maintenance Expenses: While ongoing maintenance incurs costs, a well-planned approach can significantly reduce unexpected repair expenses and extend the roller’s service life.
- Energy Efficiency: Efficient operation of well-maintained rollers leads to lower energy consumption, contributing to operational cost savings.
- Replacement Frequency: The extended lifespan of carbon steel roller, thanks to their robust construction, reduces the need for frequent replacements.
- Resale Value: High-quality materials and construction mean carbon steel rollers can retain value, offering potential resale opportunities.
- Recyclability: The ability to recycle carbon steel roller at the end of their life cycle offers an environmentally friendly disposal option and potential cost recovery.
- Total Cost of Ownership: Considering all factors, including maintenance, energy efficiency, and replacement intervals, carbon steel rollers often present a favorable total cost of ownership.
By adhering to the outlined maintenance strategies and understanding the comprehensive lifecycle costs, businesses can ensure their carbon steel rollers remain a valuable and efficient part of their conveyor systems for years to come. This proactive approach not only enhances operational efficiency but also contributes to the overall sustainability of industrial operations.
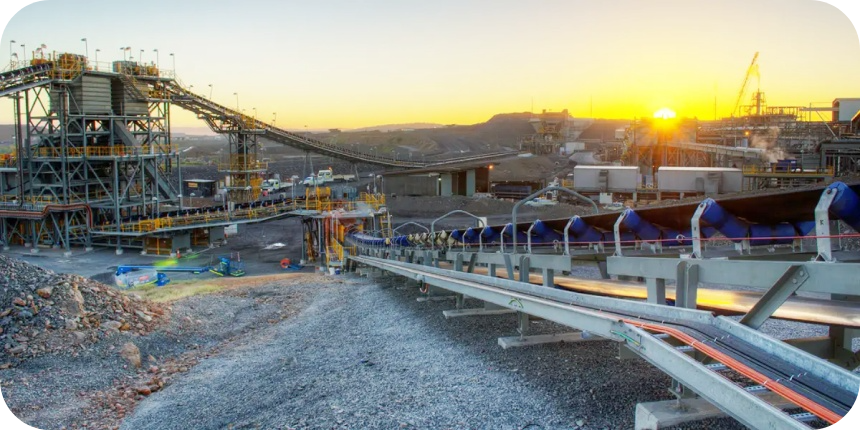
Carbon Steel Roller Chains
Carbon Steel Roller Chains are a type of mechanical component used primarily in power transmission applications. These chains are known for their strength, durability, and ability to withstand high levels of stress and wear. Here’s a detailed description:
Material Composition
Carbon steel is the primary material used in these roller chains. This type of steel typically contains a small percentage of carbon, which enhances the material’s strength and wear resistance without compromising its ductility. The exact carbon content can vary, but it usually ranges from 0.05% to 1.0%, depending on the desired properties of the chain.
Design and Structure
A typical carbon steel roller chain consists of a series of interconnected links. Each link is made up of:
- Inner and Outer Plates: The plates form the sides of each link and are punched or cut from carbon steel sheets.
- Rollers: Cylindrical components located between the inner and outer plates, the rollers reduce friction as the chain engages with the sprocket teeth.
- Pins: These are the axles that hold the inner and outer plates together. The pins are often heat-treated to improve hardness and wear resistance.
- Bushings: Situated between the rollers and pins, bushings allow the rollers to rotate freely while reducing friction and wear.
Types and Variants
Carbon steel roller chains come in various types, including:
- Single Strand Chains: Comprising one row of roller links, these are the most common and are used in straightforward power transmission applications.
- Multi-Strand Chains: These have two or more parallel strands of roller links, providing higher load capacities and strength, suitable for heavy-duty applications.
- Attachment Chains: These chains have extended pins or additional plates for attachments, making them versatile for specialized applications like conveyors.
Applications
Carbon steel roller chains are widely used across different industries, including:
- Manufacturing: Used in machinery for conveying, lifting, and driving components.
- Agriculture: Found in equipment such as tractors, harvesters, and other farm machinery.
- Automotive: Utilized in engine timing systems, transmission, and various mechanical functions.
- Construction: Applied in heavy machinery like bulldozers, cranes, and loaders.
Advantages
- Strength and Durability: Carbon steel roller chains are known for their high tensile strength, making them ideal for heavy loads.
- Cost-Effective: Compared to alloy steels and stainless steels, carbon steel is more economical while still offering excellent performance.
- Wide Availability: These chains are widely available in various sizes and configurations, making them accessible for many applications.
Maintenance
While carbon steel roller chains are durable, regular maintenance is essential to ensure longevity. This includes lubrication, cleaning to remove debris, and periodic inspection for signs of wear or damage. Proper maintenance can significantly extend the chain’s service life and improve operational efficiency.
Corrosion Resistance
Carbon steel, while strong, is susceptible to corrosion, especially in harsh environments. To mitigate this, chains may be coated with zinc, nickel, or other protective finishes, or they may be used in applications where they are not exposed to moisture or corrosive substances.
Carbon steel roller chains are robust, versatile components essential for a wide range of mechanical systems, providing reliable power transmission and movement in numerous industrial applications.
Where to Find the Best Carbon Steel Rollers for Sale
Identifying the right supplier for carbon steel rollers is crucial for ensuring that you receive high-quality components that meet your specific needs. This section provides guidance on choosing a reputable supplier and highlights some of the top-rated carbon steel rollers available in the market.
Choosing a Supplier
When it comes to selecting a supplier for carbon steel rollers, several key factors should be considered to ensure you partner with a company that can meet your requirements effectively:
- Industry Reputation: Look for suppliers with a strong reputation in the industry, evidenced by positive reviews and testimonials from other businesses.
- Quality Assurance: Ensure the supplier adheres to strict quality control standards and offers products that meet or exceed industry specifications.
- Customization Capabilities: Choose a supplier that can provide customized solutions tailored to your specific operational needs.
- Material Sourcing: Investigate the source of their materials to ensure the carbon steel used is of high quality and durability.
- Technical Support: A reputable supplier should offer comprehensive technical support, including assistance with selection, installation, and maintenance.
- Delivery and Lead Times: Consider the supplier’s ability to meet your timeline requirements, including their policies on delivery times and expedited orders.
- After-Sales Service: Look for suppliers that provide excellent after-sales service, including warranty coverage and easy access to replacement parts.
- Cost-Effectiveness: While quality should not be compromised for cost, it’s important to evaluate the overall value offered by the supplier, considering both price and service.
- Sustainability Practices: Prefer suppliers committed to sustainable practices, including the use of recyclable materials and eco-friendly manufacturing processes.
Product Highlights
Several carbon steel rollers stand out in the market for their exceptional quality, durability, and performance. Here are a few top-rated options, along with their key features and benefits:
- High-Load Capacity Rollers: Designed for heavy-duty applications, these rollers can support substantial loads without deformation, ensuring smooth operations in demanding environments.
- Precision Engineered Rollers: Offering tight tolerances and smooth surfaces, these rollers are ideal for applications requiring high precision and minimal vibration.
- Corrosion-Resistant Rollers: With special coatings or treatments, these rollers are protected against corrosion, making them suitable for use in harsh or wet environments.
- Temperature-Resistant Rollers: Capable of operating efficiently in extreme temperatures, these rollers are perfect for industries with high-heat processes.
- Low-Maintenance Rollers: Featuring sealed bearings and durable construction, these rollers require minimal maintenance, reducing operational costs.
- Eco-Friendly Rollers: Made from recyclable materials and manufactured through environmentally friendly processes, these rollers appeal to sustainability-conscious businesses.
- Customizable Rollers: Suppliers offer rollers that can be customized in terms of size, material, and surface treatment to meet specific application requirements.
- High-Speed Rollers: Engineered for high-speed conveyor systems, these rollers ensure efficient material handling with minimal noise and wear.
Finding the best carbon steel roller for sale involves careful consideration of both the supplier’s capabilities and the specific features of the rollers themselves. By focusing on quality, customization options, and customer service, you can select a supplier that will provide rollers to enhance the efficiency and reliability of your conveyor system. Highlighting top-rated products further assists in identifying rollers that offer the best performance and value for your operations.
FAQs about Carbon Steel Roller
Rollers are typically manufactured from two main types of steel: carbon steel and stainless steel. Carbon steel rollers are known for their strength and durability, making them suitable for heavy-duty applications. This type of steel is an alloy that contains varying amounts of carbon, which enhances its hardness and wear resistance. Carbon steel rollers can handle high load capacities and are often used in industries requiring robust material handling solutions.
Stainless steel rollers, on the other hand, are valued for their exceptional corrosion resistance. Made from an alloy that includes iron, carbon, and a minimum of 10.5% chromium, stainless steel forms a protective layer of chromium oxide on the surface that prevents rust and corrosion. This makes stainless steel rollers ideal for use in environments that are moist or where exposure to chemicals is common, such as in the food processing or chemical manufacturing industries. Stainless steel is also chosen for applications where sanitation is crucial, thanks to its easy-to-clean surface that resists bacterial growth.
A stainless steel roller is a component used in conveyor systems and machinery, crafted from stainless steel alloy for its notable corrosion resistance and durability. These rollers are especially beneficial in environments where exposure to moisture, chemicals, or other corrosive elements is frequent. Stainless steel’s resistance to rust and corrosion ensures the longevity and reliability of the rollers, making them a preferred choice for many industrial applications.
Stainless steel rollers are not only durable but also hygienic, with a smooth surface that’s easy to clean and disinfect. This makes them particularly suitable for industries where cleanliness is paramount, such as food and beverage processing, pharmaceuticals, and healthcare. The choice of stainless steel grade (e.g., 304 or 316) can be tailored to the specific needs of the application, with higher grades offering enhanced corrosion resistance. Overall, stainless steel rollers offer a combination of durability, hygiene, and performance, making them an excellent choice for a wide range of conveyor system applications.
Yes, carbon steel can be rolled. Rolling is a common process used in the steel industry to shape and form carbon steel into sheets, bars, or other profiles. It can be done either hot or cold, depending on the desired properties of the final product.
The best steel for rollers typically depends on the application. High-carbon steel or alloy steels like 52100 bearing steel are often used for rollers due to their high hardness, wear resistance, and durability. For heavy-duty applications, tool steels such as D2 or even stainless steels may be preferred.
Carbon steel can scratch more easily compared to stainless steel, especially if it has a softer temper or if it’s exposed to abrasive materials. However, its scratch resistance can be improved through heat treatment or by adding protective coatings.
Yes, carbon steel trowels are highly regarded, especially in construction and masonry work. They are known for their durability, strength, and the ability to hold a sharp edge, which is essential for precise work. However, they may require regular maintenance to prevent rusting.
Last Updated on August 9, 2024 by Jordan Smith
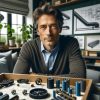
Jordan Smith, a seasoned professional with over 20 years of experience in the conveyor system industry. Jordan’s expertise lies in providing comprehensive solutions for conveyor rollers, belts, and accessories, catering to a wide range of industrial needs. From initial design and configuration to installation and meticulous troubleshooting, Jordan is adept at handling all aspects of conveyor system management. Whether you’re looking to upgrade your production line with efficient conveyor belts, require custom conveyor rollers for specific operations, or need expert advice on selecting the right conveyor accessories for your facility, Jordan is your reliable consultant. For any inquiries or assistance with conveyor system optimization, Jordan is available to share his wealth of knowledge and experience. Feel free to reach out at any time for professional guidance on all matters related to conveyor rollers, belts, and accessories.