Carrier Roller Conveyor: Efficiency Redefined
Carrier roller conveyors are specialized systems designed to facilitate the movement of goods across a range of industrial environments. Characterized by rollers mounted within a durable frame, these conveyors are instrumental in sectors such as manufacturing and logistics, efficiently handling everything from lightweight packages to heavy pallets. The versatility and reliability of carrier roller conveyor make them a vital component in streamlining operations and enhancing productivity in workplaces where quick and effective material handling is crucial.
How Do Carrier Roller Conveyor Works
Carrier roller conveyors utilize a series of rollers to move materials efficiently across their surface. Here’s a more detailed breakdown of their mechanics:
- Roller Composition: Constructed from materials like steel or heavy-duty plastic, these rollers ensure durability and smooth movement of goods.
- Frame Structure: Provides stability and support, crafted to withstand varying weights and volumes of cargo.
- Drive System: Can be powered by motors or manual effort, depending on the design and requirement.
- Load Handling: Designed to accommodate a range of loads, from lightweight items to heavy industrial products, adjusting to the necessary weight specifications.
- Speed Control: Features mechanisms for adjusting conveyor speed to match the pace of production or packing processes.
- Integration Capability: Compatible with various manufacturing systems, enhancing overall operational coherence.
- Energy Efficiency: Engineered to optimize energy consumption, reducing operational costs over time.
- Safety Features: Includes safeguards like emergency stops and protective barriers to prevent accidents.
- Maintenance Access: Strategically designed for easy access to facilitate regular maintenance and minimize downtime.
Detailed Comparison with Other Types of Conveyors
This expanded comparison and detailed points explain how carrier roller conveyors work, demonstrating their advantages over other conveyor types in various industrial settings.
Types of Carrier Roller Conveyor
Carrier roller conveyors are designed to cater to various operational requirements across industries. Here’s an expanded description of their types and operational suitability:
Gravity Roller Conveyors:
- Mechanism: Utilizes the natural force of gravity to facilitate movement, with rollers set at a slight decline.
- Suitability: Best for light to medium-weight products in a low-speed environment, such as warehouses or assembly lines where cost reduction is essential.
Powered Roller Conveyors:
- Mechanism: Features motors integrated into the roller assemblies to drive the belts, enhancing control over movement.
- Suitability: Ideal for handling heavy loads across large facilities, supports integration with automated systems for efficient operations.
Motor-Driven Roller Conveyors:
- Mechanism: Each roller has an independent motor, making it possible to control segments of the conveyor selectively.
- Suitability: Offers high precision in product handling and positioning, suitable for intricate and varied manufacturing processes.
Lineshaft Roller Conveyors:
- Mechanism: Driven by a long shaft under the rollers, connected by elastic belts, providing gentle handling of items.
- Suitability: Efficient for moderate loads, particularly where accumulation and low noise are priorities, such as in pharmaceuticals or electronic industries.
Chain-Driven Roller Conveyors:
- Mechanism: Uses a chain loop connected to a motor, which drives the rollers robustly and consistently.
- Suitability: Extremely effective for heavy-duty applications like automotive assemblies or heavy manufacturing, where durability is critical.
Accumulating Roller Conveyors:
- Mechanism: Equipped with sensors and braking systems that allow packages to accumulate on the conveyor without colliding.
- Suitability: Perfect for applications requiring the sequential handling of items without contact, minimizing damage and enhancing sorting processes.
Flexible Roller Conveyors:
- Mechanism: Consists of rollers attached to a flexible frame that can extend, curve, or contract as needed.
- Suitability: Adaptable to varying space constraints, ideal for temporary setups or dynamic operational layouts like in logistics hubs.
These diverse carrier roller conveyors ensure that different types of goods are transported effectively, meeting specific needs of industries by enhancing efficiency and safety.
Components and Parts of Carrier Roller Conveyor
Carrier roller conveyors consist of various integral parts that ensure their efficient and effective operation. Understanding these components is essential for optimal design and maintenance.
- Rollers: Central to the conveyor, these are typically made from metal or plastic and are designed to carry the load.
- Frame: Provides structural support, holding the rollers in place. It must be strong enough to handle the operational load and durable against environmental conditions.
- Drive System: Includes motors and gearboxes that power the rollers, essential for the movement of materials.
- Bearings: Facilitate smooth roller operation, reducing friction and wear, crucial for prolonging the life of the rollers.
- Motor: Acts as the power source, driving the rollers directly or through a transmission system like belts or chains.
- Gearbox: Adjusts the speed and torque from the motor, allowing the conveyor to operate at different speeds according to the requirement.
- Control Systems: These electronic systems manage the conveyor’s speed, direction, and operation, ensuring efficiency and safety.
- Conveyor Belt (if used): In some designs, a belt is used alongside rollers to move materials, especially useful in handling small or irregularly shaped items.
Maintenance Guide and Common Issues with Solutions
Proper maintenance is crucial for the longevity and functionality of carrier roller conveyor. Here are some essential maintenance tasks and common issues along with their solutions:
- Regular Lubrication: Essential for maintaining smooth roller operations and extending the life of bearings.
- Routine Inspections: Critical for identifying wear and potential failures early, preventing downtime.
- Cleaning: Removes debris and prevents buildup that can hinder conveyor efficiency.
- Alignment Checks: Necessary to ensure that all parts are properly aligned and functioning correctly, avoiding uneven wear.
- Tension Adjustments: Important for maintaining the correct tension of any belts used, which helps prevent slippage and misalignment.
- Replacing Worn Parts: Crucial for avoiding breakdowns and maintaining operational efficiency.
- Monitoring Motor Performance: Helps in detecting issues like overheating or power inefficiencies early.
- Testing Control Systems: Ensures that electronic controls and sensors are functioning properly, which is essential for automated systems.
- Checking for Rust and Corrosion: Important in preventing structural weakness, especially in harsh working environments.
- Training Staff: Ensures that all operators understand how to use and troubleshoot the conveyor, which can prevent misuse and accidents.
Understanding and maintaining these components and addressing common issues efficiently can significantly enhance the operational capacity and safety of carrier roller conveyor.
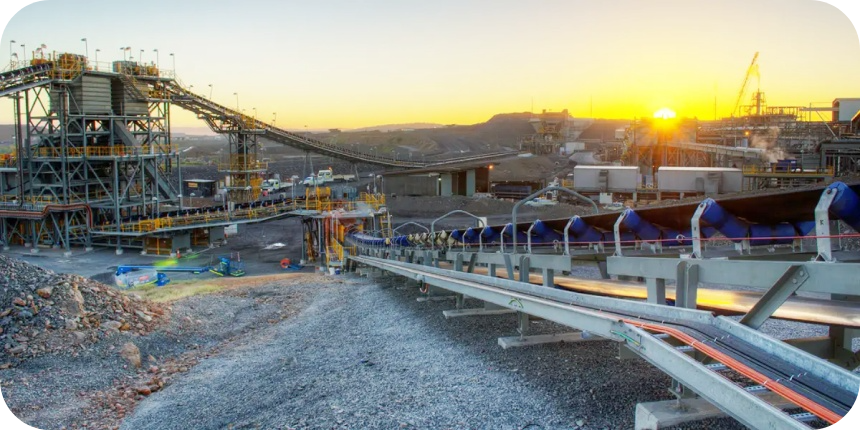
To Understand Components and Parts of Carrier Roller Conveyor
Carrier roller conveyors are composed of intricately designed parts that ensure their effective operation across various industrial applications. Understanding the configuration and function of these components is fundamental to optimizing conveyor performance and enhancing system durability. Key elements include the material selection for the rollers, the engineering of the frame to resist operational stresses, and the integration of advanced drive systems to ensure consistent and reliable movement of goods. Such design considerations are critical not just for initial functionality but also for long-term reliability and efficiency, influencing everything from daily operations to overall maintenance costs.
Maintenance Guide and Common Issues with Solutions
Maintaining a carrier roller conveyor system is essential for ensuring operational efficiency and longevity. Proper care can prevent breakdowns and extend the life of the conveyor, significantly affecting productivity and safety.
- Regular Lubrication: Essential for the smooth operation of rollers and bearings, reducing friction and preventing premature wear.
- Routine Inspections: Helps in identifying and rectifying minor issues before they escalate into major problems.
- Comprehensive Cleaning: Important for removing debris that can clog the system and reduce efficiency.
- Alignment Checks: Ensures all components are correctly aligned, preventing uneven wear and potential malfunctions.
- Tension Adjustments: Vital for maintaining the proper tension of belts and chains, which helps in avoiding slippage and misalignment.
- Part Replacements: Timely replacement of worn-out parts prevents failures and maintains performance.
- Motor and Electrical Checks: Regular testing of motors and electrical components to ensure they are operating within their designed parameters.
- Control System Updates: Keeping software and controls updated to enhance functionality and integration with other systems.
- Environmental Assessments: Regular checks for rust, corrosion, and other environmental impacts that could degrade components.
- Staff Training: Ensuring that all operators are knowledgeable about the system’s operations and maintenance procedures for safer and more efficient use.
Adhering to these maintenance steps will ensure that your carrier roller conveyor operates at peak efficiency, minimizing downtime and maximizing productivity.
Purchasing and Pricing Information for Carrier Roller Conveyor
When considering the acquisition of carrier roller conveyor, it’s important to understand both the purchasing options and the factors that influence their pricing. Whether opting for new or used equipment, each choice comes with its own set of considerations that can significantly impact both upfront costs and long-term value.
Factors Affecting the Price of Carrier Roller Conveyor
Several key factors can influence the cost of conveyor carrier roller:
- Materials: The quality and type of materials used (e.g., stainless steel vs. aluminum) directly affect durability and price.
- Size and Specifications: Larger and more complex systems naturally cost more due to increased material and manufacturing requirements.
- Customization: Custom features tailored to specific operational needs can elevate costs.
- Capacity: Conveyors designed to handle heavier loads require robust constructions, impacting the price.
- Technology: Systems equipped with advanced technology, such as automated controls and digital monitoring, command higher prices.
- Brand Reputation: Established manufacturers with proven track records may offer their products at premium prices.
- Logistical Costs: Shipping and installation logistics, especially for larger systems, can significantly affect total cost.
- Economic Factors: Market demand and economic conditions can fluctuate, influencing pricing.
- Compliance and Safety Standards: Meeting higher regulatory standards can also add to the cost.
Tips on Purchasing New vs. Used Carrier Roller Conveyors
Choosing between new and used carrier roller conveyors involves several strategic considerations:
- Define Requirements: Clearly identify what your operational needs are to determine whether a new or used conveyor would suffice.
- Evaluate Budget: Balance your budgetary constraints with the need for a reliable system.
- Physical Inspection: Thoroughly inspect used conveyors for any signs of wear or mechanical issues.
- Warranty and Technical Support: New equipment typically comes with a manufacturer’s warranty and ongoing support.
- Immediate Availability: Used equipment may be immediately available, reducing lead times.
- Long-Term Costs: Consider potential maintenance and operational costs that might be higher with used equipment.
- Custom Features: New equipment may be more suitable if specific customizations or adaptations are needed.
- Technological Edge: Evaluate if the latest technology in new models would significantly benefit your operations.
- Sustainability: Purchasing used equipment can be a more environmentally sustainable option.
- Expert Advice: Consulting with industry experts can provide insights into the best options based on current market conditions.
Understanding these factors will guide you in making a well-informed decision on purchasing carrier roller conveyors, ensuring you select the option that best fits your operational needs and budget.
Manufacturers and Suppliers of Carrier Roller Conveyors
Selecting the right manufacturer or supplier for carrier roller conveyors is crucial for ensuring you receive a high-quality, reliable system tailored to your operational needs. This section will guide you through the landscape of prominent manufacturers and how to choose the best one for your requirements.
Overview of Leading Manufacturers
Leading manufacturers of carrier roller conveyors distinguish themselves through various specialized attributes:
- Hytrac Conveyors: Renowned for robust and heavy-duty designs, suitable for intensive industrial applications.
- ConveyTech Industries: Known for their custom solutions and integration of cutting-edge technology.
- RollerMaster Global: Offers high-speed conveyor systems known for their durability and reliability.
- FlexConveyor Corp.: Provides adaptable conveyor solutions that are perfect for dynamic operational layouts.
- Durabelt Conveyors: Noted for their focus on energy efficiency and use of sustainable materials.
- Speedline Conveyor Solutions: Specializes in systems designed for high throughput, suitable for large-scale production environments.
- Precision Rollers Ltd.: Delivers conveyors with precision-engineered rollers, ensuring high accuracy in material handling.
- EcoRoll Conveyor Systems: Leads the industry with environmentally friendly practices and designs.
How to Select a Manufacturer or Supplier
Choosing the right supplier involves several crucial steps:
- Assess Compatibility: Match the supplier’s offerings to your specific conveyor needs.
- Verify Credentials: Look for industry certifications and standards compliance to ensure quality.
- Evaluate Technological Innovation: Consider if the supplier’s innovations align with your operational goals.
- Quality of Support Services: Good after-sales support is crucial for ongoing maintenance and troubleshooting.
- Customer Reviews and Feedback: Insight into other customers’ experiences can guide your decision.
- Cost Efficiency: Compare pricing to ensure you get the best value for your investment.
- Quality Assurance: Check the quality of materials and craftsmanship.
- Lead Time: Consider their ability to deliver products in your required timeframe.
- Environmental Commitment: Choose suppliers that prioritize sustainability if this aligns with your company values.
This framework helps ensure that the chosen manufacturer or supplier will meet the technical and operational needs of your business while providing a reliable and effective carrier roller conveyor system.
Innovations and Future Trends in Carrier Roller Conveyor Technology
The field of conveyor carrier roller technology is rapidly evolving, driven by advancements in automation, materials science, and digital technology. These innovations are not only enhancing the efficiency and functionality of conveyor systems but are also paving the way for more sustainable and adaptable solutions in material handling.
Latest Advancements in Carrier Roller Conveyor Technology
Technological advancements in carrier roller conveyor are significantly improving both operational efficiency and user experience:
- Smart Conveyors: Incorporation of sensors and IoT connectivity allows for real-time tracking and automated adjustments.
- Energy-efficient Designs: New motor and roller designs are minimizing power consumption while maximizing output.
- Durable Materials: The use of advanced composites and alloys increases the lifespan and reduces the maintenance needs of conveyors.
- Improved Safety Mechanisms: Enhanced sensors and automatic shut-off capabilities greatly reduce workplace accidents.
- Integration of Machine Learning: Algorithms predict maintenance needs and optimize conveyor operations.
- User-friendly Interfaces: Control systems are now more intuitive, making it easier for operators to manage conveyor operations.
Predictions for Future Developments in the Industry
The future of carrier roller conveyor technology holds promising developments:
- Artificial Intelligence: AI will likely manage systems completely, reducing the need for human oversight.
- Greater Customization: Advances in manufacturing technologies may allow for on-demand conveyor customization.
- Increased Robotics Use: More sophisticated robots could be integrated to work seamlessly with conveyor systems.
- Sustainability Initiatives: There is a trend towards creating more environmentally friendly conveyor systems.
- Global Tracking Systems: Conveyors might soon be integrated into global networks for improved logistics management.
- Enhanced Virtual Interfaces: Operators could remotely control and troubleshoot conveyor systems through advanced virtual interfaces.
Have questions about our Carrier Roller Conveyors? Contact us by filling out this inquiry form.
FAQs about Carrier Roller Conveyor
A roller conveyor is designed to facilitate the efficient transport of goods across short to medium distances within industrial, retail, or distribution environments. By using a series of rollers, the conveyor allows for the smooth and easy movement of items, minimizing human effort and enhancing workflow efficiency. It is particularly useful in applications where items need to be moved repeatedly from one point to another, such as in packaging lines, assembly operations, or sorting processes.
The rollers on a conveyor are typically called “conveyor rollers.” These are the cylindrical components that rotate to move the conveyor belt or directly support and move the items being transported. They are fundamental in defining the conveyor’s efficiency and are designed to handle various load types and sizes, depending on the specific requirements of the system.
There are several types of roller conveyors, each designed for specific applications and load requirements:
Gravity Roller Conveyors: Use gravity to move items, ideal for downward or horizontal movement.
Motorized Roller Conveyors: Equipped with motors to power the rollers and move items along the conveyor.
Flexible Roller Conveyors: Extendable and flexible, suitable for various spaces and easily movable.
Accumulating Conveyors: Allow items to accumulate at the end of the conveyor without pressure build-up.
The standard size of a roller conveyor varies depending on its intended use and the items it will carry. Typically, conveyor widths can range from 12 inches to 36 inches, and lengths can be customized to fit specific operational spaces. The roller diameter and the center-to-center spacing between rollers can also vary to accommodate different sizes and weights of the items being transported.
Last Updated on July 26, 2024 by Jordan Smith
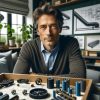
Jordan Smith, a seasoned professional with over 20 years of experience in the conveyor system industry. Jordan’s expertise lies in providing comprehensive solutions for conveyor rollers, belts, and accessories, catering to a wide range of industrial needs. From initial design and configuration to installation and meticulous troubleshooting, Jordan is adept at handling all aspects of conveyor system management. Whether you’re looking to upgrade your production line with efficient conveyor belts, require custom conveyor rollers for specific operations, or need expert advice on selecting the right conveyor accessories for your facility, Jordan is your reliable consultant. For any inquiries or assistance with conveyor system optimization, Jordan is available to share his wealth of knowledge and experience. Feel free to reach out at any time for professional guidance on all matters related to conveyor rollers, belts, and accessories.