Gram Conveyor-Carrying Garland Idlers-High Performance
Conveyor systems are the lifeline of coal mining operations, serving as the backbone for the continuous and efficient transportation of coal from the mining site to processing facilities or loading points. The efficiency and reliability of conveyor systems directly impact the productivity and safety of coal mining operations. They not only streamline the movement of coal but also significantly reduce the need for manual handling, thereby minimizing risks and enhancing operational efficiency.
Carrying garland are engineered to withstand the harsh conditions of the mining environment. Carrying garland can built to endure heavy loads, abrasive materials, and the wear and tear of continuous operation. The design of these rollers aims to ensure that the conveyor belt remains centered and stable during its journey, preventing spillage of coal and reducing the risk of belt misalignment, which can lead to costly downtime and maintenance.
The use of carrying garland sets in coal mining is not just a matter of functionality but also of efficiency and safety. By providing stable and reliable support to the conveyor belts, these rollers play a pivotal role in maintaining the continuous flow of coal, which is essential for meeting the high-demand energy production schedules. Their contribution to the overall efficiency of conveyor systems makes them an indispensable component in modern coal mining operations.
What Is Carrying Garland Idler?
A carrying garland idler is a specific type of idler used in conveyor systems to support and guide the conveyor belt, ensuring smooth and efficient operation. Here are the key aspects of a carrying garland idler:
Structure and Design
1. Configuration:
- Garland Arrangement: Carrying garland idlers are composed of several rollers linked together by chains or links, forming a flexible chain-like arrangement. This allows the idlers to adjust to the conveyor’s path more fluidly than fixed idlers.
- Roller Count: Typically, a garland idler set comprises three to five rollers. The rollers are suspended from the conveyor frame by the chains or links, forming a trough-like shape when in place.
2. Roller Characteristics:
- Materials: The rollers are generally made of steel or a combination of steel and high-strength polymers, ensuring durability and resistance to wear.
- Shape and Size: Rollers come in various diameters and lengths depending on the specific requirements of the conveyor system, ensuring optimal support and load distribution.
3. Troughing Angle:
- Adjustability: The angle of the trough formed by the rollers can vary. Common angles include 20, 35, and 45 degrees, depending on the application and the type of material being transported.
- Purpose: The troughing angle helps in keeping the bulk material centered on the conveyor belt, reducing spillage and improving material handling efficiency.
The Role of Carrying garland in Mining Conveyor Systems
Carrying garland play a crucial role in the efficient operation of conveyor systems in coal mining, ensuring the smooth, efficient, and reliable transport of bulk materials. . These specialized rollers are designed to provide enhanced guidance and support to the conveyor belts, which are integral in transporting coal from mining sites to processing or storage areas.Below is a detailed look at their functions and importance:
Functionality of Carrying Garland
Improved Belt Alignment: One of the key functions of carrying garland is to maintain the proper alignment of the conveyor belt. Misalignment can lead to uneven wear, increased maintenance costs, and potential operational hazards. The carrying garland design ensures that the belt remains centered, reducing the risk of belt drift and the associated complications.
Optimized Friction and Tension: These rollers are strategically placed to manage the tension and friction on the conveyor belt. By doing so, they ensure that the belt moves smoothly and consistently, which is essential for the continuous flow of coal. This smooth operation is crucial for maintaining the efficiency of the entire transportation system.
1. Support and Stability
- Belt Support: In mining operations, conveyor belts often carry heavy, abrasive materials like ore and rock. Carrying garland idlers provide essential support to the conveyor belt, preventing it from sagging and maintaining a consistent, stable path.
- Alignment Maintenance: Proper alignment of the conveyor belt is critical to prevent material spillage and reduce wear on the belt. Garland idlers help keep the belt centered, minimizing drift and ensuring efficient operation.
2. Load Distribution
- Even Load Bearing: The design of garland idlers, which typically includes multiple rollers connected in a flexible chain-like arrangement, ensures that the load is distributed evenly across the conveyor belt. This even distribution reduces localized stress, minimizing wear and tear on both the belt and the idlers.
- Handling Heavy Loads: In mining, the conveyors handle extremely heavy loads. The robust construction and multiple support points of garland idlers are designed to manage these loads efficiently without compromising the system’s integrity.
3. Flexibility and Adaptability
- Terrain Adaptation: Mining environments are often rugged and uneven. The flexibility of garland idlers allows them to adapt to the contour of the terrain, maintaining effective belt support even on undulating surfaces.
- Shock Absorption: The chain-like connection of the rollers provides a degree of flexibility that helps absorb shocks and vibrations, which are common in mining operations. This shock absorption protects the conveyor belt and the overall structure from damage.
4. Durability and Reliability
- Robust Construction: Garland idlers are built to withstand the harsh conditions of mining environments. They are typically made from high-strength materials that resist wear, corrosion, and impact.
- Long Service Life: Due to their durable construction, garland idlers have a long service life, reducing the frequency of replacements and the associated downtime.
5. Maintenance and Cost Efficiency
- Reduced Maintenance Needs: The even load distribution and shock absorption capabilities of garland idlers reduce the strain on the conveyor belt and the idlers themselves, leading to lower maintenance requirements.
- Cost Savings: By extending the lifespan of the conveyor belt and reducing maintenance needs, garland idlers contribute to significant cost savings in mining operations. Efficient material handling also leads to lower operational costs.
6. Enhanced Safety
- Operational Safety: Stable and well-supported conveyor belts reduce the risk of belt slippage, spillage, and other operational hazards. This contributes to a safer working environment for miners.
- Emergency Handling: In the event of unexpected loads or shifts, the flexibility of garland idlers helps to manage these situations without causing major disruptions or damage to the system.
7. Performance Optimization
- Efficient Material Transport: Garland idlers ensure smooth and continuous movement of the conveyor belt, optimizing the transport of materials from mining sites to processing areas.
- Energy Efficiency: By maintaining proper belt alignment and reducing friction, garland idlers help in conserving energy, making the conveyor system more efficient.
Impact on Coal Transportation
Efficient Coal Transportation: The primary benefit of using carrying garland in coal mining conveyor systems is the efficient transportation of coal. By providing stable and consistent support, these rollers ensure that large volumes of coal can be moved swiftly and reliably.
Reduced Downtime and Maintenance: With better support and alignment control, carrying garland contribute to reduced wear and tear on the conveyor belt. This translates to lower maintenance requirements and less downtime for repairs, which is critical in high-output mining operations where every minute of operation counts.
Adaptability to Various Conditions: Coal mining environments can be harsh and unpredictable. Carrying garland are designed to withstand these conditions, including variations in load, moisture, and temperature. This adaptability ensures that the conveyor system remains operational and efficient under different mining conditions.
Specific Benefits in Coal Transportation
1. Reduced Belt Wear and Tear:
- The even distribution of coal across the belt minimizes localized wear, reducing the need for frequent belt replacements and maintenance.
2. Minimized Spillage:
- Proper alignment and support provided by garland idlers help prevent coal spillage, ensuring cleaner operations and reducing material loss.
3. Enhanced System Reliability:
- The durability and adaptability of garland idlers enhance the overall reliability of the conveyor system, reducing the likelihood of breakdowns and associated downtime.
4. Operational Continuity:
- By absorbing shocks and vibrations, garland idlers protect the conveyor system from damage during continuous operation, ensuring uninterrupted coal transportation.
Carrying garland idlers significantly impact coal transportation within conveyor systems, enhancing efficiency, reliability, and safety. Here is an in-depth exploration of their impact on coal transportation:
1. Enhanced Belt Support and Stability
- Support for Heavy Loads: Coal is a heavy material, and the conveyor belts transporting it require strong support to prevent sagging and maintain a smooth path. Carrying garland idlers provide robust support, ensuring the belt remains stable under heavy loads.
- Consistent Alignment: Proper alignment of the conveyor belt is critical to prevent material spillage and maintain operational efficiency. Garland idlers help keep the belt centered, reducing the risk of misalignment and associated issues.
2. Improved Load Distribution
- Even Distribution of Coal: The multiple rollers in garland idlers distribute the weight of the coal evenly across the conveyor belt. This even distribution minimizes localized stress, reducing wear and tear on the belt and extending its lifespan.
- Handling Variable Loads: Coal transportation often involves fluctuating loads. Garland idlers are designed to handle these variations efficiently, maintaining consistent performance even with changing load conditions.
3. Adaptability to Harsh Conditions
- Terrain Adaptation: Coal mines and transportation routes often have uneven terrain. The flexible design of garland idlers allows them to adapt to these variations, maintaining effective support and alignment of the conveyor belt.
- Shock and Vibration Absorption: Coal transportation involves frequent loading and unloading, causing shocks and vibrations. The flexibility of garland idlers helps absorb these impacts, protecting the conveyor belt and reducing the risk of damage.
4. Durability and Longevity
- Resilience to Harsh Environments: Garland idlers are constructed from durable materials that resist wear, corrosion, and impact, making them suitable for the harsh conditions of coal transportation.
- Extended Service Life: Their robust construction ensures a long service life, reducing the frequency of replacements and the associated downtime, contributing to more efficient operations.
5. Reduced Maintenance Requirements
- Lower Maintenance Needs: The even load distribution and shock absorption properties of garland idlers reduce strain on the conveyor system, leading to lower maintenance requirements.
- Cost Savings: By extending the lifespan of the conveyor belt and reducing maintenance needs, garland idlers contribute to significant cost savings in coal transportation operations.
6. Safety Improvements
- Operational Safety: Stable and well-supported conveyor belts reduce the risk of belt slippage, spillage, and other operational hazards, creating a safer working environment for personnel involved in coal transportation.
- Emergency Handling: In the event of unexpected load variations or system shocks, the flexibility of garland idlers helps manage these situations without causing major disruptions or damage.
7. Efficiency and Performance Optimization
- Efficient Coal Transport: Garland idlers ensure the smooth and continuous movement of coal along the conveyor belt, optimizing the transportation process from mines to processing or storage facilities.
- Energy Efficiency: By maintaining proper belt alignment and reducing friction, garland idlers help conserve energy, making the conveyor system more efficient and reducing operational costs.
How Do Carrying Garland Work?
Understanding the working mechanism of carrying garland is key to appreciating their role in enhancing the efficiency of conveyor systems, particularly in demanding environments like coal mining. These rollers are ingeniously designed to optimize the performance of conveyor belts, ensuring smooth and uninterrupted coal transportation.
Technical Breakdown of the Working Mechanism
Triple Roller Configuration: Each triple idler set consists of three rollers arranged in a trough formation. This setup includes a central roller with a slight upward curve and two side rollers angled downwards. This arrangement forms a ‘trough’ that cradles the conveyor belt, providing comprehensive support across its width.
Distributed Load Handling: The carrying garland design evenly distributes the weight of the material over the belt. This distribution reduces the stress on any single point of the belt or the rollers, minimizing wear and tear. It also helps in accommodating heavier loads without compromising the belt’s integrity.
Dynamic Interaction with the Conveyor Belt: As the conveyor belt moves, it is continuously supported by these rollers. The central roller bears the bulk of the load while the side rollers stabilize the belt’s movement, preventing spillage of material and maintaining the belt’s alignment.
GRAM Conveyor carrying garland can load distribution even load bearing and ensure smooth and continuous movement of the conveyor belt, contributes to a safer working environment for miners
Design and Structure of Carrying Garland
Robust Construction: Typically, these rollers are constructed from heavy-duty materials capable of withstanding the harsh conditions of coal mining. They are designed to be durable, often featuring reinforced frames and high-quality bearings for smooth operation.
Optimized Roller Surface: The surface of the rollers is often designed to enhance grip and reduce slippage. This can include textured finishes or coatings that increase friction between the belt and the rollers, ensuring that the belt moves consistently and the material is transported efficiently.
Interaction with Conveyor Belt and Material: The unique design of carrying garland ensures optimal interaction with both the conveyor belt and the transported coal. The trough shape helps contain the material on the belt, reducing spillage. Simultaneously, the design aids in maintaining the belt’s tension and alignment, which is crucial for the long-term functionality of the conveyor system.
Benefits of Carrying Garland in Coal Mining
The implementation of carrying garland in coal mining conveyor systems brings a multitude of benefits, significantly impacting the efficiency, safety, and overall productivity of mining operations. These advantages stem from the unique design and functionality of the carrying garland, which are tailored to meet the demanding requirements of the coal mining industry.
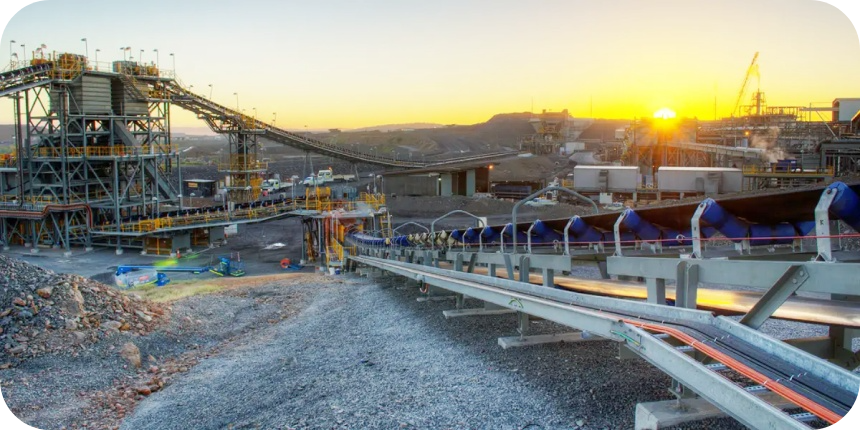
Increased Conveyor Belt Life
Even Distribution of Stress: The triple idler system’s ability to evenly distribute the weight of the coal across the belt reduces the stress on any single point. This even distribution minimizes the risk of belt wear and tear, thereby extending the lifespan of the conveyor belt.
Enhanced Stability: The stability provided by the carrying garland prevents excessive movement and misalignment of the conveyor belt, which are common causes of accelerated wear. This stability ensures that the belt remains functional for a longer period, reducing the frequency of replacements.
Reduced Maintenance
Lower Wear and Tear: The reduced stress and enhanced stability of the conveyor belt translate to less wear and tear, not only on the belt but also on the rollers themselves. This results in lower maintenance requirements and costs.
Predictable Maintenance Schedules: With less unexpected breakdowns and wear, maintenance schedules can be more predictable, allowing for better planning and less downtime.
Improved Load Distribution
Even Distribution of Coal: The multiple rollers in garland idlers distribute the weight of the coal evenly across the conveyor belt. This even distribution minimizes localized stress, reducing wear and tear on the belt and extending its lifespan.
Handling Variable Loads:Coal transportation often involves fluctuating loads. Garland idlers are designed to handle these variations efficiently, maintaining consistent performance even with changing load conditions.
Efficiency and Performance Optimization
Efficient Coal Transport: Garland idlers ensure the smooth and continuous movement of coal along the conveyor belt, optimizing the transportation process from mines to processing or storage facilities.
Energy Efficiency: By maintaining proper belt alignment and reducing friction, garland idlers help conserve energy, making the conveyor system more efficient and reducing operational costs.
Improved Efficiency
Optimized Material Handling: The trough shape formed by the carrying garland ensures that coal is contained within the center of the belt, reducing spillage and wastage. This containment leads to more efficient material handling and transport. Smooth Belt Operation: The design of the rollers allows for smoother operation of the conveyor belt. Smooth operation means less energy consumption and more consistent coal flow, contributing to overall operational efficiency.
Impact on Safety and Productivity
Enhanced Safety: The stability and reliability of the conveyor system, thanks to the carrying garland, reduce the risk of accidents and breakdowns. This enhances the overall safety of the mining operations.
Increased Productivity: With less downtime for maintenance and repairs, and more efficient material handling, the overall productivity of the coal mining operation is significantly increased. The conveyor system can handle more material in less time, contributing to the bottom line of the mining operation.
Adaptability to Harsh Conditions
Terrain Adaptation: Coal mines and transportation routes often have uneven terrain. The flexible design of garland idlers allows them to adapt to these variations, maintaining effective support and alignment of the conveyor belt.
Shock and Vibration Absorption: Coal transportation involves frequent loading and unloading, causing shocks and vibrations. The flexibility of garland idlers helps absorb these impacts, protecting the conveyor belt and reducing the risk of damage.
Carrying garland idlers play a crucial role in coal transportation, enhancing the overall performance, safety, and cost-effectiveness of conveyor systems in mining operations. Their ability to provide robust support, distribute heavy loads evenly, and adapt to harsh conditions makes them indispensable in ensuring the efficient and reliable transport of coal.
Keep Your Belt Running with Carrying Garland Idlers
Instead of fixed idlers, garland rollers can be installed in the carrying and return run, as well as in impact areas.
Conveyor Idler Garland systems provide an effective solution when transporting larger materials in high speed/high tonnage applications.
Garlands are mostly used for rollers with larger diameters and in mining areas with wider belts and higher belt speeds, as well as in underground conveyors.
The rollers are connected to each other with flexible links and fixed to the conveyor frame with suspension links, which allows free movement in the direction of belt travel.
A garland set is easy to replace by lifting the idler set from the hook. The flexible arrangement also has a positive influence on the self-centering of the belt.
- Available for various belt widths and sizes
- Troughing angles upon requests; standard 30°, 35° and 45°; for return garlands 10°
- Garlands come in 2-, 3-, 4- or 5-roller design; standard as 3-roller design for carry garlands and a 2-roller for return garlands
- Roller diameters from 63.5 mm to 219 mm and bearings from 6204 to 6312
- Rubber discs and impact rings in various dimensions are available for return and impact garlands
How to Choose the Right Carrying Garland for Your Conveyor System?
Selecting the appropriate carrying garland idlers for your conveyor system is crucial to ensure optimal performance, longevity, and efficiency. Here are key factors to consider when choosing the right carrying garland idlers for your conveyor system:
1. Understand Your Material and Load Requirements
Material Type: Different materials have varying weights, abrasiveness, and handling characteristics. For instance, coal is heavy and abrasive, requiring robust idlers. Know the specific properties of the material you are conveying.
Load Weight and Distribution: Determine the maximum load weight your conveyor will handle. Ensure the garland idlers can support this weight without sagging or causing excessive wear on the conveyor belt.
2. Consider the Operating Environment
Terrain and Installation Conditions: Evaluate the terrain where the conveyor system will be installed. Uneven or rugged terrains require idlers that can adapt and provide consistent support.
Environmental Factors: Consider factors such as temperature, humidity, and exposure to corrosive substances. Choose garland idlers made from materials that can withstand these conditions.
3. Assess the Conveyor Belt Specifications
Belt Width and Speed: Ensure the garland idlers are compatible with the width and speed of your conveyor belt. Incorrect sizing can lead to misalignment and inefficient operation.
Troughing Angle: The troughing angle of the idlers should match the conveyor belt’s requirements. Common angles include 20, 35, and 45 degrees, which help in maintaining the belt’s alignment and carrying capacity.
4. Evaluate the Idler Design and Construction
Roller Material and Quality: The rollers in garland idlers should be made from high-quality, durable materials such as steel or high-strength polymers. These materials resist wear and tear, ensuring a longer service life.
Number of Rollers: Garland idlers typically have three to five rollers. The choice depends on the load distribution needs and the specific design of your conveyor system.
Bearing Type and Sealing: Bearings should be robust and well-sealed to prevent contamination from dust and moisture, which can lead to premature failure.
5. Check for Compliance and Standards
Industry Standards: Ensure that the garland idlers comply with relevant industry standards and regulations. This guarantees quality, safety, and reliability.
Manufacturer Reputation: Choose garland idlers from reputable manufacturers known for their quality and reliability. Check for customer reviews, certifications, and warranties.
6. Consider Maintenance and Accessibility
Ease of Maintenance: Select garland idlers that are easy to inspect, maintain, and replace. This reduces downtime and maintenance costs.
Spare Parts Availability: Ensure that spare parts for the garland idlers are readily available. This facilitates quick repairs and reduces operational disruptions.
7. Evaluate Cost-Effectiveness
Initial Investment vs. Long-Term Savings: While high-quality garland idlers may have a higher initial cost, they often result in long-term savings by reducing maintenance, downtime, and replacement frequency.
Energy Efficiency: Idlers that maintain proper belt alignment and reduce friction contribute to energy efficiency, lowering operational costs.
Choosing the right carrying garland idlers for your conveyor system involves a comprehensive assessment of your material and load requirements, operating environment, conveyor belt specifications, idler design and construction, compliance with industry standards, maintenance needs, and cost-effectiveness. By carefully considering these factors, you can select garland idlers that will enhance the performance, reliability, and efficiency of your conveyor system, ensuring smooth and continuous operation.
Practical Applications of Carrying Garland in Various Industries
Carrying garland idlers are versatile components used in a variety of industries where conveyor systems are essential for material handling. Here’s an overview of their practical applications across different sectors:
1. Mining and Quarrying
- Coal Mining: In coal mining, carrying garland idlers support the heavy loads of coal transported from extraction sites to processing plants. Their robust design ensures stability and reduces belt wear.
- Ore and Mineral Transportation: These idlers are also used in the transportation of ores and minerals, providing the necessary durability and flexibility to handle the rough, abrasive nature of the materials.
2. Construction
- Aggregate Handling: In construction, garland idlers are used in conveyors transporting aggregates such as sand, gravel, and crushed stone. Their adaptability to varying load conditions and terrain makes them ideal for construction sites.
- Cement Production: Carrying garland idlers are used in cement plants to transport raw materials like limestone and clinker. Their ability to handle heavy loads and withstand harsh conditions is crucial in this industry.
3. Power Generation
- Coal-Fired Power Plants: In these plants, garland idlers are used to transport coal from storage facilities to the boilers. Their reliability and efficiency ensure a steady supply of coal, contributing to uninterrupted power generation.
- Biomass and Other Fuels: They are also used in systems transporting biomass and other alternative fuels, where their adaptability and durability are essential.
4. Bulk Material Handling
- Port and Harbor Operations: Carrying garland idlers are employed in port facilities for the bulk handling of materials such as grain, coal, ores, and other bulk commodities. Their design helps manage the heavy loads and continuous operation typical in these environments.
- Warehousing and Logistics: In large warehouses and logistics centers, these idlers facilitate the movement of bulk materials, ensuring efficient and reliable operations.
5. Agriculture
- Grain and Fertilizer Transportation: In the agricultural sector, garland idlers are used in conveyors that transport grain, seeds, and fertilizers. Their flexibility and robust construction ensure smooth and efficient handling of these materials.
- Processing Facilities: They are also found in agricultural processing plants, where they transport raw materials and finished products.
6. Manufacturing
- Automotive Industry: In the automotive industry, garland idlers are used in conveyor systems that transport heavy components and assemblies. Their ability to handle variable loads and provide stable support is crucial.
- Food and Beverage Production: They are used in food processing and beverage manufacturing facilities to transport ingredients and finished products, ensuring hygiene and efficiency.
7. Recycling and Waste Management
- Waste Sorting and Transport: In recycling facilities, carrying garland idlers are used in conveyors that sort and transport waste materials. Their durability and adaptability to different types of waste make them ideal for this application.
- Material Recovery: They are also employed in material recovery facilities, where they help transport recyclable materials efficiently.
Key Benefits Across Industries
1. Enhanced Durability and Reliability:
- Garland idlers are constructed from high-quality materials, ensuring long service life and reliable performance even under heavy and continuous loads.
2. Adaptability to Harsh Conditions:
- Their flexible design allows them to adapt to various terrains and environmental conditions, making them suitable for outdoor and harsh environments.
3. Improved Efficiency:
- By providing stable support and reducing belt wear, garland idlers enhance the overall efficiency of conveyor systems, reducing downtime and maintenance costs.
4. Cost-Effectiveness:
- The long lifespan and low maintenance requirements of garland idlers contribute to significant cost savings in various industrial applications.
5. Safety Enhancements:
- Properly supported and aligned conveyor belts reduce the risk of operational hazards, ensuring a safer working environment.
Carrying garland idlers are vital components in conveyor systems across multiple industries, including mining, construction, power generation, bulk material handling, agriculture, manufacturing, and recycling. Their ability to handle heavy and abrasive materials, adapt to different terrains, and provide reliable performance under varying load conditions makes them indispensable in enhancing the efficiency, reliability, and safety of material transportation processes.
CONTACT US
Let us help you find a better solution!