Carrying Idler Belt Conveyor Systems
Belt conveyor systems are essential in various industries for the efficient movement of materials. These systems consist of a continuous belt that moves over a series of rollers and supports, ensuring smooth transportation. A critical component within these systems is the carrying idler. The carrying idler belt conveyor is designed to support the conveyor belt and its load, ensuring even distribution and reducing wear and tear. By providing consistent support and stability, carrying idler belt conveyor systems enhance the overall efficiency and longevity of the conveyor, making them indispensable for operations that require reliable material handling solutions.
Carrying Idler Belt Conveyor Basics
Definition of Carrying Idlers in Belt Conveyors
Carrying idlers are crucial components within belt conveyor systems. They are designed to support the conveyor belt along its length and ensure that the belt maintains a smooth, continuous motion. A carrying idler typically consists of a series of rollers arranged in a horizontal row, which provides a stable surface for the conveyor belt to rest upon as it transports materials from one point to another. These idlers are positioned at regular intervals along the conveyor’s frame, distributing the weight of the load evenly and reducing the strain on the belt.
The primary function of carrying idlers in a carrying idler belt conveyor system is to support the conveyor belt and its load. This support helps to maintain the belt’s alignment and prevents it from sagging or becoming misaligned, which could lead to operational inefficiencies or damage to the belt. By ensuring that the belt remains in proper alignment, carrying idlers also help to reduce friction and wear, thereby extending the lifespan of the conveyor belt and minimizing maintenance requirements.
How Carrying Idlers Support and Move the Belt
In a carrying idlers belt conveyor system, the carrying idlers play a vital role in the overall functionality of the conveyor. These idlers work in conjunction with other components, such as the drive and tail pulleys, to create a continuous loop of motion that moves the conveyor belt and its load.
The carrying idlers are strategically placed along the length of the conveyor to provide consistent support to the belt. Each idler set is designed to hold the belt in a specific position, preventing it from sagging or becoming misaligned. This consistent support ensures that the belt can move smoothly and efficiently, even under heavy loads.
As the conveyor belt moves, the carrying idlers rotate along with the belt, reducing friction and allowing for a smoother, more efficient transfer of materials. The rollers within the idlers are typically made from durable materials, such as steel or high-impact plastic, which can withstand the constant motion and weight of the load. This durability ensures that the carrying idlers can provide reliable support over extended periods, even in demanding industrial environments.
The placement and design of carrying idlers are crucial to the performance of the carrying idler belt conveyor system. The idlers must be spaced at appropriate intervals to provide adequate support and prevent the belt from sagging. Additionally, the rollers within the idlers must be aligned correctly to ensure that the belt remains in proper alignment and moves smoothly along the conveyor’s path.
Carrying idlers are essential components of carrying idler belt conveyor systems. They provide the necessary support to ensure that the conveyor belt remains in proper alignment and moves smoothly along its path. By reducing friction and wear, carrying idlers help to extend the lifespan of the conveyor belt and enhance the overall efficiency of the conveyor system. Understanding the definition, function, and benefits of carrying idlers is crucial for optimizing the performance and reliability of belt conveyor systems in various industrial applications.
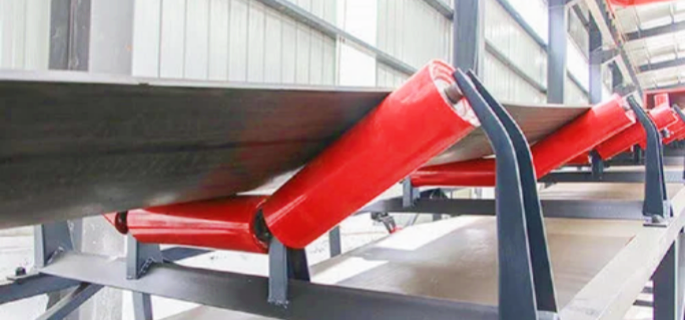
Key Components of Carrying Idler Belt Conveyor
A carrying idler belt conveyor is an essential piece of equipment used in various industries for the efficient transport of bulk materials. It consists of several key components that work together to ensure the smooth and reliable movement of the conveyor belt and the materials it carries. Here’s a detailed description of the key components:
1. Conveyor Belt
- The conveyor belt is the most critical part of the conveyor system. It is the surface on which the material is transported. The belt is typically made from rubber, fabric, or metal, depending on the material being conveyed and the working environment. The belt needs to be strong, durable, and resistant to wear and tear.
2. Carrying Idlers
- Carrying idlers are a series of rollers that support the conveyor belt and the material being transported. They are spaced at regular intervals along the length of the conveyor. The idlers are designed to reduce friction and help the belt maintain its shape under the weight of the load. Typically, carrying idlers consist of three rollers arranged in a trough shape to cradle the belt and keep the material centered.
3. Return Idlers
- Return idlers are similar to carrying idlers but are used on the return side of the conveyor belt (the side that does not carry material). Their primary function is to support the empty belt and guide it back to the start of the conveyor loop.
4. Drive Pulley
- The drive pulley is responsible for powering the conveyor belt. It is connected to a motor that drives the pulley, which, in turn, moves the belt. The drive pulley is usually located at the discharge end of the conveyor and is designed to provide sufficient friction to move the belt without slipping.
5. Tail Pulley
- The tail pulley is located at the opposite end of the conveyor from the drive pulley. It guides the conveyor belt and helps maintain tension in the system. The tail pulley is also adjustable to help ensure that the belt runs smoothly and stays centered.
6. Belt Tensioning System
- The belt tensioning system ensures that the conveyor belt remains taut and properly aligned. This system typically includes a combination of adjustable pulleys, screws, or hydraulic cylinders that apply tension to the belt. Proper tensioning is crucial to prevent belt slippage and to ensure efficient operation.
7. Belt Cleaner
- Belt cleaners are installed at strategic points along the conveyor to remove any material that may stick to the belt. This prevents material buildup, which could lead to belt misalignment, increased wear, and operational inefficiencies.
8. Skirt Board and Seal
- The skirt board is a protective barrier that runs along the edges of the conveyor belt at loading and transfer points. It helps contain the material on the belt and prevents spillage. The skirt seal is the flexible component that creates a seal between the skirt board and the conveyor belt, further reducing spillage.
9. Motor and Gearbox
- The motor provides the necessary power to drive the conveyor system. It is usually connected to the drive pulley via a gearbox that adjusts the speed and torque to match the conveyor’s operational requirements.
10. Frame
- The frame is the structural component that supports the entire conveyor system. It is typically made of steel or aluminum and is designed to withstand the load of the materials being conveyed as well as the forces exerted by the moving belt and idlers.
11. Feed Chute
- The feed chute is where the material is loaded onto the conveyor belt. It is usually designed to evenly distribute the material onto the belt to avoid overloading and ensure smooth operation.
12. Discharge Chute
- The discharge chute is located at the end of the conveyor and directs the material off the belt and onto the next stage of the process or into storage. It is designed to minimize spillage and material degradation during transfer.
13. Control System
- The control system includes all the necessary components for operating the conveyor, such as start/stop buttons, emergency stop switches, speed controllers, and sensors. The control system ensures that the conveyor operates safely and efficiently.
14. Safety Devices
- Safety devices include emergency stop switches, guards, pull cords, and other mechanisms designed to protect workers from injury and to prevent damage to the conveyor system. They are an essential component of any conveyor system, ensuring compliance with safety regulations.
These components collectively enable the carrying idler belt conveyor to efficiently transport materials over long distances, making it a vital piece of equipment in industries such as mining, manufacturing, and logistics.
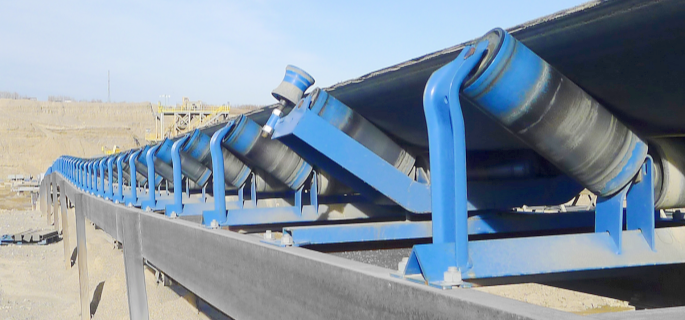
Benefits of Using Carrying Idlers Belt Conveyor Systems
Using carrying idler belt conveyor systems offers a wide range of benefits, making them a popular choice in various industries for material handling. Here are some of the key advantages:
1. Efficient Material Handling
- Carrying idler belt conveyors are highly efficient for transporting bulk materials over long distances. They can handle a wide variety of materials, including granular, powdery, or lumpy substances, at a steady and controlled pace, reducing the need for manual handling.
2. Cost-Effective Operation
- Belt conveyors with carrying idlers require relatively low maintenance and operational costs. The system is designed for long-term use, and when properly maintained, it can operate continuously with minimal downtime. This reduces labor costs and increases overall productivity.
3. High Capacity
- These conveyor systems can transport large volumes of material quickly and efficiently. They are capable of handling high throughput, making them suitable for industries that require the movement of significant quantities of materials, such as mining, agriculture, and manufacturing.
4. Versatility
- Carrying idler belt conveyors can be customized to fit specific operational needs. They can be designed to handle various materials, adapt to different layouts, and accommodate varying conveyor lengths, inclines, and declines, making them versatile for a wide range of applications.
5. Reduced Material Spillage
- The use of trough-shaped carrying idlers helps keep the material centered on the belt, significantly reducing the risk of spillage. This containment improves cleanliness, reduces waste, and minimizes the need for cleanup operations.
6. Low Power Consumption
- Compared to other material handling methods, carrying idler belt conveyors typically consume less power. The rolling action of the idlers reduces friction between the belt and the conveyor frame, leading to lower energy consumption and operating costs.
7. Smooth and Controlled Movement
- The design of the carrying idlers ensures smooth and consistent movement of the conveyor belt, which is crucial for maintaining the integrity of the materials being transported. This controlled movement helps prevent material degradation and ensures that products reach their destination in good condition.
8. Improved Safety
- Carrying idler belt conveyors reduce the need for manual handling of materials, thereby lowering the risk of workplace injuries. Additionally, these systems can be equipped with various safety features, such as emergency stop mechanisms and guards, to further enhance operational safety.
9. Scalability
- These systems can be easily scaled up or down to match production requirements. Whether you need to extend the length of the conveyor, increase its capacity, or modify its layout, carrying idler belt conveyors offer the flexibility to adapt to changing operational needs.
10. Environmental Benefits
- By reducing the need for fuel-powered vehicles or manual labor to move materials, carrying idler belt conveyors contribute to lower greenhouse gas emissions and a reduced environmental footprint. Additionally, their energy efficiency further supports sustainable operations.
11. Reliability and Durability
- Carrying idler belt conveyors are designed for durability and reliability. With proper maintenance, they can provide long service life even in harsh environments, such as mining or heavy industrial settings, making them a dependable choice for continuous operations.
12. Minimal Maintenance
- The simplicity of the design, coupled with the quality of materials used, means that these conveyors require minimal maintenance. Regular inspections and occasional lubrication of moving parts are generally sufficient to keep the system running efficiently.
13. Customizable Design
- These conveyor systems can be customized to meet specific operational needs, including variable speeds, different belt materials, and special design considerations for handling specific materials or operating in unique environments.
14. Ease of Installation
- Carrying idler belt conveyor systems are relatively easy to install compared to more complex material handling systems. Their modular design allows for quick assembly and disassembly, facilitating installation in new locations or modification of existing setups.
Overall, carrying idler belt conveyor systems provide a reliable, efficient, and cost-effective solution for material transportation in a variety of industries. Their versatility, scalability, and low operating costs make them an excellent choice for both small-scale operations and large industrial applications.
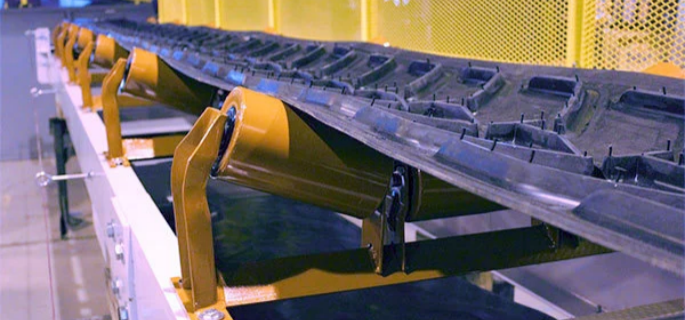
Pricing Overview on Carrying Idler Belt Conveyors
Factors Influencing the Price of Carrying Idlers
The cost of carrying idlers in a carrying idlers belt conveyor system can vary widely based on several factors. Understanding these factors can help buyers make informed decisions and optimize their investment.
- Material Quality: The type and quality of materials used in the construction of carrying idlers significantly affect their price. High-quality materials such as stainless steel or high-impact plastic are more expensive but offer greater durability and longevity. For instance, idlers made from corrosion-resistant materials are essential in environments with high moisture or chemical exposure, but they come at a premium cost.
- Bearing Type and Quality: The bearings within carrying idlers play a crucial role in reducing friction and ensuring smooth rotation. High-quality bearings that offer better performance and longer life tend to be more expensive. For example, sealed bearings that protect against dust and contaminants increase the cost but reduce maintenance needs and downtime.
- Customization and Design Specifications: Custom-designed carrying idlers tailored to specific conveyor system requirements often come with higher costs. Customization may include specific dimensions, unique shapes, or additional features such as reinforced frames or special coatings. These bespoke solutions are designed to meet unique operational challenges, but they require more resources and expertise to manufacture.
- Production Volume: The number of carrying idlers ordered can also influence the price. Bulk orders typically benefit from economies of scale, leading to a lower cost per unit. Conversely, smaller orders may not qualify for discounts and thus, each idler may be more expensive.
- Supplier and Brand Reputation: Established brands and reputable suppliers may charge higher prices due to their proven track record of quality and reliability. Investing in carrying idlers from a well-known manufacturer can provide peace of mind and assurance of performance, but it can also mean paying a premium.
Tips on Cost-Saving Without Compromising Quality
While the price of carrying idlers can be influenced by various factors, there are several strategies buyers can employ to save costs without sacrificing quality.
- Bulk Purchasing: Ordering carrying idlers in bulk can significantly reduce the cost per unit. Suppliers often offer discounts for larger orders, so consolidating purchases can lead to substantial savings. This approach is particularly beneficial for large-scale operations where a high volume of idlers is required.
- Opt for Standard Sizes: Customization can drive up costs. If possible, opting for standard-sized carrying idlers that are readily available from suppliers can help keep prices down. Standard sizes are mass-produced, leading to lower manufacturing costs and quicker delivery times.
- Supplier Negotiation: Building a good relationship with suppliers can provide opportunities for negotiation on pricing. Long-term partnerships or repeat business can lead to discounts and more favorable terms. Additionally, negotiating payment terms, such as longer payment periods or installment plans, can help manage cash flow more effectively.
- Regular Maintenance: Investing in regular maintenance of carrying idlers can extend their lifespan and reduce the need for frequent replacements. Proper maintenance practices, such as regular lubrication and inspection, ensure that idlers remain in good working condition, thereby lowering overall costs associated with premature wear and tear.
- Comparative Shopping: Conducting thorough research and comparing prices from different suppliers can help identify the best deals. Online marketplaces and trade shows are excellent venues for comparing options and finding competitive pricing. It is important, however, to ensure that lower prices do not come at the expense of quality.
By understanding the factors that influence the price of carrying idlers and employing these cost-saving strategies, buyers can make informed decisions that balance cost and quality. This approach ensures that carrying idler belt conveyor systems remain efficient and reliable, supporting smooth operations and minimizing downtime.
Types of Carrying Idler Belt Conveyor and Their Functions
Detailed Enumeration and Description of Different Types of Idlers
In a carrying idler belt conveyor system, various types of idlers play crucial roles in supporting and guiding the conveyor belt. Understanding the different types of idlers and their specific functions can help in selecting the appropriate components for optimal conveyor performance. Below is a detailed enumeration and description of the most common types of idlers used in carrying idler belt conveyor systems.
Carrying Idlers: Carrying idlers are designed to support the weight of the conveyor belt and the material being transported. They are typically placed on the carrying side of the belt and are arranged in sets of two or more. The primary function of carrying idlers is to prevent the belt from sagging and to ensure smooth movement. They are available in various configurations, such as flat, troughing, and impact, to suit different operational needs.
- Flat Carrying Idlers: Used for light to medium loads, these idlers provide a flat surface for the belt and are ideal for transporting packaged or loose materials.
- Troughing Carrying Idlers: Featuring a set of rollers arranged at an angle, these idlers form a trough shape that helps to center the load and prevent spillage. They are commonly used for transporting bulk materials.
- Impact Carrying Idlers: Equipped with shock-absorbing rollers, these idlers are placed at loading points to cushion the impact of heavy materials being dropped onto the belt, protecting both the belt and the idlers from damage.
Return Idlers: Return idlers are positioned on the return side of the belt to support the empty belt as it travels back to the loading point. These idlers help to maintain belt alignment and reduce drag.
- Flat Return Idlers: These idlers provide a flat surface for the return belt, ensuring it stays aligned and reducing wear.
- V-Return Idlers: Featuring rollers arranged in a V-shape, these idlers help to center the belt and prevent it from wandering, especially on longer conveyor runs.
Self-Aligning Idlers: Self-aligning idlers are designed to automatically correct belt misalignment. They are typically installed at intervals along the conveyor to ensure the belt remains centered and to prevent tracking issues.
- Troughing Self-Aligning Idlers: Used on the carrying side, these idlers help to correct any misalignment that occurs during the transportation of bulk materials.
- Return Self-Aligning Idlers: Placed on the return side, these idlers ensure the empty belt stays aligned, reducing the risk of belt damage and operational disruptions.
Training Idlers: Training idlers are another type of idler used to guide the belt and ensure it runs true along the conveyor path. They can be manually adjusted to correct belt alignment and are often used in conjunction with self-aligning idlers.
Transition Idlers: Transition idlers are placed at the point where the belt changes from a flat profile to a trough profile, or vice versa. These idlers help to gradually transition the belt, reducing stress and preventing material spillage.
This table provides a concise overview of the specific roles each type of idler plays in the smooth and efficient operation of a carrying idler belt conveyor system.
PDF Resources for Deeper Understanding
To gain a deeper understanding of the various types of idlers and their functions in a carrying idler belt conveyor system, several PDF resources are available that provide detailed information and technical specifications. These resources often include diagrams, operational guidelines, and maintenance tips to ensure optimal performance and longevity of the conveyor system.
- Manufacturer Catalogs: Many conveyor belt manufacturers offer comprehensive catalogs in PDF format, detailing the specifications and applications of their idlers. These catalogs often include product codes, dimensions, material types, and recommended uses, providing valuable information for selecting the right idlers for specific needs.
- Industry Guidelines: Industry organizations, such as the Conveyor Equipment Manufacturers Association (CEMA), publish guidelines and standards in PDF format that outline best practices for conveyor system design and maintenance. These documents provide authoritative insights into the proper selection and use of carrying idlers and other conveyor components.
- Technical White Papers: Technical white papers from engineering firms and research institutions offer in-depth analyses of conveyor idler performance and innovations. These papers often include case studies and experimental data, providing evidence-based recommendations for optimizing carrying idler belt conveyor systems.
- Maintenance Manuals: PDF maintenance manuals from equipment suppliers provide detailed instructions on how to maintain and troubleshoot idlers. These manuals cover routine inspection procedures, lubrication schedules, and common issues, helping to ensure the longevity and reliability of the conveyor system.
- Training Materials: Training materials in PDF format, such as those offered by professional development courses or industry workshops, can help operators and engineers gain a thorough understanding of idler functions and maintenance. These resources often include practical exercises and quizzes to reinforce learning.
By consulting these comprehensive PDF resources, operators and engineers can deepen their knowledge of carrying idler belt conveyor systems and make informed decisions about idler selection, installation, and maintenance. Understanding the different types of idlers and their specific functions is crucial for ensuring efficient and reliable conveyor operations, ultimately leading to improved productivity and reduced operational costs.
Dimensions and Specifications for Carrying Idler Belt Conveyor
The dimensions and specifications for carrying idler belt conveyors can vary depending on the specific application, the type of materials being transported, and the overall design requirements. Below is a general overview of the typical dimensions and specifications that are considered when designing or selecting a carrying idler belt conveyor system:
These dimensions and specifications should be adjusted according to the specific requirements of the operation, the nature of the material being conveyed, and the environmental conditions of the installation site. Proper selection and design ensure optimal performance and longevity of the conveyor system.
Importance of Dimensions and Specifications for Carrying Idlers
In a carrying idler belt conveyor system, the dimensions and specifications of carrying idlers are critical factors that influence the overall performance and efficiency of the conveyor. These parameters determine how well the idlers support the conveyor belt, handle loads, and maintain belt alignment.
- Roller Diameter: The diameter of the rollers in carrying idlers affects the load-bearing capacity and the speed at which the belt can operate. Larger diameter rollers can handle heavier loads and reduce the stress on the bearings, which enhances the durability of the idlers. Conversely, smaller diameter rollers are suitable for lighter loads and can help achieve higher belt speeds, but they may wear out faster under heavy use.
- Roller Length: The length of the rollers must match the width of the conveyor belt to provide adequate support. If the rollers are too short, they will not fully support the belt, leading to potential sagging and misalignment. Conversely, rollers that are too long can create unnecessary friction and increase the wear on both the belt and the idlers. Proper roller length ensures even distribution of the load across the belt, maintaining stability and efficiency.
- Bearing Type and Size: Bearings are crucial components of carrying idlers, and their specifications, including type and size, determine the idler’s performance. High-quality bearings with appropriate load ratings can handle the stresses of heavy-duty operations and reduce maintenance needs. Sealed bearings are often preferred for harsh environments as they protect against dust and moisture, ensuring smoother operation and longer service life.
- Frame Dimensions: The frame that holds the rollers must be sturdy and properly dimensioned to ensure stability and alignment. Frames that are too weak or improperly sized can lead to misalignment of the rollers, causing increased wear on the belt and reducing the overall efficiency of the conveyor system. Properly dimensioned frames ensure that the rollers remain in alignment and provide consistent support to the belt.
- Troughing Angle: The troughing angle of the carrying idlers affects how the belt forms a trough shape, which is critical for transporting bulk materials. A higher troughing angle can increase the capacity of the belt by allowing it to carry more material. However, it also requires more robust rollers and frames to handle the increased load. The correct troughing angle ensures optimal material handling while maintaining belt stability and minimizing spillage.
How These Specifications Impact the Performance and Efficiency of Belt Conveyors
The specifications of carrying idlers in a carrying idler belt conveyor system directly impact the system’s performance and efficiency.
- Load-Bearing Capacity: The dimensions and material specifications of carrying idlers determine their ability to support the weight of the conveyor belt and the materials being transported. Idlers with larger diameters and high-quality bearings can handle heavier loads, reducing the risk of belt sagging and misalignment. This capability is crucial for maintaining efficient operation and minimizing downtime due to belt maintenance or replacement.
- Belt Speed and Smoothness: The specifications of the rollers, including their diameter and surface finish, affect the speed at which the conveyor belt can operate. Smooth, properly sized rollers reduce friction and wear, allowing the belt to move more quickly and smoothly. This improvement in belt speed enhances overall productivity and ensures that materials are transported efficiently along the conveyor system.
- Durability and Maintenance: High-quality materials and precise specifications contribute to the durability of carrying idlers. Idlers with well-designed frames, robust rollers, and durable bearings require less frequent maintenance and have longer service lives. Reduced maintenance needs translate to lower operational costs and less downtime, improving the overall efficiency of the conveyor system.
- Energy Efficiency: Properly specified carrying idlers can reduce the amount of energy required to operate the conveyor system. Idlers that minimize friction and provide smooth support to the belt reduce the power needed to move the belt and its load. This energy efficiency not only lowers operational costs but also reduces the environmental impact of the conveyor system.
- Belt Alignment and Stability: The dimensions and alignment of carrying idlers are crucial for maintaining the proper alignment of the conveyor belt. Misaligned idlers can cause the belt to run off-track, leading to increased wear and potential damage. Properly specified idlers ensure that the belt remains centered and stable, reducing the risk of spillage and improving the overall reliability of the conveyor system.
The dimensions and specifications of carrying idlers are vital to the performance and efficiency of carrying idler belt conveyor systems. By selecting idlers with appropriate roller diameters, lengths, bearing types, frame dimensions, and troughing angles, operators can optimize their conveyor systems for better load-bearing capacity, smoother belt movement, enhanced durability, improved energy efficiency, and reliable belt alignment. Understanding these factors and their impact on conveyor operations is essential for designing and maintaining efficient and effective belt conveyor systems.
The Role of Return Carrying Idler Belt Conveyor
Comparative Analysis of Carrying and Return Idlers
Carrying idlers and return idlers are both essential components of a carrying idler belt conveyor system. While they serve different purposes, both types of idlers contribute to the overall efficiency and stability of the conveyor. Below is a comparative analysis of carrying and return idlers summarized in a table:
Significance of Return Idlers in Maintaining Belt Stability and Efficiency
Return idlers play a crucial role in the overall performance of carrying idler belt conveyor systems. They ensure that the empty conveyor belt returns smoothly to the loading point, maintaining stability and efficiency.
- Maintaining Belt Alignment: Return idlers help keep the conveyor belt aligned as it travels back to the loading point. Properly aligned return idlers prevent the belt from drifting or veering off track, which can cause excessive wear and tear. This alignment is essential for the continuous and efficient operation of the conveyor system, reducing the risk of downtime due to belt misalignment issues.
- Reducing Belt Wear: By supporting the empty belt and keeping it aligned, return idlers help to reduce the wear and tear on the belt. This reduction in wear extends the life of the conveyor belt, lowering maintenance costs and minimizing operational disruptions. Properly maintained return idlers ensure that the belt remains in good condition, even after prolonged use.
- Enhancing Energy Efficiency: Properly aligned return idlers reduce the drag on the conveyor belt as it returns to the loading point. This reduction in drag decreases the amount of energy required to move the belt, resulting in lower energy consumption and reduced operational costs. Energy-efficient conveyor systems are not only cost-effective but also environmentally friendly, as they reduce the overall carbon footprint of the operation.
- Supporting Belt Tension: Return idlers help to maintain the appropriate tension in the conveyor belt. Proper belt tension is critical for the efficient operation of the conveyor system, as it ensures smooth movement and prevents slippage. Return idlers that maintain consistent tension help to optimize the performance of the carrying idler belt conveyor system, improving productivity and reliability.
- Preventing Material Buildup: In some conveyor systems, material buildup on the return side of the belt can cause operational issues and increase wear. Return idlers are designed to minimize material buildup by providing consistent support and alignment for the empty belt. This reduction in material buildup helps to maintain a clean and efficient conveyor system, reducing the need for frequent cleaning and maintenance.
Return idlers are essential components of carrying idler belt conveyor systems. They play a significant role in maintaining belt stability and efficiency by ensuring proper alignment, reducing wear, enhancing energy efficiency, supporting belt tension, and preventing material buildup. By understanding the importance of return idlers and their contribution to the overall performance of the conveyor system, operators can ensure the reliable and efficient operation of their carrying idler belt conveyors.
Selection Criteria for Types of Carrying Idler Belt Conveyor
Factors to Consider When Choosing Idlers for Belt Conveyors
Selecting the appropriate idlers for a carrying idler belt conveyor system is crucial for ensuring optimal performance and longevity. Various factors must be considered to make the right choice.
- Load Capacity: The load capacity of the idlers must match the weight of the materials being transported. Carrying idlers need to support the full weight of the conveyor belt and its load, whereas return idlers only need to support the empty belt. Overloading idlers beyond their capacity can lead to premature failure and increased maintenance costs. It is important to consider the material density, belt width, and the maximum load per unit length when selecting idlers.
- Environmental Conditions: The operating environment plays a significant role in the selection of idlers. Factors such as temperature, humidity, exposure to chemicals, and the presence of abrasive materials can impact the performance and lifespan of idlers. For example, idlers used in corrosive environments should be made of materials that resist corrosion, such as stainless steel or coated metals. In extremely cold or hot environments, idlers with materials designed to withstand such temperatures should be chosen.
- Belt Speed: The speed at which the conveyor belt operates affects the type of idlers required. High-speed belts generate more friction and heat, requiring idlers with robust bearings and materials that can handle the increased wear and thermal stress. Conversely, slower belts may not require such heavy-duty idlers. Ensuring that the idlers can accommodate the operational speed of the belt is crucial for maintaining efficiency and reducing wear.
- Troughing Angle: The troughing angle of carrying idlers affects the belt’s capacity to transport materials. Different applications may require different troughing angles to optimize the belt’s load-carrying ability. For instance, a higher troughing angle can increase the belt’s capacity to carry bulk materials by creating a deeper trough. However, this also means that the idlers and frames must be designed to support the increased load. Selecting the appropriate troughing angle based on the material being conveyed is essential for maximizing efficiency.
- Maintenance Requirements: The ease of maintenance and availability of replacement parts should be considered when selecting idlers. Idlers that require frequent maintenance can increase operational costs and downtime. Choosing idlers with high-quality bearings and durable materials can reduce maintenance frequency and extend the lifespan of the idlers. Additionally, selecting idlers from reputable manufacturers with readily available replacement parts can simplify maintenance and reduce downtime.
Impact of Different Types of Idlers on Conveyor Performance
The type of idlers used in a carrying idler belt conveyor system significantly impacts its performance. Different idlers are designed for specific functions and choosing the right type is crucial for achieving optimal conveyor operation.
- Carrying Idlers: Carrying idlers are essential for supporting the loaded belt and maintaining its alignment. Flat carrying idlers are suitable for light to medium loads and provide a flat surface for the belt. Troughing carrying idlers, which create a trough shape, are ideal for transporting bulk materials, as they help center the load and prevent spillage. Impact carrying idlers, with shock-absorbing rollers, are used at loading points to cushion the impact of heavy materials, reducing belt wear and extending its lifespan.
- Return Idlers: Return idlers support the empty belt on its return journey to the loading point. Flat return idlers provide a flat surface for the belt, ensuring it stays aligned and reducing wear. V-return idlers, with rollers arranged in a V-shape, help to center the belt and prevent it from wandering, especially on longer conveyor runs. Properly selected return idlers minimize drag and reduce energy consumption, enhancing the overall efficiency of the conveyor system.
- Self-Aligning Idlers: Self-aligning idlers automatically correct belt misalignment, ensuring the belt remains centered. Troughing self-aligning idlers are used on the carrying side to handle misalignment during the transportation of bulk materials. Return self-aligning idlers are placed on the return side to maintain belt alignment during its return journey. These idlers are crucial for preventing tracking issues and reducing wear on the belt and other components.
- Training Idlers: Training idlers guide the belt and ensure it runs true along the conveyor path. They can be manually adjusted to correct belt alignment and are often used in conjunction with self-aligning idlers. Properly adjusted training idlers help prevent belt misalignment, reducing wear and operational disruptions.
- Transition Idlers: Transition idlers are placed where the belt changes from a flat profile to a trough profile or vice versa. These idlers help to gradually transition the belt, reducing stress and preventing material spillage. Properly selected transition idlers ensure smooth transitions and maintain the belt’s stability and efficiency.
The selection criteria for types of idlers in carrying idler belt conveyor systems involve careful consideration of load capacity, environmental conditions, belt speed, troughing angle, and maintenance requirements. The impact of different types of idlers on conveyor performance underscores the importance of choosing the right idlers for specific applications. By understanding these factors and their implications, operators can ensure efficient, reliable, and long-lasting conveyor operations.
FAQs About Carrying Idler Belt Conveyor
A carrying idler is a component of a belt conveyor system designed to support the conveyor belt and the material being transported. These idlers are positioned on the carrying side of the conveyor belt, ensuring the belt remains flat and prevents sagging under the load’s weight. Carrying idlers are essential for maintaining the belt’s alignment and reducing wear and tear, thus extending the belt’s lifespan. They typically consist of a series of rollers arranged in a horizontal row, which provide a stable surface for the belt. Carrying idlers come in various types, including flat, troughing, and impact idlers, each suited for different operational needs and material handling requirements.
Idlers for belt conveyors are cylindrical components that support and guide the conveyor belt as it moves. They are crucial for maintaining the belt’s alignment and ensuring smooth, efficient operation. Idlers can be found on both the carrying side, where they support the loaded belt, and the return side, where they support the empty belt returning to the loading point. The main functions of idlers include reducing friction, preventing belt sagging, and minimizing wear and tear on the belt. Idlers come in various types, such as carrying idlers, return idlers, self-aligning idlers, and training idlers, each serving specific roles within the conveyor system to enhance performance and reliability.
The distance between carrying idlers, also known as the idler spacing, depends on several factors, including the load being transported, the belt width, and the type of material being conveyed. Typically, carrying idlers are spaced closer together for heavy loads to provide adequate support and prevent the belt from sagging. For lighter loads, the spacing can be increased. Standard idler spacing ranges from 1 meter to 1.5 meters (approximately 3 to 5 feet). Proper idler spacing is crucial for maintaining belt stability and ensuring even load distribution across the conveyor belt. Incorrect spacing can lead to increased wear on the belt and idlers, reducing the system’s overall efficiency and lifespan.
Conveyor idlers come in various types, each designed for specific functions within a belt conveyor system. The primary types include:
Carrying Idlers: Positioned on the carrying side of the belt, these idlers support the loaded belt and prevent sagging. They include flat carrying idlers for light to medium loads, troughing carrying idlers for bulk materials, and impact carrying idlers for cushioning heavy material drops.
Return Idlers: These idlers support the empty belt on its return journey. Flat return idlers provide a flat surface, while V-return idlers help center the belt and prevent wandering.
Self-Aligning Idlers: These idlers automatically correct belt misalignment. They come in troughing and return types, ensuring the belt remains centered and reducing wear.
Training Idlers: Manually adjustable idlers used to guide and correct belt alignment, often working alongside self-aligning idlers.
Transition Idlers: Placed where the belt changes from a flat to a trough profile, these idlers ensure smooth transitions and reduce stress on the belt.
Each type of idler plays a crucial role in maintaining the efficiency and reliability of a carrying idler belt conveyor system, contributing to optimal material handling and reduced operational downtime.
The idler in a belt conveyor supports the conveyor belt and the materials carried on it, reducing friction and wear while guiding the belt along the intended path.
Yes, conveyor belts need to be guarded to protect workers from moving parts, pinch points, and other potential hazards, ensuring safe operation in compliance with safety regulations.
The purpose of the belt idler is to provide support to the conveyor belt, reduce sagging, and ensure smooth and efficient operation by maintaining proper belt alignment and tension.
The number of idlers a conveyor belt has depends on the length of the conveyor and the design specifications, with idlers typically spaced at regular intervals along the entire length of the conveyor.
A carrying idler supports the loaded section of the conveyor belt, while an impact idler is positioned at loading points to absorb the impact from material falling onto the belt, reducing wear and tear.
The factor of safety for a conveyor belt typically ranges from 6:1 to 10:1, depending on the application and design standards, ensuring the belt can handle the required loads without risk of failure.
Last Updated on August 9, 2024 by Jordan Smith
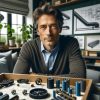
Jordan Smith, a seasoned professional with over 20 years of experience in the conveyor system industry. Jordan’s expertise lies in providing comprehensive solutions for conveyor rollers, belts, and accessories, catering to a wide range of industrial needs. From initial design and configuration to installation and meticulous troubleshooting, Jordan is adept at handling all aspects of conveyor system management. Whether you’re looking to upgrade your production line with efficient conveyor belts, require custom conveyor rollers for specific operations, or need expert advice on selecting the right conveyor accessories for your facility, Jordan is your reliable consultant. For any inquiries or assistance with conveyor system optimization, Jordan is available to share his wealth of knowledge and experience. Feel free to reach out at any time for professional guidance on all matters related to conveyor rollers, belts, and accessories.