Conveyor Belt Carrying Idler Roller
Carrying idler roller is fundamental components of conveyor systems, designed to support the conveyor belt and the materials it transports. Positioned strategically along the length of the conveyor, these rollers ensure the belt remains in a continuous, smooth motion, preventing any sagging or misalignment that could disrupt the transportation process. The role of carrying idlers extends beyond merely supporting the belt; they play a crucial part in maintaining the efficiency and longevity of the conveyor system by reducing the friction between the belt and the conveyor frame. This not only facilitates the seamless movement of goods but also significantly minimizes wear and tear on the belt, thereby extending its service life. The importance of carrying idler rollers cannot be overstated, as they are key to the reliable and effective operation of conveyor systems in various industries.
What Are the Components of Carrying Idler Roller
In the realm of conveyor systems, the carrying idler roller plays a pivotal role, ensuring the smooth operation and longevity of the conveyor belt. Delving into the components that make up this essential part of the conveyor system reveals a complex interplay of engineering and design. Here are six critical components, each contributing uniquely to the conveyor’s functionality:
Carrying Idler Frame: The carrying idler frame is the backbone that supports the carrying idler rollers. This sturdy structure is crucial for maintaining the conveyor belt’s alignment, ensuring it remains straight and true during operation. The frame’s design and construction material are tailored to withstand the conveyor system’s environmental and operational demands, providing a stable base for the rollers and, by extension, the conveyor belt.
Carrier Conveyor Roller Idler: Within the carrying idler frame lies the carrier conveyor roller idler, a cylindrical component that directly supports and propels the conveyor belt. These rollers are designed to minimize friction and facilitate the belt’s smooth movement, crucial for transporting materials efficiently. The variety in roller types—ranging from smooth to textured surfaces—allows for customization based on the specific needs of the conveyor system, such as material type and weight.
Return Idler Roller: Contrasting with the carrying idler rollers, the return idler roller functions on the underside of the conveyor belt. This component supports the belt as it returns to the starting point after offloading its materials. The return idler differs in design from the carrying idler, often featuring a simpler structure, as it does not bear the direct weight of the transported materials. This distinction is vital for optimizing the conveyor system’s efficiency and cost-effectiveness.
Impact Idler Roller: Designed to absorb the shock and impact of heavy materials when they are loaded onto the conveyor, impact idler rollers are typically located at the loading points. These rollers have a robust construction and are often equipped with a rubber coating to cushion the impact, protecting both the conveyor belt and the structure from damage.
Guide Idler Roller: Guide idler rollers are strategically placed to ensure the conveyor belt remains centered and does not drift laterally during operation. These rollers are pivotal in preventing the belt from slipping off the conveyor’s frame, which could lead to significant operational disruptions and potential damage to the belt and the system.
Self-Aligning Carrying Idler: The self-aligning carrying idler is engineered to automatically correct any misalignment of the conveyor belt. This component is particularly beneficial in long conveyor systems where belt misalignment could lead to uneven wear, increased maintenance costs, and downtime. The self-aligning feature ensures the belt consistently runs in the center, enhancing the conveyor system’s reliability and efficiency.
Each of these components plays a specific role in the functionality and efficiency of a conveyor system, with the carrying idler roller at the heart of ensuring smooth and effective material transport. Understanding these components and their interrelations is crucial for optimizing conveyor performance and longevity.
Types of Carrying Idler Roller
The carrying idler roller is an indispensable component of the conveyor system, with various types designed to meet specific operational needs. Each type of carrying idler has unique features and benefits, tailored to enhance conveyor performance and efficiency.
Standard Carrying Idlers
Standard carrying idlers are the most prevalent in belt conveyor systems, characterized by their simple yet effective design. These idlers typically feature:
- A series of cylindrical rollers set in a frame to support the conveyor belt.
- Rollers made from durable materials like steel or high-density polyethylene for longevity.
- A design that facilitates easy installation and maintenance.
- Compatibility with a wide range of belt widths and speeds.
- The ability to operate in various environmental conditions, from dry to moderately humid.
- An even distribution of load across the conveyor belt, reducing wear and tear.
- A smooth surface to minimize friction and belt wear.
- Adaptability to both flat and troughed belt designs, enhancing versatility.
Impact Idlers
Impact idlers are specifically engineered to withstand the forces exerted by heavy materials as they are loaded onto the conveyor belt. These idlers are distinguished by:
- A robust construction that absorbs and dissipates the energy from falling materials.
- Placement at critical points along the conveyor, typically at loading zones.
- Rollers equipped with a thick, shock-absorbing layer, often made of rubber.
- A design that reduces the risk of belt damage from impact.
- Enhanced durability to withstand repeated shocks without deforming.
- The ability to significantly extend the life of the conveyor belt.
- A contribution to smoother operation by stabilizing the belt’s motion.
- A reduction in maintenance costs associated with belt damage.
- Compatibility with heavy-duty applications in industries like mining and construction.
Self-aligning Carrying Idlers
Self-aligning carrying idlers are designed to automatically correct any misalignment of the conveyor belt, characterized by:
- A pivoting action that gently steers the belt back to its central path.
- Installation at strategic intervals along the conveyor to ensure continuous alignment.
- A mechanism that responds to belt movement, activating the self-aligning feature.
- The ability to prevent material spillage caused by belt misalignment.
- A reduction in the wear and tear on edges of the conveyor belt.
- Compatibility with both single-direction and reversible conveyor systems.
- A design that minimizes the need for manual belt adjustments.
- Essential for long-distance conveyors where alignment issues are more prevalent.
Specialized Idler Rollers
Specialized idler rollers are designed for specific applications, offering solutions to unique conveyor challenges. These include:
- Rubber-Coated Idlers: Featuring a rubber coating for extra grip and noise reduction, ideal for slippery or wet materials.
- Tapered Idlers: Used in curved sections of conveyors to maintain belt alignment.
- Guide Rollers: Positioned on the sides of the conveyor belt to prevent lateral movement.
- Spiral Rollers: Designed to clean the belt and reduce material buildup on the roller surface.
- Adjustable Idlers: Allowing for changes in the angle to control belt tracking.
- High-Temperature Idlers: Constructed from materials that can withstand extreme temperatures, suitable for heat-treating processes.
- Anti-Corrosive Idlers: Made from materials resistant to corrosion, ideal for chemical processing environments.
- Impact Troughing Idlers: Combining the features of impact idlers with a troughing design to support heavy loads in a troughed belt configuration.
Each type of carrying idler roller serves a specific purpose, contributing to the efficiency, safety, and longevity of conveyor systems across various industries. Understanding the distinct features and applications of these idlers is crucial for optimizing conveyor performance and selecting the right components for specific operational needs.

The Size of Carrying idler roller
The size of a carrying idler roller can vary based on its application and the specifications required for a particular conveyor system. However, there are common sizes and dimensions used in the industry. Here are some typical sizes:
Diameter:
- Small diameter: 63.5 mm (2.5 inches)
- Medium diameter: 127 mm (5 inches)
- Large diameter: 152.4 mm (6 inches)
Length:
- Common lengths range from 300 mm (11.8 inches) to 1800 mm (70.9 inches), depending on the width of the conveyor belt and the load it needs to carry.
Shaft Diameter:
- Typically ranges from 20 mm (0.8 inches) to 40 mm (1.6 inches).
Bearing Size:
- Depends on the shaft diameter and load requirements but typically ranges from 6204 (20 mm bore) to 6310 (50 mm bore).
These sizes are indicative, and the actual dimensions can vary based on specific design requirements and industry standards. If you have a specific application or need precise measurements, providing those details will help in determining the exact size of the carrying idler roller.
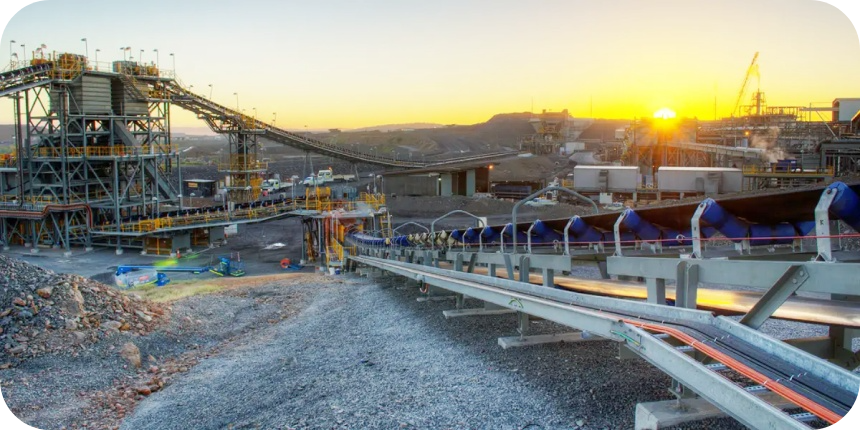
The 3 Most Common Conveyor Carrying Idler Roller
Conveyor idlers are essential components in conveyor systems, providing support and facilitating smooth movement of the conveyor belt. Here are the five most common types of conveyor idlers:
Carrying Idlers:
- Function: Support the loaded belt and material.
- Common Use: Found along the length of the conveyor, these idlers support the conveyor belt and the material being transported.
- Design Variants: Can be flat or troughed (usually 20°, 35°, or 45° trough angles).
Return Idlers:
- Function: Support the empty belt on its return journey after the discharge point.
- Common Use: Placed on the underside of the conveyor belt to prevent sagging.
- Design Variants: Can be flat or vee-shaped.
Transition Idlers:
- Function: Provide smooth transition between different sections of the conveyor belt, particularly at the head and tail ends.
- Common Use: Placed where the belt transitions from a flat to a troughed profile or vice versa.
- Design Variants: Usually adjustable to accommodate varying troughing angles.
These idlers play crucial roles in ensuring the efficient and reliable operation of conveyor systems by supporting the belt, reducing friction, and aiding in proper alignment.

The Functions of Carrying Idler Rollers
Carrying idler rollers serve several essential functions in a conveyor system. Here are the primary functions of carrying idler rollers:
Supporting the Conveyor Belt:
- Carrying idler rollers support the conveyor belt along its length, ensuring it remains flat and stable as it moves.
Supporting the Load:
- These rollers bear the weight of the material being transported on the conveyor belt, preventing the belt from sagging and maintaining an even distribution of the load.
Reducing Friction:
- By providing a rolling surface for the conveyor belt, carrying idler rollers reduce friction between the belt and the conveyor structure, which helps in reducing wear and tear on the belt and improving energy efficiency.
Guiding the Belt:
- Properly aligned carrying idler rollers help guide the conveyor belt and maintain its path, preventing misalignment and potential spillage of materials.
Absorbing Impact:
- Although this is more commonly associated with impact idlers, carrying idler rollers also play a role in absorbing minor impacts and vibrations from the transported materials, contributing to the overall smooth operation of the conveyor system.
Maintaining Belt Tension:
- Carrying idler rollers help maintain the proper tension in the conveyor belt, which is crucial for efficient operation and to avoid belt slippage or excessive wear.
Enhancing System Longevity:
- By supporting and stabilizing the conveyor belt and load, carrying idler rollers contribute to the longevity and reliability of the entire conveyor system.
Overall, carrying idler rollers are critical components that ensure the smooth, efficient, and reliable operation of conveyor systems by providing support, reducing friction, and maintaining proper belt alignment and tension.
Selection and Application of Carrying Idler Roller
The selection and application of carrying idler rollers are critical to the efficiency, safety, and longevity of conveyor systems. Understanding the nuances of these components can significantly impact the operational success of conveyor systems.
Choosing the Right Type of Carrying Idler Roller
Selecting the appropriate carrying idler roller involves considering various factors to ensure compatibility with the conveyor’s operational demands:
- Material Type: The nature of the material being conveyed (e.g., abrasive, corrosive, sticky) can dictate the choice of idler material and coating.
- Load Size: Heavier loads require more robust idlers designed to withstand increased weight without deformation.
- Conveyor Length: Longer conveyors may need specialized idlers like self-aligning idlers to maintain belt alignment.
- Belt Speed: Higher speeds may necessitate idlers with precision bearings to reduce friction and heat buildup.
- Operating Environment: Conditions such as temperature, humidity, and exposure to chemicals can affect idler material selection.
- Impact Zones: Areas where material is dropped onto the belt might need impact idlers to absorb the force and protect the belt.
- Trough Angle: The angle of the idler sets can influence the belt’s capacity to carry materials and must match the conveyor design.
- Maintenance Accessibility: Ease of maintenance and replacement can lead to the selection of certain idler types over others.
- Cost and Lifespan: Balancing upfront costs with expected service life and maintenance requirements is crucial for cost-effective operations.
Carrying Idler Belt Conveyor Integration
Integrating carrying idlers into belt conveyor systems is pivotal for optimizing performance:
- Support and Stability: They provide a stable platform for the conveyor belt, ensuring smooth operation.
- Load Distribution: Properly spaced idlers distribute the load evenly, preventing belt sag and material spillage.
- Reduced Belt Wear: By minimizing friction and belt movement, idlers extend the life of the conveyor belt.
- Energy Efficiency: Efficient idlers reduce the power required to move the belt, lowering energy costs.
- Safety: Well-designed idler installations prevent accidents and reduce the risk of belt misalignment.
- Noise Reduction: Quality idlers can decrease operational noise, contributing to a better working environment.
- Versatility: Idlers can be adapted to various conveyor configurations, enhancing system flexibility.
- Compliance: Meeting industry standards and regulations is facilitated by using appropriate idlers.
Installation and Maintenance of Carrying Idler Roller
Proper installation and maintenance are paramount for the performance and longevity of carrying idler rollers:
- Correct Spacing: Idlers should be installed at intervals that prevent belt sag but avoid unnecessary stress.
- Alignment: Ensuring idlers are perfectly aligned with the conveyor frame prevents belt tracking issues.
- Secure Mounting: Idler frames must be securely attached to the conveyor structure to withstand operational forces.
- Lubrication: Regular lubrication of idler bearings, according to manufacturer recommendations, extends their life.
- Inspection Routines: Regular inspections can identify wear and tear before it leads to failure.
- Cleanliness: Keeping idlers clean from material buildup ensures they function correctly.
- Replacement Strategy: Having a strategy for replacing worn or damaged idlers minimizes downtime.
- Training: Personnel should be trained on the correct procedures for idler installation and maintenance.
- Documentation: Maintaining records of maintenance activities helps in planning and troubleshooting.
By carefully selecting, integrating, and maintaining carrying idler roller, conveyor systems can achieve optimal performance, safety, and reliability, ensuring the smooth and efficient transport of materials across various industries.

Purchasing and Replacement of Carrying Idler Roller
The procurement and timely replacement of carrying idler rollers are crucial for maintaining the efficiency and longevity of conveyor systems. Understanding the nuances of purchasing and replacing these components can significantly impact the operational success of conveyor systems.
Used Carrying Idler Rollers
When considering the purchase of used carrying idler rollers, it’s essential to evaluate several factors to ensure they meet your operational requirements:
- Wear and Tear: Assess the extent of wear on the rollers and frames, looking for signs of excessive wear or damage.
- Compatibility: Verify that the used idlers are compatible with your conveyor system in terms of size, type, and load capacity.
- Operational History: Inquire about the operational history of the idlers, including the type of materials they have conveyed and the environment they were used in.
- Maintenance Records: Request maintenance records to understand how well the idlers were maintained and to identify any recurring issues.
- Manufacturer and Model: Ensure the idlers are from a reputable manufacturer and that replacement parts are readily available.
- Inspection: Conduct a thorough inspection, preferably in person, to check for any defects or potential failure points.
- Refurbishment: Determine if the idlers have been refurbished by a credible source and to what extent.
- Warranty: Look for a warranty or guarantee from the seller, providing some assurance of the idlers’ reliability.
- Cost-Benefit Analysis: Weigh the cost savings against the potential risk of increased maintenance or shorter lifespan compared to new idlers.
Carrying Idler Rollers for Sale
Finding quality carrying idler rollers for sale, whether new or refurbished, requires considering various sources and factors:
- Manufacturer Direct: Purchasing directly from the manufacturer ensures authenticity and access to the latest models and technology.
- Authorized Distributors: These entities often offer a wide range of products from various manufacturers, along with expert advice.
- Online Marketplaces: Platforms like Alibaba and Amazon Business can be sources for both new and used idlers, offering competitive pricing.
- Industry Trade Shows: These events provide opportunities to see products firsthand and to network with manufacturers and distributors.
- Refurbished Equipment Dealers: Specialized in refurbished conveyor components, these dealers can offer cost-effective solutions.
- Auction Sites: Industrial auction sites may list high-quality carrying idler rollers at reduced prices.
- Peer Recommendations: Recommendations from industry peers can lead to trusted suppliers of carrying idler rollers.
- Technical Specifications: Ensure the idlers meet the specific technical requirements of your conveyor system.
- After-Sales Support: Consider the level of after-sales support offered, including availability of spare parts and technical assistance.
Whether opting for used or new carrying idler rollers, thorough research and consideration of the above points can lead to informed purchasing decisions, ensuring the chosen idlers meet the operational demands and contribute to the efficient running of conveyor systems.
Have questions about our conveyor rollers? Reach out today!
Advanced Topics in Carrying Idler Roller Technology
Exploring advanced topics in carrying idler roller technology unveils the depth of innovation and research dedicated to enhancing conveyor system efficiency and reliability. These discussions not only highlight the technical advancements but also provide insights into the future direction of conveyor system components.
Types of Idlers PDF
Technical documents and PDF resources play a crucial role in disseminating detailed information about carrying idler rollers, offering:
- Comprehensive Overviews: Detailed descriptions of various idler types, including their design principles and intended applications.
- Specification Sheets: Precise measurements, material compositions, and performance ratings that aid in selecting the appropriate idler for specific conveyor needs.
- Installation Guides: Step-by-step instructions on the correct installation procedures to ensure optimal performance and longevity.
- Maintenance Manuals: Best practices for routine maintenance, troubleshooting tips, and replacement guidelines to maximize idler lifespan.
- Case Studies: Real-world applications demonstrating the effectiveness of different idler types in various industrial settings.
- Research Papers: Cutting-edge research on material science and mechanical engineering that informs the development of more efficient idlers.
- Regulatory Standards: Information on industry standards and regulations that idler designs must comply with for safety and performance.
- Innovation Highlights: Insights into new materials and technologies being incorporated into idler designs to address specific conveyor challenges.
- Supplier Catalogs: Comprehensive listings from manufacturers showcasing their range of idlers, including custom and standard options.
Innovations in Carrying Idler Design
Recent advancements in carrying idler roller technology have focused on enhancing energy efficiency, reducing operational noise, and improving durability, including:
- Energy-Efficient Bearings: Development of low-friction bearings that reduce energy consumption by minimizing the resistance the conveyor motor must overcome.
- Noise-Reducing Materials: Use of materials and designs that absorb vibration and reduce the noise generated by the rollers, contributing to a safer and more pleasant working environment.
- High-Durability Coatings: Application of advanced coatings that resist wear, corrosion, and material buildup, extending the idler’s service life even in harsh conditions.
- Self-Cleaning Designs: Innovations that prevent material buildup on the roller surface, maintaining optimal balance and reducing maintenance requirements.
- Smart Idlers: Integration of sensors and IoT technology to monitor idler performance in real-time, predicting failures before they occur and optimizing maintenance schedules.
- Eco-Friendly Materials: Use of sustainable materials in idler construction to reduce environmental impact without compromising performance.
- Modular Configurations: Designing idlers that can be easily modified or adjusted on-site to accommodate changes in conveyor operations or material types.
- Thermal Management: Innovations in materials and designs that dissipate heat more effectively, crucial for high-speed or high-load conveyors.
- Advanced Sealing Systems: Development of superior sealing mechanisms that protect bearings from contaminants, significantly extending the life of the idler in dirty or wet environments.
These advanced topics in carrying idler roller technology underscore the ongoing commitment to innovation within the conveyor industry, aiming to address evolving operational challenges and contribute to the overall efficiency and sustainability of material handling systems.

FAQs about Carrying Idler Roller
Carrying idlers, integral components of conveyor systems, serve the primary function of supporting the conveyor belt along with the materials it carries. These idlers are strategically placed along the length of the conveyor path and are pivotal in maintaining the stability and integrity of the conveyor belt’s movement. By providing a consistent and reliable support structure, carrying idlers prevent the conveyor belt from sagging, which could otherwise lead to uneven material distribution, potential spillage, and increased wear and tear on the belt. Furthermore, carrying idlers help to distribute the load evenly across the conveyor belt, enhancing the belt’s efficiency and longevity. Their design and spacing are critical factors that influence the conveyor system’s overall performance, ensuring smooth operation and minimizing downtime due to maintenance and repairs. In essence, carrying idlers are fundamental to the seamless operation of conveyor systems, facilitating the efficient transport of materials across various industries.
Idler rollers play a crucial role in conveyor systems by supporting the conveyor belt and facilitating its smooth movement. These cylindrical components are mounted on frames and are positioned at regular intervals along the conveyor path. The primary function of idler rollers is to provide a stable, rolling surface for the conveyor belt, which helps in the efficient transport of materials from one point to another. By reducing friction between the belt and the conveyor structure, idler rollers contribute to lower energy consumption and decreased wear on the belt, thereby extending its service life. Additionally, idler rollers help in maintaining the proper tension and alignment of the conveyor belt, preventing slippage and misalignment that could lead to operational disruptions. Depending on their placement and function within the conveyor system, idler rollers can be classified into different types, such as carrying idlers, return idlers, and impact idlers, each designed to meet specific operational needs and challenges.
The primary distinction between carrying idlers and impact idlers lies in their design and application within conveyor systems. Carrying idlers are designed to support the conveyor belt and the materials being transported along the length of the conveyor. These idlers are typically spaced evenly and provide a smooth surface for the belt to ride on, ensuring stability and preventing sagging.
On the other hand, impact idlers are specifically engineered to absorb the shock and impact of materials as they are loaded onto the conveyor belt. These idlers are usually installed at the loading points of the conveyor system, where materials are dropped from a height onto the belt. Impact idlers are constructed with robust materials and often feature a design that includes a series of cushioned rollers or discs. This design helps to dissipate the energy from falling materials, protecting the belt from damage and reducing the risk of belt deformation or failure.
While carrying idlers are used throughout the conveyor system to support the belt and materials, impact idlers are specialized components designed to withstand and absorb the high impact forces at material loading points, thereby safeguarding the conveyor belt and enhancing the system’s durability.
An idler on a conveyor system serves as a critical support component, ensuring the smooth and efficient operation of the conveyor belt. Idlers are cylindrical rollers that are mounted on frames and strategically placed along the conveyor path. Their primary function is to provide a stable and consistent support for the conveyor belt, helping to maintain its proper tension, alignment, and movement. This, in turn, facilitates the seamless transport of materials from one point to another within the system.
Idlers also play a significant role in reducing the friction between the conveyor belt and the structure of the conveyor system. By minimizing this friction, idlers contribute to lower operational energy costs and reduce the wear and tear on the belt, thereby extending its lifespan. Additionally, idlers help to prevent the conveyor belt from sagging between supports, which could lead to material spillage, uneven belt wear, and potential operational disruptions.
Depending on their specific placement and function, idlers can be categorized into various types, such as carrying idlers, return idlers, impact idlers, and self-aligning idlers, each designed to address different challenges and requirements within the conveyor system. Overall, idlers are indispensable to the functionality and efficiency of conveyor systems, playing a key role in the smooth and reliable transport of materials across diverse industrial applications.
A self-aligning carrying idler is a specialized type of conveyor idler designed to automatically correct the alignment of the conveyor belt during operation. It features a pivot mechanism that allows the idler to adjust its angle in response to the belt’s lateral movements, ensuring that the belt stays centered on the conveyor. This self-adjustment helps prevent belt misalignment, which can cause material spillage, increased wear on the belt and idlers, and potential downtime for maintenance. Self-aligning carrying idlers are typically used in areas where belt tracking issues are common, such as long conveyor systems or those with varying loads. By maintaining proper belt alignment, these idlers enhance the efficiency and longevity of the conveyor system, reducing maintenance costs and improving overall productivity.
Last Updated on August 9, 2024 by Jordan Smith
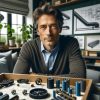
Jordan Smith, a seasoned professional with over 20 years of experience in the conveyor system industry. Jordan’s expertise lies in providing comprehensive solutions for conveyor rollers, belts, and accessories, catering to a wide range of industrial needs. From initial design and configuration to installation and meticulous troubleshooting, Jordan is adept at handling all aspects of conveyor system management. Whether you’re looking to upgrade your production line with efficient conveyor belts, require custom conveyor rollers for specific operations, or need expert advice on selecting the right conveyor accessories for your facility, Jordan is your reliable consultant. For any inquiries or assistance with conveyor system optimization, Jordan is available to share his wealth of knowledge and experience. Feel free to reach out at any time for professional guidance on all matters related to conveyor rollers, belts, and accessories.