Causes of Conveyor Belt Failure Issue
Conveyor belts play a critical role in industrial operations, facilitating the efficient and continuous movement of materials. However, when a conveyor belt fails, it can significantly disrupt productivity and pose serious safety risks. Understanding the causes of conveyor belt failure is essential to maintaining operational efficiency and ensuring a safe working environment. This blog post outlines the common issues that lead to belt failures, providing valuable insights for those looking to prevent such occurrences. By exploring the causes of conveyor belt failure, we aim to equip you with the knowledge needed to identify, address, and mitigate these problems effectively.
Conveyor Belt Failure Issues
Common Conveyor Belt Problems
- Misalignment: One of the most frequent issues is conveyor belt misalignment. This occurs when the belt strays from its intended path, causing it to rub against the conveyor structure. This friction can lead to severe wear and tear, reducing the belt’s lifespan and potentially causing it to snap.
- Slippage: Slippage happens when the conveyor belt does not move at the same speed as the rollers. This can be due to improper tension, worn-out drive pulleys, or excessive load. Slippage reduces the conveyor’s efficiency and can lead to product loss or damage.
- Material Spillage: Material spillage occurs when the transported goods spill over the sides of the conveyor belt. This can result from overloaded belts, improper loading techniques, or belt misalignment. Spillage not only leads to material loss but also poses a safety hazard by creating slip and trip risks.
- Belt Wear and Tear: Conveyor belts are subjected to constant use, and over time, they experience wear and tear. This can be due to various factors, including abrasive materials, heavy loads, and environmental conditions. Regular inspection and maintenance are necessary to identify signs of wear early and replace the belt before it fails.
- Belt Tracking Issues: Proper belt tracking is essential for the smooth operation of conveyor belts. Tracking issues arise when the belt does not run in a straight line along the conveyor structure. This can cause the belt to drift to one side, leading to uneven wear and potential failure.
- Belt Mistracking:This occurs when the conveyor belt does not follow its intended path.
- Excessive Noise:This occurs when materials fall off the conveyor belt.
Common Issues Addressed in the Resource
To help industries tackle these problems, the “Conveyor Belt Problems and Solutions” resource provides detailed insights and practical solutions.
- Misalignment Solutions: The resource offers strategies to correct and prevent misalignment, such as adjusting the conveyor structure, using alignment tools, and regular monitoring. It emphasizes the importance of ensuring that the belt runs centrally and evenly to avoid excessive wear.
- Slippage Prevention: To prevent slippage, the resource suggests maintaining proper belt tension, using high-quality drive pulleys, and ensuring that the conveyor is not overloaded. It also recommends regular maintenance checks to identify and rectify potential slippage causes before they lead to significant issues.
- Spillage Control: The resource provides guidelines on preventing material spillage, such as proper loading techniques, using side guards, and ensuring the belt is adequately aligned. It highlights the importance of training personnel on correct loading methods to minimize spillage risks.
- Wear and Tear Management: To manage wear and tear, the resource suggests using durable belt materials, implementing regular inspection schedules, and replacing worn-out belts promptly. It also recommends keeping the conveyor system clean and free from debris that can cause abrasion.
- Belt Tracking Solutions: The resource offers various methods to address belt tracking issues, including adjusting the conveyor rollers, using tracking devices, and ensuring the conveyor structure is level. It stresses the importance of regular monitoring and adjustment to maintain proper belt alignment.
By understanding these common problems and implementing the suggested solutions, industries can significantly reduce the risk of conveyor belt failures. This proactive approach not only enhances operational efficiency but also ensures a safer working environment. Identifying and addressing the causes of conveyor belt failure is a critical aspect of maintaining a reliable and efficient conveyor system.
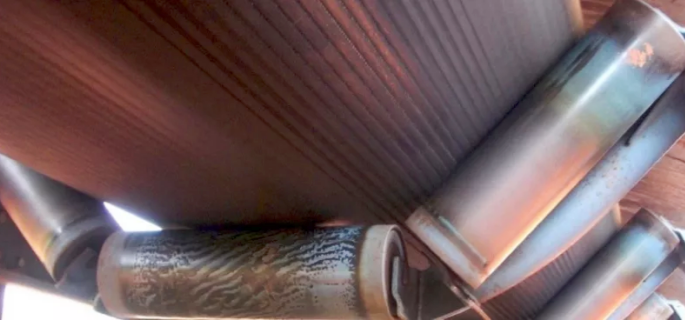
The Importance of Identifying Common Conveyor Belt Problems
In industrial operations, conveyor belts are vital for transporting materials efficiently and reliably. However, they are susceptible to a variety of problems that can cause significant disruptions if not addressed promptly. Identifying these common problems is crucial for maintaining productivity and ensuring safety. By understanding and diagnosing these issues early, industries can implement effective solutions to prevent further damage and costly downtime.
Recognizing the causes of conveyor belt failure is fundamental to this process. When operators can pinpoint the root causes, they are better equipped to take corrective actions and put preventive measures in place. This proactive approach not only enhances operational efficiency but also extends the lifespan of the conveyor belts, leading to significant cost savings.
Identifying common conveyor belt problems is crucial for several reasons. Here are some of the primary benefits and importance of doing so:
1. Minimizing Downtime
- Explanation: Conveyor belt systems are often critical components in production and material handling processes. Unplanned downtime can halt production lines and disrupt operations.
- Impact: Early identification of issues helps in scheduling maintenance during planned downtimes, thus avoiding unexpected production halts.
2. Enhancing Safety
- Explanation: Conveyor belt failures can pose significant safety hazards to workers. Problems like belt mistracking or spillage can lead to accidents.
- Impact: Identifying and addressing potential issues reduces the risk of accidents, ensuring a safer working environment.
3. Extending Equipment Lifespan
- Explanation: Regularly identifying and fixing common problems prevents minor issues from escalating into major failures.
- Impact: This proactive approach can significantly extend the lifespan of the conveyor belt and related components, providing better return on investment.
4. Improving Efficiency
- Explanation: Conveyor belts running smoothly and efficiently are vital for optimal production processes.
- Impact: Identifying and resolving common issues ensures that the conveyor operates at peak efficiency, improving overall productivity.
5. Cost Savings
- Explanation: Major repairs and replacements are more expensive than regular maintenance.
- Impact: By identifying problems early, companies can save on costs associated with extensive repairs, part replacements, and production downtime.
6. Maintaining Product Quality
- Explanation: Conveyor belt issues can affect the quality of the products being transported.
- Impact: Ensuring the conveyor operates correctly helps maintain consistent product quality and reduces the risk of damage or contamination.
7. Preventing Environmental Impact
- Explanation: Spillage and leakage from conveyor belts can lead to environmental contamination.
- Impact: Identifying and addressing these issues promptly helps in maintaining environmental compliance and reducing the risk of pollution.
8. Ensuring Regulatory Compliance
- Explanation: Many industries are subject to strict health and safety regulations.
- Impact: Regularly identifying and rectifying conveyor belt issues helps ensure compliance with relevant regulations, avoiding fines and legal issues.
9. Boosting Employee Morale
- Explanation: A well-maintained system reduces the frequency of breakdowns and the associated stress.
- Impact: A reliable working environment contributes to higher employee morale and job satisfaction.
Strategies for Identifying Common Problems
- Regular Inspections: Schedule routine inspections to spot wear and tear, misalignments, and other issues.
- Condition Monitoring: Implement technology like sensors and monitoring systems to detect potential failures early.
- Employee Training: Train employees to recognize signs of common problems and report them promptly.
- Maintenance Logs: Keep detailed maintenance logs to track recurring issues and address root causes effectively.Types of Conveyor Belt Damage and Causes of Conveyor Belt Failure
By proactively identifying and addressing common conveyor belt problems, companies can ensure smoother operations, higher productivity, and a safer working environment.
Types of Conveyor Belt Damage and Causes of Conveyor Belt Failure
Understanding the conveyor belt damage causes requires a comprehensive examination of the different types of damage that can affect conveyor belts. Damage can arise from various factors, each leading to potential system failures if not addressed promptly. Causes of conveyor belt failure issues such as improper idler spacing, seized or worn rollers, misaligned frames, and material buildup.This section delves into the common forms of conveyor belt damage and explains how such damage can escalate into more significant operational issues.
Various Forms of Conveyor Belt Damage
- Abrasion and Wear:
Abrasion is one of the most common types of conveyor belt damage. It occurs when the belt surface is worn down due to continuous friction with the materials being transported. Over time, abrasive materials can erode the belt, leading to thinning and eventual tears. For example, carrying sharp or coarse materials like gravel or minerals can accelerate wear and tear on the belt, reducing its lifespan and efficiency. - Impact Damage:
Impact damage happens when heavy or sharp objects fall onto the conveyor belt with significant force. This type of damage often results in punctures, cuts, or even complete tears in the belt material. For instance, in mining operations, large rocks falling onto the conveyor belt can cause substantial damage that not only affects the belt itself but also the overall system’s reliability. - Chemical Degradation:
Exposure to harsh chemicals can degrade the material of the conveyor belt. Chemicals used in industrial processes, such as acids or solvents, can react with the belt’s material, causing it to weaken and break down. Chemical degradation can be particularly problematic in industries like chemical manufacturing or food processing, where the belt may come into contact with corrosive substances. - Heat Damage:
Excessive heat can cause significant damage to conveyor belts, especially those made from synthetic materials. Heat can cause the belt to become brittle, crack, or even melt in extreme cases. This type of damage is common in industries where high-temperature processes are involved, such as metal forging or glass manufacturing. Prolonged exposure to high temperatures can severely compromise the belt’s structural integrity. - Edge Wear:
Edge wear occurs when the sides of the conveyor belt experience excessive friction against the conveyor structure or guide rollers. This type of damage often leads to fraying and weakening of the belt edges, which can eventually cause the belt to split. Edge wear is typically a result of misalignment or improper tensioning, and it can significantly reduce the belt’s operational life.
How Damage Leads to Larger System Failures
Understanding the causes of conveyor belt failure is crucial because even minor damage can escalate into major system failures if not addressed promptly. Here’s how different types of conveyor belt damage can lead to larger issues:
- Abrasion and Wear: If not identified early, abrasion can lead to the belt becoming too thin and eventually tearing. A torn belt can cause a sudden halt in operations, leading to significant downtime and loss of productivity. Additionally, pieces of the worn belt can contaminate the transported materials, causing quality control issues.
- Impact Damage: Punctures and cuts from impact damage can grow over time, leading to complete tears in the belt. This type of failure can cause the conveyor system to malfunction, requiring extensive repairs or replacement of the entire belt. The sudden failure of a belt due to impact damage can also pose safety risks to workers nearby.
- Chemical Degradation: Chemical damage weakens the belt material, making it more susceptible to other forms of damage like tearing and cracking. A chemically degraded belt can fail unexpectedly, disrupting the production process and leading to potential safety hazards from the release of transported chemicals.
- Heat Damage: Belts that have been damaged by heat are more likely to crack or melt, causing immediate and catastrophic failure of the conveyor system. Heat damage can also lead to the belt becoming less flexible and more prone to breaking under stress, resulting in frequent stoppages and maintenance issues.
- Edge Wear: Edge wear can cause the belt to misalign, leading to further damage and potential system failures. Misalignment can result in the belt rubbing against the conveyor structure, increasing friction and the risk of fire. It can also cause the belt to track improperly, leading to spillage and loss of materials.
Uunderstanding the causes of conveyor belt failure involves recognizing the various types of damage that can affect conveyor belts and how these damages can escalate into larger system failures. By identifying and addressing issues such as abrasion, impact damage, chemical degradation, heat damage, and edge wear, industries can implement effective maintenance strategies to prevent belt failures. Proactive monitoring and timely intervention are essential to maintaining the efficiency and safety of conveyor systems, ultimately ensuring uninterrupted operations and reducing costs associated with downtime and repairs.
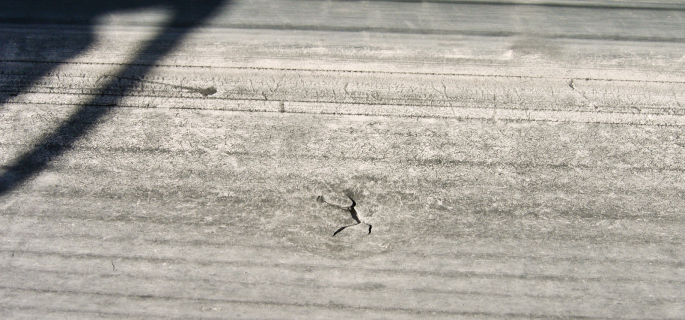
Causes of Conveyor Belt Failure
Understanding the causes of conveyor belt failure is essential for maintaining efficient and reliable operations. This section presents a systematic approach to diagnosing the roots of failure and discusses various causes, including wear and tear, improper tensioning, and environmental factors. By identifying these causes, industries can implement effective preventive measures to minimize downtime and extend the lifespan of their conveyor belts.
Systematic Approach to Diagnosing Conveyor Belt Failure
Diagnosing the causes of conveyor belt failure involves a methodical process that includes inspection, data collection, and failure analysis of belt conveyor systems. Here is a step-by-step approach to systematically identify the root causes of conveyor belt failures:
- Visual Inspection: Conduct a thorough visual inspection of the conveyor belt to identify obvious signs of damage, such as tears, fraying, or misalignment. Look for areas where the belt may be rubbing against the conveyor structure or where materials may have spilled.
- Data Collection: Gather data on the operational history of the conveyor belt, including maintenance records, previous repairs, and any incidents of failure. This information can help identify patterns and recurring issues that may indicate underlying problems.
- Operational Monitoring: Monitor the conveyor belt during operation to observe its behavior. Pay attention to any unusual noises, vibrations, or fluctuations in speed, which could indicate mechanical issues or improper tensioning.
- Root Cause Analysis: Use techniques such as fault tree analysis (FTA) or failure modes and effects analysis (FMEA) to systematically analyze the potential causes of the observed issues. These methods help identify the most likely root causes based on the symptoms and collected data.
- Implement Corrective Actions: Based on the findings of the root cause analysis, implement corrective actions to address the identified issues. This may involve adjusting the conveyor belt tension, replacing worn components, or modifying operational procedures to prevent future failures.
Common Causes of Conveyor Belt Failure
- Wear and Tear: Conveyor belts are subject to constant use, which leads to natural wear and tear over time. The continuous movement of materials across the belt surface causes abrasion, leading to thinning and eventual failure. For example, in industries handling abrasive materials like sand or gravel, the belt surface can become worn down quickly, reducing its effectiveness and lifespan.
- Improper Tensioning: Maintaining the correct tension in a conveyor belt is crucial for its proper functioning. If the belt is too loose, it can slip on the drive pulleys, leading to slippage and inefficient operation. On the other hand, if the belt is too tight, it can cause excessive stress on the belt and the conveyor components, leading to premature wear and potential failure. Improper tensioning is a common cause of conveyor belt failure and requires regular monitoring and adjustment.
- Environmental Factors: Environmental conditions can have a significant impact on the performance and lifespan of conveyor belts. For example, exposure to extreme temperatures, humidity, or corrosive substances can weaken the belt material and cause it to degrade over time. In industries such as mining or chemical processing, where belts may be exposed to harsh environments, it is essential to choose materials that can withstand these conditions and to implement protective measures to minimize damage.
- Material Buildup: The accumulation of materials on the conveyor belt or in the conveyor structure can cause significant issues. For instance, if debris or product residues build up on the belt, it can lead to misalignment, increased friction, and potential damage to the belt surface. Regular cleaning and maintenance are necessary to prevent material buildup and ensure smooth operation.
- Mechanical Failures: Conveyor belts rely on various mechanical components, such as rollers, pulleys, and bearings, to function correctly. Any failure in these components can lead to belt malfunction and potential failure. For example, worn-out bearings can cause the rollers to seize, leading to increased friction and belt wear. Regular inspection and maintenance of these mechanical components are crucial to prevent such failures.
Preventive Measures to Address Conveyor Belt Failure
By understanding the common causes of conveyor belt failure, industries can implement effective preventive measures to minimize the risk of failure and extend the lifespan of their conveyor belts.
- Regular Inspections: Conduct regular inspections of the conveyor belt and its components to identify and address issues early. This includes checking for signs of wear and tear, misalignment, and material buildup.
- Proper Maintenance: Implement a comprehensive maintenance program that includes regular cleaning, lubrication, and replacement of worn components. Proper maintenance helps prevent issues such as improper tensioning and mechanical failures.
- Environmental Protection: Use protective measures, such as covers or coatings, to shield the conveyor belt from harsh environmental conditions. Choose belt materials that are resistant to the specific environmental factors present in the operational environment.
- Training and Education: Train personnel on the proper operation and maintenance of conveyor belts. Educated operators are more likely to identify potential issues early and take appropriate corrective actions.
- Monitoring and Data Analysis: Use monitoring systems to track the performance of conveyor belts in real-time. Analyze the collected data to identify patterns and trends that may indicate potential issues, allowing for proactive maintenance and timely intervention.
Understanding the causes of conveyor belt failure is essential for maintaining efficient and reliable conveyor systems. By implementing a systematic approach to diagnosing failures and addressing common causes such as wear and tear, improper tensioning, environmental factors, material buildup, and mechanical failures, industries can significantly reduce the risk of conveyor belt failures. Proactive maintenance, regular inspections, and proper training are key to ensuring the longevity and performance of conveyor belts, ultimately leading to improved productivity and reduced downtime.
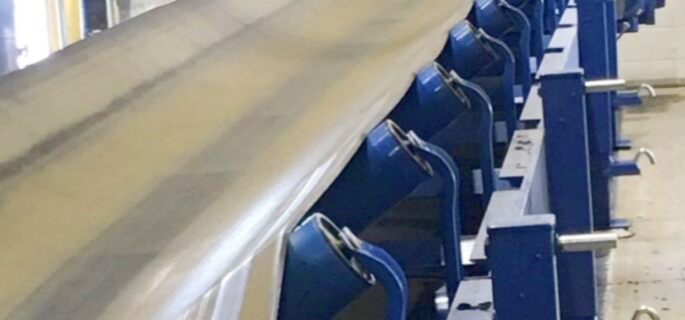
Troubleshooting Common Issues
Troubleshooting common conveyor belt issues is essential for maintaining efficiency and preventing operational disruptions. By systematically identifying and addressing the causes of conveyor belt failure, industries can enhance the reliability of their conveyor systems. This section provides step-by-step troubleshooting procedures and practical advice on how to resolve specific conveyor belt challenges.
Step-by-Step Troubleshooting Procedures
- Identify the Problem: Begin by identifying the specific issue affecting the conveyor belt. This can involve observing the belt during operation, listening for unusual sounds, and noting any irregularities in movement or performance.
- Isolate the Cause: Once the problem is identified, isolate the potential causes. This may involve checking for common issues such as misalignment, improper tension, or wear and tear. Use diagnostic tools and inspection checklists to narrow down the root cause.
- Implement Corrective Actions: Based on the identified cause, implement appropriate corrective actions. This can include adjusting the belt tension, realigning the belt, replacing worn components, or cleaning the conveyor system.
- Test and Verify: After implementing the corrective actions, test the conveyor belt to ensure the problem is resolved. Monitor the belt for any signs of recurring issues and verify that the system is operating smoothly.
- Document and Review: Document the troubleshooting process, including the identified problem, root cause, corrective actions taken, and the outcome. Review the process to identify any areas for improvement and to prevent similar issues in the future.
Practical Advice on Addressing and Resolving Specific Conveyor Belt Challenges
Misalignment Issues
Cause: Misalignment occurs when the conveyor belt deviates from its intended path, often due to improper installation, uneven loading, or worn components.
Solution:
- Inspection: Visually inspect the belt for signs of misalignment and check the alignment of the pulleys and rollers.
- Adjustment: Adjust the alignment of the belt using the tensioning devices or tracking systems. Ensure that the belt runs centrally along its path.
- Maintenance: Regularly maintain and lubricate the pulleys and rollers to prevent misalignment.
Prevention: Ensure proper installation and alignment of the conveyor system from the start. Implement routine inspections and maintenance to identify and correct alignment issues early.
Slippage Problems
Cause: Slippage occurs when the conveyor belt slips on the drive pulley, often due to insufficient tension, excessive load, or worn drive components.
Solution:
- Tensioning: Check the belt tension and adjust it to the manufacturer’s recommended specifications. Use tension gauges for accurate measurements.
- Component Replacement: Inspect the drive pulley and other drive components for wear and replace them if necessary.
- Load Management: Ensure that the conveyor is not overloaded and that the load is evenly distributed.
Prevention: Regularly monitor belt tension and adjust it as needed. Maintain and replace drive components to prevent wear and slippage. Train personnel on proper loading techniques to avoid overloading.
Wear and Tear
Cause: Wear and tear occur due to constant use and exposure to abrasive materials, leading to thinning, fraying, and eventual failure of the belt.
Solution:
- Inspection: Regularly inspect the belt for signs of wear, such as thinning, cuts, and fraying edges.
- Replacement: Replace worn sections of the belt promptly to prevent complete failure. Use high-quality replacement belts designed for the specific application.
- Protective Measures: Implement protective measures such as belt covers or liners to reduce exposure to abrasive materials.
Prevention: Use durable belt materials suited for the specific application. Implement a regular inspection and maintenance schedule to identify and address wear early.
Material Buildup
Cause: Material buildup occurs when transported materials accumulate on the belt or conveyor components, leading to increased friction, misalignment, and potential blockages.
Solution:
- Cleaning: Regularly clean the conveyor belt and components to remove any buildup. Use appropriate cleaning tools and solutions to avoid damaging the belt.
- Inspection: Inspect the conveyor system for areas prone to material buildup and implement measures to prevent accumulation.
- Component Maintenance: Maintain and clean components such as rollers and pulleys to ensure smooth operation.
Prevention: Implement a regular cleaning schedule for the conveyor system. Use belt scrapers or brushes to remove material buildup during operation.
Environmental Factors
Cause: Environmental factors such as extreme temperatures, humidity, and exposure to chemicals can degrade the belt material and lead to failure.
Solution:
- Material Selection: Use conveyor belts made from materials resistant to the specific environmental conditions, such as heat-resistant or chemical-resistant belts.
- Protective Measures: Implement protective measures such as covers, enclosures, or ventilation systems to shield the belt from harsh conditions.
- Monitoring: Regularly monitor the environmental conditions and the condition of the belt to identify and address any issues early.
Prevention: Choose the appropriate belt material for the operating environment. Implement protective measures and regularly monitor the system to ensure it can withstand environmental conditions.
By following these step-by-step troubleshooting procedures and addressing specific conveyor belt challenges, industries can effectively identify and resolve the causes of conveyor belt failure. Regular inspections, proper maintenance, and the implementation of preventive measures are essential for maintaining the reliability and efficiency of conveyor systems. Through proactive troubleshooting and maintenance, industries can minimize downtime, extend the lifespan of their conveyor belts, and ensure smooth and continuous operation.
Preventive Maintenance Strategies for Preventing the Causes of Conveyor Belt Failure
Preventive maintenance is essential for addressing the causes of conveyor belt failure and ensuring the smooth and efficient operation of conveyor systems. By implementing a structured maintenance program, industries can reduce downtime, extend the lifespan of conveyor belts, and maintain optimal productivity. This section introduces the “Conveyor Belt Maintenance Checklist” and outlines routine checks and maintenance tasks designed to prevent failures.
The Conveyor Belt Maintenance Checklist
The “Conveyor Belt Maintenance Checklist” is a comprehensive guide that outlines essential maintenance tasks to keep conveyor belts in optimal condition. It serves as a practical tool for maintenance teams to systematically address potential issues before they lead to significant failures. The checklist includes routine inspections, preventive measures, and corrective actions to ensure the reliability and longevity of conveyor belts.
Routine Checks and Maintenance Tasks
Implementing routine checks and maintenance tasks is crucial for preventing the causes of conveyor belt failure. Here are some key areas to focus on:
1. Visual Inspections
Daily Inspections: Conduct visual inspections of the conveyor belt and its components daily. Look for signs of wear and tear, such as fraying, cuts, or punctures. Check for misalignment, unusual noises, or vibrations that could indicate underlying issues.
Weekly Inspections: Perform more detailed inspections weekly. Examine the belt surface for abrasion, check the condition of the rollers and pulleys, and ensure that the belt is tracking correctly. Identify any signs of material buildup or debris that could interfere with the belt’s operation.
2. Belt Tension and Alignment
Tension Adjustments: Regularly check the tension of the conveyor belt to ensure it is within the manufacturer’s recommended range. Use tension gauges or other tools to measure tension accurately. Adjust the tension as needed to prevent slippage and excessive wear.
Alignment Checks: Verify that the conveyor belt is properly aligned with the pulleys and rollers. Misalignment can cause the belt to drift, leading to edge wear and potential failure. Adjust the alignment to ensure the belt runs centrally and smoothly along its path.
3. Cleaning and Lubrication
Belt Cleaning: Clean the conveyor belt regularly to remove dirt, dust, and debris. Use appropriate cleaning solutions and tools to avoid damaging the belt material. Keeping the belt clean helps prevent material buildup and reduces the risk of abrasion.
Lubrication: Lubricate the moving parts of the conveyor system, such as bearings and rollers, according to the manufacturer’s recommendations. Proper lubrication reduces friction and wear, ensuring the smooth operation of the conveyor belt.
4. Component Inspections and Replacements
Roller and Pulley Checks: Inspect the rollers and pulleys for signs of wear or damage. Ensure that they rotate freely without any obstructions. Replace worn or damaged components promptly to prevent further issues.
Bearing Inspections: Check the bearings for any signs of wear, noise, or overheating. Bearings play a crucial role in supporting the conveyor system’s load, and their failure can lead to significant downtime. Replace faulty bearings to maintain system reliability.
5. Environmental Considerations
Temperature Monitoring: Monitor the operating temperature of the conveyor belt, especially in environments with extreme temperatures. Excessive heat can cause the belt to become brittle, while cold temperatures can make it stiff. Implement measures to regulate temperature and protect the belt material.
Chemical Exposure: Identify any chemicals that the conveyor belt may come into contact with and assess their potential impact. Use belts made from materials resistant to chemical degradation and implement protective measures to minimize exposure.
6. Training and Documentation
Operator Training: Train personnel on the proper operation and maintenance of conveyor belts. Educated operators can identify potential issues early and take appropriate corrective actions, reducing the risk of failures.
Maintenance Records: Keep detailed records of all maintenance activities, including inspections, adjustments, and component replacements. Documenting maintenance tasks helps track the belt’s condition over time and identify recurring issues that may require further investigation.
Implementing a Preventive Maintenance Program
A successful preventive maintenance program involves integrating these routine checks and tasks into the daily operations of the conveyor system. Here are some steps to implement an effective maintenance program:
- Develop a Schedule: Create a maintenance schedule that outlines daily, weekly, and monthly tasks. Assign responsibilities to maintenance team members and ensure that the schedule is adhered to consistently.
- Use Checklists: Utilize the “Conveyor Belt Maintenance Checklist” to guide maintenance activities. Ensure that all items on the checklist are addressed during each inspection and maintenance session.
- Monitor Performance: Continuously monitor the performance of the conveyor belt and track any deviations from normal operation. Use performance data to identify potential issues early and take proactive measures to address them.
- Review and Improve: Regularly review the effectiveness of the maintenance program and make improvements as needed. Solicit feedback from maintenance personnel and operators to identify areas for enhancement.
Preventive maintenance is key to addressing the causes of conveyor belt failure and ensuring the reliable operation of conveyor systems. By implementing a structured maintenance program that includes routine checks, proper tensioning and alignment, cleaning and lubrication, component inspections, environmental considerations, and thorough documentation, industries can significantly reduce the risk of conveyor belt failures. The “Conveyor Belt Maintenance Checklist” serves as an invaluable tool for guiding maintenance activities and ensuring that all critical tasks are completed. Through diligent maintenance and proactive monitoring, industries can extend the lifespan of their conveyor belts, enhance productivity, and minimize costly downtime.
Scientific and Technical Perspectives on Conveyor Belt Issues and Causes of Conveyor Belt Failure
Understanding the causes of conveyor belt failure from a scientific and technical standpoint is crucial for diagnosing problems accurately and implementing effective solutions. By examining the physical principles and scientific mechanisms underlying conveyor belt issues, industries can better prevent malfunctions and enhance the efficiency of their conveyor systems.
Conveyor Belt Problems Physics
The study of “Conveyor Belt Problems Physics” involves analyzing the physical forces and interactions that affect conveyor belts during operation.
- Tensile Stress and Strain: Conveyor belts are subjected to significant tensile forces as they carry loads across long distances. Over time, these forces can cause the belt material to stretch and weaken, leading to tears and eventual failure. The physics of stress and strain help explain how these forces impact the belt’s integrity and how to design belts that can withstand high tensile loads.
- Friction and Wear: Friction between the conveyor belt and the materials it carries, as well as between the belt and the conveyor components, leads to wear. Understanding the physics of friction allows for the selection of materials and surface treatments that minimize wear and extend the belt’s lifespan. For example, using low-friction coatings can reduce the rate of abrasion and prolong belt life.
- Heat Generation and Dissipation: Conveyor belts can generate heat due to friction and mechanical work. Excessive heat can degrade the belt material, causing it to become brittle and prone to cracking. The principles of thermodynamics and heat transfer explain how heat is generated and dissipated in conveyor systems, guiding the design of belts and cooling mechanisms to manage temperature effectively.
- Dynamic Loading and Fatigue: Conveyor belts experience dynamic loads as they start, stop, and change direction. These dynamic forces can lead to material fatigue, causing the belt to crack or fail over time. The physics of dynamic loading and fatigue analysis help in designing belts that can absorb and withstand these fluctuating forces, reducing the risk of fatigue failure.
- Belt Tracking and Alignment: Proper belt tracking is essential for the smooth operation of conveyor systems. Misalignment can cause the belt to drift and rub against the conveyor structure, leading to edge wear and potential failure. The physics of motion and alignment explain how forces act on the belt and how to design tracking systems that keep the belt aligned correctly.
Scientific Principles Leading to or Preventing Malfunctions
Several scientific principles can either contribute to or help prevent conveyor belt malfunctions. Understanding these principles is key to addressing the causes of conveyor belt failure effectively.
1. Material Science
Contribution to Malfunctions: The choice of belt material plays a significant role in its susceptibility to wear, chemical degradation, and thermal damage. Inappropriate material selection can lead to premature belt failure due to environmental conditions or operational stresses.
Prevention: Advances in material science have led to the development of high-performance conveyor belt materials that offer enhanced resistance to abrasion, chemicals, and temperature extremes. For example, belts made from reinforced polymers or coated with specialized compounds can withstand harsh conditions and extend operational life.
2. Thermodynamics
Contribution to Malfunctions: Excessive heat generated by friction or external environmental factors can degrade the belt material, causing it to become brittle and crack. Poor heat dissipation exacerbates this problem.
Prevention: Understanding thermodynamics allows for the design of cooling systems and the selection of heat-resistant materials. Implementing proper ventilation and cooling mechanisms can effectively manage heat, preventing thermal degradation of the conveyor belt.
3. Mechanics and Dynamics
Contribution to Malfunctions: Dynamic loads and mechanical stresses during operation can lead to material fatigue and structural failure. Sudden starts and stops, as well as changes in load distribution, contribute to these dynamic stresses.
Prevention: Using principles of mechanics and dynamics, engineers can design conveyor systems that minimize dynamic loads and distribute stress evenly. This includes using soft start mechanisms, shock absorbers, and designing for optimal load distribution to reduce the risk of fatigue failure.
4. Friction and Wear Control
Contribution to Malfunctions: High friction between the belt and transported materials or conveyor components leads to accelerated wear and tear. Improper lubrication and material buildup exacerbate this issue.
Prevention: Applying principles of tribology, the study of friction, wear, and lubrication, helps in selecting materials and lubricants that reduce friction and wear. Regular maintenance and cleaning also play a crucial role in minimizing friction-related damage.
5. Structural Engineering
Contribution to Malfunctions: Poor structural design of the conveyor system can lead to misalignment, excessive vibration, and uneven load distribution, all of which contribute to belt failure.
Prevention: Structural engineering principles guide the design of conveyor systems that are robust, stable, and properly aligned. Ensuring that the conveyor frame and components are well-designed and precisely installed can prevent alignment issues and reduce vibrations.
The causes of conveyor belt failure from a scientific and technical perspective is essential for diagnosing and preventing malfunctions. By applying the principles of material science, thermodynamics, mechanics and dynamics, friction and wear control, and structural engineering, industries can design and maintain conveyor systems that are efficient, reliable, and durable. The study of “Conveyor Belt Problems Physics” provides valuable insights into the physical interactions and forces that affect conveyor belts, guiding the development of innovative solutions to extend their lifespan and enhance operational efficiency. Through proactive maintenance and informed design choices, industries can effectively address the conveyor belt damage causes and ensure the smooth operation of their conveyor systems.
FAQs ABout Causes of Conveyor Belt Failure
Conveyor belts can fail for several reasons, which are often linked to improper maintenance, environmental factors, and mechanical issues. Common causes include wear and tear due to continuous use, improper tensioning, and misalignment. Exposure to extreme temperatures or chemicals can degrade the belt material, making it brittle and prone to cracking. Overloading the conveyor system or carrying abrasive materials can accelerate wear and cause premature failure. Additionally, lack of regular inspections and maintenance can result in unnoticed minor issues escalating into significant problems, leading to unexpected belt failures and operational downtime. Understanding these factors is crucial for implementing effective preventive measures and ensuring the longevity of conveyor belts.
Misalignment: Misalignment occurs when the conveyor belt does not run in a straight line along the conveyor structure. This can be caused by uneven loading, improper installation, or worn-out components. Misalignment leads to increased wear and tear on the belt edges and can cause the belt to drift, leading to operational inefficiencies.
Slippage: Slippage happens when the conveyor belt does not move at the same speed as the rollers due to insufficient tension or worn drive components. This reduces the efficiency of the conveyor system and can cause product loss or damage.
Material Buildup: Accumulation of materials on the belt or conveyor components can lead to increased friction, misalignment, and potential blockages. This is often due to improper cleaning and maintenance practices.
Wear and Tear: Continuous use and exposure to abrasive materials can cause significant wear and tear on conveyor belts. This leads to thinning, cuts, and fraying edges, eventually resulting in belt failure if not addressed promptly.
Conveyor belts can rip due to several factors, including excessive tension, impact from heavy or sharp objects, and material buildup. Over-tensioning the belt can put undue stress on the material, making it more susceptible to tearing. Impact damage occurs when large or sharp items fall onto the belt with significant force, causing punctures or cuts that can expand into rips. Material buildup on the belt or in the conveyor system can also create uneven load distribution, increasing the risk of ripping. Additionally, environmental factors such as exposure to harsh chemicals or extreme temperatures can weaken the belt material, making it more prone to ripping. Regular inspections and maintenance are crucial for identifying and mitigating these risks.
Troubleshooting a conveyor belt involves a systematic approach to identify and resolve issues. Here are the steps to follow:
Identify the Problem: Observe the conveyor belt during operation to pinpoint the issue. Look for signs of misalignment, unusual noises, vibrations, or visible damage.
Isolate the Cause: Determine the root cause of the problem by checking common areas of concern such as belt tension, alignment, and the condition of rollers and pulleys. Use diagnostic tools and reference maintenance records to narrow down potential causes.
Implement Corrective Actions: Based on the identified cause, take appropriate corrective actions. This might involve adjusting the belt tension, realigning the belt, replacing worn components, or cleaning the conveyor system.
Test and Verify: After making the necessary adjustments or repairs, test the conveyor belt to ensure the problem has been resolved. Monitor the belt for any signs of recurring issues and verify that the system is operating smoothly.
Document and Review: Keep detailed records of the troubleshooting process, including the problem identified, root cause, corrective actions taken, and the outcome. Review this information regularly to improve maintenance practices and prevent future issues.
By following these steps, you can effectively troubleshoot and resolve conveyor belt issues, ensuring minimal downtime and optimal performance.
Drive failure on a conveyor can be caused by several factors, including:
Overloading: Exceeding the conveyor’s capacity can strain the drive system.
Poor Maintenance: Lack of regular maintenance can lead to wear and tear.
Misalignment: Misaligned components can cause uneven stress on the drive.
Lubrication Issues: Inadequate lubrication can cause excessive friction and heat.
Electrical Problems: Faulty wiring or electrical components can lead to drive failure.
Contamination: Dirt, dust, or debris can interfere with the drive mechanism.
Component Wear: Worn-out parts such as bearings, belts, or gears can lead to failure.
Improper Installation: Incorrect installation can lead to operational issues.
Thermal Overload: Excessive heat can damage drive components.
Vibration: Excessive vibration can cause loosening or damage to drive parts.
Last Updated on August 1, 2024 by Jordan Smith
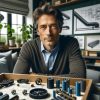
Jordan Smith, a seasoned professional with over 20 years of experience in the conveyor system industry. Jordan’s expertise lies in providing comprehensive solutions for conveyor rollers, belts, and accessories, catering to a wide range of industrial needs. From initial design and configuration to installation and meticulous troubleshooting, Jordan is adept at handling all aspects of conveyor system management. Whether you’re looking to upgrade your production line with efficient conveyor belts, require custom conveyor rollers for specific operations, or need expert advice on selecting the right conveyor accessories for your facility, Jordan is your reliable consultant. For any inquiries or assistance with conveyor system optimization, Jordan is available to share his wealth of knowledge and experience. Feel free to reach out at any time for professional guidance on all matters related to conveyor rollers, belts, and accessories.