CEMA 5 Inch Dia Steel Garland Roller: Setup and Use
Welcome to our in-depth exploration of the CEMA 5 inch dia steel garland roller, an essential component in modern conveyor systems. Developed by the Conveyor Equipment Manufacturers Association (CEMA), this specific roller is designed to enhance the efficiency and longevity of conveyor operations. Throughout this blog, we’ll delve into various aspects of the cema 5 inch dia steel garland roller, examining its design, functionality, and the significant role it plays in the bulk material handling industry. We will also provide insights into its specifications as per CEMA standards, and discuss the best practices for its installation, maintenance, and operational efficiency. Our goal is to equip you with the knowledge needed to optimize your conveyor system using the cema 5 inch dia steel garland roller, ensuring smooth and effective operations across numerous applications.
CEMA Standards and the CEMA 5 Inch Dia Steel Garland Roller
The Conveyor Equipment Manufacturers Association (CEMA) plays a pivotal role in setting design standards for various material handling equipment, including the CEMA 5 inch dia steel garland roller. These standards ensure reliability, safety, and efficiency, essential for the industry’s robust operation. CEMA standards cover a broad range of equipment specifications from roller diameter to load capacity. Here are five examples of how CEMA standards influence the design and functionality of material handling equipment:
- Dimensional Standards: Ensuring that the CEMA 5 inch dia steel garland roller fits universally into existing systems without the need for additional adjustments.
- Load Ratings: Specifying the maximum load the CEMA 5 inch dia steel garland roller can consistently support during operation.
- Material Specifications: Defining the types of materials that can be used to manufacture the CEMA 5 inch dia steel garland roller, which impacts its durability and wear resistance.
- Operational Speed: Setting limits on the operational speed of the conveyor systems that utilize the CEMA 5 inch dia steel garland roller to ensure safety and mechanical integrity.
- Quality Control: Providing guidelines for quality assurance testing of the CEMA 5 inch dia steel garland roller to ensure it meets the required performance standards before deployment.
Delving into the specificities of the CEMA 5 inch dia steel garland roller, it is designed to offer superior performance in conveyor systems. Its specifications are meticulously aligned with CEMA standards to ensure optimal compatibility and performance. The roller’s diameter allows for smoother motion of the conveyor belt, reducing the wear and tear on both the belt and the roller itself. Additionally, the steel construction enhances the durability and load-bearing capacity of the CEMA 5 inch dia steel garland roller, making it ideal for heavy-duty applications in various industries. By adhering to CEMA standards, this roller ensures a high degree of reliability and efficiency in conveyor operations.
Product Manual of the CEMA 5 Inch Dia Steel Garland Roller
The product manual for the CEMA 5 inch dia steel garland roller serves a critical function by providing users with detailed guidance on the correct setup, operation, and maintenance of this specific piece of equipment. The manual is designed to ensure that all users, regardless of their previous experience with conveyor systems, can understand and efficiently use the CEMA 5 inch dia steel garland roller to its fullest potential.
Purpose of Product Manuals
Product manuals are essential for several reasons:
- Safety: They provide important safety instructions to prevent accidents and ensure safe operation.
- Efficiency: Manuals offer step-by-step guides to setting up and operating machinery correctly, thereby optimizing performance.
- Troubleshooting: They help users diagnose and resolve issues that may arise during the lifespan of the equipment.
- Maintenance: Manuals provide scheduled maintenance procedures to extend the longevity and reliability of the equipment.
Walkthrough of the CEMA 5 Inch Dia Steel Garland Roller Manual
The manual for the CEMA 5 inch dia steel garland roller includes comprehensive sections covering installation, operational procedures, and maintenance. Here’s a detailed look at each section:
Installation:
- Detailed diagrams and step-by-step instructions guide users through the assembly of the CEMA 5 inch dia steel garland roller into existing conveyor systems.
- Tips on alignment and tensioning of the roller to ensure smooth operation and minimal wear.
Operation:
- Instructions on how to start and operate the conveyor with the CEMA 5 inch dia steel garland roller installed.
- Guidelines on speed settings and load capacities specific to the CEMA 5 inch dia steel garland roller, ensuring optimal performance and avoiding overloading.
Maintenance:
- Regular maintenance schedules that detail when and how to inspect the CEMA 5 inch dia steel garland roller for wear and potential issues.
- Procedures for lubrication, cleaning, and replacement of parts that are crucial for maintaining the performance and extending the service life of the CEMA 5 inch dia steel garland roller.
- Troubleshooting tips to help quickly identify common problems and solutions to keep downtime to a minimum.
This manual is an indispensable resource for ensuring the CEMA 5 inch dia steel garland roller operates efficiently and continues to meet the needs of the industry while complying with CEMA standards.
Component Parts of CEMA 5 Inch Dia Steel Garland Roller
Understanding the component parts of the CEMA 5 inch dia steel garland roller is essential for both maintenance and effective use. Each part plays a crucial role in ensuring the operational efficiency and durability of the roller. Below, we examine five key components and discuss their functions and significance in the overall operation of the roller.
Key Components of the CEMA 5 Inch Dia Steel Garland Roller
Roller Shell:
- Description: The outer tube of the CEMA 5 inch dia steel garland roller, typically made from heavy-duty steel.
- Function: Provides the primary surface for the conveyor belt to roll over, and supports the belt load.
- Significance: The shell’s durability directly impacts the roller’s lifespan and the smooth operation of the conveyor system.
Bearing and Bearing House:
- Description: Bearings are fitted inside the bearing house at each end of the roller shell.
- Function: Bearings allow the roller to turn smoothly and with minimal friction.
- Significance: Critical for reducing wear and tear and maintaining the efficiency of the CEMA 5 inch dia steel garland roller, especially under high-load conditions.
Shaft:
- Description: A central rod that connects to the bearing and extends across the length of the roller.
- Function: Acts as the core structure that holds the roller together and provides the axis of rotation.
- Significance: The shaft’s strength is vital for bearing the load and ensuring the roller does not bend under pressure.
Seals:
- Description: Seals are located near the bearings within the bearing house.
- Function: Protect the bearings by preventing dirt, dust, and other contaminants from entering the bearing area.
- Significance: Ensures the longevity and reliability of the bearings in the CEMA 5 inch dia steel garland roller, reducing maintenance frequency and costs.
Mounting Brackets:
- Description: These are the parts used to secure the cema 5 inch dia steel garland roller to the conveyor frame.
- Function: Facilitate the installation and positioning of the roller within the conveyor system.
- Significance: Properly designed mounting brackets ensure the roller is held firmly, preventing misalignment that could lead to uneven wear or operational disruptions.
By understanding each of these components and their functions, operators and maintenance personnel can ensure that the CEMA 5 inch dia steel garland roller operates at peak efficiency. Regular checks and maintenance of these parts are crucial for prolonging the operational life of the roller and by extension, the conveyor system it supports.
Professional Paint Roller Sizes and the CEMA 5 Inch Dia Steel Garland Roller
While discussing professional paint roller sizes might seem tangential, there’s an interesting correlation when examining specialized industrial tools like the CEMA 5 inch dia steel garland roller. Just as paint rollers are selected based on the job requirements in the painting industry, so too are components like the CEMA 5 inch dia steel garland roller chosen for their specific utility in conveyor systems across various industrial applications.
Using Paint Rollers in Industrial Applications
In industrial settings, paint rollers are not merely tools for applying coatings but are integral in processes such as applying protective layers, adhesives, and other substances that contribute to manufacturing and maintenance. The size and material of the roller are selected based on the surface area, the type of coating, and the precision required.
Discussion on Various Sizes of Paint Rollers and Their Applications
Small Rollers (3 to 5 inches):
- Usage: Ideal for furniture, cabinets, and other small or detailed surfaces.
- Rationale: Allows for precision and control, minimizing waste and ensuring even coverage on intricate details.
Medium Rollers (7 to 9 inches):
- Usage: Commonly used for walls and ceilings in residential and commercial buildings.
- Rationale: Balances coverage area and ease of handling, providing efficient application over standard flat surfaces.
Large Rollers (12 inches and above):
- Usage: Best for large, flat industrial surfaces like factory floors or large exterior walls.
- Rationale: Maximizes coverage area, reducing labor time and effort on big jobs.
Specialty Rollers (texture-specific or patterned rollers):
- Usage: Used to create specific finishes like textured, stippled, or faux finishes on feature walls.
- Rationale: Provides a unique aesthetic without the need for multiple coat applications or complex techniques.
Foam Rollers:
- Usage: Employed for smooth surfaces needing a fine finish, such as metal doors or cabinets.
- Rationale: Delivers a smooth, bubble-free finish and is particularly effective with gloss paints.
Linking back to the cema 5 inch dia steel garland roller, just as the size and type of a paint roller are crucial for the task at hand in painting, the dimensions and design specifications of industrial components like the cema 5 inch dia steel garland roller are critical in selecting the right equipment for specific conveyor needs. This ensures operational efficiency, longevity, and cost-effectiveness in material handling environments. Understanding the comparative significance of tool sizing in different industries highlights the importance of precise engineering and application-specific design in industrial components.
FAQs About CEMA 5 Inch Dia Steel Garland Roller
The CEMA C rating refers to a classification of conveyor idlers designated by the Conveyor Equipment Manufacturers Association (CEMA). This rating is part of a broader set of standards that define the specifications for various conveyor system components based on expected usage, load capacity, and environmental conditions. CEMA C rated idlers are designed to handle moderate load applications and are commonly used in industries such as aggregate, cement, and coal mining. These idlers are characterized by their ability to support belt widths from 18 to 60 inches, with load ratings that typically range from 20,000 to 30,000 hours of operation under normal conditions. CEMA ratings, including CEMA C, help users select the appropriate idlers based on operational requirements, ensuring durability and efficient functionality of conveyor systems.
The full form of CEMA in the context of conveyor systems is the “Conveyor Equipment Manufacturers Association.” CEMA is a trade association representing the conveyor industry, established with the aim of promoting standards among manufacturers, users, and other stakeholders in the conveyor industry. The association is responsible for developing standards for the design, manufacture, and application of conveying machinery and component parts. These standards are widely respected and followed within the industry globally. They are essential for ensuring safety, reliability, and operational efficiency in the design and implementation of conveyor systems across various sectors including mining, automotive, and food processing.
The angle of a troughing idler refers to the angular arrangement of the rollers that support the conveyor belt. This angle is critical as it helps to shape the belt to contain the material being transported. Troughing idlers typically come in standard angles of 20, 35, and 45 degrees, which correspond to the depth of the trough they create, influencing both the carrying capacity and the stability of the belt under load. The choice of angle depends on the type of material being conveyed, the conveyor speed, and the overall design of the system. A higher angle provides greater carrying capacity but may require more power to drive the belt and can increase the wear on the belt and idlers. Selecting the correct angle for troughing idlers is crucial for optimizing conveyor performance and efficiency.
A Garland idler consists of a series of 2 to 5 rollers arranged in a flexible configuration that hangs from the conveyor frame. This type of idler is used to support the belt and material load and is particularly effective in accommodating shifts and variations in the alignment and elevation of the conveyor pathway. Garland idlers are especially useful in rough terrain where fixed-frame idlers might not offer adequate flexibility. Each roller in the garland idler can pivot independently, allowing for better contact with the belt and improved distribution of loads. This flexibility helps in reducing belt wear and tear, improving the life span of both the belt and the idlers. Garland idlers are commonly used in heavy-duty applications such as mining, where they accommodate the irregularities of rough and uneven conveyor paths.
Last Updated on June 7, 2024 by Jordan Smith
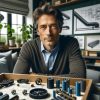
Jordan Smith, a seasoned professional with over 20 years of experience in the conveyor system industry. Jordan’s expertise lies in providing comprehensive solutions for conveyor rollers, belts, and accessories, catering to a wide range of industrial needs. From initial design and configuration to installation and meticulous troubleshooting, Jordan is adept at handling all aspects of conveyor system management. Whether you’re looking to upgrade your production line with efficient conveyor belts, require custom conveyor rollers for specific operations, or need expert advice on selecting the right conveyor accessories for your facility, Jordan is your reliable consultant. For any inquiries or assistance with conveyor system optimization, Jordan is available to share his wealth of knowledge and experience. Feel free to reach out at any time for professional guidance on all matters related to conveyor rollers, belts, and accessories.