CEMA Standard for Belt Conveyor Design & Installation
CEMA standards, set forth by the Conveyor Equipment Manufacturers Association, serve as the cornerstone for safety and operational efficiency within the conveyor industry. These guidelines, particularly the CEMA standard for belt conveyor, establish critical benchmarks for quality and performance, influencing design, installation, and maintenance processes across diverse applications. CEMA Standard for Belt Conveyor that helps identify the appropriate industrial conveyor belt system for specific applications. By outlining rigorous safety protocols and engineering standards, they ensure that conveyor systems operate under optimal conditions, significantly reducing the risk of workplace incidents and increasing system longevity. This introduction not only emphasizes the association’s role in promoting these industry-wide standards but also highlights their specific relevance to belt conveyors, making it clear how integral they are in maintaining the high standards of reliability and functionality expected in modern material handling and processing industries.
CEMA Standard for Belt Conveyor Design & Construction
The CEMA Standard for Belt Conveyor Design & Construction refers to the technical guidelines and best practices established by the Conveyor Equipment Manufacturers Association (CEMA). These standards provide a comprehensive framework to ensure safe, efficient, and reliable design, construction, operation, and maintenance of belt conveyors used in various industries such as mining, food processing, bulk material handling, and manufacturing. Below is a detailed breakdown of key aspects covered by the CEMA standards:
1. General Principles of Conveyor Design
The CEMA standards emphasize designing conveyors for both functionality and safety. They highlight the importance of understanding the specific application, including material characteristics, operational requirements, and environmental factors. Some general design principles include:
- Capacity planning: Determining the volume of material to be conveyed and the belt speed required.
- Belt width and speed: Selection of appropriate belt width and speed to balance efficiency with operational safety.
- Load profile and material flow: Designing conveyors to ensure smooth, uninterrupted material flow, preventing bottlenecks and spillage.
2. Components and System Design
CEMA standards define the specifications for key conveyor components to ensure durability and efficiency. These components include:
- Belting: Guidelines for selecting materials and construction of conveyor belts based on their tensile strength, flexibility, and resistance to abrasion.
- Idlers: Specification of idler types (such as troughing and return idlers) and their spacing to ensure adequate belt support and alignment.
- Pulleys: Recommendations for conveyor belt pulley size and construction to minimize belt wear and increase operating life.
- Drives and Motors: Standards for motor sizing, drive power, and torque requirements to meet the conveyor’s operational demands.
- Frames and Supports: Specifications for structural elements that ensure proper alignment, belt tensioning, and safe operation.
3. Material Characteristics and Handling
Understanding the properties of the material being conveyed is essential for designing an efficient conveyor system. The CEMA standards provide guidance on:
- Material classification: Grouping materials based on factors like particle size, moisture content, and abrasiveness.
- Flowability: Ensuring proper handling of materials prone to sticking, clogging, or degradation during transport.
- Environmental considerations: Taking into account the presence of dust, humidity, or corrosive environments when selecting materials and components.
4. Power Calculations and Load Considerations
CEMA standards detail the procedures for calculating the power required to operate conveyors efficiently. These calculations include:
- Belt tension calculations: Determining the required tension to overcome friction, acceleration, and lift.
- Power demand: Estimating motor power needed for steady-state operation and peak loads.
- Friction and resistance factors: Incorporating friction coefficients, idler resistance, and other operational forces into calculations.
5. Safety Standards and Best Practices
CEMA places significant emphasis on safety in conveyor design and operation. Important safety recommendations include:
- Guards and emergency stops: Installation of protective guards around moving parts and accessible emergency stop controls.
- Belt tracking and alignment: Ensuring proper belt tracking to prevent accidents and reduce downtime.
- Maintenance access: Designing systems with easy access points for inspection, cleaning, and maintenance tasks.
- Noise reduction: Recommendations for reducing noise levels by using low-noise components and proper belt tensioning.
6. Maintenance and Operation Guidelines
Proper maintenance and operation are essential to extend the life of a conveyor system. The CEMA standards include:
- Preventive maintenance schedules: Regular inspection and replacement of wear parts to avoid unexpected failures.
- Lubrication practices: Guidelines for the frequency and type of lubrication needed for bearings, rollers, and other moving parts.
- Monitoring systems: Recommendations for integrating monitoring systems to detect misalignment, belt slippage, or overheating.
7. Environmental and Regulatory Compliance
Conveyors often operate in regulated environments where compliance with health, safety, and environmental standards is essential. CEMA standards help manufacturers align with relevant regulations by:
- Dust control and ventilation: Managing dust emissions to comply with environmental standards.
- Energy efficiency: Promoting energy-efficient designs to minimize operational costs and environmental impact.
- Noise and vibration control: Ensuring compliance with local noise regulations by designing conveyors that minimize vibrations.
8. Specialty Conveyors and Custom Applications
CEMA recognizes that some operations require customized conveyor solutions. The standards include guidelines for:
- High-angle or curved conveyors: Design considerations for specialized conveyors used in mining or steep terrains.
- Food-grade conveyors: Specifications for materials and components suitable for hygienic applications, such as food and pharmaceuticals.
- Hazardous environments: Designing conveyors that meet the specific needs of operations in explosive or corrosive environments.
The CEMA Standard for Belt Conveyor Design & Construction serves as an essential resource for engineers, manufacturers, and operators involved in the design and maintenance of conveyor systems. By adhering to these standards, companies can ensure their conveyors are safe, efficient, and aligned with industry best practices. The focus on material properties, power calculations, safety features, and operational guidelines makes the CEMA standards highly relevant across industries.

CEMA Standard for Belt Conveyor Rating
The CEMA Standard for Belt Conveyor Rating provides guidelines to classify and rate belt conveyors to ensure safe, efficient, and reliable performance. These standards cover critical aspects like capacity, belt strength, drive power, structural integrity, and environmental considerations. The purpose of the rating system is to align conveyor components and operations with specific application demands, ensuring both performance optimization and safety compliance. Below is a detailed explanation of the key elements.
Belt Capacity Rating
The belt capacity rating determines how much material a conveyor can transport over a certain period. It considers several key parameters:
- Belt width: Wider belts offer greater capacity.
- Belt speed: Higher speeds increase throughput.
- Material bulk density: Measured in pounds per cubic foot (PCF) or kilograms per cubic meter (kg/m³), bulk density impacts the weight and flow of material being conveyed.
- Troughing angle: Affects how much material can be carried in the trough formed by the idlers beneath the belt.
CEMA offers formulas to calculate capacity in tons per hour based on these parameters, helping engineers optimize design according to operational needs.
Belt Tension Rating
Belt tension rating focuses on ensuring the belt material can handle the stresses encountered during operation. This involves:
- Maximum Allowable Working Tension (MAWT): Specifies the safe working load, often expressed as a percentage of the belt’s ultimate tensile strength.
- Tension ratings: Usually provided in units such as pounds per inch width (PIW) or Newtons per millimeter (N/mm).
- Safety factors: These factors ensure that belts can withstand conditions like sudden start-ups or jams without failure. Applications with high-impact loads or abrasive materials require higher safety margins.
Selecting a belt with an appropriate tension rating ensures reliability, minimizing the risk of wear or rupture during use.
Power Rating and Drive Requirements
Proper power rating is crucial to determine the motor and drive components required to run the conveyor efficiently. CEMA standards include:
- Effective tension (Te): The force needed to move the loaded belt.
- Start-up torque requirements: Extra power needed during the initial acceleration phase.
- Drive power: A calculation of motor size and power requirements, considering resistance factors such as friction and elevation changes.
This ensures the conveyor can handle both normal operation and occasional peak loads, preventing belt slippage or overloading of motors.
Structural and Load Rating
The conveyor structure must be rated to withstand operational loads without excessive wear or misalignment. Key components evaluated include:
- Idlers and pulleys: Their spacing, alignment, and capacity to handle loads without failure are crucial for smooth operation.
- Support frames: Must be strong enough to bear static and dynamic loads, including vibrations and material impact.
- Belt support systems: Ensuring the belt remains aligned and tensioned reduces wear and minimizes operational disruptions.
These ratings ensure that the conveyor’s mechanical components can withstand the demands of continuous use in various environments.
Belt Life and Durability Rating
CEMA standards also address belt longevity to reduce maintenance and replacement costs. Key factors include:
- Belt cover material: Abrasion-resistant covers extend belt life in harsh conditions.
- Temperature resistance: Belts must perform reliably across expected temperature ranges, whether in extremely hot or cold environments.
- Tracking and alignment systems: Proper alignment systems reduce belt wear, ensuring smoother operation and extended life.
Long-lasting components improve reliability and lower maintenance costs over the conveyor’s lifespan.
Environmental Ratings
Conveyor systems often operate in challenging environments, requiring specialized ratings to maintain performance. CEMA standards consider:
- Dust and moisture resistance: Components should withstand exposure to corrosive elements, dust, or high humidity.
- Noise and vibration control: Minimizing noise and vibration helps meet regulatory requirements and ensures worker safety.
- Sealing systems: Proper sealing prevents material leakage and environmental contamination, improving both operational efficiency and environmental compliance.
These environmental ratings help ensure conveyors operate efficiently while minimizing their environmental impact.
Safety and Compliance Ratings
CEMA emphasizes safety in conveyor design and operation. Safety ratings include:
- Guarding systems: All moving parts, such as pulleys, motors, and belts, must be properly guarded to prevent accidents.
- Emergency stop systems: Easily accessible emergency stops along the conveyor ensure quick intervention in case of malfunction.
- Fire resistance and anti-static properties: Conveyor belts used in hazardous areas must meet specific fire-resistant or anti-static standards to prevent accidents.
These safety measures ensure that operations comply with local and international safety regulations, reducing risks to personnel.
Application-Specific Ratings
Conveyors may require specialized ratings depending on the industry or operating conditions. CEMA provides guidance for:
- Underground mining conveyors: These systems must meet higher fire-resistance and durability standards.
- Food-grade conveyors: Belts must comply with hygienic standards, such as FDA or USDA requirements, to ensure food safety.
- Inclined and high-angle conveyors: Special cleated or sidewall belts are used to prevent material slippage on steep inclines.
Custom ratings ensure that conveyors are designed to meet the specific demands of each application, ensuring optimal performance.
The CEMA Standard for Belt Conveyor Rating provides a comprehensive framework for evaluating and selecting the right conveyor components based on the intended use. It covers critical areas such as belt capacity, power requirements, tension, environmental performance, and safety, helping manufacturers and operators design systems that are efficient, durable, and compliant with industry regulations. Adhering to these standards ensures optimal conveyor performance, reduces maintenance costs, and promotes safe operation across various industries.
CEMA Standard for Belt Conveyor for Screw Conveyor Systems
The CEMA Standard for Belt Conveyor for Screw Conveyor Systems integrates both the principles of belt conveyors and screw conveyors, ensuring compatibility and optimal design when these two conveying methods are used together. Screw conveyors are often employed to transfer bulk materials from hoppers, feeders, or silos into belt conveyors. CEMA standards ensure that these systems function seamlessly by providing guidelines for capacity, power requirements, safety, and operational efficiency. Below is a comprehensive overview of the key areas covered by CEMA standards when integrating belt conveyors with screw conveyor systems.
System Integration between Belt and Screw Conveyors
The goal of integrating belt and screw conveyors is to ensure smooth material flow between the two systems without clogging, spillage, or damage to components. Key considerations include:
- Material transfer points: Smooth transfer from the screw conveyor to the belt conveyor is critical to avoid spillage and ensure even loading of the belt.
- Flow control: Proper control of material flow ensures that the belt conveyor operates within its designed capacity, preventing overloading or belt misalignment.
CEMA provides guidelines on system design to achieve efficient integration, including the use of chutes, hoppers, and variable-speed controls.
Capacity Rating and Material Handling
Capacity planning is essential to match the output of the screw conveyor with the input capacity of the belt conveyor. Important considerations include:
- Screw conveyor capacity: Depends on screw diameter, pitch, and speed.
- Belt conveyor capacity: Determined by belt width, speed, and troughing angle.
- Bulk material properties: Moisture content, abrasiveness, and particle size affect the flow rate and potential for material buildup in screw conveyors.
CEMA offers formulas to calculate the required capacity for both conveyors, ensuring they are properly synchronized for uninterrupted material transfer.
Power Requirements and Torque Ratings
Screw conveyors often require more torque at start-up due to material compaction, while belt conveyors require consistent power to maintain steady operation. CEMA provides guidelines to:
- Calculate motor power: For both screw and belt conveyors, including allowances for start-up torque.
- Screw conveyor drive design: Selecting the right motor and gearbox to handle peak loads.
- Belt conveyor power rating: Ensuring the belt drive system can manage the load transferred from the screw conveyor without slippage or excessive strain.
Proper motor sizing helps avoid power losses and ensures both systems operate efficiently, minimizing downtime.
Load Distribution and Material Flow
Balanced load distribution is critical to avoid wear and damage in either system. CEMA standards include recommendations for:
- Hopper design: Ensuring consistent feed into the screw conveyor without clogs or surges.
- Chute and transfer point design: Optimizing material drop height from the screw conveyor onto the belt conveyor to prevent impact damage and reduce belt wear.
- Feed rate controls: Using flow gates, variable frequency drives (VFDs), or sensors to regulate material flow and maintain smooth operation.
These load management practices minimize the risk of belt misalignment, overloading, or material spillage.
Safety and Maintenance Considerations
CEMA places significant emphasis on safety when combining belt and screw conveyor systems. Some key safety practices include:
- Guards and covers: Protecting rotating shafts and moving belts to prevent accidents.
- Emergency stops: Positioned at key points along both conveyors for quick shutdown.
- Access for maintenance: Ensuring that both conveyors are easy to inspect, clean, and service.
Regular maintenance, such as lubricating screw conveyor bearings and checking belt tension, ensures long-term reliability and safety.
Environmental Considerations
Conveyor systems often operate in harsh environments that demand specific design adjustments. CEMA standards address:
- Dust control: Using enclosed screw conveyors or belt covers to reduce dust emissions.
- Sealing systems: Preventing material leakage at transfer points to maintain environmental compliance.
- Corrosion-resistant materials: Specifying stainless steel or coated components for use in corrosive or wet conditions.
These recommendations ensure that the system performs efficiently while meeting environmental and safety regulations.
Application-Specific Design
CEMA standards acknowledge that different industries have unique requirements for conveyor systems. Some examples include:
- Mining and bulk material handling: Systems must handle abrasive materials with minimal wear.
- Food and pharmaceutical industries: Components must meet hygienic standards, with easy-to-clean surfaces and minimal contamination risks.
- Inclined applications: Screw conveyors are often used to elevate material onto inclined belt conveyors, requiring special considerations for belt cleats and screw pitch.
These application-specific designs help ensure the smooth operation of both belt and screw conveyors in various industries.
The CEMA Standard for Belt Conveyor for Screw Conveyor Systems provides a comprehensive framework for designing and integrating these two systems effectively. By aligning capacities, motor power, load distribution, and safety practices, the standard ensures that belt and screw conveyors work harmoniously. Proper integration enhances operational efficiency, reduces downtime, and minimizes maintenance costs. These standards are critical for industries that rely on multiple conveying systems, helping them achieve optimized performance and regulatory compliance.

CEMA Standard for Belt Conveyor Bulk Material
The CEMA Standard for Belt Conveyors for Bulk Materials provides comprehensive guidelines for the design, construction, and operation of belt conveyors used to transport bulk materials. These standards focus on ensuring efficiency, safety, and reliability while considering the material properties, operational environment, and equipment components involved. Below is a detailed breakdown of the key elements covered in the CEMA standards for bulk material handling.
Material Characteristics and Classification
Understanding the properties of the material being conveyed is essential for designing an efficient conveyor system. CEMA classifies materials based on the following characteristics:
- Particle size: Determines whether fine, granular, or coarse materials are being conveyed.
- Bulk density: Measured in pounds per cubic foot (PCF) or kilograms per cubic meter (kg/m³), it impacts the weight of material on the conveyor.
- Flowability: Some materials may tend to stick, clog, or degrade during transportation.
- Moisture content: Wet materials may require special belt types or cleaning systems to avoid buildup and slippage.
- Abrasiveness: Highly abrasive materials can cause excessive wear on belts, idlers, and pulleys, requiring specialized covers and components.
CEMA provides a classification table that helps engineers select appropriate belt materials and system designs for specific bulk material types.
Capacity and Belt Width Selection
The conveyor’s capacity must align with the intended throughput of the operation. Key factors influencing capacity include:
- Belt width: Wider belts can transport larger volumes of material. Standard belt widths range from 18 inches to 96 inches (450 mm to 2400 mm).
- Belt speed: Faster belt speeds allow for higher throughput, but they also increase wear and energy consumption.
- Troughing angle: Formed by idlers supporting the belt, the trough helps contain bulk materials. Common angles include 20°, 35°, and 45°.
CEMA offers capacity formulas based on these variables, enabling designers to calculate tons per hour (TPH) accurately for the conveyor system.
Power and Tension Calculations
Accurate power calculations ensure the conveyor can operate efficiently while minimizing energy consumption. CEMA provides methods to calculate:
- Effective tension (Te): The tension required to move the loaded belt under normal conditions.
- Breakaway tension: Additional tension needed to start the belt from rest.
- Friction factors: Resistance from idlers, pulleys, and material properties.
- Power demand: Based on belt speed, elevation changes, and material weight.
These calculations help determine the motor size and drive system needed to operate the conveyor reliably under various loading conditions.
Belt Selection and Material Construction
Selecting the appropriate belt type is critical for reliable operation. CEMA provides guidelines for choosing belts based on:
- Tensile strength: Measured in pounds per inch width (PIW) or Newtons per millimeter (N/mm), it defines the belt’s ability to withstand tension.
- Cover material: Abrasion-resistant covers are recommended for rough materials, while oil-resistant or flame-retardant covers may be necessary for specific environments.
- Belt thickness: A thicker belt may be required for heavy loads or long-distance applications to prevent stretching and wear.
These recommendations ensure that the belt can handle the operational stresses and environmental conditions of bulk material handling.
Conveyor Components and Idlers
CEMA provides specifications for critical conveyor components that affect performance and reliability:
- Idlers: These rollers support the belt and guide it along its path. Types include troughing idlers, return idlers, and impact idlers.
- Pulleys: Drive and tail pulleys control belt movement. Lagged pulleys may be used to increase traction and prevent slippage.
- Belt cleaners: Positioned at key points to remove material buildup on the belt and reduce carryback.
- Take-up systems: Maintain proper belt tension to avoid sagging and slippage.
Proper selection and installation of these components are crucial to ensure efficient, trouble-free operation.
Load Transfer and Chute Design
Smooth transfer of material between conveyors or from hoppers to belts is essential to avoid spillage and belt damage. CEMA provides recommendations for:
- Chute design: Properly angled chutes ensure smooth material flow with minimal impact.
- Impact beds: Placed at loading points to absorb the force of falling material and protect the belt.
- Skirt boards: Installed along the conveyor to contain material and prevent spillage.
Well-designed transfer points enhance operational efficiency and reduce maintenance needs.
Environmental Considerations
Conveyors operating in outdoor or hazardous environments must be designed to withstand environmental challenges. CEMA offers guidelines to address:
- Dust control: Use of dust suppression systems or enclosed conveyors to minimize emissions.
- Corrosion resistance: Materials and coatings to withstand corrosive environments.
- Noise reduction: Proper installation of idlers and belt tensioning to minimize noise levels.
- Weather protection: Covers or enclosures to shield belts from rain, snow, or extreme temperatures.
These recommendations help ensure reliable performance while complying with environmental regulations.
Safety Standards and Best Practices
CEMA emphasizes safety in the design, installation, and operation of belt conveyors for bulk materials. Key safety measures include:
- Guards and covers: Protecting workers from moving parts such as belts, pulleys, and idlers.
- Emergency stop systems: Positioned at accessible points along the conveyor for quick shutdown.
- Training programs: Educating personnel on safe conveyor operation and maintenance procedures.
- Regular inspections: Ensuring that belts, idlers, and other components are in good working condition to avoid accidents.
These safety practices reduce risks and ensure compliance with occupational health and safety regulations.
Maintenance and Operational Guidelines
Proper maintenance extends the life of conveyor systems and reduces downtime. CEMA recommends:
- Routine inspections: Regularly checking belt tension, idler alignment, and component wear.
- Lubrication schedules: Ensuring bearings and rollers are properly lubricated to reduce friction.
- Monitoring systems: Sensors and software can detect misalignment, slippage, or belt wear, allowing for timely interventions.
- Spare parts management: Keeping critical components on hand to minimize downtime during repairs.
Adhering to these guidelines helps operators maintain high productivity and reduce long-term costs.
Conclusion
The CEMA Standard for Belt Conveyor for Bulk Materials provides a comprehensive framework for the design, construction, and operation of conveyor systems handling bulk materials. By focusing on material properties, capacity planning, power requirements, environmental factors, and safety practices, the standard ensures that conveyors operate efficiently and reliably. Compliance with these standards minimizes downtime, reduces maintenance costs, and promotes safe, sustainable operations across a variety of industries, including mining, agriculture, and manufacturing.

Accessibility of CEMA Standard for Belt Conveyor PDF: Industry Compliance
The CEMA standard for belt conveyor PDF is readily accessible, making it a pivotal resource for industry professionals who aim to uphold safety and efficiency in conveyor system operations. This document is available in various formats, offering extensive coverage of essential topics such as safety, design, and operational guidelines.
Overview of Document Availability
The CEMA standard for belt conveyor PDF can be found through several channels, ensuring that professionals in the conveyor industry have easy access to these critical guidelines. Available in both print and digital formats, the standard can be purchased directly from the Conveyor Equipment Manufacturers Association (CEMA) website or through authorized distributors. This accessibility supports a wide dissemination of its crucial safety and operational standards, which are foundational for industry practices
Importance of the Standard PDF
The content of the CEMA standard for belt conveyor PDF is indispensable for industry professionals, covering a wide range of topics from safety to detailed design and operational guidelines. This document serves not only as a guideline but also as a benchmark for designing, installing, and maintaining efficient and safe conveyor systems. Access to this PDF ensures that engineering decisions are aligned with the best practices endorsed by CEMA, fostering an environment of safety and efficiency within facilities that rely heavily on conveyor systems.
In-Depth Analysis of CEMA Standard for Belt Conveyor: Core Components for Bulk Materials
The CEMA standard for belt conveyor is exemplified in the “CEMA Belt Conveyors for Bulk Materials” PDF, which serves as a comprehensive guide for the design, safety, and maintenance of conveyor systems. This document is a critical resource for professionals across various industries, providing a robust foundation for the safe and efficient operation of belt conveyors.
Comprehensive Coverage
The “CEMA Belt Conveyors for Bulk Materials” PDF offers an exhaustive overview of topics crucial to the conveyor industry, incorporating a detailed exploration of conveyor belt design and safety guidelines. This document encompasses a wide range of subjects from the fundamental properties of materials being conveyed to the intricate details of conveyor mechanics. The guidelines are meticulously crafted to ensure that all aspects of conveyor design enhance both safety and productivity, adhering strictly to the CEMA standard for belt conveyor. The comprehensive approach ensures that industry professionals have a thorough understanding of the best practices and are equipped to design and operate efficient conveyor systems.
Target Audience and Application
This pivotal document is designed for a broad audience within the conveyor industry, from engineers who are tasked with designing state-of-the-art conveyor systems to field technicians responsible for maintenance and troubleshooting. The application of the CEMA standard for belt conveyor is particularly significant in industries such as mining, manufacturing, and bulk material handling where the reliability and efficiency of conveyor systems are critical. By following the guidelines detailed in this PDF, professionals can ensure that their conveyor systems are not only compliant with industry standards but also optimized for performance and safety. This broad applicability makes the document essential for anyone involved in the design, operation, or maintenance of conveyor systems.
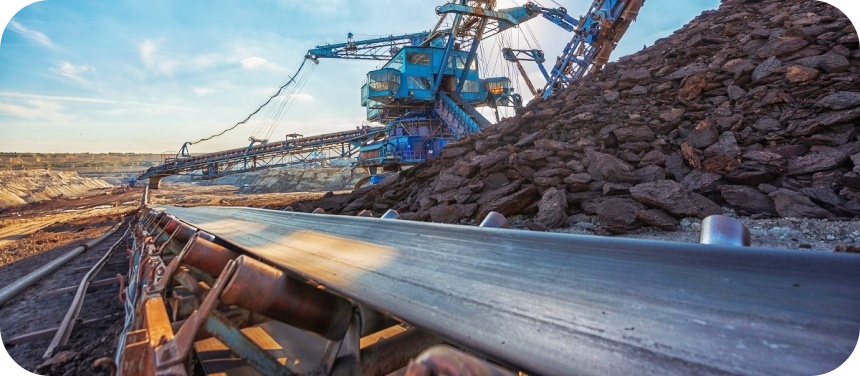
Free Access to CEMA Standard for Belt Conveyor: 7th Edition Bulk Materials
The 7th Edition of the “CEMA Belt Conveyors for Bulk Materials” is an essential update to the CEMA standard for belt conveyor, reflecting the latest advancements in conveyor technology. This edition is freely available under certain conditions, emphasizing CEMA’s dedication to the dissemination of knowledge and the enhancement of safety across the industry.
Availability of Free Resources
Professionals seeking to access the 7th Edition of the “CEMA Belt Conveyors for Bulk Materials” can obtain a free PDF download through various legal avenues. This accessibility is part of CEMA’s commitment to promoting educational opportunities and safety in the conveyor industry. By making these resources available at no cost, CEMA aims to ensure that all industry participants, regardless of company size or budget, have the ability to stay informed about the latest standards and best practices. The availability of such important documents helps maintain a high level of safety and operational excellence across the field.
What’s New in the 7th Edition
The latest edition of this cornerstone document introduces numerous updates and innovations that are critical for modern conveyor systems. These enhancements include advanced safety features, such as improved guard designs and emergency stop protocols, as well as modernized design practices that incorporate the latest materials and technologies. Emphasizing the importance of keeping abreast with these updates, the 7th Edition ensures that professionals are equipped with the knowledge to design, maintain, and operate conveyors that meet today’s highest standards of safety and efficiency. This continuous update cycle reflects CEMA’s ongoing dedication to advancing industry standards and promoting best practices in conveyor design and operation.
CEMA Standard for Belt Conveyor: Screw and Belt Interrelation for Design Safety
The CEMA standard for belt conveyor and the CEMA standard for screw conveyor, though addressing different types of conveyors, share fundamental principles that underscore the importance of a unified approach in conveyor design and safety. This interrelation facilitates a comprehensive understanding that benefits the design and operation of varied conveyor systems within the industry.
Cross-application of Standards
The CEMA standards for screw conveyors offer guidelines that are complementary to those set for belt conveyors, particularly in areas like safety, material handling, and efficiency. By examining how these standards intersect, it becomes evident that many principles, such as load consistency, speed control, and preventive maintenance, are applicable across both types of conveyors. This cross-application enhances a cohesive approach to conveyor design, ensuring that engineers and designers can apply a broad spectrum of best practices that improve the reliability and safety of all conveyor systems under the CEMA umbrella.
Integration in Design Practices
Integrating the standards of screw conveyors with those of belt conveyors can significantly enhance the functionality and safety of conveyor system designs. For instance, the design techniques recommended for screw conveyors regarding bulk material handling can be adapted to improve the loading and discharge methods used in belt conveyors. Such integration not only optimizes the operational efficiency but also bolsters safety measures, providing a well-rounded approach to conveyor system design. Practical examples include the use of similar safety guards, emergency stop systems, and maintenance protocols, which ensure that the conveyors operate under the safest conditions possible, minimizing risks and maximizing efficiency. This comprehensive integration of standards leads to more robust, efficient, and safer conveyor systems, fulfilling the CEMA’s mission of promoting industry-wide best practices.
Exploring the Broad Scope of the CEMA Standard for Belt Conveyor and Beyond
The CEMA standard for belt conveyor is part of a broader suite of guidelines developed by the Conveyor Equipment Manufacturers Association (CEMA) to enhance safety, efficiency, and standardization across various conveyor system designs. These standards collectively facilitate the advancement of conveyor technology and the harmonization of industry practices.
Range of CEMA Standards
CEMA’s standards cover a wide array of conveyor system components, not limited to belt conveyors alone. They extend to rollers, screw conveyors, and other specialized conveying systems, each with detailed guidelines on design, operation, and safety. The diverse range of standards illustrates CEMA’s comprehensive approach to addressing the needs of the conveyor industry. This extensive coverage ensures that all aspects of conveyor system design and operation are underpinned by a set of well-considered and universally applicable guidelines, promoting consistency and safety across industry practices.
Evolving Standards
CEMA standards are dynamic and evolve in response to new technological developments, changes in safety practices, and feedback from industry professionals. This ongoing review and update process ensures that CEMA standards remain at the forefront of industry needs, providing current and relevant guidance that reflects the latest advances in technology and changes in regulatory requirements. Regular updates to the standards help prevent obsolescence, ensuring that conveyor systems are designed and operated in a manner that not only meets current industry demands but also anticipates future trends and challenges. This proactive approach in maintaining and enhancing standards demonstrates CEMA’s commitment to continuous improvement and excellence in conveyor design and safety.
Review of CEMA Conveyor Standards within the CEMA Standard for Belt Conveyor Framework
The CEMA standard for belt conveyor not only addresses the belts themselves but extends to a comprehensive system of standards covering rollers and other critical components. This meticulous approach ensures all aspects of conveyor operations are optimized for safety and efficiency.
Standards for Rollers and Other Components
CEMA’s roller standards are specifically tailored to enhance the operational integrity of belt conveyor systems. These standards stipulate precise guidelines for the design, material selection, and maintenance of rollers, ensuring they can handle the rigorous demands of continuous operation. By defining critical factors such as load capacities, dimensions, and appropriate materials, CEMA standards help ensure that rollers and other conveyor components are both durable and efficient. This level of detail supports the longevity of conveyor systems and minimizes downtime caused by component failure, thereby maintaining the smooth operation of material handling processes.
Benefits of Compliance
Adhering to CEMA standards for belt conveyors and rollers brings multiple advantages to operations. First and foremost, compliance enhances operational efficiency by ensuring that conveyor systems are designed and maintained to operate at peak performance. Safety is another critical area that benefits from adherence to these standards, as they include guidelines that help prevent accidents and ensure the well-being of personnel. Additionally, regulatory compliance is simplified, as CEMA standards are often aligned with national and international safety regulations. By following these standards, companies not only improve their operational capabilities but also build systems that are robust, reliable, and safe, thereby fostering a productive environment and maintaining industry credibility.
Fill out the form to discuss your CEMA standard for belt conveyor needs with our team.
FAQs about Cema Standard For Belt Conveyor
CEMA stands for the Conveyor Equipment Manufacturers Association. This organization sets guidelines and standards that design, manufacture, and application engineers follow to ensure that conveyors and their components are safely and efficiently designed. CEMA has been influential in the material handling industry since its establishment in 1933, promoting standardization to facilitate interchangeability between various conveyor components and systems. CEMA standards cover a wide array of conveyor types including, but not limited to, belt conveyors, screw conveyors, and pulley systems. These standards are used globally by companies to ensure consistency and to promote safety and efficiency in conveyor operations.
CEMA (Conveyor Equipment Manufacturers Association) does not specify a single width for conveyor belts, as the appropriate belt width varies based on the application, material to be conveyed, and the conveyor system design. However, CEMA provides guidance for determining the minimum belt width based on the material lump size, the capacity of the material to be conveyed per hour, and other operational considerations. The standard belt widths as per CEMA specifications start from 12 inches and can go up to 72 inches or more, depending on the requirements of the material handling system. Conveyor designers and engineers use these guidelines to select a suitable belt width for specific applications, ensuring efficient handling and minimal spillage.
The CEMA standards for screw conveyors, specifically detailed in the CEMA 350 book, provide guidelines for the design, engineering, and fabrication of screw conveyors. These standards cover dimensional data, horsepower calculations, and the various classes of screw conveyor applications. CEMA classifies screw conveyors into different categories based on their intended service, such as light, medium, heavy, and extra-heavy-duty services, which dictate the thickness of the screw conveyor’s flights, the type of bearings used, and other construction details. These guidelines ensure that screw conveyors are designed to handle the expected load efficiently and safely. The standards also include recommendations on safety labels, operational instructions, and maintenance practices to prolong the life of the equipment and ensure safety during operation.
The CEMA standard for pulleys (CEMA B502) provides comprehensive guidelines on the design, selection, and application of conveyor pulleys. These standards cover aspects such as pulley dimensions, load ratings, bearing types, shaft dimensions, and safety factors. According to CEMA, pulleys must be designed to handle various stresses such as bending from the tension of the conveyor belt and the load of the material. The standard also specifies requirements for drum and wing pulleys with different hub and bushing systems. By adhering to these standards, manufacturers and engineers ensure that pulleys are durable and can perform reliably in their specific conveyor system environments, thereby reducing downtime and maintenance needs.
CEMA stands for Conveyor Equipment Manufacturers Association. It is a trade organization in North America that establishes standards and best practices for the design, production, and safety of conveyor equipment and systems. CEMA’s guidelines cover areas such as conveyor design, belt specifications, and operational safety. Many industries, such as mining, manufacturing, and food processing, rely on CEMA standards to ensure efficient and safe conveyor operations.
Standard belt widths commonly used in conveyors include 18 inches, 24 inches, 30 inches, 36 inches, 42 inches, 48 inches, 54 inches, 60 inches, 72 inches, and 84 inches. These sizes are selected based on the material to be transported, the volume of the load, and operational requirements. Wider belts are typically used for handling bulk materials such as coal or aggregates, while smaller belts are employed in lightweight and packaged goods industries.
The standard belt width for a conveyor depends on the industry and application. However, for general bulk handling applications, common widths are 24 inches to 48 inches. In industries such as mining or power plants, larger widths like 60 or 72 inches are frequently used to transport heavy or large quantities of materials. For package handling or assembly lines, smaller widths around 18 to 30 inches are more common.
A CEMA C rating refers to a specific standard established by CEMA for conveyor components such as idlers and rollers. This rating applies to medium-duty equipment designed to handle moderate loads with a belt speed up to around 400 feet per minute (FPM). The CEMA C rating ensures the components meet the durability and performance standards required for a wide range of industrial conveyor systems, including agriculture, manufacturing, and mining.
The full form of CEMA is Conveyor Equipment Manufacturers Association. It is an industry association founded to develop technical standards and promote the best practices for conveyor equipment manufacturers. CEMA provides guidelines, engineering tools, and safety recommendations, helping companies across different sectors improve conveyor design and ensure consistency in operations.
Last Updated on October 23, 2024 by Jordan Smith
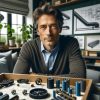
Jordan Smith, a seasoned professional with over 20 years of experience in the conveyor system industry. Jordan’s expertise lies in providing comprehensive solutions for conveyor rollers, belts, and accessories, catering to a wide range of industrial needs. From initial design and configuration to installation and meticulous troubleshooting, Jordan is adept at handling all aspects of conveyor system management. Whether you’re looking to upgrade your production line with efficient conveyor belts, require custom conveyor rollers for specific operations, or need expert advice on selecting the right conveyor accessories for your facility, Jordan is your reliable consultant. For any inquiries or assistance with conveyor system optimization, Jordan is available to share his wealth of knowledge and experience. Feel free to reach out at any time for professional guidance on all matters related to conveyor rollers, belts, and accessories.