The Role of Cement Conveyor Belt in Manufacturing
In the world of cement manufacturing, the cement conveyor belt plays an indispensable role. These belts are pivotal in the efficient handling and transport of raw materials and finished products within the plant. A cement conveyor belt ensures seamless movement, reducing manual labor and enhancing productivity. From the initial stages of cement production to the final transportation of cement, these conveyor belts are integral. They are specifically designed to withstand the heavy loads and harsh conditions typical of cement plants. By focusing on the conveyor belt cement, manufacturers can achieve greater efficiency, reduce operational costs, and ensure a smooth production process from start to finish.
The Evolution of Cement Conveyor Belt Manufacturing
The manufacturing of cement conveyor belts has undergone significant transformations over the years, driven by the need for increased efficiency, durability, and environmental sustainability. From the early days of simple rubber belts to the modern, technologically advanced materials and designs, the evolution of the cement conveyor belt reflects the broader advancements in industrial manufacturing.
Innovations in Cement Conveyor Belt Manufacturing
Cement conveyor belt manufacturers have continually innovated to meet the demanding requirements of cement plants. These innovations have focused on improving the strength, durability, and functionality of conveyor belts to handle the heavy loads and abrasive materials typically found in cement production.
One of the significant advancements in cement conveyor belt manufacturing has been the development of specialized materials. Early conveyor belts were made from natural rubber, which, while effective, had limitations in terms of wear resistance and lifespan. Modern belts use synthetic materials like neoprene, nitrile, and polyurethane, which offer superior durability and resistance to chemicals, oils, and extreme temperatures.
Additionally, the incorporation of advanced reinforcement materials has revolutionized the strength and longevity of cement conveyor belts. Traditional belts used cotton or canvas for reinforcement, which has now been replaced by materials like steel cords, aramid fibers, and polyester. These materials provide enhanced tensile strength, allowing the belts to carry heavier loads and withstand greater wear and tear.
Technological Advancements in Cement Conveyor Belt Production
The production of cement conveyor belts has also benefited from significant technological advancements.
- Steel Cord Belts: Steel cord belts are among the most robust and durable conveyor belts available today. They are made with steel cords embedded within the rubber, providing exceptional strength and resistance to impact and wear. These belts are ideal for high-capacity, long-distance transportation in cement plants, where reliability is crucial.
- Chevron Belts: Chevron belts feature a distinctive V-shaped pattern on their surface, which enhances grip and prevents materials from sliding back, especially on inclined conveyors. This design is particularly useful in cement plants where materials need to be transported at steep angles.
- Heat-Resistant Belts: Cement manufacturing involves the handling of materials at very high temperatures. Heat-resistant belts are designed to withstand these extreme conditions without degrading. They are made from special rubber compounds that maintain their integrity and performance, even when exposed to high temperatures for extended periods.
- Oil-Resistant Belts: In cement plants, conveyor belts often come into contact with oils and chemicals that can degrade the belt material. Oil-resistant belts are made with nitrile rubber or other synthetic materials that resist oil absorption, ensuring longevity and reducing maintenance costs.
- Energy-Efficient Belts: With a growing focus on sustainability, energy-efficient conveyor belts have become increasingly popular. These belts are designed to reduce energy consumption by minimizing rolling resistance. They are typically made with special rubber compounds and optimized structural designs that lower the amount of energy required to move the belt.
Modern Manufacturing Techniques
Modern manufacturing techniques have also played a crucial role in the evolution of cement conveyor belt production. Advances in automation, precision engineering, and quality control have significantly improved the consistency and reliability of conveyor belts.
For example, automated manufacturing processes ensure that each belt is produced to exact specifications, minimizing defects and ensuring uniformity. Precision engineering allows for the creation of complex belt designs, such as chevron patterns, with high accuracy. Quality control systems, including real-time monitoring and testing, ensure that each belt meets the stringent performance standards required for use in cement plants.
Environmental Considerations
In recent years, environmental sustainability has become a key consideration in the manufacturing of cement conveyor belts. Manufacturers are increasingly using recycled materials and developing eco-friendly production processes to reduce their environmental footprint. For instance, some belts are made from recycled rubber and plastics, which not only conserves natural resources but also reduces waste.
Additionally, the development of longer-lasting belts reduces the frequency of replacements, thereby minimizing waste and the environmental impact associated with belt disposal. Innovations in belt design and materials also contribute to lower energy consumption, further enhancing the sustainability of cement conveyor belt manufacturing.
The evolution of conveyor belt cement manufacturing is a testament to the ongoing advancements in industrial technology and materials science. From the early days of simple rubber belts to the modern, high-performance belts made from advanced synthetic materials and reinforced with steel cords, the journey has been marked by continuous innovation and improvement. Today’s cement conveyor belts are more durable, efficient, and environmentally friendly than ever before, ensuring that they can meet the demanding requirements of modern cement plants. As technology continues to advance, we can expect further innovations that will enhance the performance and sustainability of cement conveyor belts even further.
The Journey of a Used Cement Conveyor Belt
Cement conveyor belts play a crucial role in the cement manufacturing process, ensuring the efficient transport of raw materials and finished products throughout the plant. However, like all industrial equipment, these belts have a finite lifespan. The journey of a used cement conveyor belt doesn’t end when it is taken out of service. Instead, it continues through various stages of recycling and repurposing, contributing to environmental sustainability and resource conservation.
Life Cycle of a Cement Conveyor Belt
The life cycle of a cement conveyor belt begins with its manufacture, progresses through its operational phase, and eventually reaches the point where it is no longer suitable for its original purpose. At this stage, the belt is considered used and ready for disposal or repurposing. The life cycle of a cement conveyor belt can be broken down into several stages:
- Manufacturing: The belt is produced using advanced materials and technologies designed to withstand the harsh conditions of cement manufacturing. This includes the use of synthetic rubbers, steel cords, and other reinforcement materials that provide durability and strength.
- Installation and Use: The conveyor belt is installed in the cement plant, where it operates for several years. During this time, it undergoes regular maintenance and inspections to ensure optimal performance and longevity.
- Wear and Tear: Over time, the belt experiences wear and tear due to the abrasive nature of the materials it transports. Eventually, it reaches a point where it can no longer perform effectively and must be replaced.
- Removal: Once the belt is deemed unfit for continued use, it is removed from the conveyor system. At this point, the belt is classified as used and can either be discarded or repurposed.
Recycling and Repurposing Used Cement Conveyor Belts
Recycling and repurposing used cement conveyor belts offer numerous environmental benefits, including reducing waste, conserving resources, and minimizing the environmental impact of industrial operations.
- Recycling into New Products: One of the most common ways to recycle used cement conveyor belts is to process them into new products. The rubber and other materials can be ground down and used to create new belts, rubber mats, playground surfaces, and various other items. This not only reduces the amount of waste sent to landfills but also conserves raw materials.
- Repurposing in Agriculture: Used cement conveyor belts can be repurposed for agricultural use. Farmers and ranchers often use old conveyor belts as durable ground covers, fencing, or even livestock feeders. The belts’ strength and resistance to harsh weather conditions make them ideal for these applications.
- Landscaping and Erosion Control: In landscaping, used conveyor belts can be utilized as liners for ponds, water features, and retaining walls. Additionally, they can be used in erosion control projects to stabilize soil and prevent erosion on slopes and embankments. The belts’ durability and impermeability make them effective in these roles.
- Industrial Applications: Used cement conveyor belts can find new life in other industrial applications. For example, they can be used as protective barriers or mats in areas where heavy machinery operates. The belts’ toughness and resistance to impact make them suitable for protecting surfaces and equipment.
- Art and Furniture: In a more creative approach, some artists and designers repurpose used conveyor belts into unique art pieces and furniture. The belts’ texture and industrial aesthetic provide a distinctive look that can be incorporated into various designs, from chairs and tables to sculptures and wall art.
Environmental Benefits of Reusing and Recycling Conveyor Belts
The environmental benefits of reusing and recycling used cement conveyor belts are significant. By diverting these belts from landfills and finding new uses for them, we can reduce the environmental footprint of cement manufacturing and promote sustainability.
- Waste Reduction: Recycling and repurposing used conveyor belts help reduce the amount of industrial waste that ends up in landfills. This not only conserves landfill space but also reduces the environmental impact associated with waste disposal.
- Resource Conservation: By reusing materials from old conveyor belts, we can conserve natural resources that would otherwise be needed to produce new products. This includes reducing the demand for raw materials such as rubber and steel.
- Energy Savings: Recycling materials from used conveyor belts often requires less energy than producing new materials from scratch. This can result in significant energy savings and a reduction in greenhouse gas emissions associated with manufacturing processes.
- Pollution Prevention: Repurposing used conveyor belts can help prevent pollution by reducing the need for new raw materials and minimizing the environmental impact of mining and processing these materials. Additionally, recycling processes are typically more environmentally friendly than traditional manufacturing methods.
- Sustainable Practices: Embracing the recycling and repurposing of used conveyor belts is an essential aspect of sustainable industrial practices. It demonstrates a commitment to environmental stewardship and responsible resource management, which can enhance the reputation of companies within the cement industry.
The journey of a used cement conveyor belt extends far beyond its initial service life in a cement plant. Through innovative recycling and repurposing efforts, these belts can continue to provide value in various applications while contributing to environmental sustainability. By understanding the life cycle of cement conveyor belts and exploring the many ways they can be reused, we can make more informed decisions that benefit both industry and the environment.
Cement Conveyor Belts for Sale: What to Look For
When it comes to purchasing a cement conveyor belt, several critical factors need to be considered to ensure that you select the right belt for your specific needs. The right choice can significantly enhance the efficiency and durability of your conveyor system, leading to better productivity and lower maintenance costs. Here, we will provide comprehensive guidance on selecting the right cement conveyor belt for sale, focusing on key factors such as size, material, and durability. Additionally, we will offer tips on sourcing from reputable manufacturers and suppliers.
Key Factors to Consider When Selecting a Cement Conveyor Belt
Selecting the right cement conveyor belt involves evaluating several important factors. Here are the primary considerations to keep in mind:
1. Size
The size of the conveyor belt is one of the most critical factors. This includes both the width and length of the belt. The size must match the specifications of your conveyor system to ensure proper operation.
Example:
- Width: If your conveyor system is designed for a 36-inch belt, ensure that the belt you purchase matches this width precisely.
- Length: Measure the required length accurately, considering the layout of your conveyor system. An incorrectly sized belt can cause operational issues and increased wear.
2. Material
The material of the conveyor belt is crucial for its performance and longevity. Different materials offer varying levels of durability, flexibility, and resistance to environmental conditions.
Example:
- Rubber: Traditional rubber belts are suitable for general-purpose applications. They offer good flexibility and durability.
- PVC: Polyvinyl chloride belts are resistant to oils and chemicals, making them ideal for environments where these substances are present.
- Steel Cord: These belts are reinforced with steel cords, providing exceptional strength and durability for heavy-duty applications.
3. Durability
Durability is a key factor, especially in the demanding environment of a cement plant. A durable belt will reduce downtime and maintenance costs.
Example:
- Heat-Resistant Belts: For areas where the belt will be exposed to high temperatures, selecting a heat-resistant belt is essential to prevent premature wear and failure.
- Abrasion-Resistant Belts: In situations where the belt will transport abrasive materials, an abrasion-resistant belt will significantly extend the belt’s lifespan.
4. Load Capacity
The load capacity of the conveyor belt must align with the demands of your operation. This involves understanding the weight and volume of materials that the belt will transport.
Example:
- High Load Capacity: For applications involving heavy materials, choose a belt designed to handle high loads without stretching or breaking.
5. Environmental Resistance
Consider the environmental conditions where the belt will operate. Factors such as temperature, humidity, and exposure to chemicals can affect the belt’s performance.
Example:
- Cold-Resistant Belts: In environments with low temperatures, cold-resistant belts maintain flexibility and strength.
- Oil-Resistant Belts: In areas with oil exposure, oil-resistant belts prevent degradation and maintain performance.
Tips on Sourcing from Reputable Manufacturers and Suppliers
Choosing the right manufacturer or supplier is just as important as selecting the right belt. Here are some tips for sourcing from reputable sources:
1. Research and Reviews
Conduct thorough research on potential manufacturers and suppliers. Look for reviews and testimonials from previous customers to gauge their reliability and product quality.
Example:
- Online Reviews: Check online reviews on platforms like Google and industry-specific forums to gather feedback about the manufacturer’s products and services.
2. Industry Experience
Consider manufacturers and suppliers with extensive experience in the conveyor belt industry. Experienced companies are more likely to offer high-quality products and reliable customer support.
Example:
- Established Brands: Opt for well-known brands that have been in the industry for several years and have a proven track record of delivering quality products.
3. Product Range
A reputable manufacturer should offer a wide range of conveyor belts to cater to different needs. This variety ensures that you can find a belt that matches your specific requirements.
Example:
- Diverse Product Line: Look for suppliers that offer various types of belts, including rubber, PVC, steel cord, and specialized belts like heat-resistant and oil-resistant options.
4. Customization Options
Sometimes, standard conveyor belts may not meet your exact needs. Reputable manufacturers should provide customization options to tailor the belts to your specific requirements.
Example:
- Custom Belts: Choose suppliers that can customize belts in terms of size, material, and other specifications to ensure a perfect fit for your application.
5. After-Sales Support
Reliable after-sales support is crucial for addressing any issues that may arise post-purchase. Ensure that the manufacturer offers comprehensive support, including installation assistance, maintenance tips, and warranty services.
Example:
- Support Services: Select manufacturers that provide robust after-sales support, including technical assistance and warranty coverage.
Selecting the right cement conveyor belt for sale involves careful consideration of factors such as size, material, durability, load capacity, and environmental resistance. By paying close attention to these factors, you can ensure that you choose a belt that meets the demands of your operation and enhances the efficiency and longevity of your conveyor system. Additionally, sourcing from reputable manufacturers and suppliers is essential to guarantee the quality and reliability of your conveyor belt. By following the tips provided, you can make informed decisions and secure a belt that will serve your needs effectively and sustainably.
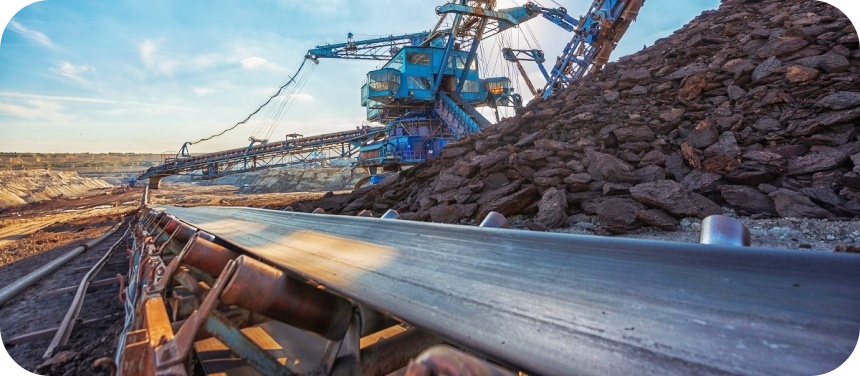
Unraveling the Cement Conveyor Belt Diagram
A cement conveyor belt diagram is a detailed illustration that maps out the components and layout of a conveyor belt system used in cement plants. Understanding this diagram is crucial for anyone involved in the operation, maintenance, or troubleshooting of these systems. This section will explain the typical components of a cement conveyor belt diagram and highlight the importance of understanding these components for effective troubleshooting and maintenance.
Key Components of a Cement Conveyor Belt Diagram
A typical cement conveyor belt diagram includes several key components that work together to ensure the efficient transport of materials. Here are the main components and their functions:
1. Conveyor Belt
The conveyor belt itself is the most critical component. It serves as the moving surface that carries materials from one point to another. In a cement plant, the belt must be strong and durable to handle the heavy loads and abrasive materials typical of cement production.
Example:
- Rubber Belt: A standard rubber belt is often used for its flexibility and resilience. It can withstand high impact and resist wear from abrasive materials.
2. Drive Pulley
The drive pulley is responsible for moving the conveyor belt. It is powered by a motor, and its rotation causes the belt to move. The drive pulley must provide adequate torque to handle the weight of the materials and the resistance of the belt.
Example:
- Motorized Drive Pulley: A motorized drive pulley with sufficient horsepower ensures smooth and consistent belt movement, essential for maintaining production flow.
3. Idler Rollers
Idler rollers support the conveyor belt and help maintain its shape and alignment. These rollers are spaced at regular intervals along the length of the conveyor and can be either flat or trough-shaped, depending on the design of the belt system.
Example:
- Trough Idlers: Trough idlers are used to form the belt into a U-shape, which helps contain bulk materials and prevent spillage.
4. Take-Up Unit
The take-up unit is used to maintain proper tension on the conveyor belt. It compensates for belt stretch and ensures that the belt remains tight and aligned, preventing slippage and improving efficiency.
Example:
- Gravity Take-Up: A gravity take-up unit uses a counterweight to automatically adjust belt tension, ensuring consistent performance.
5. Belt Cleaner
Belt cleaners are installed at various points along the conveyor to remove any material that may stick to the belt. This helps prevent material buildup, which can cause damage to the belt and other components.
Example:
- Scraper: A scraper positioned at the discharge point effectively removes residual material from the belt surface, keeping it clean and reducing wear.
6. Belt Support System
The belt support system includes components like the frame and support structures that provide stability and support to the conveyor belt and its associated components. Proper support is crucial for maintaining belt alignment and preventing sagging.
Example:
- Steel Frame: A robust steel frame provides a sturdy foundation for the entire conveyor system, ensuring stability and reducing the risk of misalignment.
Importance of Understanding the Diagram for Troubleshooting and Maintenance
Understanding the cement conveyor belt diagram is vital for effective troubleshooting and maintenance. Here are five examples that illustrate the importance of this knowledge:
1. Identifying Problem Areas
A thorough understanding of the diagram helps operators identify potential problem areas quickly. For instance, if the belt is misaligned, knowing the location and function of idler rollers and take-up units can expedite the troubleshooting process.
Example:
- Misalignment: By recognizing the role of idler rollers in maintaining belt alignment, maintenance personnel can inspect and adjust these components to correct misalignment issues.
2. Efficient Maintenance
Regular maintenance is essential for the longevity and efficiency of conveyor systems. Understanding the diagram allows for more efficient maintenance scheduling and execution, as technicians can easily locate and service critical components.
Example:
- Belt Tension: Proper belt tension is crucial for optimal performance. Understanding the function and location of the take-up unit enables timely adjustments, preventing issues like belt slippage.
3. Preventing Downtime
Quick and accurate troubleshooting minimizes downtime. Knowing the layout and components of the conveyor system helps operators diagnose and resolve issues promptly, keeping production interruptions to a minimum.
Example:
- Belt Wear: Early detection of belt wear can prevent sudden failures. By regularly inspecting belt cleaners and understanding their placement, operators can replace or service them before they cause significant damage.
4. Enhancing Safety
Safety is a top priority in any industrial setting. Familiarity with the conveyor belt diagram enhances safety by ensuring that operators and maintenance personnel know where to safely access and service the system without exposing themselves to hazards.
Example:
- Emergency Stops: Knowing the location of emergency stop devices and how they integrate into the conveyor system ensures that personnel can quickly shut down the system in case of an emergency.
5. Optimizing Performance
Understanding the conveyor belt diagram helps in optimizing the performance of the system. By knowing how each component contributes to the overall operation, operators can make informed decisions about upgrades and improvements.
Example:
- Energy Efficiency: By understanding the drive pulley’s role and selecting a motor with the appropriate horsepower and efficiency rating, operators can optimize energy use and reduce operational costs.
Unraveling the cement conveyor belt diagram provides invaluable insights into the operation and maintenance of conveyor systems in cement plants. By understanding the key components and their functions, operators and maintenance personnel can troubleshoot issues more effectively, perform efficient maintenance, prevent downtime, enhance safety, and optimize performance. A thorough knowledge of the conveyor belt diagram is essential for ensuring the smooth and efficient operation of cement conveyor systems, ultimately contributing to the productivity and sustainability of cement manufacturing operations.
Systems in Cement Conveyor Belt Plants
Belt conveyor systems are integral to the efficient and cost-effective operation of cement plants. These systems facilitate the continuous movement of materials, from raw components to finished products, significantly enhancing productivity and operational efficiency. Understanding how belt conveyor systems are integrated into cement plants and their impact on material handling efficiency is crucial for optimizing their use.
Integration of Belt Conveyor Systems in Cement Plants
Belt conveyor systems are meticulously designed and strategically integrated into cement plants to streamline the movement of materials. The integration process involves several key steps:
1. Design and Planning
The first step in integrating a belt conveyor system is detailed design and planning. Engineers assess the plant layout, material flow requirements, and specific needs of the cement production process. This includes determining the optimal paths for conveyors to minimize transportation distances and avoid obstacles.
Example:
- Customized Layouts: Engineers design customized conveyor layouts that ensure seamless integration with existing infrastructure, such as silos, crushers, and mills.
2. Installation
Once the design is finalized, the installation phase begins. This involves assembling the conveyor components, such as the belt, drive pulleys, idler rollers, and support structures, on-site. Precision in installation is critical to ensure the system operates smoothly and efficiently.
Example:
- Modular Installation: Using modular components allows for easier installation and future expansions or modifications to the conveyor system.
3. Integration with Plant Systems
The conveyor system is integrated with other plant systems, including material handling equipment, control systems, and safety mechanisms. This ensures that the conveyor operates in harmony with the overall production process.
Example:
- Automated Controls: Conveyor systems are often equipped with automated control systems that synchronize with the plant’s central control system, allowing for real-time monitoring and adjustments.
4. Testing and Commissioning
Before full-scale operation, the conveyor system undergoes rigorous testing and commissioning. This phase ensures that all components are functioning correctly and that the system meets the performance and safety standards.
Example:
- Load Testing: Simulated load testing is conducted to verify the conveyor’s ability to handle the expected material loads without issues.
Efficiency and Cost-Effectiveness of Cement Conveyor Belt Systems
Belt conveyor systems are renowned for their efficiency and cost-effectiveness in material handling within cement plants. Here’s a detailed discussion on these aspects:
1. Continuous Material Flow
One of the primary advantages of belt conveyor systems is their ability to provide a continuous flow of materials. Unlike other transportation methods that may require intermittent stops and starts, conveyor belts operate continuously, ensuring a steady supply of materials to various stages of the production process.
Example:
- Reduced Downtime: Continuous material flow minimizes production downtime, enhancing overall plant efficiency.
2. Energy Efficiency
Modern conveyor belt systems are designed to be energy-efficient. They use advanced materials and technologies that reduce friction and power consumption, making them more sustainable and cost-effective in the long run.
Example:
- Energy-Saving Motors: High-efficiency motors and variable frequency drives (VFDs) are used to optimize energy consumption, reducing operational costs.
3. Labor Cost Reduction
Belt conveyor systems significantly reduce the need for manual labor in material handling. Automated systems can transport large volumes of materials with minimal human intervention, leading to substantial labor cost savings.
Example:
- Automated Loading and Unloading: Automated systems for loading and unloading materials onto and off the conveyor belts reduce the reliance on manual labor.
4. Material Handling Flexibility
Conveyor systems offer flexibility in material handling, accommodating various types of materials, including raw materials, clinker, and finished cement products. They can be customized to handle different material properties and volumes.
Example:
- Adjustable Speed: Conveyor belts with adjustable speeds allow operators to control the flow rate of materials based on production needs.
5. Maintenance and Longevity
Belt conveyor systems are designed for durability and ease of maintenance. Regular maintenance ensures that the systems remain in optimal condition, reducing the likelihood of unexpected breakdowns and extending their operational lifespan.
Example:
- Predictive Maintenance: Modern conveyor systems are equipped with sensors and monitoring devices that enable predictive maintenance, identifying potential issues before they lead to failures.
6. Cost-Effectiveness
The initial investment in a belt conveyor system can be substantial, but the long-term cost benefits are significant. Reduced labor costs, lower energy consumption, and minimal maintenance expenses contribute to the overall cost-effectiveness of these systems.
Example:
- Return on Investment (ROI): Over time, the savings in operational costs and the increased efficiency provided by conveyor systems result in a high ROI for cement plants.
Belt conveyor systems are a cornerstone of material handling in cement plants, offering unparalleled efficiency and cost-effectiveness. Their seamless integration into the production process ensures continuous material flow, reduces labor costs, and enhances energy efficiency. Understanding the design, installation, and operational aspects of these systems is crucial for optimizing their use and achieving the best possible outcomes in cement manufacturing. By leveraging the advantages of belt conveyor systems, cement plants can enhance productivity, reduce operational costs, and contribute to a more sustainable production process.
Types of Cement Conveyor Belt Plants
Belt conveyor systems are vital in the efficient transport of materials within cement plants. Various types of belt conveyors are used, each designed to meet specific needs and conditions in cement production. This section explores different types of belt conveyors, including apron, troughed, and bucket conveyors, and compares their applications, benefits, and challenges.
Different Types of Belt Conveyors
Comparison of Applications, Benefits, and Challenges
Different types of cement conveyor belts offer various advantages and face distinct challenges based on their design and application. Here’s a comparison of their applications, benefits, and challenges:
Understanding the different types of belt conveyors used in cement plants is crucial for optimizing material handling processes. Each type, including apron, troughed, bucket, pipe, and sidewall conveyors, offers unique advantages and faces specific challenges. By selecting the appropriate conveyor type based on material properties, transport distance, and plant layout, cement plants can enhance operational efficiency, reduce maintenance costs, and ensure reliable material transport.
Ready to enhance your operations? Contact us now!
FAQs About Cement Conveyor Belt
The cement industry employs various types of conveyor belts to handle the diverse range of materials involved in the production process. Key types include:
Apron Conveyors: These use overlapping metal plates, making them ideal for handling hot, abrasive materials like clinker. Their robust construction ensures durability in harsh conditions.
Troughed Belt Conveyors: Featuring a belt shaped into a trough by idler rollers, these conveyors are suited for transporting bulk materials over long distances. They are versatile and widely used for both indoor and outdoor applications.
Bucket Elevators: Comprising a series of buckets attached to a belt or chain, these conveyors are used for vertical lifting of materials such as cement powder and granular substances.
Pipe Conveyors: The belt forms a tubular shape to enclose the material, preventing spillage and contamination, making them suitable for transporting dusty or fine materials over long and curved routes.
Sidewall Belt Conveyors: Equipped with corrugated sidewalls, these conveyors can transport materials at steep inclines and even vertical lifts, optimizing space utilization in confined areas.
Each type of conveyor belt serves a specific purpose, tailored to the requirements of different stages in cement production.
The cost of a conveyor belt per foot can vary significantly depending on factors such as the type of belt, the materials used, and the specific requirements of the application. On average, you can expect to pay:
Standard Rubber Belt: $10 to $20 per foot for general-purpose applications.
PVC Conveyor Belt: $15 to $30 per foot, suitable for environments with exposure to oils and chemicals.
Steel Cord Belt: $40 to $100 per foot, offering high durability and strength for heavy-duty applications.
Heat-Resistant Belt: $30 to $60 per foot, designed to withstand high temperatures in industrial settings.
Specialty Belts: Costs can exceed $100 per foot for belts with unique properties or custom designs.
These prices are estimates and can vary based on the belt width, thickness, and additional features such as abrasion resistance or special coatings. It’s advisable to consult with manufacturers or suppliers for precise quotes tailored to your specific needs.
The strongest conveyor belts are typically steel cord belts, renowned for their exceptional tensile strength and durability. These belts consist of steel cords embedded within the rubber, providing unparalleled strength and resistance to impact and wear. Key characteristics include:
High Tensile Strength: Steel cord belts can handle extremely high loads, making them ideal for heavy-duty applications in industries like mining and cement.
Durability: The steel cords enhance the belt’s resistance to cuts, tears, and abrasions, extending its operational lifespan even in harsh environments.
Minimal Elongation: These belts exhibit very low stretch, maintaining their shape and performance under heavy loads and high tension.
Temperature Resistance: Many steel cord belts are designed to withstand extreme temperatures, suitable for applications involving hot materials like clinker in cement plants.
Overall, steel cord conveyor belts are the go-to choice for scenarios demanding the highest strength and durability.
The price of a brick belt conveyor depends on various factors, including its length, width, capacity, and additional features such as automation and material quality. On average, the cost can range from:
Small, Basic Models: $2,000 to $5,000, suitable for smaller operations or specific tasks like loading and unloading bricks.
Medium-Sized Conveyors: $5,000 to $15,000, offering higher capacity and often equipped with more advanced features such as adjustable speeds and improved material handling capabilities.
Large, Industrial-Grade Conveyors: $15,000 to $50,000 or more, designed for extensive brick production facilities. These conveyors are typically robust, durable, and equipped with sophisticated control systems to optimize performance.
Prices can vary based on customization, installation requirements, and supplier pricing policies. It’s essential to get detailed quotes from manufacturers that match the specific operational needs and production scale of your brick handling processes.
Last Updated on July 10, 2024 by Jordan Smith
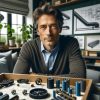
Jordan Smith, a seasoned professional with over 20 years of experience in the conveyor system industry. Jordan’s expertise lies in providing comprehensive solutions for conveyor rollers, belts, and accessories, catering to a wide range of industrial needs. From initial design and configuration to installation and meticulous troubleshooting, Jordan is adept at handling all aspects of conveyor system management. Whether you’re looking to upgrade your production line with efficient conveyor belts, require custom conveyor rollers for specific operations, or need expert advice on selecting the right conveyor accessories for your facility, Jordan is your reliable consultant. For any inquiries or assistance with conveyor system optimization, Jordan is available to share his wealth of knowledge and experience. Feel free to reach out at any time for professional guidance on all matters related to conveyor rollers, belts, and accessories.