Factors Influencing Ceramic Conveyor Prices: A Buyer’s Guide
Ceramic conveyor systems are specialized types of conveyors that utilize ceramic materials for their belts or components. These systems are known for their exceptional durability, heat resistance, and ability to handle abrasive materials, making them ideal for use in high-temperature and heavy-duty environments. Ceramic conveyors find applications in industries such as ceramics manufacturing, metalworking, and glass production, where traditional conveyor materials might fail due to extreme conditions. The importance of ceramic conveyors lies in their ability to maintain efficiency and reliability under harsh conditions, thereby ensuring smooth operations and minimizing downtime. Their robustness and longevity make them a valuable asset in various industrial settings.
Ceramic Conveyor for Sale
Detailed Explanation of What Ceramic Conveyors Are
A ceramic conveyor is a specialized type of conveyor system designed to transport materials that are subjected to high temperatures, abrasive conditions, or require precise handling. These conveyors are particularly prevalent in industries such as ceramics manufacturing, metallurgy, glass production, and chemical processing. The defining feature of a ceramic conveyor is its ability to maintain structural integrity and performance in harsh environments where traditional conveyors would fail.
Ceramic conveyors often incorporate components made from ceramic materials, such as ceramic rollers, plates, and guides. These ceramic parts are highly resistant to heat, wear, and corrosion, making them ideal for transporting hot, abrasive, or chemically aggressive materials. The ceramic elements can withstand temperatures that would damage or deform metal or plastic parts, ensuring the conveyor’s longevity and reliability.
The design of a ceramic conveyor varies depending on its intended application. Some ceramic conveyors are belt-driven, using ceramic-coated belts to transport materials, while others might use ceramic plates or rollers in a more rigid, modular configuration. Regardless of the specific design, all ceramic conveyors share the common goal of providing durable and efficient material transport under challenging conditions.
Benefits of Purchasing Ceramic Conveyors for Industrial Use
Investing in ceramic conveyors offers numerous benefits for industrial operations, particularly those dealing with extreme conditions or requiring high precision. Here are some key advantages:
- Durability and Longevity: Ceramic conveyors are designed to withstand harsh operating environments. The use of ceramic components ensures that the conveyor can handle high temperatures, abrasive materials, and corrosive substances without suffering significant wear and tear. This durability translates to a longer lifespan for the equipment, reducing the need for frequent replacements and minimizing downtime.
- High Temperature Resistance: One of the primary benefits of ceramic conveyors is their ability to operate at high temperatures. Industries such as ceramics manufacturing and metallurgy often require the transportation of materials that are heated to several hundred degrees Celsius. Ceramic conveyors can handle these temperatures without deforming or losing structural integrity, ensuring continuous and efficient operation.
- Abrasion and Corrosion Resistance: Ceramic materials are inherently resistant to abrasion and corrosion, making them ideal for applications where materials are rough, sharp, or chemically reactive. This resistance helps maintain the conveyor’s performance and reduces maintenance needs, as the ceramic parts do not wear down as quickly as metal or plastic alternatives.
- Precision and Stability: Ceramic conveyors provide precise and stable material handling, which is crucial in industries where accuracy is essential. The rigidity and stability of ceramic components ensure that materials are transported smoothly and consistently, reducing the risk of errors and improving overall product quality.
- Reduced Maintenance Costs: The robust nature of ceramic conveyors means they require less frequent maintenance compared to traditional conveyors. This reduction in maintenance needs lowers operational costs and minimizes production interruptions, contributing to a more efficient and cost-effective operation.
- Improved Safety: Ceramic conveyors can enhance workplace safety by reducing the risk of equipment failure and accidents. Their ability to withstand extreme conditions and handle hazardous materials safely ensures that operations run smoothly and securely, protecting both workers and equipment.
- Energy Efficiency: Some ceramic conveyor systems are designed to be energy-efficient, using advanced materials and engineering techniques to reduce power consumption. This efficiency can lead to significant energy savings over time, making ceramic conveyors an environmentally friendly and cost-effective choice.
- Versatility: Ceramic conveyors can be customized to suit a wide range of applications and industries. Whether it’s a high-temperature kiln conveyor or a chemical-resistant transport system, ceramic conveyors can be tailored to meet specific operational requirements, providing versatile and reliable material handling solutions.
Purchasing ceramic conveyors for industrial use offers substantial benefits, including durability, high temperature and abrasion resistance, precision, reduced maintenance costs, improved safety, energy efficiency, and versatility. These advantages make ceramic conveyors a valuable investment for industries looking to optimize their material handling processes under challenging conditions.
Advantages of Used Ceramic Conveyor Systems
Explanation of Used Ceramic Conveyors
Used ceramic conveyors are pre-owned conveyor systems that have been refurbished and made available for resale. These conveyors have previously been employed in industrial settings and are now offered at a reduced cost compared to new systems. Used ceramic conveyors can vary in age, condition, and configuration, but they are typically maintained and restored to ensure they remain functional and reliable for future use.
Purchasing used ceramic conveyors involves sourcing these systems from suppliers who specialize in second-hand industrial equipment. These suppliers inspect, refurbish, and test the conveyors to ensure they meet operational standards before offering them for sale. Used ceramic conveyors can include various types, such as belt-driven, roller, or plate conveyors, each designed to handle specific industrial applications.
Benefits of Opting for Second-Hand Ceramic Conveyor Systems
Opting for used ceramic conveyor systems can provide several advantages, making them an attractive option for many businesses:
- Cost Savings: One of the most significant benefits of purchasing used ceramic conveyors is the cost savings. Second-hand equipment is generally available at a fraction of the price of new systems, allowing businesses to invest in high-quality conveyors without a substantial financial outlay. This cost-effectiveness is particularly beneficial for smaller operations or startups with limited budgets.
- Immediate Availability: New conveyor systems often come with long lead times for manufacturing and delivery. In contrast, used ceramic conveyors are typically available for immediate purchase and deployment. This immediacy can be crucial for businesses needing to replace faulty equipment quickly or expand their operations without waiting for new systems to be built.
- Sustainability: Purchasing used equipment is an environmentally sustainable practice, as it reduces the demand for new materials and the energy required to manufacture new systems. By opting for used ceramic conveyors, businesses contribute to environmental conservation and promote the recycling and reuse of industrial equipment.
- Proven Performance: Many used ceramic conveyor systems have a track record of reliable performance in similar applications. This history provides an added level of assurance that the equipment will function effectively in a new setting. Reputable suppliers of used conveyors often refurbish and test the equipment to ensure it meets operational standards, further enhancing its reliability.
- Flexibility and Adaptability: Used ceramic conveyors offer flexibility and adaptability, allowing businesses to experiment with different configurations and setups without committing to the higher costs of new equipment. This flexibility can be particularly beneficial when testing new processes or scaling operations to meet changing demands.
- Reduced Depreciation: New equipment depreciates rapidly in its initial years of use. By purchasing used ceramic conveyors, businesses can avoid the steepest depreciation costs, preserving more of their investment’s value over time. This reduced depreciation makes used equipment a financially prudent choice.
- Access to High-Quality Brands: Used ceramic conveyor markets often feature equipment from well-known and reputable manufacturers. This access allows businesses to acquire high-quality systems that may have been outside their budget if purchased new. Investing in reputable brands ensures reliability and performance, even when the equipment is pre-owned.
- Comprehensive Testing and Refurbishment: Reputable suppliers of used ceramic conveyors typically conduct thorough inspections, testing, and refurbishment to ensure the equipment is in good working condition. This process involves repairing or replacing worn parts, cleaning, and performing operational tests to verify functionality. As a result, businesses can be confident in the reliability and performance of the used conveyors.
- Support and Availability of Parts: Many used ceramic conveyor systems are popular models with readily available spare parts and accessories. This ensures that maintenance and repairs can be carried out efficiently, minimizing downtime and keeping operations running smoothly. Access to parts also simplifies the integration of used conveyors into existing systems.
Opting for used ceramic conveyor systems offers several advantages, including cost savings, immediate availability, sustainability, proven performance, flexibility, reduced depreciation, access to high-quality brands, comprehensive testing and refurbishment, and support for maintenance and repairs. These benefits make used ceramic conveyors a practical and cost-effective solution for businesses seeking reliable material handling equipment without the expense of new systems.
Key Ceramic Conveyor Parts
Identification and Description of Essential Ceramic Conveyor Parts
Ceramic conveyor systems are composed of several key parts, each playing a critical role in the overall functionality and efficiency of the system. Understanding these components and their functions is essential for maintaining and optimizing ceramic conveyors. Here are the essential parts of a ceramic conveyor:
- Ceramic Rollers: Ceramic rollers are cylindrical components that support and guide the conveyor belt. They are made from high-strength ceramic materials that provide excellent wear resistance and durability. Ceramic rollers can withstand high temperatures and abrasive conditions, ensuring smooth and efficient operation. They are essential for maintaining the belt’s alignment and reducing friction.
- Conveyor Belt: The conveyor belt is the primary element that transports materials along the conveyor system. In ceramic conveyors, the belt may be made from ceramic-coated materials or other heat-resistant and durable substances. The belt’s design and material are crucial for handling the specific requirements of the transported materials, such as high temperatures or abrasive properties.
- Drive Unit: The drive unit consists of the motor and gearbox that power the conveyor system. The motor converts electrical energy into mechanical energy, which is then transferred to the gearbox. The gearbox reduces the motor’s speed to a suitable level and increases the torque to drive the conveyor belt. The efficiency and reliability of the drive unit are critical for the smooth operation of the conveyor system.
- Pulleys: Pulleys are essential components that drive and guide the conveyor belt. There are two main types of pulleys: the drive pulley and the tail pulley. The drive pulley is connected to the motor and is responsible for moving the belt, while the tail pulley provides tension and helps guide the belt back towards the drive pulley. Proper maintenance of pulleys is vital as they are subject to wear and tear due to continuous operation.
- Idlers: Idlers are cylindrical rollers that support the conveyor belt and help reduce friction. They are strategically placed along the length of the conveyor to support the weight of the belt and the material being transported. Idlers can be classified into different types, such as carrying idlers, return idlers, and impact idlers, each serving a specific purpose. Carrying idlers support the loaded belt, return idlers support the empty belt on its return journey, and impact idlers are used at loading points to absorb the impact of falling materials.
- Support Frame: The support frame is the structural backbone of the ceramic conveyor system. It provides support for all the other components and ensures the conveyor’s stability and alignment. Frames are typically made from steel or aluminum and are designed to withstand the harsh conditions of industrial environments. Proper design and construction of the frame are essential for the durability and longevity of the conveyor system.
- Loading and Unloading Mechanisms: These mechanisms are used to load materials onto the conveyor belt and unload them at the desired location. Loading mechanisms can include hoppers, chutes, or feeders that direct the materials onto the belt, while unloading mechanisms can consist of discharge chutes or gates that allow controlled release of the materials. The design of these mechanisms must ensure efficient and safe handling of the materials to prevent spillage and contamination.
- Belt Cleaner: Belt cleaners are installed to remove any residual material from the conveyor belt after unloading. This prevents the buildup of material on the belt, which can cause damage and reduce efficiency. Belt cleaners are typically made of rubber or polyurethane and are placed at strategic points along the conveyor to ensure thorough cleaning.
- Safety Devices: Safety devices are integral components that protect both the conveyor system and the personnel operating it. These devices can include emergency stop switches, belt misalignment sensors, and over-speed detectors. They help prevent accidents and ensure that the conveyor operates within safe parameters.
Importance of Each Part in the Overall Functionality of Ceramic Conveyors
Each component of a ceramic conveyor system plays a vital role in its overall functionality and efficiency. Understanding the importance of these parts helps in maintaining and optimizing the system:
- Ceramic Rollers: Ceramic rollers are crucial for reducing friction and maintaining the belt’s alignment. Their high durability and resistance to wear ensure the smooth and efficient operation of the conveyor system. Regular inspection and maintenance of ceramic rollers are essential to prevent operational disruptions and extend the conveyor’s lifespan.
- Conveyor Belt: The conveyor belt is the main transport medium in the system. Its material and design must match the specific requirements of the transported materials. A high-quality belt ensures efficient material transport, minimizes spillage, and reduces the risk of damage or contamination. Regular maintenance and cleaning of the belt are necessary to maintain its performance and longevity.
- Drive Unit: The drive unit powers the conveyor system and determines its operational efficiency. A well-maintained drive unit ensures consistent and reliable movement of the conveyor belt. Regular inspection and maintenance of the motor and gearbox are critical to prevent breakdowns and ensure the smooth operation of the system.
- Pulleys: Pulleys are essential for driving and guiding the conveyor belt. Proper maintenance of pulleys is vital to prevent belt slippage and ensure smooth operation. Regular inspection and replacement of worn pulleys help maintain the system’s efficiency and reduce the risk of operational disruptions.
- Idlers: Idlers support the weight of the conveyor belt and the transported materials, reducing friction and wear. Regular inspection and maintenance of idlers are necessary to ensure they function correctly and prevent belt misalignment. Replacing damaged or worn idlers helps maintain the system’s efficiency and longevity.
- Support Frame: The support frame provides the structural integrity of the conveyor system. A well-designed and maintained frame ensures the stability and alignment of all components, preventing operational issues and extending the system’s lifespan. Regular inspection and maintenance of the frame are essential to identify and address any structural issues.
- Loading and Unloading Mechanisms: Efficient loading and unloading mechanisms are crucial for minimizing material spillage and contamination. Proper design and maintenance of these mechanisms ensure safe and efficient material handling, contributing to the overall efficiency of the conveyor system. Regular inspection and maintenance help prevent operational disruptions and maintain the system’s performance.
- Belt Cleaner: Belt cleaners are essential for maintaining the cleanliness of the conveyor belt. Regular cleaning prevents material buildup, reduces wear and tear, and maintains the system’s efficiency. Proper maintenance and replacement of belt cleaners ensure thorough cleaning and prevent operational issues.
- Safety Devices: Safety devices protect both the conveyor system and personnel. Regular inspection and maintenance of safety devices are critical to ensure they function correctly and prevent accidents. Implementing and maintaining safety measures contribute to a safe and efficient working environment.
Each component of a ceramic conveyor system plays a crucial role in its overall functionality and efficiency. Regular inspection, maintenance, and proper design of these components ensure the system operates smoothly, efficiently, and safely. By understanding the importance of each part, businesses can optimize their ceramic conveyor systems and achieve significant operational improvements.
Ceramic Conveyor Price Considerations
Factors That Influence the Price of Ceramic Conveyors
When investing in a ceramic conveyor, understanding the factors that influence the price is crucial for making an informed decision. Several elements can affect the cost of ceramic conveyors, and being aware of these factors helps in budgeting and financial planning. Here are some key factors that influence the price of ceramic conveyors:
- Material Quality: The quality of materials used in the construction of ceramic conveyors significantly impacts the price. High-quality ceramic components, such as ceramic rollers and plates, offer better durability, heat resistance, and abrasion resistance, which can increase the cost. However, investing in high-quality materials ensures long-term performance and reduces maintenance costs.
- Design and Customization: The complexity of the conveyor design and the level of customization required also affect the price. Customized ceramic conveyors tailored to specific operational needs and dimensions may cost more than standard models. Custom features such as specialized loading and unloading mechanisms, unique belt designs, or additional safety features can add to the overall cost.
- Size and Capacity: The size and capacity of the ceramic conveyor are crucial price determinants. Larger conveyors with higher load capacities require more materials and more robust construction, leading to higher costs. Additionally, the length and width of the conveyor belt, as well as the overall dimensions of the system, influence the price.
- Technological Features: Advanced technological features, such as automated controls, sensors, and monitoring systems, can increase the price of ceramic conveyors. These features enhance the efficiency, reliability, and safety of the conveyor system but come at an additional cost. Investing in advanced technology can lead to long-term operational benefits and cost savings.
- Brand and Manufacturer: The reputation and brand of the manufacturer can also impact the price of ceramic conveyors. Well-known and reputable manufacturers may charge higher prices for their products due to their established track record of quality and reliability. Choosing a reputable brand ensures better customer support, warranty, and availability of spare parts.
- Installation and Setup: The cost of installation and setup is another factor to consider. Some suppliers offer turnkey solutions that include installation and setup services, which can add to the overall price. However, professional installation ensures proper setup and minimizes the risk of operational issues, making it a worthwhile investment.
- Additional Accessories and Spare Parts: The inclusion of additional accessories, spare parts, and maintenance kits can influence the price of ceramic conveyors. These extras can enhance the functionality and longevity of the conveyor system but add to the initial investment cost.
Tips for Budgeting and Financial Planning When Purchasing a Ceramic Conveyor
Effective budgeting and financial planning are essential when purchasing a ceramic conveyor. Here are some tips to help manage the costs and ensure a successful investment:
- Conduct a Needs Assessment: Begin by conducting a thorough needs assessment to determine the specific requirements of your operation. Consider factors such as the type of materials to be transported, the operating environment, and the desired capacity and dimensions of the conveyor. This assessment will help you identify the most suitable ceramic conveyor for your needs and avoid unnecessary expenses.
- Research and Compare Options: Take the time to research and compare different ceramic conveyor options available in the market. Look for suppliers and manufacturers that offer a range of products and compare their features, prices, and customer reviews. Request quotes from multiple suppliers to get a clear understanding of the market rates and available options.
- Consider Total Cost of Ownership: When budgeting for a ceramic conveyor, consider the total cost of ownership, including the initial purchase price, installation costs, maintenance expenses, and potential downtime costs. Investing in a higher-quality conveyor with advanced features may have a higher upfront cost but can result in long-term savings through reduced maintenance and improved efficiency.
- Allocate a Contingency Budget: Allocate a contingency budget to account for any unexpected expenses that may arise during the purchase and installation process. This budget can help cover additional costs such as modifications, unforeseen installation challenges, or the need for extra accessories or spare parts.
- Plan for Maintenance and Upkeep: Include a budget for regular maintenance and upkeep of the ceramic conveyor system. Proper maintenance is essential for ensuring the longevity and performance of the conveyor, and allocating funds for routine inspections, cleaning, and part replacements will help prevent costly breakdowns and extend the system’s lifespan.
- Explore Financing Options: If the upfront cost of purchasing a ceramic conveyor is a concern, explore financing options such as leasing, installment plans, or equipment loans. Financing can help spread the cost over time, making it more manageable and allowing you to invest in high-quality equipment without straining your budget.
- Negotiate with Suppliers: Don’t hesitate to negotiate with suppliers to get the best possible deal. Suppliers may offer discounts, bundled packages, or additional services at reduced rates. Building a good relationship with suppliers can also lead to better after-sales support and maintenance services.
- Seek Expert Advice: Consult with industry experts or engineers who have experience with ceramic conveyors. Their insights and recommendations can help you make informed decisions, avoid common pitfalls, and select the best conveyor system for your specific needs.
By following these tips, you can effectively budget and plan for the purchase of a ceramic conveyor, ensuring that you get the best value for your investment while meeting your operational requirements.
Finding the Best Ceramic Conveyor
Characteristics of High-Quality Ceramic Conveyors
Selecting the best ceramic conveyor involves identifying key characteristics that define high-quality systems. Here are some essential attributes to look for:
- Durability and Robustness: High-quality ceramic conveyors are built to withstand harsh operating conditions, including high temperatures, abrasive materials, and corrosive substances. Look for conveyors with robust construction and high-quality ceramic components that offer excellent wear resistance and longevity.
- Precision and Stability: The best ceramic conveyors provide precise and stable material handling. They should be designed to maintain accurate alignment and consistent movement of materials, minimizing the risk of errors and improving overall efficiency.
- Advanced Technological Features: Modern ceramic conveyors often incorporate advanced technological features such as automated controls, sensors, and monitoring systems. These features enhance the performance, reliability, and safety of the conveyor system, making them more efficient and easier to manage.
- Ease of Maintenance: High-quality ceramic conveyors are designed for easy maintenance. Features such as accessible components, self-cleaning mechanisms, and modular designs facilitate routine inspections and part replacements, reducing downtime and maintenance costs.
- Energy Efficiency: Look for ceramic conveyors that are designed to be energy-efficient. Energy-efficient systems consume less power, leading to lower operational costs and a reduced environmental footprint. Advanced engineering and materials can contribute to improved energy efficiency.
- Safety Features: Safety is a critical consideration in any industrial operation. The best ceramic conveyors are equipped with safety features such as emergency stop switches, protective guards, and belt misalignment sensors to prevent accidents and ensure safe operation.
- Customization Options: High-quality ceramic conveyors offer customization options to meet specific operational needs. Whether it’s adjusting the size, capacity, or configuration, the ability to customize the conveyor ensures it fits seamlessly into your production process.
- Reputable Manufacturer: Choose ceramic conveyors from reputable manufacturers known for their quality and reliability. Established brands with a strong track record provide better customer support, warranty services, and availability of spare parts.
Tips for Selecting the Best Ceramic Conveyor for Specific Needs
Selecting the best ceramic conveyor for your specific needs requires careful consideration and evaluation. Here are some tips to help you make the right choice:
- Define Your Requirements: Start by clearly defining your operational requirements. Consider the type of materials to be transported, the environmental conditions, the required capacity, and any specific features or customizations needed. This clarity will guide your search and help you narrow down your options.
- Evaluate Material Compatibility: Ensure that the ceramic conveyor you choose is compatible with the materials you will be handling. Consider factors such as temperature resistance, abrasion resistance, and chemical compatibility to ensure the conveyor can handle your materials without degradation or damage.
- Assess Load Capacity and Size: Choose a ceramic conveyor with the appropriate load capacity and size for your operation. Ensure that the conveyor can handle the volume and weight of materials you need to transport and that its dimensions fit within your facility’s layout.
- Consider Technological Features: Evaluate the technological features of the conveyor system. Look for automation options, monitoring systems, and advanced controls that can enhance efficiency, reliability, and safety. Advanced features may come with a higher upfront cost but can lead to long-term benefits.
- Review Maintenance Requirements: Consider the maintenance needs of the ceramic conveyor. Choose a system that is easy to maintain and has readily available spare parts. Low maintenance requirements reduce downtime and operational disruptions, leading to cost savings and improved productivity.
- Check Manufacturer Reputation: Research and select conveyors from reputable manufacturers with a proven track record of quality and reliability. Read customer reviews, request references, and evaluate the manufacturer’s customer support and warranty services.
- Request Demos and Trials: If possible, request demos or trials of the ceramic conveyors you are considering. Hands-on evaluation allows you to assess the performance, ease of use, and suitability of the conveyor for your specific application. It also helps identify any potential issues before making a final purchase.
- Consult with Experts: Seek advice from industry experts, engineers, or consultants who have experience with ceramic conveyors. Their insights and recommendations can provide valuable guidance and help you make an informed decision.
- Consider Long-Term Value: When selecting a ceramic conveyor, consider the long-term value rather than just the initial cost. Invest in a high-quality system that offers durability, efficiency, and low maintenance requirements. The long-term benefits of a reliable conveyor system far outweigh the initial investment.
By following these tips, you can select the best ceramic conveyor that meets your specific needs, enhances your operational efficiency, and provides long-term value.
Maintenance Tips for Ceramic Conveyor Parts
Essential Maintenance Practices for Ceramic Conveyor Parts
Proper maintenance is crucial for ensuring the longevity and performance of ceramic conveyor systems. Regular maintenance helps prevent breakdowns, reduces downtime, and extends the lifespan of the equipment. Here are some essential maintenance practices for ceramic conveyor parts:
- Regular Inspections: Conduct regular inspections of all ceramic conveyor parts, including rollers, belts, pulleys, and idlers. Look for signs of wear, damage, or misalignment. Early detection of issues allows for timely repairs and prevents more significant problems from developing.
- Cleaning: Keep the conveyor system clean to prevent the buildup of debris and contaminants that can cause wear and damage. Regularly clean the conveyor belt, rollers, and other components using appropriate cleaning methods and materials. Avoid using harsh chemicals that can degrade the ceramic parts.
- Lubrication: Lubricate moving parts, such as bearings and gears, to reduce friction and wear. Use the recommended lubricants specified by the manufacturer and follow the proper lubrication schedule. Over-lubrication or using the wrong type of lubricant can cause damage, so follow the guidelines carefully.
- Tension and Alignment: Ensure that the conveyor belt is properly tensioned and aligned. Incorrect tension can cause slippage, excessive wear, and damage to the belt and rollers. Regularly check and adjust the tension and alignment to maintain optimal performance.
- Replacement of Worn Parts: Replace worn or damaged parts promptly to prevent further damage to the conveyor system. Keep a stock of essential spare parts, such as rollers, belts, and bearings, to facilitate quick replacements and minimize downtime.
- Monitoring Systems: Utilize monitoring systems and sensors to keep track of the conveyor’s performance. These systems can detect issues such as belt misalignment, excessive vibration, or abnormal temperatures, allowing for proactive maintenance and repairs.
- Documentation and Records: Maintain detailed records of all maintenance activities, including inspections, cleaning, lubrication, and part replacements. Documenting these activities helps track the conveyor’s condition, identify recurring issues, and plan future maintenance schedules.
How to Extend the Lifespan of Ceramic Conveyor Systems Through Proper Care
Proper care and maintenance can significantly extend the lifespan of ceramic conveyor systems, ensuring they remain efficient and reliable for years to come. Here are some strategies to achieve this:
- Develop a Maintenance Schedule: Create a comprehensive maintenance schedule that outlines regular inspection, cleaning, lubrication, and part replacement tasks. Adhere to this schedule consistently to keep the conveyor system in optimal condition.
- Train Personnel: Ensure that all personnel responsible for operating and maintaining the ceramic conveyor are properly trained. They should be familiar with the maintenance schedule, procedures, and safety protocols. Well-trained personnel can identify and address issues promptly, reducing the risk of major breakdowns.
- Use Quality Spare Parts: When replacing parts, use high-quality spare parts that are compatible with the conveyor system. Avoid using cheap or substandard parts, as they can lead to further damage and reduced performance.
- Implement Preventive Maintenance: Focus on preventive maintenance to address potential issues before they become significant problems. Regularly inspect and service the conveyor system, even if there are no apparent issues. Preventive maintenance helps avoid unexpected breakdowns and extends the equipment’s lifespan.
- Monitor and Adjust: Continuously monitor the performance of the conveyor system and make necessary adjustments to maintain optimal operation. This includes checking tension, alignment, and lubrication levels. Regular monitoring helps identify trends and potential issues early, allowing for timely intervention.
- Protect Against Environmental Factors: Protect the conveyor system from harsh environmental factors such as extreme temperatures, moisture, and dust. Use appropriate covers, enclosures, and barriers to shield the conveyor from these elements. Environmental protection helps prevent damage and extends the system’s lifespan.
- Upgrade and Modernize: Consider upgrading and modernizing the conveyor system with advanced technology and features. Modern sensors, automation, and monitoring systems can enhance performance, improve efficiency, and reduce maintenance needs. Upgrading the system can also extend its lifespan and ensure it remains competitive with new advancements.
- Conduct Regular Audits: Perform regular audits of the conveyor system to assess its condition and identify areas for improvement. Audits should include a thorough inspection of all components, performance evaluation, and a review of maintenance records. Use the audit findings to refine maintenance practices and implement necessary upgrades.
- Engage Professional Services: Utilize professional maintenance and repair services for more complex tasks or when specialized expertise is required. Professional services can provide comprehensive maintenance, diagnostics, and repairs, ensuring the conveyor system remains in top condition.
By implementing these strategies and maintaining a proactive approach to care and maintenance, you can extend the lifespan of ceramic conveyor systems and ensure they continue to operate efficiently and reliably. Proper care not only enhances performance but also maximizes the return on investment, making ceramic conveyors a valuable asset for industrial operations.
FAQs about Ceramic Conveyor
Conveyors are essential in various industries for moving materials efficiently. The three primary types of conveyors are belt conveyors, roller conveyors, and chain conveyors. Belt conveyors use a continuous belt made of various materials, driven by pulleys, to transport items. Roller conveyors consist of a series of rollers supported in a frame over which objects are moved manually, by gravity, or by power. Chain conveyors use a chain to move materials along a fixed path and are particularly useful for heavy loads and harsh environments.
The best material for a conveyor system depends on the specific application and the type of materials being transported. Common materials include rubber, plastic, fabric, and metal. For general purposes, rubber and plastic are often used due to their flexibility and durability. Metal conveyors, such as those made of stainless steel, are ideal for heavy-duty applications and environments that require high hygiene standards, such as the food and pharmaceutical industries. Ultimately, the choice of material should consider factors like load weight, operating environment, and maintenance requirements.
The strongest conveyor belts are typically made from a combination of materials, including steel cords or synthetic fibers like Kevlar, which offer superior strength and durability. Steel cord belts are especially known for their high tensile strength, making them suitable for transporting heavy materials over long distances and in demanding environments. Kevlar belts provide excellent resistance to impact and tearing, ensuring long-lasting performance even under extreme conditions. The specific application and operating conditions will dictate the best choice for maximum strength and durability.
The most common type of conveyor is the belt conveyor. Belt conveyors are widely used in various industries, including manufacturing, logistics, and mining, due to their simplicity, cost-effectiveness, and versatility. They can transport a wide range of materials, from small parts to large packages, and can be designed to operate in different environments, including inclined or declined paths. Their ability to be customized for different lengths and load capacities makes them a popular choice for many material handling needs.
Last Updated on June 3, 2024 by Jordan Smith
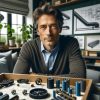
Jordan Smith, a seasoned professional with over 20 years of experience in the conveyor system industry. Jordan’s expertise lies in providing comprehensive solutions for conveyor rollers, belts, and accessories, catering to a wide range of industrial needs. From initial design and configuration to installation and meticulous troubleshooting, Jordan is adept at handling all aspects of conveyor system management. Whether you’re looking to upgrade your production line with efficient conveyor belts, require custom conveyor rollers for specific operations, or need expert advice on selecting the right conveyor accessories for your facility, Jordan is your reliable consultant. For any inquiries or assistance with conveyor system optimization, Jordan is available to share his wealth of knowledge and experience. Feel free to reach out at any time for professional guidance on all matters related to conveyor rollers, belts, and accessories.