Benefits of Ceramic Lagging Conveyor Pulley Systems
Conveyor systems play a crucial role in industrial efficiency, with the global market for conveyor belts expected to reach $5.5 billion by 2026. A key component of these systems is the conveyor pulley lagging, which is essential for maintaining friction and grip, preventing slippage, and ensuring smooth operation, particularly in harsh environments. Ceramic lagging conveyor pulley solutions offer superior durability and performance, making them ideal for demanding applications. This article will explore ceramic lagging for conveyor pulleys, focusing on its benefits, types, and specific products like Flexco ceramic lagging and diamond lagging, to help you choose the best option for your needs.
Ceramic Lagging Conveyor Pulley
A ceramic lagging conveyor pulley is a critical component in various industries where conveyor belts are used to transport materials. This advanced pulley design incorporates ceramic lagging to enhance durability, performance, and efficiency. In this section, we will delve into the importance of ceramic lagging, focusing on its durability, performance, and its ability to enhance grip and friction.
Importance of Ceramic Lagging
Ceramic lagging is a specialized type of pulley lagging that uses ceramic tiles or inserts on the surface of the pulley. This material choice offers several advantages over traditional rubber lagging, making it a preferred option in many industrial applications.
Durability and Performance
One of the primary reasons for using ceramic lagging in conveyor pulleys is its exceptional durability and performance. Ceramic materials are renowned for their hardness and wear resistance, which are crucial properties in environments where pulleys are exposed to abrasive materials and harsh conditions.
- Wear Resistance: Ceramic lagging significantly outlasts traditional rubber lagging. The ceramic inserts are designed to withstand continuous exposure to abrasive materials, reducing the frequency of maintenance and replacement. This wear resistance is particularly beneficial in industries such as mining, where conveyors transport materials like coal, ores, and aggregates that can quickly degrade less robust materials.
- Longevity: The enhanced durability of ceramic lagging translates to a longer operational life for the conveyor pulley. This longevity not only reduces maintenance costs but also minimizes downtime, leading to increased productivity. In operations where conveyor systems run continuously, the extended life span of ceramic-lagged pulleys can result in substantial cost savings over time.
- Performance Under Harsh Conditions: Ceramic lagging performs exceptionally well in harsh conditions, including high temperatures, heavy loads, and exposure to chemicals. This makes ceramic lagging conveyor pulleys suitable for a wide range of industrial environments, ensuring reliable performance regardless of the operational challenges.
Enhanced Grip and Friction
Another critical advantage of ceramic lagging is its ability to enhance the grip and friction between the pulley and the conveyor belt. This improved interaction is vital for the efficient operation of conveyor systems.
- Minimizing Slippage: One of the main issues in conveyor belt systems is slippage, which can lead to decreased efficiency and increased wear on both the belt and pulley. Ceramic lagging provides a textured surface that significantly increases the friction between the belt and the pulley. This enhanced grip minimizes slippage, ensuring that the conveyor belt moves smoothly and consistently.
- Enhanced Efficiency: By reducing slippage, ceramic lagging enhances the overall efficiency of the conveyor system. The improved friction ensures that the belt maintains its speed and alignment, which is crucial for the accurate and efficient transport of materials. This efficiency is particularly important in industries where precision and timing are critical, such as manufacturing and packaging.
- Load Handling: The increased grip provided by ceramic lagging also allows the conveyor system to handle heavier loads without the risk of slippage. This capability is essential in industries like mining and construction, where conveyor systems are often required to transport large quantities of heavy materials.
Applications of Ceramic Lagging Conveyor Pulley
Ceramic lagging conveyor pulleys are used in a variety of industries due to their durability and performance advantages. Some key applications include:
- Mining: In the mining industry, conveyor systems are exposed to abrasive materials and harsh conditions. Ceramic lagging helps extend the life of the pulleys and ensures reliable performance, even under the most challenging conditions.
- Cement and Aggregate: These industries deal with heavy and abrasive materials. The wear resistance of ceramic lagging makes it an ideal choice for maintaining the efficiency and longevity of conveyor systems.
- Manufacturing: In manufacturing, precision and reliability are paramount. Ceramic lagging conveyor pulleys help maintain the smooth operation of conveyor belts, ensuring consistent and accurate material transport.
- Food Processing: Even in the food industry, where cleanliness and efficiency are crucial, ceramic lagging provides a durable and hygienic solution for conveyor systems.
Installation and Maintenance
The installation of ceramic lagging on conveyor pulleys involves attaching ceramic tiles or inserts to the surface of the pulley. This process requires precision to ensure that the tiles are evenly spaced and securely attached, providing a consistent gripping surface for the conveyor belt.
- Installation Process: Professional installation is recommended to ensure that the ceramic lagging is correctly applied. This process typically involves cleaning the pulley surface, applying adhesive, and attaching the ceramic tiles in a specified pattern. Proper installation ensures maximum performance and longevity.
- Maintenance: While ceramic lagging is highly durable, regular inspection and maintenance are essential to maintain optimal performance. Checking for any signs of wear or damage and addressing them promptly can help extend the life of the lagging and the pulley.
How about Ceramic Lagging Conveyor Pulley
In the world of conveyor systems, the ceramic lagging conveyor pulley plays a critical role in enhancing performance and durability. Ceramic lagging involves applying a ceramic coating to the surface of a pulley, which can significantly improve the pulley’s grip, reduce slippage, and extend the life of both the pulley and the conveyor belt. This makes it a valuable component in heavy-duty and high-stress conveyor applications. Let’s explore the common types of ceramic lagging used in conveyor pulleys.
Common Types of Ceramic Lagging
Dimple Ceramic Lagging
Dimple Ceramic Lagging features a textured surface with a pattern of dimples or protrusions. This design is specifically engineered to provide superior grip, making it ideal for drive pulleys where high traction is necessary. The increased friction that dimple ceramic lagging provides can significantly improve the conveyor system’s performance by reducing slippage and ensuring smoother, more efficient operation.
Dimple ceramic lagging is particularly beneficial in environments where materials are wet, oily, or otherwise prone to slipping. The dimples create additional contact points between the pulley and the belt, enhancing the grip and reducing the likelihood of the belt slipping under load. This type of lagging not only enhances performance but also contributes to the longevity of the conveyor belt by distributing the load more evenly and minimizing localized wear.
Advantages of Dimple Ceramic Lagging:
- Enhanced traction and reduced slippage
- Improved conveyor performance and efficiency
- Extended belt and pulley lifespan
- Ideal for challenging environments with wet or oily conditions
Smooth Ceramic Lagging
Smooth Ceramic Lagging is another type of ceramic lagging used on conveyor pulleys, typically on non-drive pulleys. Unlike dimple ceramic lagging, smooth ceramic lagging offers a more balanced approach between grip and minimizing belt wear. It provides sufficient friction to prevent slippage while being less abrasive compared to dimple ceramic lagging.
Smooth ceramic lagging is suitable for non-drive pulleys because it ensures the belt runs smoothly without excessive friction that could lead to premature wear and tear. This type of lagging is beneficial in applications where the primary goal is to maintain a steady, controlled movement of the conveyor belt without the additional traction required for driving pulleys.
Advantages of Smooth Ceramic Lagging:
- Balanced grip with minimized belt wear
- Suitable for non-drive pulleys
- Ensures smooth and controlled belt movement
- Less abrasive, reducing wear and tear on the belt
Benefits of Using Ceramic Lagging Conveyor Pulley
Implementing a ceramic lagging conveyor pulley in your conveyor system can provide several significant benefits:
- Increased Lifespan: The ceramic coating protects the pulley and belt from wear and tear, leading to a longer lifespan for both components. This reduces the need for frequent replacements and maintenance, saving time and costs.
- Enhanced Performance: The superior grip provided by ceramic lagging improves the overall performance of the conveyor system. It ensures efficient material handling, reduces downtime due to belt slippage, and maintains consistent operational flow.
- Durability: Ceramic lagging is highly durable and resistant to harsh environmental conditions, making it suitable for heavy-duty applications in mining, construction, and other industrial sectors.
- Reduced Maintenance Costs: By minimizing slippage and wear, ceramic lagging reduces the frequency and cost of maintenance. This leads to more reliable operation and lower total cost of ownership.
The Key of Ceramic Lagging Conveyor Pulley
A ceramic lagging conveyor pulley is an essential component in various industrial applications, enhancing the performance and durability of conveyor systems. By incorporating ceramic lagging, these pulleys offer superior wear resistance, reduced slippage, and extended lifespan, even under challenging conditions. This section will delve into the key products available in the market, specifically focusing on Flexco Ceramic Lagging and Diamond Lagging.
Key Products
Flexco Ceramic Lagging
Durability and High Coefficient of Friction
Flexco ceramic lagging is renowned for its exceptional durability and high coefficient of friction, making it a top choice for industries requiring reliable conveyor pulley performance. The ceramic tiles embedded in the lagging provide a hard, wear-resistant surface that significantly extends the life of the pulley. This durability is particularly beneficial in environments where the pulley is exposed to abrasive materials and harsh operating conditions.
The high coefficient of friction offered by Flexco ceramic lagging ensures excellent grip between the pulley and the conveyor belt. This increased friction minimizes slippage, enhancing the overall efficiency and reliability of the conveyor system. The reduced slippage not only improves material handling efficiency but also helps maintain the alignment and speed of the conveyor belt, critical for precise operations.
Performance in Wet or Muddy Conditions
One of the standout features of Flexco ceramic lagging is its performance in wet or muddy conditions. Traditional rubber lagging can struggle in such environments, leading to increased slippage and reduced efficiency. However, the ceramic tiles in Flexco lagging maintain their grip and friction even when wet, ensuring consistent performance regardless of the conditions.
The ability to perform well in wet or muddy environments makes Flexco ceramic lagging ideal for industries such as mining and agriculture, where conveyors often operate in challenging conditions. This reliability helps reduce maintenance requirements and operational downtime, leading to improved productivity and cost savings.
Diamond Lagging
Unique Diamond Pattern
Diamond lagging is another highly effective type of ceramic lagging, characterized by its unique diamond pattern. This pattern provides multiple points of contact between the pulley and the conveyor belt, enhancing grip and reducing the likelihood of slippage. The design ensures that the conveyor belt maintains its speed and alignment, contributing to the smooth operation of the entire conveyor system.
The diamond pattern also helps distribute the load more evenly across the pulley surface, reducing wear and tear and extending the life of both the pulley and the conveyor belt. This even distribution is particularly beneficial in applications involving heavy loads or continuous operation, where consistent performance is crucial.
Excellent Grip and Wear Resistance
The primary advantage of diamond lagging is its excellent grip and wear resistance. The ceramic material used in diamond lagging is highly resistant to abrasion, ensuring that the pulley remains effective over extended periods. This wear resistance is critical in industries such as cement and aggregate, where the conveyor systems are exposed to abrasive materials that can quickly degrade less durable lagging options.
Moreover, the enhanced grip provided by the diamond pattern reduces slippage, which is vital for maintaining the efficiency and reliability of the conveyor system. By preventing slippage, diamond lagging helps avoid interruptions in the material handling process, ensuring that operations run smoothly and efficiently.
Effectiveness in Preventing Material Buildup
Material buildup on conveyor pulleys can lead to several issues, including reduced efficiency and increased wear on the conveyor belt. Diamond lagging is particularly effective in preventing material buildup, thanks to its unique surface design. The diamond pattern creates a self-cleaning effect, dislodging materials that might otherwise accumulate on the pulley surface.
This self-cleaning property is especially valuable in industries where material buildup is a common problem, such as in bulk material handling and processing. By preventing buildup, diamond lagging helps maintain the performance and efficiency of the conveyor system, reducing the need for frequent cleaning and maintenance.
What is Ceramic Lagging Conveyor Pulley
The ceramic lagging conveyor pulley is an essential component in enhancing the performance and longevity of conveyor systems. By applying a ceramic coating to the surface of the pulley, it significantly improves grip, reduces slippage, and extends the lifespan of both the pulley and the conveyor belt. This makes ceramic lagging particularly valuable in heavy-duty and high-stress applications, ensuring efficient and reliable operation in various industrial settings.
Benefits of Ceramic Lagging
Increased Service Life
One of the most significant benefits of using a ceramic lagging conveyor pulley is the increased service life it provides. The robust nature of ceramic lagging materials ensures that both the pulley and the conveyor belt experience less wear and tear, leading to a longer operational lifespan. This durability means that the components do not need to be replaced as frequently, which in turn reduces maintenance costs and downtime.
Ceramic lagging is highly resistant to abrasion and the harsh conditions often found in industrial environments. This resistance to wear and tear means that conveyor systems can operate for extended periods without the need for frequent maintenance or part replacement. In industries such as mining, where equipment is subject to extreme conditions, the increased service life provided by ceramic lagging can be particularly advantageous.
Customizable Coverage
Ceramic lagging can be tailored to meet specific operational needs, offering varying levels of coverage to provide the right amount of friction and grip for different applications. This customization ensures that the conveyor system can handle a wide range of materials and conditions effectively.
For instance, dimple ceramic lagging, which features a textured surface with dimples or protrusions, is ideal for drive pulleys that require high traction. The increased friction provided by the dimples enhances grip and reduces slippage, improving the overall efficiency of the conveyor system. On the other hand, smooth ceramic lagging offers a balanced approach for non-drive pulleys, providing sufficient grip while minimizing belt wear.
This ability to customize the coverage of ceramic lagging ensures that each pulley is optimized for its specific role within the conveyor system. Whether handling heavy loads or maintaining smooth belt movement, the right type of ceramic lagging can significantly improve performance and efficiency.
Eco-Friendly Solutions
In addition to performance benefits, many ceramic lagging products are designed with sustainability in mind. These eco-friendly solutions offer durable and long-lasting performance, reducing waste and the need for frequent replacements. By extending the lifespan of conveyor components, ceramic lagging helps to minimize the environmental impact associated with manufacturing and disposing of these parts.
Moreover, the reduced need for maintenance and part replacement translates into lower energy consumption and fewer resources spent on repairs and production. This commitment to sustainability aligns with the growing demand for eco-friendly industrial practices, making ceramic lagging an attractive option for companies looking to reduce their environmental footprint.
Common Types of Ceramic Lagging
Dimple Ceramic Lagging
Dimple Ceramic Lagging features a textured surface with a pattern of dimples or protrusions. This design is specifically engineered to provide superior grip, making it ideal for drive pulleys where high traction is necessary. The increased friction that dimple ceramic lagging provides can significantly improve the conveyor system’s performance by reducing slippage and ensuring smoother, more efficient operation.
Dimple ceramic lagging is particularly beneficial in environments where materials are wet, oily, or otherwise prone to slipping. The dimples create additional contact points between the pulley and the belt, enhancing the grip and reducing the likelihood of the belt slipping under load. This type of lagging not only enhances performance but also contributes to the longevity of the conveyor belt by distributing the load more evenly and minimizing localized wear.
Smooth Ceramic Lagging
Smooth Ceramic Lagging is another type of ceramic lagging used on conveyor pulleys, typically on non-drive pulleys. Unlike dimple ceramic lagging, smooth ceramic lagging offers a more balanced approach between grip and minimizing belt wear. It provides sufficient friction to prevent slippage while being less abrasive compared to dimple ceramic lagging.
Smooth ceramic lagging is suitable for non-drive pulleys because it ensures the belt runs smoothly without excessive friction that could lead to premature wear and tear. This type of lagging is beneficial in applications where the primary goal is to maintain a steady, controlled movement of the conveyor belt without the additional traction required for driving pulleys.
The Types of Ceramic Lagging Conveyor Pulley
A ceramic lagging conveyor pulley is an essential component in various industrial applications, enhancing the performance and durability of conveyor systems. Ceramic lagging offers superior wear resistance, reduced slippage, and extended lifespan, making it a valuable investment. This section explores key considerations for implementing ceramic lagging, focusing on application specificity, cost vs. durability, and installation and maintenance.
Considerations for Implementation
Application Specificity
When selecting a ceramic lagging conveyor pulley, it is crucial to consider the specific application and operational environment. The choice between dimple and smooth ceramic lagging depends on several factors, including the type of pulley, the nature of the material being transported, and the operational conditions.
- Dimple Ceramic Lagging: This type of lagging features a textured surface with dimples that enhance grip and reduce slippage. Dimple ceramic lagging is ideal for environments where slippage is a significant concern, such as in wet or muddy conditions. The dimples increase the friction between the pulley and the conveyor belt, ensuring smooth operation even in challenging settings.
- Smooth Ceramic Lagging: Smooth ceramic lagging, on the other hand, provides a hard, wear-resistant surface without additional texture. This type of lagging is suitable for applications where the primary concern is abrasion resistance rather than enhanced grip. Smooth ceramic lagging is often used in dry, abrasive environments where the materials being transported do not pose a significant risk of slippage.
Choosing the appropriate type of ceramic lagging based on the specific needs of the application ensures optimal performance and longevity of the conveyor pulley.
Cost vs. Durability
One of the primary considerations when implementing a ceramic lagging conveyor pulley is the cost. While ceramic lagging typically has a higher initial cost compared to traditional rubber options, its long-term benefits make it a cost-effective solution.
- Initial Cost: The initial investment in ceramic lagging is higher due to the cost of materials and the complexity of installation. However, this cost is offset by the numerous advantages that ceramic lagging offers.
- Durability and Longevity: Ceramic lagging is renowned for its exceptional durability and wear resistance. It can withstand harsh conditions and abrasive materials much better than rubber lagging. This durability translates to a longer lifespan for the pulley, reducing the frequency of replacements and maintenance.
- Maintenance Costs: The reduced need for maintenance and repairs is a significant advantage of ceramic lagging. Rubber lagging tends to wear out more quickly, leading to increased maintenance costs and downtime. Ceramic lagging minimizes these issues, ensuring continuous operation and lower overall maintenance expenses.
When considering the cost vs. durability, ceramic lagging proves to be a more cost-effective solution in the long run, especially in demanding industrial environments.
Installation and Maintenance
Proper installation is crucial for maximizing the benefits of a ceramic lagging conveyor pulley. The installation process varies based on the specific product and application, and it is essential to follow best practices to ensure optimal performance.
- On-Site Bonding: One common method of installing ceramic lagging is on-site bonding. This involves applying an adhesive to the pulley surface and then attaching the ceramic tiles or inserts. On-site bonding allows for precise placement of the tiles, ensuring even coverage and maximum grip.
- Pre-Lagged Pulleys: Another option is to use pre-lagged pulleys, which are manufactured with ceramic lagging already in place. This approach simplifies the installation process and ensures consistent quality. Pre-lagged pulleys are particularly beneficial for applications where quick installation is required to minimize downtime.
- Proper Alignment and Tension: During installation, it is essential to ensure proper alignment and tension of the conveyor belt. Misalignment can lead to uneven wear and reduced efficiency. Regular inspections and adjustments are necessary to maintain optimal performance.
- Maintenance Practices: Although ceramic lagging reduces the need for frequent maintenance, regular inspections are still important. Checking for any signs of wear, damage, or misalignment can help address issues before they become significant problems. Maintaining proper tension and alignment also contributes to the longevity of the ceramic lagging.
FAQS about Ceramic Lagging Conveyor Pulley
Ceramic pulley lagging is a type of pulley lagging that involves the application of ceramic tiles to the surface of a conveyor pulley. This type of lagging is designed to increase the grip between the conveyor belt and the pulley, thereby reducing slippage and improving the overall efficiency of the conveyor system. Ceramic lagging is particularly advantageous in environments where the pulley is exposed to abrasive materials, as the ceramic tiles offer superior wear resistance compared to traditional rubber lagging. Additionally, ceramic pulley lagging can enhance the lifespan of the conveyor system by protecting the pulley surface from damage and reducing maintenance requirements. It is widely used in industries such as mining, cement, and steel, where conveyors are subject to harsh operating conditions.
Conveyor pulley lagging can be made from various materials, each chosen based on the specific requirements of the conveyor system. The most common materials include rubber, ceramic, and polyurethane. Rubber lagging is widely used for its flexibility, cost-effectiveness, and ability to provide adequate traction under normal operating conditions. Ceramic lagging, which consists of ceramic tiles embedded in a rubber matrix, offers superior wear resistance and is ideal for abrasive environments. Polyurethane lagging is another option, known for its excellent resistance to wear and impact, making it suitable for heavy-duty applications. Additionally, some specialized lagging materials incorporate a combination of these materials to achieve specific performance characteristics, such as increased grip or improved durability. The choice of lagging material depends on factors like the type of conveyed material, operating conditions, and maintenance considerations.
A lag pulley, also known as a lagging pulley, is a conveyor pulley that has a layer of material applied to its surface to improve grip and reduce slippage between the pulley and the conveyor belt. The lagging material can be made from rubber, ceramic, or other durable substances and is designed to increase friction, thereby enhancing the efficiency and reliability of the conveyor system. Lag pulleys are essential in applications where the conveyed material or the operating environment causes slippage, leading to decreased productivity and potential damage to the conveyor components. By using lag pulleys, operators can ensure better belt alignment, reduced wear and tear, and extended service life of the conveyor system. Lag pulleys are commonly used in various industries, including mining, manufacturing, and logistics, where conveyors play a critical role in material handling processes.
The thickness of pulley lagging varies depending on the application, the type of lagging material used, and the specific requirements of the conveyor system. For rubber lagging, the thickness typically ranges from 6 mm to 25 mm, with the choice depending on factors such as the conveyor’s load capacity, speed, and operating conditions. Ceramic lagging often has a thickness between 10 mm and 15 mm, providing a balance between durability and performance. Polyurethane lagging thickness can vary but usually falls within a similar range to rubber lagging. In some specialized applications, thicker lagging may be used to provide additional protection and longevity, especially in highly abrasive environments. It is crucial to select the appropriate lagging thickness to ensure optimal performance, longevity, and cost-effectiveness of the conveyor system. Consulting with conveyor equipment manufacturers or experts can help determine the most suitable lagging thickness for specific operational needs.
Last Updated on June 7, 2024 by Jordan Smith
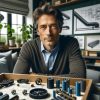
Jordan Smith, a seasoned professional with over 20 years of experience in the conveyor system industry. Jordan’s expertise lies in providing comprehensive solutions for conveyor rollers, belts, and accessories, catering to a wide range of industrial needs. From initial design and configuration to installation and meticulous troubleshooting, Jordan is adept at handling all aspects of conveyor system management. Whether you’re looking to upgrade your production line with efficient conveyor belts, require custom conveyor rollers for specific operations, or need expert advice on selecting the right conveyor accessories for your facility, Jordan is your reliable consultant. For any inquiries or assistance with conveyor system optimization, Jordan is available to share his wealth of knowledge and experience. Feel free to reach out at any time for professional guidance on all matters related to conveyor rollers, belts, and accessories.