Modern Applications of Chevron Belt Conveyor Design
Chevron belt conveyor design is a specialized configuration used in various industries to enhance the movement of materials, especially on inclined surfaces. The chevron pattern, characterized by its V-shaped cleats, provides improved grip and stability, ensuring efficient material transport. This design reduces slippage and increases load capacity, making it ideal for handling bulk materials like coal, gravel, and agricultural products. For a comprehensive understanding of the principles and benefits of chevron belt conveyor design, a detailed PDF guide is available for download, offering in-depth insights and practical applications.
Historical Perspective: Old Chevron Belt Conveyor Design
Old Chevron Belt Conveyor Design: Evolution and Innovations
The history of chevron belt conveyor design is a fascinating journey through the annals of industrial engineering. Understanding the origins and progression of these designs offers valuable insights into how modern chevron belt conveyors have come to be. The old chevron belt conveyor design was developed in response to the growing need for efficient material handling systems that could operate under challenging conditions, such as steep inclines and rough terrains.
Early Innovations
The earliest forms of chevron belt conveyors emerged in the mid-20th century. These designs were rudimentary compared to today’s standards but represented a significant advancement in material handling technology. Initially, the belts were made from basic rubber materials, and the chevron patterns were manually cut or molded into the belt surface. These early belts provided improved grip and reduced material slippage, particularly when transporting loose or granular materials.
The chevron pattern itself, characterized by its V-shaped ridges, was an innovative feature that differentiated these belts from traditional flat belts. The pattern created a series of pockets that helped to catch and hold materials, preventing them from sliding back, especially on inclined conveyors. This design made it possible to transport materials up steeper slopes than was previously possible, which was a crucial development for industries such as mining and agriculture.
Advancements in Materials
As the demand for more robust and durable conveyor belts grew, so did the advancements in the materials used in chevron belt conveyor design. In the 1960s and 1970s, synthetic rubbers and polymers began to replace natural rubber, offering enhanced wear resistance and longevity. These new materials could withstand harsher working conditions and prolonged exposure to abrasive substances without deteriorating as quickly as their predecessors.
The introduction of textile reinforcements in the belts marked another significant milestone. These reinforcements, often made from polyester or nylon, provided additional strength and flexibility. This innovation allowed the belts to handle heavier loads and increased the overall durability of the conveyor systems. The combination of advanced rubber compounds and textile reinforcements laid the foundation for the modern chevron belt conveyor designs we see today.
Mechanization and Standardization
The mechanization of chevron belt production processes also played a critical role in the evolution of their design. By the 1980s, automated manufacturing techniques had become commonplace, enabling more precise and consistent production of chevron patterns. This not only improved the quality and reliability of the belts but also made them more affordable and accessible to a wider range of industries.
Standardization of chevron belt conveyor design was another key development during this period. Industry standards were established to ensure compatibility and interchangeability of belts and components across different conveyor systems. This standardization facilitated the widespread adoption of chevron belts and simplified maintenance and replacement processes.
Modern Innovations and Future Directions
In recent years, chevron belt conveyor design has continued to evolve with the integration of advanced technologies and materials. Modern belts are now engineered with enhanced performance characteristics, such as increased heat and chemical resistance, to meet the demands of more specialized applications. Innovations in sensor technology and automation have also led to the development of smart conveyor systems that can monitor and adjust their operation in real-time for optimal efficiency and safety.
The future of chevron belt conveyor design looks promising, with ongoing research and development focused on further improving durability, energy efficiency, and sustainability. As industries continue to seek more efficient and cost-effective material handling solutions, the chevron belt conveyor design will undoubtedly remain a critical component in achieving these goals.
Chevron Belt Conveyor Design: Detailed Chevron Conveyor Belt Specifications
Chevron Conveyor Belt Specifications: A Comprehensive Guide
Chevron conveyor belts are designed with distinct patterns to meet specific material handling needs. These patterns are crucial for improving the efficiency and safety of transporting materials, especially on inclined or slippery surfaces. Understanding the detailed specifications of chevron conveyor belts is essential for selecting the right belt for a given application.
Dimensions and Patterns
Chevron conveyor belts come in a variety of dimensions and patterns to suit different operational requirements. The width of these belts typically ranges from 300 mm to 2200 mm, accommodating various conveyor systems. The thickness of the belts can vary from 4 mm to 20 mm, depending on the type of material being transported and the operating conditions.
The chevron patterns themselves are designed in different shapes and heights. Common patterns include open V, closed V, U-shaped, and Y-shaped designs. The height of the chevrons can range from 5 mm to 32 mm. Higher chevron patterns are used for steeper inclines and heavier loads, providing better grip and reducing the risk of material rollback.
Material Composition
The materials used in the construction of chevron conveyor belts are critical to their performance and durability. The base belt is usually made from high-quality rubber compounds that offer excellent resistance to abrasion, wear, and environmental factors such as temperature and moisture. Common rubber compounds include natural rubber, SBR (styrene-butadiene rubber), and nitrile rubber, each chosen for specific properties like flexibility, strength, and chemical resistance.
Textile reinforcements are embedded within the rubber to enhance the belt’s tensile strength and flexibility. These reinforcements are typically made from polyester, nylon, or a blend of both. Polyester provides low elongation and high tensile strength, making it ideal for heavy-duty applications. Nylon, on the other hand, offers excellent flexibility and fatigue resistance, suitable for dynamic and high-speed operations.
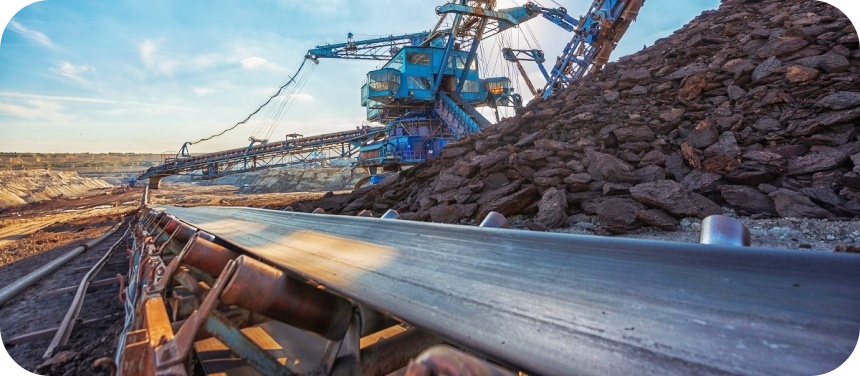
Performance Characteristics
Chevron conveyor belts are designed to provide superior performance in various operating conditions. Key performance characteristics to consider include:
- Grip and Traction: The chevron patterns significantly improve grip and traction on inclined surfaces, reducing material slippage and enhancing safety.
- Load Capacity: The reinforced structure of chevron belts allows them to handle heavier loads compared to flat belts, making them suitable for transporting bulky and dense materials.
- Durability: The combination of robust rubber compounds and textile reinforcements ensures that chevron belts can withstand harsh operating conditions, including abrasion, impact, and exposure to chemicals.
- Flexibility: Despite their reinforced construction, chevron belts maintain a degree of flexibility that allows them to operate smoothly over pulleys and other conveyor components without excessive wear or fatigue.
Application-Specific Specifications
Different industries and applications may require specialized chevron conveyor belt specifications. For instance:
- Mining and Quarrying: Belts used in these industries often feature thicker rubber covers and higher chevron patterns to handle the abrasive nature of materials like ores and rocks. They are also designed to withstand the harsh environmental conditions of mining sites.
- Agriculture: In agricultural applications, chevron belts are used to transport grains, seeds, and other bulk materials. These belts may have lower chevron heights and be made from materials that can resist exposure to moisture and organic matter.
- Construction and Recycling: For transporting construction debris and recyclable materials, chevron belts with high wear resistance and strong reinforcements are essential. These belts are designed to handle sharp and irregularly shaped materials without getting damaged.
Customization and Standards
Manufacturers often provide customization options to meet specific client needs. Customization can include varying the chevron pattern design, adjusting belt dimensions, and selecting specific rubber compounds and reinforcements to match the operational requirements.
Industry standards such as ISO, DIN, and CEMA provide guidelines for the design and manufacturing of chevron conveyor belts. Adherence to these standards ensures the belts meet quality and performance criteria, providing reliability and safety in various applications.
Chevron Belt Conveyor Design: The Role of Textile Conveyor Belt
Textile Conveyor Belt: Enhancing Durability and Performance in Chevron Designs
Textile conveyor belts play a pivotal role in the chevron belt conveyor design, providing essential properties that enhance the overall durability and performance of the system. The integration of textile materials within chevron conveyor belts has revolutionized the material handling industry, enabling the creation of more robust and efficient conveyor solutions.
Textile Materials and Their Properties
Textile materials used in conveyor belts are typically made from synthetic fibers such as polyester, nylon, and aramid. Each of these materials brings unique properties that contribute to the overall performance of the belt.
- Polyester: Known for its low elongation and high tensile strength, polyester is an ideal material for heavy-duty conveyor belts. It provides stability and maintains its shape under high loads, reducing the risk of stretching and deformation over time.
- Nylon: Nylon offers excellent flexibility and resistance to fatigue, making it suitable for dynamic applications where the belt undergoes frequent bending and movement. Its high impact resistance also protects the belt from damage caused by sharp or heavy materials.
- Aramid: This high-performance fiber, often known by the trade name Kevlar, provides exceptional strength and resistance to heat and abrasion. Aramid-reinforced belts are used in extreme conditions where conventional materials might fail.
Benefits of Textile Reinforcements in Chevron Belt Conveyor Design
The incorporation of textile reinforcements in chevron belt conveyor design offers several key benefits:
- Increased Tensile Strength: Textile reinforcements significantly enhance the tensile strength of the belt, allowing it to carry heavier loads without stretching or breaking. This is crucial for applications that involve the transportation of bulky and dense materials.
- Improved Flexibility: Despite their strength, textile reinforcements maintain a degree of flexibility that is essential for the smooth operation of the belt over pulleys and other conveyor components. This flexibility helps to reduce wear and tear on the belt and extends its service life.
- Enhanced Durability: The combination of durable rubber compounds and strong textile reinforcements results in a conveyor belt that can withstand harsh operating conditions, including exposure to chemicals, extreme temperatures, and abrasive materials. This durability reduces the frequency of belt replacements and maintenance, leading to cost savings for the operator.
- Resistance to Impact and Fatigue: Textile-reinforced belts are designed to absorb and dissipate impact energy, protecting the belt from damage caused by heavy or sharp materials. Additionally, their resistance to fatigue ensures that the belt can endure repeated flexing and bending without suffering structural failure.
Applications of Textile Conveyor Belts in Chevron Designs
Textile conveyor belts are used in a wide range of industries and applications where chevron belt conveyor design is employed. Some of the notable applications include:
- Mining and Quarrying: In these industries, conveyor belts must transport large quantities of ore, rock, and other heavy materials. Textile-reinforced chevron belts provide the necessary strength and durability to handle these demanding conditions.
- Agriculture: Chevron belts are used to move grains, seeds, and other agricultural products. The flexibility and strength of textile-reinforced belts ensure efficient and reliable operation, even in environments with varying moisture levels and organic matter.
- Construction: The transportation of construction materials, such as sand, gravel, and debris, requires conveyor belts that can withstand high impact and abrasion. Textile reinforcements provide the necessary durability to handle these harsh materials.
- Recycling: In recycling facilities, conveyor belts transport a variety of materials, including plastics, metals, and paper. Textile-reinforced chevron belts offer the strength and flexibility needed to handle these diverse and often abrasive materials.
Future Trends in Textile Conveyor Belt Technology
The future of textile conveyor belt technology in chevron belt conveyor design is likely to see further advancements in materials and manufacturing processes. Research and development efforts are focused on creating even stronger and more durable fibers, as well as improving the efficiency and sustainability of belt production.
Innovations in nanotechnology and advanced composites may lead to the development of textile materials with enhanced properties, such as increased heat resistance and reduced weight. These advancements will enable the creation of conveyor belts that are not only more robust but also lighter and more energy-efficient.
Furthermore, the integration of smart technologies, such as sensors and monitoring systems, will enhance the performance and reliability of textile-reinforced chevron belts. These systems can provide real-time data on belt conditions, allowing for proactive maintenance and reducing the risk of unexpected failures.
The role of textile conveyor belts in chevron belt conveyor design is integral to the advancement of material handling systems. The unique properties of textile materials, combined with innovative design and manufacturing techniques, continue to drive the development of more efficient, durable, and reliable conveyor solutions. As technology evolves, textile-reinforced chevron belts will undoubtedly play a crucial role in meeting the growing demands of various industries.
Chevron Belt Conveyor Design: Benefits and Applications of Cleated Belt Conveyor Systems
Advantages of Cleated Belt Conveyors
Cleated belt conveyors, including those designed with chevron patterns, offer a multitude of advantages that make them indispensable in various industries. The cleats, which are essentially protrusions on the belt surface, significantly enhance the conveyor’s performance by providing additional grip and preventing material slippage. This section delves into the specific benefits of cleated belt conveyors and highlights their applications, with a particular focus on chevron belt conveyor design.
Enhanced Grip and Traction
One of the most notable advantages of cleated belt conveyors is their enhanced grip and traction. The cleats, arranged in various patterns such as chevron, create a textured surface that firmly grips the material being transported. This feature is particularly beneficial in applications involving steep inclines or declines, where maintaining material stability is crucial. The chevron belt conveyor design, with its V-shaped cleats, is especially effective in preventing slippage, ensuring that materials are transported smoothly and efficiently.
Increased Load Capacity
Cleated belt conveyors can handle heavier loads compared to flat belt conveyors. The cleats provide additional support to the materials, distributing the load more evenly across the belt. This increased load capacity is a significant advantage in industries where large quantities of materials need to be moved efficiently. For instance, in the mining industry, chevron belt conveyors are used to transport heavy ores and aggregates, taking full advantage of the increased load-bearing capabilities of the cleated design.
Versatility in Material Handling
Cleated belt conveyors are highly versatile and can handle a wide range of materials, from fine powders to bulky items. The chevron belt conveyor design is particularly adept at transporting loose and bulk materials such as sand, gravel, and grain. The cleats help to keep the materials centered on the belt, preventing them from spilling over the edges. This versatility makes cleated belt conveyors suitable for use in diverse industries, including agriculture, construction, and logistics.
Improved Material Flow
The cleats on the conveyor belt help to guide and control the flow of materials, ensuring a consistent and predictable movement. This improved material flow is crucial in automated systems where synchronization between different conveyor sections is necessary. The chevron belt conveyor design, with its V-shaped pattern, provides an even more structured flow, making it ideal for applications where precise material handling is required, such as in packaging and assembly lines.
Applications of Cleated Belt Conveyors
Cleated belt conveyors are used in a variety of industries due to their ability to handle challenging material handling tasks. Here are some specific applications where cleated belt conveyors, particularly those with chevron designs, excel:
Mining and Quarrying
In the mining and quarrying industries, cleated belt conveyors are essential for transporting bulk materials such as coal, ore, and aggregates. The chevron pattern provides the necessary grip to move these materials up steep inclines and around curves, ensuring efficient and reliable transportation. The durability and robustness of the cleated design make it suitable for the harsh conditions typically found in mining operations.
Agriculture
Cleated belt conveyors are widely used in the agricultural sector for handling crops, grains, and other agricultural products. The chevron belt conveyor design helps to prevent spillage and ensures that the materials are transported efficiently during harvesting and processing. These conveyors are particularly useful in grain elevators and feed mills, where large volumes of bulk materials need to be moved quickly and efficiently.
Construction
In the construction industry, cleated belt conveyors are used to transport building materials such as sand, gravel, and concrete. The enhanced grip provided by the chevron design ensures that these heavy and often abrasive materials are moved securely over various terrains and inclines. This capability is essential for maintaining the efficiency and safety of construction projects.
Recycling
The recycling industry relies on cleated belt conveyors to transport a variety of materials, including paper, plastic, and metal. The cleats help to keep these materials centered on the belt, reducing the risk of spillage and ensuring efficient processing. The durability of the chevron belt conveyor design makes it ideal for handling the abrasive nature of recycled materials, providing reliable performance over time.
Food Processing
Cleated belt conveyors are also employed in the food processing industry, where they handle products such as fruits, vegetables, and packaged goods. The raised cleats provide the grip needed to move items smoothly through different stages of processing, from sorting to packaging. The choice of food-grade rubber materials ensures that the belts meet hygiene standards and are safe for use in food handling applications.
Logistics and Warehousing
In logistics and warehousing, cleated belt conveyors facilitate the movement of goods and packages. The enhanced grip and material control ensure that items are transported quickly and efficiently, reducing the risk of damage or loss. Chevron belt conveyors can handle a wide range of items, from small packages to large pallets, making them a versatile solution for modern logistics operations.
Waste Management
Cleated belt conveyors play a crucial role in waste management by transporting waste materials to sorting and processing facilities. The V-shaped cleats provide the grip needed to move waste materials, including bulky and irregularly shaped items, up inclines and around curves. This ensures that waste is processed efficiently, contributing to effective waste management and recycling efforts.
Chevron Belt Conveyor Design: Innovations in Trellex Conveyor Belt Technology
Advancements in Trellex Conveyor Belt Technology
Trellex conveyor belts are renowned for their innovative designs and advanced technologies that enhance the efficiency and reliability of conveyor systems. This section highlights the latest advancements in Trellex conveyor belts and their impact on the performance of chevron belt conveyor systems.
High-Performance Materials
One of the key innovations in Trellex conveyor belt technology is the use of high-performance materials. Trellex belts are made from a variety of advanced materials, including reinforced rubber and synthetic compounds, which provide superior durability and resistance to wear and tear. These materials ensure that the belts can withstand harsh operating conditions, such as extreme temperatures, abrasive materials, and heavy loads.
Enhanced Cleat Designs
Trellex has developed enhanced cleat designs that improve the performance of chevron belt conveyors. These cleats are designed to provide optimal grip and traction, reducing slippage and ensuring smooth material flow. The innovative designs also help to distribute the load more evenly across the belt, increasing its load-bearing capacity and extending its lifespan.
Improved Energy Efficiency
Energy efficiency is a critical consideration in modern conveyor systems, and Trellex conveyor belts have been designed to optimize energy consumption. The advanced materials and cleat designs reduce the amount of power required to move materials, leading to lower operational costs and a reduced environmental impact. This energy efficiency is particularly beneficial in large-scale operations where conveyor systems run continuously.
Customizable Solutions
Trellex offers customizable conveyor belt solutions to meet the specific needs of different industries. Customers can choose from a range of belt widths, lengths, and cleat designs to create a conveyor system that is tailored to their requirements. This flexibility ensures that Trellex conveyor belts can be used in a wide variety of applications, from mining and construction to food processing and logistics.
Advanced Monitoring and Control Systems
Trellex conveyor belts are equipped with advanced monitoring and control systems that enhance their performance and reliability. These systems provide real-time data on belt speed, tension, and load, allowing operators to monitor the conveyor system’s performance and make adjustments as needed. The use of advanced sensors and control software helps to prevent downtime and reduce maintenance costs by identifying potential issues before they become major problems.
Impact on Chevron Belt Conveyor Systems
The innovations in Trellex conveyor belt technology have a significant impact on the performance and reliability of chevron belt conveyor systems. Here are some specific ways in which Trellex advancements enhance chevron belt conveyors:
Increased Durability and Longevity
The use of high-performance materials and advanced cleat designs in Trellex conveyor belts increases the durability and longevity of chevron belt conveyor systems. These belts are better able to withstand the wear and tear of transporting heavy and abrasive materials, reducing the frequency of replacements and lowering maintenance costs. This increased durability is particularly valuable in industries with demanding operating conditions, such as mining and construction.
Enhanced Material Handling Efficiency
The improved grip and traction provided by Trellex’s enhanced cleat designs enhance the efficiency of chevron belt conveyor systems. Materials are transported more smoothly and securely, reducing the risk of slippage and spillage. This enhanced material handling efficiency leads to faster processing times and increased productivity, making Trellex conveyor belts a valuable investment for industries that rely on efficient material transport.
Reduced Energy Consumption
The energy-efficient designs of Trellex conveyor belts reduce the amount of power required to operate chevron belt conveyor systems. This reduced energy consumption leads to lower operational costs and a reduced environmental impact, making Trellex conveyor belts an environmentally friendly and cost-effective solution for material handling. The energy savings can be significant, especially in large-scale operations where conveyor systems run continuously.
Improved Safety and Reliability
The advanced monitoring and control systems in Trellex conveyor belts improve the safety and reliability of chevron belt conveyor systems. Real-time data on belt performance allows operators to identify and address potential issues before they lead to downtime or accidents. This proactive approach to maintenance and monitoring enhances the overall safety and reliability of the conveyor system, protecting both workers and equipment.
Chevron Belt Conveyor Design in Modern Material Handling
Modern Design Considerations
Chevron belt conveyor design is a critical aspect of modern material handling systems. This section explores the key design considerations that must be taken into account to ensure the efficiency and effectiveness of chevron belt conveyors.
Material Characteristics
One of the primary considerations in chevron belt conveyor design is the characteristics of the material being transported. Factors such as material size, weight, abrasiveness, and flowability must be considered to select the appropriate belt specifications and cleat design. For example, coarse and heavy materials may require more robust cleats and thicker belt materials to handle the increased load and prevent wear.
Incline and Decl
ine Angles
The incline and decline angles of the conveyor system are crucial design considerations for chevron belt conveyors. The chevron pattern is particularly effective for transporting materials on steep inclines, as the V-shaped cleats provide additional grip and prevent slippage. Designers must carefully calculate the optimal angle for the conveyor system to ensure efficient material transport without compromising stability or safety.
Load Distribution
Proper load distribution is essential for the efficient operation of chevron belt conveyors. Uneven load distribution can lead to belt misalignment, increased wear, and potential system failures. The chevron belt conveyor design must ensure that the load is evenly distributed across the belt to maintain stability and reduce the risk of damage. This can be achieved through the strategic placement of cleats and the use of load distribution devices.
Belt Tension and Speed
Belt tension and speed are critical factors in chevron belt conveyor design. Proper belt tension ensures that the belt remains in contact with the drive and idler pulleys, preventing slippage and maintaining consistent material flow. The speed of the conveyor must also be carefully controlled to match the material handling requirements and prevent overloading or underloading. Advanced control systems can be used to monitor and adjust belt tension and speed in real-time.
Applications in Material Handling
Chevron belt conveyors are used in a variety of modern material handling applications, thanks to their ability to handle challenging tasks with efficiency and reliability. Here are some specific applications where chevron belt conveyor design excels:
Bulk Material Handling
Chevron belt conveyors are widely used in bulk material handling applications, such as the transportation of coal, ore, and aggregates in the mining and quarrying industries. The chevron pattern provides the necessary grip to move these heavy and abrasive materials up steep inclines and around curves, ensuring efficient and reliable transportation.
Agricultural Processing
In agricultural processing, chevron belt conveyors are used to handle crops, grains, and other agricultural products. The enhanced grip provided by the chevron design prevents spillage and ensures that the materials are transported efficiently during harvesting and processing. These conveyors are particularly useful in grain elevators and feed mills, where large volumes of bulk materials need to be moved quickly and efficiently.
Construction and Demolition
Chevron belt conveyors are essential in the construction and demolition industries for transporting building materials such as sand, gravel, and concrete. The chevron pattern ensures that these heavy and often abrasive materials are moved securely over various terrains and inclines, maintaining the efficiency and safety of construction projects.
Recycling and Waste Management
In recycling and waste management, chevron belt conveyors are used to transport a variety of materials, including paper, plastic, and metal. The cleats help to keep these materials centered on the belt, reducing the risk of spillage and ensuring efficient processing. The durability of the chevron design makes it ideal for handling the abrasive nature of recycled materials, providing reliable performance over time.
Food and Beverage Industry
Chevron belt conveyors are also employed in the food and beverage industry, where they handle products such as fruits, vegetables, and packaged goods. The raised cleats provide the grip needed to move items smoothly through different stages of processing, from sorting to packaging. The choice of food-grade rubber materials ensures that the belts meet hygiene standards and are safe for use in food handling applications.
Interested in Our Chevron belt conveyor? Contact Us Now.
Chevron Belt Conveyor Design PDF
For a comprehensive understanding of the principles and benefits of chevron belt conveyor design, a detailed PDF guide is available for download. This guide provides in-depth insights into the key design considerations, material specifications, and practical applications of chevron belt conveyors. It serves as a valuable resource for engineers, designers, and industry professionals looking to implement efficient and reliable material handling solutions.
The PDF guide covers topics such as:
- Overview of chevron belt conveyor design principles
- Detailed specifications and material choices
- Design considerations for various applications
- Case studies and practical examples
- Maintenance and troubleshooting tips
By providing a thorough understanding of chevron belt conveyor design, the PDF guide helps industry professionals optimize their material handling systems for maximum efficiency and reliability.
The chevron belt conveyor design offers numerous advantages across various industries, from improved grip and material control to enhanced durability and energy efficiency. The choice of materials, particularly high-performance rubber and synthetic compounds, significantly impacts the performance and longevity of these conveyors. Innovations in Trellex conveyor belt technology further enhance the efficiency, reliability, and safety of chevron belt conveyor systems.
Modern design considerations, such as material characteristics, incline angles, load distribution, and belt tension, are crucial for optimizing chevron belt conveyor performance. These conveyors are widely used in bulk material handling, agricultural processing, construction, recycling, and the food and beverage industry, demonstrating their versatility and effectiveness in handling challenging material handling tasks.
For a detailed understanding of chevron belt conveyor design, a comprehensive PDF guide is available, offering valuable insights and practical applications to help industry professionals implement efficient and reliable material handling solutions.
FAQs about Chevron Belt Conveyor Design
The maximum inclination of a Chevron conveyor belt typically ranges between 30 to 45 degrees, depending on the specific design and application requirements. Chevron belts are designed with a distinct V-shaped pattern that provides additional grip and traction, making them ideal for transporting materials on steep inclines. The exact maximum inclination can vary based on factors such as the type of material being transported, the belt speed, and the specific pattern of the chevron cleats. In general, the enhanced grip provided by the chevron pattern allows for steeper inclines compared to flat conveyor belts, making them highly effective in industries like agriculture, mining, and construction where transporting bulk materials up sharp inclines is essential.
Designing a conveyor belt system involves several critical steps to ensure efficiency, reliability, and longevity. Start by defining the purpose and requirements of the conveyor, including the type and volume of material to be transported, the conveyor length, and the operating environment. Next, select the appropriate belt type and material, considering factors like load capacity, incline, and environmental conditions. Design the conveyor structure, including the frame, idlers, pulleys, and drive system, ensuring they are robust enough to handle the operational demands. Incorporate safety features such as emergency stops and guards. Calculate the power requirements and select a suitable motor and drive system. Lastly, plan for regular maintenance and inspections to ensure the system remains in optimal working condition. Proper design and planning are crucial for building a conveyor belt system that meets operational needs and maintains high efficiency.
The best angle for a conveyor belt depends on the type of material being transported and the specific application. For flat belts, the maximum incline angle is generally around 20 degrees to prevent material slippage. Chevron and cleated belts, designed for steeper inclines, can handle angles up to 30 to 45 degrees, thanks to their enhanced grip and traction. In applications requiring even steeper inclines, special high-grip belts or bucket conveyors might be used. It’s essential to consider the material’s properties, such as size, weight, and flow characteristics, when determining the best angle. Properly selecting the incline angle ensures efficient material transport and reduces the risk of spillage or belt wear.
The strongest conveyor belts are typically steel cord belts, known for their high tensile strength and durability. These belts are reinforced with steel cords, making them capable of handling extremely heavy loads and long-distance transport. Steel cord conveyor belts are commonly used in mining, heavy industry, and bulk material handling applications where durability and reliability are crucial. They offer excellent resistance to impact, abrasion, and elongation, ensuring a long service life even under harsh operating conditions. The specific strength of a conveyor belt can vary based on the design and materials used, but steel cord belts are widely recognized as the strongest option available.
Last Updated on July 30, 2024 by Jordan Smith
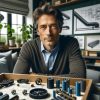
Jordan Smith, a seasoned professional with over 20 years of experience in the conveyor system industry. Jordan’s expertise lies in providing comprehensive solutions for conveyor rollers, belts, and accessories, catering to a wide range of industrial needs. From initial design and configuration to installation and meticulous troubleshooting, Jordan is adept at handling all aspects of conveyor system management. Whether you’re looking to upgrade your production line with efficient conveyor belts, require custom conveyor rollers for specific operations, or need expert advice on selecting the right conveyor accessories for your facility, Jordan is your reliable consultant. For any inquiries or assistance with conveyor system optimization, Jordan is available to share his wealth of knowledge and experience. Feel free to reach out at any time for professional guidance on all matters related to conveyor rollers, belts, and accessories.