Chevron Conveyor Belt Materia: Anti-Slip Conveyor Belt
Chevron conveyor belt material features unique “V” or “U” shaped patterns, essential for preventing material slippage on steep inclines. This design is pivotal in conveyor systems where standard flat belts fail to provide adequate grip, particularly in the mining, agriculture, and recycling industries. The selection of the right material for chevron conveyor belts is crucial, as it directly influences their efficiency and durability. Materials are chosen based on the nature of the materials transported, environmental factors, and the conveyor’s angle of operation. Optimal material selection not only maximizes the functionality of chevron conveyor belts but also extends their lifespan, ensuring they meet stringent industry demands.
What is Specifications of Chevron Conveyor Belt Material for Optimal Performance?
Chevron conveyor belt material is engineered to meet specific requirements and standards that ensure optimal functionality under diverse operational conditions. These specifications vary widely, addressing factors such as the height and width of the chevron patterns, the spacing between them, and the overall thickness and width of the belt. Each of these elements is crucial as they determine the belt’s capacity to handle varying volumes and types of materials without slippage.
Material choice in chevron conveyor belts significantly impacts their performance and durability. For instance, rubber materials are commonly used due to their resilience and ability to form high-relief patterns necessary for gripping large lumps of material. However, for environments involving oils, chemicals, or extreme temperatures, specialized materials such as PVC or polyurethane are preferred to enhance resistance and longevity. These materials are selected based on their ability to withstand wear, tear, and environmental challenges, thereby ensuring that the chevron conveyor belt material not only meets the required specifications but also exceeds the operational demands of industries reliant on efficient bulk material handling.
For optimal performance of chevron conveyor belts, the material specifications must be carefully selected to match the application’s demands. Below are the key specifications to consider:
Material Composition
- Base Material: High-quality natural rubber or synthetic compounds (like SBR, NBR, EPDM) are commonly used in chevron conveyor belt materia. These materials offer a good balance of flexibility, durability, and resistance to abrasion.
- Cover Grade: The outer cover should be made of a wear-resistant compound that can withstand the type of material being conveyed (e.g., oil-resistant, heat-resistant, flame-resistant).
Chevron Pattern
- Height of Cleats: Typically ranges between 5 mm to 32 mm, depending on the angle of incline and the type of material being conveyed.
- Angle of Chevron: Usually between 15° and 40°, optimized based on the incline of the conveyor and the material’s slip characteristics.
- Pattern Design: V-shaped or U-shaped patterns are most common, chosen based on the application. The pattern must be designed to prevent material rollback while allowing for smooth loading and unloading.
Tensile Strength
- Belt Tensile Strength: A typical tensile strength specification might range from 200 N/mm to 315 N/mm, depending on the load requirements.
- Carcass Type: Common carcass types include fabric plies (like EP, NN), steel cord, or a combination, which provide the necessary strength and flexibility.
Abrasion Resistance
- DIN Standards: Abrasion resistance is often specified according to DIN 22102, with abrasion values ranging from less than 120 mm³ to as low as 70 mm³, depending on the application. Lower values indicate higher abrasion resistance.
- Tear Resistance: High tear resistance is crucial, especially for handling sharp or abrasive materials. Specifications might indicate a tear strength of over 25 N/mm.
Temperature Resistance
- Operating Temperature Range: Standard chevron belts typically operate between -20°C to +80°C, but special materials can extend this range (e.g., up to +200°C for heat-resistant belts).
- Cold Resistance: For cold environments, belts may need to resist temperatures as low as -40°C without becoming brittle.
Oil and Chemical Resistance
- Oil-Resistant Grades: For applications involving oily or greasy materials, the belt material should resist degradation. NBR (Nitrile Butadiene Rubber) is commonly used for its oil-resistant properties.
- Chemical Resistance: Special compounds can be added to resist acids, alkalis, and other chemicals, as required by the application.
Belt Width and Thickness
- Standard Widths: Typically available in widths ranging from 300 mm to 2200 mm, depending on the conveyor design.
- Thickness: The overall belt thickness might range from 8 mm to 30 mm, based on the number of plies and the height of the chevrons.
Adhesion Properties
- Adhesion Between Layers: High-quality chevron conveyor belts should have excellent adhesion between the cover and the carcass layers, typically exceeding 3 N/mm, to ensure longevity and resistance to delamination.
Flexibility and Elongation
- Belt Elongation: Should be low, typically less than 1.5% at full load, to minimize stretching and maintain belt tension over time.
- Flexibility: The belt should have adequate flexibility to navigate pulleys and rollers without cracking or breaking.
Flame Resistance
- Fire-Resistant Grades: For applications in hazardous environments, the belt material should be fire-resistant, often meeting standards like ISO 340 or ASTM D378.
Surface Finish
- Rough Top: Some chevron belts may have a rough top finish to further enhance grip on the conveyed materials.
- Smoothness: The smoothness of the belt surface between chevrons should allow for easy cleaning and minimal material buildup.
UV and Ozone Resistance
- Environmental Durability: The belt material should resist degradation due to UV exposure and ozone, particularly for outdoor applications.
The optimal specifications for chevron conveyor belt material depend on the specific requirements of your application. These include material composition, chevron design, tensile strength, abrasion resistance, and other factors that contribute to the belt’s performance, durability, and suitability for the conveyed material and operational environment.
If you have a specific application in mind or need further advice on selecting the right specifications for your needs, feel free to ask for more detailed recommendations.

Choosing Chevron Conveyor Belt Materia
Choosing the right chevron conveyor belt material involves several considerations to ensure that the belt performs optimally for your specific application. Below is a step-by-step guide to help you make an informed decision:
1. Understand Your Application Requirements:
- Material Being Conveyed: Identify the type of material the conveyor belt will handle. Consider factors like abrasiveness, moisture content, temperature, and oil or chemical exposure.
- Conveyor Angle: Determine the incline angle of the conveyor. Chevron belts are particularly useful for steep inclines, so the material should match the specific angle to prevent slippage.
- Load Weight: Understand the load weight that the belt will carry. Heavier loads require belts with higher tensile strength.
2. Choose the Right Base Material:
- Rubber Compounds: Natural rubber or synthetic compounds like SBR (Styrene-Butadiene Rubber), NBR (Nitrile Butadiene Rubber), and EPDM (Ethylene Propylene Diene Monomer) are commonly used. Choose based on the environment (e.g., oil-resistant NBR for greasy materials).
- Cover Grade: Ensure the outer cover is made of a compound resistant to wear, cuts, or abrasion. For special environments, select belts with specific properties like heat, flame, or chemical resistance.
3. Select the Chevron Pattern:
- Height of Cleats: The height of the chevrons should match the angle of incline and the material characteristics. Higher cleats are better for steeper inclines or loose materials.
- Pattern Design: V-shaped or U-shaped patterns are typical. The pattern should effectively prevent material rollback while ensuring smooth transitions and minimal material loss.
4. Evaluate Durability and Strength:
- Tensile Strength: Ensure the belt has adequate tensile strength to handle the load. A higher tensile strength is necessary for heavy-duty applications.
- Abrasion Resistance: Select a belt with a low abrasion value, according to standards like DIN 22102, to extend the belt’s lifespan in abrasive environments.
5. Consider Temperature and Environmental Conditions:
- Temperature Resistance: Choose materials that can withstand the operating temperatures of your application. For example, EPDM is suitable for higher temperatures.
- Environmental Exposure: If the belt will be used outdoors, ensure it has UV and ozone resistance to prevent degradation.
6. Assess Customization Needs:
- Tailored Chevron Design: Depending on your specific needs, you may require a custom chevron pattern or cleat design. Ensure your supplier can provide this customization.
- Belt Width and Thickness: Choose the appropriate width and thickness based on your conveyor design and the material’s weight.
7. Check Supplier Quality and Support:
- Supplier Reputation: Choose a reputable supplier with a history of providing high-quality chevron belts. Look for customer testimonials or industry certifications.
- Technical Support: Ensure the supplier offers robust technical support, including help with installation, maintenance, and troubleshooting.
8. Consider Cost and Warranty:
- Cost-Effectiveness: While cost is a factor, focus on the overall value, including durability, maintenance costs, and belt lifespan.
- Warranty and After-Sales Service: Select a supplier that offers a solid warranty and reliable after-sales support, which can save you money in the long term.
9. Evaluate Lead Times and Supply Chain Reliability:
- Availability: Ensure the supplier can consistently provide the belt material without long lead times that could disrupt your operations.
- Logistics: Consider the location of the supplier and the associated shipping costs and delivery times.
10. Test the Material if Possible:
- Pilot Testing: If possible, conduct a pilot test with a sample of the conveyor belt material in your actual operating conditions to ensure it meets all your performance requirements.
Choosing the right chevron conveyor belt material requires careful consideration of your application’s specific needs, environmental conditions, and the material’s properties. Working with a reputable supplier who offers customization and robust technical support is crucial to ensure you select a belt that will perform effectively and efficiently.
If you have any specific conditions or challenges related to your application, I can help further refine the selection process.
Key Factors of Choosing the Right Supplier for Chevron Conveyor Belt Material
When selecting chevron conveyor belt material, identifying top suppliers who stand out in terms of material quality and innovation is crucial. These suppliers not only offer materials that meet rigorous industry standards but also bring continuous advancements in the technology and composition of their conveyor belts. Notable suppliers excel in providing durable, high-grip chevron patterns crafted from superior rubber or synthetic compounds tailored to specific environmental and operational demands.
Choosing the right supplier for chevron conveyor belt material is a critical decision that can significantly impact your operations’ efficiency, cost-effectiveness, and overall success. Here are the key factors to consider when selecting a supplier:
1. Quality of Materials:
- Material Composition: Ensure the supplier uses high-quality rubber or synthetic compounds that offer durability, resistance to wear and tear, and compatibility with the materials being conveyed.
- Manufacturing Standards: The supplier should adhere to industry standards and certifications, ensuring that their products meet or exceed quality requirements.
2. Customization Capabilities:
- Tailored Solutions: Look for suppliers who can customize the chevron pattern (size, shape, and angle) according to your specific conveyor design and operational needs.
- Flexibility in Design: The supplier should be able to accommodate unique requests, such as specific cleat designs or additional features like oil, heat, or flame resistance.
3. Experience and Expertise:
- Industry Experience: Suppliers with extensive experience in manufacturing chevron conveyor belts for various industries are more likely to understand your needs and challenges.
- Technical Support: Ensure the supplier offers technical expertise, including support for installation, maintenance, and troubleshooting.
4. Supply Chain Reliability:
- Consistent Availability: The supplier should have a reliable supply chain, ensuring consistent availability of materials to prevent operational downtime.
- Lead Times: Evaluate the supplier’s lead times for manufacturing and delivering products, especially if you require custom solutions.
5. Reputation and References:
- Customer Feedback: Check the supplier’s reputation in the market by seeking customer reviews and testimonials. Positive feedback from other companies in your industry can be a good indicator of the supplier’s reliability.
- References: Request references from the supplier to verify their track record in delivering quality products and services.
6. Cost-Effectiveness:
- Price vs. Value: While cost is an important factor, focus on the value offered by the supplier. A cheaper product may lead to higher maintenance costs or shorter lifespan, so consider the overall cost of ownership.
- Warranty and Support: Assess the warranty terms and post-purchase support offered by the supplier. A good warranty can save costs in the long run.
7. Innovative Solutions:
- R&D Capabilities: Suppliers that invest in research and development are likely to offer innovative solutions that enhance the performance and longevity of your conveyor belts.
- Sustainability: Consider suppliers that provide environmentally friendly materials or manufacturing processes if sustainability is a priority for your business.
8. Geographical Proximity:
- Logistics and Shipping: Suppliers located closer to your operations may offer advantages in terms of reduced shipping costs and faster delivery times. However, do not compromise on quality for proximity.
- Local Support: Local suppliers can provide on-site support more easily, which can be crucial for installations or troubleshooting.
9. Compliance and Certification:
- Regulatory Compliance: Ensure the supplier complies with relevant industry regulations and standards, including safety and environmental guidelines.
- Certification: Look for certifications such as ISO, which indicate that the supplier adheres to high standards in manufacturing and quality control.
10. After-Sales Service:
- Maintenance Support: Choose a supplier who offers robust after-sales support, including maintenance services, availability of spare parts, and prompt responses to issues.
- Training and Education: Suppliers who provide training on the installation, use, and maintenance of their products can add significant value.
Selecting the right supplier for chevron conveyor belt material involves a thorough evaluation of their quality, reliability, customization options, and overall value. Prioritizing these factors ensures that you partner with a supplier who can meet your specific needs and support your operations effectively.

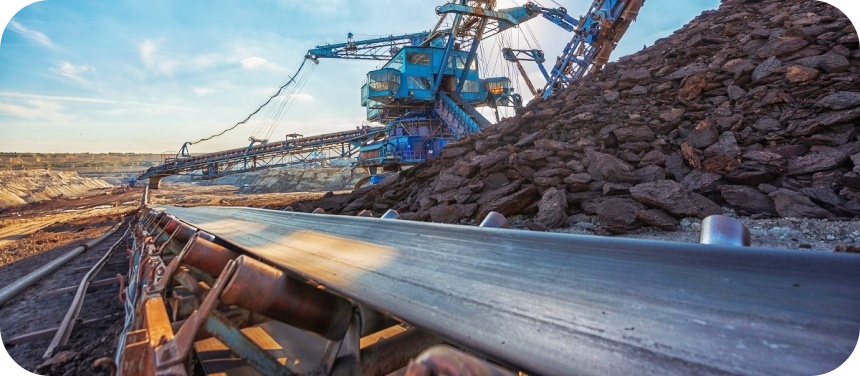
Chevron vs. Rough Top Conveyor Belt Materials
Chevron and rough tip top conveyor belts are designed to address different material handling challenges, each utilizing distinct material properties to optimize performance in specific environments. Chevron conveyor belt material typically features high-profile patterns such as ‘V’ or ‘U’ shapes, which provide excellent grip for transporting materials on inclines, preventing slippage and roll-back. These belts are commonly made from rubber compounds that offer flexibility and durability under stress, making them suitable for industries like mining and agriculture where large volumes of material need to be moved vertically.
On the other hand, rough top conveyor belts are characterized by a textured surface that also enhances grip but in a less aggressive manner than the chevron patterns. This texture is often achieved through materials like PVC or coated fabrics, which provide a softer interface for handling packages or delicate items in industries such as packaging or manufacturing. The rough texture ensures stability and reduces the risk of items shifting or sliding during transit on slight inclines or flat surfaces.
Choosing Between Chevron and Rough Top Conveyor Belts:
The Role of Chevron Conveyor Belt Material in Cleated Belt Conveyors
Cleated belt conveyors utilize raised elements or cleats to securely transport materials at various inclines without slippage. Chevron conveyor belt material plays a critical role in the effectiveness of these conveyors, especially where high grip and precise material placement are needed. The chevron pattern, with its distinctive ‘V’ and ‘U’ shapes, is integral in providing the additional traction required to hold materials in place during transport.
The material used to make chevron conveyor belts is predominantly rubber because of its flexibility, durability, and ability to form high-relief patterns that are essential for effective cleating. The rubber’s elasticity allows the belt to adapt to various loads and resist the mechanical pressures from the movement of bulky or abrasive materials. This adaptability is crucial for applications in industries such as mining, agriculture, and construction, where the belts face rigorous operating conditions.
Impact of Material Choice on Functionality
Chevron conveyor belt material plays a crucial role in the design and function of cleated belt conveyors, which are widely used in various industries for transporting materials at steep inclines. Here’s an overview of the importance and role of this material:
1. Enhanced Grip and Traction:
- Chevron Patterns: The unique V-shaped chevron patterns on the conveyor belt material provide excellent grip, preventing materials from sliding back, especially on steep inclines. This is essential for maintaining a continuous flow of materials in cleated belt conveyors.
- Material Handling Efficiency: The chevron design enhances the conveyor’s ability to handle various materials, including loose or bulk materials like grains, sand, coal, and more.
2. Material Compatibility:
- Rubber and Synthetic Compounds: Chevron conveyor belts are typically made from high-quality rubber or synthetic compounds, making them durable and resistant to wear and tear. This ensures longevity and reduces maintenance needs.
- Versatility: The material is also resistant to oils, chemicals, and weather conditions, making it suitable for diverse industrial applications, from agriculture to mining.
3. Impact on Conveyor Design:
- Customization: The material allows for customization of the chevron pattern (size, shape, and angle) to match specific conveyor design requirements. This adaptability is critical in ensuring the conveyor’s effectiveness in various operational environments.
- Belt Flexibility: The flexibility of the chevron material is vital for the conveyor belt to conform to different angles and contours, making it efficient in transporting materials over uneven terrain.
4. Reduction of Material Spill:
- Cleat Design: The raised sections (cleats) in conjunction with the chevron pattern help in holding the material firmly on the belt, reducing spillage and ensuring that materials reach their destination without loss.
5. Improved Load Carrying Capacity:
- Strength and Durability: Chevron conveyor belt material is designed to support heavier loads due to its strength and durability. This enhances the load-carrying capacity of cleated belt conveyors, making them suitable for heavy-duty applications.
6. Energy Efficiency:
- Reduced Slippage: The material’s grip reduces slippage, which in turn minimizes energy loss. This leads to more energy-efficient operations, which is especially important in large-scale industrial processes.
7. Noise Reduction:
- Smoother Operation: The quality and design of chevron belt material can also contribute to quieter operation, which is beneficial in environments where noise reduction is a priority.
Chevron conveyor belt material is integral to the effectiveness of cleated belt conveyors. Its role in providing traction, durability, and flexibility directly impacts the efficiency, safety, and longevity of the conveyor system, making it indispensable in industries requiring steep incline material handling.
Innovations in Chevron Conveyor Belt Material
The evolution of textile conveyor belt materials has been marked by significant advancements that cater to more complex and demanding industrial environments. Chevron conveyor belt material, with its distinct patterned design, has been at the forefront of this innovation, enhancing the functionality of traditional textile belts.
Textile conveyor belts, traditionally made from layers of fabric such as cotton, nylon, or polyester, are known for their flexibility and lightweight properties. However, these materials often require additional features to handle specific industrial tasks effectively, especially in inclined or high-load situations. This is where the chevron pattern comes into play. The inclusion of chevron patterns on textile belts provides increased traction, prevents material rollback, and ensures a more stable transport of materials at various angles.
Impact of New Material Technologies on Textile Belts:
- High-Performance Fibers: The integration of high-performance synthetic fibers like Kevlar or Twaron has significantly improved the tensile strength and durability of textile conveyor belts. These fibers resist stretching and ensure the belts can handle heavier loads.
- Coating and Treatments: Advances in materials science have led to the development of special coatings and treatments for textile conveyor belts. These enhancements include chemical-resistant coatings and heat-resistant properties, which extend the belts’ operational life and broaden their application range.
- Hybrid Materials: The combination of traditional textiles with advanced polymers or rubber composites has produced hybrid conveyor belts. These belts benefit from the flexibility of textiles and the durability of heavier-duty materials, making them suitable for a variety of challenging conditions.
Chevron patterns, when applied to these advanced materials, further enhance the belts’ efficiency by adding the necessary grip and reducing slippage in critical applications such as steep incline conveyance and heavy material transport. This synergy between innovative materials and chevron designs encapsulates the ongoing evolution in the conveyor belt industry, driving higher performance and reliability in textile conveyor belts.

The Impact of Material on Calculating Chevron Conveyor Belt Material Weight and System Efficiency
The weight of a conveyor belt is a crucial factor in the design and efficiency of a conveyor system. The material used in chevron conveyor belt material not only determines its durability and suitability for specific applications but also significantly influences its overall weight. This is especially important because the weight impacts the energy consumption and the mechanical stress placed on the conveyor system’s structure and drive components.
Chevron patterns, which provide higher grip and stability for material transport, especially on inclines, are typically made from heavier materials such as rubber. This material choice, while excellent for traction and wear resistance, contributes to a greater overall weight of the conveyor belt compared to smoother and lighter materials like PVC or fabric.
Guidelines for Calculating Weight of Chevron Conveyor Belt Material:
- Determine Material Density: Start by identifying the density of the conveyor belt material, typically expressed in pounds per cubic foot (lb/ft³) or kilograms per cubic meter (kg/m³). Rubber, for example, has a higher density compared to other materials like fabric or PVC.
- Measure Belt Dimensions: Measure the length, width, and thickness of the conveyor belt. For chevron conveyor belts, include the height of the chevron profiles as they add to the overall volume of material.
- Calculate Volume: Multiply the length, width, and total thickness (including chevron profiles) to find the volume of the material.
- Compute Weight: Multiply the volume by the density of the material to find the overall weight of the conveyor belt.
Understanding the weight of chevron conveyor belt material is essential for designing an efficient conveyor system. Heavier belts may require more powerful motors and stronger structural components to handle the added weight, impacting the system’s operational costs and energy efficiency. Conversely, optimizing the material composition and thickness can lead to significant savings in terms of energy consumption and maintenance costs.
Incorporating these calculations early in the system design process helps ensure that the conveyor is suitably equipped to handle the expected loads without excessive wear or energy use, ultimately leading to a more cost-effective and reliable system.
Get Expert Advice on Conveyor Belts by Filling Out This Form.
FAQs aobut Chevron Sonveyor Belt Material
Conveyor belts can be made from a variety of materials, each selected based on the specific requirements of the application and environment in which the belt will operate. The most commonly used materials include rubber, PVC, polyurethane, and fabric such as nylon or polyester. Rubber conveyor belts are prized for their durability and flexibility, making them suitable for a wide range of conditions, including abrasive and heavy materials. PVC belts are popular in food industry applications due to their resistance to chemicals and easy cleaning. Polyurethane belts offer excellent resistance to wear, oil, and grease, whereas fabric belts are typically used in applications that require a high degree of flexibility and are lighter in weight. Each material provides different advantages such as resistance to abrasion, chemical resistance, and suitability for food-grade applications.
Chevron rubber refers to the type of rubber used in the production of chevron conveyor belts, which are characterized by patterns of raised “V,” “U,” or “C” shapes on their surface. These patterns, or cleats, help in preventing the slippage of materials being transported on inclined planes. The rubber used in chevron belts is generally more robust and durable compared to other types of conveyor belt materials. It is designed to withstand the rough handling of materials like aggregates, coal, or minerals that could otherwise cause slippage or spillage. Chevron rubber is essential in applications where increased traction is required, making it ideal for industries such as mining, agriculture, and recycling, where belts need to handle bulk materials at inclines.
Conveyors can be constructed using a wide range of materials, depending on the specific needs of the operation and the materials being handled. The primary materials include metals such as steel and aluminum, plastics, rubber, and various textile materials. Steel is often used for its strength and durability, making it suitable for heavy-duty applications and environments with high temperatures. Aluminum offers a lighter weight alternative that is also resistant to corrosion, making it ideal for food processing applications. Plastics such as polyethylene, polypropylene, and PVC are used for their versatility and cost-effectiveness, suitable for lighter applications and where corrosion resistance is necessary. Textiles and fabrics are used in conveyor belts where flexibility is more critical than durability. Each material brings its own set of properties to the conveyor system, influencing factors like weight, speed, load capacity, and maintenance needs.
Metals used in conveyor belts primarily include steel and stainless steel. Steel is favored for its high strength and durability, making it ideal for heavy-load carrying and high-speed applications. It is commonly used in mining, milling, and heavy manufacturing industries. Stainless steel is preferred where corrosion resistance is crucial, such as in food processing or chemical industries. Stainless steel conveyor belts resist rust and are easy to clean, ensuring compliance with hygiene standards and preventing contamination. Additionally, some conveyor systems use aluminum because of its lighter weight, which reduces the load on the conveyor’s motor and can be beneficial in applications such as packaging or assembly lines where heavy strength is not a primary requirement.
Conveyor belts are typically made of a combination of materials, including rubber, plastic, fabric, and metal. The choice of material depends on the application, with rubber and PVC being common for general-purpose belts, while metal belts are used in high-temperature or heavy-duty environments.
The raw materials used in conveyor belts include natural rubber, synthetic rubber (such as SBR or NBR), PVC (polyvinyl chloride), and various fabric reinforcements like polyester or nylon. For specific applications, other materials like silicone, polyurethane, or Teflon may also be used.
Stainless steel is the most commonly used metal in conveyor belts, especially for applications requiring high strength, durability, or resistance to corrosion and heat. Other metals like carbon steel or aluminum may also be used depending on the application.
The ply material in a conveyor belt is typically made of fabric such as polyester, nylon, or a combination of both (EP fabric). These fabrics provide the belt with tensile strength and flexibility, with multiple layers (plies) being laminated together to form the belt’s carcass.
Last Updated on August 27, 2024 by Jordan Smith
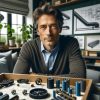
Jordan Smith, a seasoned professional with over 20 years of experience in the conveyor system industry. Jordan’s expertise lies in providing comprehensive solutions for conveyor rollers, belts, and accessories, catering to a wide range of industrial needs. From initial design and configuration to installation and meticulous troubleshooting, Jordan is adept at handling all aspects of conveyor system management. Whether you’re looking to upgrade your production line with efficient conveyor belts, require custom conveyor rollers for specific operations, or need expert advice on selecting the right conveyor accessories for your facility, Jordan is your reliable consultant. For any inquiries or assistance with conveyor system optimization, Jordan is available to share his wealth of knowledge and experience. Feel free to reach out at any time for professional guidance on all matters related to conveyor rollers, belts, and accessories.