Necessary Cold Resistant Conveyor Belt
Cold resistant conveyor belts are specially designed to operate efficiently in environments with extremely low temperatures. These belts are essential in industries such as mining, construction, and agriculture, where materials need to be transported in freezing conditions. The primary purpose of cold resistant conveyor belt is to maintain flexibility and durability despite the harsh cold, ensuring uninterrupted operation. Their importance cannot be overstated, as they prevent material handling delays and equipment malfunctions, which are common in sub-zero environments. Cold resistant conveyor belt available in laceration-resistant, abrasion-resistant are ideal for conveying materials in freezing areas. By utilizing cold resistant conveyor belts, industries can enhance productivity and safety, reducing the risks associated with brittle or malfunctioning standard conveyor systems in cold climates.
The Effects of Cold on Conveyor Belt
Cold temperatures can significantly impact the performance and longevity of conveyor belts. Understanding these effects is crucial for selecting the right type of conveyor belt for low-temperature environments. Here are the main effects of cold on conveyor belts:
1. Reduced Flexibility
- Brittleness: Cold temperatures can cause conveyor belts to become brittle, leading to cracking and breaking under stress.
- Stiffness: The materials used in conveyor belts may lose their flexibility in cold conditions, resulting in a reduced ability to bend and flex around pulleys and rollers.
2. Decreased Adhesion
- Cover Layer Separation: The bond between the cover layers and the carcass of the conveyor belt may weaken in cold temperatures, causing delamination or separation.
- Splice Failure: Cold conditions can negatively affect the adhesive used in splices, potentially leading to splice failure and conveyor belt breakage.
3. Material Properties Changes
- Rubber Hardening: The rubber compounds in conveyor belts can harden in low temperatures, reducing their ability to absorb impact and resist abrasion.
- Plastic Brittle Fracture: In plastic conveyor roller belts, cold temperatures can lead to brittle fractures where the material snaps or shatters instead of bending.
4. Increased Wear and Tear
- Abrasion: The hardening of materials can increase the rate of wear and tear on the conveyor belt, leading to a shorter lifespan.
- Surface Damage: The surface of the belt may become more susceptible to cuts, gouges, and other forms of damage when operating in cold environments.
5. Reduced Tensile Strength
- The tensile strength of the conveyor belt materials can be compromised in cold temperatures, making the belt less capable of handling heavy loads and increasing the risk of breakage.
6. Operational Issues
- Tracking Problems: Cold temperatures can affect the tracking of the conveyor belt, causing it to drift off course and potentially leading to jams or operational disruptions.
- Slippage: The belt’s grip on pulleys and rollers may be reduced in cold conditions, resulting in slippage and decreased efficiency.
7. Impact on Belt Components
- Rollers and Pulleys: Cold can affect the lubrication in rollers and pulleys, leading to increased friction and wear.
- Bearings: Bearings can become stiff and less effective in cold temperatures, causing operational issues and increased maintenance needs.
8. Frost and Ice Accumulation
- Surface Ice: Frost and ice can form on the surface of the conveyor belt, causing materials to slip and reducing the belt’s efficiency.
- Frozen Material: Materials being transported can freeze to the belt surface, making it difficult to unload and potentially damaging the belt during removal.
Mitigation Strategies
To mitigate the effects of cold on conveyor belts, several strategies can be employed:
- Use Cold-Resistant Materials: Selecting belts made from materials specifically designed to remain flexible and durable in cold temperatures.
- Proper Maintenance: Regular maintenance to check for signs of wear, lubricate moving parts, and ensure proper tension and alignment.
- Heated Enclosures: Using heated enclosures or warming systems to keep the conveyor belt and its components at a temperature that prevents brittleness and operational issues.
- Protective Covers: Applying protective covers or coatings to the belt surface to prevent ice accumulation and reduce wear.
Understanding these effects and taking appropriate measures can help maintain the efficiency and longevity of conveyor belts in cold environments.
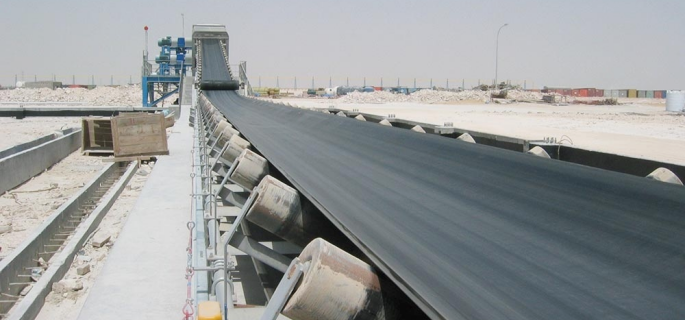
The Need Cold Resistant Conveyor Belt
Cold resistant conveyor belts are crucial for industries operating in extremely cold environments. These belts are engineered to withstand harsh temperatures, maintaining their functionality and durability where standard belts fail. By preventing common issues such as brittleness and cracking, cold resistant conveyor belts ensure smooth and efficient material handling, reducing downtime and maintenance costs. Their use is essential for maintaining high productivity levels and ensuring worker safety in freezing conditions.
Challenges in Cold Environments
Operating in cold environments presents several challenges that standard conveyor belts are not equipped to handle. The low temperatures affect the physical properties of the belts, leading to various operational issues. Here are some of the key challenges faced in cold environments:
- Impact of Low Temperatures on Standard Conveyor Belts: Traditional conveyor belts are not designed to withstand the rigors of extremely cold environments. Low temperatures can cause significant damage to standard belts, leading to operational issues.
- Loss of Elasticity: In cold environments, standard conveyor belts tend to lose their elasticity, making them less flexible and more prone to damage during operation.
- Hardening: Exposure to cold temperatures causes standard conveyor belts to harden. This hardening effect reduces their ability to function effectively, leading to potential breakdowns.
- Brittleness: Cold temperatures make standard conveyor belts brittle. This brittleness increases the likelihood of the belts cracking or breaking under stress.
- Cracking: Standard belts exposed to freezing temperatures are susceptible to cracking. Cracks compromise the integrity of the belt, leading to frequent replacements and maintenance.
- Reduced Performance: The performance of standard conveyor belts declines significantly in cold environments. Reduced performance can lead to slower production rates and increased operational costs.
- Material Handling Issues: Standard belts can struggle with handling materials in cold conditions, causing delays and inefficiencies in the production process.
- Increased Maintenance: Operating standard conveyor belts in cold environments necessitates more frequent maintenance, increasing downtime and labor costs.
- Safety Hazards: Brittle and cracked conveyor belts pose safety risks to workers, as they can fail unexpectedly, leading to accidents and injuries.
- Higher Operational Costs: The need for frequent repairs and replacements of standard conveyor belts in cold environments leads to higher operational costs, affecting the overall profitability of industrial operations.
Using a cold resistant conveyor belt addresses these challenges by providing a reliable and efficient solution for material handling in freezing temperatures, ensuring optimal performance and safety.
Types of Cold Resistant Conveyor Belts
Cold resistant conveyor belts are essential for ensuring smooth operations in industries where materials must be transported under extremely low temperatures. These belts are designed to maintain their flexibility, durability, and performance despite the harsh conditions. There are two main categories of cold resistant conveyor belt: standard cold resistant belts and specialized cold resistant belts. Each type is tailored to meet specific industrial needs and challenges.
Standard Cold Resistant Belts
Standard cold resistant conveyor belts are designed to operate efficiently within typical low-temperature ranges. They are suitable for a variety of general applications where cold temperatures are a factor.
Typical Temperature Ranges and General Applications
- Temperature Range: Standard cold resistant conveyor belts can typically handle temperatures ranging from -40°C to -20°C, ensuring reliable performance in moderately cold environments.
- General Material Handling: These belts are used in general material handling applications, such as transporting bulk goods in outdoor settings where temperatures drop significantly.
- Mining Industry: In the mining industry, these belts are employed to move ores and minerals in cold regions, maintaining operational efficiency.
- Construction Industry: Construction sites in colder climates utilize these belts to transport materials like sand, gravel, and concrete, ensuring timely project completion.
- Agriculture: In agricultural settings, these belts are used for moving harvested crops in cold storage areas or outdoor environments.
- Food Processing: Cold storage facilities for food processing use these belts to handle frozen goods, ensuring they remain intact during transport.
- Warehousing: Warehouses in cold climates rely on these belts for the efficient movement of goods and materials, reducing manual handling.
- Logistics and Distribution: These belts facilitate the transport of packages and goods in cold supply chain environments, ensuring timely deliveries.
Specialized Cold Resistant Belts
Specialized cold resistant conveyor belts are designed with additional properties to meet the demands of more challenging environments. These belts offer enhanced features such as oil resistance or fire resistance, making them suitable for specific applications.
Belts with Additional Properties
- Oil Resistance: Some cold resistant conveyor belts are engineered to resist oil, making them ideal for environments where materials are coated with oils or greases.
- Fire Resistance: These belts are designed to withstand high temperatures and resist fire, providing safety in industries where there is a risk of ignition.
Examples and Specific Applications
- Oil-Sprayed Coal: In the energy sector, specialized cold resistant belts are used to transport oil-sprayed coal, ensuring efficient handling without degradation of the belt material.
- Tar Sands: The oil industry uses these belts to move tar sands, which are heavy and often oil-laden, ensuring durability and resistance to both cold and oil.
- Chemical Plants: In chemical processing plants, these belts handle materials that may be exposed to harsh chemicals and cold temperatures, requiring both chemical and cold resistance.
- Petrochemical Industry: Specialized belts are used to transport petrochemical products, which are often exposed to cold environments and require oil resistance.
- Waste Management: In waste management facilities, these belts handle cold and potentially hazardous waste materials, ensuring safe and efficient transport.
- Steel Industry: The steel industry employs these belts to move cold, oil-coated steel materials, ensuring longevity and performance despite the harsh conditions.
By utilizing cold resistant conveyor belts tailored to their specific needs, industries can maintain efficient and safe operations in even the harshest environments.
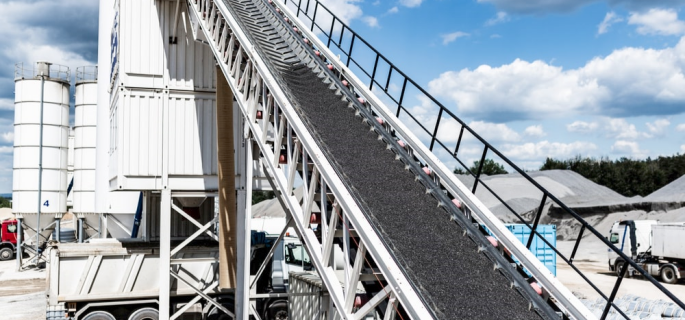
Conveyor Belts for Cold Weather
Cold resistant conveyor belts are designed to perform efficiently in low-temperature environments, typically found in cold storage facilities, outdoor transportation in winter, and other similar conditions. Here are the main types of cold resistant conveyor belts:
1. Fabric Conveyor Belts
- EP (Polyester/Nylon) Belts: These are made from polyester (warp) and nylon (weft) fabric. They offer good dimensional stability and excellent resistance to impact and abrasion.
- NN (Nylon/Nylon) Belts: Made entirely of nylon fabric, these belts are highly flexible and have good impact resistance. They perform well in cold environments but are less stable dimensionally compared to EP belts.
2. Steel Cord Conveyor Belts
- These belts are reinforced with steel cords, providing high tensile strength and excellent durability. They are suitable for long-distance and heavy-duty applications in cold conditions.
3. Chevron Conveyor Belts
- Designed with a v-shaped pattern on the surface, chevron conveyor belts are ideal for carrying loose materials up steep inclines in cold environments. The pattern helps prevent materials from slipping back.
4. Oil Resistant Cold Conveyor Belts
- These belts are specially formulated to resist the combined effects of cold temperatures and oil, making them suitable for environments where both conditions are present.
5. PVC/PVG Conveyor Belts
- PVC Belts: These belts have a PVC cover, making them ideal for light to medium-duty applications in cold storage and refrigerated environments.
- PVG Belts: These have a rubber cover on the top and a PVC layer on the bottom. They provide better durability and resistance to abrasion, suitable for more demanding cold environments.
6. Specialty Cold Resistant Belts
- Flame Resistant Cold Belts: These belts are designed to be fire-resistant as well as cold-resistant, used in environments where both properties are essential.
- High Impact Resistant Belts: Formulated to withstand high impacts in cold conditions, suitable for heavy-duty applications like mining and quarrying.
7. Modular Plastic Conveyor Belts
- Made from special cold-resistant plastic materials, these belts offer flexibility and ease of maintenance. They are suitable for food processing and packaging industries in cold environments.
8. Rubber Conveyor Belts
- These belts are made from specially formulated rubber compounds that remain flexible and durable at low temperatures. They are widely used in various industries due to their versatility.
Key Features of Cold Resistant Conveyor Belts
- Temperature Range: They can typically operate in temperatures ranging from -40°C to -60°C (-40°F to -76°F), depending on the specific belt material and construction.
- Flexibility: Even at low temperatures, these belts maintain their flexibility, preventing cracking and breaking.
- Durability: Designed to withstand the physical and chemical stresses of cold environments, including impacts and abrasion.
- Resistance to Moisture: Many cold resistant belts are also designed to resist moisture and frost, preventing slippage and maintaining efficiency.
Each type of cold resistant conveyor belt is tailored to specific applications and conditions, ensuring optimal performance and longevity in cold environments.
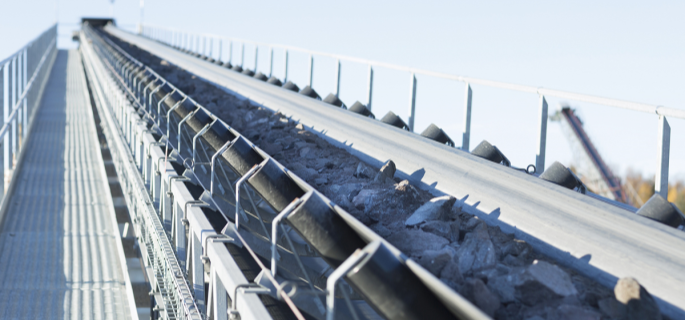
Key Features and Specifications of Cold Resistant Conveyor Belt
Cold resistant conveyor belts are engineered to deliver high performance in low-temperature environments. Their design and construction are tailored to meet the demanding conditions of various industrial applications, ensuring durability, flexibility, and reliability. Below are the key features and specifications that make cold resistant conveyor belts indispensable in cold environments.
Material and Construction
Cold resistant conveyor belts are built using advanced materials and construction techniques to ensure they can withstand harsh, low-temperature environments while maintaining high performance and longevity. The selection of materials, the number of plies, and the type of edges all contribute to the belt’s overall effectiveness.
- Common Materials Used:
Cold resistant conveyor belts are commonly made from high-strength fabrics like Nylon-Nylon (NN) and Polyester-Nylon (EP). NN fabric offers excellent flexibility and tensile strength, while EP fabric provides good dimensional stability and resistance to environmental stress. - Number of Plies:
The belts typically have multiple plies, with the number ranging from 2 to 6. Each ply adds strength and durability to the belt, allowing it to handle heavy loads and harsh operating conditions without compromising its structural integrity. - Rubber Cover Thickness Options:
The rubber cover thickness varies depending on the application. Standard options range from 3 mm to 8 mm for the top cover and 1.5 mm to 4.5 mm for the bottom cover. Thicker covers provide better protection against abrasion and impact. - Edge Types:
Cold resistant conveyor belts come with either cut edges or moulded edges. Cut edge belts are more cost-effective, while moulded edge belts offer enhanced protection against edge wear and delamination, making them suitable for more demanding applications. - Surface Texture:
The surface texture can be smooth, rough, or patterned to meet specific material handling requirements. Smooth surfaces are ideal for general purposes, while rough or patterned surfaces improve grip and material flow in more challenging conditions. - Heat Treatment:
The fabrics used in these belts undergo heat treatment to enhance their dimensional stability and resistance to environmental stress, ensuring consistent performance even under fluctuating temperatures. - Adhesion Strength:
High adhesion strength between the plies and the rubber covers is crucial for the belt’s durability. This feature prevents delamination and ensures that the belt can withstand mechanical stresses and temperature variations. - Reinforcement Layers:
Additional reinforcement layers can be added to the belt for extra strength and resistance to tearing and impact. This makes the belts suitable for heavy-duty applications where durability is paramount.
Performance Metrics
The performance of cold resistant conveyor belts is defined by various metrics that ensure they meet the rigorous demands of industrial applications. These metrics include tensile strength, abrasion resistance, and flexibility, among others, ensuring that the belts perform reliably in cold environments.
- Tensile Strength:
Cold resistant conveyor belts are designed to offer high tensile strength, typically ranging from 200 N/mm to 3150 N/mm. This ensures the belts can handle heavy loads without stretching or breaking, maintaining their structural integrity under stress. - Elongation at Break:
The elongation at break measures the belt’s flexibility and ability to stretch without breaking. Cold resistant conveyor belts typically exhibit elongation rates of 10% to 25%, ensuring they can bend and flex without cracking, even in low temperatures. - Abrasion Resistance:
These belts are built to resist abrasion, with typical abrasion resistance values of less than 200 mm³. This high level of abrasion resistance ensures longevity even in environments where the belt is subjected to rough and abrasive materials. - Impact Resistance:
The belts are designed to absorb impacts, reducing the risk of damage when handling heavy or sharp materials. This is achieved through the use of tough, flexible materials and reinforced construction, ensuring the belts can withstand sudden and heavy impacts. - Temperature Ranges for Different Grades:
Cold resistant conveyor belts are available in various grades to suit different temperature ranges. Standard grades can operate from -40°C to -20°C, while specialized grades can function effectively at temperatures as low as -60°C, ensuring performance in the coldest environments. - Chemical Resistance:
In addition to cold resistance, these belts often provide resistance to chemicals, oils, and other corrosive substances. This makes them suitable for diverse industrial applications, including those involving harsh chemicals and cold conditions. - Flexibility:
The flexibility of cold resistant conveyor belts is crucial for maintaining performance in low temperatures. The belts are designed to remain pliable and functional even in extreme cold, preventing brittleness and cracking, which can lead to mechanical failure.
By incorporating these key features and specifications, cold resistant conveyor belts ensure reliable performance, durability, and safety in harsh, low-temperature environments, catering to a wide range of industrial needs.
Specific Cold Resistant Grades for Cold Resistant Conveyor Belt
Cold resistant conveyor belts come in various grades, each designed to meet specific industrial needs and conditions. These grades are tailored to provide optimal performance in different low-temperature environments, ensuring durability, flexibility, and resistance to various elements.
- Cold Oil MINING-FFORN:
This grade is designed for mining operations where both cold temperatures and oil resistance are critical. The Cold Oil MINING-FFORN belt can handle temperatures as low as -50°C, making it ideal for transporting oil-laden materials in extremely cold environments. Its robust construction ensures longevity and reliable performance in challenging conditions. - Cold Oil CWOR:
The Cold Oil CWOR grade is perfect for applications requiring cold and oil resistance, such as chemical plants and petrochemical industries. It can operate efficiently at temperatures down to -40°C. This grade is especially useful for transporting oil-coated materials, ensuring that the belt remains flexible and durable despite the presence of oils and low temperatures. - Abrasion Cold Cut Gouge ZR1:
Designed for environments where both abrasion resistance and cold tolerance are necessary, the Abrasion Cold Cut Gouge ZR1 grade can function in temperatures as low as -45°C. This belt is suitable for handling abrasive materials like coal and minerals, providing excellent wear resistance and durability. - Abrasion Cold Cut Gouge ZR2 ORB:
The ZR2 ORB grade offers enhanced abrasion resistance and is engineered to withstand temperatures down to -50°C. It is ideal for heavy-duty applications in mining and construction where materials are both cold and abrasive. The belt’s construction ensures minimal wear and tear, even under intense conditions. - Cold Resistant ARCTIC-TUFF:
The ARCTIC-TUFF grade is specifically designed for Arctic conditions, with an operating range that extends to -60°C. This belt is perfect for extremely cold environments, such as those found in the Arctic and Antarctic regions. Its superior cold resistance ensures reliable performance without becoming brittle or cracking. - Cold Resistant CRYOGENIC-X:
CRYOGENIC-X belts are developed for cryogenic applications, handling temperatures as low as -70°C. They are suitable for scientific research facilities and industries dealing with liquefied gases. This belt maintains flexibility and strength, even in the most extreme cold conditions. - Cold Resistant ICE-FLEX:
ICE-FLEX belts are designed for general cold storage and handling applications, with a temperature range of -40°C to -20°C. These belts are used in food processing, warehousing, and logistics where consistent performance in cold environments is required. - Cold Resistant POLAR-PLUS:
POLAR-PLUS belts are suitable for harsh winter environments, operating effectively at temperatures down to -55°C. They are used in outdoor applications, such as transporting materials in polar regions or high-altitude locations where extreme cold is a factor.
Standards and Compliance
Cold resistant conveyor belts must comply with various international standards to ensure quality, safety, and performance. These standards provide guidelines for material properties, construction, and operational capabilities.
- ISO Standards:
Many cold resistant conveyor belts comply with ISO (International Organization for Standardization) standards, which specify requirements for belt construction, tensile strength, elongation, and abrasion resistance. Compliance with ISO standards ensures that the belts meet global quality and performance benchmarks. - DIN Standards:
The Deutsche Institut für Normung (DIN) standards are widely recognized in the industry. Cold resistant conveyor belt adhering to DIN standards, such as DIN 22102, are tested for their resistance to cold, oil, and abrasion, ensuring they can withstand the rigors of industrial use in harsh environments. - EN Standards:
European Norm (EN) standards, like EN 14890, specify the requirements for conveyor belts, including cold resistance. Belts that comply with these standards are tested for their ability to maintain performance at low temperatures, ensuring reliability in European industrial applications. - ASTM Standards:
The American Society for Testing and Materials (ASTM) provides standards for material properties and testing methods. Cold resistant conveyor belt meeting ASTM standards have undergone rigorous testing to confirm their suitability for use in low-temperature environments. - REACH Compliance:
Belts that comply with the REACH (Registration, Evaluation, Authorization, and Restriction of Chemicals) regulation ensure that the materials used are safe for both the environment and human health, making them suitable for use in various industrial applications. - RoHS Compliance:
RoHS (Restriction of Hazardous Substances) compliance indicates that the belts are free from hazardous materials like lead, mercury, and cadmium, making them safe for use in sensitive environments.
By adhering to these standards and providing a range of specialized grades, cold resistant conveyor belts ensure optimal performance, safety, and reliability across various industries and extreme cold conditions.
Slecting Cold Resistant Conveyor Belt
Selecting a cold-resistant conveyor belt involves considering several factors to ensure the belt will perform effectively in low-temperature environments. Here are the key considerations and steps to guide the selection process:
1. Understand the Operational Environment
- Temperature Range: Determine the minimum and maximum temperatures the conveyor belt will be exposed to. This will help in selecting a belt that can maintain its properties and performance within this range.
- Exposure Duration: Consider how long the belt will be exposed to cold temperatures. Continuous exposure may require different specifications compared to intermittent exposure.
2. Material and Construction
- Belt Material: Choose a belt made from materials specifically formulated for cold resistance, such as cold-resistant rubber or plastic compounds.
- Rubber Belts: Look for belts with additives that enhance flexibility and durability at low temperatures.
- Plastic Belts: Ensure the plastic used can withstand cold without becoming brittle.
- Reinforcement: Select the appropriate reinforcement for the belt’s carcass, such as steel cords or fabric (EP, NN) that can handle cold conditions without losing strength.
3. Mechanical Properties
- Flexibility: Ensure the belt remains flexible at low temperatures to prevent cracking and breaking.
- Tensile Strength: Verify that the belt maintains its tensile strength in cold conditions to handle the required load.
- Abrasion Resistance: Choose a belt with high abrasion resistance to withstand the wear and tear associated with cold environments.
4. Application Requirements
- Type of Material Conveyed: Consider the type of material being transported and its interaction with the belt at low temperatures.
- Incline/Decline: If the belt operates on an incline or decline, ensure it has the necessary grip to prevent slippage.
- Load Capacity: Ensure the belt can handle the load requirements without compromising its integrity in cold conditions.
5. Belt Design
- Chevron or Patterned Belts: For inclined transport, chevron or other patterned belts can provide additional grip.
- Modular Belts: For food processing and packaging, consider modular plastic belts that can be easily maintained and cleaned.
6. Additional Features
- Oil and Chemical Resistance: If the belt will be exposed to oils or chemicals, select a belt that offers both cold and chemical resistance.
- Flame Resistance: In environments where fire resistance is also a concern, choose belts that meet the necessary safety standards for both cold and flame resistance.
7. Manufacturer Specifications and Recommendations
- Technical Data Sheets: Review the technical data sheets provided by manufacturers to compare properties such as temperature range, tensile strength, elongation, and abrasion resistance.
- Industry Standards: Ensure the selected belt meets industry standards and certifications for cold-resistant conveyor belts.
8. Consult with Experts
- Supplier Consultation: Engage with suppliers or manufacturers who specialize in cold-resistant conveyor belts to get recommendations tailored to your specific needs.
- Field Testing: If possible, conduct field tests to evaluate the belt’s performance in actual operating conditions before making a final decision.
Selecting the right cold-resistant conveyor belt involves a comprehensive evaluation of the operational environment, material properties, application requirements, and additional features. By carefully considering these factors and consulting with experts, you can ensure the chosen conveyor belt will perform reliably and efficiently in cold conditions.
Maintenance and Care for Cold Resistant Conveyor Belt
Maintaining a cold resistant conveyor belt is crucial to ensure its longevity, reliability, and optimal performance in harsh environments. Regular inspection and proper maintenance practices help prevent unexpected breakdowns and extend the lifespan of the conveyor belt. Special considerations must be taken into account due to the extreme cold conditions in which these belts operate. Here are ten essential tips for maintaining and caring for cold resistant conveyor belts:
- Regular Inspection:
Conduct regular visual inspections of the cold resistant conveyor belt to identify any signs of wear, tear, or damage. Look for cracks, fraying edges, or any irregularities that could indicate potential problems. - Lubrication:
Proper lubrication of the belt and its components is essential to ensure smooth operation. Use lubricants that are suitable for low-temperature environments to prevent the belt from becoming stiff or brittle. - Tension Adjustment:
Regularly check and adjust the tension of the conveyor belt to ensure it is operating at the correct tension. Incorrect tension can lead to slippage, excessive wear, and potential belt failure. - Alignment:
Ensure that the conveyor belt is properly aligned to prevent uneven wear and reduce the risk of the belt slipping off the rollers. Misalignment can cause significant damage over time if not addressed promptly. - Cleaning:
Keep the conveyor belt clean by removing any debris, ice, or foreign materials that may accumulate on the belt. Regular cleaning prevents material buildup that can cause abrasion and damage to the belt surface. - Temperature Monitoring:
Continuously monitor the temperature of the operating environment and the belt itself. Extreme cold can affect the belt’s flexibility and performance. Ensure that the belt is designed to operate within the specific temperature range of the environment. - Preventive Maintenance:
Implement a preventive maintenance schedule that includes regular checks and servicing of all conveyor belt components. This proactive approach helps identify and address potential issues before they become major problems. - Edge Protection:
Pay special attention to the edges of the cold resistant conveyor belt. Edge protection measures, such as applying edge sealants or using moulded edge belts, can prevent fraying and damage to the belt edges. - Splice Inspection:
Regularly inspect the splices on the conveyor belt to ensure they are intact and secure. Weak or damaged splices can lead to belt failure, especially in cold environments where materials can become brittle. - Storage Conditions:
Store spare cold resistant conveyor belts in a cool, dry place away from direct sunlight and extreme temperatures. Proper storage conditions help maintain the belt’s integrity and prevent premature aging or deterioration.
Special Considerations for Extreme Cold Conditions
Operating a cold resistant conveyor belt in extreme cold conditions requires additional care and special considerations to ensure optimal performance and longevity. These conditions can pose unique challenges that necessitate tailored maintenance practices and precautions.
- Cold Flexibility:
Choose a cold resistant conveyor belt specifically designed for extreme cold conditions. These belts are formulated to remain flexible and resilient at very low temperatures, preventing brittleness and cracking. - Low-Temperature Lubricants:
Use lubricants that are formulated to remain effective at low temperatures. Standard lubricants can become viscous and less effective in the cold, leading to increased friction and wear. - Thermal Insulation:
In extremely cold environments, consider insulating the conveyor system to protect the belt and components from the harsh temperatures. Insulation helps maintain a more stable operating temperature for the belt. - Winterization Procedures:
Implement winterization procedures for your conveyor system, such as covering exposed sections and components to protect them from snow, ice, and freezing winds. - Heat Tracing:
In severe cold conditions, heat tracing systems can be installed along the conveyor belt to maintain a minimum temperature and prevent freezing. This helps ensure continuous operation even in extreme cold. - Material Handling Adjustments:
Adjust the handling and processing of materials to account for the cold. Materials can behave differently at low temperatures, so it’s important to ensure they do not cause undue stress or damage to the belt. - Cold-Resistant Components:
Use cold-resistant components for the entire conveyor system, including rollers, pulleys, and idlers. These components are designed to perform reliably in low temperatures, reducing the risk of mechanical failure. - Frequent Inspections in Winter:
Increase the frequency of inspections during the winter months to promptly identify and address any issues that arise due to the cold. Early detection and correction of problems are crucial in extreme conditions. - Employee Training:
Train employees on the specific maintenance and operational procedures for cold resistant conveyor belts. Proper training ensures that staff are aware of the special considerations and practices needed to maintain the belts in cold environments. - Emergency Preparedness:
Have an emergency maintenance plan in place to quickly respond to any issues that may arise during extreme cold conditions. This plan should include readily available spare parts and tools to minimize downtime and ensure continuous operation.
By following these maintenance and care tips, you can ensure that your cold resistant conveyor belt remains in optimal condition, providing reliable performance and longevity even in the harshest cold environments.
Innovations and Future Trends in Cold Resistant Conveyor Belt
The cold resistant conveyor belt industry is continually evolving, driven by advancements in materials science and an increasing focus on sustainability. Innovations in this field are aimed at enhancing performance, durability, and environmental responsibility, ensuring that conveyor belts can meet the demanding requirements of modern industries operating in extreme cold conditions.
Advancements in Cold Resistant Materials
Recent advancements in materials science have led to significant improvements in the performance and durability of cold resistant conveyor belts. Researchers and engineers are developing new materials and technologies to enhance the capabilities of these belts.
- Latest Research:
Ongoing research focuses on developing polymer composites that offer superior cold resistance. These new materials are designed to maintain flexibility and strength at lower temperatures than traditional materials, extending the operational range of cold resistant conveyor belts. - Nanotechnology:
The integration of nanotechnology in belt manufacturing is revolutionizing the industry. Nanoparticles are being used to enhance the mechanical properties of belt materials, providing better wear resistance, increased tensile strength, and improved elasticity in cold conditions. - Advanced Fabrication Techniques:
Innovations in fabrication techniques, such as 3D printing and advanced weaving methods, are enabling the production of conveyor belts with customized properties. These techniques allow for precise control over the material composition and structure, resulting in belts that are better suited to specific industrial needs. - Improved Elastomers:
Development of new elastomers that can withstand extreme cold without becoming brittle is a major focus area. These elastomers are designed to provide consistent performance across a wide temperature range, ensuring reliability in varying environmental conditions. - Hybrid Materials:
Combining different materials to create hybrid belts offers a way to leverage the benefits of each component. For instance, blending rubber with high-strength fibers can result in belts that offer both flexibility and durability, making them ideal for harsh conditions. - Smart Materials:
The incorporation of smart materials that can self-heal or change properties in response to environmental conditions is an emerging trend. These materials can enhance the longevity and performance of cold resistant conveyor belts by automatically adjusting to the operating environment. - Enhanced Coatings:
New coating technologies are being developed to protect conveyor belts from abrasion, chemicals, and extreme temperatures. These coatings extend the life of the belts and improve their resistance to harsh operating conditions. - Bio-Based Materials:
Research into bio-based materials aims to create more sustainable and environmentally friendly conveyor belts. These materials are derived from renewable resources and offer comparable performance to traditional synthetic materials.
Sustainability and Efficiency
The drive towards sustainability and energy efficiency is shaping the future of the cold resistant conveyor belt industry. Innovations are not only focused on improving performance but also on reducing the environmental impact of conveyor belt production and operation.
- Energy Efficiency:
Innovations in belt design and materials are leading to more energy-efficient conveyor systems. Lightweight materials and reduced rolling resistance help decrease the energy required to operate conveyor belts, resulting in lower operational costs and reduced carbon footprints. - Recyclability:
Modern cold resistant conveyor belts are being designed with end-of-life recyclability in mind. Using recyclable materials and designing belts for easy disassembly ensures that they can be recycled rather than ending up in landfills, promoting a circular economy. - Reduced Emissions:
The use of eco-friendly materials and cleaner production processes helps reduce the emissions associated with manufacturing conveyor belts. This shift towards greener production methods supports global efforts to combat climate change. - Durability and Longevity:
Enhanced durability and longer lifespan of modern conveyor belts reduce the need for frequent replacements. This not only saves resources but also minimizes the environmental impact associated with manufacturing and disposing of conveyor belts. - Renewable Resources:
Incorporating materials derived from renewable resources into conveyor belt production is becoming more common. These materials offer a sustainable alternative to traditional petrochemical-based products. - Waste Reduction:
Advanced manufacturing processes are focused on minimizing waste. Techniques such as precision cutting and efficient material usage ensure that waste generated during production is kept to a minimum. - Improved Logistics:
Innovations in conveyor belt design are improving the efficiency of material handling systems. More efficient logistics operations reduce energy consumption and greenhouse gas emissions associated with transportation. - Smart Monitoring Systems:
The integration of smart monitoring systems into conveyor belts allows for real-time tracking of performance and maintenance needs. This proactive approach helps optimize energy use and reduce downtime, contributing to more efficient and sustainable operations.
By embracing these innovations and future trends, the cold resistant conveyor belt industry is set to enhance its performance and sustainability, meeting the evolving demands of modern industries while minimizing environmental impact.
FAQs about Cold Resistant Conveyor Belt
To prevent your cold resistant conveyor belt from freezing, several strategies can be employed. Firstly, ensure that the belt and its components are made from materials specifically designed for cold resistance. These materials maintain their flexibility and strength even at very low temperatures. Secondly, consider installing heat tracing systems along the conveyor belt. These systems maintain a minimum temperature to prevent the belt from freezing, ensuring continuous operation. Additionally, insulating the conveyor system can protect it from harsh external temperatures, maintaining a more stable operating environment for the belt. Regular maintenance is crucial; keep the belt clean from snow, ice, and debris that could cause freezing. Use low-temperature lubricants to keep the belt and its components moving smoothly. Lastly, implementing a winterization protocol can be very effective. This includes covering exposed parts of the conveyor system and regularly monitoring temperature conditions to promptly address any freezing issues. By combining these measures, you can effectively keep your conveyor belt from freezing and ensure its reliable operation in cold environments.
A cold conveyor belt is a type of conveyor belt specifically designed to operate efficiently in low-temperature environments. These belts are constructed from materials that can withstand extreme cold without becoming brittle or losing flexibility. The primary function of a cold resistant conveyor belt is to transport materials in industries where operations occur in freezing conditions, such as mining, construction, food processing, and outdoor material handling. These belts are crucial in ensuring uninterrupted operations by preventing issues commonly associated with standard belts in cold environments, such as cracking and reduced performance. Cold conveyor belts come in various grades and configurations, each tailored to specific applications and temperature ranges. They often include features like reinforced edges, multiple plies for added strength, and specialized rubber compounds that resist the adverse effects of cold. By maintaining their integrity and functionality in sub-zero temperatures, cold conveyor belts play a vital role in maintaining productivity and safety in cold-weather industrial operations.
For temperature resistance, several grades of cold resistant conveyor belts are available, each designed to handle different levels of extreme cold. One commonly used grade is the Cold Oil MINING-FFORN, which is ideal for mining operations involving cold and oil-resistant conditions, capable of functioning efficiently at temperatures as low as -50°C. Another grade is the Cold Oil CWOR, suitable for applications requiring both cold and oil resistance, like chemical plants and petrochemical industries, with an operational range down to -40°C. For environments where abrasion resistance and cold tolerance are necessary, the Abrasion Cold Cut Gouge ZR1 grade is suitable, operating effectively at temperatures as low as -45°C. The ZR2 ORB grade offers enhanced abrasion resistance and can withstand temperatures down to -50°C, making it ideal for heavy-duty applications. For Arctic conditions, the Cold Resistant ARCTIC-TUFF grade operates in temperatures as low as -60°C, while the CRYOGENIC-X grade is designed for cryogenic applications, functioning at temperatures as low as -70°C. Lastly, the Cold Resistant ICE-FLEX grade, suitable for general cold storage and handling applications, operates within a temperature range of -40°C to -20°C. These grades ensure optimal performance and durability in various cold-resistant applications.
The temperature range of a conveyor belt varies depending on the type and grade of the belt. Standard conveyor belts typically operate within moderate temperature ranges and are not suitable for extreme conditions. However, cold resistant conveyor belts are designed to function effectively in very low temperatures. For example, the Cold Oil MINING-FFORN grade can handle temperatures as low as -50°C, making it suitable for harsh mining conditions. The Cold Oil CWOR grade operates efficiently at temperatures down to -40°C, ideal for chemical and petrochemical industries. The Abrasion Cold Cut Gouge ZR1 grade functions in temperatures as low as -45°C, providing both cold tolerance and abrasion resistance. The ZR2 ORB grade, with enhanced abrasion resistance, can operate at temperatures as low as -50°C. For extremely cold environments, the ARCTIC-TUFF grade is designed to work in temperatures as low as -60°C, while the CRYOGENIC-X grade is suitable for cryogenic applications, handling temperatures down to -70°C. Additionally, the ICE-FLEX grade, used for general cold storage, operates within a range of -40°C to -20°C. These varied temperature ranges ensure that cold resistant conveyor belts can meet the specific needs of different industrial applications.
Last Updated on August 9, 2024 by Jordan Smith
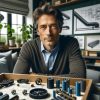
Jordan Smith, a seasoned professional with over 20 years of experience in the conveyor system industry. Jordan’s expertise lies in providing comprehensive solutions for conveyor rollers, belts, and accessories, catering to a wide range of industrial needs. From initial design and configuration to installation and meticulous troubleshooting, Jordan is adept at handling all aspects of conveyor system management. Whether you’re looking to upgrade your production line with efficient conveyor belts, require custom conveyor rollers for specific operations, or need expert advice on selecting the right conveyor accessories for your facility, Jordan is your reliable consultant. For any inquiries or assistance with conveyor system optimization, Jordan is available to share his wealth of knowledge and experience. Feel free to reach out at any time for professional guidance on all matters related to conveyor rollers, belts, and accessories.