Enhancing Industrial Productivity with Continental Conveyor Rollers
In the dynamic world of conveyor technology, Continental conveyor rollers stand out as pivotal components crucial for the seamless operation of conveyor systems across a wide range of industries. These rollers, emblematic of Continental’s commitment to quality and innovation, are designed to enhance efficiency and reliability in material handling and transportation tasks. This blog post aims to delve into the intricacies of Continental conveyor rollers, exploring their integral roles, diverse applications, and the comprehensive options available to businesses seeking to optimize their conveyor systems. Through this exploration, we’ll uncover the significance of selecting the right components to meet the specific demands of various conveyor operations, underlining the importance of Continental’s solutions in the broader conveyor industry landscape.
What are Continental Conveyor Rollers
Continental Conveyor Rollers: Design and Functionality
Continental conveyor rollers are integral components of modern material handling systems, designed to facilitate the smooth and efficient transportation of goods across a variety of industrial settings. These rollers, characterized by their durability and performance, play a pivotal role in minimizing the operational costs and maximizing the productivity of conveyor systems.
At the heart of continental conveyor rollers is their robust design, which is tailored to withstand the harsh conditions of industrial environments. These rollers are constructed from high-quality materials that ensure longevity and reliability. The design incorporates features such as precision bearings, dust-proof seals, and reinforced steel tubes, which together enhance the roller’s performance and reduce the need for frequent maintenance.
Functionality-wise, continental conveyor rollers are designed to efficiently manage the load, reducing the friction between the conveyor belt and the materials being transported. This not only aids in the smooth movement of goods but also extends the lifespan of the conveyor belt itself. The versatility of these rollers allows them to be used in various configurations, including flat, inclined, and curved conveyor systems.
The Extensive Range of Continental Conveyor Rollers
Delving into the Continental idler catalog reveals an extensive range of rollers and idlers, each engineered to meet specific industrial requirements. These variations are categorized based on factors such as the load capacity, the type of materials being transported, and the environmental conditions of the operational area. The eight primary types of rollers and idlers available in the Continental lineup include:
- Standard Duty Rollers: Designed for light to medium load applications, these rollers are ideal for general-purpose use in warehousing and light manufacturing processes.
- Heavy Duty Rollers: Built to accommodate higher load capacities, heavy-duty rollers are suitable for mining, construction, and other high-demand industrial environments.
- Impact Rollers: Specifically designed to absorb the impact at loading points, impact rollers help in reducing the wear and tear on the conveyor belt.
- Return Rollers: These rollers support the return side of the conveyor belt and are essential for maintaining belt alignment and preventing sagging.
- Guide Rollers: Installed on the sides of conveyor systems, guide rollers play a crucial role in preventing the conveyor belt from drifting off its intended path.
- Spiral Rollers: These are used to remove debris from the conveyor belt, ensuring a clean operational environment and reducing maintenance needs.
- Troughing Idlers: Troughing idlers are used to shape the conveyor belt in a troughed position, optimizing the carrying capacity of the conveyor system.
- Specialty Rollers: Addressing unique operational challenges, specialty rollers include options for high-temperature applications, corrosive environments, and other specialized requirements.
Each category within the Continental idler catalog is tailored to enhance the efficiency, safety, and reliability of conveyor systems across diverse industrial landscapes. By leveraging the specific functionalities and advantages of these various roller types, industries can significantly improve their operational workflows and reduce downtime.
Applications and Industries for Continental Conveyor Rollers
Varied Industries Relying on Continental Conveyor Rollers
Continental conveyor rollers are pivotal in a myriad of industries, where their role extends far beyond mere transport of goods. These industries leverage the advanced design and engineering of continental conveyor systems to enhance their operational efficiency, safety, and productivity. Here’s a look at eight key sectors where these systems play a crucial role:
- Manufacturing: In the manufacturing industry, continental conveyor rollers are essential for the seamless movement of raw materials, components, and finished products through different stages of the production line. They reduce manual handling, thereby minimizing the risk of injury and increasing production speed.
- Mining: The rugged and durable design of continental conveyor rollers makes them ideal for the harsh conditions of the mining industry. They are used for transporting mined materials over long distances, including vertical conveyance, through open pit and underground operations.
- Packaging: In packaging facilities, precision and efficiency are paramount. Continental conveyor systems ensure the swift and safe movement of products into packaging stations, facilitating rapid processing and dispatch.
- Agriculture: From the transportation of grains to the handling of livestock feed, continental conveyor rollers are instrumental in modern agricultural processes. They offer a gentle handling solution that minimizes damage to sensitive agricultural products.
- Food Processing: Hygiene and cleanliness are critical in the food processing industry. Stainless steel continental conveyor rollers are used here for their easy-to-clean surfaces, resistance to corrosion, and compliance with food safety standards.
- Logistics and Warehousing: The logistics sector benefits significantly from the adaptability of continental conveyor systems, which are used for sorting, loading, and unloading goods. They enhance the efficiency of distribution centers and warehouses by automating the movement of goods.
- Recycling and Waste Management: Continental conveyor rollers play a vital role in the sorting and processing of recyclables and waste materials. Their durability ensures they can handle rough and abrasive materials, contributing to effective waste management practices.
- Pharmaceuticals: In the pharmaceutical industry, precision and contamination control are essential. Continental conveyor rollers are used to transport sensitive products and components throughout the manufacturing process, adhering to strict regulatory standards.
Specific Roles of Continental Conveyor Rollers and Idlers
In each of these industries, the roles of continental conveyor rollers and idlers are tailored to meet unique operational needs. For example, in manufacturing and mining, heavy-duty rollers support the weight and abrasion of raw materials and finished goods. Meanwhile, in the food processing and pharmaceutical sectors, specialized rollers are designed to meet hygiene standards and prevent contamination.
Impact rollers are particularly valuable in the mining industry, where they absorb the shock and impact of heavy loads, thereby protecting the conveyor belt and prolonging its lifespan. Similarly, in agriculture and recycling sectors, the use of spiral rollers helps in keeping the belts clean by removing debris, thus ensuring uninterrupted operations.
In logistics and warehousing, guide rollers are crucial for maintaining the alignment of conveyor belts, ensuring that goods are correctly sorted and directed to their intended destinations. This precision is critical for the efficiency of automated systems and for minimizing the risk of errors.
The diverse applications of continental conveyor rollers across these sectors highlight their versatility and the pivotal role they play in modern industry. By optimizing the design and functionality of conveyor rollers and idlers for specific industry needs, Continental continues to contribute significantly to the efficiency and productivity of a wide range of industrial operations.
Selection Guide for Continental Conveyor Rollers
Making the Right Choice: Selecting Continental Conveyor Rollers
The process of selecting the appropriate Continental conveyor rollers is critical to ensuring the efficiency, longevity, and reliability of your conveyor system. Given the wide array of options available in the Continental portfolio, understanding the key factors that influence the selection process is essential. These factors include the size of the roller, the material from which it is made, and its intended application. Here, we delve into how these considerations play a pivotal role in selecting the right continental conveyor rollers for specific needs.
Size Considerations
The size of the conveyor roller is a fundamental aspect that directly impacts the conveyor system’s efficiency and compatibility. The diameter of the roller, along with the length, must be chosen based on the size of the products being transported and the overall dimensions of the conveyor system. Selecting the correct size ensures that the conveyor can handle the intended load without undue stress or strain, which could otherwise lead to premature wear or failure.
Material Selection
Continental conveyor rollers are available in a variety of materials, each offering distinct advantages for different applications. For instance:
- Steel Rollers are preferred for their strength and durability, making them suitable for heavy-duty applications in industries like mining and construction.
- Plastic Rollers offer a lightweight and corrosion-resistant alternative, ideal for food processing and pharmaceutical applications where hygiene and contamination control are critical.
- Rubber-Coated Rollers are used in applications requiring gentle handling of sensitive materials to prevent damage during transportation.
Application-Specific Selection
Understanding the specific requirements of your application is crucial in selecting the right type of roller. For example, in environments where the conveyor is exposed to water, chemicals, or extreme temperatures, selecting rollers made from materials that can withstand these conditions is paramount. Similarly, for applications requiring precise control over the movement of goods, such as in sorting facilities, rollers with specialized features like high-grip surfaces or integrated sensors may be necessary.
The Importance of Compatibility with Existing Conveyor Systems
When integrating new rollers into an existing conveyor system, ensuring compatibility is of utmost importance. This encompasses not only physical dimensions but also the operational characteristics of the rollers. Here are ten reasons why compatibility is crucial:
- Seamless Integration: Compatible rollers ensure a smooth transition, eliminating potential bottlenecks or disruptions in the conveyor line.
- Load Handling: Rollers must be capable of supporting the specific loads expected in your operations without compromising performance.
- Speed Synchronization: The roller’s design should match the conveyor’s operational speed, ensuring efficient and uniform material flow.
- Environmental Resistance: Compatibility with the operational environment’s conditions (e.g., temperature, humidity, exposure to chemicals) is essential for long-term reliability.
- Maintenance Requirements: Selecting rollers that align with the existing system’s maintenance protocols simplifies upkeep and reduces downtime.
- Operational Lifespan: Compatible rollers can enhance the overall lifespan of the conveyor system by reducing undue stress on components.
- Safety Considerations: Ensuring that new rollers are compatible with safety features and protocols of the existing system is paramount.
- Energy Efficiency: Properly matched rollers can contribute to the energy efficiency of the conveyor system, reducing operational costs.
- Noise Reduction: Compatibility in design can also influence the noise level of the system, improving the work environment.
- Future Scalability: Choosing rollers that are not only compatible but also adaptable to future expansions or modifications of the conveyor system ensures long-term flexibility and cost-efficiency.
Selecting the right Continental conveyor rollers involves a comprehensive understanding of your specific needs, including the size, material, and application of the rollers, as well as their compatibility with your existing conveyor system. Considering these factors carefully will lead to an optimized conveyor system that is efficient, reliable, and tailored to your operational requirements.
Pricing and Value of Continental Conveyor Rollers
Understanding Cost Factors for Continental Conveyor Rollers
The investment in Continental conveyor rollers is influenced by a variety of cost factors. These elements not only affect the initial outlay but also have long-term implications on the value derived from the conveyor system. Identifying and understanding these cost factors ensure that businesses can make informed decisions that align with their operational needs and budget constraints. Here are six key cost factors affecting Continental conveyor rollers and systems:
- Material Quality: The choice of material (steel, plastic, rubber-coated) directly impacts the cost. High-quality materials that offer durability and longevity tend to be more expensive upfront but provide better value in the long run.
- Design Complexity: Customized designs tailored to specific industry needs or challenging operational environments may increase costs. However, these customizations often result in enhanced efficiency and system performance.
- Size and Load Capacity: Larger rollers and those designed to support heavier loads typically cost more due to the increased material and structural requirements.
- Technological Features: Rollers equipped with advanced features such as integrated sensors for monitoring or specialized coatings for specific applications can elevate the price point.
- Environmental Resilience: Rollers designed to withstand harsh conditions such as extreme temperatures, corrosive substances, or abrasive materials may involve additional costs for enhanced materials and engineering.
- Supply Chain and Logistics: The cost of transportation and logistics, influenced by factors such as global supply chain dynamics and local availability, can also affect the overall pricing of conveyor rollers.
Long-Term Benefits of High-Quality, Durable Components
Opting for high-quality, durable components from Continental not only addresses immediate operational requirements but also delivers a range of long-term benefits. Here are eight compelling advantages:
- Reduced Downtime: High-quality rollers are less likely to fail, minimizing disruptions in operations and avoiding costly downtime.
- Lower Maintenance Costs: Durable components require less frequent replacements and repairs, translating into significant savings over the life of the conveyor system.
- Enhanced Safety: Superior quality rollers contribute to a safer working environment by reducing the risk of accidents associated with equipment failure.
- Improved Efficiency: Premium rollers ensure smoother operations, reducing energy consumption and enhancing the overall efficiency of the conveyor system.
- Greater Productivity: With fewer breakdowns and maintenance interventions, conveyor systems can operate at optimal levels, boosting productivity.
- Longer Lifespan: Investing in durability extends the usable life of the conveyor system, delaying the need for comprehensive overhauls or replacements.
- Environmental Sustainability: Longer-lasting components mean less waste and reduced demand for raw materials, contributing to more sustainable operational practices.
- Better ROI: While the initial investment in high-quality components may be higher, the long-term cost savings, operational efficiencies, and extended service life result in a more favorable return on investment.
While various factors influence the pricing of Continental conveyor rollers, the long-term benefits of selecting high-quality, durable components far outweigh the initial costs. By considering both the immediate and extended value that these components provide, businesses can make strategic investments in their conveyor systems that optimize performance, enhance safety, and deliver sustained operational benefits.
Custom Solutions vs. Off-the-Shelf for Continental Conveyor Rollers
When considering conveyor solutions, businesses often face the decision between opting for off-the-shelf systems or investing in custom solutions tailored to their specific needs. This choice is particularly relevant when selecting Continental conveyor rollers, given their impact on the overall efficiency and reliability of conveyor systems. To aid in this decision-making process, let’s compare the DIY approaches with Continental’s professional, tailor-made conveyor solutions, highlighting the advantages of professional solutions backed by Continental’s global material handling expertise.
The Value of Professional Solutions
Opting for Continental’s custom conveyor solutions over DIY approaches brings numerous benefits, primarily due to the reliability and efficiency of professional solutions supported by Continental’s extensive expertise in material handling across the globe. These solutions are not just about the immediate needs but also about foreseeing future requirements and challenges, ensuring that the investment today continues to deliver value for years to come.
Continental’s approach combines innovative design with cutting-edge technology and materials to create conveyor systems that are both robust and adaptable. Moreover, the professional installation and ongoing support offered ensure that the systems remain at peak performance, reducing the likelihood of downtime and enhancing overall productivity.
While DIY approaches may seem attractive initially, especially from a cost perspective, the long-term benefits of choosing Continental’s professional, tailor-made solutions far outweigh the perceived savings. With Continental’s custom solutions, businesses not only invest in the efficiency and reliability of their conveyor systems but also gain a partner equipped with global expertise in material handling, ready to support their operational needs at every step.
Technological Advancements in Continental Conveyor Rollers
Continental has consistently been at the forefront of innovation within the conveyor industry, introducing a range of technological advancements that redefine the efficiency and longevity of conveyor systems. These developments span across various aspects of conveyor technology, including materials science, design optimizations, and digital integrations. Here, we explore eight latest advancements in Continental conveyor rollers and how these innovations contribute significantly to the operational capabilities of conveyor systems.
- Advanced Materials: Continental has invested in research into new materials that offer enhanced durability and wear resistance. These materials, including specialized polymers and high-strength alloys, extend the life of conveyor rollers while reducing the need for maintenance.
- Smart Roller Technology: Incorporating sensors and IoT connectivity into rollers allows for real-time monitoring of performance and wear. This predictive maintenance capability can identify potential issues before they lead to system failures, enhancing overall system reliability.
- Energy-Efficient Designs: The latest designs include features that minimize friction and energy consumption, such as optimized bearing configurations and dynamic balancing. These improvements make conveyor systems more sustainable and cost-effective to operate.
- Improved Dust and Water Resistance: Advances in sealing technology protect against the ingress of dust and water, crucial for rollers operating in harsh environments. This protection ensures consistent performance and prolongs the lifespan of the rollers.
- Modular Construction: Continental has developed rollers with modular components, allowing for quick and easy replacement of parts. This design innovation significantly reduces downtime and maintenance costs.
- Noise-Reduction Technologies: With the use of advanced materials and design techniques, Continental has been able to produce rollers that generate less noise. This improvement enhances workplace conditions and complies with increasingly stringent regulations on noise pollution.
- High-Load Capacity Rollers: Through engineering advancements, Continental offers rollers capable of handling exceptionally high loads without compromising performance. These rollers are ideal for industries with heavy-duty conveying needs, such as mining and construction.
- Eco-friendly Solutions: Recognizing the importance of environmental sustainability, Continental has introduced eco-friendly rollers made from recycled materials. These rollers maintain the high performance standards expected while reducing the environmental footprint of conveyor systems.
Contribution to Efficiency and Longevity
These technological advancements contribute significantly to the efficiency and longevity of conveyor systems. Advanced materials and design innovations ensure that rollers can withstand the demands of diverse operating environments, reducing wear and extending service life. Smart roller technology and modular construction address maintenance challenges, allowing for proactive management and swift repairs. Furthermore, improvements in energy efficiency and eco-friendliness reflect a commitment to sustainability, reducing operational costs and environmental impact.
Continental’s continual investment in technological advancements underscores its dedication to providing conveyor solutions that meet the evolving needs of industries. By focusing on innovation, Continental ensures that its conveyor rollers not only enhance the immediate performance of conveyor systems but also contribute to long-term operational success and sustainability.
FAQs about Continental Conveyor Rollers
Rollers in conveyor belts are critical components that facilitate the movement of the belt and the materials being transported. These cylindrical elements are mounted on the frame of the conveyor system and can vary in size, material, and design based on the application. Rollers support the conveyor belt and move it along by rotating when the belt is in motion. They are strategically placed to handle the load efficiently and can be designed to suit various environmental conditions, load requirements, and operational speeds. High-quality rollers minimize resistance and wear on the conveyor belt, enhance operational efficiency, and reduce energy consumption. They must be robust, durable, and often require precision engineering to ensure smooth and reliable operation of the conveyor system.
There are several types of rollers that can be found on conveyor systems, each serving a specific purpose:
Carry Rollers: Positioned under the conveyor belt, they carry the belt and material load.
Return Rollers: Located on the underside of the conveyor system, they return the belt after the cargo is offloaded.
Impact Rollers: Placed at points where material is loaded onto the belt, they absorb the shock and impact of the falling material.
Guide Rollers: These rollers help to keep the conveyor belt in alignment, preventing it from drifting sideways.
Troughing Rollers: Configured in a concave shape, they shape the belt to hold material and prevent it from spilling.
Spiral Rollers: Used to clean the belt and remove any debris that may stick to it during operation.
Idler Rollers: A general term for rollers that are not powered but are used to support the belt and load.
The standard dimensions for conveyor rollers can vary widely depending on the application, the weight of the material being conveyed, and the width of the conveyor belt. Typically, rollers can range from a few inches to several feet in length, with diameters also varying. The most common diameters are typically between 2-6 inches. The length of the roller will often correspond with the width of the belt it is designed to support, with a little extra on each end for mounting. The sizing is critical as it affects the load distribution, belt support, and overall efficiency of the system. When choosing rollers, it’s important to consider the space between rollers (pitch), as this can affect the smoothness of the belt movement and the type of materials that can be transported.
Conveyor idler rollers, commonly referred to as simply ‘idlers’, are rollers that do not have the ability to drive the conveyor belt but are used to support the belt and the material being conveyed. They play a crucial role in the conveyor system by maintaining the integrity of the conveyor belt profile, ensuring that it is shaped correctly to hold the material it transports. Idler rollers come in various designs to support different functions, such as standard flat idlers, trough idlers which help in holding a larger volume of material, and return idlers that support the belt on its return journey. The quality and condition of idler rollers directly impact the efficiency, safety, and longevity of a conveyor belt system, making them an essential component for trouble-free conveyor operations.
Last Updated on April 10, 2024 by Jordan Smith
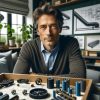
Jordan Smith, a seasoned professional with over 20 years of experience in the conveyor system industry. Jordan’s expertise lies in providing comprehensive solutions for conveyor rollers, belts, and accessories, catering to a wide range of industrial needs. From initial design and configuration to installation and meticulous troubleshooting, Jordan is adept at handling all aspects of conveyor system management. Whether you’re looking to upgrade your production line with efficient conveyor belts, require custom conveyor rollers for specific operations, or need expert advice on selecting the right conveyor accessories for your facility, Jordan is your reliable consultant. For any inquiries or assistance with conveyor system optimization, Jordan is available to share his wealth of knowledge and experience. Feel free to reach out at any time for professional guidance on all matters related to conveyor rollers, belts, and accessories.