Conveyor Belt Classes,Grades And Standards
Understanding the various classes of conveyor belts is crucial for selecting the right belt for specific industrial applications. Each conveyor belt class is designed to meet distinct operational and environmental challenges, ensuring efficiency and safety in material handling. The conveyor belt specification standards, such as ISO 433, provide a comprehensive framework that categorizes belts into different classes. These standards help in identifying the appropriate belt class based on factors like strength, durability, and resistance to elements like heat, abrasion, and chemicals. By familiarizing oneself with these classes and their corresponding specifications, one can make informed decisions that optimize conveyor system performance and longevity.
Conveyor Belt Class: Specification Standards
What are Conveyor Belt Specification Standards
The world of conveyor belts is diverse and complex, with a myriad of types suited for various applications and environments. Understanding conveyor belt specification standards is crucial in navigating this complexity. These standards, such as ISO 433, provide a universal language and a structured framework for classifying different types of conveyor belts based on their material, construction, and intended use.
The Role of ISO 433 in Conveyor Belt Class
ISO 433 is particularly significant in the conveyor belt industry. It outlines the specifications for various grades of rubber belts, focusing on aspects like abrasion resistance, heat resistance, and oil resistance. This standard helps in categorizing belts into different classes, each tailored for specific conditions and materials they will be handling. For instance, a belt class designed for mining operations where it would be exposed to sharp and heavy materials would differ significantly from a belt intended for agricultural products.
Part of EN 12882 Standard
The EN 12882 standard is a crucial benchmark in the conveyor belt industry, ensuring the safety and efficiency of conveyor belts used in various applications. This standard specifies the necessary fire safety classifications and standards for conveyor belts, providing guidelines to determine the appropriate level of fire resistance required for different operational environments.
Overview of EN 12882 Standard for Conveyor Belts
The EN 12882 standard is designed to set forth the classifications and requirements for conveyor belts used for general purposes, particularly focusing on establishing the correct level of fire resistance for conveyors operating in open air. The primary aim is to enhance safety in environments where combustible materials are handled, reducing the risk of fire-related incidents.
Basic Requirements and Categories of EN 12882
The standard categorizes conveyor belts into several classifications, each with specific requirements to ensure optimal fire resistance and safety. Below are the primary categories defined under the EN 12882 standard:
Category 1: Anti-static Belts
- Conforming to EN ISO 284 Standards: These belts are designed to be anti-static, which is crucial in environments where static electricity could ignite combustible materials such as coal, grain, and biomass. The anti-static property helps in preventing sparks and reducing the likelihood of fire.
Category 2A (K Grade): Fire Resistance with Covers
- K Grade Belts: These conveyor belts are designed with fire-resistant covers, providing an added layer of protection. The covers help in preventing the ignition and spread of fire, making them suitable for a wide range of applications where fire resistance is essential.
Category 2B (S Grade): Fire Resistance with or without Covers
- S Grade Belts: These belts offer fire resistance with or without covers, focusing on the wear resistance of the belt’s fire-resistant layer. The versatility of Category 2B belts makes them suitable for various industrial applications, especially where the abrasiveness of the material being transported is a concern.
Higher Classes: Specific Conditions and Testing Requirements
- Classes 3A and 3B: These classes include belts that undergo a drum friction test, making them suitable for conditions where there is a risk of blocked or seized drums without a safety system in place.
- Class 4A: Recommended for conveyors operating above ground in closed or covered conditions. This class involves a severe fire test (EN12881-1), ensuring high levels of fire resistance.
- Classes 4B and 5A-C: These categories incorporate more intensive drum friction tests. They are aimed at very specific conditions that typically can be mitigated with modern drum rotation detection sensors, enhancing the safety and reliability of conveyor systems.
Comprehensive PDF Resources
Numerous resources are available in PDF format that detail these specification standards. These documents serve as invaluable guides for engineers, procurement managers, and maintenance personnel. They offer detailed insights into the technical aspects of conveyor belts, such as tensile strength, elongation at break, and wear resistance. These resources often include charts and tables that make it easier to compare different belt classes and select the most suitable one for a specific application.

Classes of Conveyor Belts: Bed Belts vs. Roller Belts
Conveyor belts are critical components in various industrial processes, moving materials efficiently from one point to another. Two common types of conveyor belts are bed belts and roller belts. Understanding the differences between these types can help in selecting the right conveyor system for specific applications.
Choosing between bed belts and roller belts depends on the specific needs of your operation. Bed belts are ideal for applications requiring uniform support and simpler maintenance, making them suitable for lighter loads and shorter distances. Roller belts, on the other hand, are designed for heavy-duty applications, offering reduced friction and energy efficiency for transporting heavy loads over long distances. Understanding these differences can help in selecting the most suitable conveyor belt system for your industrial processes.
9 Basic Types of Conveyor Belts and Their Applications
Conveyor belts are an essential component in various industries, helping to transport materials efficiently and safely. Understanding the different types of conveyor belts and their specific applications can help in selecting the right belt for the job.
1. Flat Belt Conveyors
Overview: Flat belt conveyors are the most common type of conveyor belt. They are made of a continuous loop of material and are typically driven by an electric motor.
Applications:
- Manufacturing: Used to transport parts and products along assembly lines.
- Warehousing: Used for moving packages and goods.
- Airports: Used for baggage handling systems.
2. Modular Belt Conveyors
Overview: Modular belt conveyors use a series of interlocking plastic pieces, creating a belt that can be easily modified and repaired.
Applications:
- Food and Beverage: Ideal for sanitary applications as they are easy to clean.
- Pharmaceuticals: Used in applications requiring frequent cleaning.
- Automotive: Suitable for transporting parts and components.
3. Cleated Belt Conveyors
Overview: Cleated belt conveyors have vertical cleats attached to the belt to keep materials from sliding backward.
Applications:
- Agriculture: Used for transporting grain, seeds, and other bulk materials.
- Food Processing: Ideal for moving products up inclines.
- Recycling: Used for moving recyclables uphill.
4. Curved Belt Conveyors
Overview: Curved belt conveyors are designed to transport materials around corners or curves without changing the direction of the conveyor belt.
Applications:
- Airports: Used in baggage handling systems to navigate around corners.
- Manufacturing: Used to transport products through complex assembly lines.
- Warehousing: Suitable for optimizing space by navigating around obstacles.
5. Incline/Decline Belt Conveyors
Overview: Incline or decline belt conveyors are designed to move products up or down at an angle.
Applications:
- Packaging: Used for moving products between different levels.
- Mining: Ideal for transporting materials from one elevation to another.
- Food Processing: Used for moving products to different processing stages.
6. Roller Bed Conveyors
Overview: Roller bed conveyors use rollers to support the belt and reduce friction, making them suitable for longer distances.
Applications:
- Distribution Centers: Used for transporting goods over long distances.
- Manufacturing: Ideal for moving heavy products.
- Warehousing: Used for sorting and transporting packages.
7. Wire Mesh Belt Conveyors
Overview: Wire mesh belt conveyors use a woven metal belt, making them suitable for high-temperature applications.
Applications:
- Food Processing: Used for baking, cooling, and freezing products.
- Industrial: Suitable for transporting hot or abrasive materials.
- Automotive: Used in painting and coating applications.
8. Hinged Belt Conveyors
Overview: Hinged belt conveyors consist of a series of metal plates or hinges, creating a durable and robust belt.
Applications:
- Recycling: Used for transporting scrap metal and other heavy materials.
- Manufacturing: Ideal for handling parts and components in stamping and machining operations.
- Waste Management: Suitable for moving waste and debris.
9. Specialty Belt Conveyors
Overview: Specialty belt conveyors are designed for specific applications, often customized to meet unique requirements.
Applications:
- Pharmaceuticals: Used in cleanroom environments for transporting sensitive products.
- Aerospace: Ideal for handling delicate components.
- Electronics: Used for transporting sensitive electronic parts and assemblies.
Choosing the right type of conveyor belt depends on the specific requirements of the application, such as the type of material being transported, the operating environment, and the desired efficiency. By understanding the various types of conveyor belts and their applications, industries can enhance their material handling processes, improve productivity, and ensure safety.

Choosing the Correct Standard of Fire-Resistant Conveyor Belt Class
Choosing the Correct Fire-Resistant Conveyor Belt Class
Selecting the right conveyor belt class is crucial for ensuring safety and operational efficiency in environments with fire hazards. Here are some key considerations:
- Assess the Operational Environment: Determine whether the conveyor will operate in open air, closed, or covered conditions. This will guide the selection of the appropriate category.
- Material Characteristics: Consider the abrasiveness and combustibility of the materials being transported. Anti-static properties and wear resistance are critical for combustible materials.
- Safety Systems: Evaluate the presence of safety systems such as drum rotation detection sensors. Higher classes with intensive testing requirements may be necessary for operations lacking advanced safety systems.
- Industry Requirements: Ensure compliance with industry-specific standards and regulations. Different industries may have unique requirements for fire-resistant conveyor belts.
- Consult with Experts: Engage with conveyor belt manufacturers and industry experts to select the most suitable fire-resistant conveyor belt class. They can provide valuable insights and recommendations based on the specific operational needs.

Conveyor Belt Class Chart
Deciphering the Conveyor Belt Class Chart
A conveyor belt class chart is a vital tool in the belt selection process. It visually represents the different classes of conveyor belts and their key characteristics. This chart typically includes information on the belt’s material, thickness, tensile strength, and suitable applications. By understanding how to read and interpret this chart, one can make informed decisions about the right type of conveyor belt needed for their specific operational requirements.
Visual Representation and Interpretation
The chart usually presents a clear and organized visual representation of various belt classes. It may use color coding or symbols to indicate different properties like heat resistance or oil resistance. For example, a belt class designed for high-temperature environments might be marked with a specific color or symbol, making it easy to identify at a glance.
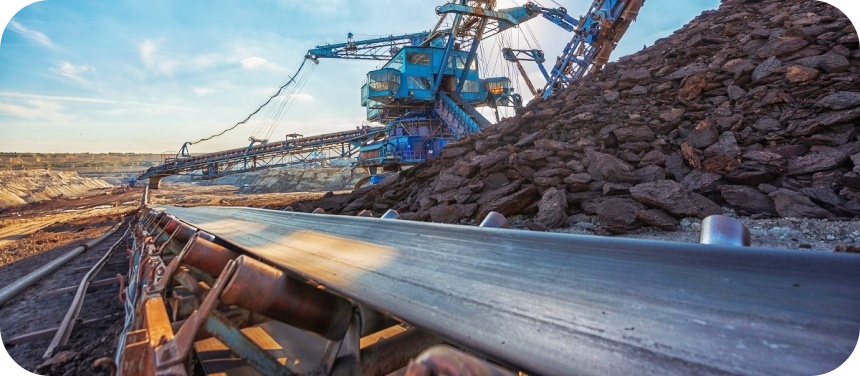
Utilizing the Chart for Belt Selection
Using the conveyor belt class chart effectively involves matching the operational requirements of a system with the properties of the belts displayed on the chart. Factors such as the nature of the materials being conveyed, the environmental conditions, and the mechanical demands of the conveyor system should be considered. The chart serves as a starting point, guiding users towards a narrower selection of belt classes suitable for their specific needs.
Conveyor Belt Grades & What They’re Used For
Conveyor belts are essential for the smooth operation of material handling systems in various industries. They are classified into different grades based on their composition, properties, and intended applications.Conveyor belts are divided into different grades: M grade (mining), N grade (normal), E grade (conductive), F grade (flame retardant), RMA grade, L grade (lightweight), H grade (high temperature resistance), O Grade (oil-resistant), AR grade (wear-resistant). Understanding these grades helps in selecting the right conveyor belt for specific needs, ensuring efficiency, safety, and longevity.
1. Grade M (Mining)
Overview: Grade M conveyor belts are specifically designed for mining applications, offering high resistance to cutting, gouging, and abrasion.
Applications:
- Coal Mining: Transporting coal and related materials.
- Underground Mining: Handling ores and other mined materials.
- Heavy-Duty Operations: Suitable for environments with rough and abrasive materials.
2. Grade N (Normal)
Overview: Grade N belts are general-purpose conveyor belts with moderate resistance to abrasion and impact.
Applications:
- General Manufacturing: Moving products and parts along assembly lines.
- Packaging: Transporting packaged goods in warehouses.
- Material Handling: Suitable for everyday use in various industries.
3. Grade E (Electrical Conductive)
Overview: Grade E belts are designed to prevent the buildup of static electricity, making them ideal for environments where sparks could cause fires or explosions.
Applications:
- Electronics Manufacturing: Transporting sensitive electronic components.
- Chemical Processing: Handling chemicals where static discharge must be avoided.
- Explosive Environments: Suitable for areas with flammable materials.
4. Grade F (Flame Retardant)
Overview: Grade F belts are made from materials that resist ignition and prevent the spread of fire.
Applications:
- Underground Mining: Transporting materials in areas prone to fires.
- Power Plants: Handling coal and other combustible materials.
- Tunneling Projects: Suitable for enclosed spaces where fire hazards exist.
5.Grade RMA (Rubber Manufacturers Association)
Overview: RMA belts are classified into two grades, Grade 1 and Grade 2, based on their tensile strength and elongation.
- Grade 1: Higher tensile strength and elongation requirements, offering better resistance to cutting and gouging.
- Grade 2: Suitable for less severe conditions, offering good durability and flexibility.
Applications:
- Construction: Transporting materials like sand, gravel, and aggregate.
- Agriculture: Handling grain, seeds, and other agricultural products.
- Recycling: Moving recyclable materials and waste.
6. Grade L (Lightweight)
Overview: Grade L belts are lightweight and designed for applications requiring low strength and high flexibility.
Applications:
- Food Processing: Transporting food products in hygienic environments.
- Textiles: Handling delicate textile materials.
- Pharmaceuticals: Suitable for cleanroom environments and transporting medicinal products.
7.Grade H (High-Temperature Resistant)
Overview: Grade H belts can withstand high temperatures, making them suitable for conveying hot materials.
Applications:
- Foundries: Transporting hot metal and other high-temperature materials.
- Glass Manufacturing: Handling hot glass products.
- Ceramics: Moving ceramic products through kilns and ovens.
8. Grade O (Oil Resistant)
Overview: Grade O belts are designed to resist the damaging effects of oil, grease, and other hydrocarbons.
Applications:
- Automotive: Transporting parts and materials exposed to oils and lubricants.
- Food Processing: Handling food products that contain oils and fats.
- Chemical Industry: Suitable for environments where oil and chemicals are prevalent.
9. Grade AR (Abrasion Resistant)
Overview: Grade AR belts are specifically engineered to resist wear and tear from abrasive materials.
Applications:
- Mining: Handling abrasive ores and minerals.
- Quarrying: Transporting stones, sand, and gravel.
- Construction: Moving construction materials like concrete and asphalt.
Choosing the right conveyor belt grade is crucial for optimizing material handling processes, ensuring safety, and extending the lifespan of the belt. By understanding the specific properties and applications of each grade, industries can make informed decisions that enhance productivity and operational efficiency.

Comprehensive Guide to the Conveyor Belt Class (PDF)
The Importance of Comprehensive Guides
In the complex world of conveyor belt technology, comprehensive guides, particularly those available in PDF format, are invaluable resources. These guides offer in-depth information on conveyor belt classes, enabling professionals in various industries to make informed decisions regarding conveyor belt selection and application.
Content of Comprehensive Conveyor Belt Class Guides
A typical comprehensive guide to conveyor belt classes covers a wide range of topics, each crucial for understanding the full scope of conveyor belt capabilities and applications. These topics include:
- Detailed Descriptions of Belt Classes: Each class is described in detail, including the materials used in the belts, their design features, and the specific applications they are suited for.
- Technical Specifications: The guides provide technical data such as tensile strength, maximum operating temperatures, abrasion resistance levels, and other critical specifications.
- Application Suitability: Information on which conveyor belt classes are best suited for various industries, such as mining, agriculture, manufacturing, and logistics.
- Safety and Compliance Standards: Details on safety standards and compliance requirements for different conveyor belt classes, including those related to fire resistance, static conductivity, and food-grade materials.
- Installation and Maintenance Guidelines: Tips and best practices for the installation and maintenance of different classes of conveyor belts, ensuring longevity and optimal performance.
- Case Studies and Real-World Applications: Inclusion of case studies that demonstrate how specific conveyor belt classification have been successfully implemented in various industrial settings.
Benefits of Using PDF Guides
The format of these guides in PDF offers several advantages:
- Ease of Access and Distribution: PDF guides can be easily downloaded, shared, and accessed on various devices, making them a convenient resource for professionals on the go.
- Comprehensive and Searchable Content: The comprehensive nature of these guides, combined with the ability to search for specific terms or topics, makes them an efficient tool for finding relevant information quickly.
- Regular Updates and Revisions: PDF guides can be regularly updated to reflect the latest advancements and changes in conveyor belt technology and standards.
How to Utilize These Guides
To effectively utilize these comprehensive guides, users should:
- Identify Specific Needs: Before consulting the guide, clearly define the specific requirements of the conveyor system, including the type of materials to be transported, environmental conditions, and operational demands.
- Cross-Reference with Standards: Use the guide in conjunction with relevant industry standards, such as ISO 433, to ensure that the selected conveyor belt class meets all necessary criteria.
- Consult with Experts: When in doubt, use the guide as a basis for discussion with conveyor belt experts or manufacturers to get tailored advice for specific applications.
Conveyor Belt Class Nomenclature
The Language of Conveyor Belts
Understanding the nomenclature used in conveyor belt class specifications is akin to learning a new language. It’s a critical skill for professionals in the industry, as it enables clear communication and precise specification of conveyor belt requirements. This section delves into the terminology and nomenclature commonly used in conveyor belt specifications, shedding light on the meanings behind the technical jargon.
Key Terms in Conveyor Belt Class Specifications
- Belt Class: Refers to the categorization of conveyor belts based on their strength, durability, and application suitability. For example, classes like Grade M, Grade E, or Grade F each signify different properties and uses.
- Tensile Strength: A term indicating the maximum load a belt can handle without breaking. It’s usually measured in pounds per inch of width (PIW) or Newtons per millimeter (N/mm).
- Elongation at Break: This term describes the extent to which a belt can stretch before it breaks, indicating flexibility and resilience.
- Abrasion Resistance: A measure of how well the belt can withstand wear and tear from rough materials. Higher abrasion resistance means a longer lifespan in harsh conditions.
- Cover Grade: Refers to the composition and quality of the outer layers of the belt, which protect the carcass from external damage. Different cover grades offer varying levels of resistance to heat, oil, chemicals, and abrasion.
What is Conveyor Belt Nomenclature
- Belt Width and Thickness: These are expressed in inches or millimeters and are crucial for determining the load capacity and suitability for the conveyor structure.
- Carcass Material: The term ‘carcass’ refers to the internal layer of the belt, which provides structural strength. Common materials include fabrics like polyester, nylon, and steel cords.
- Compound: Refers to the material composition of the belt cover, which can vary based on the application – for example, natural rubber, PVC, or synthetic compounds.
- Modulus of Elasticity: This term describes the belt’s ability to resist stretching under tension, a critical factor in maintaining belt alignment and preventing slippage.
The Significance of Conveyor Belt Nomenclature in Belt Selection
- Accurate Specification: Understanding nomenclature allows for the accurate specification of belts, ensuring that the chosen belt meets the operational demands.
- Comparative Analysis: Knowledge of these terms enables professionals to compare different belts and make informed decisions based on performance criteria.
- Communication with Suppliers: Clear understanding of nomenclature facilitates effective communication with suppliers and manufacturers, leading to better guidance and product selection.

Dunlop Conveyor Belt Class Catalogue (PDF)
Overview of Dunlop’s Conveyor Belt Offerings
Dunlop Conveyor Belting, a leading manufacturer in the conveyor belt industry, offers a comprehensive range of conveyor belt class solutions. Their catalogue, available in PDF format, is a detailed resource that provides insights into their extensive product range. This section explores the key aspects of the Dunlop Conveyor Belt Catalogue and how it serves as a crucial tool for industry professionals.
Content of the Dunlop Conveyor Belt Catalogue
The Dunlop Conveyor Belt Catalogue is a meticulously compiled document, presenting a wide array of conveyor belt options. It includes:
- Detailed Product Descriptions: Each conveyor belt type is described in detail, including its design, intended use, and technical specifications such as tensile strength, wear resistance, and temperature range.
- Material Specifications: The catalogue provides information on the materials used in belt construction, including the type of rubber compounds, carcass materials, and cover grades.
- Application Suitability: It outlines the suitability of different conveyor belt types for various industrial applications, such as mining, agriculture, manufacturing, and bulk material handling.
- Technical Data Sheets: These sheets offer in-depth technical data, including belt thickness, weight, and maximum roll lengths, aiding in precise engineering calculations and planning.
Utilizing the Catalogue for Conveyor Belt Selection
The Dunlop Conveyor Belt Catalogue is an essential tool for selecting the right conveyor belt for specific applications. To effectively use the catalogue:
- Identify Operational Requirements: Start by defining the operational requirements, including the type of materials to be conveyed, environmental conditions, and mechanical demands.
- Match Requirements with Belt Specifications: Use the catalogue to match these requirements with the specifications of different conveyor belts. Look for belts that meet or exceed the necessary criteria.
- Consult Technical Data Sheets: Refer to the technical data sheets for detailed specifications and to ensure that the chosen belt can be integrated seamlessly into the existing conveyor system.
Advantages of the Dunlop Conveyor Belt Catalogue
- Comprehensive Information: The catalogue provides a one-stop resource for all conveyor belt needs, offering a range of options and detailed specifications.
- Ease of Access: Available in PDF format, the catalogue can be easily downloaded, shared, and accessed, making it a convenient reference tool.
- Updated Information: Dunlop regularly updates its catalogue to include the latest products and innovations, ensuring that users have access to current and relevant information.
Standards in Conveyor Belt Class Selection
The Role of Standards in Conveyor Belt Industry
Standards play a pivotal role in the conveyor belt industry, serving as benchmarks for quality, safety, and performance. They ensure that conveyor belts are manufactured and operated to meet specific criteria, which are crucial for the safety and efficiency of conveyor systems. This section delves into how standards guide the manufacturing and application of the conveyor belt class.
Key Standards in Conveyor Belt Manufacturing
- International Standards: Organizations like ISO (International Organization for Standardization) provide globally recognized standards. For instance, ISO 433 specifies conveyor belts’ characteristics and minimum requirements.
- Regional and National Standards: Different regions may have specific standards. For example, in Europe, DIN (Deutsches Institut für Normung) standards are prevalent, while the United States might follow ASTM (American Society for Testing and Materials) standards.
- Industry-Specific Standards: Certain industries have unique requirements leading to specialized standards. For example, the mining industry has stringent standards for belts used in coal mining to ensure safety and durability.
Importance of Adhering to Standards
- Quality Assurance: Standards ensure that the conveyor belts are of high quality, durable, and reliable.
- Safety Compliance: Adherence to safety standards is crucial, especially in industries where conveyor belts are used to transport hazardous materials.
- Interoperability: Standards ensure compatibility between different parts of a conveyor system, which is essential for efficient operation and maintenance.
How Standards Influence Conveyor Belt Selection
- Material Selection: Standards dictate the types of materials that can be used in belt construction, influencing factors like tensile strength and abrasion resistance.
- Design Specifications: They provide guidelines on design aspects, such as belt width, thickness, and load capacity, ensuring the belt is suitable for its intended application.
- Performance Criteria: Standards define performance criteria like maximum operating speed, temperature range, and resistance to chemicals or heat.
Utilizing Standards for Optimal Belt Selection
- Cross-Referencing Requirements with Standards: Match the operational requirements of the conveyor system with the standards to ensure the selected belt class meets all necessary criteria.
- Consulting with Manufacturers: Work with manufacturers who adhere to these standards to ensure the conveyor belt is suitable for the specific application and environment.
- Regular Updates on Standards: Stay updated on changes and advancements in standards, as they can impact the selection and maintenance of conveyor belts.

Conveyor Belt Class: Thickness Chart
What is the Conveyor Belt Thickness Chart
The thickness of a conveyor belt is a critical factor that impacts its durability, strength, and suitability for different applications. A conveyor belt thickness chart is a tool that provides detailed information about the thickness of the conveyor belt class, helping professionals make informed decisions. This section explores the nuances of the conveyor belt thickness chart and its significance in the selection process.
Components of the Conveyor Belt Thickness Chart
- Belt Types and Their Thicknesses: The chart lists different types of conveyor belts and their respective thicknesses, typically measured in millimeters or inches.
- Carcass and Cover Layers: It details the thickness of the carcass (the internal strength layer) and the top and bottom cover layers, which protect the belt from external damage.
- Standard and Custom Thicknesses: The chart includes both standard thicknesses for common belt types and options for custom thicknesses based on specific requirements.
How Thickness Impacts Conveyor Belt Performance
- Load Capacity: Thicker belts generally have higher load capacities, making them suitable for heavy-duty applications.
- Flexibility: Thinner belts are more flexible, which is advantageous for systems with small pulley diameters.
- Wear and Tear: Thicker belts can withstand more wear and tear, making them ideal for abrasive or harsh environments.
- Weight Considerations: The thickness also affects the weight of the belt, which can impact the power requirements and the design of the conveyor system.
Using the Thickness Chart for Belt Selection
- Match Belt Thickness to Application: Use the chart to select a belt with a thickness that matches the operational demands, such as the type of material being conveyed and the environmental conditions.
- Consider System Specifications: Ensure that the chosen belt thickness is compatible with the conveyor system, including aspects like pulley diameters and tension requirements.
- Balance Between Thickness and Flexibility: Find the right balance between thickness for durability and flexibility for system compatibility.
Factors Influencing Belt Thickness
- Material Type: The type of material being conveyed (e.g., sharp, abrasive, or heavy materials) influences the required belt thickness.
- Conveyor Length and Speed: Longer and faster conveyor systems may require thicker belts for added strength and stability.
- Environmental Conditions: Exposure to harsh environmental conditions like extreme temperatures or chemicals may necessitate thicker belts in terms of the conveyor belt class.
Need a reliable conveyor belt? Reach out to us!
FAQs about Conveyor Belt Class
“Conveyor belt class 10” is not a standard term commonly used in the conveyor belt industry. It’s possible that this term could be specific to a certain educational curriculum, a particular manufacturer’s product line, or a unique classification system within a company or industry. In general conveyor belt terminology, there are no widely recognized “class” numbers like “class 10.”
Conveyor belts are typically classified based on their material, strength, application, and specific properties such as heat resistance, oil resistance, or suitability for food-grade applications. If “class 10” refers to a specific type or grade in a particular context, it would be best to consult the relevant documentation or source for clarification on what this classification represents.
Conveyor belts are graded based on their application, material, and durability. Common grades include:
General Purpose: Standard belts used in everyday applications.
Food Grade: Made with materials safe for food handling and processing.
Heat Resistant: Designed to withstand high temperatures.
Oil Resistant: Suitable for environments where oil exposure is possible.
Flame Retardant: Used in applications where there’s a risk of fire.
Abrasion Resistant: Designed for transporting abrasive materials.
Chemical Resistant: For environments where chemical exposure is a concern.
Conveyors are classified based on their function, design, and the materials they handle. The main types include:
Belt Conveyor: Uses a belt to transport materials.
Roller Conveyor: Uses rollers for movement, suitable for heavy loads.
Chain Conveyor: Uses a chain to move materials, ideal for heavy or hot items.
Screw Conveyor: Uses a rotating helical screw blade for moving granular or liquid materials.
Pneumatic Conveyor: Transports materials through tubes using air pressure.
Vertical Conveyor: Moves materials vertically, often used in packaging industries.
Belt conveyors come in various types, each suited for different applications:
Flat Belt Conveyor: Standard conveyor with a flat belt surface.
Modular Belt Conveyor: Features a belt made of interlocking plastic modules.
Cleated Belt Conveyor: Has raised cleats on the belt surface to prevent material from sliding.
Curved Belt Conveyor: Designed to go around curves and corners.
Incline/Decline Belt Conveyor: Used for moving materials between different elevations.
Slider Bed Conveyor: Features a smooth surface under the belt for it to slide on.
Roller Bed Conveyor: Uses rollers underneath the belt to support heavier loads.
Last Updated on June 18, 2024 by Jordan Smith
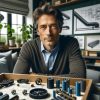
Jordan Smith, a seasoned professional with over 20 years of experience in the conveyor system industry. Jordan’s expertise lies in providing comprehensive solutions for conveyor rollers, belts, and accessories, catering to a wide range of industrial needs. From initial design and configuration to installation and meticulous troubleshooting, Jordan is adept at handling all aspects of conveyor system management. Whether you’re looking to upgrade your production line with efficient conveyor belts, require custom conveyor rollers for specific operations, or need expert advice on selecting the right conveyor accessories for your facility, Jordan is your reliable consultant. For any inquiries or assistance with conveyor system optimization, Jordan is available to share his wealth of knowledge and experience. Feel free to reach out at any time for professional guidance on all matters related to conveyor rollers, belts, and accessories.