Conveyor Belt Connector: Types and Uses
Selecting the right conveyor belt connector is crucial for maintaining the efficiency and longevity of a conveyor system. These connectors, also known as splices or fasteners, play a pivotal role in joining the ends of conveyor belts to ensure a continuous and smooth operation. The choice of a conveyor belt connector can significantly impact the operational efficiency, downtime, and maintenance costs of a conveyor system. There are various types of connectors available, each suited for different applications, belt types, and operational demands. From mechanical fasteners that offer quick and easy installation to vulcanized splices that provide a seamless and durable bond, understanding the specific requirements of your conveyor system is key to choosing the most appropriate connector. This introductory overview aims to highlight the importance of conveyor belt connectors and their applications in various industries, setting the stage for a deeper exploration of this essential component in conveyor belt technology.
Types of Conveyor Belt Connector
Exploring the various types of conveyor belt connectors is essential for understanding how they contribute to the seamless operation of conveyor systems. These connectors, integral to the functionality and efficiency of conveyor belts, come in different forms, each suited to specific applications and operational requirements.
Mechanical Belt Fasteners: This type of conveyor belt connector is widely used for its ease of installation and versatility. Mechanical belt fasteners join the belt ends through metal or plastic plates that are attached to the belt with hinges or staples. Here are six specific examples:
- Alligator Lacing: Ideal for light-duty belts, featuring a low-profile design that minimizes noise and wear on pulleys.
- Clipper Lacing: Uses wire hooks and is suitable for belts with a thickness of up to 12.7mm, offering a smooth joint.
- Bolt Hinged Fasteners: Best for belts subjected to frequent repairs or length adjustments, providing a strong, yet flexible joint.
- Rivet Hinged Fasteners: Known for their durability and high resistance to pull-out, suitable for heavy-duty applications.
- Plate Fasteners: Commonly used for thick, heavy-duty belts, these fasteners offer a strong splice to withstand tough conditions.
- Spiral Lace: Ideal for low-tension and small pulley applications, spiral lace offers a seamless joint with easy installation.
Vulcanization: This process involves the chemical bonding of conveyor belt ends through heat and pressure, creating a strong and seamless splice. Vulcanization can be categorized into two processes:
- Hot Vulcanization: This method uses heat and pressure along with a vulcanizing cement or material to bond the belt ends. The process requires specialized equipment and skilled technicians but results in a very strong and durable joint, ideal for high-tension and critical applications.
- Cold Vulcanization: Unlike hot vulcanization, this process does not involve heat. Cold vulcanization uses a bonding agent that cures at room temperature to splice the belt ends. It is less labor-intensive and does not require specialized equipment, making it a suitable option for quick repairs and less demanding applications.
Each type of conveyor belt connector has its unique advantages and is chosen based on the specific needs of the conveyor system, including the belt material, operational environment, and the load it carries. Understanding these types and their applications ensures the selection of the most appropriate connector, contributing to the optimal performance and longevity of the conveyor system.
Conveyor Belt Connector Types and Sizes
The diversity in conveyor belt connector types and sizes accommodates a wide range of applications, from light-duty material handling to heavy-duty mining operations. Understanding the differences and specific uses of these connectors is crucial for optimizing conveyor system performance.
Heavy-Duty vs. Light-Duty Connectors: Differences and Applications
Hinged Plate and Solid Plate Fasteners: Features and Suitable Applications
Hinged Plate Fasteners are ideal for belts that require frequent length adjustments or repairs. They offer flexibility and ease of installation, making them suitable for applications with smaller pulleys or where belts need to be frequently disconnected.
- Flexco® Bolt Hinged: Designed for belts with a thickness of up to 12.7mm, offering easy installation and maintenance.
- Minet Lacing Technology (MLT) MS® Fasteners: Suitable for heavy-duty applications, providing strong resistance to wear and tear.
- Goro Titan Fasteners: Known for their durability in harsh conditions, ideal for quarry and mining applications.
Solid Plate Fasteners provide a strong, sift-free splice, making them suitable for heavy-duty applications where a smooth splice is crucial.
- Flexco® SR™ Rivet Hinged Fasteners: Designed for demanding applications, offering a high strength-to-weight ratio.
- Alligator® Ready Set™: Ideal for package and parcel handling, providing a strong, yet low-profile splice.
- Clipper® Wire Hook Fasteners: Suitable for light-duty applications, offering quick and easy installation.
Hook and Lacing Styles: Use in Light-Duty Applications
Hook and Lacing styles are predominantly used in light-duty applications, where ease of installation and minimal impact on conveyor components are key considerations.
- Alligator® Lacing: Offers a continuous belt width with minimal interruption, ideal for applications requiring a smooth joint.
- Clipper® Unibar® Hook: Provides a strong, yet low-profile splice, suitable for belts in food processing and package handling.
- Flexco® Clipper® Wire Hooks: Designed for a variety of belt thicknesses, offering versatility and ease of use.
- Minet Lacing Technology (MLT) Super-Screw®: Offers a flexible and leak-proof splice, ideal for belts in agricultural applications.
- K27 & K28 Staple Hinged Fasteners: Suitable for light to medium-duty applications, offering ease of installation and maintenance.
- Flexco® Alligator® Plastic Rivet: Ideal for belts used in food processing, providing a splice free of metal parts.
Each conveyor belt connector type and size is designed to meet specific operational needs, ensuring the longevity and efficiency of the conveyor system. Whether for heavy-duty mining operations or light-duty packaging lines, selecting the appropriate connector is paramount for optimal system performance.
Types of Conveyor Belt Fasteners
The selection of the right conveyor belt connector is pivotal for the optimal performance and longevity of conveyor systems. Conveyor belt fasteners are a key component in this selection process, offering various solutions tailored to different operational needs. Below is a detailed comparison of various types of conveyor belt fasteners, including popular options like Flexco belt fasteners.
Comparison of Conveyor Belt Fastener Types
Advantages and Disadvantages of Each Conveyor Belt Connector Type
Each type of conveyor belt fastener offers unique benefits and potential drawbacks, making it crucial to consider the specific requirements of your conveyor system, including the type of material being transported, the environment in which the system operates, and the desired balance between strength and flexibility.
Heavy-Duty Conveyor Belt Connector
In demanding industrial environments such as mining, cement, and aggregate industries, selecting the right heavy-duty conveyor belt connector is crucial for ensuring operational efficiency, durability, and reliability. These connectors are designed to withstand harsh conditions, including heavy loads, abrasive materials, and extreme weather conditions.
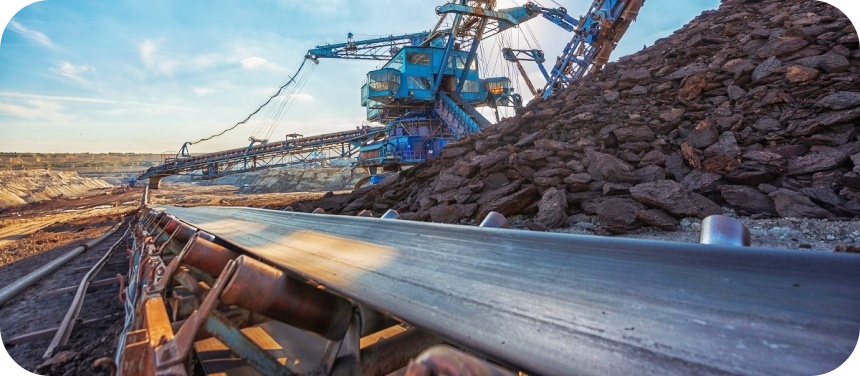
Connectors Suitable for Challenging Environments
- Flexco® SR™ Rivet Hinged Fasteners: Ideal for high-tension applications in mining and aggregates, these fasteners offer exceptional resistance to the demanding conditions of heavy-duty operations.
- Goro Titan Fasteners: Known for their robust construction, Goro Titan fasteners are suitable for heavy-duty belts in mining and quarrying, providing a strong, reliable splice.
- Minet Lacing Technology (MLT) Super-Screw®: This flexible rubber splice uses self-tapping screws, making it adaptable to all types of belts and suitable for heavy-duty applications where vulcanization is not an option.
- Flexco® Bolt Solid Plate Fasteners: Designed for the toughest applications, these fasteners provide a strong, sift-free splice for heavy-duty belts, making them suitable for mining, cement, and aggregates.
- Alligator® Staple Fastening System: While typically used in lighter applications, the Alligator® system also offers a heavy-duty version suitable for sand, gravel, and crushed stone, providing a strong, yet low-profile splice.
- MLT MS® Fasteners: These heavy-duty fasteners are designed for challenging environments, offering high resistance to wear and tear, making them ideal for mining, cement, and aggregate industries.
Emphasis on Durability and Reliability
- Flexco® SR™ Rivet Hinged Fasteners: Their high tensile strength and durability make them reliable in the most challenging conditions, ensuring long service life.
- Goro Titan Fasteners: The robust design and high-quality materials used in Goro Titan fasteners provide a reliable connection that minimizes maintenance and downtime.
- MLT Super-Screw®: The innovative design and flexibility of the Super-Screw® allow it to withstand impacts and abrasion, ensuring reliability in heavy-duty applications.
- Flexco® Bolt Solid Plate Fasteners: The solid plate design ensures a strong splice that can withstand the high impact and heavy loads typical of heavy-duty environments.
- Alligator® Staple Fastening System: The heavy-duty version of this system is engineered for enhanced durability, capable of resisting the harsh conditions of heavy industries.
- MLT MS® Fasteners: These fasteners are specifically designed for heavy-duty applications, offering high resistance to wear and ensuring reliability even in the most demanding conditions.
In heavy-duty applications, the choice of a conveyor belt connector significantly impacts the conveyor system’s efficiency, maintenance requirements, and overall operational costs. The aforementioned heavy-duty conveyor belt connectors are engineered to meet the rigorous demands of industries where durability and reliability are paramount, ensuring uninterrupted operation and longevity of the conveyor system.
Conveyor Belt Connector Fastener Tools
The installation of a conveyor belt connector is a precise process that requires specific tools to ensure effectiveness and safety. The right tools not only facilitate a secure and durable connection but also significantly reduce installation time and potential downtime. Below is an overview of essential tools required for installing various types of conveyor belt fasteners, along with tips for effective and safe installation.
Essential Tools for Conveyor Belt Connector Installation
- Belt Skivers: These tools are used to remove the top cover of the conveyor belt, preparing the surface for a lower-profile splice that reduces wear on the splice and the conveyor system components.
- Belt Cutters: A clean, straight cut is crucial for a strong splice. Belt cutters ensure a precise cut across the belt width, preparing the ends for a uniform splice.
- Lacing Tools: For fasteners like Alligator® Lacing, lacing tools are used to properly position and secure the lacing in the belt ends, ensuring a flat and smooth splice.
- Installation Tools for Rivet Hinged Fasteners: These specialized tools help in accurately applying rivet hinged fasteners like the Flexco® SR™ series, ensuring the rivets are properly set for a strong, durable splice.
- Bolt Fastener Installation Tools: Tools such as wrenches and bolt breakers are essential for installing bolt solid plate fasteners, ensuring the bolts are tightened to the correct tension and then trimmed flush with the belt surface.
- Roller Lacers: For certain hook and loop fasteners, roller lacers efficiently press the fasteners into the belt, ensuring a consistent and secure attachment across the belt width.
Tips for Effective and Safe Conveyor Belt Connector Installation
- Proper Training: Ensure that personnel involved in the installation process are properly trained in the use of fastening tools and safety procedures.
- Preparation: Thoroughly prepare the belt ends according to the fastener manufacturer’s instructions, including skiving and cutting, to ensure the best possible splice.
- Alignment: Carefully align the belt ends before fastening to ensure a straight, smooth splice that will not cause tracking issues or premature wear.
- Tension: Follow the manufacturer’s guidelines for fastener tension to avoid over-tightening, which can damage the belt and fasteners, or under-tightening, which can lead to splice failure.
- Inspection: After installation, inspect the splice and the surrounding belt area to ensure there are no sharp edges or protrusions that could damage the belt or the conveyed material.
- Safety Gear: Always wear appropriate safety gear, including gloves and eye protection, when cutting, skiving, and installing conveyor belt connectors.
Using the right tools and following these tips can significantly enhance the efficiency, durability, and safety of conveyor belt connector installations, contributing to the overall reliability and longevity of the conveyor system.
Finding Conveyor Belt Connector Fasteners Suppliers
Locating reliable suppliers for conveyor belt connectors is a critical step in ensuring the efficiency and longevity of your conveyor system. The right supplier not only provides high-quality fasteners but also offers valuable support and services. Here are key considerations when choosing a supplier for conveyor belt connectors, with Flexco highlighted as a notable example.
Considerations for Choosing a Conveyor Belt Connector Supplier
- Product Range: Look for suppliers with a wide range of conveyor belt connectors to ensure compatibility with your specific conveyor belt type and application. This diversity allows for more tailored solutions to your conveyor system’s needs.
- Quality Assurance: Ensure the supplier has a strong reputation for quality. High-quality fasteners contribute to the durability and reliability of your conveyor system. Certifications or compliance with industry standards can be indicators of quality.
- Technical Support: A supplier that offers comprehensive technical support, including installation guidance and troubleshooting, can be invaluable, especially for complex conveyor systems or when transitioning to a new type of connector.
- Availability and Lead Times: Consider the supplier’s ability to fulfill orders promptly. Short lead times and high availability can minimize downtime, especially in critical repair or maintenance situations.
- Customization Options: Some applications may require customized fastening solutions. Suppliers like Flexco that offer customization can provide connectors tailored to your specific operational requirements.
- After-Sales Service: Post-purchase support, including warranty services and the availability of replacement parts, ensures that you can maintain the efficiency of your conveyor system over time.
Flexco: A Notable Conveyor Belt Connector Supplier
Flexco stands out as a leading supplier in the conveyor belt connector market. Known for their extensive product range, Flexco offers a variety of fasteners suitable for different belt types and applications, from light-duty material handling to heavy-duty mining operations. Their catalog provides detailed information on each product, helping customers select the most appropriate fasteners for their needs.
Flexco also emphasizes quality assurance, with products designed to meet high durability and reliability standards. Their technical support team is well-regarded for providing expert advice, installation guidance, and ongoing support, ensuring customers get the most out of their conveyor belt connectors.
When sourcing conveyor belt connectors, considering these factors and exploring reputable suppliers like Flexco can significantly impact the performance and longevity of your conveyor system.
Fill Out the Inquiry Form: Let us know your conveyor belt needs, and we’ll get back to you with a quote and relevant details.
Conveyor Belt Connector and Jointing Kits
Conveyor belt lacing plays a pivotal role in the splicing process, serving as a critical conveyor belt connector that joins the ends of a belt to form a continuous loop. Lacing comes in various forms, each designed to address specific needs based on the belt material, thickness, and application. Jointing kits, on the other hand, provide all the necessary tools and components for effective belt repair and maintenance, ensuring the longevity and efficiency of the conveyor system.
Conveyor Belt Lacing: Types and Applications
- Alligator Lacing: Ideal for light- to medium-duty applications, Alligator lacing provides a strong, yet low-profile splice, minimizing interference with conveyor components and products.
- Clipper Lacing: Utilizes wire hooks and is suitable for a wide range of belt thicknesses. Clipper lacing is known for its versatility and ease of installation, making it a popular choice for many industries.
- Staple Hinged Lacing: Features steel staples for high strength and durability, making it suitable for heavy-duty applications where resistance to impact and abrasion is crucial.
- Plastic Rivet Lacing: A non-metallic option that provides a smooth splice, ideal for applications requiring metal-free zones or in industries such as food processing.
- Spiral Lace: Offers a flexible and seamless splice, suitable for belts operating over small pulleys and in systems requiring a high degree of flexibility.
- Rivet Hinged Lacing: Combines the durability of rivets with the flexibility of a hinged splice, ideal for heavy-duty applications with varying loads and impacts.
Introduction to Conveyor Belt Jointing Kits
Conveyor belt jointing kits are essential for the repair and maintenance of conveyor belts, ensuring quick and efficient handling of belt issues. A typical jointing kit includes:
- Lacing Tools: Specific to the type of lacing being used, these tools ensure the correct installation of the lacing into the belt ends.
- Skiving Tools: Used to remove the top layer of the belt where the splice will be made, ensuring a flat, even surface for the lacing.
- Cutting Tools: Provide a clean, straight cut across the belt, essential for a strong, even splice.
- Punches and Drills: For fasteners that require bolt holes, these tools create precise holes in the belt ends for bolt insertion.
- Fasteners and Rivets: A selection of fasteners and rivets compatible with the belt material and application, ensuring a strong and durable splice.
- Installation Instructions: Detailed guidelines on how to properly use the tools and components in the kit for effective belt repair and maintenance.
Equipped with the right conveyor belt lacing and a comprehensive jointing kit, maintenance teams can effectively address belt issues, minimizing downtime and maintaining the smooth operation of the conveyor system. These tools and components are crucial for ensuring the reliability and longevity of conveyor belt connectors in various industrial applications.
FAQs About Conveyor Belt Connector
Connecting conveyor belts together is a critical process that ensures the smooth operation of the conveyor system. The most common method to connect conveyor belts is through mechanical fastening or vulcanization. Mechanical fastening involves using metal or plastic fasteners to join the ends of the belts. This method is preferred for its simplicity, cost-effectiveness, and the ability to quickly disconnect and reconnect the belts if needed. Vulcanization, on the other hand, involves the use of heat, pressure, and a bonding material to splice the belt ends together, creating a seamless and strong joint. This method is more permanent and is typically used for heavy-duty applications where the strength of the belt joint is crucial. The choice between these methods depends on the specific requirements of the conveyor system, including the type of material being transported, the operating environment, and the need for belt flexibility.
Joining a conveyor belt involves carefully aligning the belt ends and choosing an appropriate splicing method. The two primary methods for joining conveyor belts are mechanical splicing and vulcanization. Mechanical splicing uses fasteners to join the belt ends, which can be installed using simple tools and do not require specialized skills. This method allows for easy installation and removal, making it suitable for temporary or movable conveyor systems. Vulcanization, on the other hand, creates a strong, seamless joint by applying heat, pressure, and a vulcanizing agent to the belt ends. This method requires specialized equipment and skilled technicians but results in a durable and high-strength joint. The choice of joining method depends on the belt’s application, the materials being conveyed, and the operational demands of the conveyor system.
Connecting the ends of a conveyor belt is a crucial step in setting up or repairing a conveyor system. The process typically involves aligning the belt ends, trimming them to ensure a clean, straight edge, and then choosing a splicing method. Mechanical splicing involves using hinges or fasteners to connect the belt ends, which is a quick and straightforward process that can be done on-site with basic tools. Vulcanization, a more permanent solution, involves using heat and pressure to bond the belt ends together with a rubber or plastic compound. This method requires specialized equipment and skilled personnel but provides a stronger and more durable joint. The choice of method depends on various factors, including the belt type, the material being conveyed, and the operational requirements of the conveyor system.
Joining a broken conveyor belt requires assessing the extent of the damage and deciding on the most appropriate repair method. For minor damages, such as small tears or punctures, a patch can be applied using mechanical fasteners or a cold vulcanization process. This involves cleaning the damaged area, applying a suitable adhesive, and then placing a patch over the area, which is then secured in place. For more significant damages, such as a complete break, the ends of the belt must be squared off and joined using either mechanical splicing or vulcanization. Mechanical splicing involves using metal or plastic fasteners to join the ends, which is a quick and cost-effective method suitable for temporary repairs or belts with low tension. Vulcanization provides a more permanent solution by using heat, pressure, and a bonding agent to create a seamless and strong joint, ideal for high-tension belts and critical applications. The choice of repair method depends on the belt’s condition, the type of material being conveyed, and the operational requirements of the conveyor system.
Last Updated on July 22, 2024 by Jordan Smith
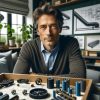
Jordan Smith, a seasoned professional with over 20 years of experience in the conveyor system industry. Jordan’s expertise lies in providing comprehensive solutions for conveyor rollers, belts, and accessories, catering to a wide range of industrial needs. From initial design and configuration to installation and meticulous troubleshooting, Jordan is adept at handling all aspects of conveyor system management. Whether you’re looking to upgrade your production line with efficient conveyor belts, require custom conveyor rollers for specific operations, or need expert advice on selecting the right conveyor accessories for your facility, Jordan is your reliable consultant. For any inquiries or assistance with conveyor system optimization, Jordan is available to share his wealth of knowledge and experience. Feel free to reach out at any time for professional guidance on all matters related to conveyor rollers, belts, and accessories.