Innovative Conveyor Belt Corner Solutions for Small Spaces
The world of material handling and logistics is intricately designed to enhance efficiency and productivity. At the heart of this intricate design lies the conveyor belt, a fundamental tool that has revolutionized the way industries move materials and products. From the sprawling assembly lines of automotive factories to the bustling corridors of airport baggage handling systems, conveyor belts play a pivotal role. However, not all conveyor paths are straight; this is where the concept of the conveyor belt corner becomes crucial.
Conveyor belt corners allow for the seamless change of direction of a conveyor belt path, enabling facilities to optimize space and improve operational flow. In essence, the implementation of a conveyor belt corner can dramatically transform the layout of a production floor, warehouse, or any area where conveyor belts are utilized. The importance of these corners cannot be overstated. They not only facilitate a smooth transition and flow of goods but also contribute significantly to the overall efficiency of the conveyor system. Without these ingeniously designed corners, the flexibility and functionality of conveyor systems would be significantly hindered, showcasing their indispensable role in the world of material handling.
Used Conveyor Belt Corner: A Cost-Efficient Approach
In an era where businesses are constantly seeking ways to optimize their operations and reduce costs, the appeal of used machinery and equipment has significantly increased. Within the realm of material handling, the demand for used conveyor belt corners illustrates a keen interest in achieving cost efficiency without compromising functionality. These pivotal components, crucial for optimizing space and enhancing the flow within production lines, can be quite an investment when purchased new. Thus, many businesses turn to the used market to find cost-effective solutions.
The Demand for Used Conveyor Belt Corners
As industries expand and renovate their facilities, the need for conveyor systems that are both efficient and adaptable becomes paramount. The used conveyor belt corner market thrives on this necessity. Companies looking to upgrade or modify their conveyor systems without extensive costs find great value in these pre-loved items. The environmental aspect also plays a role, with many businesses aiming to reduce their carbon footprint by opting for used equipment, underlining a growing trend towards sustainability.
Factors to Consider When Buying Used Conveyor Belt Corners
Purchasing a used conveyor belt corner requires a thorough assessment to ensure it meets your specific needs. Key factors to consider include:
- Condition and Longevity: Understanding the wear and tear on the conveyor belt corner is essential. It’s crucial to inspect for any damage or signs of excessive wear that might affect its performance or necessitate early replacement.
- Compatibility: Ensure the used conveyor belt corner fits seamlessly with your existing conveyor system. Mismatched components can lead to operational inefficiencies or require additional modifications.
- Supplier Reputation: Purchasing from reputable suppliers who are known for quality used equipment can mitigate risks. Seek out suppliers who offer some form of guarantee or return policy on their used items.
- Price vs. Performance: While cost savings are a significant advantage, balancing the price with the expected performance and longevity of the conveyor belt corner is vital. The cheapest option isn’t always the most cost-effective in the long run.
Places Where Used Conveyor Belt Corners Can Be Purchased
Identifying the right source for purchasing a used conveyor belt corner is as crucial as the equipment itself. Several avenues offer opportunities to find quality used components:
- Specialized Online Marketplaces: Websites dedicated to used industrial equipment often list conveyor system components, including corners. These platforms provide a broad range of options from various sellers, allowing for comparison.
- Auctions and Liquidation Sales: Businesses closing down or upgrading their facilities may auction off their existing equipment. These events are excellent opportunities to purchase used conveyor belt corners at competitive prices.
- Refurbishing Companies: Some companies specialize in refurbishing industrial equipment, including conveyor systems. Purchasing from these companies can offer peace of mind, as the equipment often comes with some certification of quality or a limited warranty.
Investing in a used conveyor belt corner can be a pivotal decision for many businesses looking to optimize their operations economically. Through careful consideration and diligent selection, companies can benefit from these cost-efficient solutions, proving that quality and performance need not be compromised for the sake of budget.
Modern Use Cases: Conveyor Belt Sushi Tysons Corner
Conveyor belt corners aren’t solely restricted to industrial environments. They have found a culinary niche that’s as delicious as it is fascinating: sushi conveyors, or kaiten sushi. Among the top locations where you can experience this delightful fusion of technology and gastronomy is Tysons Corner Mall, where the conveyor belt sushi delights patrons.
Introduction to the Concept of Sushi Belt Conveyors
Sushi belt conveyors, or kaiten sushi, revolutionized the sushi dining experience when it was introduced in the 1950s in Japan. The concept brought a fun, interactive element to dining, where customers could pick freshly made sushi from a moving conveyor belt. Here, a conveyor belt corner is an integral part, guiding the sushi plates around bends and allowing for maximum seating and comfort for diners around the conveyor.
Traditionally, the belt runs in an oval shape for sushi chefs to place their sushi masterpieces at one end. Diners then pick their choice of sushi as the plates pass by their seats. This process provides a visually engaging gastronomical journey—seeing an array of sushi rotate on the conveyor is truly a spectacle!
The Unique Experience and Popularity of Sushi Conveyor Belts at Tysons Corner Mall
At Tysons Corner Mall, conveyor belt sushi is a star attraction. Patrons enjoy a modern, yet authentic, sushi dining experience revolving—quite literally—around the conveyor belt corner, the point around which the conveyor gracefully bends its route among the diners. It adds an interactive aspect, turning a meal into a mesmerizing display of Japanese culinary artistry.
This dining concept’s unique appeal lies in the combination of visual charm and immediate gratification. Diners can directly pick up plates of tempting sushi passing by their table, making their choices based on real-time visual appeal, rather than a menu. They witness a sushi parade that merges tradition and innovation while ensuring the uncompromising freshness of their chosen delicacies.
The conveyor belt sushi at Tysons Corner Mall has quickly surged in popularity thanks to its unique dining experience. It mirrors a broader trend where conveyor belt corners are enriching and diversifying dining experiences around the world.
Conveyor belt corners, thus, demonstrate versatility—be it in the industrial sector or as part of unique dining experiences. It’s an indication of how fundamentally simple yet functional design can transform various areas of our lives.
Conveyor Belt Corner Types
When optimizing the layout of a conveyor system, adapting to the spatial constraints of a facility is essential. Conveyor belt corner sections play a pivotal role in this adaptation, allowing conveyor belts to maneuver through tight spaces, around obstacles, and maintain the flow of materials in a controlled and efficient manner. Understanding the various conveyor belt corner types is crucial for effectively integrating them into any material handling setup.
Brief about Major Conveyor Belt Corner Types
Different types of conveyor belt corner designs accommodate various industrial needs, ensuring they blend seamlessly with the entire conveyor system. Here are some of the major types:
- Roller Conveyor Corners: These corners are characterized by a series of rollers positioned at an angle to facilitate the change of direction. They are ideal for handling rigid-bottomed items and can handle varying weights depending on roller size and spacing.
- Belted Conveyor Corners: These feature a continuous belt surface that wraps around the corner. They’re typically used where a smooth transition is necessary to handle smaller items or products that might be jostled by rollers.
- Modular Conveyor Corners: Modular conveyors use a series of short, interlocking pieces and are versatile enough to be configured into corners. This design allows for flexible layouts and can be easily reconfigured if the system’s layout needs to change.
- Vertical Conveyor Corners: When elevation is a factor, vertical conveyor corners are employed. They transfer products to different heights, thereby efficient use is made of three-dimensional space.
Insights on the Corner Track Belt Conveyor
Among the different types, the corner track belt conveyor is noteworthy for its precision and efficiency. This conveyor belt corner usually features a curved track that the conveyor belt follows, enabling it to maintain the orientation of products while turning corners. This is particularly beneficial in packaging and assembly operations where maintaining product position is critical.
Here are key advantages of this conveyor belt corner type:
- Space Efficiency: It’s an excellent space-saver, as it allows conveyor systems to utilize corners that would otherwise be dead space.
- Product Safety: It provides a smooth transition for delicate products, minimizing damage risks during the turn.
- Low Maintenance: Since the belt moves around a fixed track, there are fewer moving parts in the corner section, which means lower maintenance costs and less downtime.
- Customization: The corner track belt conveyors can be designed to fit specific radius requirements and can accommodate various belt widths and materials, ensuring compatibility with a wide range of products and applications.
When selecting a corner track belt conveyor, it’s vital to consider factors such as the turning radius, belt speed, product size, and weight. An adequately chosen conveyor belt corner will enhance the efficiency of a conveyor system, reduce wear and tear on products and the conveyor itself, and expedite the overall material handling process.
Conveyor Belt Corner Specifications
Understanding the specifications of a conveyor belt corner is crucial in choosing the perfect system. This section will delve into the specifics around common conveyor belt corner sizes and conveyor belt corner material types, including their distinct applications.
Discussion Around Common Conveyor Belt Corner Sizes
The size of your conveyor belt corner largely depends on the operations and the specific requirements of your system. In general, there are standard sizes available in the market catering to most industrial needs.
The width of a conveyor belt corner usually ranges from 20mm to up to 2000mm and corners commonly offer 90-degree or 180-degree curves. However, it’s essential to remember that these sizes can vary based on the specific model and manufacturer. As a rule of thumb, the size of the conveyor belt corner should match the width of the conveyor belt used in the rest of the system, and the radius of the corner should accommodate the largest product you plan to transport.
If you are managing heavy-duty materials, you must ensure that the conveyor belt corners are robust enough to bear the weight and bulk. For instance, large warehouses, assembly lines, or package handling facilities would potentially require more extensive conveyor belt corners for effective and safe material handling.
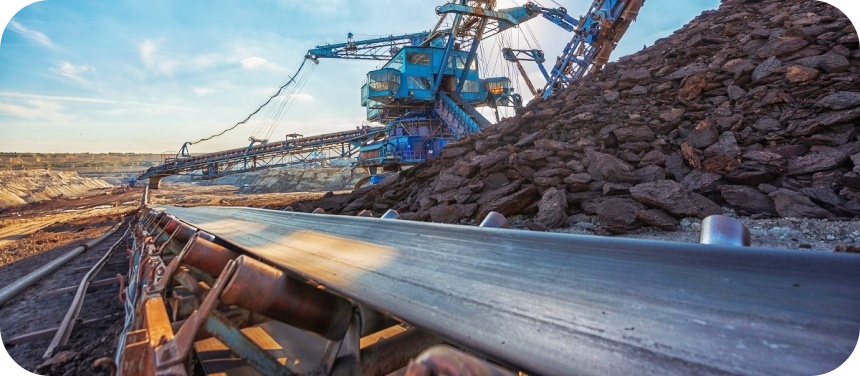
Conveyor Belt Corner Material Types and their Applications
The material type of a conveyor belt corner plays a significant role in determining its durability, functionality, and suitability to your specific needs. Let’s discuss some common materials used in conveyor belt corners and their applications.
- PVC Conveyor Belt Corners:
PVC or Polyvinyl Chloride is a popular choice for conveyor belt corners due to their versatility and durability. They are suitable for light to medium applications, including food industry, package handling, and assembly lines. PVC conveyor belt corners are resistant to fats, oils, and chemicals, making them ideal for industries requiring stringent hygiene controls. - Rubber Conveyor Belt Corners:
In situations requiring high friction for secure material handling or extreme temperature conditions, rubber conveyor belt corners are the preferred choice. Industries such as mining, quarrying, or heavy-duty manufacturing favor rubber due to its durability and resilience to wear and tear. - Metal Conveyor Belt Corners:
In high-temperature situations or where there’s a need for easy-to-clean, rust-resistant material, metal conveyor belt corners are feasible. They are mostly used in food processing, pharmaceuticals, or industries requiring sanitary handling of materials.
Choosing the correct conveyor belt corner specifications is critical in optimizing your operation. By understanding the common sizes and material types available, you’ll be better equipped to select the conveyor belt corner design that fits your needs and enhances your system’s efficiency.
Solving Conveyor Belt Corner Problems
Optimizing the performance of your conveyor system requires addressing issues specifically related to conveyor belt corners. Here, we explore solutions to frequent problems and provide maintenance tips to ensure the efficient operation of your conveyor belt corners.
Troubleshooting Common Conveyor Problems with Conveyor Belt Corners
- Misalignment: Misalignment in conveyor belt corners can cause uneven wear, potential damage to the conveyor belt, and lead to product slippage or spillage. To address misalignment, ensure that all conveyor components and the belt corners are correctly aligned and that the conveyor frame is not warped or damaged. Regularly inspect the conveyor belt’s path and make adjustments to the tension and tracking as needed to prevent misalignment.
- Blockages: Material blockages at conveyor belt corners can disrupt the smooth flow of operations. These blockages often occur due to improper conveyor speed, oversized materials, or sharp turns that the materials cannot navigate. To solve this, first, clear any jammed material from the conveyor belt corner. Then, review the corner’s design to ensure it matches the type of materials you are handling, and adjust the conveyor speed to match the capacity and flow of materials through the corner.
- Wear and Tear: Conveyor belt corners often experience more wear than straight sections due to the increased friction and pressure from changing directions. Regularly inspect corners for signs of wear, such as thinning, tearing, or cracking of the belt material. Consider using materials specifically designed for high friction areas or installing wear plates that can be easily replaced.
Maintenance Tips to Keep Your Conveyor Belt Running Smoothly
- Regular Inspection: Conduct frequent inspections of the conveyor belt corners for any signs of misalignment, wear, or damage. Identifying issues early can prevent costly repairs and downtime.
- Proper Cleaning: Keeping the conveyor belt corners clean is essential for maintaining optimal performance. Build-up of materials can lead to blockages or increased wear. Implement a regular cleaning schedule, paying close attention to the corners where materials can accumulate.
- Lubrication: If your conveyor system uses rollers or bearings in the corners, ensure they are adequately lubricated to reduce friction and prevent wear. Use the correct type of lubricant as recommended by the manufacturer, and apply it at intervals specified in the maintenance manual.
- Correct Conveyor Belt Tension: Incorrect tension can lead to numerous problems, including misalignment and increased wear at the corners. Ensure that the conveyor belt is tensioned correctly according to the manufacturer’s guidelines.
- Professional Training: Ensure that staff responsible for the operation and maintenance of the conveyor system are adequately trained. Understanding how to correctly operate the system and troubleshoot common issues can significantly reduce the risk of problems occurring.
By actively troubleshooting common conveyor problems related to conveyor belt corners and adhering to a strict maintenance schedule, you can significantly enhance the longevity and efficiency of your conveyor system. These proactive steps not only contribute to the smooth operation of the conveyor belt but also safeguard against unexpected failures that can disrupt production.
Conveyor Belt Corner Formula for Success: Proper Planning and Design
The integration of a conveyor belt corner into your system is not just about adding a curve; it’s about ensuring that every element of your conveyor belt system, including the corner elements, is meticulously planned and designed. This process is critical for optimizing efficiency, reducing downtime, and prolonging the life of the conveyor system.
Introduction to Design Factors for Conveyor Belt System, Including Corner Elements
Designing a conveyor belt system requires a comprehensive understanding of various factors that influence its performance and durability. When it comes to integrating conveyor belt corners, several additional considerations come into play:
- Material Handling Requirements: Understand the types of materials the system will transport. The weight, size, and nature of the materials can significantly influence the design of the conveyor belt corner, dictating factors like the radius of the corner, the belt material, and the speed at which the belt should operate.
- Space Constraints: Often, the available space dictates the design of your conveyor belt system. Conveyor belt corners can help navigate tight spaces effectively but require precise calculation to ensure they fit the available area while maintaining operational efficiency.
- Load Capacity: The corner conveyor belt must be able to handle the expected load without compromise. This includes considering the maximum load and ensuring that the corner’s structure and the belt material are designed to accommodate this weight without excessive wear.
- Speed Considerations: The speed at which the conveyor belt moves impacts how materials transition through corners. Too fast, and materials may slip or tip over; too slow, and it could lead to bottlenecks. The design must strike a perfect balance to maintain continuous flow.
The Importance of Proper Design and Planning for Efficiency and Longevity
A well-thought-out design and planning phase for incorporating a conveyor belt corner into your system are paramount for several reasons:
- Efficiency: A properly designed conveyor belt corner ensures a smooth transition of materials around bends, minimizing the risk of blockages or spillages. This seamless operation is crucial for maintaining an efficient production line, preventing downtime, and ensuring a consistent flow of materials.
- Safety: Safety in the workplace is non-negotiable. By considering all potential hazards and designing the corner conveyor belt accordingly, incidents caused by malfunctioning equipment can be significantly reduced. This includes proper shielding, emergency stops, and designing corners that minimize sharp turns where accidents could occur.
- Longevity: Every component of the conveyor system, including the corners, contributes to its overall lifespan. By carefully selecting materials that resist wear and tear and designing the corner to distribute stress evenly, you can extend the life of the conveyor belt system, offering a better return on investment.
- Flexibility: Future-proofing your design by considering potential changes in operation or scale can save costs and time down the line. A well-designed conveyor belt corner should allow for adjustments, be it in speed, direction, or materials handled.
The success of a conveyor belt system, particularly the integration of conveyor belt corners, hinges on meticulous planning and thoughtful design. By understanding the intricacies involved in proper conveyor belt corner incorporation—from handling requirements and space constraints to load capacity and speed considerations—you set the stage for a system that excels in efficiency, safety, and longevity.
Get in touch for durable and reliable conveyor belts.
Contact us for the best deals on conveyor belts.
FAQs About Conveyor Belt Corner
A conveyor belt system comprises several integral components, including:
Belt Support Systems: These prevent the belt from sagging or falling between conveyors. They come in various forms, like impact idlers or slider bed supports.
Pulley: A conveyor belt operates between two pulleys, which can be powered or non-powered. Motor power typically drives the drive pulley, causing the conveyor belt’s motion, while the non-powered pulley, often termed the idler, aids the belt’s movement.
Drive Unit: This is the component that powers the system. The conveyor belt’s speed and direction of movement are determined by this unit. It typically comprises an electric motor and an assembly of gears.
Conveyor Belt: This is the physical surface on which the goods travel. Conveyor belts are often constructed from robust materials like PVC or rubber and may feature different textures or grip strength to handle different types of goods.
Belt Cleaners: These are devices employed to keep the conveyor belt clean and enhance its longevity. They’re particularly essential when the conveyed material is sticky or dirty.
The end of a conveyor is often referred to as the “discharge point” or the “tail.” This is where the material or goods are off-loaded from the conveyor belt. This could be a straightforward drop-off point, or for more advanced systems, it might involve mechanical apparatus like chutes or robotic arms to aid in managing the positioning and direction of the unloaded goods. The design of the tail is crucial for ensuring smooth operations and reducing the probability of conveyor jams.
Even a simple conveyor belt comprises several parts that collaborate to ensure smooth operations. These include:
Drive Pulley: This is the pulley that is connected to a motor and drives the movement of the conveyor belt.
Idler Pulley: These pulleys maintain the belt tension and guide the conveyor belt’s path.
Conveyor Belt: This is the physical surface that carries goods or materials. It’s typically made of strong materials like rubber or PVC.
Frame: The steel or aluminium structure that supports the belt and the entire system.
Motor: This is the power source that drives the movement of the drive pullet and subsequently the conveyor belt.
Though simple conveyor systems may lack advanced features like belt cleaners or automatic control systems, these essential components ensure they can transport goods effectively across both short and long distances.
Preventing conveyor belt misalignment requires both proactive and reactive measures.
Proactive Maintenance: Regularly inspect and maintain the conveyor system. Check for signs of wear, tear, or damage to both the conveyor belt and the physical components (like idlers, pulleys). Parts that are excessively worn might contribute to misalignment.
Proper Installation and Adjustment: Make sure that the pulleys and idlers are installed correctly and are level with each other. They need to be square to the belt’s direction of travel to ensure the belt moves straight.
Belt Tension: Maintaining the correct belt tension is vital. If it’s too loose, it may slip and lead to misalignment. If it’s too tight, it can cause excessive wear and even premature equipment failure.
Training the Belt: Belt training involves adjusting the idlers, pulleys, and loading conditions to control and correct the belt tracking. Self-aligning idlers and return training idlers can automatically square the belt and maintain alignment.
Taking these measures will effectively minimize occurrences of conveyor belt misalignment, ensuring smooth and efficient operation of your conveyor system.
Last Updated on June 21, 2024 by Jordan Smith
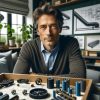
Jordan Smith, a seasoned professional with over 20 years of experience in the conveyor system industry. Jordan’s expertise lies in providing comprehensive solutions for conveyor rollers, belts, and accessories, catering to a wide range of industrial needs. From initial design and configuration to installation and meticulous troubleshooting, Jordan is adept at handling all aspects of conveyor system management. Whether you’re looking to upgrade your production line with efficient conveyor belts, require custom conveyor rollers for specific operations, or need expert advice on selecting the right conveyor accessories for your facility, Jordan is your reliable consultant. For any inquiries or assistance with conveyor system optimization, Jordan is available to share his wealth of knowledge and experience. Feel free to reach out at any time for professional guidance on all matters related to conveyor rollers, belts, and accessories.