Conveyor Belt Cost Per Meter|Cost of Conveyor belt
Conveyor belts play a critical role in industrial operations, serving as the backbone of material handling processes across various sectors. The efficiency and effectiveness of these systems directly impact productivity and operational costs. Understanding conveyor belt cost per meter is essential for businesses looking to optimize their budgets and ensure smooth operations. Several factors influence the cost per meter of a conveyor belt, including the material used, belt width and length, and the specific application requirements. By gaining a comprehensive understanding of these factors, companies can make informed decisions, selecting the most cost-effective and suitable conveyor belts for their needs. This guide provides insights into these elements, helping you navigate the complexities of conveyor belt pricing.
The Basics of Conveyor Belt Pricing: Understanding Conveyor Belt Cost per Meter
Understanding the basics of conveyor belt pricing is crucial for any business that relies on conveyor systems for their operations. The conveyor belt cost per meter can vary significantly based on several factors, and it’s important to comprehend these components to make informed purchasing decisions. This section delves into the key elements that influence the cost per meter of a conveyor belt and compares the costs between new and used belts.
Components of Conveyor Belt Pricing
Several factors contribute to the conveyor belt cost per meter. These factors include the type of material used, belt dimensions, construction, and additional features such as coatings or reinforcements. Here’s a detailed look at these components.Each of these factors plays a significant role in the final pricing, and understanding them can help you select the most cost-effective option for your needs.:
Material Type
The material used in the construction of a conveyor belt is one of the most significant determinants of its cost. Common materials include rubber, PVC, and metal. Each material has unique properties that make it suitable for different applications:
- Rubber: Rubber belt known for its durability and flexibility, rubber mining belts are commonly used in industries like mining and manufacturing. The cost per meter for rubber belts is generally higher due to their robust nature and long lifespan.
- PVC: PVC belts are less expensive than rubber and are often used in food processing and packaging industries. They offer good chemical resistance but may not be as durable as rubber.
- Metal: Metal belts, typically made of stainless steel, are used in high-temperature applications and heavy-duty industries. These belts are the most expensive due to their strength and resistance to extreme conditions.
Belt Dimensions
The width and length of the conveyor belt also play a crucial role in determining its cost. Wider and longer belts require more material and therefore cost more per meter. The following table illustrates how width and length affect pricing:
The type of material used in the conveyor belt significantly impacts its cost. Conveyor belts can be made from various materials, including rubber, PVC, and metal. Each material has its unique properties and cost implications:
- Rubber: Rubber conveyor belts are commonly used in industries such as mining and construction due to their durability and resistance to abrasion. However, they tend to be more expensive than other types.
- PVC: PVC belts are often used in food processing and packaging industries. They are less expensive than rubber belts but may not be as durable in harsh environments.
- Metal: Metal conveyor belts are highly durable and suitable for high-temperature applications. They are typically the most expensive option due to their material properties and manufacturing processes.
Comparison Between New and Used Conveyor Belt Cost per Meter
When considering conveyor belt pricing, it is essential to compare the costs of new and used belts. New conveyor belts are typically more expensive but offer the benefit of guaranteed quality and longer lifespan. Used conveyor belts, on the other hand, can be more cost-effective but may come with unknown wear and tear that could affect performance and longevity.
- New Conveyor Belts: New belts ensure that you are getting a product with no prior usage, providing peace of mind regarding quality and durability. However, this assurance comes at a higher price.
- Used Conveyor Belts: Purchasing used belts can save money upfront, but it is crucial to inspect them thoroughly for any signs of wear or damage that could lead to future maintenance costs or reduced efficiency.
Making the Right Choice
Choosing the right conveyor belt involves balancing cost with performance requirements. Consider the following factors to make an informed decision:
- Application Requirements: Determine the specific needs of your application, including the type of materials being transported, operating conditions, and desired lifespan of the belt.
- Budget Constraints: Assess your budget and compare the costs of new and used belts, keeping in mind the potential long-term savings of investing in a higher-quality, durable belt.
- Supplier Reputation: Choose reputable suppliers who can provide detailed information about the belts’ specifications and history, especially when purchasing used belts.
When deciding between new and used conveyor belts, it’s important to consider the specific needs of your operation, the expected lifespan of the belt, and the budget available. While new belts offer reliability and customization, used belts provide an economical solution with potential trade-offs in durability and lifespan.
Understanding the components and variations in conveyor belt cost per meter is essential for making informed decisions. Whether opting for new or used belts, businesses can optimize their investment by carefully considering their specific needs and the factors that influence pricing.
Enhance performance with our high-quality conveyor belts.
Calculating Conveyor Belt Cost Per Meter
Understanding and accurately calculating the conveyor belt cost per meter is crucial for effective budget planning in any industrial operation. To facilitate this process, a conveyor belt cost per meter calculator can be an invaluable tool. This section introduces the calculator, explains its functionality and importance, and provides a step-by-step guide on how to use it.
The Conveyor Belt Cost Per Meter Calculator
A conveyor belt cost per meter calculator is a specialized tool designed to help businesses estimate the total cost of their conveyor belt systems based on specific parameters. This calculator takes into account various factors such as the belt material, width, length, and additional features, providing a comprehensive cost estimate. Here’s how it works and why it’s essential for budget planning:
How It Works
- Input Parameters: The calculator requires users to input specific details about their conveyor belt needs, such as material type, belt width, length, and any additional features (e.g., coatings or reinforcements).
- Cost Calculation: Based on the input parameters, the calculator uses pre-defined cost data to estimate the total cost per meter of the conveyor belt.
- Detailed Breakdown: The calculator provides a detailed cost breakdown, showing how each factor contributes to the overall cost.
- Comparison Feature: Users can compare costs for different materials and configurations to find the most cost-effective option.
- Report Generation: The calculator can generate a comprehensive report, which can be used for budget planning and decision-making.
Importance for Budget Planning
- Accuracy: Provides precise cost estimates, reducing the risk of budget overruns.
- Efficiency: Saves time by automating the cost calculation process.
- Comparison: Enables easy comparison of different conveyor belt options.
- Informed Decisions: Helps businesses make informed purchasing decisions based on detailed cost analysis.
- Flexibility: Allows users to adjust parameters and see the impact on costs in real-time.
Step-by-Step Guide on Using the Calculator to Determine Conveyor Costs
To effectively use the conveyor belt cost per meter calculator, follow these steps:
Step 1: Gather Required Information
Before using the calculator, gather all necessary information about your conveyor belt requirements. This includes:
- Material Type: Determine the type of material you need (e.g., rubber, PVC, metal).
- Belt Dimensions: Measure the required width and length of the conveyor belt.
- Additional Features: Identify any additional features or customizations needed (e.g., heat resistance, chemical coatings).
Step 2: Access the Calculator
Open the conveyor belt cost per meter calculator on your computer or mobile device. Ensure you have a stable internet connection if the calculator is web-based.
Step 3: Input Parameters
Enter the gathered information into the calculator:
- Material Type: Select the material type from the drop-down menu.
- Belt Width: Enter the width of the conveyor belt in meters.
- Belt Length: Enter the length of the conveyor belt in meters.
- Additional Features: Select any additional features or customizations required.
Step 4: Calculate Cost
Click on the “Calculate” button to generate the cost estimate. The calculator will process the input parameters and provide a detailed cost breakdown.
Step 5: Review and Adjust
Review the generated cost estimate and detailed breakdown. If necessary, adjust the input parameters to see how changes affect the cost. This flexibility allows you to explore different options and find the most cost-effective solution for your needs.
Step 6: Generate Report
Once you are satisfied with the cost estimate, use the calculator’s report generation feature to create a detailed report. This report can be saved, printed, or shared with stakeholders for further review and decision-making.
Using a conveyor belt cost per meter calculator simplifies the process of estimating conveyor belt costs and enhances budget planning. By understanding how the calculator works and following the step-by-step guide, businesses can ensure accurate cost estimates, make informed decisions, and optimize their investment in conveyor belt systems.

The Conveyor Cost Calculator: Your Budget Planning Tool for Conveyor Belt Cost Per Meter
Efficient budgeting is critical for the successful implementation of conveyor belt systems in industrial operations. The conveyor belt cost per meter is a fundamental metric that businesses must accurately calculate to avoid financial missteps. The conveyor cost calculator is an indispensable tool that simplifies this process, ensuring precise cost estimations and streamlined budget planning. This section delves into the features of the conveyor cost calculator and how it can enhance the budgeting process for conveyor belt installations.
Features of the Conveyor Cost Calculator
The conveyor cost calculator is equipped with several features designed to facilitate accurate and comprehensive cost estimations for conveyor belts. Here are some of the key features:
1. Customizable Input Parameters
The calculator allows users to input a variety of parameters specific to their needs, including:
- Material Type: Users can select from different materials such as rubber, PVC, or metal, each with its own cost implications.
- Belt Width and Length: Input the precise dimensions of the conveyor belt to ensure accurate cost calculations.
- Additional Features: Users can specify additional features like coatings, reinforcements, or custom designs that might affect the cost.
2. Real-Time Cost Calculation
One of the standout features of the conveyor cost calculator is its ability to provide real-time cost calculations. As users input or adjust parameters, the calculator instantly updates the cost per meter, allowing for dynamic budget adjustments and scenario planning.
3. Detailed Cost Breakdown
The calculator offers a detailed breakdown of costs, showing how each parameter contributes to the overall conveyor belt cost per meter. This transparency helps users understand where their money is going and identify potential areas for cost savings.
4. Comparison Functionality
Users can compare the costs of different conveyor belt configurations side by side. This feature is particularly useful for evaluating the cost-effectiveness of various materials, dimensions, and additional features, aiding in making informed decisions.
5. Report Generation
The conveyor cost calculator can generate comprehensive reports that include all input parameters, cost calculations, and breakdowns. These reports can be saved, printed, or shared with stakeholders, providing a clear and professional overview of budget estimates.
How It Can Streamline the Budgeting Process for Conveyor Belt Installations
The conveyor cost calculator is more than just a tool for estimating costs; it is a comprehensive solution that can streamline the entire budgeting process for conveyor belt installations. Here’s how:
1. Enhancing Accuracy
Manual calculations of conveyor belt cost per meter are prone to errors, especially when dealing with complex projects involving multiple variables. The conveyor cost calculator eliminates these errors by automating the calculation process, ensuring that the cost estimates are accurate and reliable.
2. Saving Time
Budget planning for conveyor belt installations can be time-consuming, especially when adjusting multiple parameters and comparing different options. The calculator speeds up this process by providing instant cost updates and comparisons, allowing users to quickly iterate and refine their budgets.
3. Facilitating Informed Decision-Making
With the detailed cost breakdown and comparison features, users can make informed decisions about their conveyor belt purchases. Understanding the cost implications of different materials, dimensions, and features enables users to choose the most cost-effective solutions that meet their operational requirements.
4. Improving Financial Planning
The ability to generate detailed reports enhances financial planning by providing clear and comprehensive documentation of cost estimates. These reports can be used to secure funding, justify expenditures, and plan for future investments in conveyor belt systems.
5. Enhancing Communication with Stakeholders
Clear and accurate budget estimates are crucial for effective communication with stakeholders. The reports generated by the conveyor cost calculator can be easily shared with project managers, financial officers, and other stakeholders, ensuring everyone is on the same page and facilitating smoother project approvals.
The conveyor cost calculator is an essential tool for any business involved in conveyor belt installations. By accurately calculating the conveyor belt cost per meter, providing real-time cost updates, and offering detailed cost breakdowns and comparisons, the calculator streamlines the budgeting process and enhances financial planning. Whether you are planning a new installation or evaluating existing systems, the conveyor cost calculator helps ensure that your budget estimates are accurate, informed, and aligned with your operational needs.
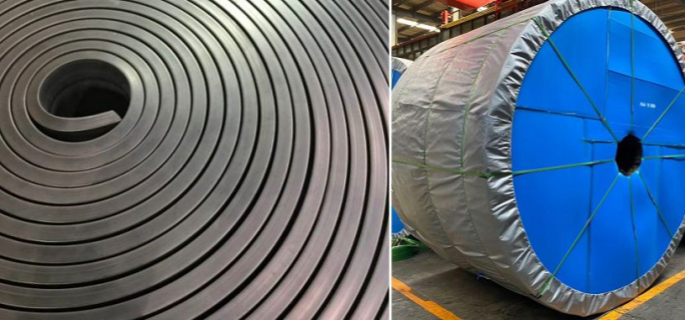
Conveyor Belt Cost Per Foot: Understanding the Difference in Conveyor Belt Cost Per Meter
When calculating the cost of conveyor belts, it’s important to understand the difference between cost per foot and cost per meter. While both measurements are used, the choice between them can impact budgeting, purchasing decisions, and cost estimations. This section explains the differences, highlights the importance of unit conversions, and provides examples to illustrate these concepts.
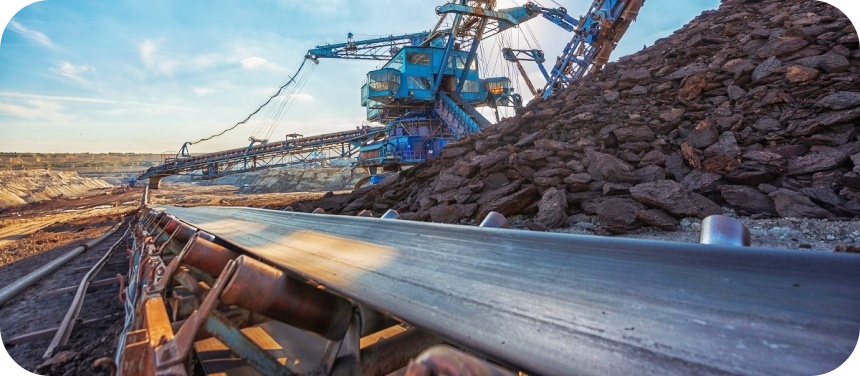
The Difference Between Cost Per Foot and Cost Per Meter
Understanding the cost metrics of conveyor belts is essential for businesses aiming to budget effectively and make informed purchasing decisions. Two common units of measurement used to price conveyor belts are meters and feet. This article explores the differences between conveyor belt cost per meter and conveyor belt cost per foot, helping you navigate pricing strategies and choose the best option for your needs.
Metric System vs. Imperial System
The primary difference between the cost per meter and the cost per foot lies in the measurement systems. The metric system uses meters, while the imperial system uses feet. Understanding these systems and how they convert is crucial for comparing prices and ensuring accurate budgeting.
- Meter: One meter is approximately 3.28084 feet.
- Foot: One foot is approximately 0.3048 meters.
Cost Conversion and Comparison
When comparing costs, it is essential to convert one unit to the other accurately. For example, if a conveyor belt costs $10 per meter, the equivalent cost per foot can be calculated by dividing the cost per meter by the number of feet in a meter (3.28084).
Example Calculation:
- Cost per meter: $10
- Cost per foot: $10 / 3.28084 ≈ $3.05
Similarly, if a conveyor belt costs $3 per foot, the equivalent cost per meter can be calculated by multiplying the cost per foot by the number of feet in a meter (3.28084).
Example Calculation:
- Cost per foot: $3
- Cost per meter: $3 x 3.28084 ≈ $9.84
Practical Implications
Understanding the cost differences between meters and feet is crucial for international transactions and comparisons. Different countries and industries may prefer one measurement system over the other, affecting how prices are quoted and understood.
- International Transactions: When purchasing conveyor belts from suppliers in different countries, being aware of the preferred measurement system helps avoid confusion and ensures accurate cost comparisons.
- Industry Standards: Some industries may predominantly use one measurement system. Knowing the standard in your industry can streamline procurement processes and improve communication with suppliers.
Cost Per Foot
The cost per foot measurement is commonly used in countries like the United States, where the imperial system is prevalent. This measurement reflects the price for each foot of the conveyor belt and is particularly useful for businesses accustomed to working in feet and inches. The cost per foot is calculated by dividing the total cost of the conveyor belt by its length in feet.
Cost Per Meter
Conversely, the cost per meter measurement is widely used in countries that follow the metric system. This measurement shows the price for each meter of the conveyor belt and is more suitable for businesses operating in regions where the metric system is standard. The cost per meter is determined by dividing the total cost of the conveyor belt by its length in meters.
Importance of Unit Conversions in Cost Estimations
Unit conversions are crucial when comparing costs and making budget estimations in different regions. Converting costs from feet to meters or vice versa ensures consistency and accuracy in financial planning. Here’s why unit conversions are important:
- Consistency in Budgeting: Using a consistent unit of measurement helps in creating accurate budgets and financial plans.
- Global Operations: For businesses operating internationally, understanding both measurements allows for easier comparison and decision-making.
- Supplier Communication: Clear communication with suppliers who may use different measurement systems ensures accurate quotes and orders.
- Avoiding Misunderstandings: Prevents costly misunderstandings and errors in procurement and installation.
- Regulatory Compliance: Ensures compliance with local regulations and standards which may specify certain measurement units.
Understanding the difference between cost per foot and cost per meter is essential for accurate budgeting and cost estimations. The conveyor belt cost per meter provides a standardized approach for regions using the metric system, while cost per foot is suitable for regions using the imperial system. Accurate unit conversions are crucial for businesses operating globally or dealing with suppliers and customers who use different measurement systems. By mastering these conversions, companies can ensure precise financial planning, avoid misunderstandings, and make informed purchasing decisions.
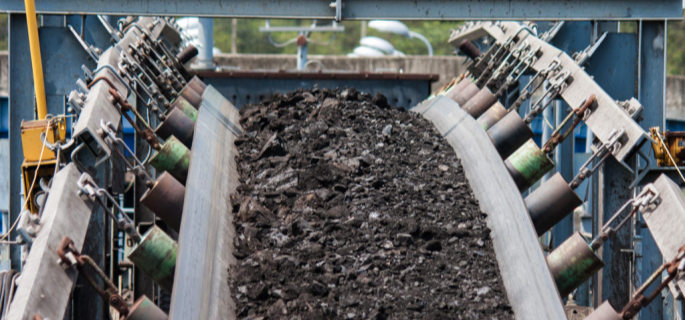
Factors Influencing How Much a Conveyor Belt Costs: Understanding Conveyor Belt Cost Per Meter
The conveyor belt cost per meter is a critical factor in budgeting for industrial operations. Various elements influence the overall cost, and understanding these can help businesses make informed decisions and optimize their investments.Conveyor Belt Cost Per Meter $ 50.00 – $150.00,depending on the type of material used, belt dimensions, construction, and additional features such as coatings or reinforcements. This section provides a detailed analysis of the factors affecting conveyor belt prices, including material, length, width, and application type, with illustrative examples.
Material Type
The material used to manufacture the conveyor belt significantly impacts its cost. Different materials offer varying levels of durability, flexibility, and suitability for specific applications. Here are some common materials and their cost implications:
Rubber Conveyor Belts
Rubber is a popular choice due to its durability and flexibility. It is suitable for heavy-duty applications such as mining and manufacturing. The cost per meter for rubber belts can be higher due to their robust nature and long lifespan.
- Cost Per Meter: $45 – $65
- Applications: Mining, construction, heavy manufacturing
- Advantages: High durability, resistance to abrasion
PVC Conveyor Belts
PVC belts are less expensive than rubber and are widely used in industries like food processing and packaging. They offer good chemical resistance but may not be as durable as rubber belts.
- Cost Per Meter: $20 – $40
- Applications: Food processing, packaging, light manufacturing
- Advantages: Chemical resistance, affordability
Metal Conveyor Belts
Metal belts, typically made from stainless steel, are used in high-temperature applications and heavy-duty industries. These belts are the most expensive due to their strength and resistance to extreme conditions.
- Cost Per Meter: $80 – $150
- Applications: High-temperature environments, heavy-duty industrial applications
- Advantages: High strength, heat resistance
Length of the Conveyor Belt
The length of the conveyor belt directly affects the total cost. Longer belts require more material, leading to higher overall costs. Additionally, the installation and maintenance costs can also increase with the length of the belt.
Impact of Length on Cost
Consider a rubber conveyor belt priced at $50 per meter. For a system requiring 100 meters of belt, the total material cost would be:
- Total Cost: 100 meters x $50 = $5,000
If the length increases to 200 meters, the cost would be:
- Total Cost: 200 meters x $50 = $10,000
This demonstrates how length directly impacts the budget.
Width of the Conveyor Belt
The width of the conveyor belt also plays a significant role in determining the cost. Wider belts require more material and additional conveyor belt structural support, which increases the cost per meter.
Application Type
The specific application of the conveyor belt influences its design and material requirements, thereby affecting the cost. Specialized applications may require belts with unique properties, such as resistance to chemicals, heat, or heavy loads.
Specialized Applications
- Chemical Industry: Belts used in chemical processing need to be resistant to corrosive substances. A specialized PVC belt with chemical-resistant properties might cost around $50 per meter.
- Food Industry: Conveyor belts in food processing must comply with hygiene standards and are often made from FDA-approved materials. A food-grade PVC belt might cost approximately $35 per meter.
- High-Temperature Applications: Metal belts used in high-temperature environments, such as furnaces or ovens, need to withstand extreme heat. A stainless steel belt might cost about $120 per meter.
- Anti-Static Properties: In industries where static electricity can pose a risk, such as electronics manufacturing, belts with anti-static properties are essential, adding to the cost.Hygienic Standards: Food processing and pharmaceutical industries require belts that meet stringent hygienic standards, often made from specialized materials that are easy to clean and resistant to contamination, leading to higher costs.
Several factors influence the conveyor belt cost per meter, including material type, length, width, and application type. Understanding these elements helps businesses accurately estimate costs and choose the most suitable and cost-effective conveyor belts for their needs. By considering the specific requirements of their operations and the different properties of conveyor belt materials, companies can optimize their investments and ensure efficient and reliable material handling systems.
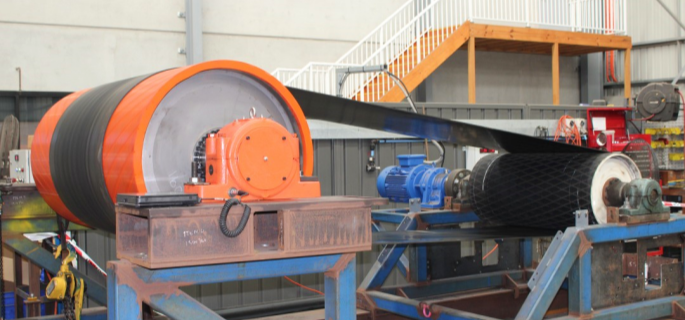
FAQs About Conveyor Belt Cost per Meter
The cost of conveyor belts varies significantly based on several factors, including material type, belt width, length, and any additional features. For instance, rubber conveyor belts typically range from $25 to $65 per meter, depending on their specifications and durability. PVC belts, often used in food processing and packaging, can cost between $15 and $40 per meter. Metal conveyor belts, which are used in high-temperature environments, are the most expensive, ranging from $80 to $150 per meter. When budgeting for conveyor belts, it’s essential to consider the specific needs of your operation, as specialized features like chemical resistance or heat tolerance can further impact the cost.
The installation cost of a conveyor belt depends on several factors, including the complexity of the installation, the length and width of the belt, and the type of conveyor system. On average, installation costs can range from $100 to $250 per meter. For a 100-meter conveyor belt, the installation could cost anywhere between $10,000 and $25,000. Additional factors that influence installation costs include the need for specialized equipment, the complexity of the conveyor layout, and labor costs in your region. It’s also important to factor in potential downtime during installation, which can impact overall operational costs.
The cost of a conveyor per foot can vary depending on the type and specifications of the conveyor. For example, a basic rubber conveyor belt might cost around $10 to $20 per foot, while a more specialized metal conveyor belt could cost upwards of $30 to $50 per foot. These prices reflect the base cost of the conveyor belt itself and do not include additional expenses such as installation, maintenance, or customization. When planning your budget, it’s important to consider the total cost of ownership, including these additional factors, to ensure an accurate and comprehensive financial plan.
Calculating the conveyor belt cost per meter involves several steps. First, determine the material type, as different materials have varying costs. Next, measure the required width and length of the conveyor belt. Multiply the length by the width to get the total area. Then, consider any additional features or customizations that might be necessary, such as heat resistance or chemical coatings. Add these costs to the base material cost. For example, if you need a 100-meter long, 1-meter wide rubber belt at $45 per meter, the base cost is $4,500. If additional features add $10 per meter, the total cost is $5,500. This method ensures an accurate estimate tailored to your specific requirements.
The cost of a conveyor belt system for mining varies significantly based on several factors such as material type, length, width, and customization. On average, conveyor belts range from $1,500 to $10,000 per meter. Heavy-duty belts, required for the harsh conditions of mining, generally fall on the higher end of this spectrum. Additionally, the total cost includes components like drives, rollers, and support structures, which can increase the overall expense. A complete conveyor belt system, including installation, can start from $100,000 and may reach several million dollars depending on the scale and complexity of the operation. Long-term costs such as maintenance, energy consumption, and component replacement also need to be considered for accurate budgeting.
The installation cost of a conveyor system depends on various factors including the system’s length, complexity, and the specific requirements of the mining site. Typically, installation costs can range from 20% to 50% of the equipment cost. For instance, if a conveyor belt system costs $500,000, the installation may add $100,000 to $250,000 to the total expense. This includes labor, equipment setup, and potential site modifications. Additionally, installation costs can be higher if the site requires significant preparation or if the system includes complex features such as steep inclines or automated controls. Proper installation is crucial for ensuring the system’s efficiency and longevity, making it a vital part of the overall investment.
Last Updated on June 28, 2024 by Jordan Smith
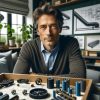
Jordan Smith, a seasoned professional with over 20 years of experience in the conveyor system industry. Jordan’s expertise lies in providing comprehensive solutions for conveyor rollers, belts, and accessories, catering to a wide range of industrial needs. From initial design and configuration to installation and meticulous troubleshooting, Jordan is adept at handling all aspects of conveyor system management. Whether you’re looking to upgrade your production line with efficient conveyor belts, require custom conveyor rollers for specific operations, or need expert advice on selecting the right conveyor accessories for your facility, Jordan is your reliable consultant. For any inquiries or assistance with conveyor system optimization, Jordan is available to share his wealth of knowledge and experience. Feel free to reach out at any time for professional guidance on all matters related to conveyor rollers, belts, and accessories.