Conveyor Belt Design Manual: Essential Techniques and Standards
The conveyor belt design manual serves as a comprehensive guide for professionals involved in conveyor system design and operations. The conveyor belt design manual exhibit conveyor belt construcyion, capacities, diameters, specifications, quality, considerations… It aims to provide in-depth insights into the design, installation, maintenance, and selection of conveyor belts, catering to engineers, technicians, and managers in various industries.In the conveyor belt design manual, detailed information is provided on fire safety tests essential for ensuring the reliability and safety of conveyor belts. These tests include the drum friction test, laboratory flame test, gallery fire test, and electrical resistance test. Each test method is meticulously explained, covering procedures, standards, and industry best practices.Within the conveyor belt design manual, significant attention is devoted to the evaluation of wear and tear in conveyor belts. Techniques for measuring thickness, assessing changes in profile, and early detection of damage are discussed in detail. Additionally, strategies for scheduling repairs and minimizing downtime are outlined to ensure uninterrupted conveyor operation.
Conveyor Belt Design Manual: Conveyor Belt Construcyion
Conveyor belts are critical components in material handling systems. They are used extensively in various industries, such as mining, manufacturing, and logistics, to transport bulk materials or discrete units over short or long distances. A well-designed conveyor belt ensures efficiency, safety, and longevity in operation.
Conveyor Belt Structure
The conveyor belt is composed of several layers, each serving a specific function. The typical structure of a conveyor belt includes the following layers:
- Top Cover Layer:
- Material: Often made of rubber, PVC, polyurethane, or other synthetic materials.
- Purpose: Protects the belt from wear and tear, environmental conditions, and the material being transported. It also provides a grip for the material.
- Thickness: Varies depending on the application, typically ranging from 1.5 mm to 15 mm.
- Carcass (Reinforcement Layer):
- Material: The carcass is usually made of fabric (e.g., polyester, nylon) or steel cords.
- Purpose: Provides tensile strength and flexibility. It determines the belt’s load-bearing capacity and elongation properties.
- Types:
- Fabric Carcass: Composed of multiple plies (layers), often referred to as EP (Polyester/Nylon) belts.
- Steel Cord Carcass: Contains steel cords that offer high tensile strength, ideal for long-distance and heavy-load applications.
- Bottom Cover Layer:
- Material: Similar to the top cover, usually made of rubber or other synthetic materials.
- Purpose: Protects the carcass from damage due to contact with conveyor idlers and pulleys.
- Thickness: Typically thinner than the top cover layer.
- Additional Layers:
- Breakers and Skim Coats: Sometimes added between the carcass and the covers to enhance adhesion and impact resistance.
- Sidewalls and Cleats: Optional components added to prevent spillage and facilitate the transportation of materials on inclined planes.
A well-designed conveyor belt system is essential for efficient material handling. By considering the structure, material properties, environmental conditions, and maintenance requirements, you can ensure a reliable and durable conveyor belt system. Proper design and regular maintenance are key to minimizing downtime and maximizing productivity.
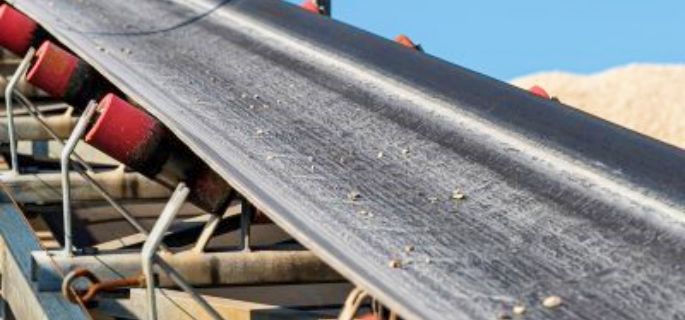
Conveyor Belt Design Manual: Belt Capacities
The capacity of a conveyor belt is a critical factor in the design and operation of conveyor systems. Belt capacity determines the volume of material that can be transported per unit of time and directly influences the efficiency and performance of the conveyor system. Understanding the factors that affect belt capacity is essential for designing an optimal conveyor system.
Key Factors Affecting Belt Capacity
Belt capacity is influenced by several factors, including:
- Belt Width
- The width of the conveyor belt is one of the primary determinants of its capacity. Wider belts can carry more material, as they provide a larger surface area. Standard belt widths range from 300 mm to 2000 mm, but custom widths are also available for specific applications.
- Belt Speed
- Belt speed is the rate at which the belt moves, usually measured in meters per second (m/s). Higher speeds increase the material flow rate, thereby increasing the capacity. However, speed must be balanced with other factors such as material handling and wear.
- Material Characteristics
- The type of material being transported affects capacity. Material characteristics like bulk density, particle size, and flowability must be considered. Denser materials occupy less volume for the same mass, increasing capacity, while fine materials may require slower belt speeds to prevent spillage.
- Inclination Angle
- The angle of inclination of the conveyor affects the belt’s capacity. As the angle increases, the effective capacity decreases due to the material’s tendency to slide back down the belt. This necessitates the use of special belts, like cleated or sidewall belts, to maintain capacity on steep inclines.
- Load Profile
- The cross-sectional shape of the material load on the belt influences capacity. A uniform, well-distributed load maximizes the use of the belt’s width, enhancing capacity.
Calculating Belt Capacity
The belt capacity can be calculated using the following formula:
[{Belt Capacity (C)} = A × V × \rho × 3600]
Where:
- C = Capacity in tons per hour (tph)
- A = Cross-sectional area of the material on the belt (m²)
- V = Belt speed (m/s)
- ρ = Material bulk density (kg/m³)
- 3600 = Conversion factor to convert seconds to hours
Cross-Sectional Area (A)
The cross-sectional area of the material on the belt is determined by the belt width, the surcharge angle (which depends on the material’s properties), and the depth of the material on the belt. For a flat belt, the cross-sectional area can be calculated as:
[A = \frac{W × h}÷{2}]
Where:
- W = Belt width (m)
- h = Height of the material on the belt (m)
For a troughed belt, which is more common, the cross-sectional area is influenced by the troughing angle and can be estimated using more complex geometric formulas depending on the shape of the load.
Belt Speed (V)
Belt speed is typically specified by the design requirements and operational considerations. Standard conveyor belt speeds range from 0.5 m/s to 5 m/s, depending on the application.
Material Bulk Density (ρ)
The bulk density of the material, measured in kilograms per cubic meter (kg/m³), varies depending on the type of material. For instance, coal may have a bulk density of 800 kg/m³, while iron ore could have a bulk density of 2500 kg/m³.
Practical Considerations
When determining belt capacity, several practical considerations must be addressed:
- Loading and Unloading Points
- Ensuring that the belt is loaded evenly and at the correct rate to match the belt’s capacity is essential. Similarly, the unloading mechanisms must be capable of handling the material flow without causing blockages or spillage.
- Belt Tension
- Proper tensioning is necessary to prevent slippage, which can reduce effective capacity. Over-tensioning can cause excessive wear and reduce the belt’s lifespan.
- Material Flow Characteristics
- Materials with poor flowability or cohesive materials may require special belt designs or handling techniques to ensure consistent capacity.
Understanding and calculating belt capacities is crucial in designing an efficient conveyor system. By considering factors such as belt width, speed, material characteristics, and incline, engineers can design systems that meet the specific needs of their operations. Proper capacity calculation ensures the conveyor system can handle the expected material flow, contributing to smooth, efficient, and safe operation.
Conveyor Belt Design Manual: Diameters
The diameter of conveyor belt components, particularly pulleys, plays a critical role in the overall performance and longevity of a conveyor system. The diameters influence the belt tension, the amount of flexing the belt undergoes, and the power required to drive the conveyor. Proper selection of pulley diameters is essential to avoid excessive belt wear and operational inefficiencies.
Key Diameter Components in Conveyor Systems
There are several diameter-related components in a conveyor system that need to be considered during the design process:
- Drive Pulley Diameter
- Tail Pulley Diameter
- Snub Pulley Diameter
- Bend Pulley Diameter
- Idler Roller Diameter
Drive Pulley Diameter
The drive pulley is responsible for transmitting the motor’s power to the conveyor belt. It needs to be carefully sized to provide the necessary torque while minimizing belt stress.
Diameter Selection
The diameter of the drive pulley is typically the largest in the system. The minimum drive pulley diameter is determined by the belt’s construction (e.g., fabric or steel cord) and the belt’s tension rating. A larger diameter reduces the bending stress on the belt, thereby prolonging its life.
- For Fabric Belts: The minimum pulley diameter is typically 200-500 mm, depending on the belt’s tensile strength and thickness.
- For Steel Cord Belts: The minimum pulley diameter is often larger, ranging from 400 mm to over 1000 mm, due to the lower flexibility of steel cords.
Pulley Face Width
The face width of the drive pulley should be slightly wider than the belt width to ensure full contact and proper belt tracking. The width typically exceeds the belt width by 25-50 mm on each side.
Tail Pulley Diameter
The tail pulley is located at the opposite end of the conveyor and helps in redirecting the belt back to the drive pulley. It often serves as the take-up pulley in tensioning systems.
Diameter Selection
The diameter of the tail pulley should be similar to or slightly smaller than the drive pulley diameter. However, it must still adhere to the minimum diameter guidelines to prevent undue stress on the belt.
- Fabric Belts: Similar guidelines as for drive pulleys, typically around 200-500 mm.
- Steel Cord Belts: Often around 400 mm or more.
Alignment Considerations
The tail pulley must be precisely aligned to ensure proper belt tracking and to prevent belt edge damage.
Snub Pulley Diameter
Snub pulleys are used to increase the belt wrap angle around the drive pulley, enhancing the friction and grip between the belt and the drive pulley.
Diameter Selection
Snub pulleys are generally smaller in diameter compared to drive and tail pulleys. However, the diameter should not be too small to avoid excessive belt bending and stress.
- Fabric Belts: Typical diameters range from 150 mm to 350 mm.
- Steel Cord Belts: Diameters often range from 250 mm to 500 mm.
Placement
Proper placement of the snub pulley is crucial for optimizing belt tension and minimizing wear.
Bend Pulley Diameter
Bend pulleys are used to change the direction of the belt in the conveyor system. They are often employed in systems with complex routing or multiple belt transitions.
Diameter Selection
Bend pulleys typically have diameters similar to or slightly smaller than those of snub pulleys.
- Fabric Belts: Diameters range from 150 mm to 350 mm.
- Steel Cord Belts: Diameters range from 250 mm to 500 mm.
Multiple Bend Pulleys
In systems with multiple bend pulleys, consistent diameters are preferred to maintain uniform belt tension and tracking.
Idler Roller Diameter
Idler rollers support the conveyor belt along its length, preventing sagging and maintaining the belt’s alignment. They do not drive the belt but are critical in maintaining the belt’s shape and reducing friction.
Diameter Selection
The diameter of idler rollers is smaller compared to pulleys, and they are chosen based on the belt width, load, and speed.
- Standard Diameters: Range from 89 mm to 219 mm, with larger diameters used for heavier loads and wider belts.
Spacing Considerations
The spacing of idler rollers should be carefully calculated to ensure the belt does not sag between rollers, which could affect the material handling efficiency.
Calculating Pulley Diameters
The calculation of pulley diameters involves considering the following factors:
- Belt Type and Construction
- Belt Speed
- Load Requirements
- Belt Tension and Wrap Angle
- Operational Environment
For a specific application, pulley diameter can be calculated using empirical formulas provided by belt manufacturers or industry standards, which take into account the belt’s tension rating and construction type.
Practical Considerations
- Belt Flexibility: A smaller pulley diameter increases the frequency of flexing, leading to potential fatigue and shorter belt life. Therefore, always adhere to the minimum recommended pulley diameters.
- Pulley Surface: The surface of the pulleys should be smooth and properly aligned to prevent belt slippage and wear.
- Environmental Factors: Consider the operating environment, such as temperature and humidity, as these can affect the belt material’s flexibility and the pulley’s performance.
Proper selection of pulley and roller diameters is essential for the efficient and reliable operation of a conveyor belt system. By considering factors such as belt type, load, and speed, and by adhering to the recommended minimum diameters, designers can ensure that the conveyor system operates smoothly, with minimal wear and maximum efficiency.
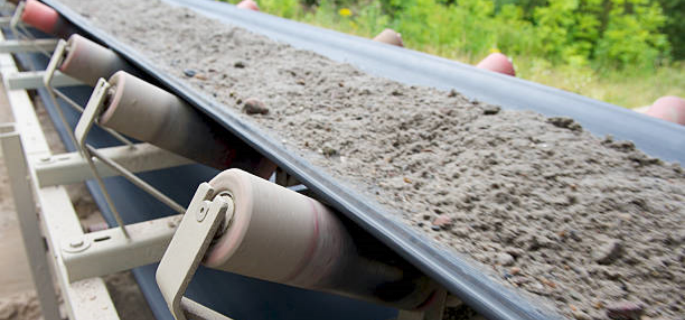
Conveyor Belt Design Manual: Specifications and Quality
Designing a conveyor belt involves several key specifications and quality parameters that must be met to ensure efficient, safe, and long-lasting operation. Here’s an overview of the main considerations:
Specifications
a. Belt Width and Length:
- Width: Determined by the load and type of material being conveyed. Common widths range from 300 mm to 2400 mm.
- Length: Depends on the layout of the conveyor system and the distance the materials need to travel.
b. Belt Material:
- Rubber: Commonly used due to its durability and flexibility.
- PVC: Used in food processing and packaging.
- PU (Polyurethane): Offers high resistance to oil, fat, and chemicals.
- Steel Cord: Used for heavy-duty applications requiring high tensile strength.
c. Belt Strength:
- Measured in terms of tensile strength (N/mm). It is critical for determining the load-carrying capacity.
- Rating: Common ratings are EP (polyester/nylon) belts, with strengths ranging from 200 N/mm to 3150 N/mm.
d. Belt Speed:
- Typically measured in meters per second (m/s).
- Should match the operational requirements to ensure efficient material handling without causing spillage or damage.
e. Tension:
- Operational Tension: The force required to move the belt and the load.
- Breaking Tension: The maximum tension the belt can withstand before breaking.
f. Belt Thickness:
- Depends on the type of material being handled and the required durability.
- Thicker belts are used for heavy-duty applications.
g. Pulley Specifications:
- Diameter: Should be compatible with the belt design to prevent excessive wear.
- Lagging: Improves grip between the belt and pulley, reducing slippage.
h. Idlers and Rollers:
- The arrangement and spacing of idlers affect the belt’s load distribution and wear.
- Rollers should be designed to support the belt and load without causing deformation.
Quality Considerations:
a. Material Quality:
- Belts should be made from high-quality materials that resist wear, corrosion, and degradation from environmental factors.
- Testing: Should include tensile strength, elongation, and abrasion resistance.
b. Manufacturing Standards:
- The manufacturing process should adhere to relevant industry standards, such as ISO 9001.
- Consistency: The belt should maintain consistent thickness, width, and quality throughout its length.
c. Durability and Lifespan:
- A high-quality belt should have a long service life with minimal maintenance.
- Wear Resistance: Should be high to reduce the frequency of replacements.
d. Safety Standards:
- Conveyor belts should comply with safety standards, such as fire resistance, to prevent accidents in hazardous environments.
- Certification: Look for certifications such as ISO 340 (flame retardant) and ISO 284 (antistatic).
e. Surface Finish:
- The surface of the belt should be smooth to ensure efficient material transport and reduce wear.
f. Edge Quality:
- Belt edges should be straight and properly sealed to prevent fraying and damage.
g. Quality Control:
- Each belt should undergo rigorous quality checks, including visual inspections, dimensional checks, and load testing.
By adhering to these specifications and quality standards, a conveyor belt can be designed to meet the specific needs of various industries, ensuring reliability, safety, and efficiency in material handling operations.
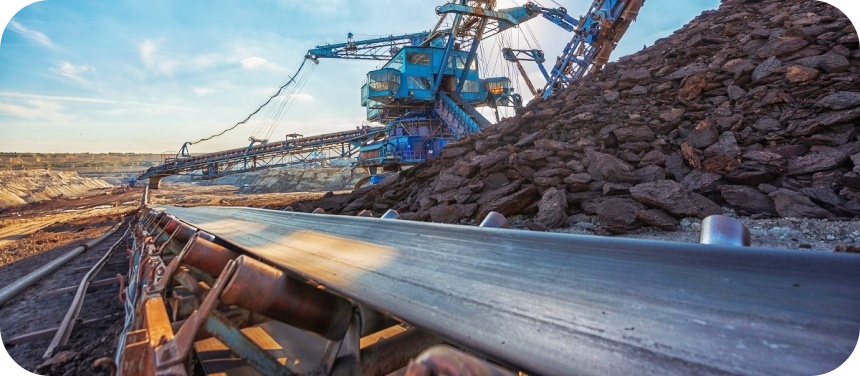
Conveyor Belt Design Manual: In-depth Analysis and Calculations
Belt Tension Calculation Example and Material Characteristics
In the conveyor belt design manual, a step-by-step example of belt tension calculation is provided to assist engineers and technicians in accurately determining the tension requirements for conveyor belt systems. This example illustrates the calculation process using relevant material characteristics such as belt width, carcass type, and load factors. Additionally, comprehensive tables detailing material properties such as tensile strength, elongation at break, and modulus of elasticity are included to facilitate accurate tension calculations for various conveyor applications.
Conveyor Capacity Determination and Friction Factors
Within the conveyor belt design manual, detailed methodologies for determining conveyor capacity and friction factors are outlined to ensure optimal system performance. Engineers can refer to tables and equations provided in the manual to calculate conveyor capacity based on factors such as belt speed, material density, and troughing angle. Friction factors, including belt-to-pulley friction and material-to-belt friction, are quantified to accurately assess power requirements and operational efficiency.
Selection Tables for Tension, Pulley Diameters, and Belt Plies
The conveyor belt design manual offers comprehensive selection tables to aid engineers in choosing the appropriate conveyor belt components for their specific applications. Tables detailing recommended tension values based on belt type, pulley diameters, and belt plies are provided to ensure safe and efficient conveyor operation. Engineers can utilize these tables to select the optimal combination of belt type, carcass construction, and cover material to meet the unique demands of their material handling systems.
Rate of Wear Graph and Belt Modulus Calculations
In the conveyor belt design manual, engineers will find detailed information on predicting belt wear and calculating belt modulus to assess belt performance and durability. A rate of wear graph is included to illustrate the expected wear patterns of different conveyor belt materials under various operating conditions. Additionally, equations and calculation methods for determining belt modulus, which influences belt elasticity and load distribution, are provided to aid in optimizing conveyor system design and maintenance practices.
Conveyor Belt Design Manual: Understanding the Basics of Conveyor Systems
Overview of Material Handling Systems and Objectives
In the conveyor belt design manual, an overview of material handling systems and their objectives is provided to contextualize the role of conveyor systems in industrial settings. Material handling systems are essential for facilitating the movement of goods, raw materials, or products through various stages of production or distribution. The primary objectives of material handling systems include quick and precise load pick-up, efficient transfer, safe transport, accuracy, automation, cost-effectiveness, maintenance simplicity, and safe operation.
Classification of Material Handling Systems
Within the conveyor belt design manual, material handling systems are classified into three main groups based on their design and operational characteristics. These groups include hoisting equipment, conveying equipment, and surface and overhead equipment. Hoisting equipment encompasses devices such as jacks, winches, pulley blocks, cranes, and elevators, used for vertical movement of materials. Conveying equipment includes belt conveyors, chain conveyors, screw conveyors, and apron conveyors, designed for horizontal or inclined transport of materials. Surface and overhead equipment consist of forklifts, trucks, railway cars, and overhead monorails, used for surface-level or overhead transport within facilities.
Introduction to Belt Conveyors
The conveyor belt design manual offers a comprehensive introduction to belt conveyors, highlighting their significance, components, advantages, layouts, loading/discharge methods, and major equipment requirements. Belt conveyors are defined as systems designed to transport materials, goods, or people using a loop of flexible material between rollers, actuated by an electrical motor. The components of a belt conveyor include the head pulley, tail pulley, idler rollers, conveyor belt, and conveyor frame. Belt conveyors offer numerous advantages such as operational flexibility over long distances, high load capacity, quiet operation, simple maintenance, reliability, environmental friendliness, and low labor/energy requirements. Various loading and discharge methods, including hopper-based loading and head and discharge methods, are utilized based on specific material handling requirements. Major equipment requirements for belt conveyors include conveyor belts, pulleys, idlers, drive units, electric motors, and cleaning devices.
Maintenance and Safety Practices
The conveyor belt design manual emphasizes the importance of regular maintenance procedures and safety protocols to ensure the reliable and safe operation of conveyor systems. Regular maintenance procedures include inspections, cleaning, lubrication, and belt tension adjustment. Safety protocols encompass guarding, emergency stop systems, lockout/tagout procedures, and personnel training. Preventive maintenance strategies, such as predictive maintenance techniques and emergency response planning, are essential for minimizing downtime and preventing accidents or equipment failures. Regular training drills and simulations are conducted to ensure that personnel are adequately prepared to respond to emergency situations promptly and effectively. Collaboration with local emergency services and first responders is essential to coordinate emergency response efforts and mitigate the impact of conveyor-related incidents.
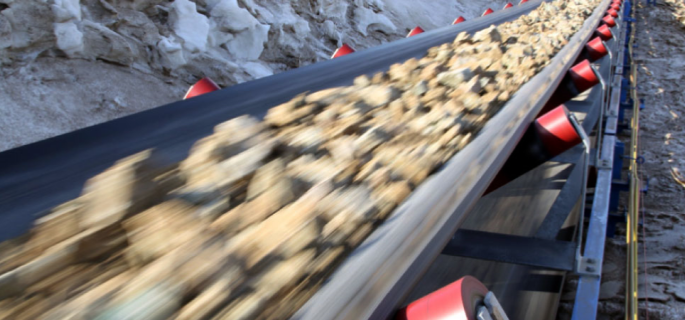
Conveyor Belt Design Manual: Enhancing Efficiency with Conveyor Design Software
Main Software Offerings: Features and Capabilities
In the conveyor belt design manual, a detailed exploration of conveyor design software is provided, focusing on the features and capabilities of prominent offerings such as Belt Analyst with Dynamic Analyst and Bulk Flow Analyst software. Belt Analyst with Dynamic Analyst is highlighted as the world’s most popular engineering software tool for belt conveyor design and analysis. It offers a wide range of features, including:
- Dynamic analysis capabilities for simulating complex conveyor behaviors.
- Intuitive interface for easy model creation and manipulation.
- Extensive library of conveyor components and material properties.
- Advanced optimization tools for improving conveyor performance and efficiency.
- Comprehensive reporting and visualization options for presenting analysis results.
Bulk Flow Analyst utilizes the Discrete Element Method (DEM) to simulate bulk material flow in conveyor systems. Key features and capabilities of Bulk Flow Analyst include:
Get personalized support for your conveyor belt requirements by filling out this form.
- Accurate simulation of material flow dynamics, particle interactions, and conveyor performance.
- Customizable material properties and loading conditions for realistic simulations.
- Visualization tools for analyzing material flow patterns, particle trajectories, and system behavior.
- Integration with other engineering software tools for seamless workflow integration.
Additional Resources and Services: Training Programs, Support Services, and Testimonials
The conveyor belt design manual also provides information on additional resources and services offered by conveyor design software providers. These include:
- Training programs: Comprehensive training sessions are available to help users master the features and functionalities of conveyor design software. Training courses cover topics such as model creation, analysis techniques, and best practices for conveyor design.
- Support services: Dedicated support teams are available to assist users with technical issues, software updates, and troubleshooting. Support services may include phone support, email support, online forums, and knowledge bases.
- Testimonials: Customer testimonials and case studies are showcased to highlight the success stories of users who have benefited from using conveyor design software. These testimonials provide insights into the real-world applications and advantages of using conveyor design software for optimizing conveyor systems.
Conveyor Belt Design Manual: Conveyor Considerations
When selecting a conveyor belt for your operations, several critical considerations should be taken into account to ensure the belt meets your specific needs and enhances operational efficiency. Here are the primary factors:
Material to be Conveyed
- Type of Material: The nature of the material (e.g., bulk, unit, granular, sticky) affects the belt choice. For example, sticky materials may require belts with specific surface properties to prevent sticking.
- Material Characteristics: Consider the weight, size, abrasiveness, temperature, and chemical properties of the materials.
- Volume: The volume or load capacity determines the belt width and strength requirements.
Operating Environment
- Temperature: The operating temperature can affect the belt’s material choice. High temperatures may require belts made of heat-resistant materials, while cold environments may require materials that remain flexible at low temperatures.
- Chemical Exposure: If the belt will be exposed to chemicals, choose a material that is resistant to those chemicals.
- Humidity and Moisture: In environments with high humidity or exposure to water, consider belts that are resistant to moisture and corrosion.
- Outdoor vs. Indoor Use: Outdoor use might require UV-resistant belts or those that can withstand harsh weather conditions.
Belt Type and Construction
- Material: Conveyor belts can be made from various materials like rubber, PVC, polyurethane, and metal. The choice depends on the application.
- Belt Strength: The belt’s tensile strength must be sufficient to handle the load and operational demands.
- Flexibility: The belt must be flexible enough to move over pulleys and rollers without excessive wear or failure.
- Belt Speed: The operating speed of the belt should be considered, as it influences the type of material used and the construction of the belt.
- Load Support: The belt should be capable of supporting the load without sagging or stretching excessively.
Maintenance and Durability
- Wear Resistance: Choose a belt that is resistant to wear and tear, especially if it’s handling abrasive materials.
- Ease of Maintenance: Consider belts that are easy to clean, repair, or replace. Modular belts, for example, can be more easily repaired than solid belts.
- Durability: The belt should have a long operational life, reducing the frequency of replacements and associated downtime.
System Design
- Belt Tracking: Proper tracking is essential to prevent misalignment and extend belt life. Consider belts with good tracking characteristics.
- Belt Tension: Ensure that the tensioning system is appropriate for the type of belt and application to prevent slippage and excessive wear.
- Pulley and Roller Compatibility: The belt must be compatible with the pulleys and rollers in the conveyor system, considering factors like diameter, alignment, and material.
Safety
- Fire Resistance: In certain industries, such as mining, fire-resistant belts are crucial to prevent accidents.
- Hygiene: In food processing, pharmaceutical, and other hygienic applications, consider belts that meet FDA or other relevant standards for cleanliness and safety.
- Static Conductivity: In environments where static electricity is a concern, such as in electronics manufacturing, antistatic belts are necessary.
Cost Considerations
- Initial Cost vs. Total Cost of Ownership: While lower-cost belts might be appealing initially, it’s important to consider the long-term costs, including maintenance, downtime, and replacement frequency.
- Energy Efficiency: Belts that reduce energy consumption can lead to significant savings over time.
Custom Requirements
- If your application has unique requirements, such as specific belt patterns, textures, or coatings, custom belts might be necessary.
Choosing the right conveyor belt is essential for optimizing operational efficiency, reducing downtime, and maintaining safety in your manufacturing processes.
Conveyor Belt Design Manual: Selecting The Proper Conveyor Belt
Selecting the proper conveyor belt for your application is crucial for ensuring optimal performance, longevity, and efficiency in your operations. Here’s a step-by-step guide to help you make the right choice:
1. Understand Your Application
- Material Type: Identify the type of material you will be conveying (e.g., bulk solids, food products, heavy-duty materials). Understanding the characteristics such as size, weight, abrasiveness, and temperature of the material is essential.
- Material Behavior: Consider how the material behaves. Is it sticky, oily, abrasive, or prone to generating static? These properties will influence the choice of belt material and surface treatment.
2. Determine the Operating Environment
- Temperature Range: Consider the ambient and material temperatures. High temperatures may require heat-resistant belts, while cold environments need belts that remain flexible.
- Chemical Exposure: If the belt will be exposed to chemicals (e.g., in food processing, chemical industries), select a material that is resistant to those chemicals.
- Moisture and Humidity: In wet environments, choose belts that are moisture-resistant and prevent slippage.
3. Select the Right Belt Material
- Rubber: Offers excellent durability and is ideal for handling heavy loads and abrasive materials.
- PVC: Suitable for general-purpose applications and offers resistance to chemicals and moisture.
- Polyurethane: Provides excellent wear resistance and flexibility, ideal for applications requiring high precision.
- Metal: Best for high-temperature environments or when strength and rigidity are required.
- Fabric: Lightweight and flexible, suitable for light to medium-duty applications.
4. Consider the Conveyor Design
- Belt Width: Determine the appropriate width based on the size and volume of material to be transported.
- Belt Speed: The speed at which the conveyor belt will operate influences the material selection and construction of the belt. High-speed applications may require special considerations to prevent wear.
- Load Capacity: Ensure the belt can handle the maximum load without excessive stretching or sagging.
- Incline or Decline: If the conveyor operates on an incline or decline, consider belts with special surface textures or cleats to prevent slippage.
5. Evaluate Belt Construction
- Single-Ply or Multi-Ply: Multi-ply belts offer increased strength and durability, while single-ply belts are lighter and more flexible.
- Patterned Surface: For applications requiring grip or where slippage is a concern, belts with patterned surfaces, such as rough top or diamond-shaped, may be necessary.
- Coating: Special coatings (e.g., Teflon, silicone) can enhance belt properties like heat resistance, non-stick surfaces, or improved durability.
6. Assess Maintenance and Durability
- Wear Resistance: Choose a belt with high wear resistance for applications with abrasive materials to minimize maintenance needs.
- Ease of Maintenance: Consider belts that are easy to clean, repair, or replace. Modular belts can offer ease of maintenance due to their replaceable sections.
- Expected Lifespan: Opt for belts with a long operational life to reduce the frequency of replacements and associated downtime.
7. Safety and Compliance
- Fire Resistance: In certain environments, such as mining, fire-resistant belts are essential for safety.
- Hygienic Requirements: In industries like food processing, select belts that comply with hygiene standards, such as FDA or EU food-grade certifications.
- Static Conductivity: In environments where static electricity is a concern, such as electronics manufacturing, antistatic belts are necessary.
8. Cost vs. Performance
- Initial Cost: While the upfront cost is important, consider the total cost of ownership, including maintenance, energy consumption, and belt lifespan.
- Energy Efficiency: Belts that reduce energy consumption can provide significant cost savings over time.
9. Custom Requirements
- If your application has specific requirements such as unique belt patterns, textures, or special coatings, consider custom-made belts to meet these needs.
10. Consult with Experts
- Working with a reputable conveyor belt supplier or manufacturer can help ensure that you choose the most appropriate belt for your specific application. They can offer valuable insights and recommendations based on their expertise.
Selecting the proper conveyor belt involves a thorough understanding of your operational needs, the materials being handled, and the environment in which the belt will operate. By carefully considering these factors, you can choose a conveyor belt that will enhance efficiency, reduce downtime, and contribute to the overall success of your operations.
Conveyor Belt Design Manual: Installation, Trouble Shooting & Tracking
Proper installation, troubleshooting, and tracking of conveyor belts are essential for ensuring optimal performance, longevity, and minimizing downtime in your operations. Here’s a guide on how to handle these aspects effectively:
Conveyor Belt Installation
A. Preparation
- Inspection: Before installation, inspect all components, including the conveyor structure, rollers, pulleys, and the belt itself, for any damage or irregularities.
- Cleanliness: Ensure the conveyor frame, pulleys, and rollers are clean and free of debris, oil, or grease that could affect the belt’s performance.
- Check Alignment: Verify that the conveyor structure is square and level. Misalignment can cause tracking issues and reduce the belt’s lifespan.
B. Belt Installation Process
- Positioning: Place the belt on the conveyor system. Make sure it is centered on the frame and aligned with the pulleys and rollers.
- Pulling the Belt: Use a belt puller or come-along to draw the belt over the pulleys. Ensure the belt is handled carefully to avoid kinks, twists, or sharp bends.
- Tensioning: Apply initial tension to the belt. Proper tension is crucial to prevent slippage while ensuring the belt can run smoothly over the pulleys. Over-tensioning can lead to excessive wear, while under-tensioning can cause slippage.
- Splicing (if required): If the belt is supplied in multiple sections, you may need to splice them together. Follow the manufacturer’s guidelines for splicing to ensure a strong and smooth joint.
- Run-In: After installation, run the belt for a few cycles without load to check for proper operation and make necessary adjustments.
Troubleshooting Conveyor Belt Issues
A. Common Issues and Solutions
- Belt Slippage:
- Cause: Insufficient tension, improper drive pulley lagging, or belt overloading.
- Solution: Increase belt tension, check and possibly replace the pulley lagging, and ensure the belt is not overloaded.
- Mistracking:
- Cause: Misaligned pulleys, damaged rollers, or uneven loading.
- Solution: Realign pulleys, replace damaged rollers, and ensure even loading.
- Belt Wear or Damage:
- Cause: Abrasive materials, sharp objects, or improper installation.
- Solution: Inspect and remove sharp objects, use wear-resistant belts, and ensure proper installation.
- Noise and Vibration:
- Cause: Misaligned components, worn rollers, or improper tension.
- Solution: Align components properly, replace worn rollers, and adjust tension.
- Material Spillage:
- Cause: Incorrect belt speed, improper skirt boards, or belt misalignment.
- Solution: Adjust the belt speed, install or adjust skirt boards, and ensure proper belt tracking.
- Belt Overheating:
- Cause: Excessive friction due to misalignment, over-tensioning, or inappropriate belt material for the application.
- Solution: Realign the belt, adjust tension, or switch to a more heat-resistant belt material.
Conveyor Belt Tracking
Proper tracking is crucial for the efficient operation of the conveyor belt. Misaligned belts can lead to uneven wear, increased energy consumption, and potential system failures.
A. Steps to Ensure Proper Tracking
- Initial Setup:
- Align the Conveyor Frame: Ensure the frame is level and square. This provides a solid foundation for proper tracking.
- Center the Belt: Start by centering the belt on the conveyor structure before applying tension.
- Check the Pulleys:
- Adjusting the Tail Pulley: The tail pulley can be adjusted to center the belt. Moving the pulley away from the belt’s running direction will cause the belt to move towards that side.
- Snub Pulleys and Return Idlers: Use snub pulleys and adjustable return idlers to fine-tune the belt’s path and help with tracking.
- Running the Belt:
- Observe During Operation: Run the conveyor and observe the belt’s tracking. Make gradual adjustments rather than large ones to avoid overcorrecting.
- Adjust Based on Observation: If the belt moves off-center, adjust the pulleys or idlers slightly until the belt tracks properly.
B. Tracking Adjustments
- Start at the Head Pulley: Begin tracking adjustments at the head (drive) pulley, which typically exerts the most influence on belt tracking.
- Work Backwards: Adjust the tail pulley, followed by any additional snub pulleys and return idlers as necessary.
- Make Incremental Adjustments: Always make small adjustments, allowing time for the belt to react before making further changes.
C. Preventative Measures for Tracking
- Regular Inspections: Conduct regular inspections to catch any misalignment or wear that could lead to tracking issues.
- Training the Belt: If the belt continues to mistrack, it may need to be retrained by adjusting the tension and alignment over several cycles.
- Maintenance: Ensure that all conveyor components are in good condition and properly maintained to prevent tracking issues.
Proper installation, diligent troubleshooting, and precise tracking are key to maintaining the efficiency and longevity of your conveyor belt system. Regular inspections and timely maintenance will help prevent issues, reduce downtime, and extend the life of your conveyor belts. If persistent issues arise, consulting with a conveyor belt specialist or the manufacturer may be necessary to identify and resolve underlying problems.
Get personalized support for your conveyor belt requirements by filling out this form.
FAQs about Conveyor Belt Design Manual
Designing a conveyor belt involves several key steps to ensure optimal performance and efficiency. Firstly, gather information on the material to be conveyed, including its size, weight, and handling requirements. Next, determine the conveyor’s layout, considering factors such as space constraints, material flow direction, and loading/unloading points. Select appropriate conveyor components, including belt type, pulleys, idlers, and drive systems, based on the application requirements and operating conditions. Finally, use specialized software tools or manual calculations to validate the conveyor design, ensuring proper belt tension, load capacity, and safety factors are met.
Calculating conveyor belt specifications involves determining key parameters such as belt tension, belt speed, material density, and conveyor length. To calculate belt tension, consider factors such as the weight of the material being conveyed, the angle of incline/decline, and frictional forces. Belt speed is typically determined based on the desired throughput rate and material handling requirements. Material density is crucial for determining load capacity and belt selection. Conveyor length is calculated based on the layout and configuration of the conveyor system. Utilize specialized equations or conveyor design software to perform these calculations accurately.
A conveyor belt PDF is a document that provides comprehensive information on conveyor belt systems, including their design, operation, maintenance, and safety considerations. It typically includes detailed descriptions of conveyor components, material handling applications, and best practices for conveyor system design and operation. A conveyor belt PDF may also contain technical specifications, installation guidelines, and troubleshooting tips to assist engineers, technicians, and operators in effectively managing conveyor systems.
Several software options are available for belt conveyor design, each offering unique features and capabilities to meet various engineering needs. Some popular choices include Belt Analyst with Dynamic Analyst and Bulk Flow Analyst software. These software packages provide advanced tools for modeling, analyzing, and optimizing conveyor systems, including dynamic simulations, material flow analysis, and optimization algorithms. Additionally, they offer extensive libraries of conveyor components, material properties, and industry-standard calculation methods to ensure accurate and efficient conveyor design. Ultimately, the best software for belt conveyor design depends on the specific requirements and preferences of the user.
When designing a conveyor belt, it’s essential to consider the material characteristics, such as bulk density and abrasiveness, to choose the right belt type. Load capacity and belt speed determine the belt’s width and strength. Environmental factors, including temperature and chemical exposure, influence material selection. Proper belt tension and alignment are crucial to prevent slippage and wear. Additionally, design for easy maintenance and incorporate safety features like emergency stops. Energy efficiency is also important, using efficient motors and low-friction materials to reduce operational costs.
To size a conveyor belt, first determine the material flow rate and calculate the required belt speed. Choose the appropriate belt width based on load capacity and material size. Then, calculate the necessary belt strength and power requirements. Always include a safety margin and ensure compatibility with existing systems for optimal performance.
Last Updated on August 22, 2024 by Jordan Smith
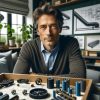
Jordan Smith, a seasoned professional with over 20 years of experience in the conveyor system industry. Jordan’s expertise lies in providing comprehensive solutions for conveyor rollers, belts, and accessories, catering to a wide range of industrial needs. From initial design and configuration to installation and meticulous troubleshooting, Jordan is adept at handling all aspects of conveyor system management. Whether you’re looking to upgrade your production line with efficient conveyor belts, require custom conveyor rollers for specific operations, or need expert advice on selecting the right conveyor accessories for your facility, Jordan is your reliable consultant. For any inquiries or assistance with conveyor system optimization, Jordan is available to share his wealth of knowledge and experience. Feel free to reach out at any time for professional guidance on all matters related to conveyor rollers, belts, and accessories.