Design Conveyor Belt Engineering
Conveyor belt systems are integral to a myriad of industries, from mining and manufacturing to logistics and food processing, facilitating the efficient and continuous movement of goods and materials. At the heart of these systems lies the field of conveyor belt engineering, a specialized discipline dedicated to the design, optimization, and maintenance of conveyor belts. This engineering domain not only ensures the operational efficiency of conveyor systems but also plays a crucial role in enhancing their reliability and longevity. By applying principles of mechanical engineering, material science, and automation, conveyor belt engineering contributes significantly to the advancement and innovation of industrial operations worldwide.
The Basics of Conveyor Belt Engineering Systems
Conveyor belt systems are pivotal in various sectors, providing a streamlined approach to moving materials efficiently. The design and functionality of these systems are grounded in the principles of conveyor belt engineering, ensuring optimal performance and reliability. Let’s delve into the essence of what conveyor belts are and their critical role in material handling.
What Conveyor Belts Are and Their Functioning
Conveyor belts are more than just physical entities; they are the lifeline of production lines and distribution centers. Their engineering involves careful consideration of material, design, and application to ensure they meet the specific needs of different industries.
- Core Functionality: At its most basic, a conveyor belt transports items from one location to another. This simple yet effective mechanism is vital in minimizing manual labor and optimizing workflow.
- Material Composition: Conveyor belts are made from various materials, including rubber, PVC, fabric, and metal, each selected based on the application’s specific requirements for durability, flexibility, and environmental resistance.
- Power and Movement: The driving force behind a conveyor belt is typically an electric motor that transfers power to a drive pulley, setting the belt in motion and controlling its speed to match the operational demands.
- Adaptability: Modern conveyor belt engineering allows systems to adapt to different operational needs, including changes in direction, elevation, and speed, making them highly versatile in industrial applications.
- Load Handling: The surface and structure of conveyor belts are designed to handle different types of loads, from fine grains to large, heavy products, ensuring stability and reducing spillage.
- System Integration: Conveyor belts are often part of a larger automated system, integrated with sorting devices, scanners, and packaging equipment for a cohesive material handling solution.
- Automated Controls: Advanced conveyor systems come equipped with automated control systems, using sensors and software to monitor and adjust the conveyor’s performance for efficiency and safety.
- Safety Mechanisms: Safety is paramount in conveyor belt engineering, with systems featuring guards, emergency stops, and other safety devices to protect workers and the materials being transported.
Main Components of a Conveyor Belt System and Their Functions
The effectiveness of a conveyor belt system lies in its components, each meticulously engineered for durability and performance. Understanding these components provides insight into the complexity and ingenuity of conveyor belt engineering.
- Belt Material: The choice of belt material is crucial, affecting the system’s durability, flexibility, and suitability for specific types of cargo. Engineers select materials that balance strength, wear resistance, and maintenance needs.
- Pulleys and Drums: Pulleys guide and drive the conveyor belt, with the drive pulley providing the motion and tension needed for effective material transport. Tail pulleys and idler pulleys support the belt’s weight and adjust its tension.
- Drive System: The motor and gearbox assembly is the powerhouse of the conveyor system, calibrated to provide the necessary force to move the belt at the desired speed, even under varying load conditions.
- Support Frame: The frame serves as the backbone of the conveyor system, designed to withstand the weight of the belt, the materials it carries, and the dynamic forces in operation. It must be robust and adaptable to different installation environments.
- Carrying Rollers: These rollers support the belt and its load, reducing friction and wear on the belt itself. They are strategically placed along the conveyor’s length to ensure smooth and efficient belt movement.
- Control Systems and Sensors: Modern conveyor systems are equipped with sophisticated control systems that manage the conveyor’s speed, direction, and operational sequences, enhancing efficiency and safety.
- Loading and Unloading Points: These are specially designed zones where materials are efficiently loaded onto the conveyor and offloaded at their destination. They are engineered for smooth transitions to minimize bottlenecks and ensure continuous flow.
Each component in a conveyor belt system plays a pivotal role, and their design and integration are fundamental aspects of conveyor belt engineering. This engineering discipline ensures that conveyor systems meet the specific needs of various industries, enhancing efficiency and safety in material handling processes.
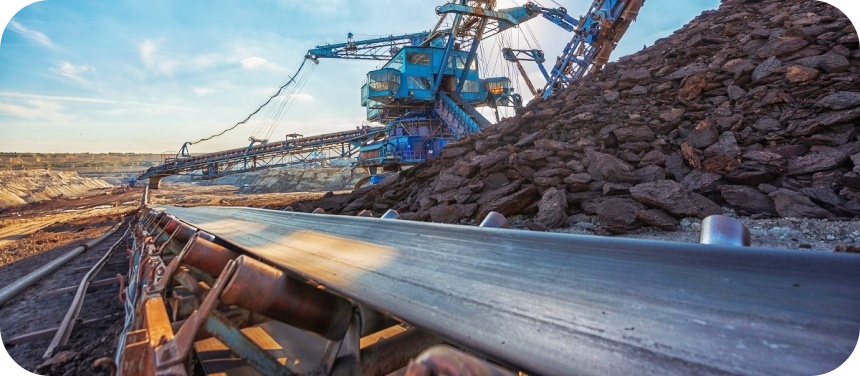
Types of Conveyor Belts in Conveyor Belt Engineering
In the intricate field of conveyor belt engineering, the selection of the appropriate conveyor belt type is pivotal for ensuring operational efficiency, safety, and longevity. This choice is influenced by a myriad of factors, including the nature of the materials being transported, the environment in which the conveyor will operate, and the specific requirements of the application. Let’s explore the diverse range of conveyor belts engineered to meet these varied demands and the critical criteria guiding their selection.
Exploring Different Types of Conveyor Belts
The innovation and versatility in conveyor belt engineering have led to the development of various types of conveyor belts, each designed to fulfill specific material handling needs. From standard fabric belts to highly specialized belts, the range available reflects the engineering ingenuity in this field.
- EP (Polyester-Nylon) Belts: These belts are a testament to the engineering blend of strength and flexibility, making them suitable for a wide range of applications, from light to heavy-duty material handling.
- Steel Cord Conveyor Belts: Engineered for their high tensile strength and low elongation, these belts are the backbone of long-distance and heavy-load conveying, particularly in the mining sector.
- Modular Plastic Belts: The adaptability of these belts to various configurations, coupled with their ease of maintenance, makes them ideal for industries requiring high standards of hygiene and versatility.
- Thermoplastic Polyurethane (TPU) Belts: These belts are distinguished by their resistance to oils, fats, and chemicals, making them a go-to choice in the food processing and pharmaceutical industries.
- Flat Belts: The simplicity and efficiency of flat belts make them suitable for a multitude of light to medium-duty applications across various industries.
- Cleated Belts: The unique design of cleated belts, with raised sections for grip, addresses the challenges of transporting materials on inclines or declines, preventing slippage and product roll-back.
- Specialty Application Belts: This category encompasses belts designed for unique applications, such as high-temperature operations or environments requiring anti-static properties, showcasing the customizability in conveyor belt engineering.
Selection Criteria for Conveyor Belts
The process of selecting the right conveyor belt is a meticulous one, guided by a set of criteria that ensure the belt’s compatibility with the application’s demands. These criteria are foundational to conveyor belt engineering, ensuring that each belt performs optimally in its intended environment.
- Material Characteristics: Understanding the properties of the materials to be conveyed is crucial, as factors like weight, abrasiveness, and temperature significantly influence belt selection.
- Conveying Distance and Path: The layout of the conveyor system, including its length and the complexity of its path, dictates the need for belts with specific structural and material characteristics.
- Load Capacity: The belt’s design must accommodate the intended load without compromise, ensuring durability and reliability under operational stresses.
- Environmental Conditions: The operating environment, with its unique challenges such as chemical exposure or extreme temperatures, plays a critical role in determining the suitable belt material and construction.
- Speed Requirements: The operational speed of the conveyor system necessitates belts that can handle dynamic forces efficiently, maintaining stability and throughput.
- Maintenance and Durability: The ease of maintenance and the expected service life of the belt are key considerations, impacting the overall efficiency and cost-effectiveness of the conveyor system.
- Regulatory and Hygiene Standards: In sectors where hygiene and safety are paramount, the selection of conveyor belts must align with stringent regulatory standards, ensuring compliance and safety.
The realm of conveyor belt engineering is marked by a continuous pursuit of innovation and efficiency, with each type of conveyor belt and selection criterion reflecting a deep understanding of material handling challenges and solutions. This meticulous approach ensures that conveyor systems across industries operate with optimal efficiency, safety, and reliability.
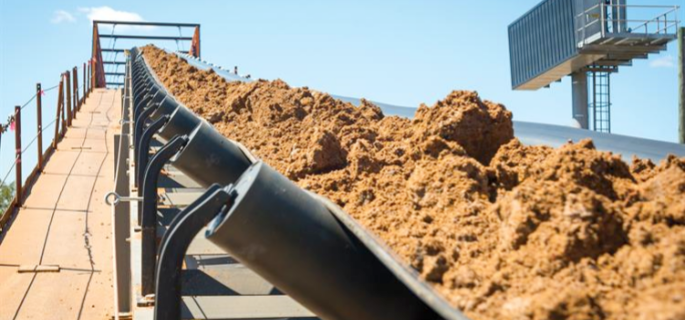
Conveyor Belt Engineering: Typical Drive Configurations
In conveyor belt engineering, the drive configuration is critical to the operation and efficiency of the conveyor system. The drive configuration refers to how the power is transmitted to the conveyor belt to move it. Below are some typical drive configurations used in conveyor belt systems:
End Drive Configuration
- Description: In an end drive configuration, the drive motor and gearbox are located at the end of the conveyor. The motor applies torque to the head (or tail) pulley, which drives the conveyor belt.
- Advantages:
- Simple and cost-effective.
- Easy to maintain and service.
- Suitable for short to medium-length conveyors.
- Applications:
- Commonly used in packaging lines, manufacturing, and general material handling where space and load are moderate.
Center Drive Configuration
- Description: The center drive configuration places the drive motor and gearbox in the middle of the conveyor. This design allows the belt to be driven from the center, which helps distribute the tension more evenly across the belt.
- Advantages:
- Better load distribution and belt tension management.
- Allows the use of longer conveyor belts without excessive belt tension.
- Can drive belts in both directions.
- Applications:
- Ideal for conveyors that require reversing or where the belt needs to be tensioned evenly across its length, such as in certain processing and assembly applications.
Dual Drive Configuration
- Description: The dual drive configuration uses two drive motors and gearboxes, usually located at both ends of the conveyor. This configuration provides additional power and control, especially for long or heavy-duty conveyors.
- Advantages:
- Increased power for moving heavy loads or very long conveyors.
- Enhanced control and synchronization of belt speed.
- Reduces the load on each individual motor, potentially increasing the system’s lifespan.
- Applications:
- Used in mining, heavy industrial applications, or very long conveyor systems where a single drive system would be insufficient.
Top or Bottom Mount Drive Configuration
- Description: In this configuration, the drive motor and gearbox are mounted on the top or bottom of the conveyor frame, rather than at the end or in the center. The drive can then be connected to either the head or tail pulley, depending on the design.
- Advantages:
- Saves space, as the drive components are mounted within the conveyor’s footprint.
- Offers flexibility in conveyor layout and design, especially in tight spaces.
- Applications:
- Commonly used in environments where floor space is limited, such as in compact manufacturing facilities or in overhead conveyor systems.
Underslung Drive Configuration
- Description: The underslung drive configuration mounts the drive motor and gearbox underneath the conveyor. The drive is usually connected to a pulley via a chain or belt.
- Advantages:
- Keeps the drive components protected and out of the way.
- Reduces the conveyor’s overall height, which can be advantageous in certain installations.
- Applications:
- Suitable for conveyors that need to be as low-profile as possible or where the drive components need to be shielded from contaminants, such as in food processing or cleanroom environments.
Internal Drive Configuration
- Description: An internal drive configuration integrates the drive motor and gearbox within the conveyor’s pulley, creating a more compact and streamlined system.
- Advantages:
- Extremely compact, with minimal external components.
- Reduces the risk of contamination, as the drive is enclosed.
- Can improve safety by eliminating exposed moving parts.
- Applications:
- Often used in food processing, pharmaceuticals, or other industries where hygiene is critical, and space is at a premium.
Shaft Mounted Drive Configuration
- Description: In shaft-mounted drive configurations, the drive motor and gearbox are directly mounted onto the shaft of the conveyor pulley. This setup eliminates the need for additional drive components like couplings or chains.
- Advantages:
- Simplified design with fewer components, reducing potential failure points.
- Compact and easy to maintain.
- Efficient power transmission, as there’s no energy loss through additional components.
- Applications:
- Typically used in straightforward conveyor designs, such as those in aggregate handling, mining, and heavy material transport.
Each drive configuration has its own set of benefits and is chosen based on the specific requirements of the conveyor system, including the type of materials being transported, the length of the conveyor, space constraints, and the required power and control. Understanding these configurations allows engineers to design more efficient, reliable, and cost-effective conveyor systems.
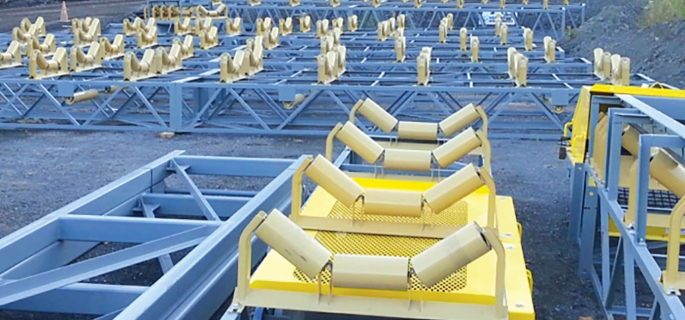
Conveyor Belt Engineering Phase
Conveyor belt engineering each phase plays a critical role in ensuring that meets the specific needs of the operation, operates efficiently. The engineering and design of a conveyor belt system typically go through several key phases. These phases ensure that the conveyor system is tailored to meet the specific needs of the application while being efficient, reliable, and safe. Here’s an overview of the typical phases involved in conveyor belt engineering:
1. Needs Assessment and Feasibility Study
- Objective: To understand the specific requirements of the project and evaluate the feasibility of various conveyor system designs.
- Activities:
- Conducting a site survey to gather data on material characteristics, flow rates, distances, and environmental conditions.
- Consulting with stakeholders to understand operational goals, budget constraints, and any special requirements (e.g., hygiene standards, hazardous materials).
- Assessing the feasibility of different conveyor belt types and configurations based on the site conditions and operational needs.
2. Conceptual Design
- Objective: To develop a preliminary design that outlines the general configuration of the conveyor system.
- Activities:
- Creating initial design sketches or CAD models to visualize different layout options.
- Selecting the type of conveyor belt (e.g., flat belt, modular belt, cleated belt) and drive configuration (e.g., end drive, center drive, dual drive).
- Estimating the required capacity, belt speed, and motor power.
- Identifying potential challenges or risks, such as space constraints, load distribution, or environmental impacts.
3. Detailed Design and Engineering
- Objective: To refine the conceptual design into a detailed and functional system ready for manufacturing and installation.
- Activities:
- Developing detailed engineering drawings and specifications for the conveyor system, including belt width, length, speed, motor size, and pulley dimensions.
- Calculating key parameters such as belt tension, power requirements, and conveying capacity using engineering formulas and software tools.
- Designing support structures, frames, and mounting systems to ensure stability and durability.
- Incorporating safety features and compliance with relevant standards (e.g., OSHA, ISO).
- Selecting materials for the belt, pulleys, and other components based on operational requirements, such as temperature, chemical resistance, or load-bearing capacity.
- Conducting finite element analysis (FEA) or other simulations to predict the performance and identify potential failure points.
4. Prototyping and Testing (if applicable)
- Objective: To build and test a prototype or scale model of the conveyor system to validate the design.
- Activities:
- Fabricating a prototype or model to simulate the conveyor’s operation under real-world conditions.
- Testing the prototype for load capacity, belt alignment, tensioning, and drive system performance.
- Making adjustments based on test results to optimize the design for durability, efficiency, and safety.
5. Manufacturing and Procurement
- Objective: To manufacture the components of the conveyor system and procure any necessary parts or materials.
- Activities:
- Producing or ordering conveyor belts, pulleys, motors, frames, and other components according to the detailed design specifications.
- Coordinating with suppliers to ensure the quality and timely delivery of materials.
- Assembling components as per the design to create the final conveyor system.
- Conducting quality checks on manufactured components to ensure they meet design standards and tolerances.
6. Installation and Commissioning
- Objective: To install the conveyor system on-site and ensure it operates as intended.
- Activities:
- Transporting the conveyor components to the installation site.
- Assembling the conveyor system, including aligning and tensioning the belt, connecting the drive system, and setting up any control systems.
- Conducting initial operational tests to check for alignment, tension, speed control, and overall performance.
- Calibrating sensors, drives, and other controls to ensure smooth and efficient operation.
- Training operators and maintenance personnel on the proper use and upkeep of the conveyor system.
7. Testing and Validation
- Objective: To verify that the installed conveyor system meets all operational requirements and safety standards.
- Activities:
- Performing load tests to ensure the system can handle the specified material flow and capacity.
- Checking for any issues with belt tracking, slippage, or noise.
- Validating that the system operates within the specified parameters, including speed, power consumption, and throughput.
- Conducting safety inspections to confirm compliance with all relevant regulations and standards.
8. Maintenance Planning and Documentation
- Objective: To develop a maintenance plan and provide documentation for the ongoing operation of the conveyor system.
- Activities:
- Creating a maintenance schedule that includes routine inspections, belt adjustments, and part replacements.
- Documenting the installation process, including wiring diagrams, component specifications, and operational guidelines.
- Providing manuals and training materials to operators and maintenance staff.
- Establishing a troubleshooting guide to help diagnose and resolve common issues.
9. Post-Installation Support
- Objective: To provide ongoing support to ensure the conveyor system continues to operate efficiently and reliably.
- Activities:
- Offering technical support and responding to any issues that arise after installation.
- Conducting periodic reviews of system performance and making recommendations for improvements or upgrades.
- Providing spare parts and replacement components as needed.
- Updating the maintenance plan and documentation based on operational experience.
Conveyor belt engineering is a complex process that requires careful planning, design, and execution. Each phase plays a critical role in ensuring that the final conveyor system meets the specific needs of the operation, operates efficiently, and complies with safety standards. By following these phases, engineers can develop conveyor systems that are reliable, durable, and capable of handling the demands of modern industrial processes.
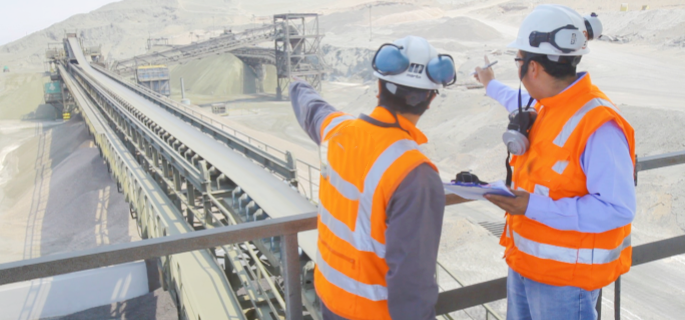
Conveyor Belt Engineering Service
Conveyor belt engineering services encompass a broad range of professional activities designed to support the planning, design, installation, maintenance, and optimization of conveyor systems. These services are essential for businesses that rely on conveyor belts for their material handling needs, ensuring that systems are efficient, reliable, and tailored to specific operational requirements. Below is an overview of the typical services provided by a conveyor belt engineering service provider:
1. Consultation and Needs Assessment
- Service Description:
- This initial phase involves working closely with the client to understand their specific material handling needs. Engineers assess the type of materials being conveyed, the required capacity, environmental conditions, and other operational parameters.
- Activities:
- On-site visits to evaluate existing systems and operational environments.
- Detailed discussions with stakeholders to understand goals, constraints, and future expansion plans.
- Feasibility studies to determine the most suitable conveyor belt solutions.
2. Custom Conveyor System Design
- Service Description:
- Designing a conveyor belt system that meets the unique requirements of the client. This includes creating detailed engineering drawings and selecting appropriate materials, components, and configurations.
- Activities:
- CAD modeling and design of conveyor layouts, including belt width, speed, drive systems, and support structures.
- Selection of belt materials based on factors such as load type, temperature, chemical exposure, and wear resistance.
- Design of safety features and compliance with industry standards (e.g., OSHA, ISO).
3. Manufacturing and Procurement Support
- Service Description:
- Assisting clients in sourcing and manufacturing the components needed for the conveyor system. This ensures that all parts meet the design specifications and are delivered on time.
- Activities:
- Identification and recommendation of reliable suppliers for belts, pulleys, motors, and other components.
- Quality control inspections to ensure that all manufactured parts conform to the design requirements.
- Coordination of logistics for the delivery of materials and components to the installation site.
4. Installation and Commissioning
- Service Description:
- Providing on-site installation services to assemble and set up the conveyor system. This phase includes testing and commissioning to ensure everything operates as designed.
- Activities:
- Assembling the conveyor system according to the engineering design, including belt tensioning, alignment, and mounting of drive systems.
- Integration of control systems, including sensors, switches, and programmable logic controllers (PLCs).
- Conducting operational tests to verify performance, including load handling, speed, and safety features.
5. System Optimization and Upgrades
- Service Description:
- Evaluating existing conveyor systems to identify areas for improvement. This may involve upgrading components, optimizing layouts, or adjusting operating parameters to enhance efficiency.
- Activities:
- Performance audits to assess energy consumption, throughput, and system reliability.
- Recommendations for upgrading belts, drives, or control systems to improve efficiency or accommodate new materials.
- Implementation of modifications or enhancements, such as adding automation features or adjusting belt speed.
6. Maintenance and Repair Services
- Service Description:
- Offering regular maintenance services to ensure the conveyor system remains in optimal condition, as well as providing emergency repair services to minimize downtime in case of failures.
- Activities:
- Scheduled inspections and preventive maintenance, including belt tensioning, lubrication, and replacement of worn parts.
- Emergency repair services to address issues such as belt tears, motor failures, or pulley misalignment.
- Spare parts management and inventory control to ensure critical components are always available.
7. Training and Technical Support
- Service Description:
- Providing training to the client’s staff on the proper operation and maintenance of the conveyor system. This ensures that the system is used safely and effectively.
- Activities:
- Training sessions covering system operation, troubleshooting, and maintenance procedures.
- Development of training manuals and operational guides tailored to the specific conveyor system.
- Ongoing technical support via phone, email, or on-site visits to address any operational concerns.
8. Compliance and Safety Audits
- Service Description:
- Conducting audits to ensure that the conveyor system complies with relevant safety regulations and industry standards. This service helps clients avoid legal issues and improve workplace safety.
- Activities:
- Inspecting the conveyor system for compliance with local and international safety standards (e.g., OSHA, CE).
- Identifying potential safety hazards and recommending corrective actions.
- Providing certification or documentation to demonstrate compliance with safety and quality standards.
9. Lifecycle Management
- Service Description:
- Managing the entire lifecycle of the conveyor system, from initial design through to decommissioning. This ensures that the system remains efficient and cost-effective throughout its operational life.
- Activities:
- Monitoring system performance over time and making recommendations for upgrades or replacement as needed.
- Planning and executing system decommissioning and disposal in an environmentally responsible manner.
- Assisting with the transition to new conveyor systems when the existing one reaches the end of its useful life.
Conveyor belt engineering services are comprehensive and tailored to meet the specific needs of various industries. Whether a client needs a new system designed from scratch or an existing system optimized, these services ensure that the conveyor belt operates efficiently, safely, and reliably. By engaging with a professional conveyor belt engineering service provider, businesses can achieve significant improvements in productivity, reduce downtime, and extend the lifespan of their material handling systems.
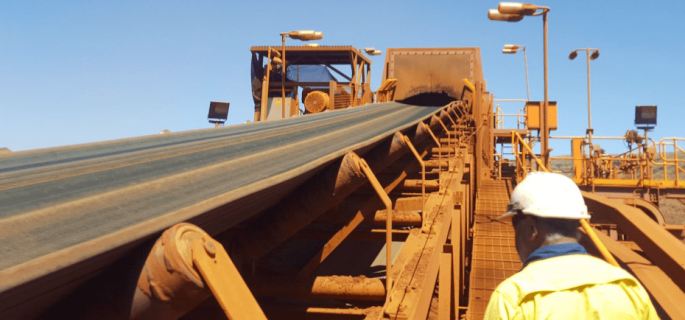
Conveyor Belt Engineering: Conveying Capacity
Conveying capacity is a fundamental aspect of conveyor belt engineering. It refers to the volume or weight of material that a conveyor belt can transport over a specified time period. Understanding and calculating the conveying capacity is crucial for designing an efficient conveyor system that meets the operational demands of a particular application. Below is a detailed exploration of conveying capacity in the context of conveyor belt engineering.
Factors Affecting Conveying Capacity
The conveying capacity of a conveyor belt is influenced by several key factors:
- Belt Width: The width of the conveyor belt directly impacts the amount of material that can be transported. Wider belts can carry more material.
- Belt Speed: The speed at which the belt moves plays a significant role in determining how much material is conveyed. Faster belt speeds increase the capacity, assuming the material is loaded uniformly.
- Material Density: The density of the material being conveyed affects the weight that the belt can carry. Higher density materials will result in a higher conveying capacity by weight but not necessarily by volume.
- Belt Troughing: The shape of the belt, particularly when it’s trough-shaped, can influence the capacity. Troughing increases the effective carrying area of the belt, allowing for more material to be transported.
- Load Cross-Section: The shape and distribution of the load on the belt (e.g., flat, concave, or piled) also impact the conveying capacity. A well-distributed load that utilizes the full width and depth of the belt maximizes capacity.
- Inclination Angle: The angle of inclination of the conveyor affects the capacity. Steeper angles typically reduce the capacity due to the tendency of the material to slip or require more energy to move.
- Belt Tension and Sag: Proper belt tension ensures the belt remains flat and stable, which is crucial for maintaining consistent capacity. Excessive sag can reduce capacity by allowing material to fall off or accumulate unevenly.
Conveying Capacity Formula
The theoretical conveying capacity of a conveyor belt can be calculated using the following formula:
[ Q = A × v × ρ ]
Where:
- Q = Conveying capacity (in cubic meters per hour or cubic feet per minute)
- A = Cross-sectional area of the material on the belt (in square meters or square feet)
- v = Belt speed (in meters per second or feet per minute)
- ρ = Bulk density of the material (in kilograms per cubic meter or pounds per cubic foot)
For practical purposes, the cross-sectional area ( A ) can be calculated based on the belt width and troughing angle, while the belt speed ( v ) and material density ( ρ ) are typically known or measured.
Example Calculation
Let’s consider an example to calculate the conveying capacity:
- Belt Width (B): 1 meter
- Belt Speed (v): 2 meters per second
- Material Bulk Density (ρ): 1500 kg/m³
- Trough Angle: 30 degrees
First, calculate the cross-sectional area ( A ). Assuming a simple approximation for a trough-shaped load:
[ A = 0.5 × B × {Height of load (H)} × {Trough Factor} ]
Where the Trough Factor depends on the angle and can typically range from 0.5 to 0.9 for practical applications.
After calculating ( A ), you multiply by the belt speed and material density to determine ( Q ).
Optimizing Conveying Capacity
To optimize conveying capacity:
- Increase Belt Width or Speed: These are the most direct ways to increase capacity, though they also increase energy consumption and may require more robust belt materials.
- Optimize Load Distribution: Ensure that the material is loaded evenly across the belt and utilizes the full cross-sectional area.
- Adjust Troughing Angle: A higher troughing angle can increase the cross-sectional area, though it may require a stronger belt to handle the increased tension.
- Manage Inclination: If possible, minimize steep inclines to reduce the loss of capacity due to material slippage.
- Proper Belt Tensioning: Maintaining the correct tension will prevent sagging, which can reduce capacity by causing material spillage or uneven loading.
Practical Considerations
In real-world applications, the theoretical conveying capacity is often reduced by factors such as:
- Material Flow Properties: Sticky or cohesive materials might not flow smoothly, reducing effective capacity.
- Belt Wear and Tear: Over time, wear and tear can affect belt tension and alignment, impacting capacity.
- Environmental Factors: Conditions such as humidity, temperature, and dust can affect material properties and belt operation.
Conveying capacity is a vital parameter in conveyor belt engineering, directly affecting the efficiency and effectiveness of material handling systems. By carefully considering and optimizing the factors that influence capacity, engineers can design conveyor systems that meet the specific needs of their operations, ensuring reliable performance and cost-effectiveness.
Engineering and Design of Belt Conveyors in Conveyor Belt Engineering
The engineering and design of belt conveyors are pivotal aspects of conveyor belt engineering, requiring a harmonious blend of theoretical principles and practical applications. This process ensures the creation of conveyor systems that are not only efficient and reliable but also tailored to meet the specific needs of various industrial applications.
Principles of Belt Conveyor Design
The design of belt conveyors in conveyor belt engineering is guided by a set of core principles that ensure the functionality and longevity of the system:
- System Layout: The initial step involves drafting a layout that optimizes the path of the conveyor, minimizing turns and elevation changes to reduce wear and energy consumption.
- Component Selection: Choosing the right components, from belts to motors and pulleys, is crucial. Each component must be matched to the operational demands of the conveyor system.
- Load Analysis: Understanding the characteristics of the material to be conveyed, including weight, size, and abrasiveness, informs the selection of belt material and design specifications.
- Belt Speed: Determining the optimal belt speed is a balance between operational efficiency and the careful handling of materials to prevent damage and spillage.
- Drive System Design: The conveyor’s drive system, including motor sizing and gear ratios, is engineered to provide sufficient power for the intended load and conveyor length.
- Tension Control: Proper tensioning of the conveyor belt is essential for maintaining alignment and preventing slippage or excessive wear.
- Support Structure: The design of the conveyor’s support structure must accommodate the operational load and environmental conditions, ensuring stability and durability.
- Safety Measures: Incorporating safety features, such as emergency stops, guards, and warning signals, is integral to the design process, protecting operators and materials.
- System Optimization: The final design is refined through simulation and testing, optimizing the conveyor’s performance for efficiency, reliability, and longevity.
Importance of Conveyor Dynamics
Conveyor dynamics play a critical role in the design of belt conveyors, influencing their stability and efficiency:
- Belt Behavior: Understanding how the conveyor belt behaves under different loads and speeds is essential for designing a system that operates smoothly and efficiently.
- Material Flow: The dynamics of material flow on the conveyor, including loading and unloading impacts, must be considered to prevent bottlenecks and ensure consistent throughput.
- Vibration Analysis: Analyzing potential vibrations and their sources within the conveyor system helps in designing countermeasures to prevent structural fatigue and failure.
- Stress Distribution: Assessing the stress distribution along the conveyor belt and its components ensures that the design can withstand operational loads without excessive wear or failure.
- Energy Efficiency: Dynamics analysis can identify areas where energy efficiency can be improved, such as optimizing motor power and reducing frictional losses.
- Control Systems: The integration of advanced control systems can enhance the dynamic performance of the conveyor, adjusting operational parameters in real-time for optimal efficiency.
- Environmental Factors: The impact of environmental conditions, such as wind and temperature, on the conveyor’s dynamics must be evaluated to ensure stable operation.
- Maintenance Planning: Understanding the dynamic forces at play within the conveyor system aids in developing effective maintenance strategies, reducing downtime and extending the system’s lifespan.
In belt conveyor engineering, the meticulous design of belt conveyors, grounded in the principles of dynamics, ensures the creation of systems that are not only efficient and reliable but also capable of meeting the diverse demands of modern industry.
Conveyor Belt Engineering Courses and Resources
The field of conveyor belt engineering is both dynamic and expansive, requiring a solid foundation of knowledge and continuous professional development. For those aspiring to excel in this field, a wealth of educational resources, courses, and certifications are available, designed to enhance expertise and foster innovation.
Educational Resources and Courses
In the realm of conveyor belt engineering, educational resources and courses play a pivotal role in shaping the competencies of professionals:
- University Programs: Several universities offer specialized courses in mechanical engineering with modules focused on conveyor belt design and material handling systems, providing a strong theoretical and practical foundation.
- Online Courses: Platforms like Coursera, Udemy, and edX offer courses on conveyor belt engineering, covering topics from basic design principles to advanced system optimization, making learning accessible to a global audience.
- Professional Workshops: Industry associations and professional bodies often conduct workshops and seminars, offering hands-on experience and insights into the latest trends and technologies in conveyor belt engineering.
- Technical Webinars: Webinars hosted by leading companies and experts in the field provide opportunities to learn about cutting-edge research, case studies, and innovative solutions to complex engineering challenges.
- Certification Programs: Certifications from recognized professional organizations validate expertise in conveyor belt engineering, enhancing credibility and career prospects.
- Industry Conferences: Attending conferences allows professionals to network with peers, discuss challenges and solutions, and stay updated on industry standards and regulations.
- Technical Publications: Journals, textbooks, and online articles offer in-depth analyses of specific aspects of belt conveyor engineering, from material properties to system dynamics and maintenance strategies.
- Vendor Training: Manufacturers of conveyor systems often provide training on the proper installation, operation, and maintenance of their products, offering practical insights into system optimization.
Value of Continuous Learning and Professional Development
Continuous learning and professional development are cornerstones of success in conveyor belt engineering:
- Adapting to Technological Advances: The field is continually evolving with new materials, technologies, and methodologies. Ongoing education ensures professionals remain at the forefront of these changes.
- Enhancing Problem-Solving Skills: Exposure to a variety of case studies and real-world scenarios sharpens analytical and problem-solving skills, essential for addressing complex engineering challenges.
- Networking Opportunities: Engaging in educational programs and industry events opens doors to networking with peers, mentors, and leaders in the field, fostering collaborative opportunities and knowledge exchange.
- Career Advancement: Advanced knowledge and certifications in conveyor belt engineering can lead to career progression, from technical roles to leadership positions within organizations.
- Innovation and Creativity: Continuous learning inspires innovation, encouraging professionals to develop creative solutions that improve efficiency, safety, and sustainability in conveyor systems.
- Regulatory Compliance: Staying informed about industry standards and regulations ensures that conveyor systems are designed and operated in compliance with legal and safety requirements.
- Quality Assurance: A deep understanding of engineering principles and best practices leads to the design and implementation of high-quality, reliable conveyor systems.
- Global Perspective: Learning from international experts and case studies provides a global perspective on conveyor belt engineering, enabling the adoption of best practices from around the world.
The pursuit of education and professional development in conveyor belt engineering is instrumental in building a rewarding career, driving innovation, and ensuring the optimal design and operation of conveyor systems.
Conveyor Belt Engineering PDFs and Technical Documents
In the specialized field of conveyor belt engineering, access to a wide range of technical documents and engineering PDFs is essential for professionals seeking to deepen their understanding and enhance their expertise. These resources serve as invaluable tools, offering detailed insights into various aspects of conveyor belt design, operation, and maintenance.
Invaluable Resources in Conveyor Belt Engineering
- Design Manuals: Comprehensive design manuals provide foundational knowledge on the principles of conveyor belt engineering, covering topics from basic configurations to complex system designs, ensuring engineers have a solid base to build upon.
- Technical Guides: Detailed technical guides delve into the specifics of conveyor belt materials, properties, and selection criteria, aiding engineers in choosing the right belt for their application based on load, speed, and environmental conditions.
- Installation Handbooks: These documents offer step-by-step instructions on the correct installation procedures for conveyor belts, ensuring optimal performance and longevity, and helping to avoid common pitfalls that can lead to premature wear or failure.
- Maintenance Strategies: Maintenance guides focus on the upkeep of conveyor belts, presenting best practices for routine inspections, cleaning, and repairs, which are crucial for maintaining system efficiency and preventing downtime.
- Safety Protocols: Safety manuals outline the essential safety measures and protocols that need to be implemented to protect workers and ensure the safe operation of conveyor belt systems, in compliance with industry standards and regulations.
- Case Studies: Real-world case studies provide insights into the challenges and solutions encountered in various conveyor belt engineering projects, offering valuable lessons learned and innovative approaches to complex problems.
- Research Papers: Academic and industry research papers explore the latest advancements and technological innovations in conveyor belt engineering, presenting findings from experimental studies and theoretical analyses that push the boundaries of current knowledge.
- Regulatory Standards: Documents detailing the regulatory standards and compliance requirements for conveyor belt systems are critical for engineers to ensure their designs meet all legal and safety criteria, avoiding potential liabilities.
These resources, ranging from engineering PDFs to technical guides and case studies, are fundamental to the ongoing education and professional development of individuals in the field of conveyor belt engineering. They not only provide a wealth of knowledge on the technical aspects of conveyor systems but also offer insights into practical applications, emerging trends, and best practices in the industry.
Maintenance and Safety in Conveyor Belt Engineering
In the realm of conveyor belt engineering, the emphasis on maintenance and safety is paramount, not only for the operational integrity of the conveyor systems but also for the protection of the workforce. These practices are ingrained in the engineering process, from the initial design to the daily operation, ensuring that each conveyor belt system is both efficient and safe. Let’s explore the best practices and the engineering principles that underpin the development of safer conveyor systems.
Best Practices for Maintenance and Safety
Effective maintenance and safety protocols are the backbone of reliable conveyor belt operation. Implementing these practices ensures system longevity and prevents accidents:
- Scheduled Maintenance: Regularly scheduled maintenance checks are essential for identifying potential issues before they escalate, ensuring the conveyor belt remains in optimal condition.
- Operator Training: Comprehensive training programs for operators and maintenance personnel emphasize the correct handling and upkeep of conveyor systems, fostering a safe working environment.
- Emergency Protocols: Robust emergency stop mechanisms and protocols ensure that in the event of a problem, the system can be quickly and safely deactivated to prevent accidents.
- Protective Guarding: Installing protective guards around moving parts is a critical safety measure that prevents injuries by reducing the risk of contact with the machinery.
- Cleanliness and Order: Maintaining cleanliness around conveyor systems minimizes the risk of slips, trips, and falls, while also preventing material buildup that could affect the conveyor’s operation.
- Monitoring System Health: Regular monitoring of the conveyor belt for signs of wear or damage allows for timely interventions, preventing unexpected failures.
- Clear Safety Signage: Properly placed safety signs and instructions promote awareness and guide behavior around conveyor systems, contributing to a safer workplace.
- Alignment and Tension Checks: Ensuring the conveyor belt is properly aligned and tensioned prevents operational issues that could lead to accidents or system damage.
Engineering’s Role in Safer Conveyor Systems
The engineering behind conveyor systems is not just about efficiency and productivity; it’s equally focused on safety. Through thoughtful design and innovation, engineers create systems that inherently minimize risk:
- Designing for Safety: From the outset, conveyor systems are designed with safety in mind, incorporating features that mitigate risks and enhance operational security.
- Safety Innovations: Engineers continually seek to innovate, developing new safety features and technologies that can be integrated into conveyor systems to enhance their safety profile.
- Material and Component Selection: The choice of materials and components in the construction of conveyor systems takes into account not only performance but also safety, ensuring that all elements contribute to a secure operating environment.
- Ergonomic Considerations: By considering ergonomics in the design phase, engineers can reduce the physical strain on operators, thereby decreasing the risk of injury.
- Incorporating Redundancies: Designing conveyor systems with redundancies ensures that even in the event of a component failure, the system can remain operational or safely shut down.
- Adherence to Standards: Compliance with national and international safety standards is a fundamental aspect of conveyor belt engineering, ensuring that systems meet rigorous safety criteria.
- Designing for Maintenance: Conveyor systems are designed to be easily accessible for maintenance, reducing the risk associated with servicing and repairs.
- Feedback and Continuous Improvement: The engineering process is iterative, with feedback from operational experiences driving continuous improvements in safety and design.
In conveyor belt engineering, the integration of maintenance and safety into every aspect of conveyor systems is a testament to the field’s commitment to protecting both the machinery and the individuals who operate it. This holistic approach ensures that conveyor belt systems are not only productive and efficient but also safe and reliable.
Innovations and Future Trends in Conveyor Belt Engineering
The landscape of conveyor belt engineering is continually evolving, driven by technological advancements and a growing emphasis on sustainability and efficiency. This dynamic field is witnessing the emergence of innovative solutions and trends that promise to redefine the future of material handling. Let’s delve into the recent innovations and future trends that are shaping conveyor belt engineering.
Recent Innovations in Conveyor Belt Engineering
The forefront of conveyor belt engineering is marked by a series of groundbreaking innovations:
- Smart Conveyor Belts: Integration of IoT (Internet of Things) sensors and RFID (Radio Frequency Identification) tags into conveyor belts enables real-time tracking of materials and condition monitoring of the belt itself, enhancing operational efficiency and predictive maintenance.
- Energy-Efficient Designs: Advances in material science and engineering have led to the development of energy-efficient conveyor belts that reduce power consumption, contributing to lower operational costs and a smaller carbon footprint.
- Modular and Flexible Systems: The advent of modular conveyor systems offers unparalleled flexibility, allowing for easy reconfiguration and scaling to meet changing production needs and space constraints.
- Advanced Materials: The use of ultra-durable materials and coatings, such as reinforced rubber compounds and high-tech fabrics, has significantly increased the lifespan and performance of conveyor belts under harsh conditions.
- Self-Healing Materials: Research into self-healing materials promises conveyor belts that can repair minor cuts and abrasions autonomously, drastically reducing maintenance requirements and downtime.
- Sustainable Materials: The push for sustainability has led to the exploration of eco-friendly materials in conveyor belt construction, including recycled plastics and bio-based polymers, minimizing environmental impact.
- Precision Control Systems: The integration of advanced control systems and AI (Artificial Intelligence) enables precise control over belt speed and material flow, optimizing throughput and reducing waste.
- Enhanced Safety Features: Innovations in safety technology, including automatic shutdown mechanisms and contactless safety guards, are making conveyor systems safer for operators and maintenance personnel.
Shaping the Future of Material Handling
These advancements in conveyor belt engineering are not just technological feats; they are shaping the future of material handling in profound ways:
- Increased Automation: Smart conveyor belts and AI-driven control systems are paving the way for fully automated material handling processes, reducing the need for manual intervention and enhancing efficiency.
- Customization and Scalability: Modular conveyor systems allow for tailored solutions that can grow and adapt with the business, offering a cost-effective approach to material handling challenges.
- Sustainability at the Core: The shift towards sustainable materials and energy-efficient designs reflects a broader industry trend towards environmental responsibility and sustainable practices.
- Predictive Maintenance: The ability to monitor the health of conveyor belts in real-time enables predictive maintenance, reducing unexpected downtime and extending the lifespan of the equipment.
- Enhanced Safety: The focus on safety innovations is leading to safer work environments, with reduced risk of accidents and injuries associated with conveyor systems.
- Operational Efficiency: Precision control and smart technologies are optimizing material flow and throughput, ensuring that conveyor systems can meet the demands of high-volume, fast-paced production environments.
- Resilience and Durability: Advances in materials and self-healing technologies are creating conveyor belts that can withstand extreme conditions and wear, ensuring reliable operation over longer periods.
- Global Compliance: Innovations in conveyor belt engineering are facilitating compliance with international standards and regulations, enabling companies to operate seamlessly across global markets.
The trajectory of conveyor belt engineering is marked by innovations that promise not only to enhance the capabilities of conveyor systems but also to redefine the principles of material handling. As these technologies mature and become more widely adopted, the future of conveyor belt engineering looks poised to offer even more efficient, sustainable, and intelligent material handling solutions.
Fill out this form to get in touch with our Conveyor Belt Cutters experts.
FAQs about Conveyor Belt Engineering
In the field of engineering, a conveyor belt is a critical component of a conveyor system, which is extensively used for transporting materials from one location to another within an industrial or commercial setting. It consists of a continuous loop of material, often made of rubber, plastic, metal, or textile, that moves over two or more pulleys. One of these pulleys is powered, moving the belt and the material on it forward. Conveyor belts are fundamental in various industries, including manufacturing, mining, agriculture, and transportation, due to their efficiency in handling bulk materials and products of different shapes and sizes. The engineering behind conveyor belts involves a deep understanding of material properties, mechanical principles, and system design to ensure optimal performance, durability, and safety.
In mechanical engineering, a conveyor refers to a system designed to transport materials or objects from one point to another with minimal manual intervention. It typically comprises a frame that supports rollers, wheels, or a belt upon which goods are transported. Conveyors are engineered based on principles of mechanics, material science, and ergonomics to move items efficiently, safely, and reliably. They can be designed to carry a wide range of items, from small components in manufacturing processes to large volumes of raw materials in mining operations. Mechanical engineers focus on the design, analysis, and maintenance of conveyor systems, ensuring they meet specific operational requirements, such as load capacity, speed, and environmental conditions. The versatility and efficiency of conveyors make them indispensable in production lines, warehouses, and distribution centers.
The manufacturing process of a conveyor belt involves several key steps, each critical to ensuring the belt’s quality and performance. Initially, the design specifications, including length, width, material composition, and intended use, are determined. The process typically begins with the creation of the belt’s carcass, made from layers of fabric or steel cords that provide structural strength. This carcass is then coated with rubber or plastic compounds through a process called calendering, where the materials are pressed and smoothed into flat sheets. The layers are assembled and then subjected to vulcanization, a heat and pressure treatment that causes the rubber to cure and bond, creating a durable and cohesive belt. Additional features, such as cleats or sidewalls, may be added depending on the belt’s intended application. Quality control checks are performed throughout the manufacturing process to ensure the conveyor belt meets all design and performance criteria.
Designing a conveyor belt involves a systematic approach that takes into account the operational requirements, material characteristics, and environmental conditions of its intended application. The process begins with defining the purpose of the conveyor system, such as the type of materials it will transport, the distance they need to be moved, and any specific handling requirements. Key parameters, including belt width, speed, load capacity, and incline angle, are calculated based on these requirements. Material selection for the belt and other components is critical, with choices made based on factors like strength, flexibility, abrasion resistance, and chemical compatibility. The design must also consider safety features, maintenance access, and compliance with industry standards. Advanced software tools and simulation models are often used to optimize the conveyor belt design, ensuring efficiency, reliability, and longevity. Collaboration with manufacturers and material handling experts can provide valuable insights and innovations to enhance the conveyor system’s performance.
A conveyor belt technician is responsible for installing, maintaining, and repairing conveyor belts used in various industries. Their tasks include inspecting belts for wear and tear, replacing damaged parts, ensuring the alignment and tension of belts, and performing preventive maintenance to ensure the efficient operation of the conveyor systems.
The three common types of conveyor belts are:
Flat Belt Conveyors: These are the most widely used type, ideal for transporting goods horizontally or with a slight incline.
Modular Belt Conveyors: These consist of interlocking plastic pieces, making them highly flexible and suitable for various applications, including curves and inclines.
Cleated Belt Conveyors: These belts have raised sections, or cleats, which help move items up steep inclines and prevent slippage.
A conveyor belt is a continuous loop of material that rotates around pulleys to transport goods, materials, or products from one point to another in a manufacturing or processing environment. It plays a crucial role in the automation of industrial processes, facilitating the movement of items efficiently and reducing manual handling.
A conveyor belt works by using a motorized pulley system to move a looped belt made of various materials. As the belt rotates around the pulleys, it creates a continuous motion that transports items placed on it from one end of the system to the other. The friction between the belt and the pulleys, along with the tension in the belt, helps keep it moving and carrying the load.
A conveyor belt transports materials, goods, or products from one location to another within a facility. It is commonly used in manufacturing, logistics, and material handling operations to move items efficiently and consistently along a production line or through various processing stages.
A conveyor belt is typically controlled by a combination of mechanical and electronic components, including:
Motor and Drives: The motor provides the power to move the belt, and the drive system regulates the speed and direction of the belt.
Sensors and Switches: These detect the position and flow of items on the belt and can trigger the belt to stop, start, or change speed based on specific conditions.
Control System (e.g., PLC): A programmable logic controller (PLC) or similar control system may be used to automate the operation of the conveyor belt, coordinating the various components and ensuring smooth and efficient movement.
Last Updated on August 12, 2024 by Jordan Smith
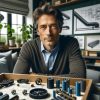
Jordan Smith, a seasoned professional with over 20 years of experience in the conveyor system industry. Jordan’s expertise lies in providing comprehensive solutions for conveyor rollers, belts, and accessories, catering to a wide range of industrial needs. From initial design and configuration to installation and meticulous troubleshooting, Jordan is adept at handling all aspects of conveyor system management. Whether you’re looking to upgrade your production line with efficient conveyor belts, require custom conveyor rollers for specific operations, or need expert advice on selecting the right conveyor accessories for your facility, Jordan is your reliable consultant. For any inquiries or assistance with conveyor system optimization, Jordan is available to share his wealth of knowledge and experience. Feel free to reach out at any time for professional guidance on all matters related to conveyor rollers, belts, and accessories.