Essential Guide to Conveyor Belt Fabrication
I
Conveyor belt fabrication plays a critical role in various industries, from manufacturing to logistics. By crafting customized solutions, businesses can optimize their material handling processes, ensuring efficiency and reliability. This blog will explore the intricate process of conveyor belt fabrication, detailing how it caters to specific needs through customization, the implementation of guidance systems, and the development of various belt types such as v-guide and miniature conveyor belts. Additionally, we will delve into the fabrication of industrial conveyor belts and complete conveyor belt systems, highlighting their applications in heavy-duty sectors. Understanding conveyor belt fabrication is essential for selecting the right materials and designs to enhance productivity and operational longevity.
Enhancing Operations with Custom Conveyor Belt Fabrication Near Me
Importance of Local Custom Conveyor Belt Fabrication Services
Local custom conveyor belt fabrication services are essential for businesses aiming to optimize their material handling systems. By working with nearby fabricators, companies can ensure timely support and quick adjustments to their conveyor belts, minimizing downtime and maintaining productivity. For example, a manufacturing plant in Ohio reduced its production delays by 30% after partnering with a local conveyor belt fabricator for on-site modifications and repairs.
Benefits of Custom Conveyor Belts: Tailored Solutions, Better Performance, and Longevity
Custom conveyor belt fabrication offers tailored solutions that meet specific operational needs. Businesses benefit from enhanced performance, as the belts are designed to handle particular materials and conditions. Additionally, custom-fabricated belts often have a longer lifespan due to their precise construction. A food processing plant, for instance, saw a 25% increase in efficiency and a significant reduction in maintenance costs after installing custom conveyor belts designed to handle wet and greasy products.
How to Find Reliable Conveyor Belt Fabricators Nearby
Finding reliable conveyor belt fabricators near you involves a few strategic steps:
- Research and Reviews: Start by researching local fabricators and reading customer reviews. Platforms like Google My Business and industry-specific forums can provide valuable insights.
- Certifications and Experience: Look for fabricators with relevant certifications and extensive experience in conveyor belt fabrication. Companies with ISO certifications and a history of successful projects are often more reliable.
- Consultations and Quotes: Schedule consultations to discuss your specific needs and request quotes. Compare the services, costs, and turnaround times to find the best match for your requirements.
Case Studies of Successful Custom Conveyor Belt Projects in Various Industries
- Automotive Industry: A major automotive manufacturer in Detroit collaborated with a local conveyor belt fabricator to design custom belts for their assembly line. The new belts, optimized for durability and precision, led to a 15% increase in production speed and a reduction in downtime.
- Pharmaceutical Industry: A pharmaceutical company in New Jersey needed conveyor belts that could withstand rigorous cleaning protocols. Through custom conveyor belt fabrication, they received belts made from FDA-approved materials, resulting in compliance with health standards and improved production hygiene.
- Agricultural Sector: A farm in Iowa required conveyor belts with cleats to transport bulk grains. The local fabricator provided custom belts that enhanced the farm’s harvesting efficiency by 20%, showcasing the impact of tailored conveyor solutions.
By focusing on custom conveyor belt fabrication, businesses can achieve significant operational improvements, tailored to their unique needs and supported by local expertise.
Comprehensive Conveyor Belt Fabrication Guide
Detailed Process of Conveyor Belt Fabrication
The process of conveyor belt fabrication is intricate and involves multiple steps to ensure that the final product meets specific operational requirements. Each stage is critical in producing a belt that is efficient, durable, and tailored to its intended use.
Material Selection: Fabric, Rubber, Metal, Thermoplastics
Choosing the right material is the first and most crucial step in conveyor belt fabrication. The material selection depends on the application and the environment where the belt will be used:
- Fabric: Commonly used for lightweight and flexible belts, ideal for packaging facilities and grocery stores.
- Rubber: Durable and resistant to wear, rubber belts are often used in mining and heavy industrial applications.
- Metal: Provides high strength and is suitable for heavy-duty applications like automotive manufacturing and food processing.
- Thermoplastics: Offer excellent resistance to chemicals and are used in food handling and pharmaceutical industries.
For instance, a pharmaceutical company may choose thermoplastic belts due to their ease of sterilization and resistance to chemical corrosion, ensuring compliance with health standards.
Design and Engineering: Specifications, Load Capacity, and Environmental Considerations
The design and engineering phase of conveyor belt fabrication involves specifying the belt’s dimensions, load capacity, and environmental requirements. Engineers consider:
- Specifications: The exact width, length, and thickness of the belt.
- Load Capacity: The maximum weight the belt can carry without compromising its integrity.
- Environmental Considerations: Factors such as temperature, humidity, and exposure to chemicals or abrasive materials.
A notable example is a mining operation that requires conveyor belts designed to withstand heavy loads and harsh environmental conditions, ensuring continuous and efficient material transport.
Manufacturing Techniques: Molding, CNC Machining, Welding, Calendering, and Vulcanizing
Various manufacturing techniques are employed in conveyor belt fabrication, each suited to different materials and applications:
- Molding: Used for thermoplastic belts, providing precision and uniformity.
- CNC Machining: Ensures exact specifications for metal components, enhancing durability and performance.
- Welding: Essential for metal belts, ensuring strong and durable joints.
- Calendering: Involves pressing rubber onto fabric layers, creating a robust and flexible belt.
- Vulcanizing: A chemical process that improves the strength and elasticity of rubber belts.
For example, an automotive manufacturer might use CNC machining and welding to produce metal belts that are critical for their high-strength requirements.
Quality Control and Testing Procedures
Quality control is integral to conveyor belt fabrication, ensuring that each belt meets stringent standards:
- Visual Inspections: Checking for defects and inconsistencies.
- Tensile Testing: Measuring the belt’s strength and elasticity.
- Abrasion Resistance Testing: Ensuring the belt can withstand wear and tear.
- Chemical Resistance Testing: For belts used in environments with exposure to chemicals.
An example of stringent quality control is seen in food processing plants, where conveyor belts undergo rigorous testing to meet food safety standards.
Importance of Precision in Conveyor Belt Fabrication for Efficiency and Durability
Precision in conveyor belt fabrication is vital for the belt’s efficiency and durability. Accurate measurements and high-quality materials ensure that the belt performs reliably under operational stresses. Precision fabrication minimizes downtime, reduces maintenance costs, and extends the lifespan of the belt.
For instance, a logistics company that implemented precisely fabricated conveyor belts saw a 20% reduction in maintenance costs and a 15% increase in operational efficiency, underscoring the importance of precision in conveyor belt fabrication.
By following a comprehensive and precise conveyor belt fabrication process, businesses can achieve superior performance and longevity in their conveyor systems, tailored to their specific operational needs.
V-Guide Conveyor Belt Fabrication: Enhancing Precision and Efficiency
Explanation of V-Guide Conveyor Belts and Their Applications
V-guide conveyor belts are designed with v-shaped profiles that run along the underside of the belt, aiding in precise tracking and alignment. These belts are crucial in applications where maintaining the straight path of the belt is essential to avoid misalignment, which can cause operational inefficiencies and increased wear. V-guide conveyor belts are widely used in industries such as packaging, where accurate positioning of goods is critical, and in food processing, where consistent alignment ensures sanitary and efficient handling of products.
Fabrication Process of V-Guide Belts: Adding Profiles to Aid in Tracking
The fabrication process of v-guide conveyor belts involves several key steps:
- Profile Selection: The first step in v-guide conveyor belt fabrication is selecting the appropriate v-guide profile based on the belt’s application and operational requirements. Profiles vary in size and material, commonly made from thermoplastics or rubber.
- Heat Welding: The chosen v-guide profile is then heat-welded or mechanically fastened to the underside of the conveyor belt. This process ensures a strong bond that can withstand the operational stresses of the conveyor system.
- Precision Alignment: During the welding process, precise alignment is critical. Any misalignment can lead to tracking issues, defeating the purpose of the v-guide. Advanced fabrication techniques, such as CNC-guided welding systems, ensure perfect alignment and bonding.
- Quality Control: The final step involves rigorous quality control checks to ensure the v-guide profile is securely attached and the belt operates smoothly without any tracking issues.
For example, a logistics company that implemented v-guide conveyor belt fabrication reported a 40% reduction in belt misalignment incidents, significantly improving their sorting efficiency.
Benefits of V-Guide Belts: Improved Tracking, Reduced Maintenance, and Enhanced Operational Efficiency
V-guide conveyor belts offer several significant advantages:
- Improved Tracking: The primary benefit of v-guide conveyor belt fabrication is enhanced tracking. The v-guide profile keeps the belt centered, preventing lateral movement and reducing the risk of belt misalignment.
- Reduced Maintenance: With improved tracking, there is less wear and tear on the belt and the conveyor system’s components, leading to lower maintenance requirements and costs. A study showed that facilities using v-guide belts experienced a 30% decrease in maintenance expenses.
- Enhanced Operational Efficiency: Consistent and accurate tracking improves overall operational efficiency. Processes that depend on precise movement of materials, such as packaging and assembly lines, benefit from the stability provided by v-guide belts.
Industries That Benefit Most from V-Guide Conveyor Belts: Packaging, Food Processing, and Logistics
Several industries gain substantial benefits from using v-guide conveyor belts:
- Packaging: In packaging operations, precise alignment is crucial for the accurate placement of products and packaging materials. V-guide belts ensure products remain in the correct position throughout the conveyor system.
- Food Processing: The food industry requires conveyor belts that maintain strict hygiene standards while providing reliable performance. V-guide belts prevent misalignment that could cause contamination or inefficient processing.
- Logistics: In logistics and distribution centers, conveyor belts must handle high volumes of packages with accuracy. V-guide conveyor belt fabrication enhances the sorting and handling processes, ensuring smooth and reliable operations.
For instance, a food processing plant that switched to v-guide conveyor belts saw a 25% increase in throughput due to the improved reliability and alignment of the belts, leading to more efficient processing and packaging of food products.
By incorporating v-guide conveyor belt fabrication, industries can achieve greater precision, reduced maintenance, and enhanced efficiency in their material handling processes, demonstrating the critical role of this technology in modern industrial applications.
Precision in Miniature Conveyor Belt Fabrication
Introduction to Miniature Conveyor Belts and Their Uses in Precision Industries
Miniature conveyor belt fabrication is essential for industries requiring precise handling and transportation of small parts and components. These compact conveyor systems are integral in settings where space is limited, and precision is paramount. Industries such as electronics manufacturing, pharmaceutical production, and small parts assembly rely heavily on miniature conveyor belts to enhance efficiency and accuracy in their operations.
Specific Fabrication Techniques for Miniature Conveyor Belts
The fabrication of miniature conveyor belts involves several specialized techniques to ensure accuracy and functionality:
- Micro-Molding: This technique is used to create small, precise components of the conveyor belt. Micro-molding allows for intricate designs and detailed features, essential for miniature belts.
- Laser Cutting: Laser cutting is employed to achieve exact dimensions and smooth edges, which are crucial for the seamless operation of miniature conveyor belts.
- Precision Welding: Welding techniques tailored for small-scale applications ensure that the components are securely joined without compromising the belt’s flexibility and strength.
- Assembly: The assembly of miniature conveyor belts requires meticulous attention to detail. Each part must be perfectly aligned to maintain the belt’s integrity and performance.
For instance, a pharmaceutical company implemented laser-cut miniature conveyor belts to handle delicate capsules, resulting in a 20% increase in packaging accuracy and a 15% reduction in product waste.
Materials Used for Miniature Conveyor Belts: Lightweight and Durable Options
Selecting the right materials is critical in miniature conveyor belt fabrication to ensure the belts are both lightweight and durable:
- Polyurethane: Known for its flexibility and resistance to wear, polyurethane is a popular choice for miniature belts used in high-precision environments.
- Stainless Steel: Stainless steel provides strength and durability, making it ideal for applications that require robust handling of small, heavy components.
- Thermoplastics: These materials offer a balance of lightweight and durability, suitable for miniature belts in electronics and pharmaceutical industries.
For example, a small parts assembly line utilized thermoplastic belts, which resulted in a 30% improvement in assembly speed and reduced downtime due to belt wear.
Examples of Applications: Electronics Manufacturing, Pharmaceutical Production, and Small Parts Assembly
Miniature conveyor belts play a crucial role in several precision-driven industries:
- Electronics Manufacturing: In this sector, miniature conveyor belts are used to transport tiny electronic components such as resistors, capacitors, and microchips. The precision of these belts ensures that delicate parts are handled carefully, reducing the risk of damage and improving assembly line efficiency.
- Pharmaceutical Production: Miniature belts are vital for the accurate and hygienic transport of small pharmaceutical items, including pills and capsules. The belts’ precise movement minimizes contamination risks and ensures that products meet stringent quality standards.
- Small Parts Assembly: In industries like watchmaking or medical device manufacturing, miniature conveyor belts facilitate the assembly of small, intricate parts. These belts enhance the speed and accuracy of the assembly process, leading to higher productivity and fewer errors.
A notable example is an electronics manufacturing plant that incorporated miniature conveyor belts into their production line, achieving a 25% increase in throughput and a 10% reduction in assembly errors, showcasing the effectiveness of precise conveyor belt fabrication.
Miniature conveyor belt fabrication is a specialized field that demands precision, high-quality materials, and advanced fabrication techniques. By employing these belts, industries can achieve significant improvements in efficiency, accuracy, and product quality, underscoring the importance of this technology in precision manufacturing environments.
Robust Industrial Conveyor Belt Fabrication
Overview of Heavy-Duty Industrial Conveyor Belts
Industrial conveyor belt fabrication is a cornerstone of heavy-duty industries, providing the necessary strength and durability to handle demanding applications. These belts are designed to withstand extreme conditions, such as high loads, abrasive materials, and harsh environments. Heavy-duty industrial conveyor belts are essential for efficient material transport in sectors like mining, construction, and bulk material handling.
Fabrication Process for Industrial Conveyor Belts: Robust Materials and Reinforced Structures
The fabrication process of industrial conveyor belts involves the use of robust materials and reinforced structures to ensure longevity and performance:
- Material Selection: Industrial belts are typically made from high-strength materials such as reinforced rubber, steel cord, and high-tensile fabrics. These materials provide the necessary durability and resistance to wear and tear.
- Reinforcement: Adding layers of reinforcement is crucial in industrial conveyor belt fabrication. Steel cords or fabric layers are embedded within the rubber to enhance the belt’s tensile strength and flexibility.
- Vulcanization: This process involves applying heat and pressure to bond the materials together, creating a seamless and durable conveyor belt. Vulcanization ensures that the belt can withstand the rigors of heavy-duty use without delaminating or deteriorating.
- Quality Control: Rigorous testing is conducted to ensure the belts meet industry standards. This includes tensile strength testing, abrasion resistance testing, and checking for uniformity and defects.
For example, a mining operation that switched to industrial conveyor belts fabricated with reinforced rubber and steel cords saw a 35% increase in operational uptime and a 20% reduction in maintenance costs. This improvement is attributed to the enhanced durability of the belts, demonstrating the benefits of investing in high-quality materials for effective mining conveyor belt maintenance.
Customization Options for Industrial Belts: Cleats, Sidewalls, and Lacing
Industrial conveyor belt fabrication often includes customization to meet specific operational needs:
- Cleats: Cleats are added to the belt’s surface to assist in transporting bulk materials uphill or in controlled spacing. They are particularly useful in applications where materials need to be moved at an incline without slipping.
- Sidewalls: Sidewalls are integrated into the belt to prevent materials from spilling over the edges, which is essential in handling loose or granular materials. This customization is crucial for operations in construction and agriculture where bulk handling is common.
- Lacing: Different types of lacing, such as mechanical fasteners or vulcanized splices, are used to join the ends of the belts. Proper lacing ensures seamless operation and quick repairs, minimizing downtime.
For instance, a construction company utilized industrial conveyor belts with customized sidewalls and cleats to efficiently transport sand and gravel to elevated areas on job sites, improving their material handling capacity by 40%.
Applications in Heavy Industries: Mining, Construction, and Bulk Material Handling
Industrial conveyor belt fabrication is integral to several heavy industries, each with unique requirements:
- Mining: Conveyor belts in mining operations transport heavy loads of ore, coal, and other materials. The belts must be exceptionally durable to handle the abrasive nature of the materials and the harsh mining environment. An example is a coal mine that employed industrial conveyor belts with reinforced structures, resulting in a 50% reduction in belt replacements.
- Construction: In the construction industry, conveyor belts are used to move materials like concrete, aggregates, and demolition waste. Customizations such as cleats and sidewalls enhance the belts’ ability to handle these materials efficiently.
- Bulk Material Handling: Industries that manage large volumes of bulk materials, such as agriculture and ports, rely on industrial conveyor belts for efficient transport. These belts ensure the smooth and continuous flow of materials, reducing manual labor and increasing productivity.
A port facility handling bulk grain shipments installed industrial conveyor belts with reinforced structures and customized lacing, achieving a 30% improvement in loading and unloading times.
By incorporating advanced materials and customization options, industrial conveyor belt fabrication addresses the specific challenges of heavy-duty applications, enhancing operational efficiency and durability across various industries.
Comprehensive Conveyor Belt Systems Fabrication
Comprehensive Look at Conveyor Belt Systems and Their Components
Conveyor belt systems fabrication involves creating an integrated system that includes the belt, motors, rollers, and control mechanisms to move materials efficiently. Each component plays a crucial role:
- Belts: The central part of the system, available in various materials like rubber, fabric, and metal, tailored to the specific needs of the industry.
- Motors: Provide the necessary power to move the belt. Motors must be appropriately sized to handle the load requirements.
- Rollers: Support the belt and facilitate smooth movement. They can be made of steel, aluminum, or plastic, depending on the application.
- Control Systems: Include sensors, switches, and automated systems to manage speed, direction, and load distribution, ensuring optimal performance and safety.
For example, a packaging facility might use a conveyor belt system with fabric belts, aluminum rollers, and advanced control systems to handle lightweight packages efficiently.
Designing Conveyor Belt Systems for Efficiency: Layout, Drive Mechanisms, and Safety Features
Designing an efficient conveyor belt system is critical for maximizing productivity and safety:
- Layout: The system’s layout should minimize the distance materials need to travel, reducing time and energy consumption. Strategic placement of curves and inclines can also enhance efficiency.
- Drive Mechanisms: These include direct drives, belt drives, and chain drives. The choice depends on the required speed, load capacity, and environmental conditions. For high-torque applications, direct drives are often preferred.
- Safety Features: Essential for preventing accidents and ensuring smooth operation. Safety features might include emergency stop buttons, guards around moving parts, and sensors that detect and respond to obstructions.
A notable example is a car manufacturing plant that redesigned its conveyor belt system layout to reduce travel distance by 20%, enhancing throughput and reducing energy costs.
Integration of Conveyor Belt Systems into Existing Infrastructure
Integrating new conveyor belt systems into existing infrastructure requires careful planning and execution:
- Compatibility Assessment: Ensuring that new systems are compatible with existing equipment and processes. This might involve customizing belt sizes, speeds, and control systems.
- Installation Planning: Detailed planning to minimize downtime during installation. This includes scheduling work during off-peak hours and having contingency plans in place.
- Testing and Calibration: After installation, the system must be thoroughly tested and calibrated to ensure it meets operational requirements. This includes load testing, speed calibration, and verifying control system integration.
A logistics company successfully integrated a new conveyor belt system into its warehouse, reducing manual handling by 30% and increasing sorting accuracy by 25%.
Case Studies of Conveyor Belt Systems in Large-Scale Operations
Examining real-world applications of conveyor belt systems fabrication can provide valuable insights:
- Mining Industry: A large mining operation implemented a robust conveyor belt system to transport ore over long distances. The system included heavy-duty rubber belts, steel rollers, and automated control systems. This setup increased ore transport efficiency by 40% and reduced labor costs by 35%.
- Food Processing: A food processing plant installed a conveyor belt system with thermoplastic belts and stainless steel rollers to comply with hygiene standards. The system’s automated features improved throughput by 25% and ensured consistent product quality.
- E-commerce Fulfillment Centers: A leading e-commerce company used conveyor belt systems with advanced control systems to manage high volumes of packages. This integration improved order fulfillment speed by 30% and reduced error rates by 15%.
By focusing on comprehensive conveyor belt fabrication, industries can significantly enhance their operational efficiency, safety, and productivity. The tailored design and seamless integration of these systems into existing infrastructures underscore the transformative impact of advanced conveyor belt fabrication.
Precision V-Shaped Conveyor Belt Fabrication
Description of V-Shaped Conveyor Belts and Their Unique Design
V-shaped conveyor belt fabrication involves creating belts with a unique V-shaped profile, designed to improve material handling by enhancing stability and control. The V-shaped design helps center materials on the belt, preventing spillage and ensuring smooth transportation. These belts are particularly useful in applications where maintaining the alignment of transported goods is crucial, such as in bulk material handling and agricultural processes.
Benefits of V-Shaped Conveyor Belts: Stability, Directional Control, and Increased Capacity
V-shaped conveyor belts offer several significant advantages over traditional flat belts:
- Stability: The V-shaped profile ensures that materials remain centered on the belt, reducing the risk of spillage and maintaining a consistent flow. This stability is crucial in operations where precise material handling is required.
- Directional Control: The design provides excellent directional control, making it easier to manage the movement of materials along the conveyor system. This control is beneficial in applications that require precise placement of goods.
- Increased Capacity: The V-shaped design can also increase the belt’s load capacity by better distributing the weight of the materials being transported. This capacity boost is essential in industries handling heavy or bulky items.
For example, an agricultural operation utilizing V-shaped conveyor belt fabrication reported a 30% improvement in the efficiency of grain transport, reducing spillage and increasing throughput.
Fabrication Techniques Specific to V-Shaped Conveyor Belts
Creating V-shaped conveyor belts involves specialized fabrication techniques to ensure the belts meet the necessary performance standards:
- Molding: The V-shaped profile is typically molded into the belt during the manufacturing process. This technique ensures precision and consistency in the belt’s shape.
- Reinforcement: To enhance the durability of the belts, materials such as steel cords or high-tensile fabrics may be embedded within the belt. This reinforcement helps the belt withstand heavy loads and harsh conditions.
- Vulcanization: This process involves heating the belt materials under pressure to create strong, seamless bonds. Vulcanization is critical in ensuring the belt’s durability and longevity.
- Quality Control: Rigorous testing is conducted to verify the belt’s performance. Tests include checking for uniformity, tensile strength, and resistance to abrasion and wear.
A mining company that adopted V-shaped conveyor belt fabrication saw a 25% reduction in maintenance costs due to the enhanced durability and performance of the belts.
Industries and Applications: Agricultural Conveyors, Bulk Material Transport, and Sorting Lines
V-shaped conveyor belts are used across various industries, each benefiting from the unique design and fabrication process:
- Agricultural Conveyors: In agriculture, V-shaped belts are ideal for transporting grains, seeds, and other bulk materials. The stability and increased capacity provided by the V-shaped profile improve efficiency and reduce product loss.
- Bulk Material Transport: Industries that handle bulk materials, such as mining and construction, benefit from V-shaped conveyor belts due to their ability to handle heavy loads and maintain material alignment. This feature is crucial for ensuring continuous and efficient transport.
- Sorting Lines: In sorting operations, V-shaped belts help in accurately positioning items for sorting, reducing errors and increasing processing speed. This application is particularly valuable in logistics and distribution centers.
For instance, a construction company implemented V-shaped conveyor belt fabrication to transport raw materials like sand and gravel. This change led to a 20% increase in transport efficiency and a significant reduction in material spillage.
By focusing on V-shaped conveyor belt fabrication, industries can achieve greater efficiency, stability, and control in their material handling processes. The specialized design and fabrication techniques ensure that these belts meet the rigorous demands of various applications, enhancing overall operational performance.
Dorner Conveyors in Conveyor Belt Fabrication
Introduction to Dorner Conveyors and Their Role in the Industry
Dorner Conveyors is a leading manufacturer in the conveyor belt fabrication industry, known for its innovative solutions and high-quality products. Dorner’s conveyors are widely used across various sectors, providing reliable and efficient material handling systems. Their extensive range of conveyor systems caters to the needs of industries such as manufacturing, packaging, food processing, and pharmaceuticals, helping businesses optimize their operations through advanced conveyor belt fabrication.
Unique Features of Dorner Conveyors: Modular Design, Easy Maintenance, and Versatility
Dorner conveyors stand out in the conveyor belt fabrication market due to several unique features:
- Modular Design: Dorner conveyors are designed with a modular approach, allowing for easy customization and expansion. This design flexibility ensures that conveyor systems can be tailored to meet specific operational requirements and can be easily reconfigured as needs change.
- Easy Maintenance: Maintenance is a critical factor in conveyor belt fabrication, and Dorner conveyors are engineered for ease of maintenance. Features such as tool-less belt changes, quick access to components, and simplified cleaning processes reduce downtime and maintenance costs.
- Versatility: Dorner’s conveyors are versatile and can be used in a wide range of applications. Their systems can handle various products, from small, delicate items to heavy, bulky materials. This versatility makes them suitable for industries with diverse material handling needs.
For instance, a packaging company utilizing Dorner’s modular conveyors reported a 30% increase in production efficiency due to the system’s adaptability and ease of maintenance.
Examples of Dorner Conveyor Systems and Their Applications
Dorner conveyor systems are employed in numerous industries, each benefiting from the specific advantages of these systems:
- Manufacturing: In manufacturing, Dorner conveyors are used for assembly lines, material transport, and packaging processes. Their modular design allows for seamless integration into existing production lines. A car parts manufacturer implemented Dorner conveyors, resulting in a 20% reduction in assembly time and a 15% increase in overall production output.
- Food Processing: Dorner’s conveyors in the food industry are designed to meet stringent hygiene standards, with easy-to-clean surfaces and materials suitable for food contact. A bakery using Dorner conveyors achieved a 25% improvement in throughput and reduced contamination risks due to the system’s hygienic design.
- Pharmaceuticals: In the pharmaceutical sector, precision and cleanliness are paramount. Dorner conveyors are used to transport delicate items such as pills and vials, ensuring they remain uncontaminated and precisely handled. A pharmaceutical company saw a 20% increase in packaging accuracy and efficiency after installing Dorner conveyor systems.
How Dorner Conveyors Contribute to Efficient Conveyor Belt Fabrication
Dorner conveyors significantly contribute to the efficiency of conveyor belt fabrication through their innovative design and functionality:
- Improved Fabrication Processes: The modular design of Dorner conveyors simplifies the fabrication process, allowing for quicker assembly and customization. This efficiency translates into faster deployment and reduced production times.
- Enhanced Durability: Dorner’s focus on high-quality materials and construction methods ensures that their conveyors are durable and reliable, reducing the frequency of repairs and replacements. This durability is crucial for maintaining continuous operation in demanding industrial environments.
- Operational Efficiency: By incorporating advanced features such as tool-less belt changes and easy-to-clean designs, Dorner conveyors help minimize downtime and maximize productivity. This operational efficiency is essential for businesses looking to streamline their material handling processes.
For example, a logistics center that adopted Dorner conveyor systems experienced a 15% reduction in maintenance downtime and a 10% increase in package handling capacity, demonstrating the tangible benefits of efficient conveyor belt fabrication.
Dorner conveyors play a pivotal role in the conveyor belt fabrication industry by providing innovative, reliable, and versatile solutions. Their unique features and proven performance in various applications underscore their contribution to enhancing operational efficiency and productivity across multiple sectors.
FAQs about Conveyor Belt Fabrication
Conveyor belt fabrication involves several intricate steps to ensure that the final product meets the specific requirements of the application. The process begins with the selection of materials, which can include rubber, fabric, metal, and thermoplastics. These materials are chosen based on the belt’s intended use and environmental conditions. After material selection, the design and engineering phase specifies the belt’s dimensions, load capacity, and other critical factors. Manufacturing techniques such as molding, CNC machining, welding, calendering, and vulcanizing are then employed to create the belt. Each method is suited to different materials and applications, ensuring precision and durability. Quality control measures, including visual inspections and tensile testing, are conducted to verify the belt’s performance. The final step involves customizing the belt with features like cleats, sidewalls, and lacing to meet specific operational needs. This comprehensive process ensures that the conveyor belt is robust, reliable, and perfectly suited to its intended application.
Conveyor belts are built by specialized companies that focus on conveyor belt fabrication, ensuring they meet industry standards and specific customer requirements. These companies employ skilled engineers and technicians who design and manufacture conveyor belts using advanced techniques and high-quality materials. Leading conveyor belt fabricators include Swanton Welding, which is renowned for its custom metal belts, and Dorner Conveyors, known for its modular and versatile conveyor systems. These manufacturers work closely with clients to understand their operational needs, providing tailored solutions that enhance efficiency and productivity. They utilize state-of-the-art equipment and adhere to strict quality control measures to produce durable and reliable conveyor belts. By partnering with reputable conveyor belt fabricators, businesses can ensure they receive high-performance belts designed to withstand demanding applications and environmental conditions.
Industry conveyor belts are manufactured by companies specializing in conveyor belt fabrication, offering robust solutions for various industrial applications. These manufacturers, such as Continental Belting and Fenner Dunlop, provide high-strength conveyor belts designed to handle heavy loads and harsh environments. The fabrication process involves selecting durable materials like reinforced rubber, steel cords, and high-tensile fabrics, ensuring the belts’ longevity and performance. Reinforcement techniques, such as embedding steel cords or fabric layers within the rubber, enhance the belts’ tensile strength and flexibility. Manufacturers also employ advanced processes like vulcanization to bond materials together, creating seamless and durable belts. Quality control tests, including tensile strength and abrasion resistance testing, ensure the belts meet industry standards. By choosing experienced industry conveyor belt fabricators, businesses can obtain reliable and efficient conveyor solutions tailored to their specific operational needs.
The best software for belt conveyor design in conveyor belt fabrication is essential for creating efficient and reliable conveyor systems. Belt Analyst by Overland Conveyor is one of the most popular engineering software tools for this purpose. It offers dynamic analysis capabilities, allowing engineers to simulate various operational conditions and optimize the conveyor belt design accordingly. The software provides features for calculating belt tensions, power requirements, and other critical parameters, ensuring the belt’s performance and longevity. Additionally, Bulk Flow Analyst uses the Discrete Element Method (DEM) to simulate bulk material flow, helping engineers test and refine material handling scenarios before implementation. These tools are invaluable in the conveyor belt fabrication process, enabling precise design and engineering that meets specific operational requirements. By using advanced software, fabricators can ensure their conveyor belts are optimized for efficiency, reliability, and durability in various industrial applications.
Last Updated on May 17, 2024 by Jordan Smith
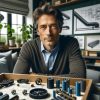
Jordan Smith, a seasoned professional with over 20 years of experience in the conveyor system industry. Jordan’s expertise lies in providing comprehensive solutions for conveyor rollers, belts, and accessories, catering to a wide range of industrial needs. From initial design and configuration to installation and meticulous troubleshooting, Jordan is adept at handling all aspects of conveyor system management. Whether you’re looking to upgrade your production line with efficient conveyor belts, require custom conveyor rollers for specific operations, or need expert advice on selecting the right conveyor accessories for your facility, Jordan is your reliable consultant. For any inquiries or assistance with conveyor system optimization, Jordan is available to share his wealth of knowledge and experience. Feel free to reach out at any time for professional guidance on all matters related to conveyor rollers, belts, and accessories.