Safety Measures for Conveyor Belt in Steel Plant
Conveyor belts play a critical role in steel plants, facilitating the efficient movement of raw materials and finished products throughout the production process. In steel plants, conveyor belts are essential for transporting materials such as iron ore, coal, and scrap metal to various stages of production, including blast furnaces, smelters, and rolling mills. This seamless transportation system minimizes manual handling, reduces labor costs, and significantly enhances operational efficiency. The importance of conveyor belt in steel plant cannot be overstated, as they ensure a continuous flow of materials, streamline production processes, and contribute to the overall productivity and profitability of steel manufacturing operations.
Types of Used Conveyor Belt in Steel Plant
General Purpose Belts
General purpose belts are the most commonly used type of conveyor belt in steel plants. These belts are designed to handle a variety of materials, making them versatile and widely applicable across different stages of the steel production process. General purpose belts are typically made from a combination of rubber and synthetic materials, providing a balance of durability, flexibility, and cost-effectiveness. They are used to transport materials such as iron ore, coal, limestone, and other raw materials from storage areas to processing units.
These belts are engineered to withstand moderate levels of abrasion and impact, ensuring longevity and reliable performance. Additionally, general purpose belts can be customized with features such as increased thickness, additional layers, and specialized coatings to meet specific operational requirements in steel plants.
Heat-Resistant Belts
Steel production involves high-temperature processes, such as those found in blast furnaces and hot rolling mills. Heat-resistant conveyor belts are specifically designed to withstand these extreme temperatures without compromising their structural integrity. These belts are constructed from heat-resistant materials, such as special rubber compounds and reinforced fabrics, which can endure temperatures ranging from 100°C to 200°C, and in some cases, even higher.
Heat-resistant conveyor belts are crucial for transporting hot materials, including molten steel, hot slag, and other high-temperature by-products. Their ability to maintain performance under intense heat conditions helps prevent belt degradation, reduces maintenance costs, and ensures a safer working environment. These belts are essential for operations where prolonged exposure to high temperatures is a common occurrence.
Fire-Resistant Belts
Fire-resistant conveyor belts are another critical type used in steel plants, particularly in areas where there is a risk of fire or explosion. These belts are made from flame-retardant materials that help prevent the spread of fire and minimize the release of toxic fumes. Fire-resistant belts are essential for the safe transportation of materials in environments such as coal storage areas, coke ovens, and other high-risk zones within steel plants.
The use of fire-resistant belts enhances workplace safety by reducing the risk of fire-related incidents. They are designed to meet stringent safety standards and regulations, ensuring compliance with industry requirements. By incorporating fire-resistant conveyor belts, steel plants can mitigate the potential hazards associated with flammable materials and improve overall operational safety.
Oil-Resistant Belts
Oil-resistant conveyor belts are specifically engineered to handle materials that contain oils and other hydrocarbons. In steel plants, these belts are used in areas where materials such as coke, coal, and oil-contaminated scrap metal are transported. Exposure to oils can cause conventional conveyor belts to deteriorate, leading to increased maintenance and replacement costs.
Oil-resistant belts are made from special rubber compounds that resist the damaging effects of oils and greases. This resistance extends the life of the belts, reduces maintenance downtime, and ensures continuous operation. By using oil-resistant belts, steel plants can maintain efficient material handling processes and prevent the operational disruptions caused by belt degradation.
Abrasion-Resistant Belts
The handling of abrasive materials is a common challenge in steel plants. Abrasion-resistant conveyor belts are designed to withstand the wear and tear caused by transporting hard and sharp materials such as iron ore, scrap metal, and slag. These belts are constructed from durable materials that provide enhanced resistance to abrasion and impact.
Abrasion-resistant belts are essential for maintaining the longevity and reliability of conveyor systems in steel plants. They help reduce the frequency of belt replacements, lower maintenance costs, and ensure the continuous flow of materials. By using abrasion-resistant belts, steel plants can achieve higher productivity and operational efficiency.
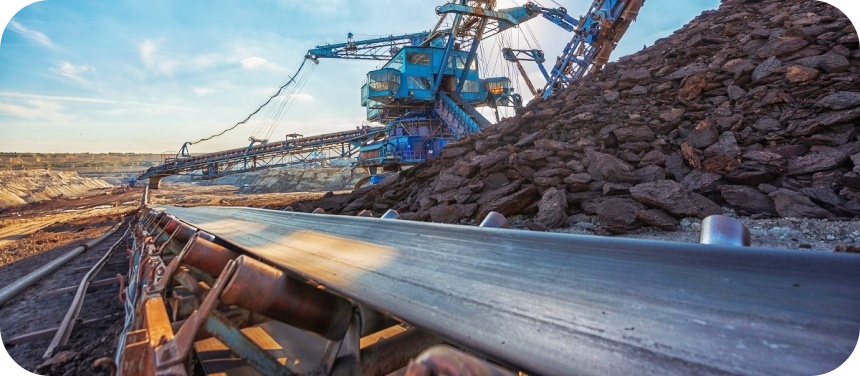
High-Capacity Belts
Steel plants often require the transportation of large volumes of materials over long distances. High-capacity conveyor belts are designed to handle these demanding requirements. These belts feature increased width and thickness, allowing them to carry heavier loads without compromising performance.
High-capacity belts are used in applications such as transporting raw materials from storage yards to processing units and moving finished products to shipping areas. Their robust construction and ability to handle large volumes of materials make them indispensable for high-demand operations in steel plants. By using high-capacity belts, steel plants can streamline their material handling processes and enhance overall productivity.
Chevron Belts
Chevron belts are a specialized type of conveyor belt used in steel plants for transporting materials on inclined surfaces. These belts feature a unique chevron pattern that provides increased grip and prevents materials from sliding backward. Chevron belts are ideal for applications where materials need to be moved vertically or on steep inclines.
In steel plants, chevron belts are used to transport materials such as iron ore, coal, and coke from ground level to elevated processing units. The chevron pattern ensures stable and efficient transportation, reducing the risk of material spillage and enhancing operational safety. By using chevron belts, steel plants can optimize their vertical material handling processes and improve overall efficiency.
Cleated Belts
Cleated conveyor belts are designed with raised sections, or cleats, that help to secure and transport materials on inclined or horizontal surfaces. These belts are used in steel plants to move bulk materials such as pellets, sinter, and scrap metal. The cleats provide additional grip and prevent materials from rolling or sliding off the belt.
Cleated belts are particularly useful in applications where precise material placement is required, such as feeding materials into processing units or transporting materials to storage areas. The design of cleated belts ensures efficient and reliable material handling, reducing the risk of spillage and improving overall productivity.
Magnetic Separator Belts
Magnetic separator belts are used in steel plants to separate ferrous materials from other materials during the transportation process. These belts are equipped with magnets that attract and remove metallic contaminants, ensuring that only clean materials are transported to the next stage of production.
In steel plants, magnetic separator belts are used in applications such as removing tramp metal from coal, iron ore, and scrap metal. The use of magnetic separator belts helps prevent damage to processing equipment, reduces downtime, and ensures the quality of the final product. By incorporating magnetic separator belts, steel plants can enhance the efficiency and safety of their material handling processes.
The various types of conveyor belts used in steel plants play a crucial role in optimizing material handling processes, enhancing operational efficiency, and ensuring workplace safety. Each type of conveyor belt is designed to meet specific operational requirements, providing tailored solutions for the diverse challenges faced by steel plants. By understanding the features and applications of these conveyor belts, steel plants can make informed decisions that contribute to the overall productivity and success of their operations.
Installation of Conveyor Belt in Steel Plant
The installation of a conveyor belt in steel plants is a meticulous process that demands careful planning and execution. Conveyor belts are integral to the efficient operation of steel plants, as they facilitate the continuous movement of raw materials and finished products throughout the facility. Ensuring the proper installation of these belts is crucial to prevent downtime, minimize maintenance costs, and enhance the overall productivity of the plant.
Process and Considerations for Installing Conveyor Belts in Steel Plants
- Site Preparation and Planning:
- Before installation, a thorough site survey is conducted to understand the layout, space constraints, and specific requirements of the steel plant. This involves measuring the dimensions and identifying potential obstacles that could affect the installation process.
- Detailed planning includes designing the conveyor belt system to fit seamlessly into the existing infrastructure, considering factors such as load capacity, belt speed, and material characteristics.
- Selection of Conveyor Belt:
- Choosing the right type of conveyor belt is essential for the efficient operation of a steel plant. Factors such as the type of material to be transported, temperature conditions, and the required durability are taken into account.
- Steel plants often use heat-resistant belts due to the high temperatures involved in the production process. Additionally, belts with high tensile strength and abrasion resistance are preferred to handle the heavy and abrasive nature of raw materials like iron ore and coal.
- Structural Support and Alignment:
- The conveyor belt system requires a robust support structure to withstand the heavy loads and constant movement. This includes the installation of frames, rollers, and idlers that provide stability and smooth operation.
- Proper alignment of the conveyor belt is critical to prevent belt slippage, uneven wear, and potential breakdowns. Alignment tools and techniques, such as laser alignment, are employed to ensure precision.
- Installation of Drive Units and Controls:
- The drive units, including motors and gearboxes, are installed to provide the necessary power to move the conveyor belt. These units must be securely mounted and aligned with the belt to ensure efficient power transmission.
- Advanced control systems, including sensors and automation, are integrated to monitor the operation of the conveyor belt. These systems help in regulating speed, detecting malfunctions, and ensuring safety.
- Splicing and Joining the Belt:
- Splicing is the process of joining the ends of the conveyor belt to form a continuous loop. This can be done through mechanical fasteners, vulcanization, or cold bonding, depending on the type of belt and operational requirements.
- Vulcanized splices are commonly used in steel plants due to their strength and durability. The process involves applying heat and pressure to bond the belt ends together, creating a seamless and robust joint.
- Testing and Commissioning:
- After installation, the conveyor belt system undergoes rigorous testing to ensure it operates as intended. This includes running the belt under load conditions, checking for alignment issues, and verifying the performance of the drive units and control systems.
- Any issues identified during testing are addressed promptly to prevent future problems. Once the system passes all tests, it is commissioned for regular operation.
Key Factors to Ensure Proper Installation
- Expertise and Experience:
- Hiring experienced professionals with expertise in conveyor belt installation is crucial. These experts are familiar with the specific challenges and requirements of installing conveyor belts in steel plants and can ensure a high-quality installation.
- Quality Materials and Components:
- Using high-quality materials and components for the conveyor belt system enhances its durability and performance. This includes selecting reputable suppliers for belts, rollers, drive units, and other critical parts.
- Safety Measures:
- Safety is a top priority during the installation process. Proper safety protocols, including the use of personal protective equipment (PPE), securing the installation area, and following safety standards, are essential to prevent accidents and injuries.
- Regular Inspections and Adjustments:
- Conducting regular inspections during and after installation helps identify potential issues early. Adjustments to alignment, tension, and other parameters ensure the conveyor belt operates smoothly and efficiently.
- Documentation and Training:
- Comprehensive documentation of the installation process, including diagrams, specifications, and maintenance guidelines, is vital for future reference. Additionally, training the plant personnel on the operation and maintenance of the conveyor belt system ensures its longevity and optimal performance.
Maintenance of Conveyor Belt in Steel Plant
Routine maintenance of conveyor belts in steel plants is essential to ensure their longevity and optimal performance. Given the harsh operating conditions in steel plants, regular maintenance helps prevent unexpected breakdowns, reduce downtime, and maintain the efficiency of the production process.
Routine Maintenance Practices for Conveyor Belts in Steel Plants
- Regular Inspections:
- Conducting regular inspections is the cornerstone of conveyor belt maintenance. Inspections should focus on identifying signs of wear and tear, misalignment, and any damage to the belt or its components.
- Inspections should be carried out on a scheduled basis, with more frequent checks during peak production periods. This proactive approach helps in detecting potential issues early and addressing them before they escalate.
- Belt Tension and Alignment:
- Maintaining proper belt tension is critical for the efficient operation of the conveyor belt. Too much tension can cause excessive wear and reduce the lifespan of the belt, while too little tension can lead to slippage and misalignment.
- Regularly checking and adjusting the alignment of the conveyor belt ensures it runs smoothly and reduces the risk of damage. Misalignment can cause uneven wear, increase energy consumption, and lead to belt failure.
- Lubrication of Moving Parts:
- Lubricating the moving parts of the conveyor belt system, such as rollers, bearings, and drive units, minimizes friction and wear. Using the appropriate type and amount of lubricant is essential to prevent contamination and ensure smooth operation.
- Regular lubrication schedules should be established and strictly followed to maintain the efficiency of the conveyor belt system.
- Cleaning and Debris Removal:
- Keeping the conveyor belt and its components clean is vital for their longevity. Accumulated debris and material build-up can cause blockages, increase wear, and reduce the efficiency of the conveyor system.
- Regular cleaning routines, including the use of specialized cleaning equipment and methods, help in maintaining the cleanliness of the conveyor belt. This includes cleaning the belt surface, rollers, and other components.
- Replacement of Worn or Damaged Parts:
- Timely replacement of worn or damaged parts is crucial to prevent breakdowns and ensure the continuous operation of the conveyor belt. This includes replacing worn belts, rollers, bearings, and other critical components.
- Maintaining an inventory of spare parts and having a replacement schedule helps in minimizing downtime and ensures the availability of essential parts when needed.
- Monitoring Systems and Automation:
- Implementing monitoring systems and automation can significantly enhance the maintenance process. Sensors and automated controls can provide real-time data on the condition of the conveyor belt, alerting maintenance personnel to potential issues.
- Advanced monitoring systems can track parameters such as belt tension, alignment, temperature, and vibration, enabling predictive maintenance and reducing the risk of unexpected failures.
Importance of Regular Maintenance for Optimal Performance
- Prevention of Downtime:
- Regular maintenance helps in preventing unexpected breakdowns and downtime, which can significantly impact the production process in a steel plant. By addressing potential issues early, maintenance ensures the continuous and efficient operation of the conveyor belt system.
- Cost Savings:
- Proactive maintenance reduces the need for costly repairs and replacements. By extending the lifespan of the conveyor belt and its components, regular maintenance minimizes the overall operational costs and enhances the return on investment.
- Enhanced Safety:
- Well-maintained conveyor belts contribute to a safer working environment. Regular maintenance helps in identifying and addressing safety hazards, such as worn belts, misaligned components, and malfunctioning drive units, reducing the risk of accidents and injuries.
- Improved Efficiency:
- A properly maintained conveyor belt operates more efficiently, reducing energy consumption and improving the overall productivity of the steel plant. Regular maintenance ensures that the conveyor belt system performs at its optimal level, handling materials smoothly and reliably.
- Compliance with Standards:
- Adhering to maintenance standards and best practices ensures compliance with industry regulations and standards. This not only enhances the reliability and performance of the conveyor belt system but also supports the plant’s commitment to quality and safety.
The installation and maintenance of conveyor belts in steel plants are critical processes that require careful planning, execution, and ongoing attention. By following best practices and investing in regular maintenance, steel plants can ensure the longevity, efficiency, and safety of their conveyor belt systems, ultimately contributing to the overall success and productivity of the plant.
Safety Measures for Conveyor Belt in Steel Plant
The implementation of safety measures for conveyor belts in steel plants is crucial to protect workers, maintain operational efficiency, and prevent costly accidents. Conveyor belts in steel plants handle heavy and often hazardous materials, making the adherence to safety protocols a top priority. This section delves into essential safety protocols and common safety challenges, providing a comprehensive guide to ensuring a safe working environment.
Essential Safety Protocols for Operating Conveyor Belts in Steel Plants
- Employee Training and Education:
- Comprehensive training programs are essential for all personnel operating and maintaining conveyor belts in steel plants. These programs should cover the correct usage of equipment, recognition of potential hazards, and emergency response procedures.
- Regular refresher courses and safety drills help reinforce the importance of safety measures and keep workers updated on any new safety protocols or equipment.
- Safety Guards and Barriers:
- Installing physical guards and barriers around conveyor belts can prevent accidental contact with moving parts. These protective measures are critical in areas where employees are likely to be close to the belt.
- Safety barriers should be regularly inspected and maintained to ensure they remain effective.
- Emergency Stop Systems:
- Emergency stop systems must be easily accessible along the entire length of the conveyor belt. These systems allow workers to quickly halt the belt in case of an emergency, such as entanglement or mechanical failure.
- Regular testing and maintenance of emergency stop systems ensure they function correctly when needed.
- Regular Maintenance and Inspections:
- Conducting regular maintenance and inspections of conveyor belts helps identify potential safety issues before they become critical. This includes checking for wear and tear, alignment issues, and proper functioning of safety devices.
- Maintenance logs should be kept up-to-date to track the condition of the conveyor belt system and schedule necessary repairs.
- Use of Personal Protective Equipment (PPE):
- Workers should be provided with and trained in the use of appropriate personal protective equipment (PPE), including gloves, hard hats, safety glasses, and steel-toed boots. PPE helps protect workers from injuries caused by moving parts, falling materials, and other hazards.
- Regular checks should be conducted to ensure PPE is in good condition and worn correctly by all personnel.
- Safe Work Procedures:
- Developing and enforcing safe work procedures for tasks involving conveyor belts helps minimize risks. Procedures should include guidelines for starting and stopping the belt, clearing blockages, and handling materials safely.
- Clear signage and instructions should be posted in areas where conveyor belts are in operation to remind workers of safe practices.
Common Safety Challenges and How to Address Them
- Entanglement and Crushing Hazards:
- Conveyor belts pose a significant risk of entanglement and crushing, especially in areas where belts intersect or move materials. To address this, ensure that all nip points and pinch points are guarded and that workers are trained to keep clear of these areas.
- Lockout/tagout (LOTO) procedures should be strictly followed during maintenance to prevent accidental start-up of the belt.
- Dust and Fume Exposure:
- The handling of materials in steel plants can generate dust and fumes, which pose health risks to workers. Implementing proper ventilation systems and dust suppression methods, such as water sprays or dust collectors, can help mitigate these risks.
- Workers should be equipped with respiratory protection when working in areas with high dust or fume concentrations.
- Fire and Explosion Risks:
- The presence of combustible materials and high temperatures in steel plants increases the risk of fires and explosions. Conveyor belts should be made of fire-resistant materials, and fire detection and suppression systems should be installed.
- Regular fire safety drills and training help ensure workers know how to respond in case of a fire emergency.
- Mechanical Failures:
- Mechanical failures, such as belt breakage or motor malfunctions, can lead to accidents and injuries. Regular inspections and preventative maintenance are crucial to identify and address potential mechanical issues before they result in accidents.
- Implementing condition monitoring systems can provide real-time data on the health of the conveyor belt system, allowing for timely interventions.
- Slips, Trips, and Falls:
- Slips, trips, and falls are common hazards in steel plants, especially around conveyor belts. Keeping work areas clean and free of debris, providing adequate lighting, and using anti-slip flooring can help reduce these risks.
- Workers should be trained to recognize and report potential hazards that could cause slips, trips, or falls.
By implementing these safety measures and addressing common safety challenges, steel plants can create a safer working environment for their employees, ensuring the efficient and safe operation of conveyor belts.
Innovations in Conveyor Belt in Steel Plant
Technological advancements have significantly transformed the design and functionality of conveyor belt in steel plant. These innovations aim to enhance efficiency, safety, and overall productivity. This section explores the latest technological advancements in conveyor belts and their benefits for steel production efficiency.
Latest Technological Advancements in Conveyor Belts for Steel Plants
- Smart Conveyor Systems:
- Smart conveyor systems equipped with sensors and Internet of Things (IoT) technology allow real-time monitoring and data collection. These systems can track various parameters such as belt speed, load, temperature, and wear, providing valuable insights for predictive maintenance and operational optimization.
- Automated alerts and diagnostics help identify potential issues early, reducing downtime and maintenance costs.
- Energy-Efficient Belts:
- Innovations in material science have led to the development of energy-efficient conveyor belts that require less power to operate. These belts are designed to reduce friction and rolling resistance, resulting in lower energy consumption and operational costs.
- Energy-efficient belts also contribute to reducing the carbon footprint of steel plants, aligning with sustainability goals.
- Heat-Resistant Belts:
- Given the high temperatures involved in steel production, heat-resistant conveyor belts are essential. Advanced heat-resistant materials, such as aramid and ceramic composites, offer superior performance and durability in extreme temperature conditions.
- These belts maintain their structural integrity and efficiency, reducing the need for frequent replacements and minimizing downtime.
- Modular Belt Systems:
- Modular belt systems consist of interlocking modules that can be easily replaced or reconfigured. This modularity enhances the flexibility of conveyor systems, allowing for quick repairs and adjustments without significant downtime.
- Modular belts are also easier to clean and maintain, improving overall hygiene and reducing maintenance efforts.
- Automated Material Handling:
- Integration of automated material handling technologies, such as robotic arms and automated guided vehicles (AGVs), with conveyor belts enhances the efficiency and precision of material transport. These systems can handle complex tasks, such as sorting, stacking, and loading, with minimal human intervention.
- Automation reduces the risk of human error, increases throughput, and ensures consistent quality in material handling.
- Advanced Belt Cleaning Systems:
- Advanced belt cleaning systems utilize innovative scrapers, brushes, and wash systems to keep conveyor belts free of material build-up. These systems improve belt performance, reduce wear, and extend the lifespan of the conveyor belt.
- Effective cleaning systems also help maintain product quality and prevent contamination in the production process.
Benefits of These Innovations for Steel Production Efficiency
- Increased Productivity:
- Innovations in conveyor belt technology enhance the speed and reliability of material transport, directly contributing to increased productivity in steel plants. Automated systems and real-time monitoring ensure smooth operations and quick responses to any disruptions.
- Improved belt performance and reduced downtime allow steel plants to operate at higher efficiency levels, meeting production targets more consistently.
- Enhanced Safety:
- Advanced safety features integrated into modern conveyor belts, such as emergency stop systems, automatic shutdowns, and real-time monitoring, significantly enhance workplace safety. These features help prevent accidents and protect workers from potential hazards.
- Automation and remote monitoring reduce the need for workers to be in close proximity to moving parts, further enhancing safety.
- Cost Savings:
- Energy-efficient belts and predictive maintenance systems contribute to significant cost savings by reducing energy consumption and minimizing unplanned maintenance. The longevity of advanced conveyor belts also means fewer replacements and lower maintenance costs.
- Automation reduces labor costs and increases operational efficiency, providing a higher return on investment for steel plants.
- Sustainability:
- Innovations in conveyor belt technology support sustainability initiatives by reducing energy consumption and carbon emissions. Energy-efficient and durable belts minimize environmental impact and contribute to the overall sustainability goals of steel plants.
- Advanced cleaning systems reduce water and chemical usage, further enhancing the environmental performance of steel production processes.
- Improved Quality Control:
- Automated and smart conveyor systems provide better control over material handling processes, ensuring consistent quality and reducing the risk of defects. Real-time data collection and monitoring enable steel plants to maintain high standards and quickly address any quality issues.
- Consistent and precise material handling contributes to the production of high-quality steel products, meeting customer expectations and industry standards.
In the context of conveyor belt in steel plant, the latest innovations in conveyor belts for steel plants offer numerous benefits, including increased productivity, enhanced safety, cost savings, sustainability, and improved quality control. By embracing these advancements, steel plants can optimize their operations, reduce risks, and achieve higher levels of efficiency and competitiveness in the industry.
Complete the form to receive expert advice on the best conveyor belt for you.
FAQs about Conveyor Belt in Steel Plant
In the context of conveyor belts, “ply” refers to the layers of fabric or synthetic material embedded within the belt. These layers are integral to the belt’s structure, providing the necessary strength, durability, and flexibility. Typically, each ply is made from materials like polyester, nylon, or cotton, bonded together with rubber or other compounds. The number of plies indicates the belt’s overall strength and thickness; more plies generally mean a sturdier and thicker belt. Ply plays a crucial role in determining the belt’s performance, with each ply contributing to its tensile strength and ability to handle heavy loads and harsh conditions.
The primary difference between 2 ply and 3 ply conveyor belts lies in the number of fabric layers they contain. A 2 ply conveyor belt has two layers of fabric, while a 3 ply belt has three. This additional layer in 3 ply belts provides extra strength, durability, and resistance to wear and tear. As a result, 3 ply belts are better suited for more demanding applications where higher tensile strength and load-bearing capacity are required. They also offer better resistance to punctures and cuts, making them ideal for industries with harsh operating conditions. In contrast, 2 ply belts are lighter and more flexible, suitable for less strenuous tasks.
The thickness of a 3 ply conveyor belt varies depending on the specific requirements and design specifications. Generally, a 3 ply conveyor belt can range from 5mm to 10mm in thickness. The exact thickness depends on the types of materials used in each ply and the intended application of the belt. Thicker belts offer increased strength and durability, making them suitable for heavy-duty tasks and environments with significant wear and tear. Conversely, thinner 3 ply belts may be used in applications requiring more flexibility and less load-bearing capacity. Always refer to the manufacturer’s specifications for precise measurements.
The strongest conveyor belts are typically made from reinforced materials and feature multiple plies or layers. Steel cord conveyor belts are considered the strongest, due to their high tensile strength and resistance to impact, cuts, and abrasions. These belts are reinforced with steel cables, providing exceptional durability and performance in heavy-duty applications such as mining, quarrying, and bulk material handling. Additionally, high-quality multi-ply belts with special synthetic fabric reinforcements can also offer substantial strength and durability. The specific strength of a conveyor belt depends on its construction, materials, and intended use, but steel cord belts are generally recognized as the most robust option available.
Last Updated on August 9, 2024 by Jordan Smith
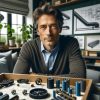
Jordan Smith, a seasoned professional with over 20 years of experience in the conveyor system industry. Jordan’s expertise lies in providing comprehensive solutions for conveyor rollers, belts, and accessories, catering to a wide range of industrial needs. From initial design and configuration to installation and meticulous troubleshooting, Jordan is adept at handling all aspects of conveyor system management. Whether you’re looking to upgrade your production line with efficient conveyor belts, require custom conveyor rollers for specific operations, or need expert advice on selecting the right conveyor accessories for your facility, Jordan is your reliable consultant. For any inquiries or assistance with conveyor system optimization, Jordan is available to share his wealth of knowledge and experience. Feel free to reach out at any time for professional guidance on all matters related to conveyor rollers, belts, and accessories.