Conveyor Belt in Underground Mining: Key Selection
The importance of conveyor systems in underground mining cannot be overstated. Conveyor belt in underground mining plays a pivotal role in enhancing the efficiency of mining operations. These belts are critical for the transportation of extracted materials, ensuring a continuous flow from the mining site to the surface. By reducing the need for manual labor and minimizing transportation time, conveyor belts significantly boost productivity. Moreover, the reliability and durability of conveyor belt in underground mining ensure that operations run smoothly and without interruption, making them indispensable to modern mining practices. This system not only optimizes operational efficiency but also contributes to the safety and sustainability of underground mining activities.
Types of Conveyor Belt in Underground Mining
Conveyor belts are essential components in the mining industry, particularly in underground mining operations. Each type of conveyor belt is designed to handle specific conditions and materials, ensuring the smooth and efficient transport of minerals. In this section, we will discuss and compare various types of conveyor belts used in underground mining, focusing on multi-ply belts, straight-warp belts, steel-cord belts, and solid woven belts.
Multi-ply Belts
Multi-ply belts are one of the most common types of conveyor belts used in underground mining. These belts consist of multiple layers of fabric, typically made from polyester, nylon, or cotton, with rubber coatings on both sides. The multiple layers provide additional strength and durability, making these belts suitable for heavy-duty applications.
Straight-warp Belts
Straight-warp belts are designed with a single layer of straight-warped fabric, offering high strength and resistance to impact. This unique construction makes straight-warp belts an excellent choice for high-impact and heavy-load applications in underground mining.
Steel-cord Belts
Steel-cord belts are reinforced with steel cables, providing exceptional strength and durability. These belts are designed to handle the most demanding underground mining applications, including the transportation of heavy and abrasive materials over long distances.
Solid Woven Belts
Solid woven belts are made from a single, continuous piece of woven fabric, typically coated with PVC or rubber. These belts are known for their exceptional strength and resistance to moisture, making them ideal for wet and humid underground mining environments.
Understanding the different types of conveyor belts in underground mining is crucial for selecting the right belt for specific mining conditions. Each type of belt offers unique advantages and disadvantages, and the choice depends on factors such as the material being transported, the layout of the mining operation, and the environmental conditions. By selecting the appropriate conveyor belt, mining operations can achieve greater efficiency, safety, and longevity in their conveyor systems.
Types of Conveyor Belt in Underground Mining
The Different Types of Conveyor Belts Based on Material, Structure, and Mining Application
The selection of a conveyor belt in underground mining is crucial for optimizing the efficiency, safety, and productivity of mining operations. Different types of conveyor belts are used based on the material they are made from, their structural composition, and their specific applications in mining environments. Here, we explore five distinct types of conveyor belts commonly used in underground mining.
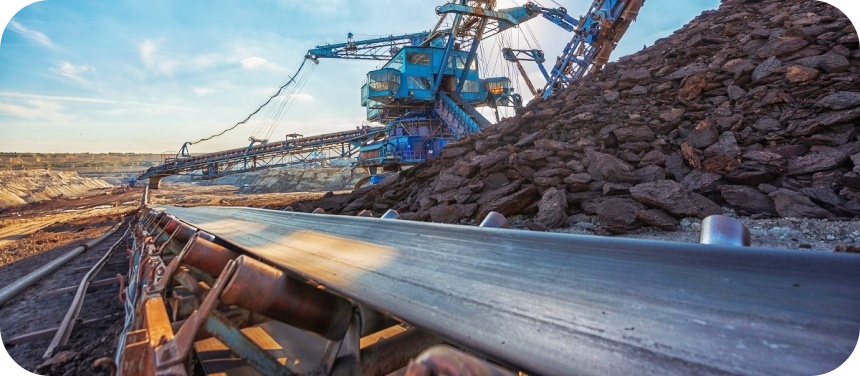
1. Multi-ply Conveyor Belts
Multi-ply conveyor belts are composed of multiple layers of fabric, usually made from polyester, nylon, or cotton, which are bonded together with rubber. These layers, or plies, provide added strength and durability, making these belts suitable for heavy-duty applications in underground mining.
Key Features:
- Material: Polyester, nylon, or cotton fabric layers with rubber coating.
- Structure: Multiple plies (layers) bonded together.
- Application: Suitable for transporting heavy loads and materials over long distances.
Advantages:
- High tensile strength due to multiple layers.
- Good flexibility, allowing for use in systems with sharp bends and inclines.
- Cost-effective compared to other high-strength belts.
Disadvantages:
- Increased weight due to multiple layers.
- Requires regular maintenance to prevent layer separation.
2. Steel-Cord Conveyor Belts
Steel-cord conveyor belts are reinforced with steel cables, providing exceptional tensile strength and durability. These belts are designed to handle the most demanding underground mining applications, including the transport of heavy and abrasive materials over long distances.
Key Features:
- Material: Steel cables embedded within rubber.
- Structure: Steel cords running parallel to the belt’s length.
- Application: Ideal for heavy-duty and high-impact applications.
Advantages:
- Superior tensile strength and durability.
- Low elongation, maintaining consistent performance.
- High resistance to wear, tear, and punctures.
Disadvantages:
- Reduced flexibility, limiting use in complex layouts.
- Higher cost compared to other belt types.
3. Solid Woven Conveyor Belts
Solid woven conveyor belts are made from a single, continuous piece of woven fabric, typically coated with PVC or rubber. These belts are known for their exceptional strength and resistance to moisture, making them ideal for wet and humid underground mining environments.
Key Features:
- Material: Continuous woven fabric with PVC or rubber coating.
- Structure: Single, solid woven piece.
- Application: Suitable for wet and humid conditions.
Advantages:
- Excellent moisture resistance, preventing belt degradation.
- High tensile strength, supporting heavy loads.
- Enhanced fire resistance due to PVC or rubber coating.
Disadvantages:
- Heavier weight, increasing energy consumption.
- Higher cost compared to multi-ply belts.
4. PVC Conveyor Belts
PVC (Polyvinyl Chloride) conveyor belts are widely used in underground mining due to their excellent resistance to chemicals, moisture, and abrasion. These belts are particularly suitable for environments where exposure to harsh conditions is common.
Key Features:
- Material: PVC coating.
- Structure: Single or multiple plies with PVC coating.
- Application: Ideal for chemically aggressive and wet environments.
Advantages:
- High resistance to chemicals and moisture.
- Good abrasion resistance, extending belt life.
- Flame retardant properties, enhancing safety.
Disadvantages:
- Lower tensile strength compared to steel-cord belts.
- May not be suitable for extremely heavy loads.
5. Rubber Conveyor Belts
Rubber conveyor belts are the most versatile and widely used type in underground mining. They are made from natural or synthetic rubber compounds and are available in various grades to suit different mining applications.
Key Features:
- Material: Natural or synthetic rubber.
- Structure: Single or multiple plies with rubber coating.
- Application: Suitable for a wide range of mining applications.
Advantages:
- Excellent flexibility, allowing use in complex systems.
- Good resistance to impact and abrasion.
- Cost-effective and widely available.
Disadvantages:
- May require more frequent replacement due to wear.
- Not as strong as steel-cord belts for extremely heavy loads.
Highlighting Specific Belts Designed for Unique Underground Mining Conditions
In addition to the standard types of conveyor belts, specific belts are designed to address unique underground mining conditions. These specialized belts include:
- Fire-Resistant Belts: Designed to withstand high temperatures and prevent fire propagation, essential for safety in underground mining.
- Anti-Static Belts: Prevent the buildup of static electricity, reducing the risk of sparks and explosions in environments with flammable gases or dust.
- Oil-Resistant Belts: Coated with materials that resist oil and grease, making them suitable for operations where these substances are prevalent.
By understanding the different types of conveyor belts in underground mining and their specific applications, mining operations can select the most appropriate belt to enhance efficiency, safety, and productivity. The right choice of conveyor belt can significantly impact the overall performance of the mining system, ensuring smooth and reliable transport of materials.
Conveyor Belt in Underground Mining Manufacturers
Leading Companies in the Manufacturing of Conveyor Belt in Underground Mining
The conveyor belt in underground mining is a critical component that demands precision engineering and robust construction. Several leading companies specialize in the production of conveyor belts tailored to the rigorous conditions of underground mining. These manufacturers are renowned for their innovation, quality, and ability to meet the specific needs of the mining industry. Below, we highlight some of the key players in this field:
1. ContiTech AG
ContiTech AG, a subsidiary of Continental AG, is a global leader in the manufacturing of conveyor belts for mining and industrial applications. Known for their high-quality products and innovative technologies, ContiTech provides a wide range of belts designed to meet the demanding conditions of underground mining.
Key Products:
- Steel-cord Belts: Offering high tensile strength and durability.
- Fabric Belts: Suitable for less demanding applications.
- Specialty Belts: Including fire-resistant and anti-static options.
Innovations:
- ContiFlex: A flexible, high-strength belt designed for challenging underground conditions.
- ContiProtect: Integrated monitoring systems for early detection of belt wear and damage.
2. Fenner Dunlop
Fenner Dunlop is another leading manufacturer of conveyor belts, known for its extensive range of products specifically designed for the mining industry. With over 150 years of experience, Fenner Dunlop focuses on providing reliable and durable belts that enhance operational efficiency and safety in underground mining.
Key Products:
- Steel-Cord Belts: Robust and capable of handling high loads.
- Solid Woven Belts: Known for their moisture resistance and durability.
- Custom Solutions: Tailored belts for specific mining applications.
Innovations:
- Ultra Tuff™: A belt designed to provide superior resistance to wear and abrasion.
- KordFlex™: A high-strength belt reinforced with aramid fibers for enhanced performance.
3. Phoenix Conveyor Belt Systems
Phoenix Conveyor Belt Systems, a subsidiary of the Continental group, is renowned for its innovative conveyor belt solutions for underground mining. Phoenix specializes in producing belts that can withstand extreme conditions, ensuring continuous and efficient operation in the harshest environments.
Key Products:
- Steel-Cord Belts: Offering exceptional strength and longevity.
- Textile Belts: Designed for lighter loads and general mining applications.
- Specialty Belts: Including fire-resistant and oil-resistant belts.
Innovations:
- Phoenocord: A steel-cord belt with integrated sensor technology for real-time monitoring.
- Phoenotec: Enhanced impact protection through specially designed reinforcement layers.
4. Bridgestone Corporation
Bridgestone Corporation, a leading name in the tire industry, also manufactures high-quality conveyor belts for underground mining. Bridgestone belts are known for their superior performance, durability, and advanced technological features.
Key Products:
- Steel-Cord Belts: Designed for heavy-duty applications.
- Rubber Belts: Versatile and suitable for various mining conditions.
- Customized Solutions: Tailored to meet specific operational needs.
Innovations:
- Heat-Resistant Belts: Designed to withstand high temperatures.
- Energy-Saving Belts: Engineered to reduce energy consumption and operational costs.
5. Yokohama Rubber Co., Ltd.
Yokohama Rubber Co., Ltd. is a prominent manufacturer of conveyor belts, offering a diverse range of products for underground mining. Known for their reliability and innovation, Yokohama belts are designed to enhance operational efficiency and safety.
Key Products:
- Steel-Cord Belts: Strong and durable, ideal for high-stress environments.
- Fabric Belts: Suitable for general-purpose mining applications.
- Specialty Belts: Including fire-resistant and abrasion-resistant options.
Innovations:
- High-Impact Belts: Designed to absorb shock and reduce wear.
- Eco-Friendly Belts: Manufactured using sustainable practices and materials.
Insights into How Manufacturers Cater to the Demanding Conditions of Underground Mining
Manufacturers of conveyor belts for underground mining understand the unique challenges posed by this demanding environment. To cater to these needs, they employ a variety of strategies and innovations:
Material Selection
The choice of materials is critical in the manufacturing of conveyor belts for underground mining. Manufacturers select high-quality materials that offer durability, flexibility, and resistance to various environmental factors such as moisture, chemicals, and extreme temperatures. For example, steel-cord belts are chosen for their strength and durability, while solid woven belts are preferred for their moisture resistance.
Technological Innovations
Leading manufacturers invest heavily in research and development to introduce innovative technologies that enhance the performance and lifespan of conveyor belts. This includes the integration of sensors and monitoring systems that provide real-time data on belt condition, helping to prevent failures and reduce downtime.
Customization
Understanding that each mining operation has unique requirements, manufacturers offer customized solutions tailored to specific needs. This includes designing belts with specific properties such as fire resistance, anti-static features, and impact protection. Customization ensures that the conveyor belt in underground mining can handle the particular challenges of the environment.
Sustainability
Sustainability is becoming increasingly important in the mining industry. Manufacturers are developing eco-friendly belts using sustainable materials and practices. These belts not only reduce environmental impact but also meet the growing demand for green solutions in mining operations.
Comprehensive Support
Manufacturers provide comprehensive support services, including installation, maintenance, and training. This ensures that the conveyor belt in underground mining operates efficiently and safely, with minimal disruptions. Regular maintenance services help extend the life of the belts and maintain optimal performance.
By focusing on these key areas, leading manufacturers of conveyor belts for underground mining continue to innovate and provide solutions that meet the evolving needs of the mining industry. Their commitment to quality, innovation, and sustainability ensures that mining operations can rely on durable and efficient conveyor systems.
Conveyor Belt in Underground Mining for Sale
Where and How to Source Conveyor Belts for Underground Mining
Sourcing a conveyor belt for underground mining involves a careful evaluation of suppliers, product specifications, and the specific needs of the mining operation. There are several avenues through which mining companies can procure these essential components:
Direct from Manufacturers
Purchasing directly from manufacturers is one of the most reliable ways to source a conveyor belt in underground mining. Leading manufacturers such as ContiTech AG, Fenner Dunlop, and Bridgestone Corporation offer a wide range of belts specifically designed for underground mining. Buying directly ensures that customers receive genuine products with the latest technological advancements and robust warranties.
Advantages:
- Access to the latest products and technologies.
- Direct support and customized solutions from the manufacturer.
- Comprehensive warranties and after-sales service.
Industrial Suppliers and Distributors
Industrial suppliers and distributors often have extensive networks and stock a variety of conveyor belts from multiple manufacturers. Companies like Motion Industries and Applied Industrial Technologies provide a wide selection of belts suitable for various underground mining applications.
Advantages:
- Wide selection from different manufacturers.
- Local availability and faster delivery times.
- Potential for bulk purchase discounts.
Online Marketplaces
Online marketplaces such as Alibaba, Amazon Business, and ThomasNet offer a platform to browse and purchase conveyor belts from various suppliers worldwide. These platforms often provide detailed product descriptions, specifications, and customer reviews, aiding in informed decision-making.
Advantages:
- Convenience of online browsing and ordering.
- Access to a global network of suppliers.
- Comparative shopping and reviews to gauge product quality.
Trade Shows and Industry Events
Attending trade shows and industry events like MINExpo International and the International Mining and Resources Conference (IMARC) allows mining companies to see the latest products and technologies in action. These events provide opportunities to meet with manufacturers, discuss specific needs, and negotiate deals.
Advantages:
- Hands-on experience with the latest products.
- Networking opportunities with industry professionals.
- Direct discussions with manufacturers and suppliers.
Second-Hand Equipment Dealers
For cost-conscious operations, purchasing second-hand conveyor belts from reputable dealers can be a viable option. Companies like Mine Source Auctions and EquipNet offer used mining equipment, including conveyor belts, often at significantly reduced prices.
Advantages:
- Cost savings compared to new equipment.
- Availability of high-quality, refurbished belts.
- Quick availability and lower lead times.
Considerations When Purchasing a Conveyor Belt for Underground Mining
When purchasing a conveyor belt in underground mining, several critical considerations must be taken into account to ensure safety, efficiency, and longevity of the belt. Here are five key factors to consider:
Conformance to Safety Standards
Safety is paramount in underground mining operations. Ensure that the conveyor belt conforms to relevant safety standards such as MSHA (Mine Safety and Health Administration) in the U.S., or equivalent standards in other countries. This includes fire resistance, anti-static properties, and durability under harsh conditions.
Material and Construction
The material and construction of the belt should match the specific requirements of the mining operation. Options include multi-ply fabric, steel-cord, and solid woven belts, each with its strengths and weaknesses.
Belt Width and Length
The width and length of the conveyor belt should be appropriate for the mining system’s design and the volume of material to be transported. Proper sizing ensures efficient operation and minimizes the risk of overloading or spillage.
Maintenance and Serviceability
Consider the ease of maintenance and availability of service support for the conveyor belt. Regular maintenance is crucial for the longevity and efficiency of the belt.
Cost and Budget
While cost is an important factor, it should not compromise the quality and suitability of the conveyor belt. Investing in a high-quality belt may result in lower overall costs by reducing downtime and maintenance expenses.
Sourcing the right conveyor belt in underground mining involves a strategic approach to ensure that the belt meets the operational demands and safety requirements of the mining environment. By considering factors such as safety standards, material and construction, belt dimensions, maintenance needs, and cost, mining companies can make informed decisions that enhance operational efficiency and safety. Whether purchasing directly from manufacturers, through industrial suppliers, online marketplaces, trade shows, or second-hand dealers, the key is to find a reliable source that offers quality products and comprehensive support.
Conveyor Belt in Underground Mining System
Underground Conveyor Systems and How They Are Tailored to Suit the Challenging Mining Environments
An underground conveyor belt system is a critical component in mining operations, designed to transport materials efficiently and safely from the mining face to the surface. These systems are specifically tailored to meet the unique challenges posed by underground mining environments, which include confined spaces, harsh conditions, and the need for continuous operation.
Underground conveyor systems are engineered to be robust, flexible, and adaptable to the specific layout of a mining operation. They must navigate through narrow tunnels, steep inclines, and sharp bends while maintaining a steady flow of materials. The primary goal is to optimize the transportation process, reduce manual labor, and enhance overall productivity.
The Design and Technological Features that Enable Efficient Functioning in Confined Spaces
To ensure efficient functioning in the challenging environments of underground mining, conveyor belt systems incorporate various design and technological features. Here are five examples:
Modular Design
One of the key features of a conveyor belt in underground mining is its modular design. This allows for easy assembly, disassembly, and reconfiguration to adapt to the changing needs of the mining operation. Modular systems are composed of standardized sections that can be quickly installed or replaced, minimizing downtime and ensuring continuous operation.
Advantages:
- Flexibility: Easily adjustable to fit different tunnel sizes and layouts.
- Maintenance: Simplified maintenance and quick replacement of damaged sections.
- Scalability: Can be extended or shortened as needed.
High-Tension Belts
Underground mining requires conveyor belts that can handle high tension and heavy loads. High-tension belts are designed with reinforced materials, such as steel cords or multi-ply fabrics, to provide the necessary strength and durability.
Advantages:
- Durability: Withstands the stress of transporting heavy and abrasive materials.
- Longevity: Reduced wear and tear, extending the belt’s lifespan.
- Efficiency: Maintains consistent performance under high load conditions.
Fire-Resistant and Anti-Static Properties
Safety is paramount in underground mining, where the risk of fire and explosions is significant. Conveyor belts used in these environments are often equipped with fire-resistant and anti-static properties to prevent accidents and ensure safe operation.
Advantages:
- Fire Resistance: Reduces the risk of ignition from heat or friction.
- Anti-Static: Prevents the buildup of static electricity, reducing the chance of sparks.
- Compliance: Meets stringent safety standards and regulations.
Belt Monitoring Systems
Advanced belt monitoring systems are an integral part of modern underground conveyor belt systems. These systems use sensors and real-time data analytics to monitor the condition of the conveyor belt, detect any signs of wear or damage, and predict potential failures before they occur.
Advantages:
- Preventive Maintenance: Identifies issues early, preventing costly downtime.
- Efficiency: Ensures optimal belt performance and reduces maintenance costs.
- Safety: Enhances operational safety by preventing unexpected failures.
Low-Profile Idlers and Rollers
In confined underground spaces, the design of idlers and rollers is crucial. Low-profile idlers and rollers are used to minimize the overall height of the conveyor system, allowing it to fit in narrow tunnels and low-clearance areas.
Advantages:
- Space-Saving: Fits within tight spaces without sacrificing functionality.
- Smooth Operation: Reduces belt sag and ensures smooth material flow.
- Maintenance: Easier to access and maintain in confined spaces.
Integration and Control Systems
Efficient functioning of a conveyor belt in underground mining also relies heavily on sophisticated integration and control systems. These systems coordinate the operation of multiple conveyor belts, ensuring synchronized movement and optimal load distribution.
Advantages:
- Automation: Reduces the need for manual intervention and increases operational efficiency.
- Load Management: Distributes material evenly across the system, preventing overload and ensuring steady flow.
- Real-Time Monitoring: Provides real-time data on system performance, enabling quick adjustments and decision-making.
The underground conveyor belt system is an indispensable part of modern mining operations, tailored to overcome the specific challenges of underground environments. Through innovative designs and advanced technological features, these systems ensure efficient material transport, enhance safety, and boost productivity. Whether through modular design, high-tension belts, fire-resistant properties, advanced monitoring, or low-profile components, each feature plays a vital role in the successful operation of a conveyor belt in underground mining. These integrated solutions enable mining companies to maintain continuous and efficient operations, even in the most demanding conditions.
Conveyor Belt in Underground Mining Factorio
Simulations and Video Game Representations That Illustrate the Workings of Underground Conveyor Belts
Simulations and video games, such as Factorio, provide a unique and interactive way to understand the intricacies of an underground conveyor belt in underground mining. Factorio, a popular simulation game, allows players to design and manage complex industrial systems, including conveyor belts. The game’s detailed mechanics and realistic representations make it an excellent tool for visualizing and experimenting with conveyor belt systems in a risk-free environment.
In Factorio, players can build extensive conveyor belt networks to transport resources from one location to another, simulating real-world mining operations. The game includes various types of conveyor belts, including underground belts, which are essential for managing space and optimizing logistics in confined environments. These underground belts function similarly to their real-world counterparts, providing a realistic model of how materials are transported in an underground mining setting.
How Such Tools Can Aid in Understanding System Logistics and Planning
Simulation tools like Factorio offer several advantages for understanding the logistics and planning of an underground conveyor belt in underground mining. By providing a virtual platform to test and optimize different conveyor belt configurations, these tools help mining professionals gain valuable insights into the operational efficiencies and challenges of underground conveyor systems.
Visualizing Complex Systems
One of the primary benefits of using simulations like Factorio is the ability to visualize complex conveyor belt systems. In the game, players can see how different conveyor belts interact, how materials flow through the system, and where bottlenecks or inefficiencies occur. This visual representation helps users understand the spatial requirements and constraints of underground conveyor belts, making it easier to plan and optimize real-world systems.
Advantages:
- Clear Visualization: See how conveyor belts navigate through confined spaces.
- Identifying Bottlenecks: Easily spot areas where material flow is obstructed or slowed.
- Optimizing Layouts: Experiment with different configurations to find the most efficient setup.
Experimenting with Different Scenarios
Factorio allows players to experiment with various scenarios and configurations without the risk and cost associated with real-world trials. Users can test different types of conveyor belts, load capacities, and system layouts to see how they impact overall efficiency and performance. This experimentation can lead to innovative solutions and improvements in real-world mining operations.
Advantages:
- Risk-Free Testing: Try out new ideas and configurations without real-world consequences.
- Cost-Effective: Save money by identifying the best solutions before implementation.
- Innovation: Discover new approaches and techniques for optimizing conveyor belt systems.
Load Management
Effective load management is crucial for the efficiency of a conveyor belt in underground mining. Factorio provides a detailed simulation of how materials are loaded, transported, and unloaded across different conveyor belts. This helps users understand the importance of balancing loads, preventing overloading, and ensuring a steady flow of materials.
Advantages:
- Load Balancing: Learn how to distribute materials evenly across the system.
- Prevent Overloading: Avoid system failures caused by excessive loads.
- Steady Flow: Ensure a consistent and reliable flow of materials.
Enhancing Strategic Planning
Strategic planning is essential for the successful implementation and operation of conveyor belt systems in underground mining. Factorio’s simulation environment helps users develop long-term strategies for system expansion, maintenance, and optimization. By planning ahead, mining operations can reduce downtime, increase productivity, and extend the lifespan of their conveyor belts.
Advantages:
- Long-Term Planning: Develop strategies for future system expansion and upgrades.
- Maintenance Scheduling: Plan regular maintenance to prevent unexpected failures.
- Resource Allocation: Allocate resources effectively for optimal system performance.
Educational and Training Tool
Factorio and similar simulation tools are valuable educational resources for training new employees and educating stakeholders about the complexities of conveyor belt systems in underground mining. By providing an interactive and engaging platform, these tools can enhance learning and improve understanding of key concepts and best practices.
Advantages:
- Interactive Learning: Engage users with hands-on experience.
- Improved Understanding: Clarify complex concepts through practical application.
- Training Resource: Prepare new employees for real-world scenarios.
Simulations and video games like Factorio offer powerful tools for understanding and optimizing the logistics and planning of an underground conveyor belt in underground mining. By visualizing complex systems, experimenting with different scenarios, understanding load management, enhancing strategic planning, and serving as educational tools, these simulations provide valuable insights and practical benefits. Leveraging these tools can lead to more efficient, safe, and productive mining operations, ultimately improving the performance and reliability of underground conveyor belt systems.
Conveyor Belt in Underground Mining Maintenance
The Critical Role of Proper Maintenance in the Lifespan and Efficiency
Proper maintenance of a conveyor belt in underground mining is essential for ensuring its longevity, efficiency, and safety. Regular maintenance practices not only prevent unexpected breakdowns but also optimize the operational performance of the conveyor system. Here are five examples illustrating the critical role of maintenance:
Prolonging Belt Life
Routine maintenance activities such as cleaning, lubrication, and inspection help prolong the lifespan of conveyor belts. By removing debris and contaminants that can cause wear and tear, the belt’s material integrity is preserved, leading to fewer replacements and lower costs over time.Regularly cleaning the belt surface and removing buildup of dirt and rocks to prevent abrasion and reduce wear.
Enhancing Operational Efficiency
A well-maintained conveyor belt operates more smoothly and efficiently. Regular adjustments and alignments ensure that the belt runs straight and true, reducing energy consumption and preventing material spillage.Periodic alignment checks to ensure the belt is properly tracking and minimizing resistance that could lead to increased energy use.
Preventing Downtime
Preventive maintenance helps identify and address potential issues before they escalate into major problems that can cause operational downtime. Scheduled inspections and timely repairs keep the conveyor system running without interruptions, maximizing productivity.Regularly inspecting and replacing worn-out rollers and idlers to prevent sudden failures that could halt operations.
Ensuring Safety
Maintaining a conveyor belt in underground mining is crucial for ensuring the safety of workers. Faulty belts can pose significant hazards, including the risk of fire, entanglement, or falling debris. Proper maintenance mitigates these risks and creates a safer working environment.Inspecting for and repairing frayed or damaged belt edges that could pose entanglement hazards.
Cost Efficiency
Investing in regular maintenance reduces the likelihood of costly emergency repairs and unplanned downtime. It also extends the operational life of the conveyor belt, providing better return on investment and overall cost savings.Conducting routine preventive maintenance to identify and fix minor issues before they become major, expensive problems.
Get a detailed quote for our Mining Conveyor Belts by filling out the inquiry form below.
Preventive Measures, Routine Checks, and Common Repair Practices
Implementing a structured maintenance program involves a combination of preventive measures, routine checks, and common repair practices. Here are five examples of each:
Preventive Measures
- Regular Inspections: Conduct regular visual inspections to identify signs of wear, damage, or misalignment. Early detection of issues prevents them from becoming severe.
- Lubrication: Apply proper lubrication to moving parts such as rollers, pulleys, and bearings to reduce friction and wear.
- Cleaning: Regularly clean the conveyor belt and its components to remove dirt, debris, and spillage that can cause damage or reduce efficiency.
- Tension Adjustment: Ensure that the belt is correctly tensioned to avoid slippage and excessive wear. Over-tensioned belts can cause strain on the system, while under-tensioned belts may slip and reduce efficiency.
- Training: Train personnel on proper operation and maintenance procedures to ensure that the conveyor belt is used correctly and maintained properly.
Routine Checks
- Belt Condition: Check for signs of wear, fraying, or damage along the belt’s edges and surface. Replace or repair as necessary to maintain integrity.
- Rollers and Idlers: Inspect rollers and idlers for wear or damage. Ensure they are spinning freely and replace any that are seized or worn out.
- Alignment: Regularly check the alignment of the conveyor belt to ensure it is running straight. Misalignment can cause uneven wear and potential damage.
- Belt Tension: Measure and adjust the belt tension regularly to maintain optimal performance and prevent slippage.
- Drive Components: Inspect drive motors, gearboxes, and pulleys for signs of wear or damage. Ensure all components are functioning correctly and efficiently.
Common Repair Practices
- Belt Splicing: When a belt is damaged or needs to be extended, splicing is performed to join two belt ends together. There are various methods, including mechanical fasteners and vulcanization.
- Patch Repairs: Small tears or holes in the belt can be repaired with patches to restore the belt’s integrity and prevent further damage.
- Replacing Rollers and Idlers: Worn or damaged rollers and idlers are replaced to ensure smooth operation and prevent belt damage.
- Realigning Belt: Misaligned belts are realigned to prevent uneven wear and ensure the belt runs true, reducing the risk of damage and improving efficiency.
- Upgrading Components: Upgrading to higher quality or more suitable components can improve the overall performance and lifespan of the conveyor belt system.
Proper maintenance of a conveyor belt in underground mining is crucial for enhancing operational efficiency, safety, and cost-effectiveness. By implementing preventive measures, conducting routine checks, and performing common repair practices, mining operations can ensure that their conveyor systems remain reliable and efficient. This proactive approach not only extends the life of the conveyor belt but also maximizes productivity and minimizes the risk of unexpected downtime and costly repairs.
FAQs About Conveyor Belt in Underground Mining
Conveyor belts are a vital component in mining operations, facilitating the continuous and efficient transport of materials. In mining, conveyor belts are used to move extracted minerals, such as coal, ore, and other raw materials, from the mining site to processing facilities or loading areas. This transport system helps to reduce the need for manual labor, minimize transportation time, and improve overall productivity. Conveyor belts also enhance safety by reducing the risk of accidents associated with the manual handling of heavy materials. Additionally, they contribute to the efficiency of mining operations by ensuring a steady and reliable flow of materials, which is essential for maintaining continuous production cycles. Overall, conveyor belts play a critical role in modern mining by optimizing the movement of materials and supporting the seamless operation of mining activities.
Several types of conveyor belts are used in mining to suit different applications and materials. The main types include:
Multi-ply Belts: Comprising multiple layers of fabric, these belts offer enhanced strength and durability, making them suitable for transporting heavy loads.
Steel-cord Belts: Reinforced with steel cables, these belts provide exceptional tensile strength and are ideal for heavy-duty applications and long-distance transport.
Solid Woven Belts: Made from a single, continuous piece of woven fabric coated with PVC or rubber, these belts are known for their high strength and resistance to moisture and chemicals.
PVC Belts: These belts are highly resistant to chemicals and moisture, making them suitable for harsh and wet environments.
Rubber Belts: Versatile and widely used, rubber belts are flexible and durable, suitable for a variety of mining applications, including the transport of heavy and abrasive materials.
Each type of belt is designed to meet specific needs in mining operations, ensuring optimal performance, durability, and safety.
In coal mining, the most commonly used type of conveyor is the steel-cord conveyor belt. These belts are favored for their high tensile strength and durability, which are essential for handling the heavy and abrasive nature of coal. Steel-cord conveyor belts are reinforced with steel cables, providing the strength needed to transport large volumes of coal over long distances and through challenging underground environments. They also offer low elongation, ensuring consistent performance and reducing the risk of belt stretch or failure. Additionally, steel-cord belts are resistant to wear and tear, making them ideal for the rigorous demands of coal mining. Their robust construction allows them to operate efficiently in harsh conditions, including exposure to moisture and high temperatures. Overall, steel-cord conveyor belts are the preferred choice in coal mining due to their reliability, strength, and ability to maintain continuous and efficient material transport.
The most commonly used type of belt in mines is the multi-ply conveyor belt. Multi-ply belts are composed of several layers of fabric, typically made from polyester, nylon, or cotton, which are bonded together with rubber. This multi-layer construction provides enhanced strength and durability, making these belts suitable for a wide range of mining applications. Multi-ply belts are versatile and can handle various materials, including ores, minerals, and coal, making them a popular choice in both surface and underground mining operations. They are also flexible enough to navigate sharp bends and inclines, allowing them to be used in complex mining layouts. Furthermore, multi-ply belts are cost-effective and relatively easy to maintain, contributing to their widespread use in the mining industry. Their ability to withstand the harsh conditions of mining environments, combined with their durability and versatility, makes multi-ply conveyor belts the go-to option for many mining operations.
Last Updated on July 31, 2024 by Jordan Smith
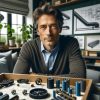
Jordan Smith, a seasoned professional with over 20 years of experience in the conveyor system industry. Jordan’s expertise lies in providing comprehensive solutions for conveyor rollers, belts, and accessories, catering to a wide range of industrial needs. From initial design and configuration to installation and meticulous troubleshooting, Jordan is adept at handling all aspects of conveyor system management. Whether you’re looking to upgrade your production line with efficient conveyor belts, require custom conveyor rollers for specific operations, or need expert advice on selecting the right conveyor accessories for your facility, Jordan is your reliable consultant. For any inquiries or assistance with conveyor system optimization, Jordan is available to share his wealth of knowledge and experience. Feel free to reach out at any time for professional guidance on all matters related to conveyor rollers, belts, and accessories.