Maximizing The Conveyor Belt Life
Conveyor belts are the backbone of countless industrial applications, silently and efficiently transporting goods across distances within manufacturing plants, mining operations, and distribution centers. Their role is so pivotal that any downtime caused by belt failures can lead to significant operational disruptions and financial losses. This underscores the importance of understanding conveyor belt life, a term that refers to the expected operational lifespan of a conveyor belt under normal working conditions. The concept of conveyor belt life is crucial not only for planning maintenance and replacements but also for initial system design and material selection.Conveyor belt lifespan varies from weeks to years, influenced by conveyed product, operating environment, design, and maintenance. By optimizing for a longer conveyor belt life, businesses can achieve greater operational efficiency and manage costs more effectively, ensuring that the conveyor system operates smoothly and reliably over time. This introduction sets the stage for a deeper exploration into how conveyor belt life can be calculated, extended, and optimized to support the overarching goals of industrial efficiency and cost-effectiveness.
What is Conveyor Belt Life
The Basics of Conveyor Belt Life
Understanding the basics of conveyor belt life is essential for anyone involved in the design, operation, or maintenance of conveyor systems. Conveyor belt life refers to the duration a conveyor belt is expected to function efficiently without significant deterioration or failure. It encompasses the period from its initial installation to the point where it no longer performs its intended function effectively, necessitating repair or replacement. This lifespan is not a fixed figure but varies widely based on several key factors.
The factors influencing Conveyor Belt Life
The service life of any conveyor belt is determined by two basic factors. Firstly, it is the overall quality of the belt, its physical properties and ability of the belt to handle both the material it is required to carry and the local working environment. The second biggest influencing factor is the type of materials being carried. In the past, the type of material was considered to be the primary influence. However, this was before the technological advances made by manufacturers such as Dunlop Conveyor Belting in the Netherlands (Fenner Dunlop), which is part of the Michelin Group, and Contitech in Germany.
Regardless of which takes precedence, the inarguable fact is that both factors are inextricably linked. The reason for this is that the true cost of a conveyor belt can only ever be measured and compared based on its purchase price, fitting and cumulative repair costs divided either by its working lifespan or the tonnage carried during that time.
As with any manufactured product, price ultimately determines the quality and the longevity. In the world of conveyor belts, it is not uncommon to see ‘economy’ belts being offered, usually by manufacturers based in Southeast Asia, at literally half the price of those being offered by the big, quality-led manufacturers based in Europe. However, a big difference in price invariably indicates a comparable difference in the quality of the materials used. The materials used to make a conveyor belt can constitute up to 70% of its ultimate cost and are therefore the prime target for cost-cutting for those wishing to offer lower prices than their competitors. To better understand the connection between the sales price, longevity and the effect on whole life cost, it is necessary to understand the methods used to minimise the selling price and their negative impact on the performance and length of operational life.
Eight primary factors influencing the lifespan of a conveyor belt include:
- Material Quality: The quality of the materials used to manufacture the conveyor belt plays a pivotal role in determining its life. High-quality materials that are resistant to wear, tear, and environmental conditions can significantly extend a belt’s operational life. Materials such as rubber, PVC, or fabric composites are commonly used, each with specific properties that affect the conveyor belt’s durability and suitability for different applications.
- Operating Conditions: The environment in which a conveyor belt operates can greatly impact its lifespan. Factors such as exposure to extreme temperatures, abrasive materials, chemicals, and moisture can accelerate wear and reduce conveyor belt life. Additionally, the load carried by the belt, the speed of operation, and the length of the conveyor system also play critical roles. Belts operating under harsh conditions or handling heavy loads at high speeds are likely to experience a shorter lifespan.
- Maintenance Practices: Regular and proper maintenance is crucial for maximizing conveyor belt life. This includes routine inspections for wear and damage, timely repairs, correct tensioning, and alignment, as well as cleaning to prevent material build-up. Effective maintenance practices not only extend the life of the conveyor belt but also ensure it operates efficiently, reducing the likelihood of unexpected breakdowns and downtime.
- Load Capacity: Overloading the conveyor belt can strain the material, leading to faster wear and potential failure. Adhering to the recommended load capacity is essential for longevity.
- Belt Speed: Operating the conveyor at speeds too high for the belt material or the goods being transported can increase wear and reduce belt life.
- Installation and Alignment: Proper installation and alignment are critical from the start. Misalignment can cause uneven wear, increased friction, and damage to the belt edges.
- Type of Goods Transported: The nature of the materials being conveyed plays a significant role. Sharp or hot materials, for example, can cause more rapid deterioration than softer, cooler items.
- Environmental Factors: External factors such as humidity, exposure to sunlight, and the presence of water or oils can affect the integrity and performance of the conveyor belt over time.
Life-shortening Omissions
Because of its adaptability, most of the rubber used to make conveyor belts is synthetic. Dozens of different chemical components, polymers and substances are used to create the numerous different rubber compounds needed to cope with the different demands that may be placed upon them. For human safety and environmental protection reasons, these chemical components and additives are strictly regulated in Europe. However, such regulation does not apply outside of Europe, including Southeast Asia of course, which is the biggest source of low-price belting. Good quality, regulated raw materials are significantly more costly than low-grade, unregulated raw materials so their use makes an important contribution towards the manufacturer’s cost-cutting objectives.
In some cases, despite their enormous influence on the operating life of the belt, some additives are omitted completely because they are seen to be an avoidable cost. One of the best examples of such an omission concerns ozone and ultraviolet light. From a longevity point of view, there is no question that all rubber conveyor belts need to be fully resistant to the damaging effects of ozone and ultraviolet light. This is because at ground-level, ozone becomes a pollutant. Exposure, which is unavoidable, increases the acidity of carbon black surfaces and causes reactions to take place within the molecular structure of the rubber. This has several consequences including surface cracking and a marked decrease in the tensile strength, all of which accelerates the wear and general degradation of the rubber.
Likewise, ultraviolet light from sunlight and fluorescent lighting also accelerates deterioration because it produces photochemical reactions that promote the oxidation of the surface of the rubber resulting in a significant loss of mechanical strength. Laboratory testing consistently reveals that so-called ‘economy’ belting is very rarely, if ever, ozone and UV resistant.
By understanding these basics of conveyor belt life, businesses can make informed decisions regarding belt selection, system design, and maintenance strategies. This knowledge enables the optimization of conveyor belt performance, ensuring that these critical components meet and exceed their expected operational life, thereby supporting continuous and efficient industrial processes.
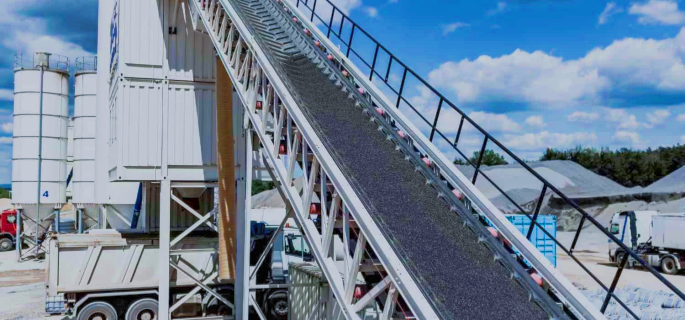
Calculating Conveyor Belt Life
Conveyor Belt Life Calculation
Calculating conveyor belt life is a critical aspect of conveyor system management, allowing operators and engineers to predict when a belt will need replacement and plan maintenance accordingly. This calculation helps in optimizing the operation and reducing unexpected downtimes, thus ensuring continuous productivity and efficiency.
Conveyor Belt Life Calculation involves understanding the factors that influence belt wear and applying formulas that consider these variables to estimate the belt’s lifespan. The basic formula for calculating conveyor belt life takes into account the belt’s material quality, operating conditions, and maintenance practices, among other factors. However, due to the complexity and variability of these factors, the calculation often requires adjustments based on empirical data and experience.
Conveyor Belt Life Formula
The expected life of conveyor belts can be calculated using various formulas, depending on the specific conditions under which the belt operates. One common approach is to use the following basic formula:
Note: The values for these factors are indicative and can vary significantly based on specific conditions and empirical data. The higher the value within the given range, the better the expected outcome for the belt’s lifespan.
To accurately calculate the conveyor belt life, it’s essential to assess each factor carefully. The Quality Factor considers the belt’s construction materials and their resistance to wear and environmental conditions. The Maintenance Factor evaluates how well the belt is maintained, including regular inspections, cleaning, and timely repairs. The Operating Condition Factor looks at the environment in which the belt operates, including temperature, exposure to chemicals or abrasives, and the load it carries.
By applying this formula and adjusting the factors based on specific operational data, conveyor system operators can estimate the expected lifespan of their conveyor belts. This calculation, while not exact, provides a useful guideline for planning maintenance and replacement, thereby helping to ensure that the conveyor system remains operational with minimal downtime.
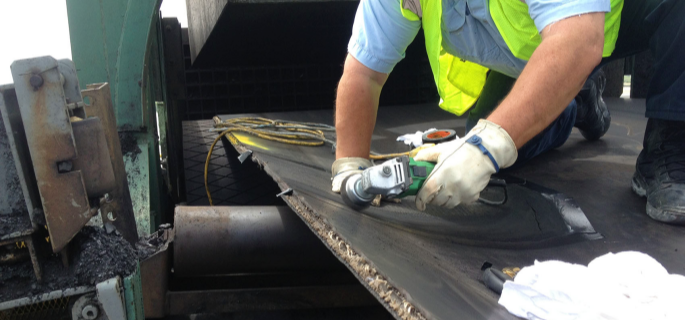
Conveyor Belt Lifespan Under Different Conditions
The lifespan of a conveyor belt, an essential component in various industrial operations, is influenced by multiple factors. Understanding these can help in effectively predicting conveyor belt life and implementing strategies to extend it. Here, we delve into specific considerations for v-belts, the impact of maintenance practices in the mining industry, and provide statistical insights into the average life of conveyor belts across different applications.
V-Belt Lifetime Calculation
V-belts, characterized by their unique V-shaped cross-section, are widely used in various industrial and mining applications. The life expectancy of v-belts is influenced by factors such as the belt’s material composition, operating temperature, load capacity, and alignment. Proper tensioning is crucial; too much tension can lead to excessive wear and premature failure, while too little can cause slippage and reduced efficiency. Environmental factors, such as exposure to oils, chemicals, and extreme temperatures, also significantly affect v-belt lifespan. Regular inspections for signs of wear, such as cracking, fraying, or glazing, are essential for timely replacement and to avoid operational disruptions.
Mining Conveyor Belt Maintenance
The harsh operating conditions in the mining industry, including abrasive materials, heavy loads, and constant operation, demand rigorous maintenance practices to extend conveyor belt life. Effective maintenance strategies include regular cleaning to prevent material build-up, timely repair of minor damages to prevent further deterioration, and proper alignment and tensioning to ensure uniform wear. Additionally, the use of wear-resistant materials and technologies, such as rip detection systems, can significantly enhance the durability and lifespan of conveyor belts in mining operations.
Average Life of Conveyor Belt
The average lifespan of conveyor belts varies significantly across different industries and applications, influenced by the operational environment, maintenance practices, and material quality. The following table provides a general overview:
Note: These values are indicative and can vary based on specific operational conditions and maintenance practices.
Understanding these factors and implementing targeted strategies can significantly impact conveyor belt life, enhancing operational efficiency and reducing downtime. Regular maintenance, appropriate material selection, and adherence to operational guidelines are key to maximizing the lifespan of conveyor belts across all applications.
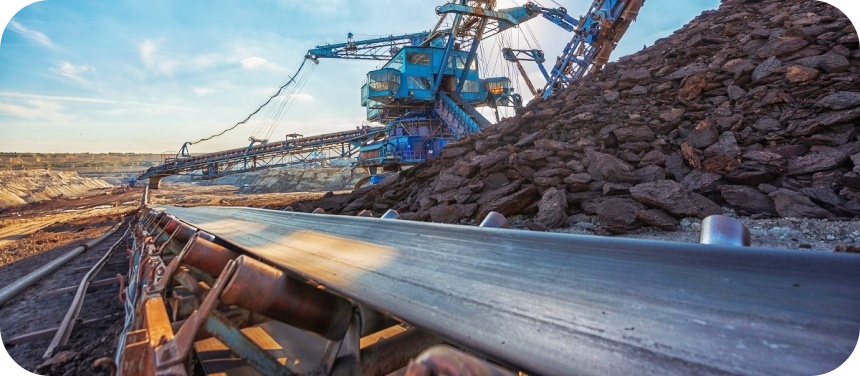
Maximizing Your Conveyor Belt Life
Maximizing the lifespan of your conveyor belts is crucial for ensuring the efficiency and cost-effectiveness of your operations. Here are some key strategies to help you achieve this:
Quality Material and Correct Belt Type
- High-Quality Materials: Invest in high-quality conveyor belts that are designed for your specific application and environment.
- Appropriate Belt Type: Choose the right type of belt for your operation. Factors include the nature of the material being conveyed, the operating environment, and load requirements.
Proper Loading Practices
- Even Loading: Ensure materials are loaded evenly onto the belt to prevent undue stress and wear.
- Avoid Overloading: Overloading can cause significant damage to the belt and reduce its lifespan. Follow manufacturer guidelines for load capacities.
Environmental Considerations
- Protect from Contaminants: Dust, dirt, and other contaminants can cause abrasion and reduce belt life. Implement measures to protect belts from contaminants.
- Temperature Control: Extreme temperatures can affect belt performance. Ensure your belts are suitable for the operating temperatures they will encounter.
Effective Training for Operators
- Operator Training: Ensure that all operators are well-trained in the proper use and maintenance of conveyor belts. They should be aware of the best practices and common pitfalls to avoid.
Utilizing the Right Accessories
- Belt Cleaners and Scrapers: Use appropriate belt cleaners and scrapers to keep the belts clean and free from debris.
- Impact Beds and Rollers: Employ impact beds and proper rollers to absorb shock and reduce wear at loading points.
Timely Repairs and Replacements
- Immediate Repairs: Address any issues immediately to prevent small problems from escalating into major repairs.
- Scheduled Replacements: Plan for timely replacement of belts that are nearing the end of their useful life to avoid unexpected downtimes.
By implementing these strategies, you can significantly extend the life of your conveyor belts, reduce downtime, and save on replacement costs. Regular maintenance, proper handling, and the right choice of materials and equipment play a crucial role in achieving maximum efficiency and longevity.
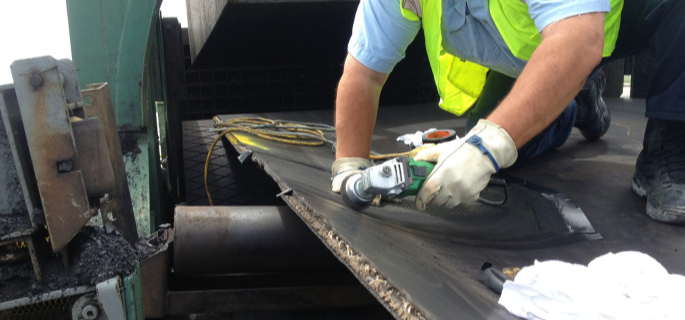
Maintenance Conveyor Belt Life
To maximize conveyor belt life, adopting a comprehensive maintenance strategy is essential. This strategy not only prevents premature wear and tear but also ensures the conveyor system operates efficiently and safely over its intended lifespan. Here, we explore best practices for routine maintenance and innovative techniques that can significantly extend the life of conveyor belts.
Best Practices for Routine Maintenance
- Regular Inspections: Conducting regular inspections is crucial for identifying early signs of wear, misalignment, or any other issues that could lead to belt damage. Inspections should focus on the belt’s surface, edges, and underside for any signs of wear or damage, as well as checking for proper tension and alignment.
- Cleanliness: Keeping the conveyor belt and its surroundings clean is essential to prevent material build-up that can cause damage. Use appropriate cleaning tools and techniques to remove debris and residues that could adhere to the belt and cause abrasion or corrosion.
- Proper Tensioning: Ensuring the conveyor belt is correctly tensioned prevents slippage and reduces stress on the belt. Over-tensioning can lead to excessive wear and energy consumption, while under-tensioning can cause the belt to slip off the pulleys.
- Alignment Checks: Misalignment is a common cause of conveyor belt damage. Regularly check and adjust the conveyor structure and idlers to ensure the belt runs straight. This prevents uneven wear and extends the belt’s lifespan.
Innovative Maintenance Techniques
- Condition Monitoring: Implementing condition monitoring technologies, such as sensors and IoT devices, can provide real-time data on the conveyor belt’s health. This allows for predictive maintenance, where issues can be addressed before they lead to failure.
- Use of High-Quality Materials: Upgrading to belts made from high-quality, durable materials can significantly extend conveyor belt life. Materials resistant to abrasion, heat, and chemicals reduce the frequency of replacements.
- Advanced Splicing Techniques: Utilizing advanced splicing techniques ensures that the belt joints are strong and durable. Mechanical fasteners or vulcanization methods can be chosen based on the belt type and application, contributing to longer belt life.
- Training for Maintenance Staff: Providing comprehensive training for maintenance personnel on the latest maintenance techniques and technologies is vital. Well-informed staff can better identify potential issues and perform effective repairs, extending the conveyor belt life.
By integrating these routine maintenance best practices and innovative techniques into a conveyor system’s operation, businesses can significantly enhance the longevity and reliability of their conveyor belts. This proactive approach to maintenance not only extends the conveyor belt’s life but also optimizes overall system performance, reducing downtime and maintenance costs.
Case Studies: Maximizing Conveyor Belt Lifespan
The pursuit of extending conveyor belt life is a critical goal across various industries, aiming to enhance operational efficiency and reduce downtime. Through real-world case studies, we can observe how proper maintenance and strategic design choices significantly contribute to achieving this goal. These examples highlight the impact of focused efforts on the longevity of conveyor belts in different operational settings.
Case Study 1: Mining Industry Implementation
In a large-scale mining operation, conveyor belts are subjected to extreme wear due to the abrasive nature of the materials being transported. The operation faced frequent belt replacements, impacting productivity and operational costs. By switching to high-durability materials designed to withstand abrasive conditions and implementing a rigorous maintenance schedule, the mine extended its conveyor belt life by over 40%. Regular inspections and the use of advanced monitoring technology allowed for predictive maintenance, further enhancing belt longevity.
Case Study 2: Manufacturing Facility Upgrade
A manufacturing facility specializing in the production of automotive parts experienced frequent conveyor belt misalignment, leading to uneven wear and tear. The facility invested in a redesign of their conveyor system, incorporating crowned pulleys and precision alignment tools. Additionally, the introduction of condition monitoring sensors enabled real-time tracking of belt performance. These strategic design choices and the adoption of a proactive maintenance approach doubled the average conveyor belt life, significantly reducing downtime and maintenance costs.
Case Study 3: Food Processing Plant’s Innovative Approach
A food processing plant faced challenges with conveyor belt contamination and material buildup, shortening the belt’s operational life. The plant introduced a comprehensive cleaning protocol using food-grade belt scrapers and implemented a belt design with antimicrobial properties. These measures not only extended the conveyor belt life but also improved hygiene standards. The plant saw a 50% increase in belt lifespan and a reduction in product contamination incidents.
Case Study 4: Logistics and Distribution Center Optimization
In a busy logistics and distribution center, conveyor belts are essential for the timely movement of goods. The center struggled with frequent belt slippage and wear, attributed to improper tensioning and alignment. By training maintenance staff in advanced tensioning techniques and investing in automatic tensioning systems, the center significantly improved its conveyor belt performance. The adoption of EPDM belts, known for their durability and resistance to wear, further extended the conveyor belt life, enhancing overall efficiency and reliability in operations.
These case studies demonstrate the tangible benefits of prioritizing conveyor belt maintenance and making informed design choices. By focusing on the specific challenges and operational demands of each setting, businesses can significantly extend the lifespan of their conveyor belts, resulting in improved operational efficiency, reduced downtime, and lower maintenance costs.
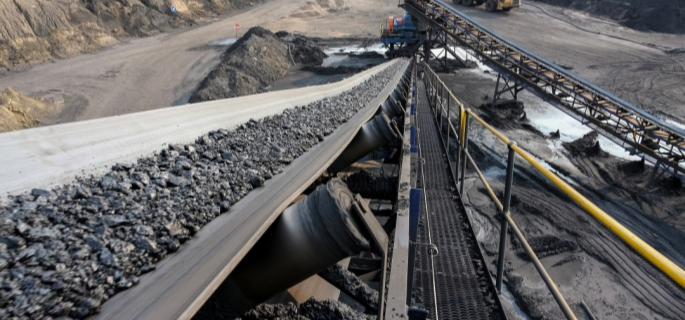
Looking for custom conveyor belts? Contact us to learn more.
FAQs about Conveyor Belt Life
The replacement frequency of conveyor belts largely depends on several factors, including the type of belt, the materials being transported, the operating environment, how the belt is used, and the maintenance practices in place. Generally, conveyor belts in light to moderate applications with proper maintenance can last between 3 to 5 years. In contrast, belts used in heavy industrial or harsh environments, such as mining or milling, may have a shorter lifespan, typically ranging from 1 to 3 years. Advanced materials and designs can extend a belt’s life up to 10 years under optimal conditions. Regular inspections are crucial for identifying wear and determining the appropriate time for replacement. Signs of wear include cracks, fraying, or brittleness. Consulting with manufacturers or specialists can provide tailored recommendations based on specific operational needs and conditions.
Calculating conveyor belt life involves assessing various factors that influence the belt’s durability and operational efficiency. While there’s no one-size-fits-all formula, the process generally considers the belt’s material quality, operating conditions, maintenance practices, and the specific demands of the application. A basic approach to estimating belt life is to analyze historical data on belt performance within similar operational contexts, considering factors such as belt speed, load capacity, environmental conditions, and maintenance schedules. Advanced methods might involve mathematical modeling to predict wear based on empirical data and theoretical analysis. Regular monitoring and inspections play a key role in adjusting these calculations, as they provide real-time insights into the belt’s condition and performance. Manufacturers often provide guidelines and tools for estimating belt life, which can be customized based on specific operational parameters.
The life expectancy of V belts can vary significantly based on their application, material composition, and maintenance. Typically, V belts should be inspected for wear after 3 years or 30-40,000 miles of use, as failure rates tend to increase sharply beyond this point. With proper maintenance, V belts can last between 3 to 5 years. Factors affecting their lifespan include the operating environment, alignment, tension, and exposure to contaminants. To maximize the life of V belts, it’s essential to ensure correct installation, maintain proper tension, and conduct regular inspections for signs of wear or damage. Replacing V belts at recommended intervals or at signs of significant wear helps prevent unexpected failures and maintains operational efficiency.
Increasing the life of your conveyor belt involves several proactive strategies focused on maintenance, operation, and design optimization. Regular and thorough inspections are crucial for early detection of wear and potential issues. Implementing a routine maintenance schedule that includes cleaning, lubrication, and adjustments can prevent premature wear. Proper tensioning and alignment reduce stress and uneven wear on the belt. Using high-quality materials and components that are suited to your specific operational needs can also extend belt life. Additionally, training personnel on best practices for conveyor operation and maintenance ensures that the system is used efficiently and cared for properly. Environmental controls, such as dust suppression and temperature regulation, can protect the belt from harsh conditions that accelerate wear. By adopting these strategies, you can significantly enhance the durability and operational lifespan of your conveyor belt, ensuring it performs reliably for as long as possible.
To prevent belting material from developing camber (swing), rolls should be stored off the floor in a dry area. They can be suspended on a bar placed through the center of the roll or placed on a pallet or skid to keep the material off the floor. Rolls should NOT be stored on their edges.
Last Updated on June 28, 2024 by Jordan Smith
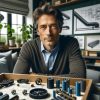
Jordan Smith, a seasoned professional with over 20 years of experience in the conveyor system industry. Jordan’s expertise lies in providing comprehensive solutions for conveyor rollers, belts, and accessories, catering to a wide range of industrial needs. From initial design and configuration to installation and meticulous troubleshooting, Jordan is adept at handling all aspects of conveyor system management. Whether you’re looking to upgrade your production line with efficient conveyor belts, require custom conveyor rollers for specific operations, or need expert advice on selecting the right conveyor accessories for your facility, Jordan is your reliable consultant. For any inquiries or assistance with conveyor system optimization, Jordan is available to share his wealth of knowledge and experience. Feel free to reach out at any time for professional guidance on all matters related to conveyor rollers, belts, and accessories.