Comprehensive Guide to Conveyor Belt Load Zone Support
Conveyor belt systems are crucial for efficient material handling in industries such as mining, manufacturing, and logistics. Ensuring optimal performance of these systems requires effective conveyor belt load zone support, which is vital for maintaining efficiency, reducing maintenance, and extending the lifespan of the belts. Conveyor belt load zone support helps in stabilizing the belt, minimizing spillage, and protecting the belt from damage, thereby ensuring smooth and continuous operation. Understanding the components and strategies for effective conveyor belt load zone support is essential for maximizing the performance and reliability of conveyor systems in various industrial applications.
Conveyor Belt Load Zone Support: Conveyor Belt Skirting
Purpose and Function
Conveyor belt skirting is a crucial component of conveyor belt load zone support, playing a significant role in maintaining the efficiency and longevity of conveyor systems. The primary function of skirting is to contain material and prevent spillage, ensuring that the load remains securely on the belt as it moves through the load zone. By doing so, skirting helps reduce material loss, minimize cleanup efforts, and protect the surrounding environment and equipment from damage.
Effective conveyor belt load zone support through skirting ensures that the material is funneled correctly onto the belt, reducing the likelihood of blockages and enhancing the overall operational efficiency of the conveyor system. For instance, in mining operations where bulk materials are handled, proper skirting is essential to manage the transfer of heavy and abrasive materials without causing excessive wear and tear on the belt and other components.
Types of Skirting Materials
Various materials are used for conveyor belt skirting, each offering distinct advantages and disadvantages. The choice of material depends on the specific requirements of the application, including the type of material being conveyed, environmental conditions, and operational demands.
Rubber Skirting
Rubber skirting is one of the most commonly used materials for conveyor belt load zone support. It is highly flexible and durable, capable of withstanding a wide range of operating conditions. Rubber skirting is particularly effective in applications where the material being conveyed is abrasive, as it can absorb impact and reduce wear on the belt.
Polyurethane Skirting
Polyurethane skirting is another popular option, known for its superior wear resistance and longevity. This material is particularly suitable for applications involving highly abrasive materials, as it offers better performance and longer service life compared to rubber.
Comparison
Installation and Maintenance
Proper installation and maintenance of conveyor belt skirting are essential to ensure effective conveyor belt load zone support. Incorrect installation can lead to gaps between the belt and the skirting, causing material spillage and reducing the overall efficiency of the conveyor system.
Best Practices for Installation
- Preparation: Ensure that the belt and the skirting surfaces are clean and free from debris. This helps in achieving a secure fit and prevents material from getting trapped between the belt and the skirting.
- Alignment: Align the skirting parallel to the belt to create a consistent seal along the entire length of the load zone. Misalignment can cause uneven wear and increase the risk of spillage.
- Tensioning: Apply the correct tension to the skirting to maintain a firm but flexible contact with the belt. Over-tensioning can cause excessive wear on both the belt and the skirting, while under-tensioning can lead to gaps and material loss.
Tips for Regular Maintenance
- Inspection: Regularly inspect the skirting for signs of wear, damage, or misalignment. Early detection of issues can prevent more significant problems and costly downtime.
- Cleaning: Keep the skirting and the surrounding areas clean to prevent buildup of material, which can cause abrasion and damage to the belt and skirting.
- Replacement: Replace worn or damaged skirting promptly to maintain effective conveyor belt load zone support. Using high-quality replacement materials, such as those from companies like Flexco or Trelleborg, can ensure longer service life and better performance.
For example, Flexco offers a range of high-performance skirting materials designed to provide superior conveyor belt load zone support. Their products are engineered to reduce maintenance requirements and extend the lifespan of both the skirting and the belt.
By adhering to these best practices and maintenance tips, industries can ensure that their conveyor belt systems operate efficiently and reliably, minimizing material loss and downtime.
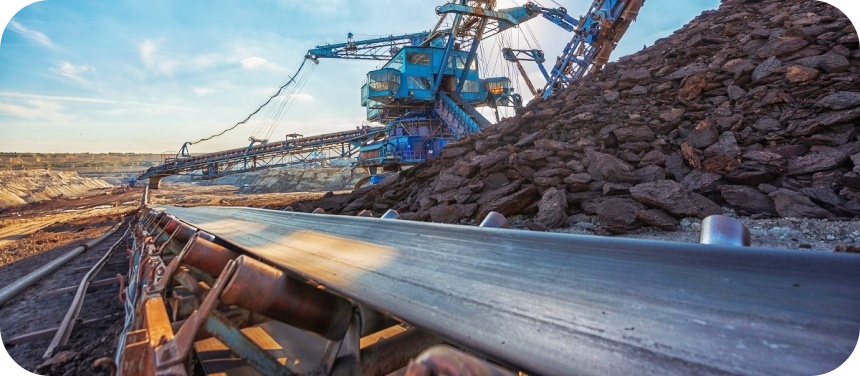
Conveyor Belt Load Zone Support: Conveyor Belt Transfer
Definition and Importance
Conveyor belt transfer points are critical junctures within conveyor systems where material is transferred from one conveyor belt to another or from one component of a conveyor system to another. These transfer points play a pivotal role in maintaining effective conveyor belt load zone support, ensuring that materials move smoothly and efficiently through the system.
The significance of efficient conveyor belt transfer points in conveyor belt load zone support cannot be overstated. Properly designed and maintained transfer points prevent material spillage, reduce dust emissions, and minimize wear and tear on the conveyor belts and other components. This not only enhances the overall efficiency of the system but also contributes to a safer working environment by reducing the risk of accidents and maintenance-related downtime. For example, in the mining industry, where large volumes of abrasive materials are handled, effective transfer points are essential to maintain continuous operations and prevent costly delays.
Types of Transfer Systems
There are several types of conveyor belt transfer systems, each designed to meet specific operational needs and challenges. Understanding these systems is essential for optimizing conveyor belt load zone support.
Chute Transfer
Chute transfer systems are among the most common methods used in conveyor systems. They are designed to guide materials from one conveyor to another by utilizing gravity. Conveyor belt chutes are typically lined with wear-resistant materials to handle the impact and abrasion from the conveyed materials.
Impact Cradle Transfer
Impact cradle transfers are designed to absorb the impact of falling materials, reducing the strain on the conveyor belt and minimizing spillage. These systems use impact bars or cradles to cushion the material as it transitions from one belt to another.
Comparison
Optimization Techniques
Optimizing conveyor belt transfer points is essential for enhancing conveyor belt load zone support. Several strategies and technologies can be employed to achieve this goal.
Advanced Technologies
Using advanced technologies such as laser alignment tools and 3D scanning can help ensure precise alignment of transfer points, reducing misalignment and wear. Additionally, incorporating automated systems for monitoring and adjusting transfer points can significantly enhance performance and reduce the need for manual intervention.
For instance, companies like Flexco and Martin Engineering offer advanced belt alignment and transfer point solutions that utilize sensors and automation to maintain optimal conveyor belt load zone support. These systems can detect misalignments or blockages in real-time and adjust the transfer points accordingly, ensuring continuous and efficient material flow.
Material Selection
Selecting the right materials for transfer points is crucial for enhancing conveyor belt load zone support. Wear-resistant materials such as UHMW (ultra-high-molecular-weight polyethylene) or AR (abrasion-resistant) steel can significantly reduce wear and extend the lifespan of transfer point components.
In high-impact areas, using rubber or polyurethane liners can help absorb shock and reduce damage to the conveyor belt. For example, Kinder Australia offers a range of high-performance wear liners and impact beds that are designed to protect conveyor belts and improve load zone support.
Design Considerations
Designing transfer points with gradual transitions and proper chute angles can help minimize material degradation and spillage. Ensuring that transfer points are adequately sized to handle the maximum load without causing blockages is also essential.
Implementing dust suppression systems at transfer points can help reduce airborne dust and improve workplace safety. Using enclosed transfer systems or adding dust curtains can effectively contain dust and prevent it from escaping into the environment.
Regular Maintenance
Regular maintenance is crucial for ensuring effective conveyor belt load zone support. Inspections should be conducted frequently to check for signs of wear, misalignment, or blockages. Promptly addressing any issues can prevent more significant problems and extend the lifespan of the conveyor system.
For example, regular inspections and maintenance of transfer points at Rio Tinto’s iron ore operations have helped the company maintain high levels of productivity and efficiency. By proactively managing wear and tear, Rio Tinto has been able to reduce downtime and improve overall operational performance.
By implementing these optimization techniques and leveraging advanced technologies, industries can significantly enhance conveyor belt load zone support, ensuring efficient and reliable material handling operations.
Conveyor Belt Load Zone Support: Conveyor Belt Trainer
Role of Conveyor Belt Trainers
Conveyor belt trainers are essential components in maintaining conveyor belt load zone support. These devices are designed to keep the conveyor belt aligned as it moves through the load zone, ensuring stability and efficient material handling. Proper alignment is critical because misaligned belts can cause significant issues, including material spillage, increased wear on belt edges, and damage to conveyor components.
Maintaining proper belt alignment through the use of conveyor belt trainers enhances load zone support by preventing the belt from drifting off course, which can lead to operational inefficiencies and safety hazards. For example, in the mining industry, where heavy and abrasive materials are commonly transported, the use of belt trainers is crucial to ensure that the belt remains in its designated path, thereby minimizing downtime and reducing maintenance costs.
Types of Trainers
Different types of conveyor belt trainers are available, each designed to address specific alignment issues and operational requirements. Understanding the various types can help in selecting the most appropriate trainer for a given application, thereby optimizing conveyor belt load zone support.
Pivoting Belt Trainers
Pivoting belt trainers are designed to automatically correct belt misalignment by pivoting around a central point. These trainers use guide rollers or sensing rollers to detect misalignment and apply corrective force to the belt, steering it back to the center.
Fixed Belt Trainers
Fixed belt trainers are stationary devices that provide a guiding mechanism for the belt. These trainers use fixed rollers or bars that the belt runs against to maintain alignment.
Adjustable Belt Trainers
Adjustable belt trainers can be manually or automatically adjusted to correct belt alignment. These trainers offer flexibility and can be fine-tuned to meet specific alignment needs.
Comparison
Installation and Maintenance
Proper installation and maintenance of conveyor belt trainers are vital to maximize conveyor belt load zone support. Following best practices ensures that trainers function effectively and prolongs their operational lifespan.
Installation Guidelines
- Positioning: Install trainers at critical points along the conveyor system, particularly before and after the load zone, to ensure continuous belt alignment.
- Alignment: Ensure that trainers are aligned correctly with the belt path. Misaligned trainers can exacerbate alignment issues instead of correcting them.
- Calibration: Calibrate adjustable trainers to the specific requirements of the belt system. Proper calibration ensures that the trainer responds correctly to misalignment.
Maintenance Tips
- Regular Inspection: Conduct regular inspections to check for wear and tear on trainers and rollers. Identifying issues early can prevent more significant problems.
- Cleaning: Keep trainers and surrounding areas clean to prevent material buildup that can affect performance. Accumulated material can obstruct the trainer’s movement and reduce its effectiveness.
- Lubrication: Ensure that moving parts of the trainers are well-lubricated to reduce friction and wear. Regular lubrication helps maintain smooth operation.
- Replacement of Worn Parts: Promptly replace any worn or damaged components. Using high-quality parts from reputable suppliers like Flexco or Martin Engineering can ensure longer service life and better performance.
For instance, Flexco offers a range of high-performance belt trainers designed to provide superior conveyor belt load zone support. Their products are engineered for durability and ease of maintenance, helping to reduce operational costs and improve overall efficiency.
By adhering to these installation and maintenance practices, industries can ensure that their conveyor belt trainers provide effective load zone support, enhancing the reliability and efficiency of their conveyor systems.
Conveyor Belt Load Zone Support: Impact Bed Conveyor
Introduction to Impact Beds
Impact beds are critical components in conveyor belt load zone support, designed to absorb and dissipate the energy from material impact as it is loaded onto the conveyor belt. By doing so, impact beds protect the conveyor belt from damage, reduce maintenance costs, and enhance the overall efficiency of the conveyor system.
The primary function of impact beds in conveyor belt load zone support is to cushion the belt and absorb the shock of falling material. This not only prevents damage to the belt but also reduces the wear and tear on the supporting structure and components. In industries such as mining, quarrying, and bulk material handling, where heavy and abrasive materials are frequently loaded onto conveyor belts, the use of impact beds is essential to maintain the integrity and performance of the conveyor system. For example, companies like Martin Engineering provide high-quality impact beds that are specifically designed to handle heavy impacts, ensuring prolonged belt life and reduced downtime.
Types of Impact Beds
There are several types of impact beds, each designed to address specific needs and applications in conveyor belt load zone support. Understanding the differences between these types is crucial for selecting the right impact bed for a particular operation.
Roller Beds
Roller beds consist of a series of rollers that support the conveyor belt and help to reduce friction as the belt moves. These beds are designed to absorb impact energy and reduce wear on the belt.
Bar Impact Beds
Bar impact beds use solid bars, often made from rubber or other resilient materials, to support the belt and absorb impact energy. These bars are typically arranged in a series to provide continuous support across the load zone.
Comparison
Installation and Maintenance
Proper installation and maintenance of impact beds are crucial for ensuring effective conveyor belt load zone support. Following best practices can enhance the performance and lifespan of impact beds, leading to reduced operational costs and improved system reliability.
Installation Steps
- Preparation: Before installation, ensure that the conveyor belt and support structure are clean and free from debris. This helps in achieving a secure fit and prevents material buildup.
- Alignment: Align the impact bed with the conveyor belt to ensure even distribution of impact forces. Misalignment can lead to uneven wear and reduce the effectiveness of the impact bed.
- Securing: Secure the impact bed to the conveyor structure using appropriate fasteners. Ensure that all bolts and connections are tight to prevent movement during operation.
- Testing: After installation, run the conveyor system to test the impact bed’s performance. Check for any signs of misalignment or unusual wear and make adjustments as necessary.
Maintenance Practices
- Regular Inspection: Conduct regular inspections to check for signs of wear or damage. Early detection of issues can prevent more significant problems and extend the life of the impact bed.
- Cleaning: Keep the impact bed and surrounding areas clean to prevent material buildup, which can cause abrasion and damage to the belt and impact bed.
- Replacement of Worn Parts: Promptly replace any worn or damaged bars or rollers. Using high-quality replacement parts, such as those from Flexco or Trelleborg, can ensure better performance and longevity.
- Lubrication: If the impact bed includes moving parts, ensure that they are well-lubricated to reduce friction and wear.
For example, at a large coal handling facility, the implementation of impact beds from Kinder Australia resulted in a significant reduction in belt damage and maintenance costs. By following a rigorous maintenance schedule, the facility was able to extend the lifespan of their conveyor belts and maintain efficient operations.
By adhering to these installation and maintenance guidelines, industries can ensure that their impact beds provide effective conveyor belt load zone support, enhancing the durability and performance of their conveyor systems.
Conveyor Belt Load Zone Support: Conveyor Belt Magnet
Purpose and Benefits
Conveyor belt magnets play a crucial role in conveyor belt load zone support by ensuring the removal of unwanted metal contaminants from the conveyed materials. These magnets are strategically placed over or near the conveyor belt to attract and capture ferrous materials that could otherwise cause significant damage to the conveyor system, downstream equipment, and the final product quality.
The primary benefit of using conveyor belt magnets in load zone support is the enhanced protection they offer. By efficiently removing metal contaminants, these magnets prevent potential damage to the conveyor belt, reduce maintenance costs, and minimize the risk of equipment downtime. This is particularly important in industries such as recycling, mining, and food processing, where metal contamination can lead to severe operational issues and product recalls. For instance, in the food industry, companies like Eriez provide high-performance magnetic separators that ensure product purity and protect processing equipment from damage.
Types of Magnets
Various types of conveyor belt magnets are available, each designed to meet specific operational needs and applications. Understanding the differences between these types can help in selecting the most suitable magnet for effective conveyor belt load zone support.
Permanent Magnets
Permanent magnets are made from materials that retain their magnetic properties over time. These magnets are typically mounted above or beneath the conveyor belt to capture ferrous metals as they pass by.
Electro-Magnets
Electro-magnets use an electric current to generate a magnetic field. These magnets can be switched on and off, allowing for greater control over the magnetic separation process.
Comparison
Installation and Maintenance
Proper installation and maintenance of conveyor belt magnets are critical to ensuring their effectiveness and longevity in providing conveyor belt load zone support. Following best practices can optimize the performance of these magnets and reduce operational disruptions.
Best Practices for Installation
- Positioning: Install the magnet at a location where it can effectively capture contaminants without obstructing the conveyor belt’s movement. Common positions include over the head pulley or at transfer points where material flow is concentrated.
- Height Adjustment: Adjust the height of the magnet to ensure optimal magnetic field strength and coverage. The magnet should be close enough to capture contaminants but not so close that it interferes with the belt.
- Securing: Secure the magnet firmly to the conveyor structure to prevent movement or vibration during operation. Use appropriate mounting hardware and supports to ensure stability.
- Testing: Conduct initial testing after installation to verify that the magnet is effectively capturing contaminants. Make any necessary adjustments to improve performance.
Maintenance Routines
- Regular Inspection: Perform regular inspections to check for signs of wear, damage, or misalignment. Inspect the magnet’s surface for accumulated contaminants and clean as necessary.
- Cleaning: Clean the magnet regularly to remove accumulated ferrous materials. For electro-magnets, ensure that the electrical components are kept clean and free from dust and debris.
- Lubrication: Lubricate any moving parts associated with the magnet’s installation, such as adjustment mechanisms, to ensure smooth operation.
- Electrical Maintenance: For electro-magnets, regularly check the electrical connections and components to ensure they are functioning correctly. Replace any worn or damaged parts promptly to prevent failures.
For example, a mining operation using Dings Co. Magnetic Group’s electro-magnets reported a significant reduction in belt damage and downtime after implementing a rigorous maintenance schedule. By regularly inspecting and maintaining their magnetic separators, they were able to maintain efficient conveyor belt load zone support and enhance overall productivity.
By following these installation and maintenance guidelines, industries can ensure that their conveyor belt magnets provide effective load zone support, protecting their conveyor systems from metal contaminants and maintaining optimal operational efficiency.
Conveyor Belt Load Zone Support: Conveyor Belt Press Machine
Role in Load Zone Support
Conveyor belt press machines are essential tools in maintaining conveyor belt load zone support, playing a crucial role in splicing and repairing conveyor belts. These machines ensure that conveyor belts remain continuous and seamless, which is vital for the efficient transfer of materials and the overall stability of the conveyor system.
Press machines contribute to conveyor belt load zone support by creating strong, durable splices that can withstand the stresses and strains of heavy loads. In industries such as mining, manufacturing, and logistics, where conveyor belts are subjected to harsh conditions and significant wear, the ability to quickly and effectively repair belts minimizes downtime and maintains operational efficiency. For example, companies like Almex Group provide advanced press machines that ensure high-quality splices, enhancing the durability and longevity of conveyor belts in load zones.
Types of Press Machines
Various types of conveyor belt press machines are available, each designed to meet specific needs and operational requirements. Understanding these different types is essential for selecting the right machine to enhance conveyor belt load zone support.
Hydraulic Press Machines
Hydraulic press machines use hydraulic power to apply pressure during the splicing process. These machines are known for their precision and ability to create strong, uniform splices
Mechanical Press Machines
Mechanical press machines use mechanical force, typically through a screw or lever system, to apply pressure during the splicing process. These machines are often more portable and easier to use in remote or field environments.
Comparison
Usage and Maintenance
Effective use and maintenance of conveyor belt press machines are crucial for maximizing their benefits and ensuring continuous conveyor belt load zone support. Following best practices can help maintain the performance and extend the lifespan of these machines.
Guidelines for Using Press Machines
- Preparation: Before using a press machine, ensure that the belt surfaces to be spliced are clean and free from debris. Proper preparation is essential for achieving a strong bond.
- Alignment: Align the belt ends accurately to avoid misalignment, which can lead to weak splices and potential failures. Use alignment tools or guides if necessary.
- Pressure Application: Apply the appropriate amount of pressure as recommended by the manufacturer. Too little pressure can result in weak splices, while too much pressure can damage the belt.
- Heating and Cooling: For vulcanizing presses, follow the specified heating and cooling times to ensure proper curing of the splice. Inconsistent temperatures can compromise the quality of the splice.
Regular Maintenance Tips
- Inspection: Regularly inspect the press machine for signs of wear, damage, or misalignment. Check the hydraulic system for leaks and ensure that all mechanical components are in good working condition.
- Cleaning: Keep the press machine clean, especially the platens and heating elements, to prevent contamination and ensure even pressure distribution.
- Lubrication: Lubricate moving parts as needed to reduce friction and wear. Follow the manufacturer’s recommendations for the type and frequency of lubrication.
- Calibration: Periodically calibrate the press machine to ensure that it applies the correct amount of pressure and heat. Calibration helps maintain the accuracy and effectiveness of the splicing process.
For example, a large manufacturing plant using the Almex Group’s hydraulic press machines reported a 30% reduction in downtime due to the machine’s reliable performance and easy maintenance. By following a rigorous maintenance schedule, the plant was able to maintain high levels of productivity and minimize belt-related issues.
By adhering to these usage and maintenance guidelines, industries can ensure that their conveyor belt press machines provide effective load zone support, enhancing the durability and performance of their conveyor systems.
Conveyor Belt Load Zone Support: Superior Conveyors
Overview of Superior Conveyors
Superior Conveyors is a leading provider of high-quality conveyor systems designed to enhance conveyor belt load zone support across various industries. Their products are known for their durability, efficiency, and innovative design, which contribute to improved material handling and reduced operational downtime.
Superior Conveyors plays a critical role in conveyor belt load zone support by offering solutions that ensure smooth material transfer, minimize spillage, and protect conveyor belts from damage. The company’s focus on advanced engineering and robust construction makes their conveyors ideal for demanding environments such as mining, aggregate processing, and bulk material handling. For instance, their custom-engineered conveyor systems are tailored to meet the specific needs of each application, ensuring optimal performance and longevity.
Product Range
Superior Conveyors offers a comprehensive range of conveyor products, each designed to address different aspects of conveyor belt load zone support. These products include impact beds, skirting systems, transfer chutes, and belt cleaners, among others.
Impact Beds
Impact beds are crucial for absorbing the energy from falling material at the load zone, preventing damage to the conveyor belt and supporting structure. Superior Conveyors’ impact beds are designed with heavy-duty construction to handle the toughest loads, ensuring maximum protection and reduced maintenance.
- Features:
- Robust steel frames
- High-impact resistant bars
- Adjustable wing angles for optimal fit
- Applications: Mining, aggregate processing, and bulk material handling
- Benefits: Enhanced belt protection, reduced downtime, and longer belt life
Skirting Systems
Skirting systems help contain material on the conveyor belt, preventing spillage and reducing cleanup efforts. Superior Conveyors offers skirting systems that provide a tight seal between the belt and the skirt board, ensuring effective material containment.
- Features:
- Flexible and durable skirting materials
- Easy installation and adjustment
- Compatibility with various conveyor belts
- Applications: Coal handling, mineral processing, and recycling
- Benefits: Improved material containment, reduced spillage, and cleaner work environments
Transfer Chutes
Transfer chutes are designed to guide material from one conveyor to another, minimizing impact and reducing material degradation. Superior Conveyors’ transfer chutes are engineered to handle high volumes of material with minimal wear and tear.
- Features:
- Wear-resistant liners
- Customizable designs
- Smooth interior surfaces to reduce friction
- Applications: Mining, ports, and industrial processing
- Benefits: Efficient material transfer, reduced wear, and lower maintenance costs
Belt Cleaners
Belt cleaners are essential for maintaining conveyor belt load zone support by removing residual material from the belt surface, preventing buildup that can cause misalignment and damage. Superior Conveyors’ belt cleaners are designed for maximum efficiency and durability.
- Features:
- High-performance blades
- Easy maintenance and replacement
- Adjustable tensioners for consistent cleaning pressure
- Applications: Aggregate processing, cement plants, and bulk material handling
- Benefits: Cleaner belts, reduced maintenance, and extended belt life
Case Studies and Examples
Superior Conveyors has a proven track record of improving conveyor belt load zone support in various industries through their innovative products and solutions. Here are some real-world examples demonstrating their impact:
Case Study 1: Mining Operation
A large mining operation in Australia faced challenges with frequent conveyor belt damage and excessive maintenance costs due to heavy impact at the load zone. Superior Conveyors provided a customized impact bed solution that significantly reduced belt wear and maintenance downtime.
- Results:
- 40% reduction in maintenance costs
- 30% increase in belt life
- Improved operational efficiency
Case Study 2: Aggregate Processing Plant
An aggregate processing plant in the United States experienced material spillage and dust issues, leading to increased cleanup efforts and reduced productivity. Superior Conveyors installed advanced skirting systems and transfer chutes, addressing the spillage and dust concerns effectively.
- Results:
- 50% reduction in material spillage
- 20% improvement in plant cleanliness
- Enhanced worker safety and productivity
Case Study 3: Recycling Facility
A recycling facility in Europe struggled with conveyor belt misalignment and buildup of residual material. Superior Conveyors implemented their belt cleaner solutions, ensuring consistent belt alignment and reducing material buildup.
- Results:
- 60% reduction in belt misalignment issues
- 25% decrease in maintenance interventions
- Increased overall equipment uptime
Superior Conveyors’ commitment to innovation and quality has made them a trusted partner in enhancing conveyor belt load zone support across various industries. By leveraging their advanced products and tailored solutions, companies can achieve improved operational efficiency, reduced maintenance costs, and prolonged equipment lifespan.
Conveyor Belt Load Zone Support: Conveyor Belt Tracking Roller
Function and Importance
Conveyor belt tracking rollers are critical components in conveyor belt load zone support, ensuring that the conveyor belt remains aligned during operation. Proper belt alignment is essential for efficient material handling, as misaligned belts can lead to significant issues such as material spillage, increased wear and tear, and damage to both the belt and the conveyor structure.
The primary function of conveyor belt tracking rollers in conveyor belt load zone support is to automatically correct any misalignment of the belt, guiding it back to the center of the conveyor system. This reduces the risk of spillage and minimizes the potential for belt damage, which can otherwise lead to costly downtime and maintenance. For example, industries such as mining and aggregate processing, where conveyors are subjected to harsh conditions and heavy loads, rely heavily on effective tracking rollers to maintain operational efficiency and safety.
Types of Tracking Rollers
There are several types of conveyor belt tracking rollers, each designed to address specific alignment challenges and operational requirements. Understanding the different types and their applications is crucial for selecting the right tracking roller to enhance conveyor belt load zone support.
Self-Aligning Tracking Rollers
Self-aligning tracking rollers are designed to automatically adjust and correct the belt’s alignment without manual intervention. These rollers pivot and tilt based on the belt’s movement, guiding it back to the center.
- Applications: Ideal for heavy-duty applications where belts frequently become misaligned due to heavy loads or varying material types.
- Benefits:
- Reduces manual adjustments and maintenance
- Improves belt alignment and reduces wear
- Enhances overall conveyor belt load zone support by maintaining consistent belt tracking
- Examples: The Flexco PTEZ™ Belt Trainer is a self-aligning tracking roller that uses pivot and tilt technology to ensure reliable belt tracking.
Adjustable Tracking Rollers
Adjustable tracking rollers can be manually set to correct belt misalignment. These rollers offer greater control and flexibility, allowing operators to fine-tune the alignment based on specific operational needs.
- Applications: Suitable for applications where belt conditions vary and require frequent adjustments, such as in manufacturing and logistics.
- Benefits:
- Provides precise control over belt alignment
- Can be adjusted to accommodate different belt speeds and loads
- Enhances conveyor belt load zone support by allowing tailored alignment solutions
- Examples: The Martin Tracker™ from Martin Engineering is an adjustable tracking roller that provides precise control over belt alignment for various applications.
Installation and Maintenance
Proper installation and maintenance of conveyor belt tracking rollers are essential to ensure effective conveyor belt load zone support. Following best practices can optimize the performance and longevity of these rollers, reducing operational disruptions and maintenance costs.
Best Practices for Installation
- Positioning: Install tracking rollers at critical points along the conveyor system, particularly before and after the load zone, to ensure continuous belt alignment.
- Alignment: Ensure that tracking rollers are aligned correctly with the belt path. Incorrect alignment can exacerbate misalignment issues instead of correcting them.
- Securing: Secure the tracking rollers firmly to the conveyor structure to prevent movement or vibration during operation. Use appropriate mounting hardware and supports to ensure stability.
- Calibration: Calibrate adjustable tracking rollers to the specific requirements of the conveyor system. Proper calibration ensures that the roller responds correctly to misalignment.
Maintenance Tips
- Regular Inspection: Conduct regular inspections to check for signs of wear, damage, or misalignment. Early detection of issues can prevent more significant problems and extend the life of the tracking rollers.
- Cleaning: Keep tracking rollers and the surrounding areas clean to prevent material buildup that can affect performance. Accumulated material can obstruct the roller’s movement and reduce its effectiveness.
- Lubrication: Ensure that moving parts of the tracking rollers are well-lubricated to reduce friction and wear. Regular lubrication helps maintain smooth operation.
- Replacement of Worn Parts: Promptly replace any worn or damaged components. Using high-quality replacement parts from reputable suppliers, such as Flexco or Martin Engineering, can ensure better performance and longevity.
For example, a coal mining operation utilizing self-aligning tracking rollers from Flexco reported a significant reduction in belt misalignment issues, leading to a 25% decrease in maintenance interventions and a 15% increase in operational uptime. By implementing a rigorous maintenance schedule and using high-quality tracking rollers, the operation was able to maintain efficient conveyor belt load zone support.
Effective use and maintenance of conveyor belt tracking rollers are crucial for ensuring continuous and efficient conveyor belt load zone support. By following best practices and utilizing the right type of tracking roller for specific applications, industries can enhance the reliability and performance of their conveyor systems, leading to reduced maintenance costs and improved operational efficiency.
Get personalized support for your conveyor belt requirements by filling out this form.
FAQs about Conveyor Belt Load Zone Support
In the context of conveyor belt load zone support, the support structure is a critical component designed to stabilize the conveyor belt and the material it carries. This structure typically includes components such as impact beds, idlers, and skirting systems. Impact beds are used to absorb the energy from heavy loads dropping onto the belt, preventing damage and reducing wear. Idlers, which are rollers that support the belt, help maintain alignment and minimize sagging under the weight of the load. Skirting systems are installed along the sides of the belt to prevent material spillage and ensure that the load remains securely on the belt. Together, these elements provide comprehensive conveyor belt load zone support, ensuring efficient and reliable operation of the conveyor system in industrial environments such as mining and manufacturing.
Impact load zone idlers play a significant role in enhancing conveyor belt load zone support by absorbing the shock and impact from heavy materials falling onto the belt. These specialized idlers are designed with cushioning materials that reduce the stress and strain on the conveyor belt, thereby preventing premature wear and tear. By mitigating the impact forces, these idlers help maintain the integrity of the belt, reducing maintenance costs and extending the belt’s lifespan. Additionally, impact load zone idlers ensure smooth material transfer, minimizing spillage and maintaining the efficiency of the conveyor system. In installations where heavy or abrasive materials are transported, such as in mining or aggregate processing, the use of impact load zone idlers is crucial for maintaining continuous operation and reducing downtime. Overall, these idlers are essential for effective conveyor belt load zone support, providing durability and reliability in demanding industrial applications.
Calculating conveyor belt load is essential for ensuring effective conveyor belt load zone support and involves several factors. Firstly, you need to determine the cross-sectional area of the load on the belt, which depends on the belt width and the loading conditions. This can be calculated using the formula: Load (kg/m) = Belt Width (m) x Load Height (m) x Load Density (kg/m³). Next, calculate the total load carried by the conveyor by multiplying the load per meter by the conveyor length. Additionally, it’s important to consider the belt speed, the material’s bulk density, and the conveyor belt rubber density to ensure the belt’s strength and durability are adequate for the specific application. These calculations help in selecting the appropriate conveyor belt and support structures, such as impact beds and idlers, to handle the load efficiently. Accurate load calculations are crucial for optimizing conveyor belt load zone support, as they ensure the conveyor system operates within its design limits, preventing overloading and reducing the risk of belt failure and maintenance issues.
In terms of conveyor belt load zone support, several requirements must be met to ensure efficient and reliable operation. Firstly, the conveyor belt must be durable and capable of handling the specific type of material being transported, whether it’s abrasive, heavy, or sharp. The belt should also be compatible with the impact beds and idlers used in the load zone to minimize wear and extend the belt’s lifespan. Proper skirting is essential to prevent material spillage and maintain a clean, safe working environment. Additionally, the conveyor system should be designed with adequate belt tension and alignment mechanisms to prevent sagging and misalignment, which can cause operational inefficiencies and increase maintenance costs. Regular inspection and maintenance are required to ensure that all components, including the belt, idlers, and impact beds, are functioning correctly and not showing signs of excessive wear or damage. Meeting these requirements is crucial for effective conveyor belt load zone support, optimizing the performance and longevity of the conveyor system in industrial applications.
Last Updated on August 2, 2024 by Jordan Smith
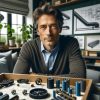
Jordan Smith, a seasoned professional with over 20 years of experience in the conveyor system industry. Jordan’s expertise lies in providing comprehensive solutions for conveyor rollers, belts, and accessories, catering to a wide range of industrial needs. From initial design and configuration to installation and meticulous troubleshooting, Jordan is adept at handling all aspects of conveyor system management. Whether you’re looking to upgrade your production line with efficient conveyor belts, require custom conveyor rollers for specific operations, or need expert advice on selecting the right conveyor accessories for your facility, Jordan is your reliable consultant. For any inquiries or assistance with conveyor system optimization, Jordan is available to share his wealth of knowledge and experience. Feel free to reach out at any time for professional guidance on all matters related to conveyor rollers, belts, and accessories.