Advanced Conveyor Belt Material Selection Tips
Selecting the right conveyor belt material is a crucial decision that significantly impacts the efficiency and safety of various industrial applications. The performance of a conveyor system hinges on its compatibility with the materials it handles, as well as the environment in which it operates. This blog post delves into the intricacies of conveyor belt material selection, providing valuable insights to aid in choosing the most suitable materials. Utilizing resources such as material selection charts, real-world examples, and formulae, this guide aims to equip you with the knowledge needed to make informed decisions. Whether you’re involved in mining, food processing, or manufacturing, understanding these selections is key to optimizing conveyor system performance.
Conveyor Belt Material Selection Basics
Conveyor belts are an essential component of modern manufacturing and logistics. They facilitate the transport and handling of materials over short to long distances within a site, enhancing efficiency and reducing labor costs. This guide covers the basics of conveyor belt material selection and outlines the fundamental purposes and common materials used in conveyor belt manufacturing.
Fundamental Purposes of Conveyor Belts in Industries
- Transportation of Goods: Conveyor belts are primarily used to transport goods from one point to another within an industrial setting.
- Assembly Line Operations: They are crucial in assembly lines, allowing for the sequential assembly of parts through workstations.
- Sorting Processes: Belts can be equipped with sensors and other devices to sort products based on size, weight, or type.
- Packaging: Conveyor systems streamline the packaging process by moving products through various packaging stages efficiently.
- Loading and Unloading: Belts are used in loading and unloading processes, reducing the need for manual labor and speeding up operations.
- Distribution Centers: They help in managing inventory and orders in warehouses and distribution centers by moving goods across different sections.
- Inspection and Testing: Conveyor belts are used to move products through inspection and testing procedures, ensuring quality control.
- Food Processing: In the food industry, conveyor belts are used for processes like washing, slicing, and packing, adhering to health and safety standards.
Common Materials Used in Conveyor Belt Manufacturing
When considering conveyor belt material selection, it’s essential to understand the properties and applications of each material:
- Rubber: Rubber belts are among the most common due to their durability and flexibility. They are suitable for carrying heavy loads at high speeds.
- PVC: PVC belts are best for general light industry applications. They are resistant to abrasion, chemicals, and moisture.
- Polyurethane (PU): Known for its hygienic qualities, PU is often used in food processing industries. It’s resistant to oils, fats, and chemicals.
- Silicone: Ideal for high-temperature applications, silicone belts are used in baking and drying processes.
- Teflon: Teflon is used in applications that require high heat resistance, such as ovens and cooling tunnels.
- Metal: Metal belts are durable and resistant to extreme temperatures; they are used in applications requiring a high degree of cleanliness and thermal resistance.
- Nylon: Known for its high strength and excellent abrasion resistance, nylon belts are typically used in heavy-duty applications.
- Kevlar: Used in applications where high strength, low stretch, and resistance to heat are required. Kevlar is often used in manufacturing conveyor belts for mining and industrial applications.
Each material offers different benefits and is suited to specific industrial applications. The key to effective conveyor belt material selection lies in understanding the operational environment, the nature of the material to be transported, and the specific needs of the industry. Choosing the right material enhances the belt’s functionality, efficiency, and longevity, impacting overall production and operational costs.
Conveyor Belt Material Selection: Types of Conveyor Belt Materials
In the realm of conveyor belt material selection, understanding the different types of materials available is essential. Each material type offers distinct properties and benefits, making it suitable for specific applications and operational conditions. Here’s a detailed look at the main types of materials used in conveyor belts, highlighting their characteristics and typical uses:
In conveyor belt material selection, choosing the right material type not only enhances the efficiency but also extends the lifespan and safety of the conveyor system. This table serves as a guide to match the material characteristics with the operational demands of various industries.
Conveyor Belt Material Selection: Factors to Consider
When it comes to conveyor belt material selection, several critical factors must be considered to ensure optimal performance and longevity. This selection process is crucial because the right material affects the efficiency, cost, and maintenance needs of the conveyor system. Here, we discuss 10 key factors that influence conveyor belt material selection:
- Load Weight and Type: The weight and type of materials being transported are paramount. Heavier loads require more robust and thicker belts, typically made from materials that can withstand substantial stress without deforming or breaking. Additionally, the type of load—whether it’s sharp-edged materials or fine grains—determines the surface texture and composition of the belt material to prevent damage or slippage.
- Environmental Conditions: The environment where the conveyor will operate significantly impacts the material choice. For instance, belts used in outdoor or refrigerated environments should be resistant to weathering, ultraviolet light, and low temperatures. Similarly, belts used in chemical plants or places where oils, greases, or other chemicals are prevalent require materials resistant to chemical attack to prevent degradation.
- Temperature Tolerance: Conveyor belts operate in various temperatures, and selecting a material that can handle these conditions is crucial. Materials like silicone are suited for high-temperature environments, whereas PVC belts are better for lower temperatures.
- Chemical Exposure: Belts exposed to chemicals need to be made from materials that can resist corrosion. For example, rubber belts can be treated to resist acids, bases, and solvents, making them suitable for use in chemical processing plants or in applications where the belt may come into contact with oils or greasy materials.
- Speed of Conveyor Operations: The speed at which the conveyor operates also affects the material selection. High-speed belts require materials that minimize friction and wear and can handle the dynamic stresses placed upon them.
- Duration of Conveyor Operations: For operations that run continuously, durability becomes a critical factor. Materials that can withstand constant wear and tear without frequent maintenance are preferred.
- Maintenance Requirements: Some materials may require more frequent maintenance than others. For instance, fabric belts might need regular adjustments and cleaning to ensure they function correctly, whereas metal belts might need less maintenance but are more challenging to repair.
- Durability: The overall durability of the belt material is crucial, especially in industrial applications where downtime can be costly. Materials that are prone to abrasion, cuts, or general wear should be avoided in harsh environments.
- Flexibility and Bend Radius: The material’s flexibility affects how it handles curves and transfers in the conveyor system. Materials that are too rigid may not perform well in systems requiring sharp bends, whereas more flexible materials may handle these challenges more effectively.
- Cost-Efficiency: Finally, the cost of materials must be considered. While it’s important to choose a material that meets the operational requirements, it must also fit within the budget constraints of the project. Often, more durable materials are more expensive upfront but may offer savings over time due to lower maintenance costs and longer service life.
Considering these factors during conveyor belt material selection is essential for developing an efficient, cost-effective, and durable conveyor system. Each factor interplays with the others, and the best choices will vary depending on the specific needs and conditions of the application.
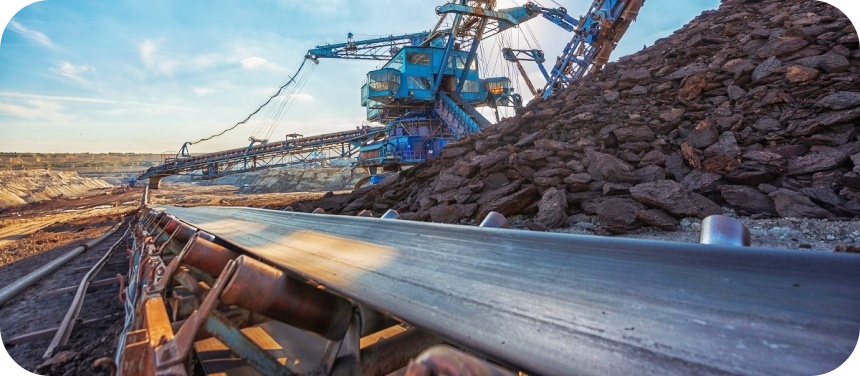
Conveyor Belt Material Selection Tools
Selecting the right conveyor belt material is pivotal for ensuring operational efficiency and longevity of the conveyor system. To assist in this critical process, a variety of conveyor belt material selection tools are available. These tools are designed to match conveyor belt materials with the specific requirements of your application, ensuring optimal performance and durability. Here’s an overview of the key tools that can facilitate effective conveyor belt material selection:
Material Selection Charts
Material selection charts are essential tools in conveyor belt material selection. These charts provide a comprehensive comparison of different materials based on their properties such as tensile strength, abrasion resistance, chemical compatibility, and temperature tolerance. To use these charts, identify the requirements of your application—consider factors like the type of goods being transported, environmental conditions, and the belt’s operational speed. Match these requirements against the properties listed in the chart to find the most suitable material options.
PDF Guides
PDF guides are invaluable resources that offer detailed information on conveyor belt materials. These guides typically include data sheets, performance metrics, and case studies. They provide an in-depth look at how different materials perform under various conditions and can help you understand the trade-offs and benefits of each material type. These guides are often available for download from manufacturers’ websites and can be an excellent starting point for making informed decisions in conveyor belt material selection.
Material Selection Formula
The material selection formula is a set of calculations used to determine the suitability of a conveyor belt material based on its mechanical properties. This formula can help calculate the expected performance of a material under given load conditions, factoring in aspects like belt speed, weight of the materials being transported, and the environmental conditions. By inputting specific operational parameters, the formula helps predict which materials will provide the best performance and durability for your specific needs.
Utilizing these conveyor belt material selection tools can significantly streamline the process of choosing the right material for your conveyor system, ensuring that it is tailored to meet the demands of your operational environment and application needs.
Practical Examples of Applications and Conveyor Belt Material Selection
In the realm of industrial automation, understanding the principles of conveyor belt material selection is crucial for the effective deployment of conveyor systems across various industries. Here, we present six practical examples where specific conveyor belt materials have been selected to meet the unique requirements of different applications:
- Food Processing Conveyors: In food processing, conveyor belts must comply with strict hygiene and safety standards. FDA-approved materials, such as food-grade PVC or urethane, are commonly used. These materials are non-toxic, easy to clean, and resistant to oils, fats, and various chemicals that are often present in food manufacturing. This ensures that there is no contamination and that the belts can withstand the rigorous cleaning protocols.
- Mining Conveyors: Mining requires conveyor belts that are exceptionally durable and abrasion-resistant to handle the heavy and rough materials. Materials such as heavy-duty rubber, reinforced with metal or other strong fibers, are chosen to endure the harsh environments of mining operations. This selection is crucial for maintaining operational efficiency and extending the lifespan of the conveyor system under extreme conditions.
- Packaging Industry Conveyors: In the packaging industry, preventing static electricity build-up is essential to protect electronic products and components from static discharge. Anti-static materials, like certain types of rubber or specially treated fabrics, are used in conveyor belts to ensure safety and efficiency. This conveyor belt material selection not only enhances safety but also improves the reliability of the packaging process.
- Airport Baggage Handling Systems: Conveyor belts in airports need to be robust, with high tensile strength to handle the heavy load of luggage. Materials such as polyester or nylon are chosen for their durability and resistance to wear and tear. Additionally, these materials can be designed to handle the various shapes and sizes of luggage smoothly, which is crucial for minimizing delays in baggage handling.
- Automotive Assembly Lines: In the automotive industry, conveyor belts must support heavy components and endure oil and other industrial fluids. Synthetic rubber belts, often reinforced with metal or other materials, are used for their resistance to oils, heat, and abrasion. This ensures that the conveyor system can operate continuously without frequent maintenance interruptions.
- Pharmaceutical Conveyors: For pharmaceutical applications, conveyor belts must not only be easy to clean but also resistant to the aggressive cleaning agents used in this industry. Silicone conveyor belts are often used because they can withstand high temperatures during sterilization processes and do not react with the pharmaceutical products or cleaning chemicals.
Each of these examples demonstrates how conveyor belt material selection is integral to the functionality and success of conveyor systems in different environments. By selecting the appropriate material, industries can enhance efficiency, reduce maintenance costs, and extend the operational lifespan of their conveyor systems.
Where to Find Conveyor Belt Materials for Optimal Selection
When embarking on conveyor belt material selection, identifying reliable suppliers and manufacturers is crucial. This section provides guidance on how to locate the best sources for conveyor belt materials and offers 12 practical tips to help you select the right supplier. Here are eight ways to find leading suppliers and manufacturers of conveyor belt materials:
- Industry Trade Shows: Attending industry-specific trade shows is an excellent way to meet multiple suppliers and manufacturers in one place. These events provide a platform to compare products, discuss customization options, and establish business relationships.
- Online Directories: Utilize online directories that list manufacturers and suppliers of industrial products, including conveyor belt materials. These directories often provide comprehensive information about the suppliers, including their product range, location, and contact information.
- Industry Associations: Join industry associations which can provide resources and connections to reputable suppliers within the conveyor belt manufacturing sector. Associations often have a list of recommended suppliers that adhere to industry standards.
- B2B Marketplaces: Explore B2B marketplaces that cater to industrial goods. These platforms can offer a variety of suppliers with detailed profiles, including reviews and ratings from previous customers, which can help in making an informed decision.
- Supplier Websites: Visit the websites of known manufacturers for detailed information on their product offerings, material specifications, and potential for customization. Most suppliers provide detailed product catalogs and case studies on their websites.
- Referrals: Ask for referrals from business contacts within your industry. Recommendations from peers can be invaluable as they come with first-hand experience regarding the reliability and quality of the supplier.
- Social Media and Forums: Leverage social media platforms and professional forums where industry experts gather to discuss their experiences and preferences regarding conveyor belt materials and suppliers.
- Local vs. Global Suppliers: Consider both local and global suppliers. Local suppliers might offer quicker delivery times and lower shipping costs, while global suppliers might provide cost advantages or access to more specialized materials not available locally.
Tips on Selecting a Supplier
When narrowing down your options for a supplier during conveyor belt material selection, consider the following tips to ensure you choose the best possible source:
- Location: Proximity to your operations can affect delivery times and shipping costs.
- Product Range: Ensure the supplier has a broad range of materials and can provide the specific type you need.
- Customization Options: Some applications may need customized solutions, so choose a supplier who can accommodate these needs.
- Experience and Reputation: Look for suppliers with proven experience and a good reputation in the market.
- Quality Certifications: Check for quality standards like ISO certifications to ensure high-quality products.
- Technical Support: Choose suppliers who offer strong technical support and customer service.
- Cost: While cost is important, consider the total value offered by the supplier, including product quality and after-sales service.
- Lead Times: Evaluate the supplier’s ability to meet your timelines.
- Minimum Order Quantities: Consider whether the supplier’s minimum order requirements align with your needs.
- Sustainability Practices: If sustainability is important to your company, look for suppliers with eco-friendly practices.
- Payment Terms: Understand and negotiate payment terms that are favorable.
- Sample Availability: Request samples to assess quality before making a large order.
By considering these factors during your conveyor belt material selection process, you can establish a reliable supply chain that supports your operational needs effectively.
Need custom conveyor belts? Contact us for tailored solutions!
FAQs about Conveyor Belt Material Selection
Conveyor belts can be made from a variety of materials, each chosen based on the application and the material’s specific properties. The most common materials include rubber, PVC, polyurethane, neoprene, nylon, polyester, leather, and metals such as steel and stainless steel. Rubber belts are popular for general use due to their durability and flexibility. PVC conveyor belts are chosen for their resistance to chemicals and abrasion. Polyurethane belts are preferred in food processing for their compliance with hygiene standards and ease of cleaning. Metal belts are used in applications requiring high strength, durability, and heat resistance. The material selection directly impacts the conveyor belt’s performance, longevity, and suitability for specific tasks.
To make a conveyor belt, several components are required, combining to create a durable and functional conveying medium. The primary materials include:
Base Material: This forms the backbone of the belt, with common options being fabrics like polyester or nylon, or metals.
Coating or Cover Material: Often, the base material is coated or covered with materials like PVC, polyurethane, rubber, or neoprene for added properties such as grip, chemical resistance, or strength.
Reinforcement: This might be necessary for belts that bear heavy loads or operate in harsh conditions. Materials for reinforcement can include steel, Kevlar, or additional layers of fabric.
Adhesives and Fasteners: These components are used to join ends of the belt material or attach additional features to the belt.
Manufacturing a conveyor belt involves precise engineering to ensure that the belt withstands operational stresses while efficiently moving materials.
Choosing a conveyor belt involves several considerations to ensure it fits the intended application effectively. Factors to consider include:
Material to be conveyed: The type, weight, and characteristics of the material can significantly influence belt choice. Sharp or hot objects, for instance, might require metal belts, whereas polyurethane belts are suitable for food items.
Conveying environment: Consider environmental factors such as temperature, presence of chemicals, and moisture. Certain materials perform better under specific conditions.
Load Capacity: Ensure the belt is capable of handling the load’s weight and volume without excessive stretching or breaking.
Speed and Direction: The belt’s material and design must accommodate the operation’s required speed and direction changes.
Maintenance and Durability: Opt for materials that offer ease of maintenance and durability within your operational constraints to ensure a cost-effective choice.
Consultation with manufacturers or experts can help pinpoint the best material and design for your specific needs.
The “best” material for a conveyor system varies based on application requirements, including the nature of materials being transported, environmental conditions, and operational demands. For general applications, rubber and PVC are widely preferred for their versatility and cost-efficiency. For food processing or pharmaceuticals, materials like polyurethane and certain grades of plastics that comply with hygiene standards are ideal. In harsh environments dealing with high temperatures or corrosive substances, metal or specially coated materials might be necessary. Ultimately, the best material is one that optimally balances performance, longevity, maintenance requirements, and cost for the specific use case. Assessing operational requirements and consulting with conveyor system experts or manufacturers is crucial in selecting the most appropriate material.
Last Updated on July 16, 2024 by Jordan Smith
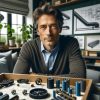
Jordan Smith, a seasoned professional with over 20 years of experience in the conveyor system industry. Jordan’s expertise lies in providing comprehensive solutions for conveyor rollers, belts, and accessories, catering to a wide range of industrial needs. From initial design and configuration to installation and meticulous troubleshooting, Jordan is adept at handling all aspects of conveyor system management. Whether you’re looking to upgrade your production line with efficient conveyor belts, require custom conveyor rollers for specific operations, or need expert advice on selecting the right conveyor accessories for your facility, Jordan is your reliable consultant. For any inquiries or assistance with conveyor system optimization, Jordan is available to share his wealth of knowledge and experience. Feel free to reach out at any time for professional guidance on all matters related to conveyor rollers, belts, and accessories.