Conveyor Belt Material Standard Grades
In the world of manufacturing and logistics, the quality and specifications of conveyor belts can significantly impact the efficiency and safety of operations. This is where understanding the conveyor belt material standard becomes crucial. These standards are not just guidelines but essential criteria that ensure conveyor belts are suitable for their intended use, enhancing reliability and performance across various industries. This blog aims to delve into the specifics of these material standards and provide an in-depth look at how they influence the design and selection of conveyor belts. By grasping the importance of the conveyor belt material standard, businesses can make more informed decisions, leading to improved productivity and safety in their operations.
What are Conveyor Belt Material Standards
Conveyor belt material standards are guidelines and specifications established to ensure the quality, performance, and safety of conveyor belts used in various industries. These standards cover the properties of materials used in belt construction, including tensile strength, abrasion resistance, heat resistance, and other relevant factors. Understanding these standards is crucial for selecting the right conveyor belt material for specific applications.
Key Conveyor Belt Material Standards
ISO 14890: Conveyor belt material standard – Specification for Rubber or Plastics-Covered ect Conveyor Belts.
- Scope: This standard specifies the dimensions and performance criteria for conveyor belts with rubber or plastic covers. It includes details on conveyor belt thickness, tensile strength, and elongation at break.
- Key Features:
- Tensile Strength: Minimum tensile strength requirements for different classes of belts.
- Elongation: Specifies allowable elongation limits under load to ensure belt stability.
- Adhesion Strength: Requirements for the adhesion strength between belt layers to prevent delamination.
- Testing Methods: Standardized methods for testing the physical properties of conveyor belts.
DIN 22102: Conveyor Belts with Textile Plies for Bulk Goods
- Scope: This German standard covers the specifications for conveyor belts with textile reinforcement layers, including fabric belts used in bulk material handling.
- Key Features:
- Fabric Type: Specifies the type and properties of textile plies, including polyester and nylon.
- Belt Thickness: Minimum and maximum thickness requirements based on the belt type.
- Tensile Strength: Defined tensile strength and elongation limits for various belt categories.
- Abrasion Resistance: Specifies abrasion resistance criteria to ensure the durability of the belt under heavy use.
AS 1332: Conveyor Belting – Textile Reinforced
- Scope: This Australian standard provides specifications for textile-reinforced conveyor belting used in general material handling.
- Key Features:
- Classification: Classification of belts based on their tensile strength and number of fabric plies.
- Cover Quality: Requirements for the quality of rubber covers in terms of tensile strength and elongation.
- Heat and Flame Resistance: Standards for belts used in high-temperature or fire-prone environments.
- Test Procedures: Defined test procedures for assessing the mechanical and physical properties of the belts.
CEMA (Conveyor Equipment Manufacturers Association) Standards
- Scope: CEMA provides a range of standards for conveyor belts used in bulk material handling, including belt design, safety, and performance criteria.
- Key Features:
- Belt Load Capacity: Guidelines for determining the appropriate belt size and strength based on load capacity.
- Design Parameters: Specifications for belt speed, tension, and other design factors to ensure safe and efficient operation.
- Safety Standards: Recommendations for safety features, including emergency stop mechanisms and belt tracking systems.
ISO 340: Conveyor Belts – Laboratory Scale Flammability Characteristics
- Scope: This standard specifies a test method for determining the flammability characteristics of conveyor belts, crucial for applications where fire safety is a concern.
- Key Features:
- Flammability Test: Describes a test method to assess the belt’s resistance to ignition and flame propagation.
- Safety Classification: Classifies belts based on their flammability properties, helping users choose the right belt for fire-prone environments.
BS 490: Conveyor Belts – Mechanical Fasteners
- Scope: This British Standard provides specifications for mechanical fasteners used in conveyor belts, ensuring they meet performance and safety criteria.
- Key Features:
- Fastener Strength: Minimum strength requirements for different types of fasteners.
- Compatibility: Guidelines for ensuring that fasteners are compatible with the belt material and thickness.
- Corrosion Resistance: Standards for fasteners to ensure they resist corrosion in various environmental conditions.
JIS K 6322: Conveyor Belts – Specification for Rubber Conveyor Belts
- Scope: This Japanese Industrial Standard covers the specifications for rubber conveyor belts, focusing on material properties and performance.
- Key Features:
- Rubber Quality: Specifies the quality and composition of rubber used in conveyor belts.
- Tensile and Elongation Properties: Defined limits for tensile strength and elongation under load.
- Durability Testing: Methods for testing the durability and wear resistance of the belt material.
Importance of Conveyor Belt Material Standards
- Ensuring Quality: Standards help ensure that conveyor belts meet minimum quality requirements, providing confidence in their performance and longevity.
- Safety Compliance: Compliance with standards, especially those related to fire resistance and load capacity, ensures that the conveyor belts operate safely under specified conditions.
- Global Consistency: International standards like ISO and DIN provide a consistent framework for manufacturers and users across the globe, facilitating trade and ensuring compatibility.
- Performance Optimization: By adhering to material standards, companies can select conveyor belts that are optimized for specific applications, reducing downtime and maintenance costs.
- Efficiency: Standards ensure that the materials used are optimal for specific functions, which can enhance the efficiency of conveyor systems by reducing maintenance needs and downtime.
- Durability: By specifying materials that are resistant to wear, tear, and environmental conditions, these standards help in extending the life of conveyor belts.
- Cost-Effectiveness: Durable and efficient conveyor belts reduce the need for frequent replacements, thus saving costs in the long run.
- Regulatory Compliance: Meeting conveyor belt material standards is often necessary for compliance with health and safety regulations in many industries.
- Quality Assurance: These standards provide a benchmark for quality, helping businesses to choose high-quality materials that meet their specific needs.
- Innovation: Standards often encourage manufacturers to develop new materials and technologies that meet or exceed existing standards.
- Interchangeability: With standardized materials, parts from different manufacturers can be used reliably in the same system, increasing flexibility for equipment maintenance and repair.
- Global Trade: Standards facilitate international trade by ensuring that products meet the safety and quality requirements of markets worldwide.
- Environmental Impact: Some standards also include guidelines on environmental impact, helping manufacturers to choose materials that are less harmful to the environment.
Conveyor belt material standards are essential for guiding the selection, design, and use of conveyor belts across various industries. These standards ensure that the belts meet the necessary criteria for strength, durability, safety, and performance, thereby enabling reliable and efficient operation in different applications. Understanding and adhering to these standards is crucial for manufacturers, suppliers, and users to ensure the success and safety of their conveyor systems.
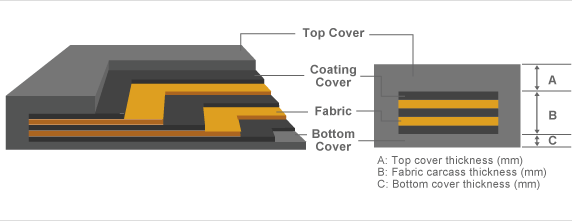
Conveyor Belt Material Standard Grades & What They’re Used For
Conveyor belts are critical components in various industries, and their material and construction are crucial for ensuring efficiency, durability, and safety. Different standard grades of conveyor belt materials are used depending on the application and environmental conditions. Here’s a detailed overview of the standard grades and their typical uses:
Grade M (General Purpose)
- Material: Made from a blend of natural and synthetic rubber.
- Properties: Moderate abrasion resistance, suitable for general conveying applications.
- Uses: Commonly used in industries like agriculture, mining, and general material handling where moderate resistance to wear and tear is required.
Grade N (General Purpose)
- Material: Similar to Grade M but with slightly lower abrasion resistance.
- Properties: Offers decent durability and cost-effectiveness.
- Uses: Used in applications where the conveyor belt is not exposed to extreme wear or temperature, such as packaging, logistics, and some light industrial uses.
Grade A (Abrasion Resistant)
- Material: Typically made from a higher concentration of natural rubber or specially formulated synthetic compounds.
- Properties: High abrasion resistance, designed to withstand heavy wear and tear.
- Uses: Ideal for conveying abrasive materials like sand, gravel, rocks, and other rough substances in industries such as mining, quarrying, and construction.
Grade S (Super Abrasion Resistant)
- Material: Advanced synthetic rubber compounds.
- Properties: Superior abrasion resistance, higher than Grade A, and also offers good tensile strength and elongation properties.
- Uses: Used in the most demanding applications involving highly abrasive materials. Common in mining, heavy-duty industrial applications, and where long-lasting performance is crucial.
Grade E (Heat Resistant)
- Material: Specially formulated rubber compounds that resist degradation at high temperatures.
- Properties: Capable of withstanding continuous exposure to high temperatures without significant loss of tensile strength or elongation.
- Uses: Used in industries like cement plants, steel mills, and foundries, where materials at elevated temperatures need to be conveyed.
Grade F (Fire Resistant)
- Material: Special flame-retardant compounds, often containing chloroprene or other halogenated materials.
- Properties: Provides resistance to fire, preventing the conveyor belt from catching fire and reducing the risk of fire spreading along the conveyor system.
- Uses: Critical in underground mining, especially in coal mines, where fire safety is a major concern. Also used in power plants and chemical processing industries.
Grade R (Oil Resistant)
- Material: Nitrile rubber or similar oil-resistant synthetic compounds.
- Properties: Resistant to oils, fats, and chemicals, which can otherwise degrade or damage standard rubber belts.
- Uses: Common in food processing, wood handling, and recycling industries where the conveyor belt may come into contact with oily or greasy materials.
Grade T (Tear Resistant)
- Material: Specially reinforced rubber with high tensile strength fibers.
- Properties: High resistance to tearing and impact, providing durability in harsh environments.
- Uses: Ideal for conveying sharp or jagged materials like broken glass, scrap metal, or sharp rocks. Used in recycling plants, glass manufacturing, and metal processing industries.
Grade W (Wear Resistant)
- Material: Often includes a blend of high-quality natural rubber or advanced synthetic materials.
- Properties: Enhanced resistance to wear, providing a longer lifespan in applications where belt wear is a concern.
- Uses: Suited for carrying bulky, heavy, or abrasive materials in industries like agriculture, forestry, and mining.
Food-Grade Belts
- Material: Typically made from PVC, PU, or other FDA-approved materials.
- Properties: Designed to meet strict hygiene standards, these belts are non-toxic, easy to clean, and resistant to bacterial growth.
- Uses: Widely used in the food processing industry, pharmaceuticals, and any application where product contamination must be minimized.
Each grade of conveyor belt material is designed to meet specific needs, whether it’s resisting abrasion, heat, oil, or fire. Selecting the right grade is essential for optimizing the performance and longevity of the conveyor belt in any given application. Understanding these standard grades allows industries to choose the most appropriate material for their specific conveyor system, ensuring efficiency, safety, and cost-effectiveness.
Conveyor Belt Material Standard: the Best General-Purpose Conveyor Belt Material
When it comes to selecting the best general-purpose conveyor belt material, Grade M and Grade N are commonly recognized as the most versatile options. These materials offer a balance between cost, durability, and performance, making them suitable for a wide range of applications across various industries. Here’s why these grades are often considered the best for general-purpose use:
Grade M (General Purpose)
- Material Composition: Grade M belts are made from a blend of natural and synthetic rubber, designed to offer moderate abrasion resistance.
- Advantages:
- Versatility: Grade M belts are suitable for most common conveyor applications, including material handling, agriculture, and light industrial use.
- Durability: They offer a good balance of durability and flexibility, making them effective in environments where the belt is subject to regular wear and tear but not extreme conditions.
- Cost-Effective: Grade M belts are generally affordable, making them a cost-effective solution for many industries.
- Typical Uses: Conveying bulk materials like grains, wood chips, or coal in industries such as agriculture, mining, and packaging.
Grade N (General Purpose)
- Material Composition: Similar to Grade M, but with a slightly different blend of rubber, offering a slight variation in abrasion resistance and elasticity.
- Advantages:
- Broad Application Range: Grade N belts are ideal for applications where the belt is not exposed to extreme conditions, such as moderate temperatures or abrasion.
- Flexibility: These belts offer good flexibility, which is essential in systems that require frequent starting, stopping, or directional changes.
- Cost-Effective: Like Grade M, Grade N belts are also a budget-friendly option for general-purpose use.
- Typical Uses: Common in light to medium industrial applications, including packaging, logistics, and some types of material handling.
Why Grade M and Grade N Are the Best for General-Purpose Use:
- Balanced Properties: Both grades provide a good mix of strength, flexibility, and abrasion resistance, suitable for handling a variety of materials without being overly specialized.
- Wide Availability: These grades are widely available and can be sourced from many manufacturers, ensuring easy replacement and maintenance.
- Affordability: They offer a cost-effective solution without compromising on quality, making them a preferred choice for companies looking to optimize both performance and budget.
- Ease of Use: These belts are easy to install, maintain, and replace, making them practical for operations that require minimal downtime.
For most general-purpose conveyor applications, Grade M and Grade N conveyor belt materials stand out as the best choices. They offer the right combination of durability, flexibility, and cost-effectiveness, making them suitable for a wide range of industries and uses. Depending on the specific needs of the application, either Grade M or Grade N can provide reliable and efficient performance.
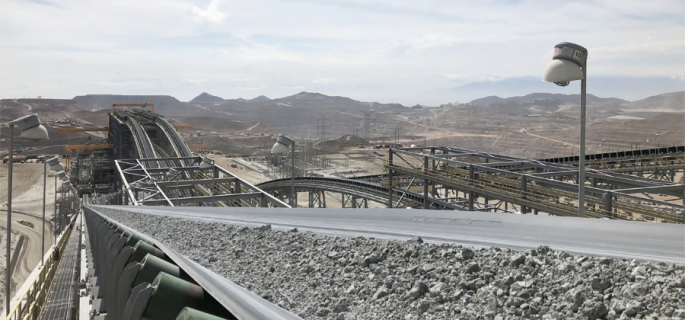
Conveyor Belt Material Standard: Sythentic Fibre Materials
Synthetic fiber materials are commonly used in conveyor belts to provide specific properties such as strength, flexibility, resistance to environmental factors, and durability. Different synthetic fibers are chosen based on the application requirements, and they offer advantages over traditional natural materials like cotton. Here’s an overview of the most common synthetic fiber materials used in conveyor belts and their associated properties:
Polyester (PET)
- Properties:
- High Tensile Strength: Polyester fibers offer excellent strength, making them suitable for heavy-duty applications.
- Low Stretch: Polyester has minimal stretch, which helps maintain belt tension and reduces the need for frequent adjustments.
- Good Resistance to Moisture and Chemicals: Polyester is resistant to water absorption and most chemicals, making it durable in wet or chemically exposed environments.
- Uses: Commonly used in general-purpose conveyor belts, as well as in applications where high strength and low stretch are required, such as in mining, agriculture, and material handling.
Nylon (Polyamide)
- Properties:
- High Strength and Durability: Nylon is known for its toughness, making it suitable for high-impact and high-wear applications.
- Good Flexibility: Nylon fibers offer excellent flexibility, which is essential in conveyor belts that require frequent bending and twisting.
- High Abrasion Resistance: Nylon’s abrasion resistance makes it ideal for applications involving sharp or abrasive materials.
- Uses: Typically used in industries such as mining, quarrying, and construction, where the belt is exposed to harsh conditions and requires high wear resistance.
Aramid (e.g., Kevlar®)
- Properties:
- Exceptional Strength-to-Weight Ratio: Aramid fibers are extremely strong and lightweight, offering superior performance in demanding applications.
- High Heat Resistance: Aramid materials can withstand high temperatures without degrading, making them ideal for heat-resistant conveyor belts.
- Cut and Tear Resistance: Aramid’s resistance to cutting and tearing extends the life of the conveyor belt in tough environments.
- Uses: Used in high-performance belts for industries like aerospace, automotive, and defense, as well as in environments where belts are exposed to extreme temperatures or require high strength and durability.
Polyurethane (PU)
- Properties:
- Flexibility and Elasticity: Polyurethane offers excellent flexibility and can return to its original shape after being stretched, which is valuable in dynamic applications.
- Good Abrasion and Tear Resistance: PU belts are resistant to wear, tearing, and impacts, making them suitable for heavy-duty use.
- Chemical and Oil Resistance: PU is resistant to oils, grease, and many chemicals, which is essential in food processing and other industries.
- Uses: Commonly used in food processing, packaging, and other industries where flexibility, hygiene, and chemical resistance are crucial.
Polyvinyl Chloride (PVC)
- Properties:
- Cost-Effective: PVC is an affordable material with a good balance of properties for general-purpose use.
- Chemical Resistance: PVC is resistant to acids, alkalis, and other chemicals, making it suitable for environments where chemical exposure is a concern.
- Durable and Easy to Clean: PVC belts are durable and easy to maintain, making them ideal for applications requiring frequent cleaning.
- Uses: Widely used in light to medium-duty applications such as logistics, food processing, and general material handling.
Polyolefin (e.g., Polyethylene, Polypropylene)
- Properties:
- Lightweight and Low Friction: Polyolefin fibers are lightweight and offer low friction, which is beneficial in conveyor systems requiring energy efficiency.
- Chemical and Moisture Resistance: These materials are highly resistant to chemicals and moisture, making them suitable for wet or corrosive environments.
- Good Insulation Properties: Polyolefins offer good electrical insulation, which can be important in certain specialized conveyor applications.
- Uses: Used in applications where weight reduction, chemical resistance, and low friction are important, such as in the food industry, packaging, and electronics.
Synthetic fiber materials offer significant advantages over natural fibers in conveyor belt construction. They provide enhanced strength, flexibility, resistance to environmental factors, and longevity, making them ideal for a wide range of industrial applications. Choosing the right synthetic fiber material depends on the specific requirements of the conveyor system, including factors like load, speed, environmental conditions, and the type of material being conveyed.
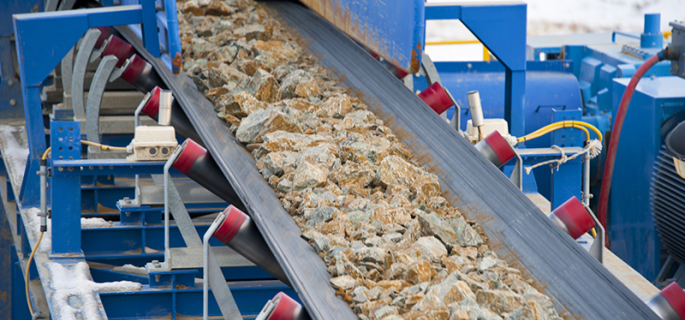
Conveyor Belt Material Standard: Rupture Strength
Rupture strength, also known as tensile strength or breaking strength, is a critical parameter in the design and selection of conveyor belts. It refers to the maximum stress or force that a conveyor belt material can withstand before it breaks or fails. Understanding the rupture strength of a conveyor belt is essential to ensure that the belt can handle the intended load and operating conditions without failing prematurely.
Factors Influencing Rupture Strength
Material Composition:
- Synthetic Fibers: Conveyor belts made from synthetic fibers like polyester (PET), nylon (polyamide), and aramid (e.g., Kevlar®) generally have higher rupture strengths compared to natural fibers. These materials are engineered to withstand significant tensile forces, making them suitable for heavy-duty applications.
- Reinforcement Layers: The strength of a conveyor belt can be enhanced by incorporating multiple layers of reinforcing materials, such as fabrics, steel cords, or synthetic fibers. These reinforcement layers significantly increase the belt’s rupture strength.
Construction Type:
- Fabric Belts: Conveyor belts reinforced with fabric, typically made from polyester or nylon, offer high tensile strength and flexibility. The construction often involves multiple plies (layers) of fabric to achieve the desired strength.
- Steel Cord Belts: These belts use steel cords as reinforcement, offering exceptional rupture strength. They are used in applications requiring the highest strength and are capable of carrying heavy loads over long distances.
- Aramid Belts: Aramid (Kevlar®) reinforced belts provide an excellent strength-to-weight ratio and are used where both high strength and light weight are essential.
Belt Width and Thickness:
- Width: The rupture strength is generally proportional to the width of the belt. Wider belts distribute the load over a larger area, reducing stress per unit width.
- Thickness: Thicker belts can endure higher tensile forces, as the material volume capable of resisting rupture increases with thickness.
Environmental Conditions:
- Temperature: High temperatures can degrade the belt material, reducing its tensile strength. Heat-resistant materials like aramid or specially formulated synthetic rubbers are used to maintain strength in high-temperature environments.
- Chemical Exposure: Exposure to chemicals, oils, or moisture can weaken certain belt materials, leading to a reduction in rupture strength. Conveyor belts for such environments are typically made from chemically resistant materials like PVC or nitrile rubber.
Typical Rupture Strength Values
- Polyester (PET) Belts:
- Strength: Polyester belts typically have a tensile strength in the range of 500 to 1000 N/mm (newtons per millimeter of belt width).
- Application: Suitable for general-purpose applications where moderate strength and flexibility are required.
- Nylon (Polyamide) Belts:
- Strength: Nylon belts can offer tensile strengths ranging from 800 to 1500 N/mm.
- Application: Ideal for applications with high impact or load demands, such as mining or heavy industrial use.
- Steel Cord Belts:
- Strength: Steel cord belts provide rupture strengths of up to 8000 N/mm or higher, depending on the cord diameter and spacing.
- Application: Used in high-capacity, long-distance conveying systems, particularly in mining and bulk material handling.
- Aramid (Kevlar®) Belts:
- Strength: Aramid belts can have tensile strengths ranging from 1000 to 3000 N/mm, with some specialty belts offering even higher values.
- Application: Preferred in industries requiring lightweight belts with very high strength, such as aerospace or high-speed conveying systems.
Importance of Rupture Strength in Belt Selection
When selecting a conveyor belt, it is crucial to consider the rupture strength in relation to the operational load and safety factors. The belt must be strong enough to handle the maximum anticipated load without reaching its breaking point. Selecting a belt with an appropriate rupture strength ensures operational safety, reduces downtime, and prolongs the belt’s service life.
In summary, rupture strength is a vital consideration in conveyor belt design, influencing the belt’s ability to carry loads without failure. The choice of material, construction, and reinforcement, along with environmental conditions, all play a role in determining the rupture strength of a conveyor belt. Understanding and selecting the correct rupture strength is key to ensuring the reliability and longevity of conveyor systems in various industrial applications.
Key Material Standards and Specifications for Conveyor Belts
The conveyor belt material standard plays a pivotal role in defining the quality and operational parameters for various types of conveyor belts, particularly in specialized environments. A prime example is the ISO 22721:2023 standard, which is specifically designed for rubber or plastics-covered conveyor belting of textile construction used in underground mines. This standard ensures that the belts are robust enough to withstand the harsh conditions of mining operations while supporting safety and durability.
Beyond the mining-specific ISO standard, there are numerous other general standards that guide the material specifications of conveyor belts across different industries. These standards are crucial for manufacturers and users alike, as they provide a framework that guarantees the belts meet minimum safety, efficiency, and environmental requirements. For example, standards often dictate the acceptable levels of tensile strength, abrasion resistance, and chemical resilience, ensuring that each conveyor belt can perform under the expected operational stresses without failure.
Understanding these conveyor belt material standards is essential not only for compliance with regulatory requirements but also for optimizing the selection process of conveyor belts. By adhering to these specifications, industries can enhance operational efficiency and extend the lifespan of their conveyor systems, ultimately contributing to more stable and cost-effective production processes.

Material Properties and Their Impact According to Conveyor Belt Material Standards
The performance of conveyor belts in various industrial applications is heavily influenced by the material properties specified by conveyor belt material standards. These properties include tensile strength, abrasion resistance, thermal stability, and others, which are critical to the belt’s functionality and longevity. Understanding these properties and their impact helps in selecting the right belt for specific applications.
Key Material Properties and Their Impact on Conveyor Belt Performance
Tensile Strength: This is the maximum load that a material can support without failure. Conveyor belts with high tensile strength are essential in industries like mining where they need to handle heavy loads. A belt with inadequate tensile strength might stretch excessively or even snap under heavy load.
Abrasion Resistance: Abrasion resistance is crucial for belts that transport sharp or rough materials, such as in quarrying or construction. This property ensures that the belt surface does not wear down quickly, which could compromise the belt’s integrity and require frequent replacements.
Thermal Stability: This property refers to a material’s ability to maintain its form and function despite temperature variations. In industries like metalworking or glass manufacturing, where belts are exposed to high temperatures, thermal stability prevents deformation, melting, or cracking of the belt material.
Examples of Material Property Importance in Specific Applications
- Mining: In mining, conveyor belts are subjected to constant heavy loads and abrasive materials. High tensile strength and exceptional abrasion resistance are necessary to withstand the harsh conditions and prevent premature wear and tear.
- Food Processing: For conveyor belts used in food processing, thermal stability and chemical resistance are vital. These properties ensure that the belts can withstand cleaning chemicals and temperature variations without degrading. Additionally, materials used must meet food safety standards to prevent contamination.
- Recycling Industry: Belts in recycling facilities must handle a wide variety of materials, including sharp, heavy, or abrasive items. High durability and abrasion resistance are essential to cope with these demands while maintaining operational efficiency.
- Packaging Industry: In packaging, belts often require moderate tensile strength but high flexibility to handle various product shapes and weights smoothly and efficiently.
- Pharmaceuticals: Conveyor belts in the pharmaceutical industry need to have excellent chemical resistance to prevent reactions with potent substances. Additionally, these belts often require antistatic properties to prevent the accumulation of static electricity, which could pose a risk in environments with flammable substances.
- Agriculture: Belts used in agriculture need to be resistant to moisture, mildew, and possibly chemicals, depending on their use in processing or pesticide applications. Their tensile strength must also be sufficient to handle loads like grain or vegetables without stretching.
In each of these applications, adherence to conveyor belt material standards is not just about selecting a belt that fits the system but choosing one that optimizes performance, safety, and cost-effectiveness. These standards ensure that the materials used can handle the specific stresses of their intended environment, thereby reducing downtime and maintenance costs while improving overall productivity.
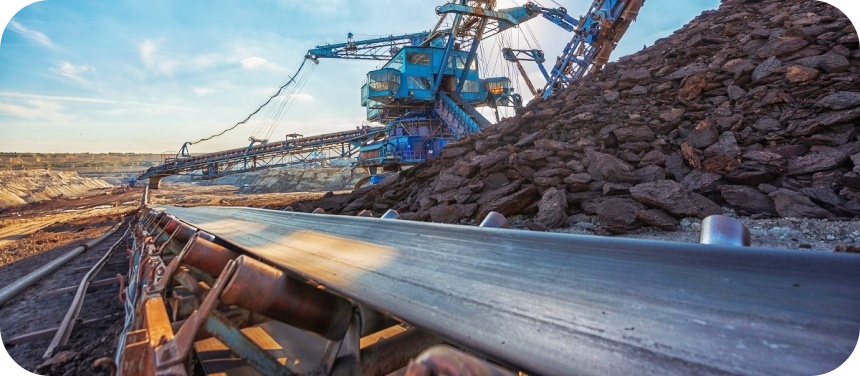
Types of Conveyor Belt Materials According to Conveyor Belt Material Standards
In line with conveyor belt material standards, it’s crucial to understand the various types of materials used in conveyor belts. These materials are chosen based on their mechanical properties, environmental compatibility, and suitability for different industrial applications. Here’s a detailed look at some common types of conveyor belt materials:
Rubber Conveyor Belts
Features:
- High Tensile Strength: Rubber belts are designed to withstand significant stress without breaking.
- Elasticity: The natural elasticity of rubber helps absorb impacts and resist mechanical damage.
- Abrasion Resistance: These belts are resistant to wear and tear from rough materials.
- Corrosion Resistance: Rubber is impervious to many chemical reactions that can corrode other materials.
- Water Resistance: Effective in environments where belts may be exposed to moisture.
- Temperature Tolerance: Rubber belts can operate under a wide range of temperatures.
- Shock Absorption: Ideal for transporting materials that may cause vibrations or shocks.
- Fire Resistance: Some rubber belts are treated to be fire-resistant, meeting safety standards.
Benefits:
- Durability: Long lifespan under typical operating conditions.
- Cost-Effectiveness: Generally more affordable compared to some advanced materials.
- Maintenance: Easier maintenance due to the material’s resilience.
- Versatility: Suitable for a wide range of applications, from mining to food processing.
- Noise Reduction: Rubber’s natural properties can reduce operational noise.
- Energy Efficiency: Good grip reduces slippage and increases energy efficiency.
- Safety: Enhances safety by reducing the risk of slips and breaks.
- Adaptability: Can be customized with various textures and properties to suit specific needs.
Nylon Conveyor Belts
Characteristics:
- High Strength-to-Weight Ratio: Nylon is exceptionally strong for its lightweight.
- Flexibility: Nylon belts can easily adapt to various pulley sizes and systems.
- High Abrasion Resistance: Suitable for transporting sharp or heavy materials.
- Low Coefficient of Friction: Reduces the energy needed for operation.
- Resistance to Chemicals: Nylon is resistant to many chemicals, enhancing its durability.
- Hygroscopic Properties: Can absorb a small amount of moisture without losing integrity.
- Thermal Stability: Maintains performance within a broad temperature range.
- Mold and Mildew Resistance: Naturally resistant to biological growth.
Typical Applications:
- Mining: Due to their durability and strength, nylon belts are commonly used in mining operations.
- Quarrying: Ideal for the harsh environments of quarrying due to abrasion resistance.
- Agriculture: Used for transporting grain and other agricultural products.
- Manufacturing: Integral in assembly lines and processing plants.
- Packaging: Utilized in packaging facilities for moving products.
- Recycling: Effective in sorting and processing recycled materials.
- Wood Processing: Handles wood products without causing damage.
- Food Processing: Suitable for non-toxic food handling applications.
Other Materials
Metal: Often used in industries requiring high strength and exposure to extreme temperatures or corrosive environments. Metal belts are ideal for their durability and ability to handle heavy loads.
Fabric: Fabric belts are lighter, quieter, and can be used in a variety of less intensive applications. They are often used in food processing and packaging industries.
Thermoplastic: These materials, including PVC and PU, are versatile and can be used in environments that require resistance to oil, chemicals, and other harsh substances.
Each material is chosen based on the conveyor belt material standards that ensure optimal performance in specific environments and applications. These standards are critical in guiding the selection process, ensuring each belt is fit for purpose, and meets safety, efficiency, and durability requirements.
Need a conveyor belt solution? Contact us for a quick response!
Factors To Consider When Choosing Conveyor Belt Materials
Selecting the appropriate conveyor belt material is crucial for ensuring efficient, reliable, and safe operation in various industrial applications. The choice of material affects the performance, durability, and maintenance needs of the conveyor system. Here are key factors to consider when choosing conveyor belt materials:
Type of Material Being Conveyed
- Weight and Density: The belt must be strong enough to support the weight of the materials being transported. Heavier and denser materials require belts with higher tensile strength and durability.
- Abrasiveness: Abrasive materials like sand, gravel, or ores require belts made from highly wear-resistant materials, such as those reinforced with aramid or steel cords.
- Temperature: If the material is hot, such as in the case of foundry or cement industries, a heat-resistant belt material like aramid or specialized rubber compounds is necessary.
- Chemical Properties: Conveying chemicals or food items with specific regulatory requirements necessitates belts made from chemically resistant or food-grade materials like PVC or PU.
Operating Environment
- Temperature: The conveyor belt must withstand the ambient temperature of the working environment. High-temperature environments require heat-resistant belts, while low-temperature environments may need belts that remain flexible and crack-resistant.
- Exposure to Chemicals or Oils: Environments where the belt may come into contact with chemicals, oils, or solvents require materials that resist degradation, such as nitrile rubber or specific synthetic compounds.
- Moisture and Corrosive Elements: Wet environments or exposure to corrosive elements like saltwater necessitate the use of moisture-resistant and corrosion-resistant materials, such as PVC or rubber with proper additives.
- Cleanliness Requirements: In industries like food processing or pharmaceuticals, belts must meet strict hygiene standards, often requiring materials that are easy to clean, non-toxic, and resistant to bacterial growth.
Mechanical Requirements
- Tensile Strength: The belt must have sufficient tensile strength to handle the maximum load without stretching or breaking. This is particularly important in heavy-duty applications like mining or quarrying.
- Flexibility: For applications requiring the belt to bend, twist, or navigate curves, a flexible material is essential. Nylon and polyester belts often offer good flexibility.
- Elongation and Stretch: The material should have low elongation characteristics to maintain the proper tension and alignment. Belts with high stretch might require frequent adjustments.
- Tear and Impact Resistance: In environments with sharp or heavy objects, the belt material should have high tear and impact resistance to prevent damage and prolong its service life.
Belt Speed and Length
- Belt Speed: High-speed conveyors require belts with smooth surfaces and materials that can handle rapid movement without excessive wear or heat generation.
- Belt Length: Longer conveyors might benefit from belts with low elongation to maintain consistent tension over extended distances. Steel cord or aramid belts are often used in such applications due to their high tensile strength and low stretch.
Load Capacity
- Static and Dynamic Loads: The belt material must support both static loads (when the belt is stationary) and dynamic loads (when the belt is in motion). The material’s strength and construction should match the load requirements.
- Load Distribution: Consider the uniformity of load distribution across the belt. Uneven loads can cause premature wear, so belts with appropriate reinforcement might be necessary.
Durability and Lifespan
- Wear Resistance: Consider the belt’s ability to withstand wear from friction, abrasion, and the conveyed material. Belts made from durable materials like polyurethane or rubber compounds with additives can have longer lifespans.
- Maintenance and Replacement Frequency: A belt with a longer lifespan might have a higher upfront cost but lower long-term maintenance costs. Consider the total cost of ownership, including downtime for replacements and repairs.
Regulatory and Industry Standards
- Food-Grade Standards: In industries like food processing, belts must meet FDA or other food safety regulations, requiring the use of food-grade materials.
- Fire Resistance: In environments where fire safety is critical, such as underground mining, belts must meet fire resistance standards, often requiring the use of flame-retardant materials.
Cost Considerations
- Initial Cost: The choice of material should fit within the budget while meeting all performance and safety requirements.
- Total Cost of Ownership: Consider not just the initial purchase price, but also the costs associated with maintenance, downtime, and replacement. A more expensive belt might be more cost-effective in the long run if it reduces maintenance and increases uptime.
Compatibility with Conveyor System
- Pulley and Drive Compatibility: The belt material must be compatible with the conveyor’s pulleys, drives, and other mechanical components. Certain materials may require specific types of pulleys or tensioning systems.
- Belt Tracking: The material should track well with the conveyor system to prevent misalignment and ensure smooth operation.
Choosing the right conveyor belt material involves a comprehensive analysis of the application requirements, environmental conditions, mechanical needs, and cost considerations. Understanding these factors ensures the selection of a conveyor belt that will perform efficiently, last longer, and require minimal maintenance, thereby optimizing the overall productivity and safety of the operation.
Conveyor Belt Design and Material Selection Charts Guided by Conveyor Belt Material Standard
Material selection charts are invaluable tools in the conveyor belt industry, providing a systematic approach to choosing the correct conveyor belt material based on specific application requirements and adhering to the conveyor belt material standard. These charts help simplify the decision-making process by categorizing various materials according to their properties, suitability for different environmental conditions, and compliance with industry standards.
The design of these charts typically begins with a broad categorization of materials based on basic characteristics such as tensile strength, abrasion resistance, and thermal resistance. From there, more detailed attributes are considered, including resistance to oils, chemicals, and UV exposure, which are crucial for belts used in harsh industrial environments. Each material type is rated according to its performance in these categories, guiding engineers and procurement specialists in selecting the best material for their specific needs.
In practical terms, these selection charts are used by designers and engineers to align conveyor belt material standards with operational requirements. For example, when designing a conveyor system for a mining operation, the chart will highlight materials that perform well in abrasive environments with heavy loads. Conversely, for a food processing conveyor system, the chart will direct the selection towards materials that are FDA approved, easy to clean, and resistant to bacterial contamination.
By integrating these material selection charts into the conveyor belt design process, industries can ensure that they meet the specific conveyor belt material standard required for their applications, thereby enhancing efficiency and extending the lifespan of their conveyor systems. This structured approach not only streamlines material selection but also supports compliance and performance optimization in various industrial contexts.
Advances in Conveyor Belt Materials According to Conveyor Belt Material Standards
The field of conveyor belt materials has seen significant advancements in recent years, driven by innovations in material science and technology. These developments not only enhance the performance and durability of conveyor belts but also align with updated conveyor belt material standards to meet the evolving needs of various industries.
Recent Advancements in Conveyor Belt Materials and Technology
- High-Performance Rubbers: New formulations of rubber that offer improved abrasion resistance and higher tensile strength, extending the life of conveyor belts in harsh environments.
- Reinforced Fabrics: The use of advanced fibers like Kevlar in fabric belts enhances their strength and reduces stretch, making them suitable for long-distance conveying.
- Smart Belts: Incorporation of sensors and IoT technology in belts allows for real-time monitoring of performance and health, facilitating predictive maintenance.
- Eco-friendly Materials: Development of sustainable, biodegradable, or recycled materials for conveyor belts to reduce environmental impact.
- Thermoplastic Polyurethane (TPU): Improved formulations provide better wear resistance and flexibility across a range of temperatures, ideal for food processing applications.
- Increased Fire Resistance: Innovations in materials that are self-extinguishing or highly resistant to fire improve safety in industries prone to fire hazards.
- Antimicrobial Coatings: Belts treated with antimicrobial agents prevent the growth of bacteria and fungi, crucial in pharmaceutical and food industries.
- Modular Belts: Advances in modular belt design, using durable plastic segments, offer improved cleanliness and easier maintenance, especially in food processing.
Future Trends in Material Science Influencing Conveyor Belt Designs
- Nanotechnology: Incorporation of nanoparticles to enhance properties like tensile strength, thermal resistance, and conductivity of belt materials.
- 3D Printing: Using 3D printing to create custom, on-demand conveyor parts and belts with complex geometries or tailored properties.
- Graphene Integration: Utilizing graphene’s exceptional strength and conductivity to create ultra-strong, lightweight belts that are highly efficient.
- Advanced Biopolymers: Development of new biopolymers that offer high performance while being environmentally friendly.
- Shape Memory Materials: Materials that can change shape in response to environmental conditions, offering potential self-repair capabilities.
- Thermal Adaptive Materials: Materials that adjust their properties based on temperature, providing optimal performance across a broader range of conditions.
- Increased UV Resistance: Improved resistance to ultraviolet light to prevent degradation in outdoor applications.
- Enhanced Elasticity: Materials that offer superior elasticity without permanent deformation for systems requiring high flexibility.
- Electrically Conductive Belts: Belts that can prevent static build-up or even conduct electricity, useful in electronic manufacturing.
- Smart Coatings: Advanced coatings that can change color or texture based on wear or damage, alerting maintenance teams to potential issues.
These advancements and trends, guided by the conveyor belt material standard, demonstrate the ongoing evolution in conveyor technology. They highlight the industry’s commitment to improving efficiency, safety, and environmental sustainability in conveyor belt design and manufacturing.
FAQs about Conveyor Belt Material Standard
Conveyor belts are manufactured from a variety of materials, each selected for its specific performance characteristics to suit different work environments and material handling needs. The material composition of a conveyor belt can significantly impact its durability, flexibility, strength, and resistance to various environmental factors.
Rubber – One of the most common materials due to its elasticity, which provides excellent shock absorption and can carry heavy loads. Rubber belts are used in both light and heavy-duty applications and can be compounded for resistance to abrasions, chemicals, and temperatures.
PVC (Polyvinyl Chloride) – Characterized by high strength, durability, and resistance to water, abrasions, chemicals, and weather. PVC belts are a good choice for general use and find applications in food processing, recycling plants, and manufacturing units.
Polyurethane (PU) – Known for its hygienic properties, PU belts are commonly used in the food, pharmaceutical, and cosmetic industries. These belts are easy to clean and maintain, resistant to oils, fats, and chemicals.
Fabric – Constructed from materials like polyester, nylon, or cotton combined with various plastics or rubber. Fabric belts offer flexibility and are used in applications requiring good grip, air flow, or specific resistances.
Each material offers unique benefits, and the choice depends on the application, including the type of product being conveyed, the environment in which the belt operates, and the conveyor design.
The International Organization for Standardization (ISO) has established various standards to ensure quality, safety, and efficiency in conveyor belt systems. A notable standard is ISO 22721:2023, which specifies requirements for rubber- or plastics-covered conveyor belting of textile construction for use in underground mines.
This standard does not cover light conveyor belts, as these are addressed in ISO 21183-1. It aims to guide manufacturers in producing conveyors that meet safety and performance criteria, specifically for underground mining environments, where durability and resistance to harsh conditions are crucial. The ISO 22721:2023 standard underscores the importance of material choice, design specifications, and the collaboration between manufacturers and purchasers to meet specific operational needs while complying with safety regulations.
Creating a conveyor belt involves several components, each contributing to the belt’s overall performance and durability. The primary materials include:
Base Material (Carcass) – Serves as the skeleton of the belt and provides structural strength. Common materials include fabrics like polyester, nylon, or cotton, and sometimes steel cables for added durability.
Covering Material – Protects the carcass from wear, tear, and environmental factors. This could be rubber, PVC, PU, or a composite material, chosen based on the application’s demands regarding chemical resistance, temperature, and abrasion.
Adhesives – Used to bond layers together or attach the covering material to the carcass. The choice of adhesive is crucial for ensuring the belt’s integrity and longevity.
Reinforcements – Additional elements like steel cords or fabric layers might be included to enhance tensile strength, impact resistance, or to provide specific properties such as antistatic behavior.
Manufacturing a conveyor belt requires careful selection of these materials to meet the intended application’s demands. The process involves precision in design and assembly to ensure that the final product can withstand operational stresses while providing reliable service.
The specification of a conveyor belt can vary widely depending on its intended use, the materials it will carry, and the environment in which it operates. Key specifications include:
Width and Length – Determined by the size of the items to be transported and the overall layout of the conveyor system.
Material – Based on the application, materials range from rubber and PVC to fabric and metal, each offering different levels of resistance and durability.
Thickness – Affects the belt’s strength and capacity to carry heavy loads.
Tensile Strength – Indicates the maximum load the belt can handle without breaking.
Working Temperature Range – Important for applications subject to extreme temperatures, specifying the minimum and maximum temperatures the belt can withstand.
Resistance Properties – Including abrasion resistance, chemical resistance, and suitability for food contact, tailored to the environmental conditions and materials handled.
The specifications must align with operational requirements, ensuring that the belt can perform efficiently and safely under the given conditions. Proper specification helps in achieving optimal productivity and extends the lifespan of the conveyor belt.
The HS code for conveyor belt fabric generally falls under 5910.00, which covers textile products and articles for technical uses, including conveyor belts or belting of textile material. However, the exact HS code can vary depending on the specific material and composition of the conveyor belt fabric. It’s always advisable to check with local customs authorities or a trade compliance expert to confirm the correct HS code for your specific product.
Last Updated on August 23, 2024 by Jordan Smith
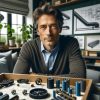
Jordan Smith, a seasoned professional with over 20 years of experience in the conveyor system industry. Jordan’s expertise lies in providing comprehensive solutions for conveyor rollers, belts, and accessories, catering to a wide range of industrial needs. From initial design and configuration to installation and meticulous troubleshooting, Jordan is adept at handling all aspects of conveyor system management. Whether you’re looking to upgrade your production line with efficient conveyor belts, require custom conveyor rollers for specific operations, or need expert advice on selecting the right conveyor accessories for your facility, Jordan is your reliable consultant. For any inquiries or assistance with conveyor system optimization, Jordan is available to share his wealth of knowledge and experience. Feel free to reach out at any time for professional guidance on all matters related to conveyor rollers, belts, and accessories.