Best Types of Conveyor Belt Motors Explained
Conveyor belt motors are crucial components in modern conveyor belt systems, providing the necessary power to move materials efficiently and reliably. These motors ensure that the conveyor belts operate smoothly, handling various loads and speeds required in industrial settings. Without reliable conveyor belt motors, productivity in industries like manufacturing, packaging, and distribution would be significantly hindered. There is a wide variety of conveyor belt motors available, each suited to different applications and requirements. These include AC induction motors, known for their durability, DC motors for precise speed control, gear motors for enhanced torque, and stepper and servo motors for precise positioning tasks.
Conveyor Belt Motors: Types and Applications
Conveyor belt motors are the driving force behind conveyor systems, ensuring the smooth and efficient transport of materials across various industries. Selecting the right type of motor is crucial for optimizing performance, energy efficiency, and reliability. In this comprehensive guide, we will explore the different types of conveyor belt motors, their applications, and their benefits.
Types of Conveyor Belt Motors
AC Induction Motors
AC induction motors are among the most commonly used motors in conveyor systems. They operate on alternating current (AC) and are known for their robustness and reliability. These motors consist of a stator and a rotor, with the stator generating a rotating magnetic field that induces current in the rotor, causing it to turn.
Description and Typical Applications:
AC induction motors are widely used in industrial applications where durability and the ability to handle varying loads are essential. They are suitable for heavy-duty tasks such as moving bulk materials, processing plants, and manufacturing lines. These motors are often chosen for applications where continuous operation and low maintenance are critical.
Advantages: Durability and Handling Varying Loads:
- Durability: AC induction motors are built to last, with a design that can withstand harsh environments and heavy usage. Their robust construction makes them ideal for demanding applications.
- Handling Varying Loads: These motors are capable of handling different load conditions without compromising performance. They can maintain consistent speed and torque, ensuring smooth operation even under fluctuating loads.
DC Motors
DC motors are another popular choice for conveyor systems, particularly when precise speed control and efficiency are required. These motors convert direct current (DC) into mechanical motion, providing excellent control over speed and torque.
Overview of DC Motors in Conveyor Systems:
DC motors are used in applications where precise speed and position control are crucial. They are commonly found in assembly lines, packaging systems, and conveyor systems that require variable speeds.
Benefits: Speed Control and Efficiency:
- Speed Control: One of the primary advantages of DC motors is their ability to provide precise speed control. This makes them ideal for applications where the conveyor speed needs to be adjusted frequently or where synchronization with other processes is necessary.
- Efficiency: DC motors are highly efficient, converting a large portion of the electrical energy into mechanical energy. This efficiency reduces energy consumption and operational costs.
Gear Motors
Gear motors combine an electric motor with a gearbox, providing both speed reduction and torque multiplication. They are essential in applications where high torque and low speed are required.
Explanation of Gear Motors and Their Role in Conveying:
Gear motors are used to drive conveyor belts at specific speeds while providing the necessary torque to move heavy loads. The gearbox reduces the speed of the motor while increasing the torque, making them ideal for applications such as material handling, packaging, and automotive assembly lines.
Benefits: Torque Multiplication and Speed Reduction:
- Torque Multiplication: Gear motors provide high torque output, which is essential for moving heavy or bulky materials. This makes them suitable for conveyors that need to handle significant weight.
- Speed Reduction: The integrated gearbox allows for precise control over the conveyor speed, ensuring smooth and efficient operation. This is particularly important in processes that require synchronized movements.
Stepper Motors
Stepper motors are known for their ability to provide precise positioning and control. They are commonly used in applications that require accurate movement and positioning.
Use in Precise Positioning Applications:
Stepper motors are ideal for applications where precise control over position and movement is necessary. They are often used in automated conveyor systems, robotics, and machinery that require detailed positioning.
Applications Where Stepper Motors are Preferred:
- Automated Systems: In automated systems, stepper motors ensure that components are positioned accurately, enhancing the overall efficiency of the process.
- Robotics: Stepper motors are used in robotic systems for precise control over the movement of robotic arms and other components.
- Printing and Labeling: These motors are used in printing and labeling machines where exact positioning of labels and prints is crucial.
Servo Motors
Servo motors offer high-precision control and are used in applications that require precise speed, position, and torque control. They are equipped with a feedback system that allows for accurate control of the motor’s operation.
Detailed Look at Servo Motors for High-Precision Tasks:
Servo motors are designed for applications that demand high precision and dynamic performance. They are used in industries such as electronics, aerospace, and medical devices, where exact control over movement is critical.
Comparison with Stepper Motors:
- Precision and Control: While both stepper and servo motors offer precise control, servo motors provide higher precision due to their closed-loop feedback system. This system continuously monitors the motor’s position and makes real-time adjustments to ensure accuracy.
- Torque and Speed: Servo motors can deliver higher torque at high speeds compared to stepper motors. This makes them suitable for applications that require both speed and power.
- Efficiency: Servo motors are more efficient than stepper motors, especially in high-speed applications. They consume less power and generate less heat, which can be beneficial in energy-sensitive environments.
The Best Way to Conveyor Belt Motors
Conveyor Belt Motor Specifications
Power Rating
The power rating of a conveyor belt motor is a critical specification that determines its ability to handle the load and perform efficiently. Power ratings are typically measured in horsepower (HP) or kilowatts (kW). These ratings indicate the motor’s capacity to perform work over time, with higher ratings signifying greater power.
Horsepower is a unit of measurement used primarily in the United States and is calculated as the power needed to move 550 pounds one foot in one second. Kilowatts, on the other hand, are part of the metric system and are widely used internationally. One horsepower is equivalent to approximately 0.746 kilowatts. When selecting conveyor belt motors, it is essential to match the power rating to the specific requirements of the conveyor system to ensure optimal performance and longevity.
In conveyor systems, the motor power rating must be adequate to move the load at the desired speed without overheating or experiencing excessive wear. Undersized motors may struggle to maintain the required performance levels, leading to increased maintenance costs and potential downtime. Conversely, oversized motors can be more expensive and less efficient. Therefore, selecting the right power rating is crucial for achieving a balance between performance, efficiency, and cost.
Torque
Torque is another vital factor in the selection of conveyor belt motors. Torque, measured in Newton-meters (Nm) or pound-feet (lb-ft), refers to the rotational force that the motor can exert. In conveyor systems, torque is essential for overcoming the inertia of the conveyor belt and the load it carries, as well as for maintaining the desired speed under varying load conditions.
The importance of torque in conveyor systems cannot be overstated. High torque is necessary to start the conveyor belt moving, especially when dealing with heavy loads or inclines. It also plays a crucial role in maintaining consistent speed and preventing slippage, which can cause uneven product flow and reduce operational efficiency.
When selecting a motor for a conveyor belt, it is essential to consider the torque specifications in relation to the system’s requirements. Motors with higher torque are better suited for heavy-duty applications, where the load and operational conditions demand greater force. Additionally, understanding the relationship between torque and speed is important, as motors may offer high torque at lower speeds, which can influence the overall design and functionality of the conveyor system.
Speed
The speed of conveyor belt motors is another critical specification that impacts the performance and efficiency of the conveyor system. Speed is typically measured in revolutions per minute (RPM) and determines how fast the conveyor belt moves. Different applications require varying speed levels, and selecting the appropriate motor speed is essential for meeting the specific needs of the operation.
In some conveyor applications, high speed is necessary to maintain a swift and continuous flow of materials, such as in packaging or assembly lines. In contrast, other applications may require lower speeds to ensure precise handling and positioning of products, such as in inspection or sorting systems. The choice of motor speed must align with the operational requirements to ensure that the conveyor system functions efficiently and effectively.
The impact of speed on motor choice is significant. Motors designed for high-speed applications may need to balance speed with torque to ensure adequate force is available to move the load. Conversely, motors for low-speed applications must provide sufficient torque to handle the load at reduced speeds. Understanding these dynamics is crucial for selecting the right conveyor belt motors that offer the desired performance without compromising efficiency or reliability.
Efficiency
Energy efficiency is a critical consideration when selecting conveyor belt motors. High-efficiency motors consume less energy to perform the same amount of work compared to standard motors, resulting in lower operating costs and reduced environmental impact. The efficiency of a motor is typically expressed as a percentage, with higher values indicating greater efficiency.
The benefits of high-efficiency motors extend beyond energy savings. These motors often have better performance characteristics, including improved torque and speed control, which can enhance the overall efficiency of the conveyor system. Additionally, high-efficiency motors tend to generate less heat, reducing the need for cooling and extending the motor’s lifespan.
When selecting conveyor belt motors, it is important to consider the energy efficiency rating and choose motors that meet or exceed industry standards. Investing in high-efficiency motors can lead to significant cost savings over the long term, particularly in operations where conveyor systems run continuously or for extended periods. Moreover, high-efficiency motors contribute to sustainability goals by reducing energy consumption and greenhouse gas emissions.
Call to Action
If you are seeking tailored conveyor belt motor solutions to enhance your material handling systems, we invite you to reach out to us for more information. Our team of experts is ready to assist you in selecting and implementing the ideal motor specifications that meet your unique requirements. Whether you need motors with specific power ratings, torque, speed, or efficiency, we are here to provide high-quality, customized solutions.
For additional insights and real-world examples of successful conveyor belt motor applications, please explore our resources and case studies. These documents offer valuable information on how our customers have benefited from our motor solutions and how you can achieve similar results.
We also encourage you to share this post on social media and engage with us in the comments section. Your questions, experiences, and feedback are invaluable, and we look forward to hearing from you. Join the conversation to learn more about the latest advancements and best practices in conveyor belt motor technology.
How to Conveyor Belt Motors
Choosing the Right Motor for Your Conveyor
Fixed or Constant Speed Applications
When selecting conveyor belt motors for fixed or constant speed applications, AC motors and gear motors are often the preferred choice. AC motors are known for their reliability and simplicity, providing consistent speed that is essential for many conveyor systems. Gear motors, which combine an electric motor with a gearbox, are particularly useful for applications that require high torque at a constant speed. These motors are efficient, durable, and relatively easy to maintain, making them ideal for continuous operation in manufacturing, assembly lines, and material handling processes.
AC motors excel in environments where a steady, unvarying speed is crucial. Their ability to maintain consistent performance without the need for complex control systems simplifies the overall conveyor design. This consistency ensures that the products or materials being transported remain in sync with other processes, reducing the risk of bottlenecks and enhancing operational efficiency.
Variable Speed and High-Speed Requirements
In contrast, conveyor systems that require variable speed or high-speed capabilities need motors that can adapt to changing operational demands. AC motors paired with speed control systems, such as variable frequency drives (VFDs), are an excellent solution for these applications. VFDs allow operators to adjust the motor speed dynamically, providing the flexibility to match the conveyor speed with varying load conditions or production requirements.
Brushless DC motors are another option for variable speed applications. These motors offer precise speed control and high efficiency, making them suitable for conveyor systems where speed variability is essential. The ability to fine-tune the motor speed ensures that the conveyor can handle different types of products and materials, adapting to the specific needs of the operation.
Variable frequency drives (VFDs) are particularly beneficial when precise control over motor speed is required. They enhance the efficiency of conveyor belt motors by optimizing energy usage and reducing wear and tear on the motor components. VFDs are ideal for applications where the conveyor speed needs to change frequently, such as in packaging lines, food processing, and material sorting systems.
Precise Positioning Needs
For applications that demand precise positioning and accurate movement, stepper motors or servo motors are the best choices. These motors are designed to provide fine control over the motor’s position, making them ideal for tasks that require exact placement of products or materials on the conveyor belt.
Stepper motors operate by moving in discrete steps, allowing for precise control over the conveyor belt’s movement. This precision is crucial in industries such as electronics manufacturing, where components must be placed accurately for assembly. Stepper motors are also used in applications like labeling and printing, where the exact positioning of products is essential for quality control.
Servo motors, on the other hand, offer even greater precision and control. They are equipped with feedback systems that monitor the motor’s position and make real-time adjustments to ensure accuracy. This makes servo motors ideal for high-precision applications in robotics, medical device manufacturing, and automated inspection systems.
Industries that benefit from the precise positioning capabilities of stepper and servo motors include pharmaceuticals, aerospace, and automotive manufacturing. In these sectors, the ability to control the exact position of components on the conveyor belt ensures high-quality production standards and reduces the risk of errors.
Call to Action
If you are looking for custom conveyor belt motor solutions tailored to your specific needs, we invite you to contact us for more information. Our team of experts is ready to assist you in selecting the ideal motor for your application, whether it involves fixed speed, variable speed, or precise positioning requirements. From AC motors and gear motors to brushless DC, stepper, and servo motors, we have the knowledge and experience to provide high-quality, customized solutions.
For additional insights and real-world examples of successful conveyor belt motor implementations, please explore our resources and case studies. These documents offer valuable information on how our customers have benefited from our motor solutions and how you can achieve similar results.
We also encourage you to share this post on social media and engage with us in the comments section. Your questions, experiences, and feedback are invaluable, and we look forward to hearing from you. Join the conversation to learn more about the latest advancements and best practices in conveyor belt motor technology.
Conveyor Belt Motors: Small Motors for Specific Applications
Small Conveyor Belt Motors
Applications Where Small Motors Are Suitable
Small conveyor belt motors are essential components in a variety of industrial and commercial applications, particularly where space is limited, and the loads are relatively light. These motors are commonly used in industries such as packaging, pharmaceuticals, food processing, and electronics manufacturing. Here, we will explore the specific applications where small conveyor belt motors excel and provide the necessary power and efficiency.
Packaging: In the packaging industry, small conveyor belt motors are used to drive conveyors that handle light packages, bottles, and other small items. These conveyors are often part of automated packaging lines where precision and speed are critical. Small motors ensure that the conveyor system operates smoothly without occupying much space, allowing for compact and efficient packaging solutions.
Pharmaceuticals: The pharmaceutical industry relies on small conveyor belt motors for handling delicate and lightweight products such as pills, capsules, and small bottles. These motors are used in cleanroom environments where space is at a premium, and contamination must be minimized. The compact size of these motors makes them ideal for integration into complex machinery that requires precise control and reliability.
Food Processing: In food processing, small motors are used to drive conveyors that transport food products through various stages of production, such as sorting, washing, and packaging. These motors are particularly useful for handling lightweight items like fruits, vegetables, and baked goods. Their small size allows for easy installation in confined spaces, ensuring that the production line remains efficient and hygienic.
Electronics Manufacturing: The electronics industry often requires the transport of small, delicate components such as circuit boards, chips, and other electronic parts. Small conveyor belt motors provide the precision and control needed to handle these items gently and accurately. They are used in assembly lines, testing stations, and packaging areas, where their compact size and efficiency are highly valued.
Advantages of Using Small Motors in Compact or Lightweight Conveyor Systems
Using small conveyor belt motors in compact or lightweight conveyor systems offers several advantages, making them a preferred choice in many applications. These advantages include space efficiency, energy savings, ease of integration, and precision control.
Space Efficiency: One of the primary benefits of small conveyor belt motors is their compact size, which makes them ideal for applications where space is limited. They can be easily integrated into tight spaces without requiring significant modifications to the existing layout. This space efficiency is particularly important in industries where maximizing floor space is crucial for optimizing workflow and productivity.
Energy Savings: Small motors typically consume less energy compared to larger motors, resulting in lower operational costs. This energy efficiency is beneficial for businesses looking to reduce their carbon footprint and achieve sustainability goals. Additionally, the reduced energy consumption can lead to lower heat generation, which is advantageous in environments where temperature control is critical.
Ease of Integration: Small conveyor belt motors are easier to integrate into existing systems due to their size and flexibility. They can be mounted in various orientations and configurations, allowing for seamless incorporation into different types of conveyor setups. This ease of integration minimizes downtime and installation costs, making it a cost-effective solution for upgrading or expanding conveyor systems.
Precision Control: Many small conveyor belt motors offer precise control over speed and positioning, which is essential for applications that require accuracy and consistency. For instance, in packaging and electronics manufacturing, small motors enable the precise movement of items, ensuring that each product is handled correctly and efficiently. This precision reduces the risk of errors and enhances the overall quality of the production process.
Reduced Maintenance: Smaller motors often have fewer moving parts and are designed for reliability, resulting in reduced maintenance requirements. This can lead to lower maintenance costs and less downtime, further enhancing the efficiency of the conveyor system. Regular maintenance checks are still necessary, but the simplicity of small motors makes them easier to service and maintain.
Cost-Effectiveness: Due to their smaller size and lower power requirements, small conveyor belt motors are generally more affordable than larger motors. This cost-effectiveness makes them an attractive option for businesses that need reliable and efficient motors without significant upfront investment. Additionally, the long-term savings from reduced energy consumption and maintenance costs contribute to the overall cost benefits.
Explan Conveyor Belt Motors
Gear Motors for Conveyor Systems
Explanation of Gear Motor Components
Gear motors are integral components in conveyor belt systems, combining an electric motor with a gear reducer. The main components of a gear motor include the motor itself, the gear reducer, and the output shaft. The electric motor generates the necessary power, while the gear reducer adjusts the motor’s output speed and torque to the desired levels. The output shaft then transmits this adjusted power to the conveyor belt.
The motor component can be an AC or DC motor, each with its specific benefits. AC motors are known for their durability and simplicity, making them ideal for continuous, high-power applications. DC motors, on the other hand, offer excellent speed control and are suitable for applications requiring variable speed. The gear reducer typically consists of a series of gears that reduce the motor’s high-speed, low-torque output to a lower speed, higher-torque output suitable for driving conveyor belts.
How Gear Motors Enhance Conveyor Performance
Gear motors significantly enhance conveyor performance by providing the necessary torque and speed adjustments required for efficient operation. One of the primary advantages of using gear motors in conveyor systems is their ability to maintain consistent performance under varying load conditions. This consistency ensures smooth and reliable movement of materials along the conveyor, reducing the risk of jams and operational downtime.
The use of gear motors allows for precise control over the conveyor belt’s speed and torque, which is crucial for applications that demand specific handling requirements. For instance, in manufacturing environments where the speed of the conveyor belt must be synchronized with other production processes, gear motors provide the necessary control and flexibility.
Additionally, gear motors contribute to the overall efficiency of conveyor systems. By optimizing the motor’s output to match the conveyor’s requirements, gear motors reduce energy consumption and minimize wear and tear on the motor components. This not only extends the lifespan of the motor but also lowers maintenance costs and improves the system’s overall reliability.
Selection Criteria for Gear Motors in Conveyor Applications
Selecting the right gear motor for a conveyor application involves considering several critical factors to ensure optimal performance and efficiency. The first criterion is the load capacity of the conveyor system. The gear motor must be capable of handling the maximum load the conveyor will transport without compromising performance. This requires careful calculation of the required torque and speed.
Another important factor is the speed of the conveyor belt. Different applications have varying speed requirements, and the gear motor must be able to meet these needs. For example, high-speed conveyor systems used in packaging or assembly lines require gear motors that can maintain high speeds without sacrificing torque. Conversely, applications that require precise positioning or slower speeds, such as inspection systems, need gear motors that provide fine control over speed and torque.
The environment in which the conveyor operates is also a crucial consideration. Gear motors used in harsh environments, such as those exposed to dust, moisture, or extreme temperatures, need to be robust and well-sealed to prevent damage and ensure longevity. Selecting gear motors with appropriate IP ratings (Ingress Protection) can help protect against these environmental factors.
Energy efficiency is another key criterion. High-efficiency gear motors consume less energy, reducing operational costs and contributing to sustainability goals. Motors with high-efficiency ratings, such as those meeting IE3 or IE4 standards, are preferable for applications where energy consumption is a concern.
Finally, the ease of maintenance and availability of replacement parts should be considered. Gear motors that are easy to service and have readily available parts can significantly reduce downtime and maintenance costs, ensuring that the conveyor system remains operational with minimal interruptions.
Conveyor Belt Motors: Single Phase vs. Three Phase
Single Phase vs. Three Phase Conveyor Motors
When it comes to selecting the right conveyor belt motors for your system, understanding the differences between single phase and three phase motors is crucial. Both types have their unique characteristics, advantages, and applications. In this section, we will explore the specifics of single phase and three phase conveyor belt motors, including their voltage, load capacity, typical uses, and factors to consider when choosing between them.
Single Phase Motors
Single phase motors are powered by a single phase electrical supply, typically found in residential and light commercial applications. These motors operate using a single alternating current (AC) voltage source, which makes them suitable for less demanding tasks.
Voltage, Load Capacity, and Typical Uses:
Single phase motors generally operate at standard voltages such as 120V or 240V, depending on the region and application. They are designed to handle moderate load capacities, making them ideal for smaller conveyor systems that do not require high power output.
Typical uses of single phase conveyor belt motors include:
- Small Workshops: Single phase motors are commonly used in small workshops where heavy-duty industrial power is not necessary.
- Retail and Light Commercial Applications: These motors are ideal for conveyor systems in retail environments, such as moving products from storage to the sales floor.
- Residential Uses: Single phase motors can be found in home-based conveyor systems, such as small DIY projects or hobbyist setups.
The main advantage of single phase motors is their simplicity and ease of installation. They are less expensive and more readily available for non-industrial applications. However, they are not suitable for heavy-duty tasks that require substantial power and continuous operation.
Three Phase Motors
Three phase motors are powered by a three phase electrical supply, providing higher power output and efficiency. These motors use three alternating currents that are phase-shifted by 120 degrees, allowing for a more balanced and efficient power delivery.
Higher Power Output, Voltage Ratings, and Industrial Suitability:
Three phase motors typically operate at higher voltages, such as 208V, 230V, 460V, or even higher, depending on the industrial requirements. They are designed to handle much higher load capacities and are capable of running continuously under demanding conditions.
Typical uses of three phase conveyor belt motors include:
- Industrial Manufacturing: Three phase motors are widely used in industrial manufacturing plants, where they drive heavy-duty conveyor systems that move large volumes of materials.
- Large Warehouses and Distribution Centers: These motors power conveyor systems in large warehouses and distribution centers, ensuring efficient handling of goods and materials.
- Heavy Machinery and Equipment: Three phase motors are essential for operating heavy machinery and equipment in sectors such as mining, construction, and transportation.
The primary advantage of three phase motors is their ability to deliver consistent and high power output, making them suitable for industrial applications. They are more efficient than single phase motors and provide better performance under heavy loads.
Choosing Between Single Phase and Three Phase
Selecting the appropriate conveyor belt motor involves considering several factors, including power source availability, load requirements, and specific industrial needs. Here are some key considerations:
Power Source Availability:
- Single Phase: If your facility has access to a single phase power supply, single phase motors may be the more convenient and cost-effective choice. This is common in residential, retail, and light commercial environments.
- Three Phase: For facilities with access to a three phase power supply, three phase motors are typically the preferred option due to their higher efficiency and power output. Industrial plants and large commercial buildings usually have three phase power available.
Load Requirements:
- Single Phase: Suitable for lighter loads and less demanding applications. If your conveyor system is designed to handle small to moderate loads, a single phase motor may be sufficient.
- Three Phase: Essential for heavy loads and continuous operation. If your conveyor system needs to move large volumes of materials or operate non-stop, a three phase motor is necessary to ensure reliability and performance.
Industrial Needs:
- Single Phase: Best for applications where high power and continuous operation are not critical. They are easier to install and maintain, making them ideal for less intensive uses.
- Three Phase: Designed for industrial and heavy-duty applications. They provide the power and efficiency needed to keep large-scale conveyor systems running smoothly.
Conveyor Belt Motors: Common Issues and Maintenance Tips
Common Issues and Maintenance Tips
Conveyor belt motors are critical components of conveyor systems, providing the power and control needed to move materials efficiently. However, these motors can encounter various issues that affect their performance and longevity. Understanding common problems and implementing effective maintenance strategies can help ensure the reliability and efficiency of your conveyor belt motors.
Overloaded Belts
Causes and Solutions:
Overloaded belts occur when the conveyor system is tasked with moving materials beyond its designed capacity. This can cause excessive strain on the conveyor belt motors, leading to overheating, reduced efficiency, and potential motor failure.
Causes:
- Exceeding Weight Limits: Loading materials heavier than the specified capacity of the conveyor system.
- Accumulation of Materials: Materials piling up on the belt due to blockages or slow downstream processes.
Solutions:
- Proper Load Management: Ensure that the load on the conveyor belt is within the specified limits. Use scales and monitoring systems to track load weights and prevent overloading.
- Regular Maintenance: Inspect the conveyor system regularly to identify and clear any blockages or build-ups that could contribute to overloading.
- Upgrading Equipment: If frequent overloading is an issue, consider upgrading to more robust conveyor belt motors and belts that can handle higher capacities.
Mistrained Belts
Prevention and Correction Methods:
Mistrained belts, or belts that do not run straight along their intended path, can cause uneven wear, increased friction, and potential damage to both the belt and the conveyor belt motors.
Prevention:
- Regular Inspection: Regularly inspect the belt alignment and adjust tracking devices to ensure the belt runs true.
- Proper Installation: Ensure that the belt is installed correctly and that all components are properly aligned from the outset.
Correction Methods:
- Adjusting Rollers: Use tracking rollers to guide the belt back into alignment. Adjust these rollers carefully to correct any deviation without causing additional strain.
- Tension Adjustment: Ensure that the belt tension is appropriate. Over-tensioned or under-tensioned belts can lead to mistraining. Adjust the tension as needed to maintain proper alignment.
Slipping Belts
Identifying and Fixing Slippage Issues:
Belt slippage occurs when the belt does not move synchronously with the conveyor belt motors, leading to inefficiencies and potential damage.
Identifying Slippage:
- Observation: Visually inspect the conveyor system for signs of slippage, such as the belt lagging behind the rollers or uneven movement.
- Monitoring Systems: Use sensors and monitoring systems to detect slippage automatically. These systems can alert operators to issues before they become severe.
Fixing Slippage:
- Adjust Tension: Ensure that the belt tension is correct. Adjust the tension to prevent slippage while avoiding excessive tightness that could cause other issues.
- Replace Worn Components: Check for worn or damaged rollers and replace them as necessary. Worn rollers can contribute to slippage.
- Surface Treatments: Apply surface treatments to increase the friction between the belt and the rollers, reducing the likelihood of slippage.
Overcurrent Protection
Importance of Protecting Motors from Overcurrent:
Overcurrent can cause significant damage to conveyor belt motors, leading to overheating, insulation failure, and potential motor burnout. Protecting motors from overcurrent is crucial for maintaining system reliability and longevity.
Methods for Implementing Overcurrent Protection:
- Circuit Breakers: Use circuit breakers that trip when the current exceeds a safe threshold. Ensure that these breakers are appropriately rated for the motor and application.
- Fuses: Install fuses that blow when overcurrent conditions occur, providing a simple and effective means of protection.
- Overload Relays: Implement overload relays that monitor the current and disconnect the motor when an overcurrent condition is detected. These relays can be adjusted to match the specific requirements of the motor and application.
- Regular Testing: Conduct regular testing and maintenance of overcurrent protection devices to ensure they are functioning correctly. Replace or recalibrate these devices as needed to maintain optimal protection.
FAQS about Conveyor Belt Motors
The type of motor used in a conveyor belt typically depends on the application and requirements of the conveyor system. Commonly, induction motors and permanent magnet synchronous motors (PMSMs) are used. Induction motors are favored for their durability and ability to handle varying loads, while PMSMs are known for their efficiency and precision. For high torque and efficiency needs, AC motors are often preferred, but in applications requiring speed control and positioning, DC motors or servo motors might be used.
Choosing the right motor for a belt conveyor involves several key considerations:
Load Capacity: Determine the maximum load the conveyor will carry.
Speed Requirements: Define the belt speed necessary for the application.
Duty Cycle: Assess how frequently and for how long the conveyor will operate.
Environment: Consider environmental factors like temperature, humidity, and exposure to chemicals or dust.
Efficiency: Opt for motors with high efficiency to reduce energy consumption.
Control Requirements: Decide if precise speed or position control is needed, which might require a servo or variable frequency drive (VFD) motor. Consulting with manufacturers or using motor selection software can also aid in making an informed decision.
A conveyor motor operates by converting electrical energy into mechanical motion to drive the conveyor belt. The motor is connected to the conveyor belt via a gear system. When electrical current passes through the motor windings, it creates a magnetic field that interacts with the rotor, causing it to spin. This rotational motion is transferred through gears to the conveyor belt, making it move. The motor’s speed and torque can be controlled using variable frequency drives (VFDs) or other control mechanisms to ensure the conveyor operates efficiently and meets the application’s requirements.
Conveyor belts are typically powered by electric motors. These motors can be AC or DC types, depending on the application’s needs. In industrial settings, three-phase AC motors are common due to their efficiency and ability to handle high loads. For applications requiring variable speed and precise control, VFDs are often used in conjunction with the motors. In some cases, hydraulic or pneumatic systems might power conveyor belts, especially in environments where electric power is not ideal. The choice of power source depends on factors like load requirements, speed control, environmental conditions, and overall system design.
Last Updated on July 10, 2024 by Jordan Smith
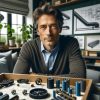
Jordan Smith, a seasoned professional with over 20 years of experience in the conveyor system industry. Jordan’s expertise lies in providing comprehensive solutions for conveyor rollers, belts, and accessories, catering to a wide range of industrial needs. From initial design and configuration to installation and meticulous troubleshooting, Jordan is adept at handling all aspects of conveyor system management. Whether you’re looking to upgrade your production line with efficient conveyor belts, require custom conveyor rollers for specific operations, or need expert advice on selecting the right conveyor accessories for your facility, Jordan is your reliable consultant. For any inquiries or assistance with conveyor system optimization, Jordan is available to share his wealth of knowledge and experience. Feel free to reach out at any time for professional guidance on all matters related to conveyor rollers, belts, and accessories.