What is Conveyor Belt Ply and Conveyor Belt Ply Adhesion
Conveyors are the backbone of many industrial operations, ensuring efficient material transport. At the core of these systems lies the crucial component: conveyor belts. But have you ever wondered what makes these belts so reliable and robust? The answer lies in the construction and quality of the conveyor belt ply. This blog post will delve into the concept of conveyor belt ply, exploring its significance, different types, thicknesses, pricing, and availability. By understanding these aspects, industrial users can make informed decisions to enhance their operations’ efficiency and longevity. Whether you’re upgrading an existing system or installing a new one, knowing about conveyor belt ply is essential for optimal performance.
What is Conveyor Belt Ply
Conveyor belts are essential components in numerous industries, from mining to manufacturing, ensuring efficient material transport. A critical aspect of conveyor belt construction is the ply. Conveyor belt ply refers to the layers of fabric or material that are bonded together to form a conveyor belt and resist ply separation. Conveyor belt ply refers to the layers of fabric or material bonded together to create the belt’s structure. These plies significantly influence the belt’s performance, durability, and application suitability. Understanding the intricacies of conveyor belt ply can help in selecting the right belt for specific industrial needs, enhancing efficiency and longevity.
- Layer Structure: Conveyor belt ply consists of multiple layers of fabric or materials, each contributing to the overall strength and functionality of the belt.
- Material Composition: Typically made from materials like polyester, nylon, cotton, or blends, each ply is chosen for its specific properties.
- Bonding Process: Layers are bonded using adhesives or heat treatments, ensuring a strong, cohesive structure.
- Number of Plies: Belts can range from single-ply to multi-ply, with each additional ply increasing the belt’s robustness.
- Thickness Variation: Ply thickness varies, impacting the belt’s flexibility and load-carrying capacity.
- Ply Adhesion: The force required to separate the plies, known as ply adhesion, is crucial for maintaining belt integrity.
- Strength Contribution: Each layer enhances the belt’s tensile strength, enabling it to handle heavier loads.
- Design Flexibility: Different configurations can be tailored to meet specific operational needs and conditions.
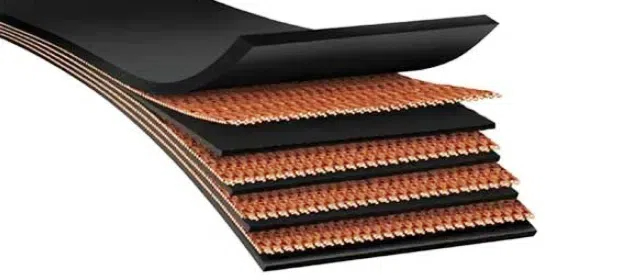
Importance of Ply in Determining the Strength and Durability of Conveyor Belts
- Tensile Strength: The number and quality of plies are vital in determining the belt’s tensile strength, directly affecting its load-bearing capacity.
- Flexibility and Bending: Adequate ply adhesion allows the belt to flex and bend over pulleys without delaminating, crucial for maintaining smooth operation.
- Durability Enhancement: Multi-ply construction enhances the belt’s resistance to cuts, tears, and impacts, significantly improving durability.
- Alignment and Tracking: Proper ply construction ensures that the belt maintains alignment and tracking, reducing operational issues.
- Lifespan Extension: High-quality ply materials and construction can extend the belt’s lifespan, decreasing downtime and maintenance costs.
- Environmental Resistance: The right ply materials provide resistance to various environmental factors like temperature extremes, chemicals, and moisture.
- Load Distribution: Multiple plies help in even load distribution across the belt, preventing localized stress points and potential failures.
- Energy Efficiency: Optimized ply construction can reduce friction and drag, leading to more efficient energy consumption in conveyor systems.
Types of Conveyor Belts
Understanding the types of conveyor belts is crucial for selecting the right belt for specific industrial applications. Conveyor belts are primarily categorized based on the number of plies they contain, with each type offering unique advantages and disadvantages. Some conveyor belts are made with one layer of fabric. This fabric layer may be coated with rubber, polymers, or elastomers. However, most conveyor belts are made with two or more layers of fabric that are bonded to each other using an inner layer of rubber, polymers, or elastomers.
Typical Materials Used in Different Plies:
- Rubber: Commonly used for general-purpose belts, offering good resistance to wear and tear.
- Polymer: Provides excellent chemical resistance, making it suitable for environments exposed to oils and solvents.
- Elastomer: Known for its flexibility and shock absorption, ideal for applications involving heavy impacts.
- Polyester: Offers high tensile strength and low stretch, suitable for high-tension applications.
- Nylon: Excellent flexibility and durability, perfect for belts requiring frequent bending and twisting.
- Cotton: Naturally coarse and absorbent, often used in food processing belts where hygiene is critical.
- Steel Cord: Provides exceptional strength and low elongation, used in heavy-duty mining and industrial applications.
- Kevlar: High impact and heat resistance, suitable for extreme conditions and high-stress environments.
Understanding conveyor belt ply is essential for selecting the right belt for specific needs, ensuring efficiency, durability, and cost-effectiveness in various industrial applications.
Conveyor Belt Ply Adhesion and Its Significance
Conveyor belts run on equipment that requires them to bend over pulleys on the belt. This repeated bending action will stress the inter-ply bond of the belt. Therefore, the belt must have an adequate inter-ply bond to prevent separation between the plies. Ply adhesion is a critical factor in the performance and longevity of conveyor belt ply. It refers to the force required to separate two adjoining plies, which directly impacts the belt’s durability and operational efficiency. Understanding ply adhesion helps in selecting the right conveyor belt for various industrial applications, ensuring optimal performance under different working conditions.
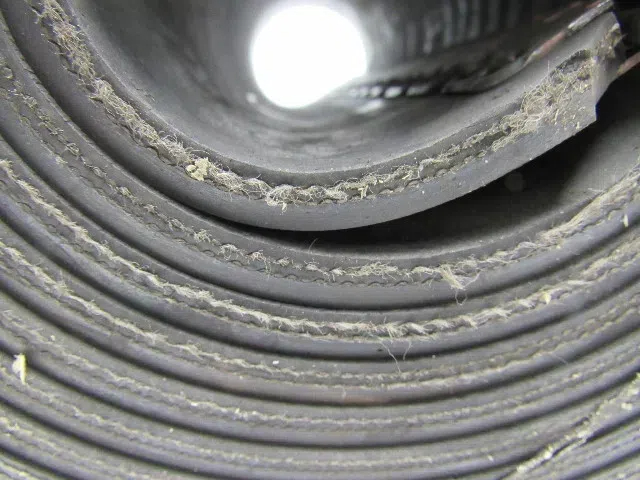
Ply adhesion is a crucial parameter that defines the bond strength between the layers, or plies, of a conveyor belt. This bond is essential for maintaining the integrity and performance of the belt under operational stresses. Proper ply adhesion ensures that the conveyor belt can endure the mechanical stresses and environmental conditions it will encounter.
- Force Required to Separate Plies: Ply adhesion is defined as the force needed to separate two layers of a conveyor belt ply, indicating the adhesive bond strength.
- Adhesive Bond Strength: It indicates the strength of the adhesive bond between the plies, which is crucial for maintaining the belt’s integrity during operation.
- Measurement Units: Ply adhesion is typically measured in pounds per inch (lbs/inch) or newtons per millimeter (N/mm), providing a quantifiable measure of bond strength.
- Adhesion Testing: The measurement involves testing the adhesive strength through various standardized methods to ensure consistency and reliability.
- Critical for Belt Performance: High ply adhesion is essential to prevent delamination during operation, which can lead to belt failure and operational downtime.
- Impact of Environmental Conditions: Adhesion strength can be affected by environmental factors like temperature, humidity, and exposure to chemicals, making it crucial to choose the right adhesive for specific conditions.
- Role in Flexibility: Good ply adhesion allows the belt to flex and bend over pulleys without separating, ensuring smooth and efficient operation.
- Material Compatibility: The choice of adhesive must be compatible with the materials used in the plies to ensure optimal adhesion and performance.
Importance of Ply Adhesion
Ply adhesion is fundamental to the durability and functionality of a conveyor belt. High adhesion strength ensures that the belt can withstand various operational stresses without delaminating, which is crucial for maintaining continuous and reliable operations in industrial environments.
- Durability Under Flexing and Stress: Adequate ply adhesion ensures the conveyor belt can withstand continuous flexing and stress without delaminating, which is essential for long-term durability.
- Longevity and Performance: Strong ply adhesion contributes to the overall longevity and consistent performance of the conveyor belt, reducing the need for frequent replacements.
- Resistance to Environmental Factors: High adhesion helps the belt resist adverse environmental conditions, such as extreme temperatures, humidity, and exposure to chemicals, ensuring reliable performance.
- Load-Bearing Capacity: Proper ply adhesion enhances the belt’s ability to carry heavy loads without the risk of ply separation, making it suitable for demanding applications.
- Operational Efficiency: Improved ply adhesion reduces the likelihood of belt failures, thus increasing operational efficiency and reducing downtime in industrial settings.
- Cost-Effectiveness: Investing in belts with high ply adhesion can lower maintenance costs and extend the belt’s service life, providing better value over time.
- Safety: Ensuring strong ply adhesion reduces the risk of sudden belt failures, contributing to safer working conditions for personnel.
- Optimized Performance: High ply adhesion ensures that the belt maintains its structural integrity, optimizing its performance in various applications, from light-duty to heavy-duty industrial use.
Testing and Standards
Testing and maintaining standards for ply adhesion are essential to ensure that conveyor belts perform reliably under various operational conditions. The “pull test” is a common method used to measure ply adhesion, providing a standardized way to evaluate the adhesive strength between plies.
- Description of the “Pull Test” Method: The pull test involves clamping a sample of the ply conveyor belt and measuring the force required to pull apart the plies, providing a direct measure of adhesive strength. In general terms, ply adhesion of fewer than 13 lbs per inch of width is considered unacceptably low. Ply adhesion of more than 50 lbs per inch of width is considered very high and can create challenges in belt fabrications where the plies need to be separated manually.
- Sample Preparation: Typically, a 1-inch wide and 8-inch long sample is prepared for testing to ensure consistency in the measurement.
- Clamping Device: The sample is secured in a clamping device designed to apply a uniform force, ensuring accurate and reliable results.
- Measurement Process: A fish scale or similar measuring device is used to record the force needed to separate the plies, providing a quantifiable measure of ply adhesion.
- Bidirectional Testing: Samples are tested in both directions to ensure consistent results and to account for any directional differences in adhesion strength.
- Statistical Reliability: Multiple samples are tested to achieve statistically reliable results, ensuring that the measured adhesion strength is representative of the belt’s overall performance.
- Industry Standards: Industry standards specify minimum ply adhesion values, ensuring the belts meet required performance criteria for safety and reliability.
- Compliance and Quality Assurance: Manufacturers must comply with these standards to ensure their conveyor belts are reliable and of high quality, providing confidence to users in various industrial applications.
Understanding ply adhesion and its significance is crucial for selecting the right conveyor belt ply. It ensures that the belt can handle the operational demands placed upon it, providing durability, efficiency, and safety in various industrial applications.
Conveyor Belt Ply Thickness
Conveyor belt ply thickness is a critical parameter that directly affects the belt’s performance and suitability for various industrial applications. The thickness of the plies in a conveyor belt determines its strength, flexibility, and load-bearing capacity. Understanding the nuances of conveyor belt ply thickness can help in selecting the right belt for specific operational needs, ensuring optimal efficiency and longevity.

Ply thickness is a fundamental aspect of conveyor belt design, influencing various operational characteristics of the belt. Here, we delve into how ply thickness is measured and why it is significant for conveyor belt performance.
- Measurement of Ply Thickness: Ply thickness is typically measured in millimeters or inches, representing the combined thickness of all layers, including the covers.
- Impact on Strength: Thicker plies generally contribute to greater tensile strength, allowing the belt to handle heavier loads without failing.
- Flexibility Considerations: While thicker plies offer more strength, they may reduce the belt’s flexibility, making it less suitable for applications requiring frequent bending.
- Wear Resistance: Increased ply thickness often enhances the belt’s resistance to wear and tear, making it more durable in abrasive environments.
- Heat Dissipation: Thicker belts can better dissipate heat generated from friction, preventing overheating and extending belt life.
- Load Distribution: The thickness of the plies affects how the load is distributed across the belt, impacting its ability to carry heavy or unevenly distributed loads.
- Customization: Conveyor belt ply thickness can be customized based on specific operational requirements, ensuring the belt meets the demands of the application.
- Adhesive Bonding: Proper adhesion between thicker plies is crucial to maintain the integrity of the belt under stress.
Common Thicknesses
The thickness of the plies in a conveyor belt varies depending on the number of plies and their intended application. Here, we examine common thicknesses for 3-ply and 4-ply conveyor belts and their typical uses.
3-Ply Conveyor Belt Thickness:
3-Ply Conveyor Belt Thickness:
- Description: Typically ranges from 5 to 10 millimeters.
- Applications: Used in medium-duty applications where a balance of strength and flexibility is needed.
- Advantages: Provides good tensile strength with moderate flexibility, suitable for general industrial use.
- Examples: Commonly found in manufacturing and assembly lines, packaging industries, and material handling.
4-Ply Conveyor Belt Thickness:
- Description: Generally ranges from 8 to 15 millimeters.
- Applications: Ideal for heavy-duty applications requiring high tensile strength and durability.
- Advantages: Offers increased strength and durability, making it suitable for more demanding environments.
- Examples: Used in mining, construction, and heavy material transport where high load-bearing capacity is essential.
Significance of Ply Thickness:
- Strength and Load Capacity: Thicker plies enhance the belt’s ability to carry heavy loads without deformation or failure.
- Durability and Longevity: Increased thickness improves the belt’s resistance to abrasion and mechanical damage, extending its service life.
- Environmental Suitability: Different thicknesses are chosen based on the operating environment, such as high temperatures, exposure to chemicals, or abrasive conditions.
- Cost Considerations: While thicker belts may cost more initially, their durability can lead to cost savings over time through reduced maintenance and replacement needs.
- Operational Efficiency: Selecting the appropriate ply thickness ensures the belt operates efficiently, minimizing downtime and maximizing productivity.
- Flexibility vs. Rigidity: The right balance of thickness ensures the belt can flex as needed without compromising its structural integrity.
Understanding the importance of conveyor belt ply thickness helps in making informed decisions about the right belt for specific applications. By considering factors such as load capacity, environmental conditions, and operational requirements, industrial users can select a conveyor belt that offers optimal performance and longevity.
Multi-Layer Rubber Textile Conveyor Belt
1. Components
A multi-layer rubber textile conveyor belt comprises several key components:
- Top Cover: Made of rubber, this layer protects the belt from wear and impact.
- Ply Layers: Multiple layers of fabric (usually polyester, nylon, or cotton) provide strength and flexibility.
- Bottom Cover: Similar to the top cover, this rubber layer protects the belt from the pulley and other mechanical elements.
- Skim Coats: Thin layers of rubber between the fabric plies enhance adhesion and overall durability.
2. Structure
The structure of a multi-layer rubber textile conveyor belt includes:
- Multiple Fabric Plies: Typically 2 to 6 layers of fabric are used, each separated by skim coats.
- Rubber Covers: Both top and bottom rubber covers protect the fabric plies and provide a smooth, durable surface.
- Bonding Layers: Skim coats of rubber between the fabric layers ensure a strong bond and enhance the belt’s resistance to flexing and bending.
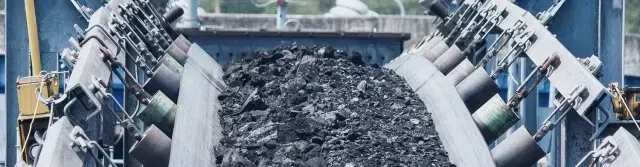
3. Materials and Quality
The materials used in multi-layer rubber textile conveyor belts include:
- Rubber: High-quality natural or synthetic rubber is used for the covers, providing abrasion resistance, flexibility, and durability.
- Fabric: Polyester, nylon, or cotton fabric is chosen for its strength, flexibility, and resistance to stretch.
- Adhesives: Specialized adhesives ensure a strong bond between rubber and fabric layers.
The quality of these materials is crucial, as it determines the belt’s performance, lifespan, and resistance to various operational stresses.
4. Production Process
The production process of multi-layer rubber textile conveyor belts involves several steps:
- Fabric Preparation: Fabric layers are treated and coated with skim rubber to ensure strong adhesion.
- Layering: Fabric plies and rubber layers are assembled in the desired configuration.
- Vulcanization: The assembled belt is subjected to heat and pressure in a vulcanization press, causing the rubber to cure and bond with the fabric layers.
- Finishing: The belt is trimmed and finished to meet specified dimensions and quality standards.
- Quality Control: Rigorous testing ensures the belt meets all performance and durability requirements.
5. Application
Multi-layer rubber textile conveyor belts are used in various industries, including:
- Mining: For transporting ores, coal, and other minerals.
- Construction: For moving sand, gravel, and other building materials.
- Agriculture: For handling grains, feed, and fertilizers.
- Manufacturing: For conveying raw materials and finished products.
- Ports and Shipping: For bulk material handling and loading/unloading operations.
These belts are chosen for their durability, strength, and ability to handle a wide range of materials and conditions.
In summary, multi-layer rubber textile conveyor belts are robust, versatile components crucial for efficient material handling across various industries. Their construction, materials, and production process ensure they meet the demanding requirements of different applications.
Used Conveyor Belt Ply
Utilizing used conveyor belt ply can be a cost-effective and practical solution for many industries. While new belts provide the latest technology and materials, used conveyor belt ply offers several advantages that make it a viable option for specific applications. However, it’s essential to consider various factors to ensure that the used belts meet operational requirements and maintain performance standards.
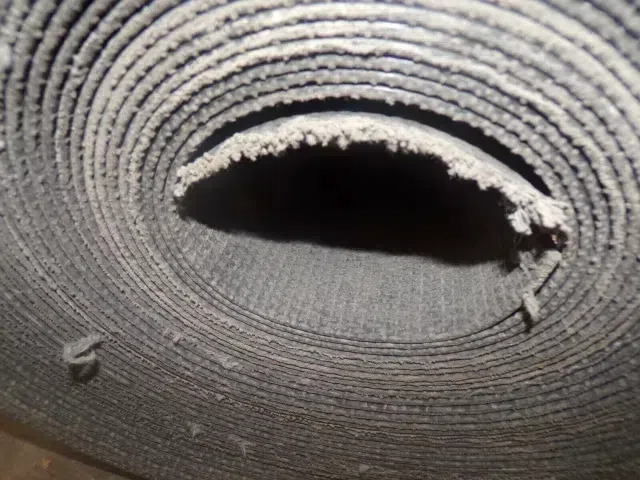
Advantages of Used Conveyor Belt Ply
There are numerous benefits to choosing used conveyor belt ply, making it an attractive option for many businesses looking to balance cost and functionality.
- Cost Savings: One of the primary advantages is significant cost savings. Used conveyor belt ply is typically much cheaper than new belts, allowing businesses to allocate their budget to other critical areas.
- Availability: Used conveyor belts are often readily available, reducing lead times associated with manufacturing new belts. This quick availability can be crucial for minimizing downtime.
- Quick Delivery: Due to their immediate availability, used belts can be delivered and installed quickly, ensuring that operations can resume without lengthy delays.
- Sustainability: Reusing conveyor belts contributes to sustainability by reducing waste and promoting the recycling of materials. This eco-friendly approach can also enhance the company’s green credentials.
- Adequate Performance for Non-Critical Applications: For less demanding applications where the highest performance levels are not required, used belts can provide adequate functionality at a lower cost.
- Testing and Proven Performance: Used belts have a history of use, which means their performance and durability are known. This track record can help in assessing their suitability for specific tasks.
- Ease of Replacement: Used belts can be an excellent option for temporary solutions or as a stop-gap measure while waiting for new belts. Their lower cost makes frequent replacements more feasible.
- Lower Initial Investment: For startups or businesses operating on tight budgets, used conveyor belt ply represents a lower initial investment, freeing up capital for other essential expenses.
- Flexibility in Applications: Used belts can be adapted or modified for various applications, offering flexibility and versatility in their use.
Considerations When Buying Used Ply
While there are many advantages to using used conveyor belt ply, it is essential to consider several factors to ensure you make an informed and suitable choice.
- Condition and Remaining Lifespan: Assess the overall condition and estimate the remaining lifespan of the belt. Check for signs of excessive wear, tears, or significant damage that could impact performance.
- History of Usage: Understand the belt’s previous applications and usage history. Belts used in less demanding environments may have longer remaining life than those used in heavy-duty applications.
- Maintenance Records: Review the maintenance history of the belt. Properly maintained belts are likely to have a longer and more reliable remaining lifespan.
- Thickness and Ply Count: Verify that the thickness and number of plies meet your operational requirements. Ensure the belt has the necessary structural integrity for your specific application.
- Ply Adhesion: Check the adhesion between the plies. Weak adhesion can lead to delamination, which can significantly reduce the belt’s effectiveness and safety.
- Environmental Suitability: Ensure the used belt is suitable for your working environment, considering factors such as temperature, humidity, and exposure to chemicals.
- Cost Comparison: Compare the cost of the used belt with the potential savings from reduced downtime and lower initial investment. Ensure that the cost benefits outweigh any potential drawbacks.
- Warranty and Support: Some suppliers may offer warranties or support for used belts. Check if such options are available, as they can provide additional assurance of the belt’s performance and longevity.
By carefully considering these factors, businesses can effectively utilize used conveyor belt ply, benefiting from cost savings and quick availability while ensuring that the belts meet their specific operational needs.
Availability and Purchasing of Conveyor Belt Ply
When it comes to purchasing conveyor belt ply, it’s essential to know where to buy from and what factors to consider to ensure you get the best quality and value for your investment. Various suppliers and online marketplaces offer a range of options, making it easier to find the right conveyor belt ply for your needs.
Where to Buy Conveyor Belt Ply
Finding reliable sources for conveyor belt ply is crucial for ensuring you get high-quality products. Here are some leading suppliers and manufacturers, as well as online marketplaces and industrial equipment dealers:
Leading Suppliers and Manufacturers:
- Dunlop Conveyor Belting: Known for producing high-quality conveyor belts with excellent durability and performance.
- Fenner Dunlop: Offers a wide range of conveyor belt products suitable for various industries, known for their reliability and advanced technology.
- Continental AG: A global leader in manufacturing conveyor belts, providing innovative solutions for diverse applications.
- Sparks Belting Company: Specializes in custom conveyor belting solutions tailored to specific industrial needs.
- Habasit: Offers a comprehensive range of conveyor belts, known for their quality and efficiency in numerous applications.
Online Marketplaces and Industrial Equipment Dealers:
- Alibaba: A vast online marketplace where you can find numerous suppliers offering conveyor belt ply at competitive prices.
- Amazon Industrial Supplies: Offers a variety of conveyor belts from different brands, catering to various industrial needs.
- ThomasNet: A reliable online platform connecting buyers with verified suppliers of conveyor belts and related products.
- Grainger: A well-known supplier of industrial equipment, including ply conveyor belt, with a focus on quality and service.
- eBay: Provides a range of new and used conveyor belts, offering cost-effective solutions for various applications.
Factors to Consider
When purchasing conveyor belt ply, several factors need to be considered to ensure you select the right product for your specific requirements. Here are the key factors to keep in mind:
- Compatibility with Existing Conveyor Systems: Ensure that the conveyor belt ply you purchase is compatible with your existing conveyor systems. Consider the dimensions, load capacity, and specific operational requirements.
- Quality and Durability: Assess the quality of the conveyor belt ply. High-quality belts are made from durable materials that can withstand the rigors of your application, reducing downtime and maintenance costs.
- Warranty and Return Policies: Understand the warranty and return policies offered by the supplier. A good warranty provides assurance of the product’s quality and can save costs in case of defects or issues.
- Supplier Reputation: Research the reputation of the supplier or manufacturer. Trusted suppliers with positive reviews are more likely to provide reliable and high-quality conveyor belt ply.
- Cost and Value: Compare prices from different suppliers to ensure you get the best value for your investment. Consider the total cost, including shipping, installation, and potential maintenance.
- Customization Options: Some applications may require custom conveyor belt ply. Check if the supplier offers customization options to meet your specific needs.
- Delivery Time: Consider the delivery time for the conveyor belt ply. Quick delivery can be crucial for minimizing downtime and maintaining operational efficiency.
- Environmental Suitability: Ensure that the conveyor belt ply is suitable for your operating environment. Factors such as temperature resistance, chemical exposure, and humidity should be considered to avoid premature wear and failure.
By considering these factors and choosing reliable suppliers, you can ensure that you purchase the right conveyor belt ply that meets your operational needs and provides long-term value and performance.
Examples and Applications of Conveyor Belt Ply
Understanding the diverse applications and success stories of conveyor belt ply can provide valuable insights into its versatility and importance across various industries. By examining specific case studies, we can see how different ply configurations and materials have been successfully implemented to meet the demands of various sectors. Additionally, practical tips can help guide the selection and maintenance of conveyor belts to ensure optimal performance and longevity.
Case Studies
Case studies offer real-world examples of how conveyor belt ply is utilized across different industries. These examples highlight the importance of selecting the right ply configuration and material to achieve operational success and efficiency.
Mining Industry – Rio Tinto:
- Ply Configuration: Multi-ply conveyor belts.
- Example: Rio Tinto uses heavy-duty multi-ply conveyor belts in their mining operations to handle large quantities of ore.
- Success Story: By choosing high-tensile strength multi-ply belts, Rio Tinto reduced maintenance costs and increased operational efficiency. The robust design of these belts allows them to withstand the harsh conditions of mining environments, ensuring continuous and reliable operation.
Food Processing – Tyson Foods:
- Ply Configuration: Single-ply and multi-ply conveyor belts.
- Example: Tyson Foods utilizes both single-ply and multi-ply conveyor belts for different stages of food processing.
- Success Story: The use of food-grade, easy-to-clean single-ply belts in processing areas ensures high hygiene standards, while durable multi-ply belts in packaging lines enhance operational efficiency. This combination has optimized hygiene and productivity, meeting stringent industry standards.
Automotive Manufacturing – Ford Motor Company:
- Ply Configuration: Multi-ply conveyor belts.
- Example: Ford Motor Company employs multi-ply conveyor belts in their assembly lines.
- Success Story: The durable and flexible nature of multi-ply belts has minimized downtime and ensured smooth production processes. This has enhanced overall productivity and maintained a steady flow of operations in their assembly lines, contributing to efficient automotive manufacturing.
Logistics and Distribution – Amazon Fulfillment Centers:
- Ply Configuration: Multi-ply conveyor belts.
- Example: Amazon uses multi-ply conveyor belts in their fulfillment centers to manage the high volume of packages.
- Success Story: The robustness of multi-ply belts has significantly reduced wear and tear, ensuring efficient and reliable handling of packages. This has enabled Amazon to maintain fast and efficient delivery times, supporting their high-paced logistics operations.
Recycling Industry – Waste Management Inc.:
- Ply Configuration: Multi-ply conveyor belts.
- Example: Waste Management Inc. uses multi-ply conveyor belts to sort and transport recyclable materials.
- Success Story: By selecting belts with high abrasion resistance, they have enhanced the longevity and reliability of their sorting lines. This has improved their recycling processes, making them more efficient and cost-effective.
Pharmaceutical Manufacturing – Pfizer:
- Ply Configuration: Single-ply and multi-ply conveyor belts.
- Example: Pfizer employs single-ply belts for cleanroom environments and multi-ply belts for bulk material handling.
- Success Story: The combination of appropriate belt types has ensured compliance with strict hygiene standards and efficient material transport. This has optimized their production processes, ensuring high-quality pharmaceutical products.
Practical Tips
Selecting the right conveyor belt ply and maintaining it properly can significantly impact the efficiency and lifespan of your conveyor system. Here are some practical tips to guide you:
- Determine the Best Ply Thickness: Assess the load requirements and operational conditions of your application. Consider the weight, size, and type of materials being transported. Consult with suppliers to understand the optimal ply thickness for your specific needs.
- Evaluate Environmental Factors: Consider temperature, humidity, and exposure to chemicals. Choose materials that can withstand the specific environmental conditions of your operation.
- Check Compatibility with Existing Systems: Ensure the new belt is compatible with your existing conveyor system. Verify dimensions, load capacities, and pulley configurations.
- Regular Maintenance: Schedule regular inspections to check for signs of wear, tear, and damage. Clean belts regularly to remove debris and prevent buildup that can cause damage.
- Proper Tensioning: Maintain proper tension in the conveyor belt to avoid slippage and excessive wear. Use tension indicators to ensure the belt is correctly tensioned.
- Lubrication: Keep moving parts well-lubricated to reduce friction and wear. Use appropriate lubricants that are compatible with the belt materials.
- Training for Operators: Train operators on the correct handling and maintenance procedures. Ensure they understand how to identify potential issues and perform basic troubleshooting.
- Invest in Quality: Choose high-quality conveyor belt ply from reputable suppliers. While it may have a higher upfront cost, it can lead to significant savings in the long run through reduced maintenance and longer lifespan.
By following these practical tips and learning from successful case studies, businesses can optimize their use of conveyor belt ply, ensuring efficient and reliable operations across various industries.
FAQs about Conveyor Belt Ply
Conveyor belt ply refers to the layers of fabric or material that are bonded together to form a conveyor belt. Each layer, known as a ply, contributes to the overall strength and durability of the belt. The plies are typically made from materials such as polyester, nylon, cotton, or a blend of these. The number of plies in a conveyor belt can vary depending on the intended application, ranging from single-ply to multiple plies. Multi-ply conveyor belts are designed to handle heavier loads and more demanding conditions by providing greater tensile strength and resistance to wear and tear. The bonding between the plies is crucial for maintaining the integrity of the belt, preventing delamination, and ensuring long-term performance. Understanding the composition and configuration of conveyor belt ply is essential for selecting the right belt for specific industrial applications.
A 3 ply conveyor belt consists of three layers of fabric or material bonded together to form the belt. The thickness of a 3 ply conveyor belt typically ranges from 5 to 10 millimeters, depending on the materials used and the specific requirements of the application. Each ply contributes to the overall strength and durability of the belt, with the three layers providing a balance of flexibility and tensile strength. This configuration is commonly used in medium-duty applications where the belt needs to withstand moderate loads and abrasion while maintaining flexibility for efficient operation. The exact thickness of a 3 ply conveyor belt can vary based on the type of fabric or material used, the bonding process, and the intended use, ensuring that the belt meets the operational demands of the industry.
The primary difference between 2 ply and 3 ply conveyor belts lies in the number of fabric or material layers that make up the belt. A 2 ply conveyor belt consists of two layers of material, while a 3 ply conveyor belt has three layers. This difference in the number of plies affects the belt’s overall strength, flexibility, and durability.
A 2 ply conveyor belt is typically thinner and more flexible, making it suitable for lighter-duty applications where the belt needs to bend around smaller pulleys or navigate more complex conveyor systems. In contrast, a 3 ply conveyor belt, with its additional layer, provides greater tensile strength and resistance to wear and tear. This makes it more suitable for medium-duty applications where the belt is subjected to higher loads and more abrasive conditions. The choice between a 2 ply and 3 ply conveyor belt depends on the specific operational requirements, including the type of material being transported, the load capacity, and the environmental conditions.
In flat belts, “ply” refers to the individual layers of fabric or material that are bonded together to create the belt. Each ply consists of a woven fabric or synthetic material that adds to the overall strength, flexibility, and durability of the belt. The number of plies in a flat belt can vary, typically ranging from a single ply to multiple plies, depending on the belt’s intended application and the required performance characteristics.
Flat belts with more plies generally offer increased tensile strength and resistance to wear and tear, making them suitable for more demanding applications. The plies are bonded together using adhesives or heat treatments to ensure a strong and cohesive structure. The construction of the plies and the materials used can significantly impact the belt’s performance, including its ability to withstand loads, resist abrasion, and maintain flexibility. Understanding the ply configuration in flat belts is crucial for selecting the right belt for specific industrial uses, ensuring optimal performance and longevity.
The primary difference between 3 ply and 4 ply conveyor belts lies in their construction and resulting strength and durability. “Ply” refers to the number of fabric layers incorporated into the belt.
3 Ply Conveyor Belts: These belts consist of three layers of fabric, typically sandwiched between layers of rubber. The three-ply construction provides a balance of strength, flexibility, and durability. They are often used in medium-duty applications where moderate tensile strength and flexibility are required.
4 Ply Conveyor Belts: These belts contain four layers of fabric, offering increased strength and durability compared to 3 ply belts. The additional ply enhances the belt’s ability to handle heavier loads and withstand greater impact and abrasion. Consequently, 4 ply belts are suitable for more demanding applications, such as heavy-duty mining, quarrying, and bulk material handling.
The choice between 3 ply and 4 ply conveyor belts depends on the specific needs of the application. 4 ply belts are preferred for their enhanced strength and durability in more rigorous environments, while 3 ply belts are suitable for medium-duty tasks that require a balance of flexibility and strength.
The thickness of a 2 ply conveyor belt can vary depending on the specific construction and the materials used. Generally, a 2 ply conveyor belt consists of two layers of fabric with a layer of rubber or other synthetic material on both sides. The overall thickness typically ranges from 3.2 mm (0.125 inches) to 5.5 mm (0.218 inches), though it can be customized to suit specific requirements.
Standard Thickness: For many standard applications, a 2 ply conveyor belt has a thickness around 4 mm (0.157 inches). This thickness is adequate for light to medium-duty applications, providing sufficient strength and flexibility for conveying a variety of materials.
Customized Thickness: Depending on the application, the thickness can be adjusted. For instance, lighter-duty belts may be thinner, while those designed for heavier loads or more abrasive materials may be thicker.
It’s important to select the appropriate belt thickness based on the operational demands, including the type of material being conveyed, the conveyor system’s configuration, and environmental conditions. A properly chosen belt thickness ensures optimal performance, longevity, and safety in material handling operations.
Last Updated on August 9, 2024 by Jordan Smith
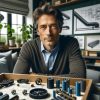
Jordan Smith, a seasoned professional with over 20 years of experience in the conveyor system industry. Jordan’s expertise lies in providing comprehensive solutions for conveyor rollers, belts, and accessories, catering to a wide range of industrial needs. From initial design and configuration to installation and meticulous troubleshooting, Jordan is adept at handling all aspects of conveyor system management. Whether you’re looking to upgrade your production line with efficient conveyor belts, require custom conveyor rollers for specific operations, or need expert advice on selecting the right conveyor accessories for your facility, Jordan is your reliable consultant. For any inquiries or assistance with conveyor system optimization, Jordan is available to share his wealth of knowledge and experience. Feel free to reach out at any time for professional guidance on all matters related to conveyor rollers, belts, and accessories.