How to Select the Right Conveyor Belt Pulley Sizes
Conveyor belt pulley sizes play a crucial role in the efficiency and functionality of industrial conveyor systems. These pulleys are integral components that drive the belts, enabling the movement of materials across various stages of production. Proper sizing of conveyor belt pulleys ensures optimal performance, reducing wear and tear on the belt, minimizing downtime, and enhancing the overall efficiency of the system. Incorrect pulley sizes can lead to belt slippage, increased energy consumption, and potential system failures. Understanding and selecting the right conveyor belt pulley sizes is essential for maintaining smooth operations and achieving maximum productivity in industrial applications. This guide will delve into the importance of these sizes and how they impact your conveyor systems.
What are Conveyor Belt Pulley Sizes
When it comes to conveyor systems, understanding conveyor belt pulley sizes is essential for ensuring optimal performance and efficiency. Conveyor belt pulleys are vital components that influence the movement, speed, and direction of the conveyor belt. Proper sizing and selection of these pulleys can greatly impact the system’s functionality, longevity, and safety. This section will provide a detailed explanation of the common terminologies related to conveyor belt pulley sizes, along with examples to enhance your understanding.
Common Terminologies Related to Conveyor Belt Pulley Sizes
To fully grasp the importance of conveyor belt pulley sizes, it is crucial to familiarize yourself with the common terminologies used in the industry.
- Diameter
- Face Width
- Shaft Diameter
- Hub Diameter
- Crown
Diameter refers to the distance across the circular cross-section of the pulley, measured from one edge to the opposite edge. It is a critical dimension as it affects the belt speed and tension. For example, a pulley with a larger diameter will have a slower belt speed compared to a smaller diameter pulley for the same rotational speed.
Face Width is the width of the pulley surface that comes into contact with the conveyor belt. This dimension is important for accommodating the belt width and ensuring proper alignment and tracking. A wider face width can support a wider belt, providing better stability and load distribution.
Shaft Diameter pertains to the diameter of the shaft that passes through the pulley, providing support and facilitating rotation. The shaft diameter must be compatible with the pulley’s bore and designed to handle the load and torque requirements of the conveyor system. For instance, a conveyor system with heavy loads may require a larger shaft diameter to prevent bending or breaking.
Hub Diameter is the diameter of the hub, which is the central part of the pulley that connects to the shaft. The hub diameter is crucial for ensuring a secure fit and proper torque transmission between the shaft and the pulley. Selecting the correct hub diameter helps maintain the structural integrity and performance of the conveyor system.
Crown refers to the slight curvature on the surface of the pulley, designed to aid in belt tracking. A crowned pulley has a higher center and gradually slopes down towards the edges. This design helps the belt stay centered on the pulley, reducing the risk of misalignment and improving overall belt performance. For example, a pulley with a 1/8 inch crown can significantly enhance the tracking of a conveyor belt, especially in long conveyor systems.
Standard Conveyor Belt Pulley Sizes
Understanding the standard sizes for conveyor belt pulleys is essential for selecting the right pulley for your system. Conveyor pulleys come in various sizes, and these sizes are often standardized to ensure compatibility with different conveyor belts and systems. The sizes typically include both metric and imperial measurements to cater to diverse industrial applications.
For instance, a standard conveyor belt pulley size might be a 12-inch diameter with a 24-inch face width and a 3-inch shaft diameter. Another example could be a metric-sized pulley with a 300mm diameter, 600mm face width, and 75mm shaft diameter. These standard sizes are designed to meet common industrial requirements and provide reliable performance across various applications.
Importance of Selecting the Right Conveyor Belt Pulley Sizes
Selecting the correct conveyor belt pulley sizes is crucial for several reasons. First, it ensures that the conveyor belt runs smoothly and efficiently, minimizing the risk of belt slippage or misalignment. Proper pulley sizing also reduces wear and tear on the belt and other conveyor components, extending their lifespan and reducing maintenance costs.
Additionally, the right pulley sizes contribute to the overall safety of the conveyor system. Incorrectly sized pulleys can lead to excessive belt tension, which may cause the belt to snap or the pulley to fail. This can result in costly downtime, equipment damage, and potential safety hazards for workers.
By understanding conveyor belt pulley sizes and the associated terminologies, you can make informed decisions when selecting pulleys for your conveyor system. This knowledge helps optimize the performance, efficiency, and safety of your industrial operations, ensuring smooth and reliable material handling processes.
Understanding conveyor belt pulley sizes involves familiarizing yourself with key terminologies such as diameter, face width, shaft diameter, hub diameter, and crown. Knowing these terms and their implications on conveyor system performance allows you to choose the right pulleys for your specific needs, enhancing the overall efficiency and reliability of your conveyor system.
Standard Conveyor Belt Pulley Sizes
When it comes to conveyor systems, standard conveyor belt pulley sizes are essential for ensuring compatibility and optimal performance. These sizes are often standardized to meet industry requirements, providing reliable and efficient material handling solutions across various applications. Understanding these standard sizes helps in selecting the right pulleys for your conveyor system, ensuring smooth operations and longevity.
Chart Overview
A comprehensive chart of standard conveyor belt pulley sizes provides a quick reference for selecting the appropriate pulley for your needs. This chart includes dimensions in both inches and metric units, catering to diverse industrial requirements. Below, we introduce a sample chart detailing standard conveyor belt pulley sizes.
Importance of Standard Conveyor Belt Pulley Sizes
Standard conveyor belt pulley sizes ensure consistency and compatibility across different conveyor systems. By adhering to these standardized dimensions, manufacturers and operators can easily replace or upgrade pulleys without extensive modifications. This standardization also simplifies maintenance and reduces downtime, as compatible parts are readily available.
Using standard sizes also aids in achieving optimal performance. Each size is designed to handle specific load capacities and operational speeds, ensuring that the conveyor system runs efficiently and reliably. Properly sized pulleys reduce the risk of belt slippage, misalignment, and excessive wear, extending the lifespan of the entire conveyor system.
Moreover, standard conveyor belt pulley sizes facilitate better design and customization. Engineers can use these standard dimensions as a baseline for designing custom solutions tailored to unique industrial requirements. This flexibility allows for the creation of specialized conveyor systems that meet specific operational needs while maintaining the benefits of standardized components.
Understanding standard conveyor belt pulley sizes is crucial for selecting the right components for your conveyor system. A comprehensive chart of these sizes provides a valuable reference, ensuring that you choose pulleys that meet your specific requirements. By using standardized pulley sizes, you can enhance the performance, efficiency, and longevity of your conveyor system, ensuring smooth and reliable material handling operations.
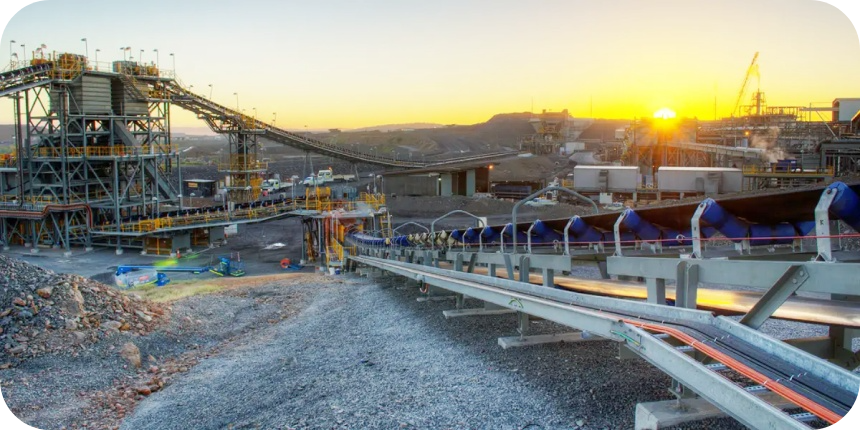
Heavy Duty Conveyor Belt Pulley Sizes
In the realm of industrial applications, heavy-duty conveyor belt pulley sizes are designed to withstand extreme conditions and handle significant loads. These pulleys are built with robust materials and specifications to ensure reliability and efficiency in demanding environments. Understanding the specifications and differences between standard and heavy-duty pulleys is essential for selecting the right components for your conveyor system.
Specifications for Heavy-Duty Applications
Heavy-duty conveyor belt pulleys are engineered to meet the rigorous demands of high-capacity and high-stress operations. Here are five examples of heavy-duty pulley specifications:
Pulley Diameter: 36 inches (914 mm)
- Face Width: 60 inches (1524 mm)
- Shaft Diameter: 10 inches (254 mm)
- Material: High-strength alloy steel
- Application: Mining operations, handling large volumes of ore.
Pulley Diameter: 42 inches (1067 mm)
- Face Width: 72 inches (1829 mm)
- Shaft Diameter: 12 inches (305 mm)
- Material: Reinforced composite materials
- Application: Heavy-duty manufacturing lines, transporting heavy equipment parts.
Pulley Diameter: 48 inches (1219 mm)
- Face Width: 84 inches (2134 mm)
- Shaft Diameter: 14 inches (356 mm)
- Material: Carbon steel with anti-corrosion coating
- Application: Port and dock loading systems, handling shipping containers.
Pulley Diameter: 54 inches (1372 mm)
- Face Width: 96 inches (2438 mm)
- Shaft Diameter: 16 inches (406 mm)
- Material: Hardened steel with wear-resistant surface
- Application: Bulk material handling, such as coal and grain transport.
Pulley Diameter: 60 inches (1524 mm)
- Face Width: 108 inches (2743 mm)
- Shaft Diameter: 18 inches (457 mm)
- Material: Ultra-high molecular weight polyethylene (UHMWPE)
- Application: Large-scale agricultural operations, moving heavy loads of crops and soil.
Difference Between Standard and Heavy-Duty Pulley Sizes and Materials
The key differences between standard and heavy-duty conveyor belt pulley sizes lie in their dimensions and the materials used. Heavy-duty pulleys are designed to handle greater stresses and loads, requiring enhanced structural integrity and durability. Below is a table that illustrates these differences:
Pulley Diameter: Heavy-duty pulleys have significantly larger diameters compared to standard pulleys, which allows them to support heavier loads and reduce the chances of belt slippage.
Face Width: The face width of heavy-duty pulleys is also greater, providing more surface area for the conveyor belt to interact with. This helps distribute the load more evenly and prevents belt wear and tear.
Shaft Diameter: The shaft diameter in heavy-duty pulleys is much larger, ensuring that the shaft can handle the increased torque and load without bending or breaking.
Material: Standard pulleys are typically made from mild steel or aluminum, which are adequate for light to moderate loads. In contrast, heavy-duty pulleys use high-strength materials such as alloy steel, reinforced composites, and UHMWPE. These materials provide enhanced durability, wear resistance, and corrosion protection.
Load Capacity: Heavy-duty pulleys are designed to handle significantly higher load capacities. This makes them suitable for applications that involve extreme loads, such as mining, bulk material handling, and port operations.
Applications: Standard pulleys are used in applications involving light to moderate loads, such as packaging and assembly lines. Heavy-duty pulleys, on the other hand, are used in environments that require the transportation of heavy and bulk materials, such as mining, ports, and heavy manufacturing.
Understanding the specifications and differences between standard and heavy-duty conveyor belt pulley sizes is crucial for selecting the right components for your conveyor system. Heavy-duty pulleys are designed to withstand higher loads and more demanding conditions, making them essential for high-capacity and high-stress industrial applications. By choosing the appropriate pulley sizes and materials, you can ensure the efficiency, reliability, and longevity of your conveyor system.
Metric and Imperial Measurements of Conveyor Belt Pulley Sizes
Understanding the metric and imperial measurements of conveyor belt pulley sizes is crucial for ensuring the proper selection and compatibility of components in various industrial applications. Both measurement systems are widely used, and knowing when to use each can significantly impact the efficiency and functionality of your conveyor system. This section provides a detailed comparison between conveyor belt pulley sizes in inches and metric measurements, along with guidelines on when to use which system.
Comparison of Conveyor Belt Pulley Sizes
Conveyor belt pulleys come in a range of sizes, and the choice between metric and imperial measurements often depends on regional preferences and industry standards. Here is a detailed comparison of common conveyor belt pulley sizes in both measurement systems:
When to Use Metric Measurements
Metric measurements are commonly used in regions and industries that follow the International System of Units (SI). Here are some scenarios where metric measurements are preferred:
International Projects:
- When working on projects that involve international partners or are located in countries that predominantly use the metric system, using metric measurements ensures compatibility and simplifies communication.
Standardization:
- Many industries, such as automotive, aerospace, and manufacturing, have standardized on metric units for consistency and precision. Using metric measurements in these sectors helps maintain uniformity and reduces errors.
Precision Engineering:
- Metric units are often preferred in precision engineering and scientific applications due to their ease of use in calculations and conversions. The metric system’s base-10 structure makes it simpler to handle detailed engineering tasks.
When to Use Imperial Measurements
Imperial measurements are still widely used in certain regions and industries, particularly in the United States. Here are some scenarios where imperial measurements are preferred:
Regional Standards:
- In regions like the United States, where the imperial system is the standard, using imperial measurements ensures compliance with local regulations and industry practices.
Existing Infrastructure:
- In industries with existing infrastructure and equipment designed around imperial measurements, it is practical to continue using this system to avoid compatibility issues and the need for extensive retooling.
Industry Tradition:
- Some industries, such as construction and mining, have long-standing traditions of using imperial measurements. Adhering to these traditions can facilitate communication and coordination within the industry.
Practical Implications of Measurement Systems
The choice between metric and imperial measurements can have several practical implications on the design, installation, and maintenance of conveyor systems. Here are some key considerations:
Compatibility:
- Ensuring that all components, including conveyor belt pulley sizes, are measured using the same system is crucial for compatibility. Mixing metric and imperial units can lead to misalignment and operational inefficiencies.
Precision:
- Metric units often provide more precise measurements due to their smaller incremental values. This precision can be beneficial in applications requiring high accuracy.
Ease of Conversion:
- While conversion between metric and imperial units is possible, it can introduce errors and complicate the design process. Sticking to a single measurement system simplifies calculations and reduces the risk of mistakes.
Supply Chain Considerations:
- The availability of parts and components in the chosen measurement system can affect lead times and costs. Ensuring that suppliers provide components in the preferred measurement system can streamline procurement and reduce delays.
Understanding the differences between metric and imperial measurements of conveyor belt pulley sizes is essential for making informed decisions in various industrial applications. By considering factors such as regional standards, industry practices, and practical implications, you can select the appropriate measurement system to enhance the efficiency and compatibility of your conveyor system. Whether you opt for metric or imperial measurements, consistency and precision are key to achieving optimal performance and reliability in your material handling operations.
Contact GRAM Conveyor for expert belt recommendations.
Conveyor Pulley Catalogue About Conveyor Belt Pulley Sizes
When selecting conveyor pulleys for your industrial applications, having access to a comprehensive conveyor pulley catalogue is invaluable. Such a catalogue lists various types of pulleys, including their dimensions, materials, and specifications, enabling you to make informed decisions based on your specific requirements. Understanding how to effectively use this catalogue ensures that you choose the correct pulley sizes to optimize your conveyor system’s performance.
Reference to a Comprehensive Catalogue
A comprehensive conveyor pulley catalogue typically includes detailed information on different types of pulleys. This information helps you select the right pulley based on your conveyor system’s needs.
Drum Pulleys
- Dimensions: Diameter: 20 inches, Face Width: 36 inches, Shaft Diameter: 5 inches
- Material: Carbon steel
- Application: General-purpose applications, suitable for light to medium loads.
Wing Pulleys
- Dimensions: Diameter: 24 inches, Face Width: 42 inches, Shaft Diameter: 6 inches
- Material: Stainless steel
- Application: Environments where debris and buildup are a concern, as the wing design helps to shed material.
Tapered Bore Pulleys
- Dimensions: Diameter: 16 inches, Face Width: 30 inches, Shaft Diameter: 4 inches
- Material: Aluminum
- Application: Applications requiring easy installation and removal, often used in systems where pulleys are frequently replaced.
Magnetic Pulleys
- Dimensions: Diameter: 12 inches, Face Width: 24 inches, Shaft Diameter: 3 inches
- Material: Magnetic steel
- Application: Ideal for separating ferrous metals from non-metal materials on the conveyor belt.
Heavy-Duty Pulleys
- Dimensions: Diameter: 36 inches, Face Width: 60 inches, Shaft Diameter: 10 inches
- Material: High-strength alloy steel
- Application: Heavy industrial applications, such as mining and bulk material handling, requiring high load capacity and durability.
How to Use the Catalogue Effectively
Using the conveyor pulley catalogue effectively requires understanding your specific needs and matching them to the available pulley options. Here are five examples of how to use the catalogue to find the exact pulley size needed based on specific requirements:
Determine the Load Capacity:
- Requirement: High load capacity for a mining conveyor system.
- Catalogue Use: Look for heavy-duty pulleys with large diameters and robust materials, such as high-strength alloy steel, to handle the demanding conditions.
Consider Environmental Conditions:
- Requirement: Conveyor system in a corrosive environment.
- Catalogue Use: Search for pulleys made from corrosion-resistant materials like stainless steel or coated carbon steel, ensuring longevity and reliability in harsh conditions.
Identify the Belt Type:
- Requirement: System using a magnetic conveyor belt.
- Catalogue Use: Select magnetic pulleys designed to interact with magnetic belts, enhancing the separation of ferrous materials from the conveyed products.
Ease of Maintenance:
- Requirement: Frequent pulley changes due to varying conveyor belt setups.
- Catalogue Use: Choose tapered bore pulleys that allow for quick and easy installation and removal, reducing downtime and maintenance efforts.
Optimize for Debris Management:
- Requirement: System prone to material buildup.
- Catalogue Use: Opt for wing pulleys with a self-cleaning design, preventing debris accumulation and ensuring smooth operation.
Practical Tips for Using the Catalogue
Cross-Reference Specifications:
- Always cross-reference the specifications listed in the catalogue with your conveyor system’s requirements. Ensure that the diameter, face width, and shaft diameter are compatible with your existing setup.
Consult Manufacturer Guidelines:
- Follow the manufacturer’s recommendations for pulley types and sizes. Manufacturers often provide valuable insights and guidelines based on their expertise and knowledge of best practices.
Consider Future Needs:
- Think about future scalability and potential changes to your conveyor system. Selecting pulleys that can accommodate increased loads or different belt types can save time and costs in the long run.
Request Samples or Demonstrations:
- If possible, request samples or demonstrations of the pulleys you are considering. This hands-on approach can help you better understand the product’s quality and suitability for your application.
Seek Expert Advice:
- Don’t hesitate to seek advice from industry experts or the catalogue provider. They can offer recommendations based on your specific needs and help you navigate the catalogue more effectively.
A comprehensive conveyor pulley catalogue is an essential tool for selecting the right pulley sizes for your conveyor system. By understanding how to use the catalogue effectively and considering factors such as load capacity, environmental conditions, belt type, maintenance requirements, and debris management, you can ensure optimal performance and reliability of your material handling operations.
Design and Customization of Conveyor Belt Pulley Sizes
In many industrial applications, standard conveyor belt pulley sizes may not always meet the unique requirements of specific operations. This is where custom pulley designs come into play. Customizing pulleys involves tailoring the size, shape, material, and other specifications to match the specific demands of the application. This section discusses the importance of custom pulley designs, the role of CAD drawings in the customization process, and provides examples of customized fabrication.
Custom Pulley Designs for Specific Applications
Custom pulley designs are essential for industrial applications that have unique requirements not addressed by standard sizes. These customizations can optimize the performance and efficiency of conveyor systems, ensuring they operate smoothly under specific conditions. Custom designs can include modifications to the diameter, face width, shaft diameter, and material composition of the pulleys.
Food Processing Industry:
- Custom Requirement: Non-corrosive and easy-to-clean pulleys.
- Customization: Use of stainless steel or food-grade plastic materials to ensure hygiene and corrosion resistance.
Mining Industry:
- Custom Requirement: Heavy-duty pulleys capable of handling high loads and abrasive materials.
- Customization: Incorporating hardened steel and larger diameters to withstand extreme conditions and high wear.
Textile Industry:
- Custom Requirement: Lightweight pulleys to reduce energy consumption and prevent fabric damage.
- Customization: Utilization of aluminum or composite materials for reduced weight and smooth operation.
Automotive Industry:
- Custom Requirement: Precision in size and alignment to ensure seamless integration with automated assembly lines.
- Customization: High precision machining and balancing to ensure exact dimensions and minimal vibration.
Pharmaceutical Industry:
- Custom Requirement: Pulleys that can operate in sterile environments without contaminating products.
- Customization: Use of non-toxic, sterilizable materials like high-grade plastics and stainless steel.
Importance of CAD Drawings and Customized Fabrication
CAD (Computer-Aided Design) drawings are instrumental in the design and customization of conveyor belt pulley sizes. They provide a detailed and precise blueprint that guides the manufacturing process, ensuring that the final product meets the exact specifications required by the application.
How CAD Drawings Help in Customizing Conveyor Pulleys
Conveyor belt CAD drawings play a crucial role in the customization of conveyor pulleys by providing a comprehensive visual and technical guide. Here’s how they contribute to the customization process:
Detailed Visualization:
- CAD drawings allow engineers to visualize the pulley design in 3D, providing a clear understanding of how it will look and function in the real world. This visualization helps in identifying and rectifying potential design flaws early in the process.
Precision Engineering:
- The high level of precision offered by CAD drawings ensures that every aspect of the pulley design, from dimensions to material specifications, is accurately represented. This precision is critical for custom applications where exact measurements are necessary.
Efficient Prototyping:
- CAD software can be used to create prototypes quickly and efficiently. Engineers can make modifications and test different designs virtually, saving time and resources before moving on to the actual manufacturing.
Stress and Performance Analysis:
- CAD tools often include features for conducting stress and performance analyses. Engineers can simulate various operating conditions to ensure that the custom pulleys will perform reliably under expected loads and stresses.
Manufacturing Integration:
- CAD drawings can be directly integrated with manufacturing technologies such as CNC machining and 3D printing. This integration ensures that the pulleys are produced exactly as designed, with minimal deviation from the specified dimensions and properties.
The design and customization of conveyor belt pulley sizes are critical for meeting the specific needs of various industrial applications. By utilizing CAD drawings, engineers can achieve precise, efficient, and reliable customization, ensuring that the pulleys enhance the overall performance and efficiency of the conveyor system. Whether dealing with unique environmental conditions, specific load requirements, or industry-specific regulations, custom pulley designs play an essential role in optimizing material handling operations.
FAQs About Conveyor Belt Pulley Sizes
Selecting a pulley for a belt conveyor involves considering several factors to ensure optimal performance and longevity. First, determine the type of conveyor system and the specific application requirements, such as the load capacity, belt speed, and environmental conditions. Next, consider the pulley diameter, face width, and shaft diameter, ensuring they are compatible with the belt and the system’s operational needs. Material selection is also crucial; choose materials that offer durability and resistance to wear, corrosion, and other environmental factors. Additionally, assess the type of pulley required, such as drum pulleys for general applications, wing pulleys for environments prone to debris buildup, or magnetic pulleys for separating ferrous materials. Consulting a comprehensive conveyor pulley catalogue and using CAD drawings can aid in making precise and informed decisions. Finally, always adhere to manufacturer guidelines and industry standards to ensure compatibility and safety.
Conveyor belts come in various standard sizes to accommodate different industrial applications. The width of standard conveyor belts typically ranges from 18 inches to 72 inches, with some specialized belts available in narrower or wider dimensions. The length of the conveyor belt can vary significantly based on the specific application, from a few feet to several hundred feet. The thickness of the belts also varies, generally falling between 0.1 inches and 1 inch, depending on the material and application requirements. Standard sizes ensure compatibility with commonly used conveyor components and simplify maintenance and replacement. These belts are usually available in both metric and imperial units, allowing for flexibility in international and regional applications. For specific requirements, custom-sized belts can be fabricated to meet unique operational needs, ensuring optimal performance and efficiency.
Determining the correct size pulley for your conveyor system involves several key steps. First, calculate the required belt speed and the rotational speed of the pulley (RPM). Using the formula 𝐷=𝑉/𝜋×𝑁 where 𝐷 is the pulley diameter, 𝑉is the belt speed, and 𝑁 is the RPM, you can find the necessary diameter. Next, consider the load capacity of the system; ensure the pulley size can handle the operational load without excessive stress or wear. Assess the belt characteristics, including thickness and flexibility, as these will influence the required pulley diameter. Additionally, review standard sizes available in a comprehensive conveyor pulley catalogue and match them with your calculated requirements. Consulting with manufacturers and using CAD drawings can provide further precision and customization, ensuring the selected pulley size meets all specific needs and industry standards.
Standard pulley sizes are designed to fit common industrial applications and are typically listed in both metric and imperial units. Standard diameters for conveyor pulleys often include 12 inches (305 mm), 16 inches (406 mm), 20 inches (508 mm), 24 inches (610 mm), and 30 inches (762 mm). Face widths also vary, with common sizes being 24 inches (610 mm), 30 inches (762 mm), 36 inches (914 mm), 42 inches (1067 mm), and 48 inches (1219 mm). Shaft diameters are usually 3 inches (76 mm), 4 inches (102 mm), 5 inches (127 mm), 6 inches (152 mm), and 8 inches (203 mm). These standard sizes ensure compatibility with a wide range of conveyor belts and systems, simplifying the selection and replacement process. Standard sizes are widely available and supported by various manufacturers, ensuring easy access to replacements and minimizing downtime in industrial operations. Custom sizes can also be fabricated for specific applications, but starting with standard sizes is often the most efficient and cost-effective approach.
Last Updated on July 19, 2024 by Jordan Smith
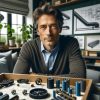
Jordan Smith, a seasoned professional with over 20 years of experience in the conveyor system industry. Jordan’s expertise lies in providing comprehensive solutions for conveyor rollers, belts, and accessories, catering to a wide range of industrial needs. From initial design and configuration to installation and meticulous troubleshooting, Jordan is adept at handling all aspects of conveyor system management. Whether you’re looking to upgrade your production line with efficient conveyor belts, require custom conveyor rollers for specific operations, or need expert advice on selecting the right conveyor accessories for your facility, Jordan is your reliable consultant. For any inquiries or assistance with conveyor system optimization, Jordan is available to share his wealth of knowledge and experience. Feel free to reach out at any time for professional guidance on all matters related to conveyor rollers, belts, and accessories.