Conveyor Belt Reel Dimensions Industrial Manufacturers
A conveyor belt reel is a fundamental component in the material handling industry, playing a crucial role in the efficient movement and management of conveyor belts. These reels are designed to store, deploy, and manage conveyor belts effectively, ensuring smooth operations in various industrial settings. The importance of conveyor belt reels cannot be overstated, as they are essential in industries ranging from mining and agriculture to manufacturing and logistics. Their ability to handle heavy-duty tasks while maintaining the integrity of the conveyor belts is vital for the productivity and safety of these operations.
Overview of the Conveyor Belt Reel
Defining Conveyor Belt Reels
Conveyor belt reels are essential tools in the material handling industry, designed to store, transport, and facilitate the deployment of conveyor belts. These reels come in various sizes and are constructed from materials like steel or heavy-duty plastic, depending on the application and environment. The primary purpose of a conveyor belt reel is to maintain the belt in optimal condition, preventing damage and ensuring longevity. This is achieved by providing a structured and secure way to wind and unwind the belt, thereby avoiding twists, kinks, and undue stress.
Historical Development
The development of conveyor belt reels can be traced back to the early days of conveyor belt usage. Initially, these reels were rudimentary, often made from wood and manually operated. However, as conveyor belts became more integral to industrial processes and their sizes increased, the need for more robust and efficient reel systems became evident. This led to the development of motorized reels, capable of handling longer and heavier belts, and the introduction of advanced materials for durability and strength.
Conveyor Belt Reels Primary Purpose
Conveyor belt reels are used across a wide range of industries, including mining, manufacturing, logistics, agriculture, and more. Their ability to handle different types of conveyor belts makes them indispensable in these sectors. The design of conveyor belt reels allows them to be used in various environments, from harsh outdoor conditions to controlled indoor settings. This adaptability ensures that they meet the specific needs of each industry.

The Role in Material Handling
In the context of material handling, conveyor belt reels serve several critical functions. They facilitate the easy and safe transport of conveyor belts to various locations, a task that would be challenging given the size and weight of these belts. In industries like mining, where conveyor belts can be several kilometers long, reels ensure that these belts are transported efficiently and without damage. Additionally, reels play a crucial role in the installation process of conveyor belts. They allow for the smooth unrolling of the belt onto the conveyor system, ensuring proper alignment and tension.
The Role in the Mining Industry
In mining, they facilitate the handling of heavy-duty belts required for transporting ore and other materials. Conveyor belt reels are crucial for handling the heavy-duty belts used in transporting raw materials from mining sites to processing facilities.
The Role in Manufacturing
In manufacturing and logistics, they support the efficient movement of goods along production lines and through distribution centers. In automotive manufacturing, conveyor belt reels help in managing the belts that move parts along the assembly line, ensuring smooth and efficient production processes.
The Role in Agriculture
In agriculture, they aid in the seamless operation of conveyor systems used for harvesting and processing crops. Conveyor belt reels are used in the harvesting and processing of crops, where they handle the belts that transport produce from the field to storage or processing areas.
Conveyor belt reels come in different types, each designed for specific applications and belt types. The most common types include:
- Stationary Reels: These are fixed in one location and are used for storing spare belts or belts that are infrequently used.
- Mobile Reels: Designed for easy movement, these reels are used in applications where belts need to be transported to different locations within a facility.
- Motorized Reels: Equipped with a motor, these reels are used for heavy-duty applications where manual winding and unwinding of the belt are impractical.
Technological Innovations
Technological advancements have significantly impacted the design and functionality of conveyor belt reels. Modern reels are equipped with features like automatic tension control, speed regulation, and remote operation capabilities. These features not only make the reels more efficient but also enhance safety by reducing the need for manual intervention.
Importance in Conveyor Belt Lifecycle
The lifecycle of a conveyor belt is greatly influenced by how it is stored and handled. Conveyor belt reels play a vital role in this aspect by providing a means to store belts in a way that minimizes damage and wear. Properly stored belts on reels are less likely to develop weak spots, deformations, or other issues that could lead to premature failure. This not only extends the life of the belt but also ensures consistent performance and reduces the likelihood of unexpected downtime.
Conveyor Belt Reel Price Factors
Pricing Dynamics
The pricing of conveyor belt reels is influenced by a myriad of factors, making it a complex aspect to navigate for buyers. Understanding these factors is crucial in making informed purchasing decisions, ensuring that the chosen reel offers the best value for its cost. The price of a conveyor belt reel is not just a reflection of its material cost but also encompasses design sophistication, durability, size, and additional features.
Material and Construction
One of the primary factors affecting the price of conveyor belt reels is the material and construction quality. Reels made from high-grade steel or specialized alloys tend to be more expensive due to their durability and strength. These materials are essential for reels that will be used in harsh environments or for heavy-duty belts. On the other hand, reels made from lighter materials like aluminum or composites may be less expensive but are suitable for less demanding applications.
Size and Capacity
The size and capacity of the reel significantly impact its price. Larger reels designed to accommodate longer and wider belts are typically more expensive due to the increased material usage and the need for a more robust structure. The capacity of the reel not only refers to its physical dimensions but also to its load-bearing capability, which is a critical factor in its design and, consequently, its cost.
Technological Features
Modern conveyor belt reels come equipped with various technological features that can influence their price. Features like automated tension control, speed regulation, and remote operation add to the cost but provide significant operational advantages. These features enhance the efficiency and safety of the reel, making them a worthwhile investment for certain applications.
Brand and Manufacturer
The brand and manufacturer of the conveyor belt reel also play a role in its pricing. Reputable brands that are known for quality and reliability often price their products higher. This premium is attributed to the brand’s reputation, the quality of customer service, and the assurance of durability and performance. However, it’s important for buyers to balance brand reputation with actual product needs and budget constraints.
Customization and Additional Services
Customization options can also affect the price of conveyor belt reels. Some manufacturers offer custom-built reels to meet specific operational requirements, which can increase the cost. Additionally, services like installation support, extended warranties, and maintenance packages, while adding to the upfront cost, can provide long-term value and reliability.
Market Trends and Economic Factors
External factors such as market trends, raw material costs, and economic conditions can influence the price of conveyor belt reels. Fluctuations in steel prices, for instance, directly impact the cost of manufacturing reels. Economic factors like exchange rates and transportation costs also play a role, especially for reels that are imported or require specialized shipping.
Conveyor Belt Reel Sizes
The Significance of Size in Conveyor Belt Reels
The size of a conveyor belt reel is a critical factor that directly impacts its functionality and suitability for specific applications. Understanding the various sizes available and their corresponding uses is essential for selecting the right reel. The size of a conveyor belt reel determines not only the length and width of the belt it can accommodate but also its handling and storage requirements.

Standard Sizes and Custom Options
Conveyor belt reels come in a range of standard sizes, designed to meet the most common requirements in the industry. These standard sizes are based on the width and length of the conveyor belts they are intended to hold. For instance, smaller reels might be used for belts in light-duty applications, such as packaging or small-scale manufacturing, while larger reels are necessary for heavy-duty applications like mining or large-scale material handling.
In addition to standard sizes, many manufacturers offer custom-sized reels. These are tailored to specific belt sizes or operational needs and are particularly useful for non-standard belt lengths or when space constraints require a bespoke solution. Custom reels can be designed to accommodate extra-long or wide belts, providing a solution for industries with unique requirements.
Determining the Right Size
Selecting the right size for a conveyor belt reel involves considering several factors:
- Belt Length and Width: The most critical factor is the size of the conveyor belt. The reel must be able to accommodate the full length and width of the belt without causing stress or damage.
- Operational Space: The available space for storing and operating the reel is also important. Larger reels require more space for storage and maneuvering.
- Handling and Transportation: The size of the reel affects how it will be handled and transported. Larger reels might require specialized equipment for loading and unloading.
Size and Its Impact on Performance
The size of the conveyor belt reel has a direct impact on its performance and the overall efficiency of the conveyor system. A reel that is too small for the belt can cause kinks or twists, leading to premature wear or damage. Conversely, a reel that is unnecessarily large can be cumbersome to handle and may take up excessive storage space. Therefore, finding the right balance is key to ensuring optimal performance and longevity of the conveyor belt.
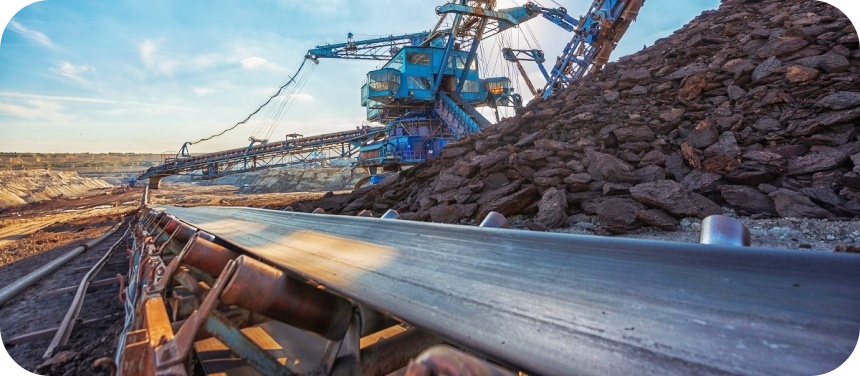
Industry-Specific Size Requirements
Different industries have varying requirements when it comes to the size of conveyor belt reels. For example:
- Mining and Quarrying: These industries often require large and robust reels for their heavy-duty and long conveyor belts.
- Food Processing and Packaging: In these sectors, smaller, more compact reels are often sufficient, catering to lighter belts used in these applications.
- Logistics and Warehousing: Reels in these industries might need to be a balance of size and maneuverability, accommodating medium-sized belts while being easy to handle.
Types of Conveyor Belt Reels
Conveyor belt reels are essential tools for managing conveyor belts in various industrial applications. They come in different types, each designed to serve specific purposes. This section details the types of conveyor belt reels, highlighting their unique features and applications.

Stationary Reels
These reels are fixed in one location and are primarily used for the storage of spare or infrequently used conveyor belts. They provide a secure and organized way to keep belts ready for future use without occupying valuable floor space.
Key Features:
- Fixed Position: Stationary reels are installed in a designated spot within a facility, ensuring that stored belts remain in a known location for easy access when needed.
- Robust Construction: Built to withstand the weight and length of conveyor belts, stationary reels are made from durable materials like steel or heavy-duty plastic to ensure longevity.
- Protective Storage: By winding belts onto stationary reels, the belts are protected from environmental factors such as dust, moisture, and physical damage, preserving their condition until needed.
Advantages:
- Space Efficiency: Stationary reels help maximize storage space by keeping belts neatly wound and off the floor.
- Organization: They provide an organized storage solution, making it easy to inventory and retrieve belts when required.
- Damage Prevention: Proper storage on reels prevents belts from becoming kinked, twisted, or otherwise damaged, which can occur with improper storage methods.
Use Case Example:
- Warehouse Storage: In warehouses, stationary reels are used to store spare conveyor belts, ensuring that replacements are readily available for maintenance or emergency repairs without taking up excessive space.
Mobile Reels
These reels are equipped with wheels or casters, allowing them to be easily moved around within a facility. They are designed for applications where conveyor belts need to be transported from one location to another within the same site.
Key Features:
- Portability: Mobile reels are designed for ease of movement, featuring wheels or casters that allow operators to transport belts to different areas within a facility.
- Adjustable Height: Many mobile reels come with adjustable height features to accommodate belts of various lengths and sizes, ensuring versatility in use.
- Locking Mechanism: To ensure stability during storage and unwinding, mobile reels are often equipped with locking mechanisms to prevent accidental movement.
Advantages:
- Flexibility: Mobile reels provide the flexibility to move belts to different parts of a facility as needed, supporting efficient operations.
- Ease of Use: They simplify the process of transporting heavy and bulky belts, reducing the physical strain on workers and improving safety.
- Versatility: Mobile reels can be used in various environments within a facility, from production lines to maintenance areas.
Use Case Example:
- Manufacturing Plants: In manufacturing plants, mobile reels are used to transport conveyor belts from storage areas to production lines, enabling quick and efficient belt replacements and installations.
Motorized Reels
These reels are integrated with motors and advanced control systems, designed for heavy-duty applications where automatic control and handling of conveyor belts are required. They are capable of winding and unwinding belts with minimal manual intervention.
Key Features:
- Motorized Operation: Equipped with powerful motors, these reels can automatically wind and unwind conveyor belts, making them suitable for handling heavy or long belts with ease.
- Automatic Control: Advanced control systems allow for precise operation, including speed regulation, tension control, and remote operation capabilities.
- Heavy-Duty Construction: Built to handle the demands of industrial environments, motorized reels are constructed with robust materials to support large and heavy conveyor belts.
Advantages:
- Efficiency: Motorized operation reduces the time and effort required to handle conveyor belts, enhancing operational efficiency.
- Safety: Automation minimizes the need for manual handling, reducing the risk of injuries associated with lifting and moving heavy belts.
- Precision: Advanced control features allow for precise management of belt tension and alignment during deployment and storage, ensuring optimal performance and longevity.
Use Case Example:
- Mining Operations: In mining operations, motorized reels are used to handle the heavy-duty conveyor belts required for transporting raw materials. The automated features allow for quick and efficient deployment and retrieval of belts, essential for maintaining continuous perations in demanding environments.
Conveyor belt reels come in various types, each designed to meet specific needs within industrial applications. Stationary reels provide efficient storage solutions, mobile reels offer flexibility and ease of transportation, and motorized reels deliver automation and precision for heavy-duty applications. Understanding the unique features and advantages of each type helps businesses choose the right reel for their operational requirements, ensuring efficient and safe handling of conveyor belts.
Conveyor Belt Reel for Sale
Navigating the Market for Conveyor Belt Reels
When it comes to purchasing conveyor belt reels, understanding the market landscape is crucial. The market offers a wide range of options, from brand-new, state-of-the-art reels to more economical used options. Knowing where to look and what to consider can significantly streamline the purchasing process.
Sources for Conveyor Belt Reels
There are several avenues through which conveyor belt reels can be purchased:
- Manufacturers and Distributors: Many companies specialize in the production and sale of conveyor belt reels. Purchasing directly from manufacturers or their authorized distributors often ensures access to the latest models and technologies, along with manufacturer warranties and support.
- Industrial Supply Stores: These stores typically stock a range of conveyor belt reels, catering to various industrial needs. They offer the advantage of being able to physically inspect the reels before purchase.
- Online Marketplaces: E-commerce platforms and specialized industrial equipment websites are increasingly popular for purchasing conveyor equipment. They offer a wide selection and the convenience of online shopping and delivery.
- Used Equipment Dealers: For those looking for more budget-friendly options, dealers in used industrial equipment can be a valuable resource. They often have a range of conveyor belt reels that have been refurbished or are in good working condition.

Considerations for Purchasing
When purchasing a conveyor belt reel, several factors should be considered to ensure that the chosen reel meets the specific needs of the operation:
- Compatibility with Conveyor Belt: The reel must be compatible with the dimensions and type of conveyor belt being used.
- Quality and Durability: The construction quality and materials used in the reel determine its durability and longevity.
- Features and Technology: Consider the technological features offered by the reel, such as automated winding mechanisms or tension control systems.
- Warranty and Support: Look for reels that come with a warranty and good customer support from the manufacturer or supplier.
- Budget Constraints: Balance the need for quality and features with the available budget. Sometimes, a used reel in good condition can be a cost-effective alternative.
New vs. Used Options
Deciding between a new or used conveyor belt reel depends on several factors:
- Budget: New reels are typically more expensive but come with the latest features and full manufacturer warranties. Used reels are more budget-friendly but may have limited warranties and less advanced features.
- Urgency and Availability: New reels may have lead times for manufacturing and delivery, while used reels are often available for immediate purchase.
- Operational Requirements: For operations that require specific features or have heavy-duty requirements, investing in a new reel might be more prudent.
Conveyor Belt Reel Storage Solutions
The Importance of Proper Storage
Proper storage of conveyor belts is crucial for maintaining their integrity, performance, and longevity. A conveyor belt reel plays a central role in this storage process, providing a systematic and safe method for handling and preserving conveyor belts when they are not in use.
Conveyor Belt Storage Racks
In addition to reels, conveyor belt storage racks are an essential component of a comprehensive storage solution. These racks are designed to keep conveyor belts in optimal condition, minimizing the risk of damage due to improper handling or environmental factors. Moreover, integrating a heavy duty reliable conveyor belt tracker into these storage solutions ensures that the belts are not only stored properly but also monitored for any potential issues, enhancing the overall efficiency and longevity of the conveyor system.
- Design and Features: Conveyor belt storage racks are typically made from robust materials like steel and are designed to accommodate various reel sizes. They often feature adjustable components to cater to different reel diameters and widths.
- Benefits: The primary benefit of using these racks is the organized and accessible storage of conveyor belts. They prevent the belts from being stored on the ground, where they could be damaged or become a safety hazard. Additionally, these racks can be designed to facilitate easy loading and unloading of the reels, further enhancing operational efficiency.

Factors to Consider in Storage Solutions
When implementing storage solutions for conveyor belt reels, several factors need to be considered:
- Space Availability: The available space in the facility will dictate the size and number of storage racks that can be installed.
- Accessibility: Storage solutions should be designed for easy access to the reels, allowing for quick and efficient deployment of the conveyor belts when needed.
- Environmental Protection: In some cases, additional protection from environmental factors like moisture, dust, or chemicals may be necessary, depending on the storage location and belt material.
- Safety and Compliance: Storage solutions should comply with safety standards and regulations, ensuring that they do not pose a hazard to workers or interfere with normal operations.
Customized Storage Solutions
For facilities with unique requirements or space constraints, customized storage solutions can be developed. These might include:
- Mobile Storage Racks: Designed for easy movement within the facility, allowing for flexible storage options.
- Vertical Storage Systems: Utilizing vertical space for storage, ideal for facilities with limited floor space.
- Integrated Handling Systems: Combining storage racks with integrated handling systems like cranes or forklift attachments for easy movement of heavy reels.
Maintenance of Storage Equipment
Regular maintenance of storage racks and reels is essential to ensure their longevity and functionality. This includes routine inspections for any signs of wear or damage, lubrication of moving parts, and ensuring that the storage system remains clean and free from obstructions.
Importance in Storing, Transporting, and Deploying Conveyor Belts Efficiently
- Efficiency in Storage: Properly storing conveyor belts on reels ensures they remain in optimal condition and are protected from environmental damage such as moisture, dust, and physical wear.
- Organization: Reels provide a neat and organized way to store belts, making inventory management easier and more efficient.
- Safety and Convenience: Using reels to transport conveyor belts minimizes the risk of damage during transit and makes it easier to move belts over long distances.
- Logistics: Conveyor belt reels facilitate the logistics of moving belts from manufacturing facilities to their point of use, whether that’s a factory, a mining site, or an agricultural field.
- Speed and Efficiency: Reels allow for quick and controlled deployment of conveyor belts, reducing the time and effort required to install new belts or replace existing ones.
- Precision: The use of reels ensures that belts are deployed smoothly and accurately, which is crucial for maintaining the alignment and functionality of conveyor systems.
- Time Savings: Efficient storage, transportation, and deployment of conveyor belts save valuable time, reducing downtime and increasing productivity.
- Cost Efficiency: Proper handling of conveyor belts through the use of reels extends their lifespan, reducing the frequency of replacements and the associated costs.
- Improved Safety: By minimizing the physical effort required to handle conveyor belts and reducing the risk of damage, reels contribute to a safer working environment.
Use Case Examples:
- Manufacturing Facilities: Conveyor belt reels streamline the process of installing and replacing belts on production lines, ensuring minimal disruption to operations.
- Construction Sites: Reels make it easier to transport and deploy conveyor belts in construction projects, where efficient material handling is critical to project timelines.
Conveyor belt reels are versatile tools that play a critical role in various industries. They ensure the efficient storage, transportation, and deployment of conveyor belts, contributing to operational efficiency, cost savings, and improved safety. Understanding their functionality and benefits helps businesses optimize their material handling processes and maintain high productivity levels.
Shore Hardness of Conveyor Belt Reel
Shore hardness is a critical property of conveyor belt reels that influences their performance, durability, and suitability for specific applications. This section provides an in-depth look at Shore hardness, explaining its significance and how it is used to select the appropriate conveyor belt for various industrial needs.
Definition and Significance of Shore Hardness in Conveyor Belt Reels
Shore hardness is a measure of the resistance of a material to indentation, expressed in Shore units. It is determined using a durometer, which measures the depth of an indentation in the material created by a given force. The scale ranges from 0 to 100, with higher numbers indicating harder materials.
Shore hardness provides valuable insight into the material properties of conveyor belts, such as elasticity, flexibility, and wear resistance. It helps determine how well a belt can withstand various stresses and strains during operation.
Different applications require conveyor belts with specific hardness levels. For example, belts used in heavy-duty applications may need higher Shore hardness to resist abrasion and impact, while belts in light-duty applications may benefit from lower Shore hardness for better flexibility.
The Shore hardness of a conveyor belt affects its performance and longevity. Properly matching the hardness to the application ensures that the belt performs optimally and has a longer service life, reducing maintenance costs and downtime.
How to Use the Hardness Chart to Select the Right Belt for Specific Applications
Determine the specific requirements of the application, including the type of materials being transported, the operating environment, and the stresses the belt will endure. Use the hardness chart to match these requirements with the appropriate Shore hardness category. Consider factors such as flexibility, durability, and resistance to abrasion and impact. For complex applications, consulting with industrial conveyor belt manufacturers or experts can provide additional insights and recommendations based on industry experience.
Advantages:
Selecting the right hardness ensures that the conveyor belt performs optimally under the given conditions, enhancing efficiency and productivity.
- Extended Lifespan: Proper hardness selection reduces wear and tear, extending the lifespan of the belt and lowering replacement and maintenance costs.
- Improved Safety: Using the appropriate belt hardness can also improve safety by ensuring the belt can handle the loads and conditions without failure.
Use Case Example:
- Mining Industry: In mining operations, belts with high Shore hardness (70-100 Shore A) are chosen for their ability to withstand the abrasive nature of ore and rock, providing durability and reducing the frequency of belt replacements.
Understanding Shore hardness and using a conveyor belt hardness chart is essential for selecting the right conveyor belt for specific applications. By matching the hardness to the operational requirements, businesses can ensure optimal performance, durability, and safety of their conveyor systems. This approach not only enhances productivity but also contributes to cost savings through reduced maintenance and extended belt life.
Get in touch for durable and reliable conveyor belts.
Conveyor Belt Reel Standards
Conveyor belt reel standards are crucial for ensuring the quality, safety, and performance of conveyor belts used in various industries. Adhering to these standards helps manufacturers produce reliable products and ensures that users benefit from durable and safe conveyor belt systems. This section provides a detailed explanation of the relevant ISO standards and the testing methods used to evaluate conveyor belts.
Conveyor Belt ISO Standard
ISO Standards: The International Organization for Standardization (ISO) develops and publishes international standards to ensure products and services are safe, reliable, and of good quality. For conveyor belts, ISO standards provide guidelines and requirements for design, manufacture, and performance.
Relevant ISO Standards:
- ISO 14890: This standard specifies the physical and mechanical properties of conveyor belts, including tensile strength, elongation, and adhesion.
- ISO 340: Focuses on the flame-retardant properties of conveyor belts, ensuring they meet safety requirements for fire resistance.
- ISO 284: Addresses the electrical conductivity of conveyor belts, essential for preventing static buildup and ensuring safety in explosive environments.
- ISO 15236: Pertains to steel cord conveyor belts, detailing requirements for their construction, performance, and testing.
Importance of Compliance with International Standards for Quality and Safety:
Quality Assurance:
- Consistent Quality: Compliance with ISO standards ensures that conveyor belts are manufactured to consistent quality levels, reducing the risk of defects and failures.
- Customer Confidence: Meeting international standards boosts customer confidence in the product’s reliability and performance.
Safety:
- Fire Resistance: Adhering to ISO 340 ensures that conveyor belts used in hazardous environments are flame-retardant, protecting personnel and equipment from fire risks.
- Electrical Conductivity: Compliance with ISO 284 prevents static electricity buildup, reducing the risk of explosions in industries like mining and grain handling.
Global Trade:
- Market Access: ISO certification facilitates international trade by meeting globally recognized standards, making it easier for manufacturers to enter new markets.
- Regulatory Compliance: ISO standards often align with national regulations, ensuring that products meet the legal requirements in various regions.
Use Case Example:
- Mining Industry: Conveyor belts used in mining must comply with ISO 14890 and ISO 284 to ensure they can withstand the demanding conditions and minimize safety risks associated with static electricity and fire.
Conveyor Belt Reel Testing
Tensile Strength Test:
Purpose: Measures the maximum force a conveyor belt can withstand before breaking, ensuring it can handle the loads expected in operation.
Method: A sample of the belt is stretched until it breaks, and the force applied is recorded.
Elongation Test:
- Purpose: Determines the extent to which a conveyor belt can stretch under a given load, providing insight into its flexibility and ability to absorb shock.
- Method: The belt is subjected to a tensile force, and the elongation is measured at specified intervals.
Adhesion Test:
- Purpose: Assesses the bond strength between the belt layers, ensuring they do not separate under stress.
- Method: Layers of the belt are peeled apart, and the force required is measured.
Abrasion Resistance Test:
- Purpose: Evaluates the belt’s ability to withstand wear and tear, crucial for applications involving abrasive materials.
- Method: The belt surface is subjected to a controlled abrasive action, and the wear is measured.
Flame Resistance Test:
- Purpose: Ensures the belt meets safety standards for flame retardancy, reducing fire risks in hazardous environments.
- Method: The belt is exposed to a flame, and its reaction is observed and measured.
Electrical Conductivity Test:
- Purpose: Ensures the belt can dissipate static electricity, preventing static buildup that could lead to explosions.
- Method: The electrical resistance of the belt is measured using specialized equipment.
Methods and Equipment Used for Testing Conveyor Belts:
- Tensile Testing Machines: Used for measuring tensile strength and elongation, these machines apply controlled force to the belt samples.
- Peel Testers: Designed to measure adhesion between belt layers by peeling them apart under controlled conditions.
- Abrasion Testers: Machines that simulate wear and tear by applying abrasive materials to the belt surface under controlled pressure and movement.
- Flame Test Chambers: Enclosed chambers where belts are exposed to flames to evaluate their fire resistance properties.
- Electrical Resistance Meters: Instruments used to measure the electrical conductivity of conveyor belts, ensuring they meet safety standards for static dissipation.
Importance of Testing:
- Quality Control: Regular testing ensures that conveyor belts meet specified standards and perform reliably in their intended applications.
- Safety Assurance: Testing verifies that belts can withstand the operational stresses and environmental conditions, reducing the risk of accidents and equipment failure.
- Performance Optimization: By identifying potential weaknesses through testing, manufacturers can improve the design and materials of conveyor belts, enhancing their performance and durability.
Compliance with ISO standards and thorough testing are essential for ensuring the quality, safety, and performance of conveyor belts. By adhering to these standards and conducting regular tests, manufacturers can produce reliable products that meet the needs of various industries, while users can trust that their conveyor systems will operate safely and efficiently.
Finding Conveyor Belt Reel Suppliers
The Quest for Reliable Suppliers
Locating dependable conveyor belt suppliers is a critical step in ensuring the smooth operation of material handling systems. The right supplier not only provides quality products but also offers valuable support and services. This section guides you through the process of finding and selecting the best conveyor belt suppliers.
Identifying Potential Suppliers
The first step in finding conveyor belt suppliers is to identify potential candidates. This can be done through:
- Industry Recommendations: Consulting with industry peers can provide insights into reputable suppliers.
- Trade Shows and Exhibitions: These events are great opportunities to meet suppliers and evaluate their products firsthand.
- Online Directories and Forums: Many online platforms list suppliers and provide reviews and ratings from other customers.
- Manufacturer Listings: Conveyor belt manufacturers often have a list of authorized distributors or suppliers.
Evaluating Suppliers
Once a list of potential suppliers is compiled, the next step is to evaluate them based on several criteria:
- Product Range: Ensure the supplier offers the conveyor belt reel and related products to suit different needs.
- Quality Assurance: Look for suppliers who provide quality guarantees or certifications for their products.
- Customer Service: Good customer service, including prompt responses and technical support, is crucial.
- Pricing and Terms: Compare pricing and terms of sale, including payment options, delivery charges, and return policies.
- Reputation and Experience: Consider the supplier’s reputation in the market and their experience in the industry.
Viacore Belting and Other Notable Suppliers
Viacore Belting is a notable name in the conveyor belt industry, known for its quality products and comprehensive range. Alongside Viacore, there are other reputable suppliers worth considering. Each of these suppliers may have unique strengths, such as specialized products, competitive pricing, or exceptional customer service.
Building Relationships with Suppliers
Developing a good relationship with your conveyor belt supplier can bring numerous benefits:
- Customized Solutions: A good supplier can work with you to provide customized solutions tailored to your specific needs.
- Technical Support and Advice: Suppliers often have in-depth knowledge of their products and can offer valuable advice and technical support.
- After-Sales Service: Reliable after-sales service, including maintenance and repair, is essential for the longevity of the products.
Online vs. Local Suppliers
Choosing between online and local suppliers depends on various factors:
- Convenience and Accessibility: Local suppliers offer the advantage of easy accessibility and personal interaction, while online suppliers provide convenience and a broader selection.
- Delivery Times and Costs: Consider the delivery times and shipping costs, which can vary significantly between online and local suppliers.
Conveyor Belt Reel Installation Companies
The Critical Role of Professional Installation
The installation of a conveyor belt reel is a complex and crucial process that directly impacts the efficiency and safety of the conveyor system. Professional conveyor belt installation companies play a vital role in ensuring that this process is carried out correctly, adhering to industry standards and safety regulations.
Selecting the Right Installation Company
Choosing the right conveyor belt installation company is as important as selecting the conveyor belt itself. Here are key factors to consider:
- Experience and Expertise: Look for companies with a proven track record and expertise in installing conveyor belts, particularly in your specific industry.
- Certifications and Standards: Ensure the company adheres to relevant industry standards and holds necessary certifications.
- Safety Record: A company’s safety record is a critical indicator of their commitment to safe and reliable installation practices.
- Customer Reviews and References: Seek feedback from other customers and ask for references to gauge the company’s reliability and quality of service.
Services Offered by Installation Companies
Conveyor belt installation companies typically offer a range of services, including:
- Initial Consultation and Planning: Assessing the site and planning the installation process to suit specific operational needs.
- Installation and Commissioning: The physical installation of the conveyor belt, followed by commissioning to ensure it operates correctly, is crucial for optimal performance. Understanding how to install conveyor belt systems properly can significantly impact their efficiency and longevity, minimizing downtime and maintenance needs.
- Training and Support: Providing training to the operational staff and offering ongoing support and troubleshooting.
- Maintenance Services: Some companies also offer regular maintenance services to ensure the conveyor system continues to operate efficiently.
The Installation Process
The installation process involves several key steps:
- Site Assessment: Evaluating the installation site to plan the layout and identify any potential challenges.
- Preparation and Delivery: Preparing the site and delivering the conveyor belt and other components.
- Installation: Installing the conveyor belt onto the system, which may involve splicing, tensioning, and alignment.
- Testing and Commissioning: Running tests to ensure the conveyor belt operates as intended and making any necessary adjustments.
Importance of Professional Installation
Professional installation is crucial for several reasons:
- Ensuring Operational Efficiency: Proper installation is key to the smooth and efficient operation of the conveyor system.
- Extending Belt Life: Correct installation reduces wear and tear, extending the life of the conveyor belt.
- Safety: Incorrect installation can pose significant safety risks. Professional installers ensure that the system is safe for operators.
Case Studies: Successful Implementations of the Conveyor Belt Reel
The Value of Real-World Examples
Case studies of successful implementations of conveyor belt reels provide invaluable insights into their practical applications and benefits. These real-world examples illustrate how different industries utilize conveyor belt reels to enhance efficiency, safety, and operational effectiveness.
Case Study 1: Mining Industry
- Background: A large mining company faced challenges with the transportation and installation of conveyor belts in their deep underground mines.
- Implementation: The company implemented heavy-duty motorized conveyor belt reels designed for high-capacity belts.
- Outcome: The reels facilitated easier transportation and installation of the belts, significantly reducing downtime and improving safety in the mines. The efficiency of belt deployment increased, leading to smoother operations and reduced labor costs.
Case Study 2: Agriculture Sector
- Background: An agricultural processing plant struggled with storing and managing multiple conveyor belts used for seasonal operations.
- Implementation: Custom-designed conveyor belt reels with a modular storage system were introduced.
- Outcome: The solution provided organized and accessible storage for the belts, protecting them from damage during off-seasons. The ease of deployment during peak seasons improved operational readiness and reduced setup times.
Case Study 3: Manufacturing Facility
- Background: A manufacturing facility required a streamlined process for replacing conveyor belts in their assembly lines without causing extensive downtime.
- Implementation: The facility adopted a system of pre-loaded conveyor belt reels, allowing for quick and efficient belt replacement.
- Outcome: The new system minimized production downtime during belt replacements. The facility also reported an increase in the lifespan of the belts due to better storage and handling.
Case Study 4: Logistics and Distribution
- Background: A logistics company needed a solution for managing conveyor belts in their expansive distribution centers.
- Implementation: They implemented a combination of stationary and mobile conveyor belt reeler for different areas of the center.
- Outcome: This approach provided flexibility and efficiency in managing conveyor belts, adapting to the dynamic needs of the logistics environment. The mobile reels were particularly beneficial in areas requiring frequent reconfiguration.
Lessons Learned
These case studies demonstrate several key lessons:
- Customization is Key: Tailoring the conveyor belt reel system to specific operational needs can significantly enhance efficiency.
- Investment in Quality Pays Off: Investing in high-quality reels leads to long-term savings through reduced maintenance and extended belt life.
- Safety and Efficiency Go Hand-in-Hand: Proper management of conveyor belts not only improves operational efficiency but also enhances workplace safety.
Reach out today for custom conveyor belt solutions.
FAQs about Conveyor Belt Reel
A conveyor belt system comprises several key components:
Belt: This is the continuous loop of material that transports items from one point to another.
Pulleys: These are the rollers over which the belt moves. There are typically two types: the drive pulley (which powers the belt) and the idler pulley (which supports the belt).
Motor: The power source that drives the conveyor belt, usually connected to the drive pulley.
Frame: The structure that supports the pulleys, motor, and the belt.
Rollers: Cylindrical components that support and guide the belt along its path.
Belt Cleaners: Devices used to remove material sticking to the belt.
Conveyor Skirting: Material used along the sides of the belt to keep materials on the belt and reduce spillage.
The conveyor belt mechanism is commonly referred to as a “conveyor system” or “belt conveyor system.” This system includes the belt itself, pulleys, rollers, a motor, and the supporting frame. The entire mechanism works together to move materials efficiently from one location to another.
A conveyor belt tracker is a device or system used to keep the conveyor belt aligned properly on its path. It prevents the belt from drifting or misaligning, which can cause operational issues or damage to the belt. Belt trackers adjust the belt’s position to ensure it runs straight and true, maintaining efficiency and prolonging the belt’s lifespan.
A belt conveyor roller is a cylindrical component that supports and guides the conveyor belt. Rollers are strategically placed along the conveyor frame and can vary in size, material, and design based on the application. They play a crucial role in ensuring smooth operation of the conveyor belt, reducing friction, and supporting the weight of the materials being transported.
The roller primarily used to track a conveyor belt is called a tracking roller or guide roller. These rollers are crucial for maintaining proper belt alignment and ensuring the conveyor belt runs smoothly along the correct path. Tracking rollers can be mounted on the top or bottom of the conveyor frame and are usually adjustable to allow precise alignment. They work by applying a slight pressure to the side of the belt, guiding it back to the center if it begins to drift off track. Properly adjusted tracking rollers prevent common issues such as belt misalignment, which can lead to wear and tear on the belt edges and the conveyor structure. Additionally, crowned rollers, which are rollers with a slightly tapered center, are often used to help keep the belt centered. The combination of tracking rollers and crowned rollers ensures that the conveyor belt remains in the correct position during operation, minimizing downtime and maintenance needs.
Keeping a conveyor belt on track involves several key steps and regular maintenance practices. Firstly, ensure that the conveyor frame is level and square. Misalignment of the frame can cause the belt to drift off track. Next, properly tension the belt; a belt that is too loose or too tight can lead to tracking issues. Adjust the tracking rollers or guide rollers to gently steer the belt back to the center if it starts to move off course. Regularly inspect and clean the conveyor components, as debris buildup can interfere with belt alignment. Additionally, make sure that all pulleys and rollers are properly aligned and in good condition. Worn or misaligned pulleys can cause the belt to drift. Another important aspect is to evenly distribute the load on the conveyor belt to avoid uneven tension and wear. Implementing these practices helps maintain proper belt tracking, ensuring efficient operation and extending the lifespan of the conveyor belt system.
Conveyor belts are connected using two primary methods: mechanical splicing and endless splicing. Mechanical splicing involves using metal fasteners to join the ends of the belt. This method is quick and relatively simple, requiring minimal equipment. It is suitable for belts that need frequent maintenance or replacement, as it allows for easy disassembly. Mechanical splices are commonly used in light to medium-duty applications.
Endless splicing, on the other hand, creates a continuous loop by bonding the belt ends together using heat or adhesives. This method provides a stronger and more seamless connection, reducing the risk of snagging and improving the belt’s overall performance. Endless splicing is preferred for high-speed or heavy-duty applications where a smooth surface is crucial for efficient operation. The splicing process involves cutting the belt ends to precise specifications, aligning them, and then using a press or vulcanizing tool to bond them together. Properly performed, endless splicing ensures a durable and reliable connection, enhancing the conveyor belt’s longevity and operational efficiency.
Conveyor belt wheels are commonly referred to as rollers or idler rollers. These components support the conveyor belt and facilitate its smooth movement along the conveyor frame. Rollers are available in various types, including carrying rollers, return rollers, and impact rollers, each serving a specific function within the conveyor system. Carrying rollers are positioned on the load-carrying side of the belt, supporting the weight of the materials being transported. Return rollers are installed on the underside of the belt to support the empty belt on its return journey. Impact rollers are used at loading points to absorb the impact of falling materials, protecting the belt from damage. These rollers are typically made from materials such as steel or high-density plastic and can feature sealed bearings to reduce maintenance needs and extend their operational life. By reducing friction and supporting the belt, rollers play a crucial role in maintaining the efficiency and reliability of conveyor belt systems.
Last Updated on June 21, 2024 by Jordan Smith
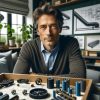
Jordan Smith, a seasoned professional with over 20 years of experience in the conveyor system industry. Jordan’s expertise lies in providing comprehensive solutions for conveyor rollers, belts, and accessories, catering to a wide range of industrial needs. From initial design and configuration to installation and meticulous troubleshooting, Jordan is adept at handling all aspects of conveyor system management. Whether you’re looking to upgrade your production line with efficient conveyor belts, require custom conveyor rollers for specific operations, or need expert advice on selecting the right conveyor accessories for your facility, Jordan is your reliable consultant. For any inquiries or assistance with conveyor system optimization, Jordan is available to share his wealth of knowledge and experience. Feel free to reach out at any time for professional guidance on all matters related to conveyor rollers, belts, and accessories.