Answers to Questions Conveyor Belt Replacement Procedure
A timely conveyor belt replacement procedure is essential for maintaining operational efficiency and ensuring safety in industrial environments. Conveyor belts are critical components in various industries, responsible for transporting materials efficiently. Over time, belts can wear out, leading to potential malfunctions, increased downtime, and even safety hazards. Implementing a regular conveyor belt replacement procedure not only minimizes these risks but also enhances the longevity of the machinery. By adhering to a systematic conveyor belt replacement procedure, companies can maintain smooth operations, reduce unexpected breakdowns, and ensure a safer working environment for their employees. This proactive approach is crucial for sustaining productivity and avoiding costly disruptions.
What is Conveyor Belt Replacement Procedure
Maintaining conveyor belts is crucial for the efficiency and safety of industrial operations. This section will provide a detailed understanding of the conveyor belt replacement procedure, emphasizing the definition, importance, and specific maintenance needs of different types of conveyor belts.
Definition and Importance of Conveyor Belt Maintenance
Conveyor belt maintenance involves the regular inspection, cleaning, adjustment, and replacement of belts to ensure they function effectively and safely. Proper maintenance is vital for several reasons:
- Prevention of Downtime: Regular maintenance helps prevent unexpected breakdowns, ensuring continuous operation and minimizing production losses. A planned conveyor belt replacement procedure allows for scheduled downtime, which is less disruptive and more cost-effective than emergency repairs.
- Safety: A well-maintained conveyor belt reduces the risk of accidents and injuries. Worn-out belts can cause materials to spill or jam, leading to hazardous situations. A systematic conveyor belt replacement procedure ensures that belts are replaced before they become a safety risk.
- Cost Efficiency: Proactive maintenance, including timely conveyor belt replacement procedures, can save costs by extending the lifespan of belts and preventing costly emergency repairs or replacements.
- Optimal Performance: Regular maintenance ensures that conveyor belts operate at their highest efficiency, maintaining consistent production quality and speed. The conveyor belt replacement procedure is a key part of this maintenance, ensuring that worn belts do not impair performance.
- Compliance with Regulations: Many industries have strict safety and operational standards. Adhering to a conveyor belt replacement procedure helps ensure compliance with these regulations, avoiding legal issues and potential fines.

Different Types of Conveyor Belts and Their Specific Maintenance Needs
Various types of conveyor belts are used in different industrial applications, each with unique maintenance requirements. Here are five common types of conveyor belts and their specific maintenance needs:
- Fabric Conveyor Belts: These belts are commonly used in food processing, textile, and other light-duty applications. Maintenance includes regular inspection for fraying or tearing, cleaning to prevent contamination, and ensuring proper tension to avoid slippage. The conveyor belt replacement procedure for fabric belts should be followed meticulously to avoid damage to delicate materials being transported.
- Modular Plastic Conveyor Belts: Often used in the automotive and beverage industries, these belts are made from interlocking plastic modules. Maintenance involves checking for cracks or breaks in the modules, cleaning to remove debris, and lubricating the connecting pins. The conveyor belt replacement procedure for modular belts includes carefully disassembling and reassembling the modules to maintain integrity.
- Metal Conveyor Belts: Used in high-temperature applications such as baking or industrial ovens, metal belts require regular inspection for corrosion or broken links, cleaning to remove build-up, and tension adjustments. The conveyor belt replacement procedure for metal belts must ensure that new belts are properly aligned and tensioned to prevent operational issues.
- Wire Mesh Conveyor Belts: Common in industries like electronics and food processing, wire mesh belts need regular checks for broken wires, cleaning to avoid product contamination, and tension maintenance. The conveyor belt replacement procedure for wire mesh belts involves careful handling to avoid bending or damaging the mesh structure.
- Chain-Driven Conveyor Belts: Utilized in heavy-duty applications such as mining or automotive manufacturing, these belts require maintenance that includes lubrication of chains, inspection for worn or broken links, and tension adjustments. The conveyor belt replacement procedure for chain-driven belts must include proper alignment of chains and sprockets to ensure smooth operation.
Conveyor Belt Replacement Procedure Step by Step
A comprehensive conveyor belt replacement procedure is essential for ensuring that your conveyor system continues to operate smoothly and efficiently. This section provides a detailed step-by-step guide to the entire process, including preparation, removal of the old belt, installation of the new belt, and testing to confirm successful replacement.

Preparation: Guidelines on How to Prepare for a Conveyor Belt Replacement
Before beginning the conveyor belt replacement procedure, it is essential to prepare thoroughly. This includes gathering all necessary tools and materials, reviewing the belt replacement manual, and ensuring safety measures are in place. Proper preparation minimizes downtime and ensures a smooth replacement process.
Proper preparation is critical to the success of the conveyor belt replacement procedure.
- Safety Measures: Before starting any maintenance work, ensure that all safety protocols are followed. This includes locking out and tagging out (LOTO) the conveyor system to prevent accidental startup. Workers should wear appropriate personal protective equipment (PPE) such as gloves, safety glasses, and hard hats.
- Gather Tools and Materials: Collect all necessary tools and materials required for the replacement. This typically includes wrenches, screwdrivers, belt clamps, tension meters, and the new conveyor belt. Having everything on hand will reduce downtime and prevent unnecessary interruptions.
- Review Manufacturer’s Manual: Consult the conveyor belt manufacturer’s manual for specific guidelines and recommendations. The manual provides valuable information on belt tension, alignment, and installation techniques specific to your conveyor system.
- Inspect Conveyor Components: Before removing the old belt, inspect the conveyor system components such as pulleys, rollers, and idlers. Check for any signs of wear or damage that may need repair or replacement during the belt replacement procedure.
- Clear the Area: Ensure that the work area around the conveyor system is clear of obstructions. This includes removing any debris, tools, or materials that could hinder the replacement process or pose safety risks.
Removal of Old Belt: Step-by-Step Instructions
The first step in the conveyor belt replacement procedure is to safely remove the old belt. This involves shutting down the conveyor system, locking out and tagging out (LOTO) the power source, and carefully detaching the belt from its pulleys and rollers. Proper disposal of the old belt is also important to prevent any environmental impact.
Safely removing the old belt is the next critical step in the conveyor belt replacement procedure. Follow these detailed steps to ensure a safe and efficient removal:

- Shutdown the Conveyor System: Ensure the conveyor system is completely shut down and locked out to prevent any accidental start-up during the removal process.
- Release Belt Tension: Using a tension meter, gradually release the tension on the old belt. This will make it easier to remove the belt from the pulleys and rollers without causing damage.
- Detach Belt from Pulleys: Carefully detach the old belt from the drive pulley, tail pulley, and any other pulleys in the system. Use appropriate tools to loosen and remove any fasteners or clamps securing the belt.
- Remove Belt from Structure: Once detached, carefully pull the old belt away from the conveyor structure. Use belt clamps to assist with handling if the belt is heavy or difficult to maneuver.
- Proper Disposal: Dispose of the old belt in accordance with environmental regulations and company policies. Some belts may be recyclable, so check with the manufacturer or local recycling facilities for proper disposal methods.
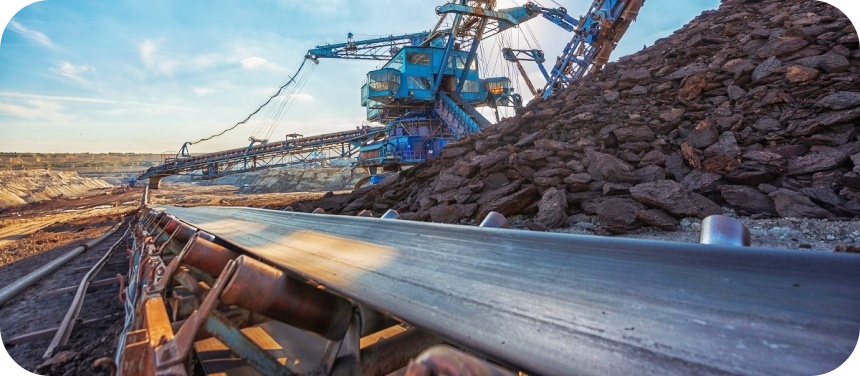
Installation of New Belt: Detailed Steps
Installing the new belt is a critical step in the conveyor belt replacement procedure. The new belt must be properly aligned with the pulleys and rollers to ensure smooth operation. Tension adjustments are necessary to prevent slippage or excessive wear. It is important to follow the manufacturer’s guidelines for belt tension and alignment during this step.
Installing the new belt is a precise task that requires attention to detail. Follow these steps to ensure the new belt is installed correctly, aligned properly, and tensioned accurately:
- Position the New Belt: Place the new belt on the conveyor system, ensuring it is positioned correctly with the smooth side facing the rollers and the textured side facing the material flow.
- Attach to Pulleys: Begin attaching the new belt to the drive pulley, tail pulley, and other pulleys in the system. Use the manufacturer’s recommended fasteners and clamps to secure the belt in place.
- Align the Belt: Proper alignment is crucial for the belt to run smoothly. Use a straightedge or laser alignment tool to ensure the belt is straight and centered on the pulleys. Adjust the pulleys if necessary to achieve perfect alignment.
- Tension the Belt: Gradually apply tension to the new belt using a tension meter. Follow the manufacturer’s guidelines for the correct tension level to prevent slippage and excessive wear. Make small adjustments and check the tension frequently.
- Secure Fasteners: Once the belt is properly aligned and tensioned, secure all fasteners and clamps. Double-check to ensure everything is tight and secure to prevent any movement during operation.
Testing: Procedures to Ensure Smooth Operation
After installing the new belt, the final step in the conveyor belt replacement procedure is to test the conveyor system. This includes running the conveyor at different speeds, checking for any abnormal noises or vibrations, and ensuring that the belt tracks properly. Any issues identified during testing should be addressed immediately to ensure the system operates efficiently and safely.
After the new belt is installed, it is essential to test the conveyor system to confirm that the replacement was successful.
- Initial Run: Start the conveyor system at a low speed and observe the belt’s movement. Check for any signs of misalignment, slippage, or abnormal noises.
- Full Speed Operation: Gradually increase the conveyor speed to its normal operating level. Continue to monitor the belt for smooth operation and any issues that may arise.
- Check Belt Tracking: Ensure the belt is tracking correctly and staying centered on the pulleys. Make any necessary adjustments to the tracking to prevent the belt from wandering off course.
- Monitor Tension: Use the tension meter to check the belt tension during operation. Ensure that the tension remains within the recommended range and make adjustments if needed.
- Inspect for Issues: After the initial run, shut down the conveyor system and inspect the belt and components for any signs of wear, misalignment, or other issues. Address any problems immediately to prevent future breakdowns.
The conveyor belt replacement procedure is a critical maintenance task that requires careful planning and execution. By following these detailed steps for preparation, removal of the old belt, installation of the new belt, and testing, companies can ensure their conveyor systems operate efficiently and safely. Regularly scheduled conveyor belt replacement procedures help maintain productivity, reduce downtime, and enhance workplace safety.
Key Tools and Resources for Conveyor Belt Replacement Procedure
A successful conveyor belt replacement procedure requires the right tools and resources to ensure the process is efficient, safe, and effective. In this section, we will discuss the essential tools needed for replacing a conveyor belt and provide examples of key resources that can aid in the process.

List of Necessary Tools Required for Replacing a Conveyor Belt
Having the correct tools on hand is crucial for the smooth execution of the conveyor belt replacement procedure. Here are five essential tools required for the job:
Tension Meter:
- Purpose: A tension meter is used to measure the tension of the conveyor belt to ensure it is within the recommended range. Proper tension is crucial to prevent slippage, reduce wear, and maintain the belt’s lifespan.
- Example: The Gates Sonic Tension Meter is a popular choice for accurately measuring belt tension using sound waves.
Belt Clamps:
- Purpose: Belt clamps are used to hold the conveyor belt in place during the replacement process. They prevent the belt from moving and ensure it stays aligned while being installed.
- Example: Flexco’s Belt Clamps are durable and designed to provide a firm grip on the belt, making them ideal for the replacement procedure.
Cutting Tools:
- Purpose: Cutting tools are necessary for trimming the conveyor belt to the correct length. They ensure clean cuts that are essential for proper belt splicing and fitting.
- Example: A utility knife with a heavy-duty blade or a specialized electric conveyor belt cutter like the Alligator® 300 Series Belt Cutter can provide precise cuts.
Splicing Kits:
- Purpose: Splicing kits are used to join the ends of the conveyor belt together. They include materials such as fasteners, adhesives, and tools needed to create a strong and durable splice.
- Example: The Flexco® Alligator® Ready Set™ Staple Splice Kit is a comprehensive kit that provides everything needed for quick and efficient belt splicing.
Alignment Tools:
- Purpose: Alignment tools ensure the conveyor belt is properly aligned with the pulleys and rollers. Proper alignment is essential to prevent tracking issues and extend the belt’s lifespan.
- Example: A laser alignment tool like the Pulley Partner® Laser Alignment System can provide accurate and easy-to-use alignment for conveyor belts.
Key Resources for Conveyor Belt Replacement Procedure
In addition to the necessary tools, there are several key resources that can assist in the conveyor belt replacement procedure. These resources provide valuable information, guidelines, and support to ensure the process is carried out correctly and efficiently.
Conveyor Belt Manufacturer’s Manual:
- Purpose: The manufacturer’s manual is a comprehensive guide that provides specific instructions for the conveyor belt replacement procedure. It includes details on belt tension, alignment, and installation techniques.
- Example: Manuals from reputable manufacturers like Fenner Dunlop, Habasit, and ContiTech offer detailed guidance tailored to their specific belt products.
Maintenance and Safety Guidelines:
- Purpose: Maintenance and safety guidelines outline best practices for safely conducting the conveyor belt replacement procedure. They cover important aspects such as lockout/tagout procedures, PPE requirements, and hazard identification.
- Example: OSHA’s guidelines on conveyor belt safety and maintenance provide essential information to ensure compliance with safety regulations.
Training Programs:
- Purpose: Training programs offer hands-on experience and instruction on performing the conveyor belt replacement procedure. They help technicians develop the skills needed to execute the replacement accurately and safely.
- Example: The National Industrial Belting Association (NIBA) offers training programs and certification courses on conveyor belt maintenance and replacement.
Technical Support from Manufacturers:
- Purpose: Many conveyor belt manufacturers offer technical support to assist with the replacement procedure. This support can include troubleshooting assistance, advice on selecting the right belt, and guidance on installation techniques.
- Example: Companies like Flexco and Fenner Dunlop provide technical support services to help customers with their conveyor belt replacement needs.
Online Resources and Forums:
- Purpose: Online resources and forums provide a platform for sharing knowledge, asking questions, and finding solutions to common issues encountered during the conveyor belt replacement procedure. They can be valuable sources of information and support.
- Example: Websites like ConveyorBeltGuide.com and forums such as those on Engineering Stack Exchange offer a wealth of information and community support for conveyor belt maintenance and replacement.
Importance of Using the Right Tools and Resources
Using the right tools and resources for the conveyor belt replacement procedure is essential for several reasons:
- Efficiency: The correct tools and resources streamline the replacement process, reducing downtime and ensuring the procedure is completed quickly and efficiently.
- Safety: Proper tools and adherence to safety guidelines minimize the risk of accidents and injuries during the replacement procedure. Ensuring the belt is correctly installed and tensioned also reduces the risk of future safety hazards.
- Accuracy: Tools like tension meters and alignment devices ensure the belt is installed accurately, preventing issues such as misalignment and improper tension that can lead to premature wear or failure.
- Longevity: Using high-quality tools and following manufacturer guidelines help extend the lifespan of the conveyor belt, reducing the frequency of replacements and associated costs.
- Compliance: Adhering to safety regulations and best practices ensures compliance with industry standards, avoiding potential legal issues and fines.
the conveyor belt replacement procedure requires careful planning and execution using the right tools and resources. By ensuring you have the necessary tools like tension meters, belt clamps, cutting tools, splicing kits, and alignment tools, and by utilizing valuable resources such as manufacturer’s manuals, safety guidelines, training programs, technical support, and online forums, you can successfully carry out the replacement procedure. This approach ensures efficiency, safety, accuracy, and longevity, ultimately maintaining the optimal performance of your conveyor system.
Hiring Professionals for Conveyor Belt Replacement Procedure
The conveyor belt replacement procedure can be complex and requires a high level of expertise to ensure it is done correctly. In some cases, hiring professional services can be the best option to guarantee quality and efficiency. This section will discuss when to consider hiring conveyor belt installation companies and what to look for in a professional service to ensure quality maintenance and installation.

When to Consider Hiring Conveyor Belt Installation Companies
There are several scenarios in which hiring professional conveyor belt installation companies is advisable:
Lack of In-House Expertise:
- If your team lacks the technical skills and experience required to carry out the conveyor belt replacement procedure, it is wise to hire professionals. They bring specialized knowledge and expertise that ensure the job is done right the first time, reducing the risk of errors and subsequent issues.
Complex Systems:
- For conveyor systems that are particularly complex or large, professional installers can handle the intricacies better. Complex systems often require precise alignment and tensioning, which can be challenging without proper experience. Professionals are equipped with the tools and know-how to manage such complexities.
Time Constraints:
- If your operation cannot afford prolonged downtime, hiring professionals can expedite the conveyor belt replacement procedure. Professionals can often complete the job faster and more efficiently than in-house teams, minimizing production losses and downtime.
Safety Concerns:
- Conveyor belt replacement involves significant safety risks, especially in industrial environments. Professional services adhere to strict safety protocols, reducing the risk of accidents and injuries. If safety is a major concern, entrusting the task to experts is the safest option.
Warranty and Compliance:
- Hiring certified professionals can help maintain the warranty on your conveyor system. Many manufacturers require that only qualified personnel perform maintenance and replacements to keep warranties valid. Professionals also ensure that the installation complies with industry standards and regulations.
What to Look for in a Professional Service to Ensure Quality Maintenance and Installation
When selecting a professional service for the conveyor belt replacement procedure, several factors should be considered to ensure quality maintenance and installation:
Experience and Expertise:
- Look for a company with a proven track record in conveyor belt installation and maintenance. Experienced professionals are more likely to handle unforeseen challenges effectively. Check their portfolio and ask for references to gauge their expertise.
Certifications and Training:
- Ensure the professionals are certified and have undergone relevant training. Certifications from recognized industry bodies, such as the National Industrial Belting Association (NIBA), indicate a high standard of competence and professionalism.
Reputation:
- Research the company’s reputation in the industry. Read reviews, testimonials, and case studies to understand their service quality. A company with a strong reputation is more likely to deliver reliable and high-quality service.
Comprehensive Services:
- Choose a company that offers a comprehensive range of services, including inspection, maintenance, installation, and emergency repairs. A full-service provider can manage all aspects of the conveyor belt replacement procedure, ensuring continuity and consistency.
Safety Record:
- Safety should be a top priority. Check the company’s safety record and ensure they follow strict safety protocols. A good safety record indicates a commitment to protecting both their workers and your team during the replacement process.
Use of Advanced Tools and Technology:
- The company should use the latest tools and technology for conveyor belt installation. Advanced tools like laser alignment devices, ultrasonic tension meters, and specialized splicing kits enhance the precision and efficiency of the conveyor belt replacement procedure.
Customer Support:
- Reliable customer support is crucial. The company should be responsive and provide clear communication throughout the process. Good customer support ensures that any issues or questions are addressed promptly.
Warranty and After-Sales Service:
- Check if the company offers a warranty on their work and provides after-sales service. A warranty ensures that they stand by their quality, and after-sales service provides ongoing support for any issues that might arise post-installation.
Cost and Value:
- While cost is an important factor, it should not be the sole consideration. Evaluate the value you are getting for the price. A slightly higher cost may be justified if it ensures higher quality, faster turnaround, and better long-term performance.
References and Recommendations:
- Ask for references from past clients and seek recommendations from industry peers. Direct feedback from previous customers can provide insights into the reliability and quality of the service.
The conveyor belt replacement procedure is a critical maintenance task that requires expertise and precision. While in-house teams can handle simpler replacements, there are situations where hiring professional services is the best course of action. Professionals bring specialized skills, advanced tools, and a commitment to safety, ensuring that the replacement is performed efficiently and correctly.
When choosing a professional service, consider their experience, certifications, reputation, safety record, use of advanced technology, customer support, warranty, and overall value. By selecting the right professionals, you can ensure that your conveyor system continues to operate smoothly, safely, and efficiently, minimizing downtime and maximizing productivity.
Maintenance and Troubleshooting for Conveyor Belt Replacement Procedure
Ensuring the longevity and efficiency of a conveyor belt system requires diligent maintenance and effective troubleshooting practices. This section provides detailed guidance on regular maintenance tips to extend the lifespan of conveyor belts and addresses common issues that might arise post-replacement along with their troubleshooting methods.
Regular Maintenance Tips to Extend the Lifespan of Conveyor Belts
Regular maintenance is key to maximizing the lifespan and performance of conveyor belts.
Regular Inspections:
- Purpose: Regular inspections help identify early signs of wear, damage, or misalignment before they lead to major issues.
- Procedure: Conduct visual inspections of the belt surface for cracks, fraying, or cuts. Check the belt’s alignment and ensure that it is running straight on the pulleys. Look for any unusual noises that might indicate mechanical problems.
Proper Tensioning:
- Purpose: Maintaining the correct tension in the conveyor belt is crucial to prevent slippage, reduce wear, and ensure smooth operation.
- Procedure: Use a tension meter to regularly check the belt tension. Adjust the tension according to the manufacturer’s specifications. Over-tensioning can cause excessive wear, while under-tensioning can lead to slippage and misalignment.
Cleaning:
- Purpose: Keeping the conveyor belt clean prevents build-up of debris that can cause premature wear and reduce efficiency.
- Procedure: Regularly clean the belt and the conveyor system using appropriate cleaning agents. Remove any materials stuck on the belt or within the system. Ensure that cleaning is done in a manner that does not damage the belt material.
Lubrication:
- Purpose: Proper lubrication of moving parts reduces friction, wear, and the risk of mechanical failures.
- Procedure: Apply lubricants to bearings, rollers, and other moving parts according to the manufacturer’s recommendations. Avoid over-lubrication as it can attract dust and debris, which can lead to additional wear.
Alignment Checks:
- Purpose: Ensuring the belt is properly aligned prevents uneven wear and potential belt damage.
- Procedure: Use alignment tools to check that the belt is running centrally on the pulleys. Adjust the pulleys and rollers as needed to correct any misalignment. Regular alignment checks help maintain the belt’s longevity and operational efficiency.
Common Issues That Might Arise Post-Replacement and How to Troubleshoot Them
After completing the conveyor belt replacement procedure, it’s essential to monitor the system for any issues that might arise.
Belt Misalignment:
- Issue: The belt is not tracking correctly and is running off-center on the pulleys.
- Troubleshooting: Check the alignment of the pulleys and rollers. Adjust the tracking devices to ensure the belt is running straight. Inspect the belt for any damage or deformation that might be causing misalignment.
Slippage:
- Issue: The conveyor belt slips on the pulleys, causing loss of efficiency and potential damage.
- Troubleshooting: Check the belt tension and adjust it to the proper level. Inspect the pulleys for wear or build-up of materials that might be causing slippage. Ensure that the belt and pulleys are clean and free of contaminants.
Excessive Wear:
- Issue: The belt shows signs of excessive wear shortly after replacement.
- Troubleshooting: Inspect the belt for proper tension and alignment. Check the system for sharp edges or rough surfaces that might be causing wear. Ensure that the belt material is suitable for the application and that it was installed correctly.
Unusual Noises:
- Issue: The conveyor system produces unusual noises, indicating potential mechanical issues.
- Troubleshooting: Identify the source of the noise. Check for loose components, misaligned parts, or worn bearings. Lubricate moving parts as needed and replace any damaged or worn components to eliminate the noise.
Belt Breakage:
- Issue: The conveyor belt breaks or tears, leading to system downtime.
- Troubleshooting: Investigate the cause of the breakage. Check for overloading, sharp objects, or improper belt tension that might have caused the damage. Ensure that the replacement belt is appropriate for the application and that it was installed following the proper conveyor belt replacement procedure.
Proper maintenance and effective troubleshooting are integral to the successful operation of a conveyor belt system following a conveyor belt replacement procedure. Regular inspections, proper tensioning, cleaning, lubrication, and alignment checks are essential maintenance practices that help extend the lifespan of conveyor belts.
By being vigilant and addressing common issues such as misalignment, slippage, excessive wear, unusual noises, and belt breakage promptly, you can maintain the efficiency and reliability of your conveyor system. A proactive approach to maintenance and troubleshooting not only enhances the performance of the conveyor belt but also minimizes downtime, reduces repair costs, and ensures a safer working environment.
Incorporating these best practices into your maintenance routine will ensure that the conveyor belt replacement procedure remains effective and contributes to the overall productivity and safety of your industrial operations.
Need More Details? Fill Out Our Inquiry Form for Conveyor Belts.
FAQs About conveyor belt replacement procedure
The conveyor belt replacement procedure involves several key steps to ensure the process is carried out efficiently and safely. Here’s a step-by-step guide:
Preparation: Gather all necessary tools and materials, review the manufacturer’s guidelines, and ensure safety measures such as lockout/tagout (LOTO) procedures are in place. Clear the work area of any obstructions.
Release Belt Tension: Use a tension meter to gradually release the tension on the old belt.
Remove Old Belt: Carefully detach the old belt from the pulleys and rollers, and properly dispose of it according to environmental regulations.
Install New Belt: Position the new belt on the conveyor system, ensuring proper alignment with the pulleys and rollers. Secure the belt using the recommended fasteners and clamps.
Adjust Tension: Apply the correct tension to the new belt using a tension meter, following the manufacturer’s specifications.
Test: Run the conveyor system at different speeds to ensure the belt tracks properly and operates smoothly. Make any necessary adjustments to alignment and tension.
Following these steps ensures the conveyor belt replacement procedure is completed safely and effectively, minimizing downtime and maintaining operational efficiency.
Joining a broken conveyor belt involves a precise splicing process to ensure the belt is restored to its full operational capability. Here’s a detailed procedure:
Identify the Break: Locate the exact point of the break and clean the area around it.
Prepare the Ends: Trim the ends of the broken belt to create clean, straight edges. This ensures a strong, even splice.
Choose Splicing Method: Depending on the belt type and operational requirements, choose an appropriate splicing method—mechanical fasteners or vulcanization.
Mechanical Fasteners: If using mechanical fasteners, align the belt ends and install the fasteners according to the manufacturer’s instructions. Use a press or other tools to ensure a tight, secure fit.
Vulcanization: For vulcanization, apply adhesive to the belt ends and use a vulcanizing press to bond them together. This method provides a strong, seamless joint.
Allow Cure Time: If using adhesive or vulcanization, allow sufficient time for the bond to cure completely.
Test the Splice: Once the splice is completed, run the conveyor system to ensure the joint is holding and the belt is tracking properly.
By following these steps, you can effectively join a broken conveyor belt and restore its functionality.
Installing a conveyor belt requires careful preparation and attention to detail to ensure proper alignment and tension. Here’s a step-by-step guide:
Preparation: Gather all necessary tools and materials, review the conveyor system’s specifications, and ensure safety measures are in place.
Position the Belt: Place the new belt on the conveyor frame, ensuring it is positioned correctly with the smooth side facing the rollers and the textured side facing the material flow.
Align the Belt: Use alignment tools to ensure the belt is properly centered on the pulleys and rollers. Adjust the pulleys as necessary to achieve perfect alignment.
Attach to Pulleys: Begin attaching the belt to the drive pulley, tail pulley, and other pulleys in the system. Secure the belt with the appropriate fasteners and clamps.
Apply Tension: Gradually apply tension to the belt using a tension meter. Follow the manufacturer’s guidelines for the correct tension level.
Secure Fasteners: Once the belt is properly aligned and tensioned, ensure all fasteners and clamps are tightly secured.
Test the Installation: Run the conveyor system at different speeds to check for smooth operation. Ensure the belt tracks correctly and make any necessary adjustments.
Proper installation of a conveyor belt is crucial for efficient operation and longevity of the system.
The process of conveyor belts involves the continuous movement of materials over a series of rollers and pulleys, driven by a motor. Here’s an overview of how conveyor belts operate:
Loading: Materials are loaded onto the conveyor belt at the input end. This can be done manually or using automated loading systems.
Transporting: The motor drives the belt, causing it to move along the rollers and pulleys. The materials are carried on the belt’s surface from the loading point to the discharge point.
Tracking and Alignment: The belt must be properly aligned to ensure it tracks correctly along the pulleys and rollers. Misalignment can cause the belt to wander off course, leading to potential damage.
Tensioning: Maintaining the correct tension in the belt is essential for smooth operation. Proper tension prevents slippage and reduces wear on the belt and pulleys.
Discharging: At the end of the conveyor system, the materials are discharged from the belt. This can be into a bin, onto another conveyor, or directly into processing equipment.
Maintenance: Regular maintenance, including inspections, cleaning, and lubrication, is necessary to keep the conveyor system running efficiently. Addressing issues such as wear, misalignment, and tension adjustments prolongs the lifespan of the conveyor belt.
Understanding the process of conveyor belts helps in optimizing their use and maintaining them effectively for industrial applications.
Preparation: Before beginning the conveyor belt replacement procedure, it is essential to prepare thoroughly.
Removal of Old Belt: The first step in the conveyor belt replacement procedure is to safely remove the old belt.
Installation of New Belt: Installing the new belt is a critical step in the conveyor belt replacement procedure.
Testing: After installing the new belt, the final step in the conveyor belt replacement procedure is to test the conveyor system.
The time needed to replace a conveyor belt varies depending on factors such as belt length, complexity of the conveyor system, and proficiency of the maintenance crew. Generally, replacing a conveyor belt can take anywhere from a few hours to a full day or more for larger, more complex systems.
For straightforward systems with accessible conveyor sections, skilled technicians can often complete the replacement within 4 to 8 hours. This includes shutdown time, preparation, removal of the old belt, installation of the new belt, splicing (if required), and testing.
However, larger or more intricate conveyor systems, especially those with multiple belts or specialized equipment, may require longer downtime and more detailed procedures, extending the replacement process to a day or more.
Effective planning, adequate preparation, and experienced personnel are crucial to minimizing downtime and completing the replacement swiftly without compromising safety or quality.
When storing a conveyor belt, keep it in the original packaging or under a cover. Make sure the belt is stored in a dark, cool, dry place.
First of all, don’t roll them. Gently place the belt on the ground, then hoist bars using a lift and spreader bar.
Conveyor belt lacings include: alligator, plastic rivet, clipper, unibar, and bolt.
Belt tension is usually adjusted at the take-up pulley or the last lacing point.
Make adjustments in small increments and equally on both sides of the take-up pulley, and ensure that the ends of the belts are lined up properly.
Last Updated on July 30, 2024 by Jordan Smith
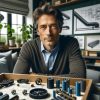
Jordan Smith, a seasoned professional with over 20 years of experience in the conveyor system industry. Jordan’s expertise lies in providing comprehensive solutions for conveyor rollers, belts, and accessories, catering to a wide range of industrial needs. From initial design and configuration to installation and meticulous troubleshooting, Jordan is adept at handling all aspects of conveyor system management. Whether you’re looking to upgrade your production line with efficient conveyor belts, require custom conveyor rollers for specific operations, or need expert advice on selecting the right conveyor accessories for your facility, Jordan is your reliable consultant. For any inquiries or assistance with conveyor system optimization, Jordan is available to share his wealth of knowledge and experience. Feel free to reach out at any time for professional guidance on all matters related to conveyor rollers, belts, and accessories.