How to Maintain Your Conveyor Belt Roll Efficiently
Before diving into the specifics, let’s define what a conveyor belt roll is and what functions it serves in industrial and commercial applications. A conveyor belt roll is a cylindrical component made of rubber or fabric that is wound around a spool. It is an essential part of conveyor belt systems, providing the movement mechanism for transporting materials. In industrial settings, conveyor belt rolls are used to move heavy goods, raw materials, and finished products efficiently. In commercial applications, they are commonly found in packaging, assembly lines, and retail logistics. Understanding the role and functionality of a conveyor belt roll is crucial for optimizing workflow and ensuring smooth operations in various sectors.
The Significance of Conveyor Belt Roll Width
The width of a roll of conveyor belt is a critical factor that influences its performance and suitability for various applications. Understanding the importance of conveyor belt roll width can help industries optimize their operations and ensure efficient material handling. This section delves into the significance of roll width, providing examples and explanations of its impact on conveyor belt applications.
Explanation of Roll Width and Its Importance
- Material Handling Capacity: The width of a conveyor belt roll directly affects the amount of material it can transport. A wider belt can carry larger or bulkier items, making it ideal for industries that handle heavy loads, such as mining or construction. For instance, a 48-inch conveyor belt roll can transport more material compared to a 24-inch roll, increasing the efficiency of operations.
- Compatibility with Machinery: Different conveyor systems are designed to accommodate specific belt widths. Using the correct width ensures that the conveyor belt roll fits seamlessly into the existing machinery, reducing the risk of mechanical failures. For example, a packaging plant may require a conveyor belt roll width of 30 inches to match its automated packing lines.
- Stability and Balance: The width of a conveyor belt roll can impact the stability of the items being transported. Wider belts provide a larger surface area, reducing the chances of items tipping over or falling off. This is particularly important in industries such as food processing, where maintaining the integrity of the product is crucial. A bakery might use a 36-inch conveyor belt roll to transport loaves of bread, ensuring they remain upright and undamaged.
- Speed and Efficiency: Wider conveyor belts can move materials more quickly, as they can accommodate higher volumes with each pass. This increased throughput can significantly enhance operational efficiency. For example, a recycling facility might use a 60-inch conveyor belt roll to rapidly sort and transport recyclable materials, increasing the speed of the sorting process.
- Customization and Flexibility: Conveyor belt rolls come in various widths to suit different industry needs. Customizing the width allows businesses to tailor their conveyor systems to specific applications. For instance, a pharmaceutical company might require a narrow 18-inch roll of conveyor belt for transporting small, delicate packages through a production line, ensuring precise handling and minimal damage.
How Roll Width Affects the Application and Efficiency of Conveyor Belts
The width of a conveyor belt roll plays a significant role in determining its application and efficiency. Here’s how:
- Optimal Load Distribution: A properly chosen conveyor belt roll width ensures optimal load distribution, preventing excessive wear and tear on the belt and machinery. For instance, a wider belt distributes the weight of heavy materials more evenly, reducing stress on the conveyor system and extending its lifespan.
- Enhanced Workflow: The appropriate width of a conveyor belt roll can streamline workflow by allowing more materials to be transported in a single pass. This reduces the number of trips required, saving time and labor. In a warehouse setting, using a 42-inch conveyor belt roll can expedite the movement of goods from storage to shipping areas, enhancing overall productivity.
- Reduced Downtime: Using the correct conveyor belt roll width minimizes the risk of jams and malfunctions, leading to less downtime for maintenance and repairs. A narrow belt might struggle with large items, causing frequent stoppages. Conversely, a wider belt can handle varied item sizes more effectively, ensuring continuous operation. For example, a distribution center might benefit from a 54-inch conveyor belt roll to accommodate diverse package sizes without interruptions.
- Energy Efficiency: The width of a conveyor belt roll can also impact the energy consumption of the conveyor system. Wider belts, by carrying more material per pass, can reduce the total operational hours needed, thereby saving energy. An agricultural processing plant, for instance, might use a 48-inch conveyor belt roll to move harvested crops, reducing the energy required for multiple shorter runs.
- Safety Considerations: Choosing the correct conveyor belt roll width enhances workplace safety by reducing the risk of material spillage and equipment strain. Wider belts provide a more secure transport surface, minimizing hazards associated with falling objects. In the automotive industry, a 36-inch conveyor belt roll might be used to transport parts securely, ensuring a safer working environment for employees.
The width of a conveyor belt roll is a fundamental aspect that affects its functionality and efficiency in various industrial and commercial applications. By understanding the significance of roll width, businesses can make informed decisions that enhance productivity, ensure compatibility with machinery, and maintain safe and stable operations.
Conveyor Belt Rolls for Sale – A Buyer’s Guide
When purchasing a conveyor belt roll, there are several key considerations to keep in mind to ensure you select the best option for your specific needs. This guide will walk you through these considerations and provide an overview of the different types of conveyor belt rolls available in the market.
Key Considerations When Purchasing Conveyor Belt Rolls
- Material Composition: The material of the conveyor belt roll is crucial as it affects the durability and suitability for various applications. For example, rubber conveyor belt rolls are highly resistant to wear and tear, making them ideal for heavy-duty industrial applications. In contrast, PVC conveyor belt rolls are better suited for lighter loads and environments where hygiene is a priority, such as in food processing.
- Roll Width and Length: The width and length of the roll of conveyor belt must match the requirements of your conveyor system. An incorrect size can lead to inefficiencies and operational issues. For instance, a 36-inch wide conveyor belt roll might be perfect for a warehouse moving bulky items, while a 24-inch wide roll could be more suitable for a manufacturing line handling smaller parts.
- Load Capacity: Understanding the load capacity that the conveyor belt roll can handle is essential. Overloading a belt can cause premature wear or even system failure. For example, a conveyor belt roll designed for light loads in a retail distribution center may not be appropriate for transporting heavy mining materials. Ensure that the roll you choose can handle the maximum load your operations require.
- Environmental Resistance: The operating environment greatly influences the type of conveyor belt roll you should choose. If your operations are exposed to harsh conditions such as extreme temperatures, chemicals, or abrasive materials, you need a conveyor belt roll that can withstand these factors. For example, a heat-resistant rolling conveyor belt would be necessary for a high-temperature manufacturing process.
- Cost and Budget: While it’s important to consider the initial cost of the conveyor belt roll, you should also think about the long-term value. A cheaper option might save money upfront but could cost more in maintenance and replacements over time. For instance, investing in a higher-quality conveyor belt roll with a longer lifespan could be more cost-effective for continuous use in a production facility.
Different Types of Conveyor Belt Rolls Available in the Market
- Standard Conveyor Belt Rolls: These are the most common types and are typically made of rubber or PVC. They are used in a variety of industries, including manufacturing, logistics, and retail. A standard conveyor belt roll is versatile and can handle a range of materials and loads.
- Heat-Resistant Conveyor Belt Rolls: Designed to withstand high temperatures, these conveyor belt rolls are ideal for industries such as metalworking and baking, where the materials being transported are often hot. For example, a heat-resistant conveyor belt roll might be used in a foundry to move molten metal parts.
- Oil-Resistant Conveyor Belt Rolls: These rolls are specifically designed to resist the damaging effects of oil and grease. They are commonly used in food processing, automotive, and chemical industries. An oil-resistant conveyor belt roll is essential in environments where contact with oily substances is frequent.
- Flame-Resistant Conveyor Belt Rolls: Safety is paramount in industries like mining and power generation, where the risk of fire is high. Flame-resistant conveyor belt rolls are designed to minimize the risk of fire and ensure safe operation in hazardous environments. For instance, a flame-resistant conveyor belt roll would be used in an underground mine to transport coal.
- High-Abrasion Resistant Conveyor Belt Rolls: In industries where materials are particularly abrasive, such as in mining or quarrying, high-abrasion resistant conveyor belt rolls are necessary. These rolls are made with tough materials that can withstand constant wear and tear, prolonging the life of the belt. An example would be a rolling conveyor belt used to transport sharp rocks in a quarry.
Selecting the right conveyor belt roll involves careful consideration of material composition, roll width and length, load capacity, environmental resistance, and cost. By understanding these factors and exploring the different types of conveyor belt rolls available, you can make an informed decision that enhances the efficiency and reliability of your operations. Whether you need a standard, heat-resistant, oil-resistant, flame-resistant, or high-abrasion resistant conveyor belt roll, ensuring it matches your specific requirements will optimize your material handling processes and contribute to the overall success of your business.
Conveyor Belt Roll Pricing – What to Expect
When planning to purchase a conveyor belt roll, understanding the pricing dynamics can help you make an informed decision. Several factors influence the price of conveyor belt rolls, and knowing these can assist you in budgeting appropriately. This section covers the key factors affecting the cost, provides estimated pricing per meter for various types of conveyor belt rolls, and offers tips for getting the best value for your purchase.
Factors Influencing the Price of Conveyor Belt Rolls
- Material Composition: The type of material used in manufacturing the conveyor belt roll significantly impacts its price. Rubber conveyor belt rolls tend to be more expensive due to their durability and resistance to wear and tear, whereas PVC conveyor belt rolls are generally cheaper but less durable. Specialty materials like silicone or Teflon, used in specific industries, can also drive up the cost.
- Roll Width and Length: The dimensions of the conveyor belt roll play a crucial role in determining its price. Wider and longer rolls require more material and manufacturing effort, thus increasing the cost. For example, a 48-inch wide conveyor belt roll will cost more than a 24-inch wide roll of the same material and thickness.
- Load Capacity: Conveyor belt rolls designed to handle heavier loads are typically more expensive. These belts are constructed with reinforced materials to ensure they can support significant weight without compromising their integrity. For instance, a heavy-duty conveyor belt roll for industrial applications will cost more than a light-duty roll intended for smaller, less demanding tasks.
- Environmental Resistance: Conveyor belt rolls with special properties to withstand harsh environmental conditions, such as high temperatures, chemical exposure, or abrasive materials, often come at a premium. Heat-resistant or flame-retardant conveyor belt rolls, for example, are more costly due to the specialized materials and treatments involved in their production.
- Brand and Quality: The manufacturer’s reputation and the quality of the rolling belt conveyor also affect the price. Established brands known for producing high-quality, reliable products often charge more than lesser-known or generic brands. Investing in a reputable brand can ensure better performance and longevity, potentially saving money in the long run.
Estimated Pricing Per Meter for Various Conveyor Belt Rolls
- Standard Rubber Conveyor Belt Roll: Typically ranges from $10 to $30 per meter, depending on the width and thickness.
- PVC Conveyor Belt Roll: Generally costs between $5 and $20 per meter, varying with the specifications.
- Heat-Resistant Conveyor Belt Roll: Prices can range from $20 to $50 per meter, based on the temperature rating and material quality.
- Oil-Resistant Conveyor Belt Roll: Usually priced between $15 and $40 per meter, depending on the level of oil resistance and material used.
- Flame-Resistant Conveyor Belt Roll: Costs approximately $25 to $60 per meter, influenced by the safety standards and certifications it meets.
Tips for Getting the Best Value for Your Purchase
- Assess Your Needs Accurately: Determine the specific requirements of your application to avoid overspending on unnecessary features. For instance, if your operations do not involve high temperatures, there is no need to invest in a heat-resistant conveyor belt roll.
- Compare Prices from Multiple Suppliers: Obtain quotes from several suppliers to compare prices and services. This can help you identify the most cost-effective option without compromising on quality. Online marketplaces and industry-specific trade shows are good places to find multiple suppliers.
- Consider Long-Term Costs: While cheaper options may seem attractive initially, consider the long-term costs associated with maintenance, repairs, and replacements. Investing in a higher-quality conveyor belt roll can be more economical over time due to its durability and reduced need for frequent replacements.
- Negotiate Bulk Discounts: If you need a large quantity of conveyor belt rolls, negotiating bulk discounts with suppliers can result in significant savings. Suppliers are often willing to offer better prices for larger orders to secure the business.
- Look for Warranties and Guarantees: Purchase conveyor belt rolls that come with warranties or guarantees to protect your investment. This ensures that you can get a replacement or repair if the product fails within the warranty period, providing peace of mind and additional value.
The price of a conveyor belt roll is influenced by several factors including material composition, dimensions, load capacity, environmental resistance, and brand quality. By understanding these factors and considering the estimated pricing, you can make informed decisions that align with your budget and operational needs. Additionally, employing strategies such as assessing your needs accurately, comparing prices, considering long-term costs, negotiating bulk discounts, and seeking warranties can help you get the best value for your purchase.
Conveyor Belt Roll – The Mechanism Explained
Understanding how a conveyor belt roll operates within a belt system is essential for optimizing its performance and ensuring efficient material handling. This section delves into the operation of conveyor belt rolls and explores the engineering principles behind their movement.
How Conveyor Belt Rolls Operate Within a Belt System
A conveyor belt roll is a fundamental component of a conveyor system, which is designed to transport materials from one point to another efficiently. The operation of a conveyor belt roll involves several key elements working in harmony:
- Roller System: The conveyor belt roll is supported by a series of rollers, which provide a stable platform for the belt to move smoothly. These rollers are strategically placed along the length of the conveyor system to minimize friction and support the weight of the materials being transported.
- Drive Mechanism: The movement of the rolling belt conveyor is powered by a drive mechanism, typically consisting of an electric motor and a drive pulley. The motor provides the necessary torque to rotate the drive pulley, which in turn moves the conveyor belt roll. The speed and direction of the belt can be controlled by adjusting the motor settings.
- Tensioning System: Proper tension is crucial for the efficient operation of a conveyor belt roll. A tensioning system ensures that the belt is taut and properly aligned, preventing slippage and maintaining consistent movement. This system can include adjustable tensioners, counterweights, or automatic tensioning devices.
- Belt Material and Construction: The conveyor belt roll itself is made from durable materials such as rubber, PVC, or fabric. The construction of the belt, including its thickness and reinforcement layers, determines its load capacity and resistance to wear and tear. The belt material is selected based on the specific requirements of the application, such as temperature resistance or chemical compatibility.
- Tracking System: To maintain the proper alignment of the conveyor belt roll, a tracking system is employed. This system uses sensors and guide rollers to monitor and adjust the position of the belt, ensuring it stays centered on the rollers and preventing misalignment that could lead to damage or inefficiency.
The Engineering Behind the Movement of Rolls on a Conveyor Belt
The movement of conveyor belt rolls involves several engineering principles that ensure smooth and efficient operation:
- Friction and Traction: The interaction between the conveyor belt roll and the rollers involves friction, which provides the necessary traction to move the belt. The surface texture and material of the belt and rollers are designed to optimize friction, ensuring the belt moves without slipping. Proper maintenance of the rollers and belt surface is essential to maintain optimal friction levels.
- Load Distribution: Engineering a conveyor belt roll system requires careful consideration of load distribution. The weight of the materials being transported must be evenly distributed across the belt to prevent uneven wear and potential damage. Rollers and support structures are designed to handle specific load capacities, ensuring the belt operates within its intended parameters.
- Belt Tension and Alignment: The tensioning system plays a critical role in maintaining the belt’s tension and alignment. Engineering calculations determine the appropriate tension levels based on the belt’s length, material, and load capacity. Automated tensioning devices can adjust the tension dynamically, compensating for changes in load or belt elongation over time.
- Pulley and Motor Dynamics: The drive pulley and motor dynamics are engineered to match the specific requirements of the conveyor system. Factors such as motor power, pulley diameter, and rotational speed are carefully calculated to provide the necessary force to move the conveyor belt roll. Variable speed drives can be employed to adjust the belt speed according to the operational needs.
- Energy Efficiency: Engineering considerations also focus on the energy efficiency of the conveyor belt roll system. Efficient motor designs, low-friction rollers, and optimized belt materials contribute to reducing energy consumption. Advanced control systems can further enhance efficiency by adjusting the motor output based on real-time operational data.
The operation of a conveyor belt roll within a belt system is a complex interplay of various components and engineering principles. From the roller system and drive mechanism to the tensioning and tracking systems, each element is designed to ensure smooth and efficient material transport. Understanding the engineering behind the movement of rolling belt conveyor allows for better maintenance, optimization, and troubleshooting of conveyor systems, ultimately enhancing their performance and longevity.
Crossword Fun: Conveyor Belt Roll
Engaging with complex topics like conveyor belt rolls can sometimes be a bit dry, but adding an element of fun can make learning more enjoyable. One way to do this is through puzzles and trivia that challenge and entertain readers while reinforcing key concepts. This section provides an interactive and entertaining approach to understanding conveyor belt rolls, complete with a crossword puzzle designed to test and enhance your knowledge about these essential industrial components.
Engaging Readers with Puzzles and Trivia
Crossword puzzles are a great way to engage readers, combining education with entertainment. They encourage critical thinking and help reinforce the learning material in a fun and memorable way. In the context of conveyor belt rolls, a crossword puzzle can cover various aspects such as terminology, components, and applications. Here are some trivia questions and puzzle clues to get started:
- What material is commonly used to make heavy-duty conveyor belt rolls?
- Answer: Rubber
- Crossword Clue: Common material for heavy-duty conveyor belt rolls (6 letters)
- Which component of the conveyor system provides the necessary tension?
- Answer: Tensioner
- Crossword Clue: Device that maintains proper belt tension (9 letters)
- What is the primary function of a conveyor belt roll in industrial settings?
- Answer: Transport
- Crossword Clue: Main function of a conveyor belt roll (8 letters)
- What type of conveyor belt roll is used in environments with high temperatures?
- Answer: Heat-resistant
- Crossword Clue: Type of belt roll used in high-temperature environments (13 letters)
- What system ensures the conveyor belt stays aligned during operation?
- Answer: Tracking system
- Crossword Clue: System that keeps the belt aligned (14 letters)
Additional Trivia and Facts
To further engage readers, here are some additional trivia questions and interesting facts about conveyor belt rolls:
- Trivia Question: What was one of the earliest uses of conveyor belt systems in history?
- Answer: The first conveyor belt system was used to transport coal in the late 19th century.
- Fact: Conveyor belt systems have evolved significantly since then, now used in a wide range of industries including mining, manufacturing, and logistics.
- Trivia Question: How does the width of a conveyor belt roll affect its load capacity?
- Answer: A wider conveyor belt roll can transport larger and heavier loads more efficiently.
- Fact: The width of the belt plays a crucial role in determining the overall capacity and efficiency of the conveyor system.
- Trivia Question: What is the primary advantage of using a heat-resistant conveyor belt roll?
- Answer: It can withstand high temperatures without degrading, making it ideal for hot environments.
- Fact: Heat-resistant belts are commonly used in industries like metalworking and food processing.
Adding a crossword puzzle and trivia about conveyor belt rolls not only makes the learning process more enjoyable but also reinforces key concepts. Engaging with the material through puzzles can help readers better retain information and gain a deeper understanding of the essential components and functions of conveyor belt rolls.
FAQs About Conveyor Belt Roll
The rollers on a conveyor belt are typically called “idlers” or “idler rollers.” Idlers are crucial components of a conveyor system, providing support for the conveyor belt and the materials being transported. They are usually spaced at regular intervals along the length of the conveyor to ensure smooth and efficient movement. There are different types of idlers, including carrying idlers, return idlers, and impact idlers, each serving a specific function. Carrying idlers support the loaded belt, return idlers support the empty belt on its return, and impact idlers are used at loading points to absorb shock and reduce wear on the belt.
The cost of a conveyor belt per foot can vary widely based on several factors, including the belt material, width, thickness, and specific application requirements. On average, a standard rubber conveyor belt might cost between $10 to $20 per foot. For specialty belts, such as those with heat-resistant or flame-retardant properties, the cost can rise significantly, ranging from $30 to $50 per foot or more. Additionally, custom-designed belts or those made from premium materials like silicone or Teflon may also come at a higher price. It’s essential to consider both the initial cost and the long-term value, including durability and maintenance requirements, when budgeting for conveyor belts.
The wheels on a conveyor belt system are typically referred to as “pulleys.” Pulleys are essential for driving the conveyor belt and maintaining tension. There are two main types of pulleys: drive pulleys and idler pulleys. The drive pulley is connected to the motor and powers the movement of the belt, while the idler pulley helps guide and tension the belt. Both types of pulleys are critical to the efficient operation of a conveyor system, ensuring the belt moves smoothly and consistently. Pulleys can be made from various materials, including steel and aluminum, and may feature rubber lagging to improve grip and reduce wear.
Last Updated on June 3, 2024 by Jordan Smith
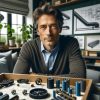
Jordan Smith, a seasoned professional with over 20 years of experience in the conveyor system industry. Jordan’s expertise lies in providing comprehensive solutions for conveyor rollers, belts, and accessories, catering to a wide range of industrial needs. From initial design and configuration to installation and meticulous troubleshooting, Jordan is adept at handling all aspects of conveyor system management. Whether you’re looking to upgrade your production line with efficient conveyor belts, require custom conveyor rollers for specific operations, or need expert advice on selecting the right conveyor accessories for your facility, Jordan is your reliable consultant. For any inquiries or assistance with conveyor system optimization, Jordan is available to share his wealth of knowledge and experience. Feel free to reach out at any time for professional guidance on all matters related to conveyor rollers, belts, and accessories.