Conveyor Belt Roller Alignment: Follow Tracking Rules
Conveyor belt roller alignment is a crucial aspect of maintaining efficient and safe conveyor belt operations. Proper alignment ensures that the belt runs smoothly and minimizes wear and tear, ultimately reducing downtime and prolonging the life of your conveyor system. Misalignment, on the other hand, can lead to common issues such as uneven belt wear, material spillage, increased energy consumption, and even belt slippage. These problems can cause unexpected production stoppages, increased maintenance costs, and potential safety hazards. Understanding and implementing effective conveyor belt roller alignment practices will help prevent these issues and maintain optimal performance in your bulk material handling processes.
What are Conveyor Belt Roller Alignment
Conveyor belt alignment is a critical aspect of conveyor system maintenance and efficiency. Proper alignment of the conveyor belt ensures smooth operation, reduced wear on the belt and rollers, and a significant extension of the system’s overall lifespan.
Definition of Conveyor Belt Alignment
Conveyor belt alignment refers to the correct positioning of the belt on the conveyor structure, ensuring it is centered and runs straight along the tracks. This is crucial for the seamless transfer of materials from one point to another without any slippage or tracking issues.
Significance of Conveyor Belt Alignment
- Extended Belt Life: Properly aligned conveyor belts suffer less wear and tear, which significantly extends their operational life.
- Reduced Maintenance Costs: Alignment reduces the need for frequent maintenance checks and replacements, thereby saving costs.
- Increased Safety: Misalignment can lead to belt slippage or entrapment of materials, posing safety risks to operators.
- Enhanced Efficiency: A well-aligned belt ensures optimal performance and throughput, which is essential for maintaining productivity.
- Lower Energy Consumption: When belts and rollers are aligned, the conveyor system operates more efficiently, using less energy.
- Decreased Downtime: Fewer alignment issues mean fewer operational interruptions, which translates to consistent production outputs.
- Improved Product Quality: Consistent and reliable handling of materials helps maintain the quality of the product being transported.
- Environmental Impact: Reduced wear and energy usage contribute to a more environmentally friendly operation.
Impact of Misalignment on Conveyor Operations and Maintenance
Misalignment of the conveyor belt can have several detrimental effects on the operation and maintenance of a conveyor system:
- Increased Wear and Tear: When the conveyor belt is not aligned properly, it can rub against the conveyor structure, causing premature wear on both the belt and the structure itself.
- Frequent Repairs: Misaligned belts often lead to damage to other components like conveyor belt rollers and bearings, necessitating more frequent repairs and replacements.
- Operational Inefficiency: A belt that is not aligned properly can cause material spillage, uneven belt wear, and inaccurate sorting or processing of materials.
- Safety Hazards: Misalignment can lead to unexpected behaviors like sudden belt movements, which pose serious safety risks to workers near the conveyor.
- Higher Energy Costs: Misaligned conveyor belts require more energy to operate, as the system has to overcome increased resistance from misaligned components.
- Environmental Risks: Increased wear and tear lead to more frequent disposal of worn-out parts, which could have environmental consequences if not managed properly.
- Production Downtime: Correcting issues caused by misalignment often requires halting the conveyor system, leading to production delays.
By ensuring proper conveyor belt roller alignment, these issues can be minimized, leading to a more efficient, cost-effective, and safe operation. Proper alignment not only helps in achieving optimum performance but also plays a pivotal role in extending the life and reliability of the conveyor system.
Basic Components of Conveyor Belt Roller Alignment Systems
Conveyor Belt Roller Alignment
Proper conveyor belt roller alignment is integral to the functioning of conveyor belt systems. This section delves into the fundamental components of these systems, namely rollers, pulleys, and the conveyor belt itself, each playing a vital role in maintaining the alignment and efficiency of the entire system.
Rollers
Rollers support the conveyor belt and facilitate its smooth movement. They must be precisely aligned to ensure the belt travels in a straight line. Misaligned rollers can lead to the conveyor belt drifting off its intended path, which can cause uneven wear or damage to the belt.
Pulleys
Pulleys are used to drive the belt, provide tension to the system, and help change the direction of the belt in looped systems. The alignment of pulleys is critical in maintaining proper conveyor belt roller alignment. Misaligned pulleys can exert uneven forces on the conveyor belt, leading to misalignment and potential operational issues.
Conveyor Belt
The conveyor belt is the carrying medium of a belt conveyor system. It needs to be tensioned properly and tracked correctly for optimal performance. The integrity and alignment of the conveyor belt are influenced by the alignment of the rollers and pulleys. Proper tension and alignment minimize the risk of belt slippage, reduce wear on the system, and ensure efficient transfer of the load.
Roles of Each Component in Maintaining Alignment
Each component of the conveyor belt system must work harmoniously to maintain effective conveyor belt roller alignment. Rollers should be regularly checked for wear and rotation, pulleys should be inspected for secure mounting and correct alignment, and the conveyor belt itself should be routinely examined for signs of conveyor belt uneven wear or damage. These practices are essential to prevent misalignment and ensure the longevity and efficiency of conveyor belt systems.
Tools Required for Conveyor Belt Roller Alignment
Laser Alignment Tool:
- Precision Alignment: A laser alignment tool provides precise measurements to ensure rollers and pulleys are correctly aligned.
- Ease of Use: Laser tools are user-friendly and offer accurate, real-time data.
Spirit Level:
- Leveling: Ensures that rollers and the conveyor frame are level and aligned horizontally.
String Line or Wire:
- Straightness Check: A string line helps to check the straightness and alignment of rollers along the conveyor length.
Measuring Tape:
- Distance Measurement: Measures distances between rollers and ensures uniform spacing.
- Checking Alignment: Verifies the alignment of rollers relative to each other and the frame.
Wrenches and Spanners:
- Adjustments: Used for loosening and tightening bolts and nuts to adjust the position of rollers and other components.
- Versatility: Available in various sizes to fit different bolts and nuts on the conveyor system.
Dial Indicator:
- Precision Measurement: Measures the deviation of rollers and pulleys from their intended position with high precision.
- Alignment Verification: Ensures that adjustments are within acceptable tolerance levels.
Plumb Bob:
- Vertical Alignment: Ensures that vertical components, such as the sides of the conveyor frame, are perfectly vertical.
Caliper:
- Accurate Measurement: Measures the diameter of rollers and the distance between critical points for precise alignment.
Torque Wrench:
- Proper Tightening: Ensures that bolts and nuts are tightened to the manufacturer’s recommended torque specifications, preventing over-tightening or under-tightening.
Marker or Chalk:
- Marking Points: Marks reference points on the conveyor frame and rollers to assist with alignment.
- Temporary Marks: Helps in tracking adjustments and verifying alignment over time.
Alignment Brackets and Clamps:
- Holding Rollers: Holds rollers in place during the alignment process, allowing for hands-free adjustments.
- Temporary Fixing: Provides temporary support to keep components in position while adjustments are made.
- Handheld Mirror:
- Inspection Tool: Allows for viewing and inspecting hard-to-see areas during the alignment process.
By using these tools , conveyor belt roller alignment can be achieved accurately, enhancing the efficiency and longevity of the conveyor system.
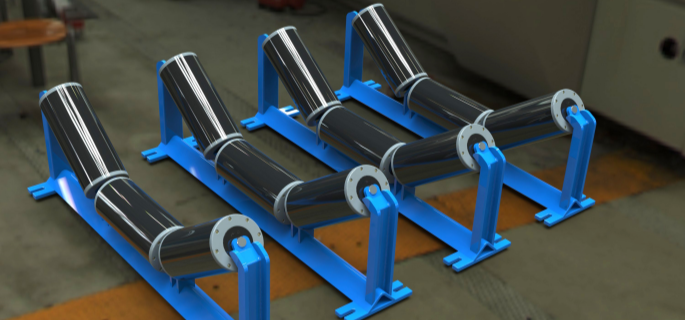
Conveyor Belt Roller Alignment Procedures
Proper conveyor belt roller alignment is essential to maintaining efficient and smooth conveyor operations. Here is a step-by-step guide to aligning a conveyor belt effectively. For further details and visual instructions, refer to a comprehensive “conveyor belt alignment procedure PDF.”
Step-by-Step Guide to Properly Align a Conveyor Belt
- Preparation and Safety Checks
Before starting the alignment process, ensure the conveyor system is turned off and locked out according to safety procedures. Check the belt for any damage and remove obstructions. - Initial Belt Centering
Place the belt in the approximate center of the conveyor structure. This can be done visually or using marking tools to ensure that the belt is centered relative to the frame. - Inspect Conveyor Rollers
Inspect all conveyor rollers to ensure they are positioned correctly and are functioning properly. Replace or repair any defective rollers to prevent alignment issues. - Adjust the Drive Pulley
The drive pulley significantly influences conveyor belt roller alignment. Make small adjustments to the drive pulley to center the belt. Use a level or square to ensure the pulley is perpendicular to the belt path. - Tension the Belt
Apply appropriate tension to the conveyor belt according to the manufacturer’s recommendations. A tension that is too loose or too tight can cause alignment problems. - Adjust the Tail Pulley
Similar to the drive pulley, the tail pulley should be adjusted to ensure the belt is centered. Ensure the pulley is square to the conveyor frame and adjust as needed. - Adjust Idler Rollers
Check the alignment of the idler rollers. They play a crucial role in maintaining proper conveyor belt roller alignment. If necessary, adjust the rollers so that they guide the belt centrally. - Run the Conveyor System
Turn on the conveyor system and let it run. Observe how the belt tracks and makes further adjustments to the pulleys or rollers as needed. - Continuous Monitoring
Even after alignment, continuously monitor the belt’s position and the overall system. Regular inspections will help detect and resolve misalignment issues early. - Document and Review
Document the alignment steps taken and review the results to refine the process in future alignments. For detailed reference, consult a “conveyor belt alignment procedure PDF” to ensure compliance with best practices and manufacturer guidelines.
By following these steps and paying close attention to conveyor belt roller alignment, you can ensure an efficient, long-lasting conveyor system that minimizes operational disruptions and maintenance costs.
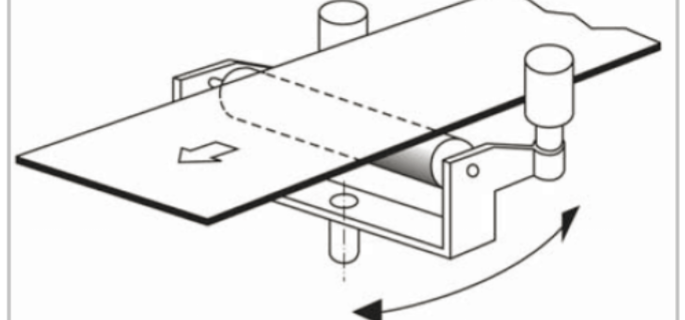
Diagrams and Visual Aids: Conveyor Belt Roller Alignment
A conveyor belt roller alignment diagram provides a visual representation of how rollers should be positioned within a conveyor belt system to ensure proper alignment. It shows the layout of each roller, their distance from one another, and their angles relative to the conveyor belt. This diagram also typically indicates the role of each roller, whether it’s carrying or guiding the belt. Understanding this diagram is crucial because it helps identify the correct positioning of rollers to achieve effective conveyor belt roller alignment.
Conveyor Belt Tracking Diagram
A “conveyor belt tracking diagram” illustrates the ideal belt path and shows how the belt should align with the rollers and pulleys. It often includes information on tracking adjustments, such as inclined rollers or crowned pulleys, that can be used to guide the belt towards the center of the system. This diagram is particularly useful when troubleshooting tracking issues because it provides visual cues on how to correct belt drift and maintain alignment.
How These Diagrams Assist in Alignment Tasks
- Visualizing Component Placement
Diagrams help visualize the correct placement and orientation of rollers, pulleys, and other key components. This is essential for accurate conveyor belt roller alignment as it ensures that each component is positioned to minimize tracking errors. - Troubleshooting Misalignment Issues
By comparing the conveyor setup with alignment diagrams, operators can identify deviations that may be causing the belt to track off-center. The diagrams often provide guidance on adjusting rollers and pulleys to correct these deviations. - Implementing Best Practices for Alignment
Alignment diagrams include best practices for adjusting rollers and pulleys. For instance, inclined rollers can guide the belt back to the center, while crowned pulleys can help maintain straight tracking. These visual aids guide operators in implementing the most effective conveyor belt roller alignment measures. - Training and Standardization
Diagrams serve as valuable training tools, helping new operators understand the intricacies of conveyor belt roller alignment. They also promote standardization across different conveyor belt systems by providing a consistent reference for alignment practices.
By utilizing conveyor belt roller alignment diagrams and conveyor belt tracking diagrams, operators can better understand their conveyor systems, swiftly diagnose alignment issues, and apply effective solutions to ensure optimal belt tracking and system efficiency.
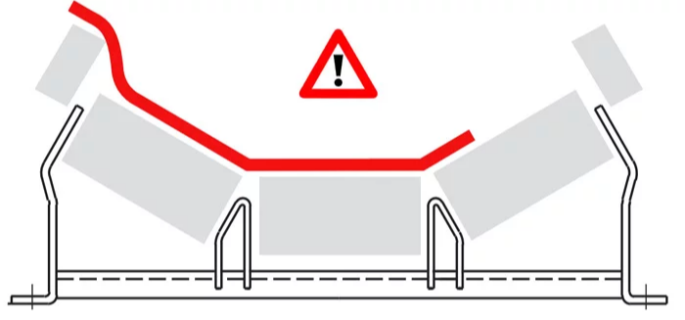
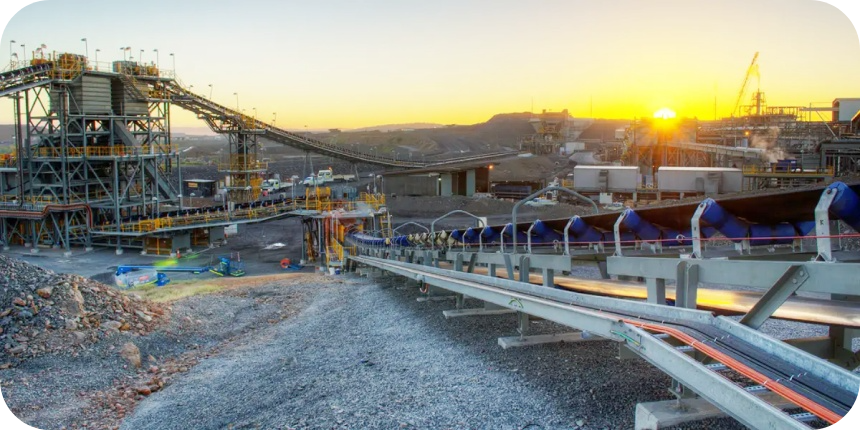
Practical Tips for Conveyor Belt Tracking: Conveyor Belt Roller Alignment
Adjusting a Conveyor Belt to Run Straight
Achieving proper conveyor belt roller alignment is essential to ensure your belt runs straight. Here are some practical steps to adjust a conveyor belt:
- Check and Adjust Roller Alignment
Begin by inspecting the rollers along the conveyor to ensure they are correctly aligned. Rollers should be perpendicular to the belt’s direction of travel. Use a standard level and measure from multiple points to confirm alignment. - Ensure Even Tension Across the Belt
Uneven tension is a common cause of misalignment. Check the tension on both sides of the conveyor belt using a tension meter to ensure they are equal. Adjust the tensioning devices as needed to balance the tension. - Examine and Adjust the Pulleys
Pulleys should also be aligned with the belt. Any misaligned pulley can pull the belt to one side, causing it to track off-center. Adjust the pulley position so that the belt runs centrally over the pulleys. - Track the Belt at Installation and Regularly Thereafter
When installing a new belt, always track it before it goes into full operation. Make fine adjustments while the belt is running under a light load. Continue to monitor and adjust the belt periodically during regular operation.
Conveyor Belt Tracking Rollers: Function and Adjustment
Conveyor belt tracking rollers play a crucial role in maintaining conveyor belt roller alignment. Here’s how they function and can be adjusted:
- Role of Tracking Rollers
Tracking rollers are designed to influence the path of the conveyor belt gently. These rollers can tilt slightly in response to the belt’s movement, guiding the belt back to the center of the conveyor path. - Adjusting Tracking Rollers
To adjust a tracking roller, first identify the direction in which the belt is misaligned. If the belt is drifting to the left, the left side of the tracking roller should be lowered or the right side raised, prompting the belt to move towards the right. Conversely, adjust the opposite side if the belt drifts to the right. - Regular Monitoring and Maintenance
Regularly check the condition and alignment of tracking rollers as part of your maintenance routine. Ensure that these rollers are not worn out and are free from material build-up, which can affect their function. - Using Self-Aligning Rollers
Consider installing self-aligning rollers, which automatically adjust their position based on the movement of the belt, reducing the need for manual adjustments.
By following these practical tips and understanding the critical role of conveyor belt tracking rollers, you can significantly enhance conveyor belt roller alignment, leading to improved system efficiency and reduced downtime.
Advanced Tracking Solutions of Conveyor Belt Roller Alignment
Advanced tracking solutions offer automated and efficient methods to achieve accurate conveyor belt roller alignment, reducing downtime and manual interventions. These systems employ cutting-edge technology to maintain belt alignment continuously, ensuring consistent and smooth operation.
Overview of Automatic Conveyor Belt Tracking Systems
Automatic conveyor belt tracking systems leverage sensors and automated mechanical components to monitor and adjust belt alignment in real time. Key components include:
- Sensors
Installed along the conveyor belt, sensors continuously monitor the belt’s lateral position. They detect any deviations from the centerline, providing immediate data for corrective actions. - Control Unit
The control unit processes the sensor data and identifies when alignment adjustments are required. It sends commands to the mechanical adjustment components. - Adjustment Mechanisms
These mechanisms, such as motorized pulleys and actuators, automatically adjust the belt’s position by moving specific pulleys or idler rollers. They keep the belt centered according to the control unit’s calculations. - Feedback Loop
The tracking system employs a feedback loop to continuously refine its adjustments. This minimizes belt drift and keeps the system running efficiently.
Benefits of Using Technology to Maintain Conveyor Belt Roller Alignment
- Reduced Manual Interventions
Automated tracking systems minimize the need for manual corrections by maintenance staff, saving time and reducing labor costs. - Enhanced Accuracy
Precision sensors and automated controls ensure more accurate conveyor belt roller alignment than traditional manual adjustments, improving overall belt performance. - Increased Efficiency
Real-time corrections mean the conveyor belt remains properly aligned, reducing material spillage and increasing productivity. - Reduced Wear and Tear
By maintaining consistent alignment, automatic systems extend the lifespan of belts, rollers, and other conveyor components, ultimately lowering maintenance expenses. - Safety Improvement
With fewer manual interventions required, automated systems contribute to a safer working environment by reducing the risk of accidents during adjustment procedures. - Decreased Downtime
Fewer unplanned shutdowns occur due to misalignment, as tracking systems detect and correct issues early, ensuring smooth operation. - Optimized Energy Consumption
Proper alignment decreases friction and resistance, resulting in optimized energy consumption for conveyor belt operations.
These advanced tracking solutions are indispensable for maintaining optimal conveyor belt roller alignment. They combine automation with sophisticated monitoring and adjustment technologies, ensuring accurate and consistent belt tracking while reducing human error and improving overall operational efficiency.
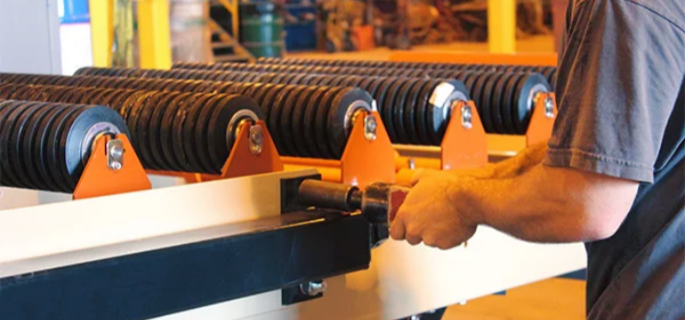
Troubleshooting Common Conveyor Belt Roller Alignment Issues
Proper conveyor belt roller alignment is crucial to the smooth operation of a conveyor system. Misalignment issues can lead to material loss, equipment damage, and production downtime. The table below outlines four common problems and solutions based on “conveyor belt tracking troubleshooting.”
Specific Scenarios and How to Address Them
- Belt Tracking to One Side:
When the conveyor belt persistently shifts to one side, it is often due to a misaligned drive or tail pulley. To address this issue, inspect the pulleys for proper alignment and ensure they are perpendicular to the belt path. Adjust as necessary to maintain correct conveyor belt roller alignment. - Belt Slippage:
Belt slippage occurs when the drive pulley loses grip on the conveyor belt. This often results from insufficient belt tension or buildup of dirt and debris on the pulleys. Increase belt tension within recommended limits, and thoroughly clean the drive pulley. If needed, replace the belt or apply additional grip-enhancing coatings. - Excessive Edge Wear:
Uneven wear along the belt’s edges indicates the belt is rubbing against the conveyor structure. Examine the entire length of the conveyor belt rollers to identify any worn or misaligned components. Adjust or replace conveyor rollers as needed and ensure the belt is properly centered and tensioned. - Material Spillage:
Misalignment, overloading, or uneven loading can cause material spillage. Adjust the belt’s load to be more centered and reduce conveyor speed if necessary to maintain stability. Additionally, check skirtboards and transfer points for alignment and ensure proper sealing to contain materials.
By following these troubleshooting steps and employing preventative maintenance, conveyor belt roller alignment issues can be quickly identified and resolved. For comprehensive guidance, consult a “conveyor belt tracking troubleshooting” manual.
5 Basic Conveyor Belt Tracking Rules To Follow
Align the Belt Properly:
- Ensure the belt is centered on the conveyor and all components are aligned with the frame. Misalignment can cause tracking issues.
Maintain Correct Tension:
- Proper tensioning is crucial for belt tracking. Too loose or too tight belts can drift off course. Use tensioning devices to achieve the correct tension.
Check and Adjust Idlers:
- Adjust the position of idlers and rollers to guide the belt correctly. Misaligned or skewed idlers can cause the belt to wander.
Regular Inspection and Maintenance:
- Regularly inspect the belt and conveyor components for wear and damage. Promptly replace or repair any faulty parts to ensure smooth operation.
Use Tracking Devices:
- Implement tracking devices such as crowned pulleys, guide rollers, and belt edge guides to help maintain proper belt alignment and prevent drifting.
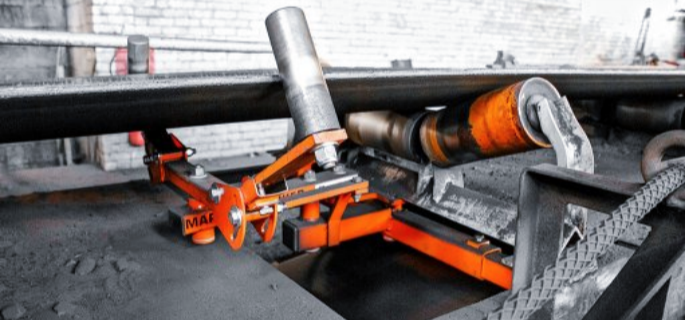
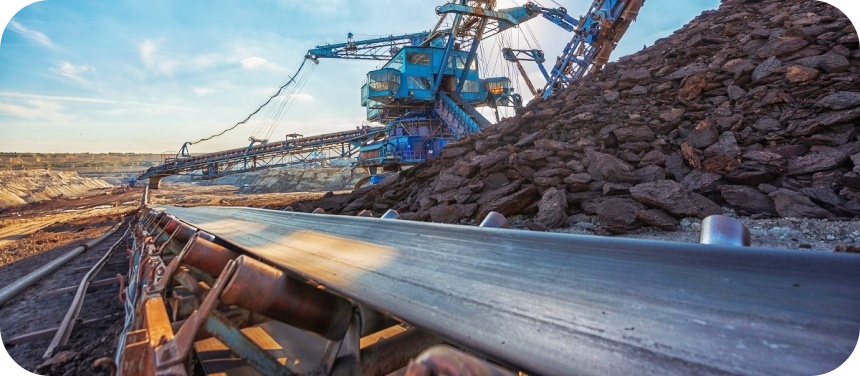
Maintenance and Regular Checks of Conveyor Belt Roller Alignment
Effective maintenance and routine checks are vital for ensuring conveyor belt roller alignment, preventing costly downtime, and reducing repair expenses. By incorporating regular inspections and a structured maintenance schedule, conveyor systems can maintain optimal performance.
Importance of Routine Inspections and Maintenance to Prevent Alignment Issues
- Early Detection of Problems
Regular inspections help identify minor alignment issues before they evolve into significant problems that could cause system shutdowns or damage to the belt and other components. - Prolonged Equipment Life
Proper conveyor belt roller alignment significantly reduces unnecessary wear and tear, extending the operational life of belts, rollers, pulleys, and other conveyor parts. - Reduced Maintenance Costs
By catching and fixing alignment problems early, routine maintenance minimizes the need for expensive emergency repairs and replacement parts. - Increased Productivity
Well-maintained belts run efficiently and with minimal interruptions, ensuring steady production output and reducing material waste due to misalignment. - Safety Compliance
Maintaining conveyor belt roller alignment improves workplace safety, reducing the risk of accidents caused by belt malfunctions or material spillage. - Energy Efficiency
An aligned conveyor belt runs smoothly, requiring less energy to operate and contributing to overall system efficiency.
Tips on Creating a Maintenance Schedule That Includes Checking Alignment
- Develop a Checklist
Create a comprehensive checklist for each inspection, including conveyor belt roller alignment, pulley and idler conditions, belt tension, and material spillage. - Frequency of Checks
Determine appropriate intervals for maintenance checks based on the conveyor’s operational intensity and environmental conditions. For high-use systems, daily or weekly inspections may be required. - Assign Trained Personnel
Ensure that maintenance tasks, particularly alignment adjustments, are performed by trained personnel who understand the system’s specifications and can identify potential issues. - Document Each Inspection
Keep detailed records of each inspection, including identified problems, maintenance performed, and future recommendations. This history will help identify patterns and recurring issues. - Inspect Rollers and Pulleys
Regularly inspect rollers and pulleys for signs of misalignment, wear, or damage. Replace any defective components immediately to maintain proper belt tracking. - Monitor Belt Tension
Improper tension can lead to belt misalignment. Ensure that the belt tension is within manufacturer-recommended limits to avoid slippage and drift. - Clean Components
Accumulation of debris can interfere with conveyor belt roller alignment. Clean rollers, pulleys, and the belt itself to maintain smooth operation. - Check Material Flow
Monitor the flow of materials along the belt to detect spillage or uneven loading. Adjust loading practices and containment systems to minimize misalignment risks. - Test the System
After each maintenance session, run the conveyor to check alignment and ensure proper tracking. Observe belt movement to detect any deviations. - Consult Manufacturer Guidelines
Follow the manufacturer’s recommendations for alignment checks and adjustments, ensuring that maintenance practices align with the specific system’s design and needs.
By implementing these tips in a consistent maintenance schedule, companies can ensure effective conveyor belt roller alignment, maintaining productivity while preventing costly disruptions.
FAQs about Conveyor Belt Roller Alignment
Conveyor belt alignment refers to the proper positioning and alignment of a conveyor belt on its track and rollers, ensuring it runs straight and does not veer off to one side. Proper alignment is crucial for the efficient operation of the conveyor system, as it prevents uneven wear on the belt, reduces the risk of damage to the belt and the conveyor structure, and minimizes downtime due to maintenance and repair. When the conveyor belt is correctly aligned, it will also help in maintaining the consistent flow of materials, reducing spillage, and improving the overall productivity of the conveyor system.
The distance between rollers, also known as roller or idler spacing, in a conveyor system can vary depending on several factors, including the type of materials being transported, the weight of those materials, the conveyor belt width, and the overall design of the conveyor system. Generally, for standard bulk material handling conveyors, carrying idlers are spaced at intervals of 1 to 1.5 meters (3 to 5 feet), while return idlers are spaced at wider intervals of 3 meters (10 feet) or more. However, these distances can be adjusted based on the specific requirements of the conveyor system, including the need to support heavier loads or to accommodate specific material characteristics.
Preventing conveyor belt misalignment involves regular maintenance and checks, ensuring all conveyor components are in good condition and properly aligned. This includes regularly checking and adjusting the tension of the conveyor belt, as improper tension can lead to misalignment. Ensuring that the conveyor frame and idlers are level and square is also crucial, as even minor deviations can cause the belt to track off-course. Cleaning the conveyor belt and components to remove debris and material buildup can prevent uneven wearing and tracking issues. Additionally, installing self-aligning idlers or training idlers can help in automatically correcting the belt’s path as it moves, reducing the risk of misalignment.
Making a conveyor belt track straight requires attention to the alignment and condition of all aspects of the conveyor system. Start by ensuring that the frame of the conveyor is level and square, as any misalignments here can cause the belt to track incorrectly. Adjust the tension of the conveyor belt to the manufacturer’s specifications, as both over-tensioning and under-tensioning can lead to misalignment. Check and align the pulleys and idlers to ensure they are perpendicular to the direction of the belt travel. Consider using self-aligning idlers in areas prone to misalignment. Regularly inspect the belt edges for wear and tear, which can indicate tracking issues, and clean the belt and parts of any material buildup. By addressing these areas, you can significantly improve the likelihood that your conveyor belt will track straight.
Last Updated on July 25, 2024 by Jordan Smith
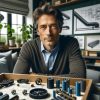
Jordan Smith, a seasoned professional with over 20 years of experience in the conveyor system industry. Jordan’s expertise lies in providing comprehensive solutions for conveyor rollers, belts, and accessories, catering to a wide range of industrial needs. From initial design and configuration to installation and meticulous troubleshooting, Jordan is adept at handling all aspects of conveyor system management. Whether you’re looking to upgrade your production line with efficient conveyor belts, require custom conveyor rollers for specific operations, or need expert advice on selecting the right conveyor accessories for your facility, Jordan is your reliable consultant. For any inquiries or assistance with conveyor system optimization, Jordan is available to share his wealth of knowledge and experience. Feel free to reach out at any time for professional guidance on all matters related to conveyor rollers, belts, and accessories.