Maximizing Efficiency with Conveyor Belt Rubber
In the modern industrial world, conveyor belt rubber plays an significant and omnipresent role. This versatile and essential material underpins operations in numerous industries—from manufacturing to mining, from food processing to agriculture, and more. The prevalence of this crucial component in production lines, assembly systems, and transportation mechanisms around the world serves as a testament to its robustness and functionality.
The secret to the success of conveyor belt rubber lies in its composition and design—custom tailored to withstand diverse working conditions and to ensure seamless material handling. These conveyor belts, when constructed with rubber, offer unparalleled durability and adaptability, attributes that make them integral to any large-scale industrial operation.
Whether you are just beginning to explore the applications of conveyor belt rubber or are a seasoned industry professional, understanding the basics of how this vital material works can provide fresh insights into your operations, boosting efficiency, and promoting the safe and smooth running of your facilities.
The Fundamentals of Conveyor Belt Rubber
Conveyor belt rubber is the foundational material that makes up the conveying solutions pivotal to numerous industries. It is defined by its exceptional tensile strength, flexibility, and resistance to wear and tear, all of which are essential for the continuous operation of conveyor belts. This type of rubber must maintain its integrity under various stressors including pressure, temperature fluctuations, and exposure to chemicals.
The essential characteristics of conveyor belt rubber are largely attributable to its unique composition. Common materials like neoprene bring weather and heat resistance to the table, making conveyor belts suitable for outdoor or high-temperature environments. Nitrile rubber is infused when oil resistance is paramount, particularly in the presence of hydrocarbons. Additionally, SBR rubber is often included for its abrasion resistance and cost-effectiveness, which makes it a standard choice for general-purpose conveyor belt rubber needs.
By combining these materials, conveyor belt rubber is designed to meet the specific demands of each application it serves, ensuring reliability and longevity. This specialized design speaks to both the innovation and the versatility that conveyor belt rubber offers to various sectors in the industrial world.
Exploring Types and Grades of Conveyor Belt Rubber
When engaging in a discussion about conveyor belt rubber, it’s important to acknowledge the range of available variants, each engineered to cater to specific industrial needs. Conveyor belt rubber is not a one-size-fits-all solution; it comes in a variety of grades, each offering unique characteristics that align with distinct purposes.
The most basic form of conveyor belt rubber serves general applications, offering good abrasion resistance and suitable for carrying bulk and packaged products alike. Then we see food-grade conveyor belt rubber, which is specially formulated to comply with stringent hygiene standards in the food processing industry, and heat-resistant rubber for high-temperature operations.
Of particular note is heavy-duty conveyor belt rubber. This specialized variant is designed to deliver seamless performances in harsh and demanding industrial environments. Its construction emphasizes enhanced resilience and durability, specifically when dealing with abrasive materials or intensive mechanical processes.
Therefore, the choice of conveyor belt rubber is contingent on the application’s requirements and the operational environment. By aligning the grade of rubber with the specific demands of an operation, industries can ensure maximum productivity and longevity of their conveyor systems.
Durability and Remarkable Features of Conveyor Belt Rubber
The durability of conveyor belt rubber is a key element that underpins its usage in diverse industries. Durability factors such as abrasion resistance, impact absorption, and longevity are integral to a conveyor system’s performance and return on investment.
Abrasion resistance ensures that conveyor belt rubber can endure long periods of rough contact with various materials, maintaining functionality despite direct wear and tear. Impact absorption is equally important, as it allows the rubber to withstand sudden or heavy loads without significant deformation or damage. Longevity, meanwhile, represents the lifespan of the conveyor belt rubber under optimal maintenance, ensuring its cost-effectiveness over time.
Cloth-inserted rubber adds another layer to these durability factors. This type of conveyor belt rubber includes layers of cloth or fabric within its construction, enhancing stability and form retention. It helps in mitigating stretching and distortion, particularly critical in high-tension applications. Thus, cloth-inserted conveyor belt rubber is specifically ideal for use in scenarios where stability and maintenance of form are paramount.
From this discussion, it becomes clear that the remarkable durability and features of conveyor belt rubber are critical drivers of its ubiquitous presence across diverse industrial environments. Understanding these unique attributes can lead to more informed decisions when selecting and maintaining conveyor belts for individual operational needs.
Strategies for Finding Conveyor Belt Rubber
For those wondering how to locate “conveyor belt rubber near me” or “rubber belting near me,” the first step is to leverage local industrial supply directories and online searches. Such resources can offer immediate insights into nearby suppliers that stock various grades and types of conveyor belt rubber suited to different industrial applications. A quick search online can often yield results not only for vendors but also for reviews and recommendations, ensuring you find a trusted source.
Additionally, tapping into industry networks or participating in forums related to conveyor systems and material handling can prove advantageous. These communities often share insider information on where to find the best deals and products, including conveyor belt rubber.
The option of finding “used conveyor belt rubber for sale” is particularly appealing for operations looking to economize without compromising quality. This can be especially useful for applications that do not require brand-new materials and for businesses that prioritize sustainability. When sourcing used conveyor belt rubber, it’s vital to inspect the material for wear and damage to ascertain its suitability and remaining lifespan. Reputable dealers of used industrial equipment often provide conveyor belt rubber that still has a significant service life ahead.
Regardless of the source, ensuring the conveyor belt rubber is appropriate for the specific industrial application remains key. Adequate research, along with procuring samples or detailed specifications and warranties, can help mitigate the risks associated with sourcing this essential material.
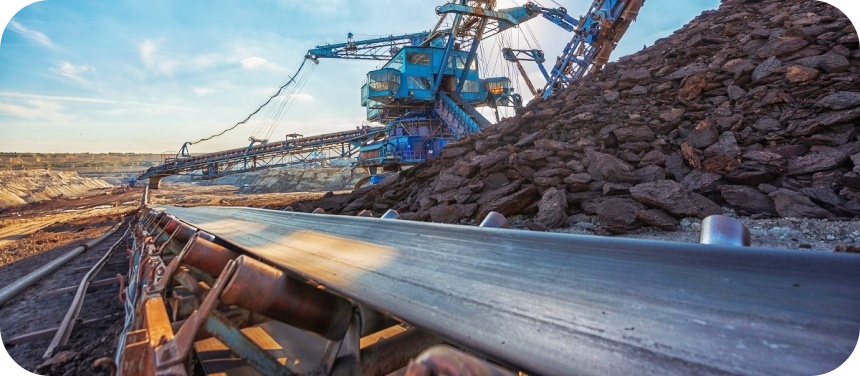
Essential Purchasing Considerations for Conveyor Belt Rubber
When navigating the process of selecting “conveyor belt rubber for sale,” there are several factors that you must take into account to ensure that you make a choice that is not only cost-effective but also conducive to the efficiency and longevity of your operational needs. Understanding these factors can significantly streamline your purchasing process.
One of the primary purchasing considerations should be the specific application or environment in which the conveyor belt rubber will be used. This encompasses assessing the kinds of materials it will transport, the operational temperature range, and whether it will be used indoors or outdoors. Such factors dictate the need for specialized rubber compounds that can withstand particular conditions, such as extreme temperatures, exposure to oils or chemicals, and the wear and tear of carrying sharp or abrasive materials.
Additionally, choosing the right thickness of the conveyor belt rubber, like “1/4 rubber belting,” plays a crucial role in performance and durability. The thickness required largely depends on the application’s demands — thicker belts, for example, offer greater durability and impact resistance but may require more power to operate. In contrast, thinner belts may be more appropriate for lighter-duty applications where flexibility and ease of movement are priorities. The 1/4 inch thickness, specifically, strikes a balance for moderate-duty applications, offering a blend of durability and flexibility that suits a wide range of industrial needs.
Moreover, it’s also essential to consider the belt’s tensile strength, which refers to how much load the belt can handle over time without stretching or breaking. The belt’s material composition—whether it’s natural rubber, synthetic rubber, or a blend of both—will influence its tensile strength, resistance to environmental factors, and ultimately its lifespan.
To navigate the broad spectrum of “conveyor belt rubber for sale,” it may also be beneficial to consult with professionals or suppliers who can provide detailed insights into the types of rubber belting that is best suited for your specific needs. They can offer advice on the best thickness for your application, discuss the advantages of different rubber compounds, and help you find a conveyor belt that meets your operational requirements and budget constraints.
When considering purchasing conveyor belt rubber, emphasizing detailed planning and consultation can vastly improve the suitability and longevity of your chosen conveyor belting solution. By taking the time to understand the unique demands of your operation and the available conveyor belt options, you can ensure that your investment supports your business’s efficiency and growth.
Diverse Industrial Applications of Conveyor Belt Rubber
Conveyor belt rubber is a critical component in various industrial sectors, enabling the seamless and efficient transfer of materials across different points of the production line. Its utility in industry is a testimony to its flexibility, durability, and economic efficiency, making it a ubiquitous presence in manufacturing and processing environments.
In mining and quarrying operations, heavy-duty conveyor belt rubber is employed to transport large volumes of raw materials, often under extreme conditions. These belts are engineered to resist abrasive materials, cuts, and gouges, which ensures that vital resources from minerals to coal are moved safely and consistently with minimal downtime.
In the food processing industry, conveyor belt rubber is used for its advantageous hygienic qualities. These belts often need to comply with stringent food safety standards, being resistant to the proliferation of bacteria and easy to clean. This ensures that everything from fresh produce to packaged goods can be handled and transported without compromising food quality.
In the recycling industry, the tough and resilient nature of conveyor belt rubber becomes vital for sorting and moving waste materials. These belts are designed to withstand sharp objects, heavy loads, and sometimes even the corrosive materials found in electronic waste.
Material handling in logistics and warehousing also benefits significantly from conveyor belt rubber. Parcels, packages, and products of all shapes and sizes are efficiently sorted and distributed, with rubber belts offering the necessary grip and support to ensure items remain stable during transit.
Manufacturing plants use conveyor belt rubber extensively, with its diverse applications seen on assembly lines for electronics, automotive, and consumer goods. The reliability and adaptability of rubber belting mean that parts and products can be moved at variable speeds through different phases of assembly with precision.
The packaging industry relies on conveyor belt rubber to move products through various stages of packaging, where speed and accuracy are particularly important. Rubber belts enable gentle handling to protect the integrity of packaging while maintaining the pace required for high-volume production.
Insight into the efficient transfer of materials afforded by rubber conveyor belts highlights their economic impact on production lines. They facilitate the quick and smooth transition between different stages of manufacturing or processing, reduce manual handling, improve workplace safety, and, ultimately, augment throughput and productivity.
Conveyor belt rubber, with its numerous industrial uses, remains an essential tool, enhancing the operational flow in enterprises, large and small. Its role in effective material transfer cannot be overstated, as it continues to evolve in sophistication to meet the demands of modern industry.
Effective Maintenance and Care for Conveyor Belt Rubber
Maintaining conveyor belt rubber is critical for ensuring the longevity, efficiency, and safety of the conveyor system as a whole. Proper care and maintenance routines can significantly extend the life of conveyor belt rubber, thereby optimizing operational performance and minimizing unnecessary downtime. Here are several key tips and practices for maintaining and extending the life of your conveyor belt rubber.
Regular Inspections and Cleaning: One of the most effective ways to maintain the condition of conveyor belt rubber is through regular inspections. Look for signs of wear, tears, or other damages. Additionally, keeping the belt clean from debris and residues can prevent premature wear and tear. Materials stuck on the belt can embed into the rubber over time, causing damage that can lead to belt failure.
Proper Tensioning: The correct tension is crucial for conveyor belt rubber performance. Too much tension can lead to excessive wear and tear, while too little tension can cause the belt to slip off the pulleys. Regular checks and adjustments to ensure proper tension can help prevent these issues and extend the belt’s lifespan.
Alignment Checks: Misalignment of the conveyor belt can lead to uneven wear, increasing the risk of damage over time. Regularly checking and adjusting the alignment of the conveyor belt and pulleys can help ensure even wear and prolong the lifespan of conveyor belt rubber.
Avoid Overloading: Overloading the conveyor system can put excessive pressure on the conveyor belt rubber, leading to premature wear and possible failure. It’s essential to adhere to the recommended load capacities to maintain the integrity and longevity of the belt.
Temperature Considerations: Extreme temperatures, whether hot or cold, can affect the durability and performance of conveyor belt rubber. When not in use, it’s advisable to store the conveyor belt material in a controlled environment where it’s protected from extreme temperature fluctuations.
Proper Storage of Used Conveyor Belt Material: When conveyor belt rubber is not in use or has been replaced, proper storage is crucial to prevent damage. Roll the belt rubber, avoiding folding or kinking that can strain the material. The storage area should be dry and free from chemicals or oils that can deteriorate the rubber quality over time. Additionally, preventing prolonged exposure to direct sunlight can help in maintaining the elasticity and condition of the rubber.
Handling Repairs Promptly: Addressing minor damages or wear signs promptly can prevent further deterioration. Qualified technicians can assess whether the conveyor belt rubber can be repaired or if it needs replacement, ensuring the safety and efficiency of the conveyor system.
By incorporating these maintenance and care practices, businesses can ensure that their conveyor belt rubber remains in optimal condition, contributing to efficient operations and reducing the likelihood of costly downtime. Regular attention and care, along with understanding and catering to the specific needs of the conveyor belt rubber based on its application, are pivotal in maximizing the return on investment for conveyor systems.
Customization and Specifications for Conveyor Belt Rubber
Customization and standardization form the cornerstone of successful conveyor belt applications in various industries. In an increasingly bespoke industry landscape, tailored solutions are essential, and the availability of custom specifications for conveyor belt rubber has helped different industrial sectors meet their nuanced requirements.
One of the key customizable aspects of conveyor belt rubber revolves around dimensions. Here, both width and thickness can be custom-tailored to specific operational needs. For instance, industries such as mining or recycling often require wider and thicker belts to accommodate heavy-duty material handling, while lighter applications like food processing may benefit from thinner, narrower belts, which can navigate tighter spaces and smaller loads.
The tensile strength of the conveyor belt rubber is another important specification that can be customized. Depending on the weight and type of materials being transported, rubber belts with higher or lower tensile strength may be necessary to ensure longevity and stability. Customizing tensile strength ensures your belt is not over or under-engineered for your specific application.
Rubber compound customization is another pivotal aspect of conveyor belt rubber specifications. Depending on the working environment and the type of materials being transported, different compounds like natural rubber, neoprene, EPDM, or silicone may be necessary. For instances, exposure to heat, oil, abrasion, or chemicals may necessitate a specific compound for optimal performance and long-lasting durability.
One of the most significant advantages of customizing conveyor belt rubber is the opportunity for clients to choose between cut lengths or continuous rolls. Particularly for large projects, continuous roll availability can be a game-changer. Projects that require long, seamless lengths of belting, such as airport baggage handling systems or long-distance mining conveyors, can benefit significantly from continuous rolls. This eliminates the need for numerous splices, which could potentially weaken the belt’s overall strength and increase the risk of operational interruptions due to breakdowns.
Moreover, the flexibility of continuous roll availability also means that users only need to purchase the exact amount of conveyor belt rubber that they need, reducing wastage and enhancing cost-effectiveness.
Conveyor belt rubber, when customized and specified to suit individual business needs, brings forth an exceptional level of efficiency and performance, aptly catering to the unique demands of various industrial applications. This level of customization, paired with the convenience of continuous roll availability for larger projects, accentuates the pivotal role that conveyor belt rubber plays in maintaining operational fluidity and net operational success.
Environmental and Economic Aspects of Conveyor Belt Rubber
The dialogue on sustainable industrial practices has intensified, with a significant focus on the reuse and recycling of materials. Within this context, the environmental and economic aspects of conveyor belt rubber, particularly regarding the sale and use of scrap and used materials, have become increasingly pertinent.
An emerging trend is the purchasing of “scrap rubber conveyor belt for sale near me.” This practice holds considerable economic benefits for businesses. By opting for scrap conveyor belt rubber, companies can significantly reduce their operational costs. These materials, often available at a fraction of the cost of new belt rubber, can still offer considerable service life. This cost-effectiveness doesn’t just reduce direct purchasing expenses but can also contribute to broader cost-saving strategies within the company’s operational dynamics.
From an environmental perspective, reusing “used conveyor belt material” is a paramount practice that aligns with global sustainability goals. The manufacturing process of fresh conveyor belt rubber entails substantial energy use and can result in significant carbon dioxide emissions. By repurposing used conveyor belt materials, companies contribute to reducing these environmental impacts. Reuse not only lessens the demand for new rubber production but also addresses the pressing issue of waste management. Given the durable nature of conveyor belt rubber, discarded materials can occupy landfill space for an extended period, adding to environmental degradation problems.
The repurposing of used conveyor belt rubber also opens pathways for innovative applications beyond their original intent. Used conveyor belt material has found a second life in various sectors, including agriculture, for lining feed troughs or as mudflaps; in construction, as walkways or barrier materials; and in sports facilities, as flooring for gyms or shooting ranges. This versatility not only underscores the economic value of used materials but also their contribution to a circular economy, where the lifecycle of products is extended to maximum lengths.
Moreover, engaging in the practice of buying “scrap rubber conveyor belt for sale near me” or reusing “used conveyor belt material” resonates with corporate social responsibility (CSR) strategies. Companies that actively participate in sustainable practices gain enhanced reputations among consumers, who are increasingly environmentally conscious. This can translate into competitive advantage in markets where sustainability becomes a deciding factor in consumer choices.
The environmental and economic aspects of conveyor belt rubber emphasize the importance of integrating sustainability into business practices. The judicious reuse and repurposing of conveyor belt materials not only foster economic benefits by reducing costs but also contribute significantly to environmental conservation efforts. As industries move towards more sustainable operations, practices like these underscore the interconnectedness of economic and environmental well-being.
Complete the form to receive expert advice on the best conveyor belt for you.
FAQs about Conveyor Belt Rubber
The type of rubber used in conveyor belts varies, depending on the specific application and environmental conditions under which the belt will operate. Commonly, Natural Rubber (NR) and Synthetic Rubbers like Styrene Butadiene Rubber (SBR), Polyurethane (PU), Neoprene (CR), and Nitrile Rubber (NBR) are used. Natural Rubber is prized for its superior elasticity and tensile strength, making it ideal for general-purpose conveyors. SBR is widely used for its good abrasion resistance and ability to withstand varying temperatures, making it suitable for handling abrasive materials. Neoprene and Nitrile Rubber offer excellent oil and chemical resistance, fitting for industries where oils, fats, or other chemicals are present. Each rubber type provides unique benefits, including wear resistance, temperature tolerance, and chemical compatibility, informing their use in diverse industrial applications to optimize the conveyor belt’s performance and longevity.
The best way to cut a rubber conveyor belt involves using the proper tools and techniques to ensure a clean, straight cut without compromising the belt’s structure or strength. A common and effective method is using a utility knife with a sharp blade or a heavy-duty cutting tool specifically designed for cutting thick rubber material. For straight cuts, it’s advisable to use a straight edge or a carpenter’s square as a guide to achieve a precise line. Before cutting, marking the cutting line with chalk or a marker can help ensure accuracy. Safety is paramount, so wearing appropriate personal protective equipment, like gloves and eye protection, is crucial. For thicker or reinforced belts, power tools such as circular saws fitted with blades designed to cut rubber might be necessary. In these instances, ensuring stability of the belt and using clamps to hold it in place can prevent shifts during cutting, ensuring a clean, precise cut.
Rubber belting is primarily made of either natural rubber, extracted from latex found in rubber trees, or synthetic rubber, which is a man-made material produced through polymerization of various monomers. The base rubber material can be blended with other components such as carbon black, reinforcing fabrics, and different chemical additives to enhance specific properties like tensile strength, wear resistance, and thermal stability. The reinforcing fabrics, often made from materials like polyester, nylon, or Kevlar, are incorporated into the rubber in layers, known as plies, to provide additional strength and durability. This composite material is then vulcanized, a chemical process that uses heat and pressure to crosslink the rubber molecules, creating a strong, elastic, and durable conveyor belt. The specific composition and construction of rubber belting are carefully selected based on the intended use, operating environment, and desired properties of the final product.
The weight of a rubber conveyor belt depends on its dimensions, including length, width, and thickness, as well as the type and amount of rubber and reinforcing materials used in its construction. Generally, conveyor belts are sold by the square meter or square foot, and their weight can vary significantly. For example, a standard conveyor belt for general use might weigh around 10 kilograms per square meter (approximately 2 pounds per square foot). Heavy-duty belts with reinforced materials for industrial applications can weigh much more, sometimes exceeding 30 kilograms per square meter (over 6 pounds per square foot). Calculating the total weight of a conveyor belt involves multiplying the area of the belt by its weight per unit area. It’s crucial for operational planning, as the weight impacts the motor’s power requirements and the support structure’s specifications needed to carry the loaded belt.
Last Updated on August 2, 2024 by Jordan Smith
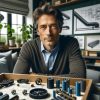
Jordan Smith, a seasoned professional with over 20 years of experience in the conveyor system industry. Jordan’s expertise lies in providing comprehensive solutions for conveyor rollers, belts, and accessories, catering to a wide range of industrial needs. From initial design and configuration to installation and meticulous troubleshooting, Jordan is adept at handling all aspects of conveyor system management. Whether you’re looking to upgrade your production line with efficient conveyor belts, require custom conveyor rollers for specific operations, or need expert advice on selecting the right conveyor accessories for your facility, Jordan is your reliable consultant. For any inquiries or assistance with conveyor system optimization, Jordan is available to share his wealth of knowledge and experience. Feel free to reach out at any time for professional guidance on all matters related to conveyor rollers, belts, and accessories.