Conveyor Belt Rubber Bands: Types and Uses Explained
Conveyor belt rubber bands are a fundamental component in the mechanics of modern industry, playing a pivotal role in the seamless operation of conveyor systems across various sectors. These bands, which form the moving surface of conveyor systems, are crucial for transporting materials efficiently and safely from one point to another. Selecting the right type of conveyor belt rubber band is essential for ensuring optimal performance and longevity of the conveyor system. The appropriate choice depends on specific operational demands such as load size, environmental conditions, and the desired speed of the conveyor, highlighting the significance of understanding the various types available to achieve maximum efficiency and reduce downtime in industrial operations.
What are Conveyor Belt Rubber Bands
Conveyor belt rubber bands are specialized flexible loops used in conveyor systems to facilitate the transportation of materials across various distances and configurations within industrial settings. These bands are critical to the efficiency and functionality of conveyor systems, playing a pivotal role in numerous industries such as manufacturing, packaging, and distribution.
Definition and Basic Description
Conveyor belt rubber bands, often simply referred to as conveyor belts, are continuous loops made from durable, flexible materials that are capable of moving goods and materials from one point to another through a series of pulleys or rollers. These bands are typically mounted on a series of rollers and powered by motors, allowing them to carry heavy or bulky materials along predetermined paths with minimal human intervention. Their design and material composition allow for a variety of applications, ranging from the simple transport of boxed goods in a warehouse to the complex movement of raw materials in a mining operation.
Primary Materials and Their Benefits
The primary materials used in the manufacture of conveyor belt rubber bands are polyurethane and rubber, each offering distinct benefits depending on the application.
- Rubber: Rubber is the most common material for conveyor belts. Its natural elasticity and ability to be formulated in various ways make it incredibly versatile. Rubber conveyor belts can be engineered to provide high resistance to wear, tearing, and abrasion. They are particularly well-suited for industries where durability and grip are essential, such as in bulk handling applications or when transporting goods in slippery or rough environments.
- Polyurethane: Known for its excellent properties such as resistance to chemicals, oil, and abrasion, polyurethane is often used in food processing, pharmaceutical, and packaging industries where cleanliness and minimal maintenance are crucial. Unlike rubber, polyurethane does not degrade under exposure to oils, greases, and many chemicals, making it ideal for environments where such exposures are common. Additionally, polyurethane belts are highly flexible, durable, and can be made transparent, which is beneficial for certain manufacturing and processing applications where visual inspection of goods is necessary.
Understanding the properties and benefits of these materials helps in selecting the right type of conveyor belt rubber bands for specific applications, ensuring not only the longevity of the belt system but also the efficiency and safety of the operations they support. These conveyor belt rubber bands are fundamental components that significantly impact the operational capabilities of industries worldwide.
Types of Conveyor Belt Rubber Bands
Conveyor belt rubber bands are integral components in various industrial and manufacturing processes, where they serve as essential mechanisms for moving items efficiently across facilities. Understanding the different types of conveyor belt rubber bands is crucial for selecting the right one for specific applications.
Standard Sizes
Conveyor belt rubber bands come in a multitude of standard sizes and dimensions tailored to suit a wide array of machinery and tasks. The length, width, and thickness of these rubber bands can vary significantly, depending on their intended use. For instance, smaller bands might be used in light applications such as packaging pharmaceuticals or electronics, while larger bands are employed in industries that require the movement of heavier items such as automotive parts or large volumes of agricultural products. The internal structure of these bands often includes layers of fabric or metal, which provide the necessary strength and flexibility.
Heavy Duty Types
Heavy duty conveyor belt rubber bands are designed to withstand the more rigorous demands of industrial environments. These types of rubber bands are typically thicker and more durable than their standard counterparts. They are often reinforced with materials like steel cords or woven meshes to enhance their tensile strength and wear resistance. This reinforcement helps prevent stretching and sagging under heavy loads, making heavy duty conveyor belt rubber bands ideal for industries such as mining, construction, and metal processing, where they must cope with sharp, heavy, or otherwise challenging materials that might easily damage lesser belts. These bands are not only more robust but also designed to resist adverse environmental conditions like extreme temperatures, corrosive substances, and high levels of moisture.
The diversity in the types of conveyor belt rubber bands ensures that there is a suitable option for virtually any industrial task, making them invaluable tools in the modern industrial landscape. Whether the requirement is for light-duty tasks or heavy-duty operations, understanding the specific properties and capabilities of each type of conveyor belt rubber band can significantly impact operational efficiency and safety.
Key Manufacturers of Conveyor Belt Rubber Bands
When it comes to the production of conveyor belt rubber bands, selecting the right manufacturer is crucial for ensuring high-quality products, reliable customer service, and suitable customization options. Below is a detailed overview of the leading manufacturers and insights on choosing the best supplier for your needs.
Leading Manufacturers of Conveyor Belt Rubber Bands
- Dura-Belt, Inc. – Known for their innovation in high-performance urethane belting, Dura-Belt specializes in durable, long-lasting conveyor belt rubber bands that are used across various industries.
- ContiTech AG – A part of Continental AG, this company offers a wide range of rubber and plastic products, including conveyor belts that are known for their robustness and versatility.
- Fenner Group – This UK-based manufacturer is renowned for their precision-made conveyor belts and rubber products designed for critical applications across multiple sectors.
- Bridgestone Corporation – As one of the largest manufacturers of rubber products, Bridgestone provides highly engineered and efficient conveyor belt systems that are tailored to meet specific industrial needs.
- Habasit – Known for their comprehensive range of conveyor and processing belts, Habasit’s products are crafted to enhance performance and reliability in automation.
- Ammeraal Beltech – This global leader offers a full line of high-quality conveyor belting solutions, including customization options for specific operational requirements.
Insights on Choosing the Right Manufacturer for Conveyor Belt Rubber Bands
- Product Quality – Assess the durability and performance of the conveyor belts. High-quality rubber bands will have better wear resistance and are likely to offer longer service life.
- Customer Service – Consider manufacturers that provide excellent customer service, including support with installation, troubleshooting, and maintenance advice.
- Customization Options – Ensure the manufacturer can tailor conveyor belt specifications to match your application needs. This includes options for different sizes, thicknesses, and resistance levels.
- Technical Expertise – Look for manufacturers with a strong technical background and proven expertise in your industry. This can significantly impact the efficiency and suitability of the conveyor system.
- Innovative Capabilities – Choose a supplier that invests in research and development to stay ahead with the latest technologies and materials in conveyor belt production.
- Supply Chain Reliability – Evaluate the manufacturer’s ability to consistently deliver products on time. A reliable supply chain is critical for maintaining uninterrupted operations.
- Certifications and Standards – Check for relevant industry certifications and adherence to international quality standards, which are indicative of the manufacturer’s commitment to excellence.
- Cost-Effectiveness – While quality should not be compromised, consider the overall cost-effectiveness of the conveyor belt rubber bands offered by the manufacturer. This includes looking at long-term operation and maintenance costs.
By carefully evaluating these factors, you can select a conveyor belt rubber band manufacturer that not only meets but exceeds your operational requirements. The right partnership will contribute to the efficiency and success of your conveyor system projects.
Buying Guide for Conveyor Belt Rubber Bands
Selecting the right conveyor belt rubber bands is essential for optimizing the performance and longevity of your conveyor systems. This buying guide offers detailed tips on purchasing conveyor belt rubber bands, highlighting what to look for in terms of quality and performance, as well as discussing the various purchasing options available, including online platforms and direct purchases from manufacturers.
Tips on Purchasing Conveyor Belt Rubber Bands
- Material Quality: Ensure that the rubber bands are made from high-grade materials that offer resistance to wear and tear, temperature, and chemicals.
- Band Strength: Check the tensile strength of the rubber bands to make sure they can handle the required load without stretching excessively.
- Flexibility and Elasticity: Look for rubber bands that maintain flexibility and elasticity under continuous use, which is crucial for efficient operation.
- Dimensional Accuracy: Accurate sizing is critical. Verify the thickness, width, and length to ensure they meet your specific requirements.
- Surface Texture: Depending on your application, consider whether a smooth or textured surface is more appropriate for optimal grip and movement of materials.
- Heat Resistance: For applications involving high temperatures, ensure the rubber bands are capable of withstanding the heat without degrading.
- Oil and Grease Resistance: Some environments may expose the bands to oils or grease, which can affect performance unless the material is resistant.
- UV Resistance: If the conveyor system is exposed to sunlight, UV-resistant rubber bands are essential to prevent deterioration.
- Certifications: Look for products that come with certifications or meet industry standards, which can be a reliable indicator of quality.
- Manufacturer Reputation: Research the manufacturer’s reputation for consistency in quality and reliability in delivery.
- Warranty and Support: Consider manufacturers that offer warranties and good customer support, which can be invaluable in case of any issues.
- Price Comparison: Compare prices from various suppliers to ensure you are getting the best deal, but always consider the total cost of ownership, including maintenance and potential downtime.
Availability of Conveyor Belt Rubber Bands
Conveyor belt rubber bands are readily available both online and directly from manufacturers. Purchasing directly from manufacturers often allows for greater customization and potential cost savings on bulk orders. Meanwhile, buying online can provide the convenience of quick comparisons and often access to a broader range of products.
Online Platforms
Many industrial supply websites and specialized online stores offer a variety of conveyor belt rubber bands. These platforms usually provide detailed product specifications, user reviews, and sometimes live chat support to help you make an informed decision.
Direct from Manufacturers
Buying directly from manufacturers is advisable when specific customizations are needed or when looking to establish a long-term supply agreement. Direct purchases can also facilitate better customer service, detailed product knowledge, and sometimes, more competitive pricing.
By following these guidelines and considering both purchasing avenues, you can effectively source conveyor belt rubber bands that meet the specific needs of your operation, ensuring both efficiency and durability in your conveyor system setups.
Innovative Uses and Tricks for Conveyor Belt Rubber Bands
Conveyor belt rubber bands are not just essential components for transmitting power and moving goods; they can also be employed in numerous innovative ways to enhance the efficiency and functionality of conveyor systems. Below, we explore various tricks and roles these versatile bands can play, including specific uses for rubber band belt tricks and the roles of drive bands.
Rubber Band Belt Trick: Enhancing Efficiency with Conveyor Belt Rubber Bands
- Variable Speed Adjustments: By using conveyor belt rubber bands of different thicknesses and elasticities, you can create adjustable-speed conveyor sections to handle different types of materials more effectively.
- Quick Splicing: Implement quick splicing techniques with rubber bands to minimize downtime during belt maintenance or replacement.
- Anti-Slip Applications: Apply textured conveyor belt rubber bands in areas where slipperiness is an issue, enhancing grip and reducing material slippage.
- Energy Savings: Employ highly elastic rubber bands to reduce the energy required to start and run the conveyor, thanks to their natural ability to store and release energy efficiently.
- Noise Reduction: Use specially designed, soft rubber bands to decrease operational noise, which is particularly beneficial in noise-sensitive environments.
- Shock Absorption: Integrate conveyor belt rubber bands that act as shock absorbers to protect delicate materials from damage during transport.
- Incremental Movement: Utilize the flexibility of rubber bands to achieve precise incremental movement in applications requiring high accuracy, such as assembly lines.
- Weight Distribution: Employ wider and more resilient rubber bands in sections of the conveyor that handle heavier loads to improve weight distribution and reduce wear.
- Enhanced Traction: Coat rubber bands with materials that enhance traction to prevent product or material slipping, especially in steep or inclined conveyor sections.
Conveyor Drive Bands: Roles in Conveyor System Efficiency
- Power Transmission: Drive bands effectively transmit power from the motor to the conveyor mechanism, optimizing energy use and reducing mechanical stress.
- Speed Control: By selecting drive bands with specific elasticity, the speed of the conveyor can be finely tuned for different operational requirements.
- Reduced Maintenance: Using durable and well-designed rubber bands decreases the frequency and cost of maintenance.
- Synchronization: Employ rubber bands to synchronize multiple conveyor sections within an integrated system, ensuring smooth and coordinated operations.
- Load Balancing: Drive bands can help distribute the operational load evenly across the conveyor system, prolonging the life of other mechanical components.
- Improved Alignment: High-quality rubber bands ensure better alignment of the conveyor belt, which reduces material spillage and misalignment-related downtime.
- Temperature Resistance: Utilize rubber bands that are designed to withstand extreme temperatures, either hot or cold, which is critical in specific industrial environments.
- Versatility in Applications: Rubber bands are adaptable to different types of conveyors, whether they are flat, incline, or even spiral conveyors.
- Customization: Rubber drive bands can be custom-made to meet specific operational needs, such as varying widths and thicknesses tailored to different loads and speeds.
- Reduced Vibrations: Using elastic conveyor belt rubber bands helps dampen vibrations, which can extend the lifespan of the conveyor system and improve the safety and comfort of the working environment.
By leveraging these innovative uses and tricks for conveyor belt rubber bands, businesses can significantly enhance the performance, efficiency, and longevity of their conveyor systems.
Specialized Applications of Conveyor Belt Rubber Bands
Conveyor belt rubber bands are not just versatile in their basic form; they also excel in specialized applications, particularly when materials like polyurethane are used, or when they are adapted into specific forms such as lineshaft conveyor drive bands. Here we explore the benefits of these specialized applications, highlighting how they enhance performance, durability, and maintenance efficiency.
Polyurethane Conveyor Belt Rubber Bands
Polyurethane conveyor belt rubber bands offer several advantages over traditional rubber, making them a preferred choice in various industrial environments:
- Superior Durability: Polyurethane is exceptionally resistant to abrasion, cuts, and tears, significantly extending the lifespan of conveyor belts even in the most demanding applications.
- Resistance to Chemicals: Unlike traditional rubber, polyurethane is highly resistant to many chemicals, oils, and solvents, making it ideal for use in chemical processing plants or places where the conveyor belt may come into contact with aggressive substances.
- Better Hygiene: Polyurethane is non-porous and can be manufactured to be antimicrobial, which prevents the growth of bacteria and mold. This makes it particularly suitable for food processing and pharmaceutical industries.
- Reduced Maintenance: The resilience and long-lasting nature of polyurethane reduce the need for frequent replacements and maintenance checks, thereby lowering downtime and maintenance costs.
- Enhanced Load Capacity: Polyurethane belts can handle heavier loads compared to traditional rubber, thanks to their better tensile strength and tear resistance.
- Improved Precision: These belts can be engineered to very tight tolerances, which is crucial for precise applications such as those in the electronics manufacturing industry.
- Temperature Versatility: Polyurethane performs well under a broader range of temperatures and is suitable for applications ranging from freezing environments to high-heat settings.
- Energy Efficiency: Due to their excellent elasticity, polyurethane belts can help reduce the energy consumption of conveyor systems by requiring less force to move and maintain speed.
Lineshaft Conveyor Drive Bands
Lineshaft conveyor drive bands are another specialized application of conveyor belt rubber bands, specifically designed for lineshaft conveyors which are used extensively in distribution centers, packaging industries, and assembly operations.
Specific Use in Conveyor Systems:
Lineshaft conveyor drive bands connect the drive shaft to the rollers, transmitting the rotational force necessary to move goods along the conveyor. These bands are critical for the smooth and efficient operation of the entire system.
Reasons for Preference:
- Flexibility: These bands are highly flexible, allowing them to be used in systems that require complex routing and tight turns.
- Durability: Made from resilient materials, lineshaft drive bands can withstand the constant stress of driving multiple rollers.
- Ease of Installation: They are easier to install and replace than many other conveyor system components, which simplifies maintenance.
- Low Noise Operation: These bands operate quietly, which is beneficial in environments where noise reduction is important.
- Energy Efficiency: They help in reducing the overall energy consumption of the conveyor system by efficiently transmitting power from the shaft to the rollers with minimal energy loss.
- Reduced Wear and Tear: Their design minimizes wear on both the bands themselves and the conveyor rollers, extending the life of all involved components.
- Cost-Effectiveness: Lineshaft drive bands are generally more cost-effective compared to other drive mechanisms, offering a budget-friendly solution without compromising on efficiency.
- Adaptability: They are suitable for lightweight to medium-weight applications, making them versatile for various industries.
Through these specialized applications of conveyor belt rubber bands, industries can achieve more efficient, durable, and cost-effective conveyor system operations. Whether through the use of innovative materials like polyurethane or specialized designs like lineshaft drive bands, the capabilities and performance of conveyor systems can be significantly enhanced.
FAQs about Conveyor Belt Rubber Bands
Rubber conveyor belts are crafted from a variety of rubber materials, each selected for its properties to suit specific industrial requirements and applications. The most commonly used rubber types include natural rubber (NR), styrene-butadiene rubber (SBR), and butadiene rubber (BR). Natural rubber is prized for its excellent tensile strength, elasticity, and resistance to abrasion, making it suitable for general-purpose conveyor belts in industries such as mining and material handling. SBR is favored for its good abrasion resistance and ability to perform well at lower temperatures, which makes it a viable choice for moderate applications. BR, on the other hand, offers superior cold resistance and is used in environments where conveyor belts are exposed to low temperatures. Additionally, nitrile rubber (NBR) is utilized in oil-resistant conveyor belts due to its oil-resistant properties, necessary in the petroleum industry or in applications where belts come into contact with fats and oils.
The manufacturing process of rubber conveyor belts involves several key steps to ensure durability, flexibility, and suitability for various applications. Initially, the design process involves selecting the appropriate type of rubber, fabric (or steel cords for reinforcement), and the belt’s structure. The first step in production is mixing the raw materials – rubber, carbon black, and other chemical additives – to create the rubber compound. This compound is then formed into sheets by a calendering process. Next follows the layering stage, where these rubber sheets are layered with fabric or steel cords to form the belt’s carcass, providing the necessary tensile strength and structural integrity. This assembly then undergoes vulcanization – a heating process under pressure – which causes the rubber to cure and bond to the reinforcement material, creating a unified and robust product. After cooling, the belts are inspected for quality, cut to size, and finished with any necessary fittings or coverings.
A rubber band belt, often made from urethane or other highly elastic materials, is used in a variety of applications that require the transfer or handling of items with precision and care. These belts are particularly beneficial in packaging, manufacturing, and assembly lines where delicate handling or specific positioning is crucial. To use a rubber band belt, it is typically mounted on a series of pulleys or rollers that are powered by a motor. The elasticity of the belt provides a certain degree of tension, which can be adjusted to suit the load and the required grip to move objects effectively. Additionally, rubber band belts are utilized for their ability to absorb vibrations and impacts, protecting the materials being conveyed. It’s important for operators to regularly inspect these belts for wear and tear and maintain proper tension to ensure efficient operation and longevity.
The composition of rubber in conveyor belts is designed to provide specific properties suitable for the belt’s intended use. The base of the rubber composition is typically natural rubber (NR), synthetic rubber like styrene-butadiene rubber (SBR), or a blend of the two, depending upon the requirements for flexibility, strength, and resistance to wear and environmental conditions. To these base rubbers, several additives are mixed to enhance performance characteristics. These additives include carbon black, which increases tensile strength and resistance to abrasion and UV light; antioxidants and antiozonants to prevent aging; plasticizers for improved flexibility; and fillers to enhance properties or reduce cost. Vulcanizing agents are also added to the mix, which, when heated, create cross-links between rubber molecules during the vulcanization process, transforming the rubber to its elastic state and setting the belt’s final properties. This careful formulation ensures that the conveyor belt can withstand the specific loads, wear, and environmental conditions it will face in service.
Last Updated on April 23, 2024 by Jordan Smith
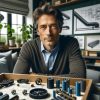
Jordan Smith, a seasoned professional with over 20 years of experience in the conveyor system industry. Jordan’s expertise lies in providing comprehensive solutions for conveyor rollers, belts, and accessories, catering to a wide range of industrial needs. From initial design and configuration to installation and meticulous troubleshooting, Jordan is adept at handling all aspects of conveyor system management. Whether you’re looking to upgrade your production line with efficient conveyor belts, require custom conveyor rollers for specific operations, or need expert advice on selecting the right conveyor accessories for your facility, Jordan is your reliable consultant. For any inquiries or assistance with conveyor system optimization, Jordan is available to share his wealth of knowledge and experience. Feel free to reach out at any time for professional guidance on all matters related to conveyor rollers, belts, and accessories.