Advanced Application Techniques for Conveyor Belt Rubber Glue
Selecting the appropriate type of conveyor belt rubber glue is crucial for effective maintenance and repair of conveyor systems. The right adhesive not only ensures durable bonding of torn or worn sections but also significantly extends the lifespan of the belt. Effective repair with quality rubber glue can restore the structural integrity of conveyor belts, preventing costly downtimes and maintaining continuous, efficient operations. Utilizing the correct type of rubber glue enhances the belt’s resistance to wear and tear under various operational conditions, including exposure to chemicals, temperature variations, and mechanical stress. This guide provides detailed insights into various types of conveyor belt rubber glues, their applications, and how to select and apply them correctly to achieve optimal performance and durability of conveyor systems.
Types of Conveyor Belt Rubber Glue
The choice of the right conveyor belt rubber glue is crucial for effective repairs and maintenance. Different types of glues are used depending on the material of the conveyor belt and the specific needs of the application.
General Purpose Conveyor Belt Glues
General purpose conveyor belt glues are versatile adhesives used for a variety of maintenance tasks on conveyor belts. These glues are designed to offer strong bonds and durability under various environmental conditions.
Common Types of Conveyor Belt Glues
- SC2000 Cement: A widely used rubber adhesive known for its strong bonding properties and durability.
- Neoprene Cement: Common for quick repairs, providing good flexibility and water resistance.
- Polyurethane Glue: Offers excellent wear resistance and is effective in a range of temperatures.
- Acrylic-based Adhesives: Known for their quick setting times and effectiveness on a variety of surfaces.
- Silicone Adhesives: Best suited for high-temperature environments and providing flexible bonds.
- Epoxy Resins: Known for their high strength and chemical resistance, suitable for demanding applications.
Benefits of Using SC2000 Adhesive Cement
- Versatility: Bonds a wide range of materials, including rubber, metal, and fabric.
- High Strength: Provides a strong bond that is essential for the durability of the repair.
- Durability: Resistant to water, oil, and other environmental factors that could degrade other types of glue.
- Flexibility: Maintains its integrity even when the belt is under tension and flexing during operation.
- Ease of Application: Simple to mix and apply, which is critical for efficient maintenance work.
- Fast Setting: Cures quickly, minimizing downtime for conveyor systems.
- Cost-Effective: Offers a reliable solution without a significant investment.
- Long Shelf Life: Can be stored for extended periods without losing effectiveness.
Specialized Rubber Glues for Conveyor Belts
For certain applications, specialized rubber glues are necessary to ensure optimal performance and longevity of the conveyor belt repairs, particularly when dealing with unique materials like metal.
Introduction to Specialized Adhesives
Specialized adhesives are formulated to meet the demands of specific materials and conditions. These glues often provide enhanced bonding properties that general-purpose adhesives cannot match, such as increased thermal stability, chemical resistance, and bonding strength.
Conveyor Belt Rubber Glue for Metal
“Conveyor belt rubber glue for metal” is designed to address the unique challenges of bonding rubber to metal surfaces. This type of adhesive is crucial in applications where conveyor belts are reinforced with metal parts or need to attach metal components.
Applications of Rubber Glue for Metal
- Attaching Cleats: Used for securing metal cleats to the belt, which improves material handling capabilities.
- Repairing Rips: Effectively bonds rubber back to metal fasteners or frameworks in the belt.
- Joint Sealing: Ensures that metal joints are sealed against environmental factors, preventing rust and wear.
- Enhancing Durability: Provides a reinforced bond that increases the overall durability of the belt.
- Temperature Resistance: Suitable for high-temperature applications where other adhesives would fail.
- Chemical Resistance: Resists degradation from chemicals that might be present in the material being transported.
- Load Distribution: Helps distribute load more evenly across metal and rubber components, reducing strain.
Selecting the appropriate type of conveyor belt rubber glue, whether general purpose or specialized, is essential for maintaining the functionality and extending the lifespan of conveyor belts. This choice impacts everything from routine maintenance to critical repairs, especially in demanding industrial environments.
Choosing the Right Conveyor Belt Rubber Glue
Selecting the appropriate conveyor belt rubber glue is a critical decision that affects the effectiveness and longevity of conveyor belt repairs. The right adhesive ensures that the repair will hold under the stress of operation and environmental conditions.
Factors to Consider
When choosing the right conveyor belt rubber glue, several factors need to be considered to ensure optimal performance and durability:
Belt Material
Different belt materials require different types of glue for effective bonding. For example, natural rubber belts might need a different adhesive compared to synthetic rubber or PVC belts.
Environmental Conditions
The operating environment plays a crucial role in selecting the right glue. Factors such as exposure to extreme temperatures, moisture, oils, and chemicals must be taken into account to ensure that the adhesive can withstand these conditions without degrading.
Type of Repair
The specific repair task—whether patching a hole, repairing a tear, or splicing a belt—can dictate the type of glue needed. Some repairs might need a more flexible adhesive, while others might require maximum strength and rigidity.
Importance of Temperature and Chemical Resistance
- Temperature Extremes: Adhesives must perform well under the temperature conditions of the application area, whether in cold storage environments or near high-temperature machinery.
- Chemical Exposure: Resistance to chemicals is critical, especially in industries where the belts are exposed to oils, solvents, or corrosive materials.
- Curing Temperature: The temperature at which a glue cures can affect its strength and durability.
- Operational Heat: Conveyor belts often generate heat from friction, and the glue must be able to maintain its properties under such conditions.
- Cold Cracking: In cold environments, some adhesives can become brittle and crack, so selecting a glue that remains flexible at low temperatures is vital.
- Longevity Under Thermal Stress: The adhesive should maintain its bonding properties over time, even when subjected to continuous thermal cycling.
- Reactivity to Temperature Changes: Some adhesives might expand or contract significantly with temperature changes, which can weaken the bond.
- Safety Concerns: High-temperature environments might necessitate the use of non-flammable adhesives.
- Ease of Application in Various Temperatures: The viscosity of the adhesive can vary with temperature, affecting its ease of application.
- Thermal Degradation: The adhesive must resist breaking down or losing effectiveness due to prolonged exposure to heat.
Best Conveyor Belt Rubber Glues on the Market
The market offers a range of products designed to meet the diverse needs of conveyor belt maintenance. Here are some of the top conveyor belt rubber glues:
Features and Advantages of SC2000 Adhesive Cement:
- Strong Bond: Provides a very strong and durable bond that is crucial for high-stress applications.
- Versatility: Suitable for a variety of materials, including different types of rubber and metal.
- Durability: Resistant to water, oil, and other environmental factors.
- Flexibility: Maintains its flexibility, which is important for belts that bend around pulleys.
- Fast Curing: Sets quickly to reduce downtime during conveyor belt repairs.
- Ease of Use: Simple mixing and application process.
- Cost-Effectiveness: Offers a reliable solution without a significant investment.
- Availability: Widely available and recognized in the industry.
When selecting the best conveyor belt rubber glue, consider these products and factors to ensure a repair that is durable and effective, minimizing downtime and maintenance costs. The right adhesive can significantly impact the operational efficiency and longevity of conveyor systems.
Application Techniques for Conveyor Belt Rubber Glue
Mastering the correct application techniques for conveyor belt rubber glue is crucial to achieving strong, durable bonds that enhance the longevity and functionality of conveyor belts. Proper preparation and application are essential for effective repairs.
Preparation Steps
The first step in ensuring that conveyor belt rubber glue adheres properly is to meticulously prepare the surface of the belt. This preparation enhances the bond strength and durability of the repair.
Guidelines on Preparing the Conveyor Belt Surface
- Clean the Surface: Remove all dirt, grease, oil, and contaminants from the surface. Solvents or specialized cleaning agents may be used depending on the belt’s material.
- Dry the Area: Ensure that the surface is completely dry before applying any adhesive to prevent moisture from weakening the bond.
- Sand the Surface: Use sandpaper or a mechanical sander to roughen the rubber surface. This increases the surface area for the adhesive to bond, enhancing adhesion.
- Remove Dust: After sanding, thoroughly dust off the surface to ensure no loose particles interfere with the glue.
- Check for Damage: Inspect the area for any underlying damage that might need repair before applying the glue.
- Tape Off the Area: Use masking tape to define the area where the glue will be applied. This helps in applying the glue neatly and accurately.
Importance of Cleaning and Roughening the Surface
- Increased Surface Area: Roughening increases the surface area, providing more space for the adhesive to latch onto.
- Enhanced Mechanical Adhesion: A textured surface creates better mechanical interlocking for the glue.
- Removal of Contaminants: Cleaning ensures that contaminants that could inhibit adhesion are removed.
- Improved Bond Strength: Both cleaning and roughening contribute to a stronger, more reliable bond.
- Prevention of Failure: Proper preparation reduces the risk of bond failure under operational stress.
- Longevity of Repair: A well-prepared surface ensures that repairs last longer, reducing the need for frequent maintenance.
- Optimal Glue Performance: Glues perform best when applied to surfaces that are prepared according to manufacturer recommendations.
- Safety: A strong adhesive bond prevents belt slippage, which can be a safety hazard.
Applying the Glue
Proper application of conveyor belt rubber glue is as critical as the preparation phase. Following the correct steps ensures a secure and durable bond.
Step-by-Step Guide on How to Apply Conveyor Belt Rubber Glue
- Mix the Glue: Prepare the glue according to the manufacturer’s instructions. This may involve mixing different components in specified ratios.
- Apply the Glue: Use a spatula, brush, or roller to apply an even layer of glue over the prepared area. Ensure the application is uniform and covers the entire area.
- Allow to Tack: Some adhesives require a few minutes to become tacky before joining the surfaces. Follow the specific instructions regarding the wait time.
- Join the Surfaces: Carefully align and press the two surfaces together. Apply sufficient pressure to ensure full contact across the glued area.
- Secure the Bond: Use rollers or a hammer to further press the belt surfaces together, enhancing the bond strength.
Tips for Using Conveyor Belt Clamps and Vulcanizing Machines
- Securely Clamp the Belt: Conveyor belt clamps should hold the belt firmly in place during the gluing and curing process.
- Apply Even Pressure: Ensure that the clamps apply even pressure across the joint to prevent weak spots.
- Heat Application: Vulcanizing machines apply heat and pressure, which can improve the curing process for some types of glue.
- Monitor Temperature: Keep the temperature within the range recommended by the adhesive manufacturer.
- Time the Process: Adhere to the specified time for heating and cooling to ensure optimal curing.
- Check Alignment: Regularly check that the belt remains aligned during the clamping and vulcanizing process.
- Post-Curing Inspection: After curing, inspect the bond and the area around it for any signs of weakness or bubbling.
- Gradual Cooling: Allow the belt to cool gradually after vulcanization to prevent thermal shock.
- Test the Repair: Once the glue has fully cured, perform a load test or run the conveyor belt at low speed to ensure the repair holds under operational conditions.
By carefully following these preparation and application techniques, the longevity and efficiency of conveyor belt repairs can be significantly enhanced, reducing downtime and maintenance costs.
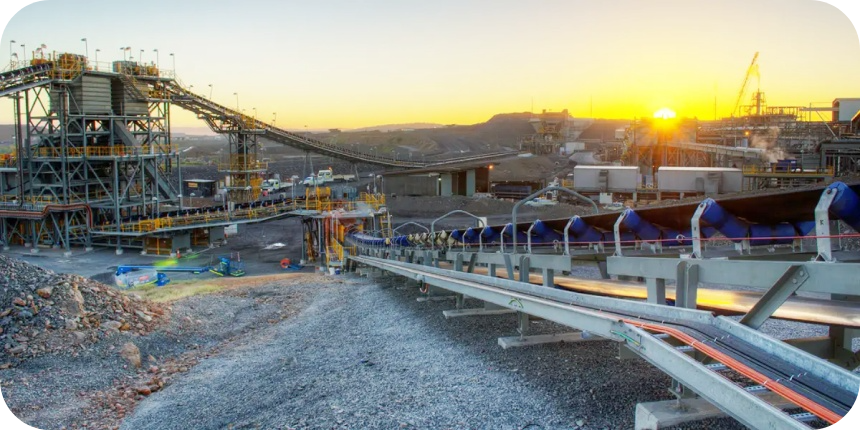
Tools and Accessories Needed
To successfully apply conveyor belt rubber glue and achieve professional-quality repairs, having the right tools and accessories is crucial. The selection of tools can significantly impact the ease and effectiveness of the repair process.
Essential Tools for Applying Rubber Glue
The correct application of conveyor belt rubber glue requires a basic toolkit designed specifically for conveyor belt repairs. Here’s a list of essential tools and their purposes:
Necessary Tools
- Conveyor Belt Clamps: Used to securely hold the belt ends in place during the repair process.
- Portable Conveyor Belt Vulcanizing Machines: These are essential for applying heat and pressure to vulcanize the rubber glue, ensuring a strong bond.
- Rubber Cement: A specific type of conveyor belt rubber glue that is used for patching and coating areas of the belt that are worn or torn.
- Rollers: Used to press and smooth the glue into the belt surface to ensure even distribution and secure adhesion.
- Brushes and Spatulas: For applying and spreading the rubber glue evenly across the repair area.
- Heat Guns: Useful for drying or accelerating the cure of some types of rubber glue.
Use of a Conveyor Belt Repair Kit
A conveyor belt repair kit typically includes a range of tools and materials designed for quick and effective belt repairs. These kits usually contain:
- Pre-measured quantities of rubber glue or cement.
- Hand tools like brushes, rollers, and cutters.
- Vulcanizing materials such as patches and strips that can be applied using the included tools.
- Detailed instructions on how to properly execute repairs.
Advanced Equipment
For more complex or large-scale repairs, advanced equipment can significantly enhance the effectiveness and durability of conveyor belt repairs.
Sophisticated Tools like Conveyor Belt Vulcanisers
Conveyor belt vulcanisers are crucial for professional-grade repairs, especially when dealing with large or critical conveyor belt systems. These tools apply precise heat and pressure to the repair area, ensuring that the rubber glue cures correctly and forms a bond that is as strong as the rest of the belt.
Information on Using Conveyor Belt Vulcanisers
- Temperature Control: Vulcanisers allow for precise temperature settings to match the specific requirements of the rubber glue used.
- Pressure Application: Even pressure distribution is critical in vulcanizing rubber glue, and these machines are designed to provide this consistency.
- Timer Settings: Built-in timers help manage the vulcanization process to prevent over or under curing.
- Portability: Some vulcanisers are portable, making them ideal for on-site repairs.
- Scalability: They come in various sizes to accommodate different belt widths and damage extents.
- Energy Efficiency: Modern vulcanisers are designed to be energy-efficient, reducing operational costs.
- Safety Features: Equipped with safety features to protect users from heat and pressure-related injuries.
- Durability: Built to withstand the harsh environments of industrial areas.
Benefits of Portable Tools for On-Site Repairs
- Immediate Repairs: Portable tools allow for repairs to be made directly on the system, reducing downtime.
- Cost-Effective: Minimizes the logistical costs of transporting belts to repair facilities.
- Flexibility: Adaptable to various sizes and types of belts and damages.
- Reduced Complexity: Simplifies the repair process, making it accessible even for less experienced operators.
- Speed: Increases the speed of repairs, which is critical in high-demand environments.
- Versatility: Can be used under different environmental conditions.
- Mobility: Easy to move from one site to another, enhancing service responsiveness.
- Efficiency: Increases the efficiency of the repair process, ensuring that belts return to service faster and in optimal condition.
With the right tools and a comprehensive understanding of how to use them, maintaining and repairing conveyor belts with conveyor belt rubber glue becomes more efficient, reliable, and cost-effective. These tools not only ensure quality repairs but also extend the operational life of conveyor belts.
Maintenance and Safety for Conveyor Belt Rubber Glue
Maintaining and ensuring safety during and after the application of conveyor belt rubber glue are pivotal to safeguarding the integrity of the repair and the health of the personnel involved. Proper post-application care and adherence to safety protocols can significantly enhance the efficacy and longevity of conveyor belt repairs. Here’s how to effectively manage maintenance and observe necessary safety precautions.
Post-Application Care
After applying conveyor belt rubber glue, it’s crucial to follow these best practices to maintain the conveyor belt and ensure the longevity of the repair:
- Curing Time: Respect the adhesive’s curing time, which can range from a few minutes to several hours, to achieve optimal bond strength.
- Inspection Schedule: Establish a routine inspection schedule post-repair. Initially inspect the conveyor belt 24 hours after the application, followed by weekly checks to monitor the condition of the repair.
- Clean the Area: Keep the repaired area clean, as dirt and debris can affect the quality of the adhesive bond.
- Monitor for Peeling: Check for signs of peeling or edges lifting, which indicate a failing bond.
- Load Gradually: Gradually reintroduce load to the conveyor belt to avoid overwhelming the new bond.
- Temperature Checks: Ensure the repaired area is not subjected to extreme temperatures that could weaken the glue.
- Chemical Exposure: Avoid exposing the repair site to harsh chemicals that may deteriorate the rubber glue.
- Document Repairs: Keep a log of all repairs made with rubber glue to track their durability and identify any recurring issues.
- Check for Alignment: Misalignment can stress the repaired area; ensure the belt is properly aligned.
- Watch for Wear and Tear: Regularly assess the belt for further wear and tear near the repaired spot.
- Use Correct Tension: Incorrect belt tension can undo the repair; always adjust to the manufacturer’s recommended settings.
- Professional Assessment: If unsure about the repair’s integrity, consult with a professional for a thorough inspection.
Safety Precautions
Using conveyor belt rubber glue involves chemicals that can be hazardous if not handled correctly. Follow these safety guidelines to prevent accidents:
- Personal Protective Equipment (PPE): Always wear appropriate PPE, including gloves, safety goggles, and masks to protect from fumes.
- Ventilation: Work in a well-ventilated area to avoid inhaling adhesive fumes.
- Skin and Eye Protection: Avoid direct contact with the skin and eyes, as the glue can cause irritation or burns.
- Proper Storage: Store rubber glue in a cool, dry place away from heat sources to prevent degradation of the adhesive.
- Spill Management: In case of spills, clean up immediately using a solvent recommended by the adhesive manufacturer to prevent slipping hazards.
- Read Instructions: Always read and follow the manufacturer’s instructions for application, curing times, and safety information.
- Dispose of Waste Properly: Dispose of any adhesive waste according to local regulations to prevent environmental contamination.
- First Aid Training: Ensure that all personnel applying conveyor belt rubber glue have basic first aid training, especially in dealing with chemical exposure incidents.
- Emergency Contacts: Have relevant emergency contact information readily available, including local emergency services and poison control centers.
By adhering to these maintenance and safety protocols, the life span of the conveyor belt repair can be maximized, and the safety of the work environment can be significantly enhanced. Regular maintenance checks and strict safety precautions are necessary to ensure that the application of conveyor belt rubber glue is both effective and safe.
Ensure smooth operations with our reliable conveyor rollers.
FAQs about Conveyor Belt Rubber Glue
When it comes to bonding the rubber of conveyor belts, choosing the right adhesive is crucial for both the efficiency and longevity of the belt’s operation. SC 2000 Cement, produced by Rema Tip Top, is widely regarded as the leading cold vulcanizing adhesive in the industry. This adhesive is favored for its exceptional bonding strength, versatility, and non-flammability, making it suitable for a wide range of applications, including underground operations where safety is paramount. SC 2000 is designed to offer superior adhesion, durability, and resistance against environmental stresses, providing a reliable bond that ensures the conveyor belt maintains its integrity under various operational conditions. It’s important to consider the specific requirements of your conveyor belt operation, including the type of rubber and the environmental conditions, to ensure that SC 2000 or any selected adhesive meets your needs effectively.
For joining rubber, whether it’s for conveyor belts, automotive applications, or general repairs, a cyanoacrylate adhesive, more commonly known as super glue, is often regarded as the best option due to its rapid bonding time and strong adhesion properties. However, for industrial applications, especially those involving operational stresses such as stretching, compression, or exposure to chemicals, a specialized rubber adhesive is recommended. Products like 3M’s Rubber and Vinyl 80 Spray Adhesive or Loctite’s rubber adhesives offer durability, flexibility, and resistance to heat, oils, and weathering, making them suitable for demanding applications. These adhesives are specifically formulated to create strong, resilient bonds that can withstand operational stresses, ensuring that the joined rubber maintains its integrity over time. Selection should be guided by the specific type of rubber, the nature of the application, and environmental factors to achieve optimal bonding results.
In the manufacturing and repair of belts and conveyors, cold vulcanizing adhesives like SC 2000 Cement play a critical role. These adhesives enable strong, durable bonds that are essential for the longevity and reliability of conveyor systems. Cold vulcanizing is preferred in scenarios where hot vulcanization is not feasible due to equipment limitations or when working with intricate parts. Unlike hot vulcanization, which requires specialized equipment and high temperatures, cold vulcanizing adhesives can be applied at room temperature, making them ideal for a wide range of settings, including field repairs. SC 2000 Cement is celebrated for its exceptional bonding strength, and it is capable of vulcanizing rubber to steel, rubber to rubber, and rubber to fabric, ensuring versatile application across different types of conveyor belts. Its formulation is designed to deliver a bond that mimics the rubber’s natural properties, providing a repair or bond that integrates seamlessly with the conveyor belt’s material.
Conveyor belts are made from various types of rubber, each chosen for its unique properties that are suited to different industrial applications and environmental conditions. Natural Rubber (NR) is prized for its exceptional tensile strength and elasticity, making it ideal for belts that require flexibility and durability under strain. Synthetic rubbers like Styrene Butadiene Rubber (SBR) and Nitrile Rubber (NBR) are frequently used due to their abrasion resistance and capability to withstand oil and chemical exposure, respectively. SBR is commonly chosen for general-purpose applications, while NBR is favored in environments where the belt may come into contact with oils, fats, and other hydrocarbons. Ethylene Propylene Diene Monomer (EPDM) rubber is utilized in applications requiring excellent weather, ozone, and heat resistance. The selection of rubber for conveyor belts involves considering the operational environment, including temperature, chemical exposure, mechanical stress, and the type of materials being conveyed, to ensure optimal performance and longevity of the belt in its specific application.
Last Updated on July 9, 2024 by Jordan Smith
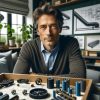
Jordan Smith, a seasoned professional with over 20 years of experience in the conveyor system industry. Jordan’s expertise lies in providing comprehensive solutions for conveyor rollers, belts, and accessories, catering to a wide range of industrial needs. From initial design and configuration to installation and meticulous troubleshooting, Jordan is adept at handling all aspects of conveyor system management. Whether you’re looking to upgrade your production line with efficient conveyor belts, require custom conveyor rollers for specific operations, or need expert advice on selecting the right conveyor accessories for your facility, Jordan is your reliable consultant. For any inquiries or assistance with conveyor system optimization, Jordan is available to share his wealth of knowledge and experience. Feel free to reach out at any time for professional guidance on all matters related to conveyor rollers, belts, and accessories.