Installation Guide for Conveyor Belt Rubber Pulley Lagging
Conveyor belt rubber pulley lagging refers to the protective layer bonded to the shells of conveyor pulleys. This lagging plays a pivotal role in enhancing conveyor system performance by increasing traction between the belt and the pulley, thus reducing slippage. The application of conveyor belt rubber pulley lagging is essential not only for prolonging the lifespan of the conveyor belt but also for optimizing the efficiency of the entire conveyor system. By improving the grip and reducing wear and tear, pulley lagging significantly mitigates operational issues, which in turn increases the reliability and productivity of material handling operations. Through these benefits, it effectively supports the continuous, smooth operation of conveyor systems in various industrial settings.
Types of Conveyor Belt Rubber Pulley Lagging
Conveyor belt rubber pulley lagging is critical for the operational efficiency and longevity of conveyor systems. Various types of lagging materials and techniques are employed to meet specific environmental and operational demands. Here, we explore the common types of conveyor belt rubber pulley lagging and their distinct applications and benefits.
Rubber Lagging Pulley
Rubber lagging pulleys are widely utilized due to their effectiveness in increasing the friction between the conveyor belt and pulley. There are two primary types:
- Plain Rubber Lagging: This type is smooth and provides sufficient grip to prevent slippage in less demanding environments. It’s often used on non-drive pulleys and is advantageous for its simplicity and cost-effectiveness.
- Diamond Pulley Lagging: Known for its distinctive diamond-shaped grooves, this lagging offers superior traction and is ideal for drive pulleys that require more grip. The grooves also aid in water dispersion, making it suitable for environments where moisture is a concern. Diamond pulley lagging enhances the belt tracking and extends the belt’s lifespan by reducing slippage.
Ceramic Lagging
Ceramic lagging is employed in scenarios that demand high durability and additional friction. The ceramic materials are embedded into rubber mats, which are then bonded to the pulley. This type of lagging is particularly beneficial in harsh, abrasive environments such as mining and quarrying where standard rubber lagging would wear down quickly. The ceramic increases grip and significantly reduces wear on the pulley, providing a longer service life than traditional rubber lagging.
Weld-On Pulley Lagging
Weld-on pulley lagging involves metal plates or strips that are directly welded to the pulley surface. This type of lagging is chosen for its extreme durability and is commonly used in applications where the pulley is exposed to severe wear conditions, such as heavy-duty mining operations. Weld-on lagging is resistant to high temperatures and aggressive wear, making it ideal for situations where other types of lagging might fail prematurely.
Each type of conveyor belt rubber pulley lagging serves distinct purposes and offers various benefits, making the choice of lagging crucial based on the specific requirements of the conveyor system and its operational environment.
Pulley Lagging Procedures for Conveyor Belt Rubber Pulley Lagging
Pulley lagging is a critical component in the maintenance and efficiency of conveyor systems. It involves the application of a rubber cover to the pulleys to increase friction between the pulley and the conveyor belt. This helps to reduce belt slippage, improve tracking, and extend the life of the belt and pulleys. Here, we outline a step-by-step guide on how conveyor belt rubber pulley lagging is installed and highlight the differences between the three common installation methods: hot vulcanizing, cold bonding, and weld-on installation.
Step-by-Step Installation Guide
- Surface Preparation: Clean the pulley surface thoroughly to remove all dirt, grease, and contaminants. The surface must be dry and roughened to enhance adhesion.
- Choosing the Right Lagging: Select the appropriate conveyor belt rubber pulley lagging material based on the belt type, environmental conditions, and load requirements.
- Cutting to Size: Measure and cut the rubber lagging to fit the pulley’s dimensions precisely.
- Adhesive Application: Apply a suitable adhesive evenly on the pulley surface and the back of the rubber lagging. The choice of adhesive depends on the installation method.
- Lagging Installation: Position the rubber lagging correctly on the pulley and press it into place, starting from the center and moving outward to eliminate air bubbles.
- Curing: Allow the adhesive to cure as per the manufacturer’s instructions. The duration will vary based on the adhesive type and environmental conditions.
- Finishing Touches: Trim any excess material and inspect the installation for any loose edges or imperfections.
- Testing: Conduct a test run to ensure the lagging is securely bonded and the conveyor belt runs smoothly over the pulley.
Differences Between Installation Methods
The table below highlights the key differences between hot vulcanizing, cold bonding, and weld-on installation methods, helping you choose the best method for your specific requirements.
Selecting the Right Installation Method
The choice between hot vulcanizing, cold bonding, and weld-on installation methods depends on several factors such as the operational demands of the conveyor system, the environmental conditions, and the available maintenance capabilities. Hot vulcanizing is best for environments where the conveyor system is subjected to high stresses and temperatures. Cold bonding is suitable for less intensive applications and where quick, easy repairs are preferred. As part of how to install a conveyor belt, weld-on installation is ideal for situations requiring a permanent and very durable bond, especially in harsh conditions.
By following these detailed procedures and understanding the differences between installation methods, you can ensure a successful installation of conveyor belt rubber pulley lagging, enhancing the efficiency and longevity of your conveyor system.
Get the best conveyor belts for your needs. Contact us now!
Cost and Providers of Conveyor Belt Rubber Pulley Lagging
When considering an upgrade or maintenance of your conveyor system with conveyor belt rubber pulley lagging, understanding the factors that influence cost and knowing how to find reliable providers are key. Below, we delve into the various factors that can affect the pricing of conveyor belt rubber pulley lagging and offer guidance on how to locate reputable providers.
Factors Influencing the Cost of Conveyor Belt Rubber Pulley Lagging
- Material Choice: The type of rubber or polyurethane used can significantly impact the cost. Specialty materials designed for extreme conditions are typically more expensive.
- Pulley Dimensions: Larger pulleys require more material and, consequently, the lagging costs increase.
- Thickness of the Lagging: Thicker lagging provides better durability and traction but also comes at a higher price.
- Type of Lagging: Different types, such as ceramic-reinforced lagging or grooved lagging, have different price points.
- Installation Method: Hot vulcanizing is generally more expensive than cold bonding due to the equipment and energy required.
- Labor Costs: The complexity of the installation and the expertise required can affect the cost. Specialized installation may require higher labor costs.
- Geographic Location: Costs can vary significantly based on where your facility is located due to differences in labor rates and material availability.
- Provider’s Brand and Reputation: Established brands with proven track records may charge more for their assured quality and reliability.
- Market Demand and Availability: Seasonal demands or supply shortages can affect prices.
- Scope of Conveyor System: Comprehensive systems requiring extensive lagging across multiple pulleys will naturally incur higher costs.
Finding Providers of Conveyor Belt Rubber Pulley Lagging
- Search Online Directories: Websites like ThomasNet or Kompass allow you to search for industrial suppliers by category and location.
- Ask for Recommendations: Consult with peers in your industry or reach out to professional networks for recommended suppliers.
- Check Local Industrial Suppliers: Many suppliers have local branches and may provide quicker delivery and installation services.
- Visit Trade Shows: Industrial and manufacturing trade shows are great places to meet suppliers and learn about new advancements directly.
- Utilize Search Engines: Simple searches for “conveyor belt rubber pulley lagging near me” can yield local results, especially on Google Maps.
- Review Industrial Magazines: Publications related to conveyor systems often feature advertisements from various suppliers.
- Consult with Conveyor System Consultants: Experts often have extensive networks and can recommend reliable providers.
- Check Supplier Reviews and Testimonials: Online reviews and testimonials can provide insights into the reliability and quality of services offered by a supplier.
- Request Quotes: Contact multiple providers to compare prices, services, and products to ensure you get the best deal.
When searching for conveyor belt rubber pulley lagging providers, it is crucial to consider both the quality of the product and the provider’s capability to support your specific requirements. Ensuring that the provider has a good track record and can offer comprehensive support will help in achieving a successful and durable installation.
Selection Considerations for Conveyor Belt Rubber Pulley Lagging
Choosing the right type of conveyor belt rubber pulley lagging is crucial for the optimal performance and longevity of your conveyor system. Various factors should be considered to ensure the selection meets the specific operational demands and environmental conditions. Below, we detail the key variables to consider and explain the differences between types of lagging suitable for different applications.
Variables to Consider When Choosing Pulley Lagging
- Type of Material Being Conveyed: Abrasive materials require durable, wear-resistant lagging, while sticky materials might need lagging with a smooth surface to prevent buildup.
- Environmental Conditions: Exposure to elements like water, oils, chemicals, or extreme temperatures can determine the type of lagging material needed.
- Belt Tension: High-tension conveyor systems generally require lagging with excellent grip to prevent belt slippage.
- Pulley Diameter: Smaller pulleys often need more flexible lagging options to accommodate the increased bending.
- Conveyor Speed: High-speed systems may need lagging that reduces heat buildup and can handle rapid movement.
- Load Type and Weight: Heavy loads require robust lagging that can support and distribute the weight evenly without deforming.
- Drive Type: Whether the system is head-driven or tail-driven can affect the type of lagging that will provide the best performance.
- Operational Safety Requirements: In environments where safety is a concern, lagging that enhances grip and tracking can prevent accidents.
- Maintenance Frequency: Some lagging types are easier to replace or repair, which could be crucial in high-throughput operations.
- Cost and Longevity: Balancing initial costs with expected lifespan and maintenance needs can affect the overall cost-effectiveness of the lagging choice.
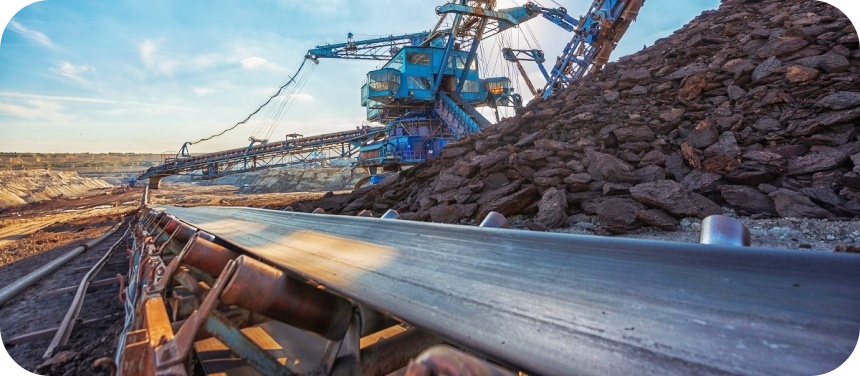
Types of Lagging and Suited Applications
Below is a table that outlines different types of conveyor belt rubber pulley lagging, detailing their primary characteristics and the applications they are best suited for, ranging from light to heavy-duty use.
Choosing the right conveyor belt rubber pulley lagging involves understanding the specific needs of your conveyor system and the conditions under which it operates. Each type of lagging offers distinct advantages and is designed to meet different operational challenges. By considering these factors carefully, you can select the most appropriate lagging that not only prolongs the life of your conveyor belt and pulleys but also enhances the efficiency and safety of the system.
FAQs about Conveyor Belt Rubber Pulley Lagging
Pulley lagging is a specialized material that is bonded to the shell of a belt conveyor pulley. Its primary roles include protecting the pulley from wear and corrosion, improving traction between the pulley and the belt, and preventing belt slippage especially under wet or muddy conditions. By increasing the coefficient of friction, pulley lagging can also help reduce the tension and energy consumption of the conveyor system. Additionally, lagging can help extend the operational life of the pulley and the belt by providing a replaceable wearing surface that is easier and less expensive to replace than the pulley or the belt itself.
Pulley lagging materials vary depending on the application and operating conditions and include rubber, ceramic, polyurethane, and composite materials. Each type has distinct advantages and is chosen based on specific requirements such as wear resistance, level of friction needed, and environmental conditions.
Rubber: Commonly used for its flexibility and excellent grip, rubber lagging is effective in most standard applications and offers good resistance to abrasion.
Ceramic: This is preferred in heavy-duty applications where conditions are harsh and abrasive. Ceramic tiles embedded in rubber or direct-bonded provide superior wear and tear resistance and optimal friction management.
Polyurethane: Known for its high wear-resistance and durability, polyurethane is often used in environments where both wear resistance and chemical resistance are needed.
Composite materials: These often combine properties of ceramics and rubber to provide both high friction and durability in extreme conditions.
What material is used for belt lagging?
The choice of material for belt lagging often depends on the operational requirements such as traction, durability, and environmental resistance needed. Rubber and ceramic are the most frequently used materials. Rubber provides elasticity and a high friction surface to prevent slippage and is suitable for most conditions except those that are extremely abrasive or have very high operating temperatures. Ceramic lagging, while more expensive, is used in harsh conditions due to its excellent resistance to wear and ability to maintain grip under higher temperatures and abrasive conditions. Occasionally, polyurethane or composites may be used when special properties such as specific chemical resistance or additional wear life are required.
Applying pulley lagging can be done through various methods depending on the type of lagging material:
Cold Bonding: This involves gluing the lagging material directly to the pulley surface with an adhesive. This method is less costly and can be done on-site but might be less durable under harsh conditions.
Hot Vulcanizing: Hot vulcanizing provides a more durable attachment by using heat and pressure to cure the bonding agent. This process usually requires specialized equipment and must often be performed in a workshop.
Direct Bonding of Ceramic Tiles: For ceramic lagging, each tile may be bonded directly to the pulley surface.
Mechanical Attaching: Some types of lagging, particularly certain ceramics, might require mechanical fastening to the pulley rather than adhesives.
Each method has its own set of advantages and considerations, and choice of the method will depend on the specific site conditions, type of pulley, and operational requirements.
Last Updated on August 16, 2024 by Jordan Smith
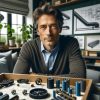
Jordan Smith, a seasoned professional with over 20 years of experience in the conveyor system industry. Jordan’s expertise lies in providing comprehensive solutions for conveyor rollers, belts, and accessories, catering to a wide range of industrial needs. From initial design and configuration to installation and meticulous troubleshooting, Jordan is adept at handling all aspects of conveyor system management. Whether you’re looking to upgrade your production line with efficient conveyor belts, require custom conveyor rollers for specific operations, or need expert advice on selecting the right conveyor accessories for your facility, Jordan is your reliable consultant. For any inquiries or assistance with conveyor system optimization, Jordan is available to share his wealth of knowledge and experience. Feel free to reach out at any time for professional guidance on all matters related to conveyor rollers, belts, and accessories.