Benefits of Using Pre-Owned Conveyor Belt Safety Devices
Understanding the importance of conveyor belt safety devices is crucial in industrial operations to ensure the safety and efficiency of conveyor systems. Conveyor belt safety devices play a vital role in preventing accidents and minimizing downtime by providing necessary protective measures. A comprehensive PDF resource can be immensely helpful in gaining a thorough understanding of these safety devices. It offers detailed explanations, diagrams, and guidelines that can aid workers and managers in implementing the best practices for conveyor belt safety. Utilizing a well-structured PDF on conveyor belt safety devices ensures that all relevant safety protocols are easily accessible and can be effectively communicated across the workforce.
Conveyor Belt Safety Devices: Creating a Conveyor Belt Safety Checklist
Ensuring the safety of workers and the efficiency of operations in a facility with conveyor belt systems requires a meticulous approach to safety management. Creating a conveyor belt safety checklist is an essential part of this process.
Step-by-Step Guide to Creating a Comprehensive Safety Checklist
Identify Potential Hazards
- Conduct a thorough risk assessment to identify potential hazards associated with conveyor belt operations. This includes mechanical failures, electrical hazards, and issues related to belt misalignment and material spillage.
- Engage employees in identifying hazards as they can provide valuable insights based on their hands-on experience.
List of Safety Devices
- Compile a list of essential conveyor belt safety devices such as emergency stop buttons, pull cord switches, and belt misalignment switches. Ensure that each device is correctly identified and its function is understood.
- Regularly update the list to include new technologies and devices that enhance safety.
Regular Inspection and Maintenance Schedule
- Establish a regular inspection and maintenance schedule for all conveyor belt safety devices. This should include daily, weekly, and monthly checks.
- Document all inspections and maintenance activities, noting any issues found and actions taken to resolve them.
Training and Awareness Programs
- Develop training programs to educate workers about the importance of conveyor belt safety devices and how to use them effectively.
- Conduct regular safety drills and refresher courses to ensure that all employees remain vigilant and knowledgeable about safety protocols.
Emergency Response Plan
- Create a detailed emergency response plan that outlines the steps to be taken in case of an emergency. This should include procedures for stopping the conveyor belt, evacuating the area, and notifying emergency services.
- Ensure that all workers are familiar with the emergency response plan and conduct regular drills to test its effectiveness.
Documentation and Record-Keeping
- Maintain comprehensive records of all safety-related activities, including risk assessments, training sessions, and maintenance logs.
- Use these records to track safety performance and identify areas for improvement.
Conveyor Belt Safety Devices: Importance of Conveyor Belt Safety Switches
Conveyor belt safety switches are critical components of any safety management system in facilities with conveyor belt systems. These devices play a crucial role in preventing accidents and ensuring the safe operation of conveyor belts.
Detailed Explanation of Various Types of Safety Switches
Emergency Stop Switches
- Emergency stop switches are designed to immediately halt the operation of the conveyor belt in the event of an emergency. They are strategically located along the conveyor belt to allow quick access by workers.
- These switches are typically large and brightly colored to ensure visibility and ease of use.
Pull Cord Switches
- Pull cord switches, also known as rope pull switches, are installed along the length of the conveyor belt. They allow workers to stop the belt by pulling on a cord that runs along the conveyor.
- This type of switch is particularly useful in long conveyor systems where an emergency stop button may not be easily accessible.
Belt Misalignment Switches
- Belt misalignment switches detect when the conveyor belt is off-center or misaligned. Misalignment can cause damage to the belt and other components, leading to potential safety hazards.
- When a misalignment is detected, the switch triggers an alarm or stops the belt to prevent further damage and allow for corrective action.
Speed Switches
- Speed switches monitor the speed of the conveyor belt and detect any deviations from the normal operating speed. If the belt moves too fast or too slow, the switch can trigger an alarm or stop the belt.
- These switches help prevent issues such as material spillage, belt slippage, and mechanical failures.
Safety Mats and Light Curtains
- Safety mats and light curtains are used to create a safety zone around the conveyor belt. If a worker steps on the mat or breaks the light beam, the conveyor belt stops automatically.
- These devices are particularly useful in areas where workers need to frequently interact with the conveyor belt, providing an additional layer of protection.
Conveyor Belt Safety Devices: Utilizing Conveyor Safety PDF Resources
Conveyor belt safety devices pdf resources are valuable tools for enhancing workplace safety protocols. These documents often contain detailed information on best practices, safety guidelines, and regulatory requirements.
How to Effectively Use Conveyor Safety PDF Documents
Accessing and Selecting Relevant PDFs
- Begin by accessing reputable sources for conveyor safety PDF documents. These can include government agencies, industry associations, and equipment manufacturers.
- Select PDFs that are relevant to your specific conveyor belt system and the types of conveyor belt safety devices you use.
Reviewing and Understanding the Content
- Thoroughly review the content of each PDF to understand the safety guidelines and recommendations provided.
- Pay special attention to sections that discuss the installation, operation, and maintenance of conveyor belt safety devices.
Integrating PDF Information into Safety Protocols
- Use the information from the PDFs to enhance your existing safety protocols. This can include updating safety checklists, revising training programs, and implementing new safety measures.
- Ensure that all workers are familiar with the updated protocols and understand how to apply the information from the PDFs in their daily tasks.
Training and Educational Programs
- Incorporate the information from conveyor safety PDFs into your training and educational programs. Use these resources to create comprehensive training materials that cover all aspects of conveyor belt safety.
- Conduct regular training sessions to keep all employees informed about the latest safety practices and guidelines.
Compliance and Auditing
- Ensure that your facility complies with all regulatory requirements by following the guidelines provided in conveyor safety PDFs.
- Use these documents as a reference during safety audits to identify areas where improvements can be made and to ensure that all safety measures are up to date.
Continuous Improvement
- Regularly review and update your safety protocols based on new information from conveyor safety PDFs. This will help you stay ahead of potential hazards and ensure a safe working environment.
- Encourage a culture of continuous improvement by involving all employees in safety discussions and encouraging them to provide feedback on safety measures.
By following these guidelines, you can create a comprehensive safety checklist, understand the importance of various conveyor belt safety switches, and effectively utilize conveyor safety PDF resources to enhance workplace safety. Ensuring the proper use and maintenance of conveyor belt safety devices is crucial for preventing accidents and maintaining a safe and efficient working environment.
Benefits of Used Conveyor Belt Safety Devices
Conveyor belt safety devices are essential in maintaining the safety and efficiency of conveyor systems in various industries. While new devices are often preferred, there are significant benefits to incorporating used conveyor belt safety devices as well. Understanding these benefits can help industries optimize their safety protocols while managing costs effectively. A comprehensive PDF guide on used conveyor belt safety devices can provide detailed insights into their advantages, ensuring informed decision-making.
Cost-Effectiveness
One of the primary benefits of using used conveyor belt safety devices is cost savings. Purchasing new safety devices can be expensive, especially for large-scale operations. Used devices, on the other hand, can provide the same level of safety and functionality at a fraction of the cost. This allows companies to allocate their budgets more efficiently, potentially investing in other critical areas such as employee training or system upgrades.
Sustainability and Environmental Impact
Incorporating used conveyor belt safety devices also promotes sustainability. By reusing existing equipment, companies can reduce their environmental footprint. The production of new devices involves the consumption of raw materials and energy, leading to environmental degradation. Utilizing used devices helps minimize waste and supports the principles of a circular economy, where resources are reused and recycled.
Availability and Quick Implementation
Used conveyor belt safety devices are often readily available, which can be a significant advantage in situations requiring immediate implementation. New devices might have longer lead times due to manufacturing and shipping processes. Having access to a supply of used devices can ensure that safety measures are in place without unnecessary delays, thus maintaining operational continuity.
Proven Performance and Reliability
Used conveyor belt safety devices have a track record of performance and reliability. Since they have been previously utilized, their effectiveness in real-world conditions is known. Companies can select devices with proven reliability, reducing the risk of malfunctions or failures. This reliability is crucial in maintaining a safe working environment and minimizing downtime caused by equipment issues.
Flexibility and Compatibility
Used safety devices often come from a variety of sources and can be compatible with different conveyor systems. This flexibility allows companies to find devices that fit their specific requirements without the need for extensive modifications. It also provides an opportunity to standardize safety equipment across multiple sites, simplifying maintenance and training processes.
Enhanced Training Opportunities
Another benefit of using used conveyor belt safety devices is the potential for enhanced training opportunities. Employees can be trained on devices that are already integrated into the system, providing practical, hands-on experience. This training can lead to a better understanding of safety protocols and the proper use of safety equipment, ultimately contributing to a safer work environment.
Used conveyor belt safety devices offer several advantages, including cost savings, sustainability, quick implementation, proven performance, flexibility, and enhanced training opportunities. A detailed PDF guide on these benefits can provide valuable information for industries looking to optimize their safety practices while managing resources efficiently.
Conveyor Belt Safety Devices: Key Conveyor Belt Specification for Safety
Ensuring the safety of conveyor belt systems requires careful consideration of various specifications. These specifications are critical in selecting and maintaining conveyor belt safety devices that provide optimal protection. A comprehensive PDF guide on conveyor belt specifications can serve as a valuable resource, detailing the key factors to consider for ensuring safety.
Material Composition and Durability
The material composition of a conveyor belt is a fundamental specification for safety. Conveyor belts must be made from durable materials that can withstand the demands of the operating environment. Common materials include rubber, PVC, and metal, each offering different levels of resistance to wear, heat, and chemicals. The durability of the belt directly impacts its ability to function safely over time.
Load Capacity and Strength
The load capacity and tensile strength of a conveyor belt are crucial specifications for safety. The belt must be capable of handling the maximum load without experiencing excessive strain or risk of failure. Ensuring that the conveyor belt meets the required load capacity specifications helps prevent accidents and equipment damage.
Belt Speed and Control
Belt speed is another important specification for safety. Conveyor belts must operate at a speed that is appropriate for the materials being transported and the overall system design. Excessive speeds can lead to accidents, while insufficient speeds may reduce efficiency. Safety devices must be capable of controlling and regulating belt speed to maintain safe operation.
Fire Resistance and Thermal Stability
In environments where high temperatures or flammable materials are present, fire resistance and thermal stability are critical specifications. Conveyor belts must be able to withstand exposure to heat and flames without compromising their structural integrity. Fire-resistant materials and coatings can enhance safety by preventing fires and reducing the risk of thermal damage.
Surface Texture and Coefficient of Friction
The surface texture of a conveyor belt affects its grip and the coefficient of friction. A proper balance between grip and smoothness is essential for safe material handling. Belts with inadequate friction may cause slippage, while overly rough surfaces can damage materials or cause unnecessary wear. Safety devices must consider these factors to ensure stable and secure transportation.
Belt Width and Length
The width and length of a conveyor belt are specifications that influence the overall design and safety of the system. The belt must be wide enough to accommodate the materials being transported without risk of spillage. The length of the belt must also be suitable for the intended application, ensuring that the system operates efficiently and safely.
Alignment and Tracking
Proper alignment and tracking of the conveyor belt are essential for safety. Misaligned belts can lead to uneven wear, increased risk of accidents, and reduced efficiency. Conveyor belt safety devices such as tracking rollers and alignment sensors help maintain proper belt positioning, ensuring smooth and safe operation.
Maintenance and Inspection Requirements
Maintenance and inspection requirements are key specifications for ensuring the ongoing safety of conveyor belt systems. Regular maintenance schedules and thorough inspections help identify potential issues before they lead to accidents. Conveyor belt safety devices must be designed for easy maintenance and inspection to facilitate timely and effective safety checks.
Understanding and adhering to key conveyor belt specifications is essential for maintaining a safe and efficient system. Material composition, load capacity, belt speed, fire resistance, surface texture, belt dimensions, alignment, and maintenance requirements all play a vital role in ensuring safety. A detailed PDF guide on these specifications can provide valuable information for selecting and maintaining conveyor belt safety devices.
Conveyor Belt Safety Devices: Components of a Comprehensive Conveyor Belt System
A comprehensive conveyor belt system consists of various components that work together to ensure safe and efficient operation. Each component plays a critical role in maintaining the overall functionality and safety of the system. Understanding these components is essential for implementing effective safety measures. A detailed PDF guide on conveyor belt system components can provide valuable insights into their functions and contributions to safety.
Conveyor Belt
The conveyor belt itself is the primary component of the system. It serves as the surface on which materials are transported. The belt must be durable, flexible, and appropriate for the specific application. Conveyor belt safety devices must be integrated to ensure the belt operates safely and efficiently.
Drive Mechanism
The drive mechanism powers the conveyor belt, providing the necessary force to move materials along the system. This component includes motors, gearboxes, and drive belts. Ensuring the drive mechanism operates correctly is essential for maintaining consistent belt speed and preventing accidents.
Idlers and Rollers
Idlers and rollers support the conveyor belt and help maintain its alignment. They reduce friction and wear on the belt, ensuring smooth operation. Properly functioning idlers and rollers are crucial for preventing belt misalignment and ensuring the stability of the transported materials.
Pulleys
Pulleys are used to guide and tension the conveyor belt. They play a key role in maintaining the belt’s alignment and tension, ensuring it runs smoothly and efficiently. Safety devices such as pulley guards and alignment sensors are essential for preventing accidents and maintaining proper belt operation.
Safety Devices
Conveyor belt safety devices are critical components that protect workers and equipment. These devices include emergency stop buttons, safety switches, pull cords, and guards. They are designed to detect potential hazards and stop the system in case of an emergency, preventing accidents and injuries.
Control System
The control system manages the operation of the conveyor belt, including speed, direction, and safety functions. It includes sensors, programmable logic controllers (PLCs), and human-machine interfaces (HMIs). A well-designed control system ensures safe and efficient operation, integrating various safety devices to respond to potential hazards.
Loading and Unloading Points
Loading and unloading points are where materials are placed onto or removed from the conveyor belt. These areas must be designed to prevent spillage, reduce dust, and ensure safe material handling. Safety devices such as chutes, hoppers, and guards are essential for maintaining safe loading and unloading operations.
Support Structure
The support structure holds the conveyor belt system in place, providing stability and support. It must be robust and well-maintained to ensure the safety and reliability of the entire system. Regular inspections and maintenance of the support structure are essential for preventing structural failures and ensuring safe operation.
Maintenance and Inspection Tools
Maintenance and inspection tools are necessary for the regular upkeep of the conveyor belt system. These tools include tension meters, alignment tools, and inspection cameras. Proper maintenance and inspection are crucial for identifying potential issues and ensuring the ongoing safety and efficiency of the system.
A comprehensive conveyor belt system consists of various components, each contributing to the overall safety and efficiency of the operation. Understanding the roles of the conveyor belt, drive mechanism, idlers, rollers, pulleys, safety devices, control system, loading and unloading points, support structure, and maintenance tools is essential for implementing effective safety measures. A detailed PDF guide on these components can provide valuable information for maintaining a safe and efficient conveyor belt system.
FAQs about Conveyor Belt Safety Devices
Conveyor belts are equipped with various safety devices to ensure safe operation and prevent accidents. Common safety devices include emergency stop switches, which allow operators to halt the conveyor in case of an emergency. Safety guards and protective barriers are installed to prevent access to hazardous areas, such as moving parts and pinch points. Pull cords, which run along the length of the conveyor, enable workers to stop the conveyor from any point along the line. Additionally, speed sensors monitor the conveyor’s speed to detect any abnormalities, and belt misalignment switches ensure the belt remains properly aligned. These devices collectively enhance the safety and reliability of conveyor belt systems, minimizing the risk of injury and equipment damage.
Chain conveyors, like other conveyor systems, incorporate specific safety devices to ensure safe and efficient operation. One critical safety device is the chain tensioner, which maintains proper chain tension and prevents slippage or derailment. Overload protection devices, such as shear pins or torque limiters, protect the conveyor from damage by disconnecting the drive mechanism in case of excessive load. Emergency stop buttons and pull cords allow for immediate shutdown of the conveyor in emergencies. Additionally, safety guards and covers are installed to prevent access to moving parts and reduce the risk of injury. Regular maintenance and inspection of these safety devices are essential to ensure their proper functioning and the overall safety of the chain conveyor system.
Along a conveyor system, several safety devices should be installed to enhance worker safety and prevent accidents. Emergency stop switches or pull cords should be placed at regular intervals along the conveyor, allowing workers to stop the conveyor from any point in case of an emergency. Safety guards and barriers should be installed around hazardous areas, such as moving parts and pinch points, to prevent accidental contact. Additionally, warning signs and labels should be prominently displayed to alert workers to potential hazards. Conveyor speed sensors and belt misalignment switches help monitor the system’s operation and detect any abnormalities. Regular training and safety drills should also be conducted to ensure workers are familiar with these safety devices and know how to respond in an emergency.
The primary human safety device in a conveyor system is the emergency stop mechanism, which includes emergency stop switches and pull cords. These devices are strategically placed along the conveyor’s length, allowing workers to quickly stop the conveyor in case of an emergency, such as a worker becoming entangled or an object obstructing the conveyor. Additionally, safety guards and barriers serve as physical protective devices to prevent accidental contact with moving parts. Regular safety training and drills ensure that workers are aware of the locations and operation of these emergency stop mechanisms, enhancing their ability to respond promptly and effectively in emergency situations. These human safety devices are critical in minimizing the risk of injury and ensuring a safe working environment around conveyor systems.
Last Updated on June 11, 2024 by Jordan Smith
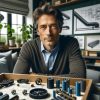
Jordan Smith, a seasoned professional with over 20 years of experience in the conveyor system industry. Jordan’s expertise lies in providing comprehensive solutions for conveyor rollers, belts, and accessories, catering to a wide range of industrial needs. From initial design and configuration to installation and meticulous troubleshooting, Jordan is adept at handling all aspects of conveyor system management. Whether you’re looking to upgrade your production line with efficient conveyor belts, require custom conveyor rollers for specific operations, or need expert advice on selecting the right conveyor accessories for your facility, Jordan is your reliable consultant. For any inquiries or assistance with conveyor system optimization, Jordan is available to share his wealth of knowledge and experience. Feel free to reach out at any time for professional guidance on all matters related to conveyor rollers, belts, and accessories.