Industrial Conveyor Belt Scale Price Analysis
Conveyor belt scales are crucial tools in various industries, ensuring precise material handling and efficient operations. The conveyor belt scale price is influenced by several factors, including the scale’s capacity, accuracy, and the technology used. Additionally, installation costs and the specific industry requirements can impact the overall price. Understanding these elements helps businesses make informed decisions when investing in conveyor belt scales, optimizing both performance and cost-efficiency. By considering these factors, companies can select the best conveyor belt scale that meets their operational needs and budget constraints.
Conveyor Belt Scale Price in India
Current Market Trends for Conveyor Belt Scale Prices in India
The market for conveyor belt scales in India has been evolving, with several notable trends influencing the conveyor belt scale price. Here are six key trends currently shaping the market:
- Technological Advancements: The integration of advanced technologies such as IoT and AI in conveyor belt scales has led to more precise and reliable measurements, but also increased costs. Modern scales with enhanced features tend to command higher prices due to their improved efficiency and accuracy.
- Demand from Various Industries: Industries such as mining, agriculture, and manufacturing have seen a growing need for conveyor belt scales. This surge in demand has led to a competitive market, with prices fluctuating based on industry-specific requirements and bulk purchases.
- Increased Focus on Automation: As automation becomes more prevalent in industrial processes, the demand for automated conveyor belt scales has risen. These advanced systems are typically more expensive, impacting the overall market price.
- Local vs. Imported Products: The market is divided between locally manufactured conveyor belt scales and imported ones. Imported scales, often perceived as more reliable and technologically advanced, tend to be priced higher than local products, affecting the average market price.
- Government Regulations and Standards: Compliance with stringent government regulations and industry standards in India can influence the pricing of conveyor belt scales. Manufacturers must ensure their products meet these regulations, sometimes leading to increased production costs and, consequently, higher market prices.
- Economic Factors: General economic conditions, such as inflation and changes in currency exchange rates, also play a significant role in determining the conveyor belt scale price. Economic stability tends to lead to more stable prices, while fluctuations can cause price variations.
Factors Affecting the Price Variations within the Indian Market
Several factors contribute to the variations in conveyor belt scale price within the Indian market. Here are eight significant factors:
- Material Quality: The quality of materials used in manufacturing conveyor belt scales greatly impacts their price. Higher-quality materials, which ensure durability and longevity, usually come at a higher cost.
- Brand Reputation: Established brands like Avery Weigh-Tronix, Siemens, and Thermo Fisher are known for their reliable products but often come with a higher price tag compared to lesser-known brands.
- Scale Capacity: Conveyor belt scales come in various capacities to handle different load sizes. Scales designed for higher capacities generally cost more due to the need for more robust construction and advanced sensors.
- Precision and Accuracy: Scales with higher precision and accuracy, essential for industries where precise measurements are crucial, are typically more expensive. This is due to the advanced technology and calibration required.
- Additional Features: Features such as data logging, remote monitoring, and integration with other systems can significantly add to the conveyor belt scale price. These features enhance functionality but also increase costs.
- Supplier Services: The level of customer service, warranty, and after-sales support provided by suppliers can affect the price. Companies offering comprehensive support services often charge more for their products.
- Customization Options: Customization to meet specific industrial needs, such as specific size requirements or special operating conditions, can lead to higher prices. Custom solutions require additional design and manufacturing efforts.
- Geographical Location: Prices can also vary based on geographical location due to differences in shipping costs, local taxes, and availability of components. Urban areas may see higher prices compared to rural regions due to logistical considerations.
Comparison of Prices from Different Manufacturers and Suppliers
To provide a clearer picture of the conveyor belt scale price in India, here is a comparison of prices from various manufacturers and suppliers:
This table highlights the variability in conveyor belt scale price based on the manufacturer, model, and features offered. Higher-end models with advanced features and greater accuracy tend to be more expensive, reflecting the added value they bring to industrial applications.
The conveyor belt scale price in India is influenced by a myriad of factors, including technological advancements, demand, material quality, brand reputation, and additional features. By understanding these factors and comparing prices from various manufacturers, businesses can make informed decisions to optimize their investment in conveyor belt scales.
Industrial Conveyor Belt Scale Price
Detailed Breakdown of Prices for Different Types of Industrial Conveyor Belt Scales
The conveyor belt scale price for industrial applications varies widely based on the type and features of the scale. Here’s a detailed breakdown:
- Basic Conveyor Belt Scales: These are entry-level scales designed for standard industrial use where high precision is not critical. They typically have basic features like simple weight measurement without additional data integration. The price range for these scales is generally between $1,000 to $5,000.
- Mid-Range Conveyor Belt Scales: These scales offer a balance between cost and functionality. They include more advanced features such as data logging, improved accuracy, and better construction materials. Mid-range scales are suitable for most industrial applications, with prices ranging from $5,000 to $15,000.
- High-End Conveyor Belt Scales: High-end models are equipped with the latest technology, providing the highest levels of accuracy and integration capabilities. They can interface with other systems and provide real-time data monitoring and analysis. These scales are used in industries where precision is critical, such as pharmaceuticals or high-value material handling. The price for these scales can range from $15,000 to $50,000 or more.
- Custom Conveyor Belt Scales: For unique industrial requirements, customized scales can be designed. These may include specific features like enhanced environmental resistance, custom sizing, or integration with specialized equipment. The cost of custom scales depends on the specifications but typically starts around $10,000 and can exceed $100,000.
How Industrial Applications Affect Pricing
The conveyor belt scale price is significantly influenced by the specific industrial applications for which the scales are intended. Here are some factors related to industrial applications that affect pricing:
- Accuracy Requirements: Industries requiring high precision in weight measurements, such as pharmaceuticals, food processing, or chemical production, will need scales with higher accuracy. These scales use advanced sensors and calibration techniques, resulting in higher prices.
- Environmental Conditions: Industrial environments can vary greatly, from clean, controlled settings to harsh, abrasive conditions in mining or quarrying. Scales designed to withstand extreme temperatures, moisture, dust, or corrosive substances are built with robust materials and protective features, increasing their cost.
- Load Capacity: The scale’s load capacity directly impacts its price. Scales that can handle heavier loads require stronger construction and more durable components, leading to higher costs. For example, scales used in heavy-duty mining operations are more expensive than those used in light manufacturing.
- Integration and Connectivity: In modern industrial setups, conveyor belt scales often need to integrate with other systems for automated data collection and process control. Scales with advanced connectivity features like IoT integration, wireless communication, and compatibility with industry-standard software are more expensive.
- Customization Needs: Specific industrial applications may require custom features, such as tailored dimensions, specific sensor types, or special data outputs. Customization adds to the development and production costs, reflecting in the final price of the scale.
- Regulatory Compliance: Industries such as food and pharmaceuticals are subject to stringent regulatory standards. Scales that comply with these standards must undergo rigorous testing and certification processes, contributing to higher prices.
Examples of Price Ranges for Specific Models Used in Industrial Settings
To illustrate the range of conveyor belt scale price in industrial settings, here are six examples of specific models and their price ranges:
These examples show the diversity in pricing based on the features and capabilities of each model. High-end models with sophisticated features and higher accuracy are priced significantly higher than basic models.
The conveyor belt scale price for industrial applications is influenced by various factors including accuracy requirements, environmental conditions, load capacity, integration needs, customization, and regulatory compliance. By understanding these factors and comparing prices from different manufacturers, industries can select the most suitable conveyor belt scale to meet their operational needs and budget constraints.
Belt Scale Conveyor
What is a Belt Scale Conveyor?
A belt scale conveyor is an essential piece of equipment in material handling systems used across various industries. It combines a conveyor belt with an integrated weighing system, allowing for real-time measurement of the material being transported. The scale typically consists of load cells that measure the weight of the material on the belt and a speed sensor that measures the belt’s velocity. This data is then used to calculate the flow rate and total weight of the material.
Significance in Various Industries
- Mining: In the mining industry, belt scale conveyors are crucial for monitoring the output of mined materials, ensuring accurate inventory management and optimizing production processes.
- Construction: Construction companies use belt scale conveyors to manage the supply of raw materials like sand, gravel, and concrete, maintaining efficiency and cost control.
- Agriculture: Farmers and agricultural businesses use these systems to weigh and transport bulk goods such as grain, ensuring accurate distribution and sales.
- Food Processing: In the food industry, belt scale conveyors are used to monitor the flow of ingredients and finished products, maintaining quality control and regulatory compliance.
- Recycling: Recycling facilities rely on belt scale conveyors to measure the amount of material processed, which helps in optimizing operations and reporting accurate data for sustainability goals.
- Pharmaceuticals: Precision is vital in the pharmaceutical industry, where belt scale conveyors ensure the accurate measurement of ingredients and products during the manufacturing process.
- Cement and Aggregates: In cement production, these systems help manage raw material input and finished product output, improving overall efficiency.
- Chemicals: Chemical manufacturing requires precise measurement and control of materials to ensure product quality and safety, which is achieved using belt scale conveyors.
- Power Generation: Belt scale conveyors in power plants are used to handle fuel materials like coal, ensuring consistent and efficient fuel supply.
- Logistics and Warehousing: These conveyors help in monitoring the movement of goods within warehouses and logistics centers, optimizing inventory management and distribution.
Pricing Components for Belt Scale Conveyors
The conveyor belt scale price is influenced by several key components:
- Type of Scale: The type of weighing system used (e.g., single-idler, multi-idler, or integrator scales) affects the price. Multi-idler scales, which provide higher accuracy, are generally more expensive.
- Load Cell Technology: Advanced load cells that offer greater precision and durability contribute to higher prices.
- Speed Sensors: The quality and type of speed sensors used can also impact the cost. High-precision sensors are more expensive but provide more accurate measurements.
- Construction Materials: The materials used in the construction of the conveyor belt and scale (e.g., stainless steel, high-strength alloys) affect the overall price. Durable materials that withstand harsh environments are costlier.
- Installation and Calibration: Professional installation and calibration services are essential for accurate functioning and can add significantly to the initial cost.
- Data Integration and Software: Advanced systems that offer data integration, real-time monitoring, and sophisticated software for data analysis tend to be more expensive.
- Customization: Custom-built systems tailored to specific industrial requirements can significantly increase the price due to additional design and manufacturing efforts.
- Brand and Manufacturer: Well-known brands and manufacturers with a reputation for quality and reliability typically charge higher prices for their products.
- Warranty and Support Services: Extended warranties and comprehensive support services add to the cost but provide long-term value through reduced downtime and maintenance expenses.
- Compliance and Certification: Scales that meet specific regulatory standards or have industry certifications may be priced higher due to the additional testing and validation required.
Comparison of Belt Scale Conveyor Prices Globally and in India
The conveyor belt scale price varies globally due to differences in manufacturing costs, local market demands, and economic factors. Here’s a comparative overview:
In India, the conveyor belt scale price is relatively competitive due to a mix of local production and imported systems. Indian manufacturers like Essae and IPA offer affordable options for basic and mid-range scales, while international brands like Siemens and Thermo Fisher Scientific provide high-end models at a premium price. The lower end of the price spectrum in India includes basic scales suitable for general industrial use, while the higher end comprises advanced systems with enhanced features for precision applications.
The conveyor belt scale price is influenced by numerous factors, including the type of scale, technology used, construction materials, and additional features. By understanding these components and comparing prices globally and within specific regions like India, businesses can make informed decisions to select the most suitable belt scale conveyor for their operational needs and budget.
Belt Weigh Scale Working Principle: Conveyor Belt Scale Price
Detailed Explanation of How a Belt Weigh Scale Works
A belt weigh scale, also known as a conveyor belt scale, is an integrated system used to measure the flow rate and total weight of material being transported on a conveyor belt. Here’s a detailed explanation of how it works:
- Load Cells: The core component of a belt weigh scale is the load cell. Load cells are sensors that measure the weight of the material on the conveyor belt. As material passes over the scale, the load cells detect the weight and convert it into an electrical signal.
- Speed Sensor: To determine the flow rate, a speed sensor is installed on the conveyor belt. This sensor measures the belt’s speed, which is crucial for calculating the rate at which material is being transported.
- Integration and Data Processing: The signals from the load cells and speed sensor are sent to an integrator. The integrator is a processing unit that combines these signals to calculate the flow rate (typically expressed in units such as tons per hour) and the total weight of material transported over a specific period.
- Weigh Frame: The load cells are mounted on a weigh frame that is installed under the conveyor belt. This frame supports the belt and ensures that the weight measurements are accurate and consistent. The weigh frame must be sturdy and precisely aligned to prevent measurement errors.
- Calibration: Calibration is a crucial step to ensure accuracy. It involves setting the scale to known weights and adjusting the system to accurately reflect these weights. Regular calibration helps maintain the scale’s accuracy over time.
- Data Output and Monitoring: The processed data can be displayed on a local readout, transmitted to a central control system, or integrated into a plant’s SCADA (Supervisory Control and Data Acquisition) system. This allows operators to monitor material flow in real-time and make informed decisions.
- Environmental Considerations: Belt weigh scales are designed to operate in various environmental conditions. Factors such as dust, moisture, and temperature can affect performance, so the scales are often equipped with protective features to ensure reliable operation in harsh environments.
- Maintenance and Upkeep: Regular maintenance, including cleaning, inspection, and recalibration, is essential to keep the belt weigh scale functioning accurately. Proper maintenance extends the lifespan of the equipment and ensures continuous reliable performance.
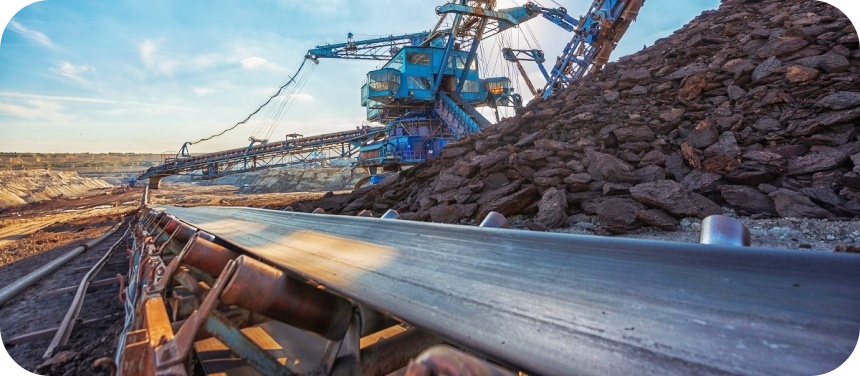
Factors that Impact the Cost Based on the Working Principle
The conveyor belt scale price is influenced by several factors related to the working principle of the belt weigh scale. Here are eight factors that impact the cost:
- Number and Type of Load Cells: Scales with multiple load cells offer higher accuracy and capacity but are more expensive. The type of load cell, whether it’s single-point, dual-point, or multi-point, also affects the price.
- Quality of Speed Sensors: High-quality, precise speed sensors that provide accurate measurements add to the cost. The choice between optical, magnetic, or mechanical speed sensors influences the overall price.
- Weigh Frame Construction: The materials and design of the weigh frame contribute significantly to the cost. Frames made of high-strength alloys or stainless steel, designed to withstand harsh environments, are more expensive.
- Calibration Mechanism: Advanced calibration mechanisms that allow for easy and frequent calibration without significant downtime increase the scale’s cost. Automatic calibration features add to the price.
- Integration Capabilities: Scales that can integrate with various data systems, such as SCADA, ERP, or other control systems, are more costly due to the additional hardware and software required.
- Environmental Protection: Features like dust and moisture protection, temperature compensation, and rugged design for harsh environments add to the scale’s cost.
- Maintenance Requirements: Scales designed for easy maintenance with minimal downtime are typically more expensive. This includes features like quick-release mechanisms and self-diagnostic tools.
- Brand and Manufacturer Reputation: Established brands known for high quality and reliability often charge a premium for their products. The reputation of the manufacturer can significantly impact the conveyor belt scale price.
Insights into How Technological Advancements Affect Pricing
Technological advancements play a crucial role in determining the conveyor belt scale price. Here are ten insights into how these advancements affect pricing:
- Improved Accuracy: Advances in sensor technology have led to more accurate load cells and speed sensors. Higher accuracy levels translate to better performance but also higher costs.
- Enhanced Data Processing: Modern integrators with advanced data processing capabilities provide more detailed and precise measurements. These high-tech integrators are more expensive.
- Wireless Connectivity: The incorporation of wireless technology for data transmission and remote monitoring increases the scale’s functionality and convenience but also adds to the price.
- Automated Calibration: Automatic calibration systems reduce the need for manual adjustments and downtime, improving efficiency. However, these systems are more costly to implement.
- Real-Time Monitoring: Technologies that allow for real-time monitoring and reporting of data improve operational efficiency but come at a higher cost due to the sophisticated hardware and software required.
- IoT Integration: Internet of Things (IoT) integration enables predictive maintenance and real-time analytics, enhancing operational efficiency but increasing the scale’s cost.
- Enhanced Durability: Advances in materials science have led to more durable components that withstand harsh environments, reducing maintenance needs but increasing initial costs.
- Energy Efficiency: Newer models are designed to be more energy-efficient, reducing operational costs but potentially increasing upfront costs due to the advanced technology involved.
- User-Friendly Interfaces: Modern scales come with intuitive interfaces and touch-screen displays, improving ease of use. These features add to the initial purchase price.
- Compliance with Industry Standards: Technological advancements that ensure compliance with stringent industry standards and regulations add to the cost due to the additional testing and certification required.
The working principle of belt weigh scales involves a combination of load cells, speed sensors, integrators, and weigh frames to accurately measure material flow. The conveyor belt scale price is influenced by factors related to the scale’s design, technology, and operational requirements. Technological advancements have significantly improved the performance and capabilities of these scales, but they also contribute to higher costs. Understanding these factors helps in making informed decisions when investing in belt weigh scales for various industrial applications.
Belt Scale Weighing System: Conveyor Belt Scale Price
Description of the Components of a Belt Scale Weighing System
A belt scale weighing system is a sophisticated arrangement designed to measure the weight of materials being transported on a conveyor belt. Here are the six key components of such a system:
- Load Cells: These are the sensors responsible for measuring the weight of the material on the conveyor belt. Load cells convert the weight into an electrical signal. They are typically installed beneath the conveyor belt and can vary in type and precision, impacting the overall accuracy of the system.
- Speed Sensor: This component measures the speed of the conveyor belt. The speed sensor’s data is crucial for calculating the material’s flow rate. Accurate speed measurement ensures precise flow rate and total weight calculations.
- Weigh Frame: The weigh frame is the structure that supports the conveyor belt and the load cells. It ensures that the load cells accurately capture the weight of the material. The frame must be robust and properly aligned to maintain measurement accuracy and stability.
- Integrator: The integrator is the brain of the weighing system. It processes the signals from the load cells and speed sensor to compute the flow rate and total weight of the material. Modern integrators come with advanced features like data logging, real-time monitoring, and connectivity options for remote access.
- Calibration Mechanism: Calibration is essential to ensure the accuracy of the belt scale. The calibration mechanism involves setting the scale to known weights and adjusting it accordingly. Regular calibration helps in maintaining the system’s precision over time.
- Data Output and Display: This component includes devices that display the measured data and provide interfaces for data output. It can range from simple digital displays to complex interfaces that integrate with broader industrial control systems, allowing for real-time monitoring and analysis.
Pricing Considerations for the Entire Weighing System Versus Individual Components
When considering the conveyor belt scale price, it is important to weigh the cost of the entire weighing system against the costs of individual components. Here are eight pricing considerations:
- System Integration: Buying a complete weighing system ensures compatibility among components and usually comes with integrated software. However, it may be more expensive than purchasing components separately.
- Load Cell Quality: High-precision load cells cost more but offer better accuracy and durability. The number and type of load cells required can significantly affect the overall system cost.
- Speed Sensor Technology: Advanced speed sensors that offer higher accuracy and reliability come at a higher cost. The choice between optical, magnetic, or mechanical sensors can influence the overall price.
- Weigh Frame Construction: The materials and construction quality of the weigh frame can vary, with high-strength alloys or stainless steel frames being more expensive but offering greater durability and longevity.
- Integrator Features: Integrators with advanced data processing capabilities, connectivity options, and user-friendly interfaces are more costly. However, they offer enhanced functionality and ease of use.
- Calibration Mechanisms: Automated calibration systems that reduce manual intervention and downtime are more expensive but can offer long-term cost savings through improved efficiency and accuracy.
- Maintenance and Support: A complete system often includes comprehensive maintenance and support services, which can add to the initial cost but reduce long-term maintenance expenses and downtime.
- Brand and Manufacturer: Established brands with a reputation for quality and reliability may charge a premium for their products. The reputation and warranty terms offered by the manufacturer can influence the decision to purchase a complete system versus individual components.
Case Studies on Cost-Effective Belt Scale Weighing System Implementations
Rio Tinto
Rio Tinto, a leading global mining company, implemented a belt scale weighing system in their iron ore operations in Western Australia. The system provided accurate measurements of ore extracted, leading to improved inventory management and process optimization. The conveyor belt scale price for the complete system, including high-capacity load cells and advanced integrators, was justified by the significant cost savings in material handling and processing efficiency.
Cargill
Cargill, an international food corporation, installed belt scale weighing systems in their grain processing facilities. The precise measurement of grain flow helped in maintaining product quality and consistency. By investing in a reliable weighing system, Cargill optimized their production processes and reduced waste, making the conveyor belt scale price a valuable investment.
LafargeHolcim
LafargeHolcim, a leading building materials company, used belt scale weighing systems in their cement plants. The accurate measurement of raw materials like limestone and clinker ensured optimal mixing ratios, enhancing product quality and reducing production costs. The initial conveyor belt scale price was offset by the savings in material costs and improved product quality.
BHP
BHP, a major player in the resources sector, implemented belt scale weighing systems in their coal mines. The systems provided real-time data on coal extraction rates, enabling better planning and resource allocation. Despite the high conveyor belt scale price, the system’s contribution to operational efficiency and cost management justified the investment.
ADM (Archer Daniels Midland Company)
ADM, a global food processing and commodities trading corporation, installed belt scale weighing systems in their oilseed processing plants. Accurate measurement of raw material flow improved process control and product yield. The conveyor belt scale price was a critical factor in achieving these operational efficiencies and cost reductions.
HeidelbergCement
HeidelbergCement, one of the world’s largest building materials companies, utilized belt scale weighing systems in their aggregate quarries. The systems ensured precise measurement of crushed stone and sand, facilitating better inventory management and sales accuracy. The investment in a high-quality weighing system, despite the significant conveyor belt scale price, resulted in improved operational performance and profitability.
The conveyor belt scale price is influenced by the quality and features of its components, the level of system integration, and the specific needs of the application. Understanding these factors helps in making informed decisions to implement cost-effective belt scale weighing systems that offer long-term value and efficiency across various industries.
Belt Conveyor Weighing System PDF: Conveyor Belt Scale Price
Availability and Importance of PDF Resources for Understanding Belt Conveyor Weighing Systems
PDF resources are invaluable for anyone involved in the operation, maintenance, or purchasing of belt conveyor weighing systems. These documents provide comprehensive information on various aspects of these systems, including their design, installation, calibration, and maintenance. Here’s why these resources are essential:
- Comprehensive Guides: PDFs offer detailed guides that cover every aspect of belt conveyor weighing systems. These guides typically include installation instructions, troubleshooting tips, maintenance schedules, and calibration procedures. Having access to such detailed information ensures that the system is set up and maintained correctly, leading to accurate and reliable performance.
- Educational Value: For new users or those unfamiliar with belt conveyor weighing systems, PDF resources serve as educational tools. They explain the fundamental principles behind the systems, the technology used, and how different components work together. This knowledge is crucial for making informed decisions about system selection and operation.
- Specification Sheets: Manufacturers often provide PDF specification sheets for their products. These sheets contain technical details about the components, such as load cells, speed sensors, and integrators. Understanding these specifications helps in comparing different products and choosing the one that best fits the operational requirements and budget.
- Case Studies and Application Notes: PDFs often include case studies and application notes that demonstrate how belt conveyor weighing systems are used in various industries. These real-world examples highlight the benefits and challenges of different systems, offering practical insights that can guide purchasing and operational decisions.
- Regulatory Compliance: PDF documents also provide information on regulatory standards and compliance requirements. Ensuring that the weighing system meets industry standards is crucial for legal and safety reasons. These resources help users stay informed about the latest regulations and how to comply with them.
- Ease of Access and Sharing: PDF files are easily accessible and can be shared across different platforms. This convenience allows team members to access critical information anytime, anywhere, facilitating better communication and collaboration within the organization.
Cost Implications of Purchasing Comprehensive Guides and Manuals
When considering the conveyor belt scale price, it is important to account for the cost of comprehensive guides and manuals. Here are some cost implications to consider:
- Initial Investment: Purchasing detailed guides and manuals often requires an initial investment. These documents can range from basic instruction manuals to comprehensive technical guides with in-depth explanations and advanced troubleshooting techniques. The cost of these resources can vary significantly based on their detail and the reputation of the provider.
- Quality of Information: Higher-priced guides typically offer more detailed and reliable information. They may include advanced troubleshooting tips, detailed maintenance schedules, and in-depth calibration procedures. Investing in high-quality manuals can reduce long-term costs by ensuring that the system is maintained correctly and operates efficiently.
- Training Costs: Comprehensive manuals can also serve as training materials for staff. Investing in detailed guides can reduce the need for expensive training programs, as employees can learn from the manuals. This can lead to significant cost savings in the long run.
- Operational Efficiency: Properly maintained and calibrated systems operate more efficiently and have a longer lifespan. Investing in good quality manuals ensures that the system is kept in optimal condition, reducing downtime and maintenance costs. This efficiency directly impacts the overall cost of the system over its operational life.
- Avoidance of Costly Mistakes: Detailed manuals help avoid costly mistakes during installation and maintenance. Incorrect setup or calibration can lead to inaccurate measurements, resulting in financial losses. Comprehensive guides provide step-by-step instructions that help prevent such errors.
Free versus Paid PDF Resources and Their Impact on Overall System Cost
When it comes to PDF resources, both free and paid options are available. Each has its advantages and disadvantages, and their impact on the overall system cost can vary.
- Free PDF Resources: Many manufacturers and industry organizations offer free PDF resources. These can include basic user manuals, installation guides, and regulatory compliance information. While free resources are budget-friendly, they may lack the depth and detail required for complex systems.
- Paid PDF Resources: Paid PDF resources are often more comprehensive and detailed. They can include advanced troubleshooting guides, detailed calibration procedures, and extensive maintenance schedules. The higher quality and depth of information provided in paid resources can justify the initial cost by ensuring more accurate and reliable system operation.
- Impact on System Cost: Investing in paid resources can lead to long-term cost savings. High-quality guides ensure that the system is installed and maintained correctly, reducing the likelihood of costly repairs and downtime. They also provide valuable training material for staff, reducing the need for external training programs.
- Access to Expertise: Paid resources often include insights from industry experts and real-world case studies. This expert knowledge can be invaluable for optimizing system performance and troubleshooting complex issues. Access to such expertise can significantly enhance the efficiency and reliability of the weighing system.
- Update and Support: Paid resources may come with additional benefits such as regular updates and customer support. As technology and regulations evolve, having access to updated information ensures that the system remains compliant and up-to-date with the latest industry standards.
- Customization and Specificity: Paid resources can be tailored to specific systems and applications, providing more relevant and useful information. Custom manuals that address the unique needs of a particular operation can greatly enhance the effectiveness of the weighing system.
PDF resources are essential for understanding and effectively using belt conveyor weighing systems. While free resources offer basic information, investing in paid, comprehensive guides can lead to significant long-term cost savings by ensuring proper system setup, maintenance, and operation. When considering the conveyor belt scale price, it is important to factor in the cost of these valuable resources to ensure optimal performance and efficiency.
Belt Weigher: Conveyor Belt Scale Price
Definition and Usage of Belt Weighers in Various Industries
A belt weigher, also known as a conveyor belt scale, is a device that continuously measures the mass of the material being transported on a conveyor belt. These systems are essential in various industries where precise measurement of bulk materials is crucial for operational efficiency and cost management. Here’s a detailed look at the definition and usage of belt weighers in different sectors:
- Mining: In the mining industry, belt weighers are used to measure the amount of ore and other raw materials being transported. Accurate measurement is critical for inventory management, ensuring that the correct quantities are processed and sold.
- Agriculture: In agriculture, belt weighers help in monitoring the flow of grains, seeds, and other agricultural products. This is important for both harvest management and processing operations, ensuring that quantities are recorded accurately for sales and storage.
- Food Processing: Belt weighers are used extensively in the food processing industry to ensure that ingredients are measured accurately during production. This is crucial for maintaining product quality and consistency.
- Construction: In the construction industry, belt weighers are used to measure materials like sand, gravel, and cement. Accurate measurement ensures that the correct mix of materials is used, which is vital for the integrity of construction projects.
- Chemicals: The chemical industry uses belt weighers to measure raw materials and products in their processes. Precise measurement is necessary to maintain the correct chemical formulations and to ensure safety and compliance with regulations.
- Recycling: Belt weighers are also used in recycling operations to measure the amount of material being processed. This helps in tracking the efficiency of recycling operations and managing inventory.
Pricing Trends and Factors Affecting Belt Weigher Prices
When evaluating the conveyor belt scale price, several factors come into play. Understanding these factors can help in making an informed purchasing decision:
- Technology: The type and level of technology used in a belt weigher significantly influence its price. Advanced systems with higher accuracy and more features, such as real-time data logging and remote monitoring, tend to be more expensive.
- Capacity: The capacity of the belt weigher, in terms of the maximum load it can measure, affects its price. Systems designed for heavy-duty industrial use are typically more costly than those intended for lighter loads.
- Accuracy: The accuracy of a belt weigher is a crucial factor. High-precision systems that can measure small variances in weight are more expensive than those with standard accuracy levels.
- Durability and Materials: The materials used in the construction of the belt weigher, as well as its durability, impact the price. Systems made from high-grade materials that can withstand harsh industrial environments cost more.
- Brand and Manufacturer: The reputation of the brand and the manufacturer’s support services can influence the price. Established brands with a history of reliable products and good customer support may charge a premium.
- Installation and Maintenance: The cost of installation and the level of maintenance required also affect the overall price. Some systems might have higher upfront costs but lower long-term maintenance expenses, making them more cost-effective over time.
Comparison of Belt Weigher Prices from Different Brands
To provide a clearer picture of the conveyor belt scale price from various brands, here is a comparison table highlighting some popular models and their price ranges:
Detailed Analysis
- Siemens Milltronics MSI: Known for its robustness and high capacity, the Milltronics MSI model is designed for heavy-duty applications in mining and bulk material handling. Its high accuracy and durability justify its higher price range.
- Schenck Multibelt® BMP: This model offers excellent accuracy and is suitable for a variety of industries including food processing and chemicals. Its mid-range price reflects its balance between performance and cost.
- Thermo Fisher Ramsey Series 20-30: Popular in industries like agriculture and recycling, this model provides reliable performance at a competitive price. It is a good choice for operations that require moderate capacity and high accuracy.
- Avery Weigh-Tronix E-90 Belt Scale: Ideal for medium-sized operations, this model offers good accuracy and capacity at a lower price point. It is well-suited for applications where cost is a significant consideration without compromising too much on performance.
- Rice Lake BCi: This entry-level model is perfect for smaller operations with lower capacity requirements. It provides reliable performance at an affordable price, making it a good option for businesses on a tighter budget.
When considering the conveyor belt scale price, it is essential to evaluate the specific needs of your operation and the features required from the belt weigher. The price can vary significantly based on the technology, capacity, accuracy, and brand reputation. By understanding these factors and comparing different models, businesses can make informed decisions that balance cost with performance, ensuring they choose the most suitable belt weigher for their needs.
Load Cell for Conveyor Belt: Conveyor Belt Scale Price
Explanation of the Role of Load Cells in Conveyor Belt Systems
Load cells are critical components in conveyor belt systems, serving as the primary sensing element that measures the weight of the material being transported. These devices convert the force exerted by the load into an electrical signal, which can then be processed to determine the weight. Here are ten key roles of load cells in conveyor belt systems:
- Weight Measurement: The primary function of load cells is to measure the weight of materials on the conveyor belt accurately. This measurement is crucial for monitoring and controlling the material flow in various industrial processes.
- Inventory Management: Load cells help in tracking the amount of material being transported, which is essential for effective inventory management. Accurate weight measurements ensure that inventory levels are maintained correctly, preventing shortages or overstocking.
- Quality Control: In industries such as food processing and pharmaceuticals, load cells are used to ensure that products meet specific weight criteria. This helps in maintaining consistent product quality and compliance with industry standards.
- Process Optimization: By providing real-time weight data, load cells enable operators to optimize the material flow and improve the efficiency of the conveyor system. This optimization can lead to increased productivity and reduced operational costs.
- Belt Tension Monitoring: Load cells can be used to monitor the tension in the conveyor belt, ensuring that it is operating within the recommended limits. Proper belt tension is crucial for the longevity and performance of the conveyor system.
- Material Distribution: In applications where material needs to be distributed evenly across different processing stages, load cells ensure that the correct amount of material is delivered to each stage. This is particularly important in batch processing operations.
- Safety: Load cells play a role in the safety of conveyor belt systems by preventing overloading. Overloading can cause damage to the conveyor belt and other components, leading to costly repairs and downtime.
- Automated Control Systems: Load cells are often integrated into automated control systems that regulate the speed and operation of the conveyor belt based on the weight of the material. This integration enhances the overall efficiency and reliability of the system.
- Data Collection and Analysis: The data collected by load cells can be used for analysis and reporting purposes. This data provides insights into the performance of the conveyor system and helps in making informed decisions for maintenance and upgrades.
- Cost Efficiency: By providing accurate and reliable weight measurements, load cells contribute to the overall cost efficiency of the conveyor belt system. They help in reducing material wastage, optimizing resource use, and minimizing downtime.
Price Range for Load Cells Used in Conveyor Belt Applications
The conveyor belt scale price can vary widely based on the specific type and configuration of load cells used. Here is an overview of the price range for load cells commonly used in conveyor belt applications:
Factors Influencing Load Cell Pricing
Several factors influence the pricing of load cells, and understanding these can help in making an informed purchase decision:
- Quality: The overall build quality of the load cell significantly impacts its price. High-quality load cells made from robust materials and featuring advanced technologies tend to be more expensive but offer greater reliability and longevity.
- Accuracy: The accuracy of a load cell, often expressed as a percentage of full scale, is a crucial factor in its pricing. Load cells with higher accuracy ratings are generally more expensive as they provide more precise measurements.
- Capacity: The load capacity of the load cell affects its price. Load cells designed to measure higher weights typically cost more due to the additional material and engineering required to ensure accurate readings under heavy loads.
- Brand: The reputation of the manufacturer can also influence the price. Established brands with a history of producing reliable and accurate load cells may charge a premium for their products.
- Technology: Load cells that incorporate advanced technologies, such as wireless communication or digital output, are generally more expensive than their basic counterparts. These technologies offer additional features and benefits that justify the higher price.
- Environmental Resistance: Load cells designed to withstand harsh environmental conditions, such as extreme temperatures, moisture, or chemical exposure, tend to be more expensive. These load cells are built with specialized materials and coatings to ensure durability.
- Certifications and Compliance: Load cells that meet specific industry standards or certifications, such as ISO, OIML, or NTEP, often have higher prices. These certifications ensure that the load cells meet stringent accuracy and performance requirements.
- Customization: Custom-designed load cells tailored to specific applications or requirements can also be more expensive. Customization ensures that the load cell meets the exact needs of the application, offering optimal performance.
Load cells play a vital role in conveyor belt systems by providing accurate weight measurements essential for various industrial applications. The conveyor belt scale price is influenced by factors such as quality, accuracy, capacity, brand, technology, environmental resistance, certifications, and customization. By understanding these factors and comparing different options, businesses can select the most suitable load cell for their needs, ensuring efficient and reliable operation of their conveyor belt systems.
Ready to enhance your operations? Contact us now!
FAQs about Conveyor Belt Scale Price
A belt scale is an essential device installed on conveyor belts to measure the rate of material flow and the total amount of material transported over a specific period. It operates by gauging the load on the conveyor belt through a weighing bridge, allowing for real-time measurement of the conveying rate and total material throughput. Belt scales are crucial in various industries, such as mining, agriculture, and bulk material handling, for inventory control, production management, and optimizing operational efficiency. By providing accurate and reliable data, belt scales help ensure that operations run smoothly and cost-effectively.
The weight of a conveyor belt per meter depends on its width, thickness, material composition, and structure. On average, a standard, medium-duty conveyor belt used for general purposes weighs about 10 kg per meter for a belt that is 800 mm wide. However, heavier duty belts designed for specific tasks or to convey heavy materials can weigh more, possibly up to 30 kg per meter or more for the same width. The weight is significant for calculating the total load on the conveyor and ensuring the equipment is suitable for the expected operational demands.
To calculate the tph (tonnes per hour) of a belt conveyor, you can use the following formula:
TPH=(W×L)/(1000×3600)
Where:
TPH is the tonnes per hour.
W is the width of the belt in meters.
L is the length of the conveyor belt in meters.
Conveyor belts are typically made from various types of rubber, each chosen for its properties that meet specific operational needs. The most common types of rubber used include:
Natural Rubber (NR): Known for its flexibility and durability, it’s often used in conveyor belts for general purposes.
Styrene-Butadiene Rubber (SBR): Offers excellent abrasion resistance and is used in many standard conveyor belts.
Nitrile Butadiene Rubber (NBR): Known for its resistance to oil, fats, and other chemicals, making it suitable for conveyor belts used in the food processing industry or places where oil resistance is crucial.
Ethylene Propylene Diene Monomer (EPDM): Exhibits exceptional resistance to weathering, heat, and ozone, suitable for outdoor or high-temperature environments.
The choice of rubber is critical to ensure the conveyor belt’s performance, longevity, and suitability for the specific materials it will carry.
Last Updated on July 16, 2024 by Jordan Smith
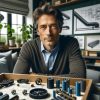
Jordan Smith, a seasoned professional with over 20 years of experience in the conveyor system industry. Jordan’s expertise lies in providing comprehensive solutions for conveyor rollers, belts, and accessories, catering to a wide range of industrial needs. From initial design and configuration to installation and meticulous troubleshooting, Jordan is adept at handling all aspects of conveyor system management. Whether you’re looking to upgrade your production line with efficient conveyor belts, require custom conveyor rollers for specific operations, or need expert advice on selecting the right conveyor accessories for your facility, Jordan is your reliable consultant. For any inquiries or assistance with conveyor system optimization, Jordan is available to share his wealth of knowledge and experience. Feel free to reach out at any time for professional guidance on all matters related to conveyor rollers, belts, and accessories.