Conveyor Belt Seam And Lacing for Longevity
A conveyor belt seam is more than just connections between two ends of a conveyor belt; they are pivotal in maintaining the integrity, functionality, and longevity of the entire conveyor system. A well-executed seam ensures that the conveyor belt operates smoothly, withstands the operational load, and minimizes the risk of breakdowns. This introduction sheds light on the critical role of conveyor belt seams, emphasizing their importance in ensuring operational continuity, safety, and the overall efficiency of conveyor systems.
Navigating the Landscape of Conveyor Belt Seam Types
The world of conveyor belt seams is diverse, with each type of seam catering to specific operational needs, material types, and environmental conditions. Understanding the nuances of each seam type is crucial for making informed decisions that align with the operational requirements and longevity of the conveyor system.The type of conveyor belt seam (or joint) is a critical aspect of conveyor belt design and application, affecting its durability, strength, and suitability for various operational environments. A seam is where two ends of a conveyor belt are joined together. The choice of seam type can significantly impact the belt’s performance, including its speed, load capacity, and the type of materials it can transport.Conveyor belt seam lacing is a method used to join the ends of a conveyor belt. Various types of lacing offer different benefits depending on the application. Below are detailed descriptions of common types of conveyor belt seams:
Overlapped Joints: These are formed by overlapping the ends of the belt and are commonly used for lightweight belts or in applications where a smooth joint is not critical. They are relatively easy to install but may not be suitable for high-tension applications.
Top-Skived Lap Joints: In this type, the top surface of one end of the belt is skived or thinned down before overlapping with the other end. This creates a smoother joint compared to a standard overlapped joint and is suitable for applications where the belt passes over small pulleys or where a smooth surface is essential.
Butt/Tape Joints: This type involves butting the ends of the belt together and bonding them with a special tape. Butt/tape joints provide a very flat and smooth joint surface, making them ideal for applications where the belt seam passes over rollers or sliders. They are also bi-directional, allowing the belt to run in either direction.
Fully Top-Skived, Grain Side, Tape on Top Joints: These are typically used for cloth belts. The grains around the joint are removed, and tape is placed on the grain side, providing a smooth surface and reducing the risk of the joint catching or snagging on parts of belt conveyor system.
Mechanical Fastener Seams:Mechanical fasteners join the ends of the belt using metal or plastic hinges or plates. This seam type is versatile and can be installed on-site, which is convenient for repairs or when welding is not possible.
Vulcanized Seams:Vulcanization uses heat and pressure to chemically bond the belt ends together, creating a seamless and strong joint. There are two main types: hot and cold vulcanization.
Metal Lacing: Metal lacing involves joining the belt ends with metal wires or strips. This method is often used for belts in light-duty applications or where a low-profile joint is needed.
Plastic Rivet Seams: Plastic rivet seams use plastic or nylon rivets pushed through the belt ends and melted or flattened to create a bond. This method is suitable for light to medium-duty applications.
Peeling Seams: Peeling seams involve skiving or peeling back layers of the belt material and bonding them together, creating a tapered joint that reduces thickness and provides a smooth transition.
Finger Seams: Finger seams are created by cutting the ends of the belts into interlocking ‘fingers’ and bonding them together, usually through vulcanization. This method is often used for belts that require high flexibility and strength at the joint.
Each conveyor belt seam type has its specific applications, advantages, and limitations. The choice of seam depends on various factors, including the operational environment, the type of materials being conveyed, the speed and load of the conveyor, and maintenance and repair considerations.

A Detailed Description of Conveyor Belt Seam’s Advantage And Disadvantage
Each type of conveyor belt seam has distinct advantages that make it suitable for different applications, operational requirements, and environmental conditions. Here’s a detailed exploration of the advantages of various conveyor belt seam types:
1. Mechanical Fastener Seams
- Flexibility in Installation and Repair: They can be installed or repaired on-site without specialized equipment, making them ideal for applications where downtime needs to be minimized.
- Versatility: Suitable for a wide range of belt materials and thicknesses, including those where vulcanization is not viable.
- Adjustability: They allow for easy re-tensioning and adjustments to the belt length as required over time.
- Disadvantages: The fasteners may catch on product or conveyor components, potentially damaging the belt or the conveyed materials. They also may not be suitable for conveyor belts running over small pulley diameters.
2. Vulcanized Seams
- Durability and Strength: Vulcanized seams offer superior durability and strength compared to other types, making them suitable for high-tension and high-load applications.
- Smooth Operation: The seamless finish reduces noise and vibration during operation, which is beneficial for the longevity of the conveyor system and the comfort of personnel.
- Reduced Maintenance: With no mechanical parts to wear out or adjust, vulcanized seams often require less maintenance over the belt’s lifespan.
- Disadvantages: Requires specialized equipment and skilled technicians. The process is more time-consuming and less flexible for on-site repairs.
3. Metal Lacing
- Low Profile: The seam is relatively flat, which minimizes disruptions to the conveyed material and reduces wear on the seam itself.
- Speed of Installation: Metal lacing can be quickly installed with basic tools, reducing downtime during belt replacement or repair.
- Suitability for Light-Duty Applications: Ideal for applications where the belt is not subjected to high loads or tensions.
- Disadvantages: Not suitable for heavy-duty applications. The metal can wear over time, potentially damaging the belt or the conveyed material.

Metal Lacing
4. Plastic Rivet Seams
- Resistance to Corrosion: Unlike metal fasteners, plastic rivets do not corrode, making them suitable for damp or corrosive environments.
- Smooth Transition: The seam provides a smoother transition than metal fasteners, reducing the risk of damage to the conveyed materials or the conveyor system.
- Ease of Installation: Plastic rivet seams can be installed with simple tools, making them a practical option for on-site repairs.
- Disadvantages: Not as strong as vulcanized seams and may not be suitable for high-speed or high-load applications.
5. Peeling Seams
- Reduced Thickness and Weight: By reducing the thickness at the seam, peeling seams can decrease the overall weight of the belt, leading to energy savings and reduced operational costs.
- Smooth Surface: The seamless transition is ideal for applications requiring a smooth belt surface, such as the transportation of sensitive or delicate materials.
- Noise Reduction: The lack of a bulky seam reduces noise during operation, contributing to a more pleasant working environment.
- Disadvantages: Requires precise preparation and skill to ensure a strong, durable bond.
6. Finger Seams
- High Flexibility: Finger seams allow for a high degree of flexibility at the joint, which is beneficial for conveyor belts that navigate around small pulleys.
- Strong Bond: When vulcanized, finger seams provide a strong bond that can handle high tension and load, making them suitable for demanding applications.
- Smooth Operation: The interlocking fingers create a smooth surface that minimizes disruptions to the flow of conveyed materials and reduces wear on the seam.
- Disadvantages: Requires precise cutting and skilled labor to prepare and bond the belt ends effectively.
Choosing the right type of conveyor belt seam depends on balancing these advantages against the specific requirements and challenges of the application, including the type of materials being conveyed, environmental conditions, operational speeds, and load capacities.

Conveyor Belt Seam Replacement: Ensuring Seamless Operations
Mastering the Art of Conveyor Belt Seam Replacement
Conveyor belt seam replacement is a critical maintenance task that, when done correctly, can significantly extend the life of the conveyor belt and ensure seamless operations. This section provides a comprehensive guide on replacing conveyor belt seams, with a focus on minimizing downtime and preventing future seam failures.
- Preparation: Before starting the seam replacement, it’s crucial to properly prepare the belt ends. This involves cleaning the areas to be joined, ensuring they are free from dirt, grease, or any other contaminants. The belt ends must be cut straight and squared to ensure a proper fit.
- Removal of the Old Seam: Carefully remove the old seam, taking care not to damage the belt. For mechanical fasteners, this may involve unfastening or cutting the fasteners. For vulcanized seams, this may involve carefully cutting and peeling the vulcanized layer.
- Installation of the New Seam: Depending on the type of seam being used, this step will vary. For mechanical fasteners, align the belt ends and install the new fasteners according to the manufacturer’s instructions. For vulcanized seams, apply the bonding material to the belt ends, carefully align them, and apply pressure to bond them together. For tape seams, apply the tape to the butted belt ends, ensuring it is centered and that there are no wrinkles or air bubbles.
- Curing and Finishing: Allow any bonding materials or adhesives to cure fully before putting the belt back into operation. This ensures a strong and durable bond. Once the seam is cured, inspect it carefully to ensure it is properly aligned and that there are no defects.
- Tips for a Strong and Durable Seam Replacement:
- Always use high-quality materials for the seam replacement, whether it’s mechanical fasteners, bonding materials, or tape.
- Follow the manufacturer’s instructions carefully, especially when it comes to curing times for adhesives or vulcanizing materials.
- Regularly inspect the seam after replacement, especially during the first few days of operation, to ensure it is holding up and that there are no signs of failure.
A well-executed conveyor belt seam replacement not only ensures the longevity of the belt but also contributes to the smooth and efficient operation of the entire conveyor system. By following these steps and tips, you can master the art of conveyor belt seam replacement, ensuring seamless operations and minimizing the risk of unexpected downtime.
Conveyor Belt Seam Endless Splices
Conveyor belt seams, specifically endless splices, represent a sophisticated technique designed to create a seamless joint in conveyor belts, ensuring a smooth, uninterrupted surface. This method is pivotal in maintaining the belt’s integrity and functionality over time. Endless splicing involves joining the two ends of a conveyor belt together without the presence of any visible seam or gap, effectively making the belt ‘endless’. This is achieved through various splicing methods, including hot vulcanization, cold vulcanization, or mechanical fastening, each with its unique benefits and applications.
Hot vulcanization creates the splice through the application of heat and pressure, facilitating a chemical bonding process that results in a splice as strong as the belt itself. This method is highly regarded for its durability and resistance to wear and tear, making it ideal for heavy-duty applications.
Cold vulcanization, on the other hand, uses chemical adhesives to bond the belt ends at room temperature. This method is quicker and requires less equipment than hot vulcanization, offering a practical solution for rapid repairs or when the use of heat is not feasible.
Mechanical fastening involves the use of metal fasteners or plastic rivets to join the belt ends. This method allows for easy installation and quick repairs but may not provide the same level of smoothness and durability as vulcanized splices.
The choice of endless splice method depends on various factors, including the type of material being conveyed, the operational environment, and the specific requirements of the conveyor system. Properly executed endless splices contribute to the efficiency of the conveyor system by minimizing belt misalignment and reducing the risk of snagging or catching on conveyed materials. Additionally, a well-spliced belt can significantly extend the life of the conveyor system, reduce maintenance downtime, and improve overall operational efficiency.
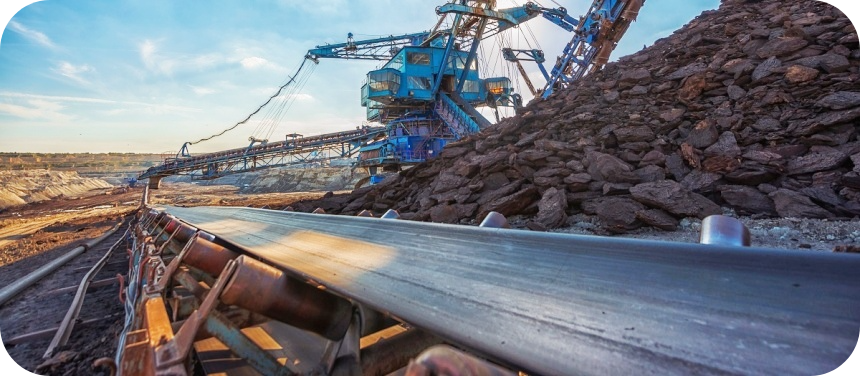
DIY Conveyor Belt Seam: A Handy Approach
DIY conveyor belt seams offers a practical solution for minor repairs or temporary fixes. It’s a cost-effective approach that can be done in-house, reducing the need for professional services for small-scale issues. This section explores the tools, materials, and techniques necessary for effective DIY conveyor belt seams
Tools and Materials Required
- Seaming Tools: Basic tools include a sharp knife, a ruler, and a marker for precise cutting and alignment.
- Adhesive Solutions: Industrial-grade adhesives or rubber cement suitable for conveyor belt materials.
- Seam Preparation Materials: Sandpaper or a grinding tool for preparing the belt edges.
- Protective Gear: Safety gloves and goggles for personal protection during the seaming process.
Step-by-Step DIY Seaming Process
- Belt Inspection: Examine the conveyor belt to locate the damaged area and assess the extent of the repair needed.
- Surface Preparation: Use sandpaper or a grinding tool to create a smooth, clean surface along the edges of the seam.
- Cutting and Alignment: Measure and cut the belt ends precisely, ensuring they align perfectly for a seamless joint.
- Applying Adhesive: Apply a layer of adhesive evenly on both edges of the belt. Wait for the adhesive to become tacky.
- Joining the Belt: Carefully align and press the belt ends together, ensuring a tight and even seam.
- Curing: Allow adequate time for the adhesive to cure and set, following the manufacturer’s instructions.
Finding Conveyor Belt Seam Lacing Services Near You
Importance of Professional Conveyor Belt Lacing Services
Professional conveyor belt seam lacing services are crucial for ensuring the longevity and efficiency of conveyor systems. Expert seam installation and maintenance play a vital role in preventing downtime and extending the life of the conveyor belt.
Locating Conveyor Belt Lacing Services
- Online Directories and Search Engines: Utilize online resources to find local conveyor belt lacing services.
- Industry Recommendations: Seek recommendations from industry peers or associations for reputable service providers.
- Manufacturer Referrals: Contact conveyor belt manufacturers for recommended lacing service providers.
Evaluating Service Providers
- Experience and Expertise: Look for providers with a proven track record and expertise in conveyor belt lacing.
- Quality of Service: Assess the quality of service based on customer reviews, case studies, and testimonials.
- Range of Services: Ensure the provider offers a comprehensive range of services, including installation, repair, and maintenance.
- Response Time and Availability: Consider the provider’s responsiveness and availability for emergency repairs.
Cost-Effectiveness
- Compare quotes from different service providers to ensure competitive pricing.
- Consider the long-term benefits of quality lacing services against the initial cost.
Building a Relationship with Service Providers
- Establish a long-term relationship with a reliable service provider for ongoing maintenance and support.
- Regularly scheduled maintenance services can prevent unexpected breakdowns and extend the life of the conveyor belt.
Finding the right conveyor belt lacing services is essential for maintaining the operational integrity of conveyor systems. A combination of expert installation, regular maintenance, and timely repairs ensures the seamless functioning of conveyor belt, contributing to the overall productivity and efficiency of industrial operations.
Conveyor Belt Seam Fasteners and Lacing Pins: The Nuts and Bolts of Seaming
Conveyor Belt Seam: Securing Durability with Fasteners and Lacing Pins
In the realm of conveyor belt maintenance and repair, the role of fasteners and lacing pins is indispensable. These small yet crucial components, often referred to as the nuts and bolts of conveyor belt seam, are fundamental in ensuring the durability and strength of belt seams. This section delves deep into the world of conveyor belt fasteners and lacing pins, exploring their types, applications, and the critical considerations involved in selecting the right ones for your conveyor system.
The Critical Role of Fasteners and Lacing Pins in Conveyor Belt Seams
Conveyor belt fasteners and lacing pins are more than mere accessories; they are the linchpins that hold the entire conveyor system together. They ensure that the belt seams are secure, minimizing the risk of seam failure, which can lead to operational disruptions and potential safety hazards. The choice of fasteners and lacing pins directly impacts the seam’s strength, the belt’s alignment, and the overall efficiency of the conveyor system.
Types of Conveyor Belt Fasteners and Lacing Pins
The market offers a wide array of fasteners and lacing pins, each designed to meet specific operational needs and belt types. These include:
- Alligator Lacing: Ideal for light- and medium-duty belts, offering a strong grip and easy installation.
- Plate Fasteners: Suitable for heavy-duty applications, providing superior holding strength and durability.
- Spiral Lace: Perfect for belts that require a seamless joint, commonly used in food processing or packaging applications.
- Rivet Hinged Fasteners: Known for their high tensile strength, suitable for belts subjected to high loads or demanding conditions.
Selecting the Right Fasteners and Lacing Pins
The selection of the appropriate fasteners and lacing pins is a decision that requires careful consideration of several factors:
- Belt Type and Material: The material and thickness of the belt dictate the type of fasteners or lacing pins needed. For instance, thicker, heavy-duty belts require fasteners that can provide a stronger grip without damaging the belt.
- Load Capacity: The operational load of the conveyor system determines the strength required from the fasteners and lacing pins. Higher loads necessitate fasteners with higher tensile strength.
- Operational Environment: Factors such as exposure to moisture, chemicals, or extreme temperatures influence the choice of fasteners and lacing pins. Corrosion-resistant materials or specialized coatings might be necessary in harsh environments.
Installation and Maintenance
Proper installation and regular maintenance of fasteners and lacing pins are crucial for ensuring the longevity and efficiency of the conveyor belt seams. Incorrect installation can lead to misalignment, premature wear, or seam failure. Regular inspections can help identify potential issues early, allowing for timely maintenance or replacement.
Conveyor belt fasteners and lacing pins play a pivotal role in the functionality and durability of conveyor belt seams. Their proper selection, installation, and maintenance are crucial in ensuring the seamless operation of the conveyor system, minimizing downtime, and maintaining operational efficiency.
Conveyor Belt Seam Lacing Wire and Flexco Belt Lacing: Advanced Seaming Solutions
Embracing Innovation with Lacing Wire and Flexco Solutions
The evolution of conveyor belt seaming technology has brought forth advanced solutions like conveyor belt lacing wire and Flexco belt lacing, setting new standards in seam durability, ease of installation, and operational efficiency. This section provides an overview of these innovative seaming solutions, highlighting their roles, benefits, and the value they add to different types of conveyor belts.
Conveyor Belt Lacing Wire: Reinforcing Seams with Precision
Conveyor belt lacing wire is a specialized solution designed to reinforce belt seams, particularly in high-tension applications. It offers a balance between flexibility and strength, ensuring that the seam can withstand operational stress while maintaining the belt’s integrity. The lacing wire is meticulously crafted to ensure a seamless fit, reducing the risk of snagging or catching on conveyor components.
Flexco Belt Lacing: The Industry Benchmark
Flexco belt lacing is synonymous with quality and reliability in the conveyor belt industry. Known for its durability and ease of installation, Flexco solutions cater to a wide range of belt types and operational requirements. The key features of Flexco belt lacing include:
- Durability: Engineered to withstand harsh operational conditions, reducing the need for frequent maintenance or replacement.
- Ease of Installation: Designed for quick and straightforward installation, minimizing downtime and ensuring a strong, reliable seam.
- Compatibility: Available in various sizes and materials, Flexco belt lacing is compatible with a wide array of belt types, from light-duty to heavy-duty applications.
Selecting the Right Seaming Solution
The choice between conveyor belt lacing wire and Flexco belt lacing depends on several factors:
- Operational Requirements: Consider the load capacity, speed, and environmental conditions of the conveyor system.
- Belt Type and Material: Ensure that the seaming solution is compatible with the belt material and suitable for the belt’s thickness and width.
- Maintenance and Longevity: Opt for solutions that offer ease of maintenance and promise longevity, ensuring that the conveyor system operates smoothly over an extended period.
Installation and Maintenance Best Practices
Proper installation is crucial for the performance of conveyor belt lacing wire and Flexco belt lacing. Follow the manufacturer’s guidelines meticulously, and ensure that the tools and techniques used align with the specific requirements of the seaming solution. Regular inspections and maintenance are essential in preserving the integrity of the seam and the overall health of the conveyor system.
Conveyor belt lacing wire and Flexco belt lacing represent the forefront of conveyor belt seam technology. Their introduction into conveyor systems marks a significant leap in seam durability, installation ease, and operational efficiency. By selecting the appropriate seaming solution and adhering to best practices in installation and maintenance, conveyor system operators can ensure seamless operations, reduce downtime, and maintain the highest standards of efficiency and safety.
Secure your success with our premium conveyor belts – don’t wait!
FAQs about Conveyor Belt Seam
Conveyor belts can be joined or spliced using various methods, depending on the type of belt and the specific requirements of the conveyor system. The main methods include:
Mechanical Fastening: This involves using metal fasteners or hinges to join the ends of the belt. It’s a quick and easy method suitable for temporary or field repairs.
Vulcanization: This is a more permanent method where the belt ends are joined together using heat and pressure. Vulcanization can be done in two ways。
Hot Vulcanization: Uses heat and pressure to bond the belt ends together, creating a strong and seamless joint.
Cold Vulcanization: Uses chemicals and pressure to bond the belt ends at room temperature.
Adhesive Bonding: This method uses a special adhesive to bond the belt ends together. It’s suitable for lightweight belts and applications where metal fasteners are not desirable.
Conveyor belt splicing is the process of joining two pieces of a conveyor belt together, often to make a longer belt or to repair a damaged belt. Splicing ensures that the belt maintains its strength and structural integrity. The most common splicing methods are mechanical fastening, vulcanization (hot and cold), and adhesive bonding.
The different types of belt joints include:
Mechanical Joints: These involve using metal fasteners or hinges.
Vulcanized Joints: These can be further divided into.
Hot Vulcanized Joints: Created through a process of heat and pressure.
Cold Vulcanized Joints: Made using adhesive and pressure at room temperature.
Adhesive Joints: These use a special adhesive to bond the belt ends.
Finger Joints: A type of joint where the ends of the belt are cut in a finger-like shape and then bonded together, often used in vulcanized splicing.
There isn’t a universal “formula” for conveyor belt splicing as the process varies greatly depending on the type of belt, the method of splicing, and the specific application. However, the process generally involves the following steps:
Preparing the Belt Ends: Squaring the belt ends, stripping layers if necessary, and cutting to the desired shape (e.g., finger shape for finger splicing).
Applying Splicing Material: Depending on the method, this could involve applying adhesive, fasteners, or preparing the belt ends for vulcanization.
Joining the Belt Ends: This could involve pressing the ends together under heat and pressure (vulcanization) or mechanically fastening them.
Curing the Splice: For vulcanized splices, this involves allowing the splice to cool under pressure to ensure a strong bond.
Last Updated on June 6, 2024 by Jordan Smith
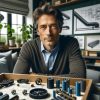
Jordan Smith, a seasoned professional with over 20 years of experience in the conveyor system industry. Jordan’s expertise lies in providing comprehensive solutions for conveyor rollers, belts, and accessories, catering to a wide range of industrial needs. From initial design and configuration to installation and meticulous troubleshooting, Jordan is adept at handling all aspects of conveyor system management. Whether you’re looking to upgrade your production line with efficient conveyor belts, require custom conveyor rollers for specific operations, or need expert advice on selecting the right conveyor accessories for your facility, Jordan is your reliable consultant. For any inquiries or assistance with conveyor system optimization, Jordan is available to share his wealth of knowledge and experience. Feel free to reach out at any time for professional guidance on all matters related to conveyor rollers, belts, and accessories.