Conveyor Belt Sensors | Monitoring Belt Conveyors
In the realm of industrial automation, conveyor belt systems stand as the backbone of production lines, facilitating the seamless movement of goods across various stages of manufacturing and packaging. Integral to the optimization and safety of these systems are conveyor belt sensors, sophisticated devices engineered to monitor and regulate the operational dynamics of conveyor belts. These sensors not only ensure the smooth and efficient flow of materials but also play a crucial role in safeguarding the machinery and the workforce from potential accidents and malfunctions. By providing real-time data on speed, alignment, and other critical parameters, conveyor belt sensors empower operators to maintain optimal performance levels, significantly enhancing both safety and productivity in industrial settings. Their importance cannot be overstated, as they directly contribute to minimizing downtime and maximizing output, making them indispensable in the modern industrial landscape.
Types of Conveyor Belt Sensors
The integration of conveyor belt sensors into conveyor systems has revolutionized the way industries monitor and control the movement of materials. These sensors are pivotal in ensuring the efficiency, safety, and reliability of conveyor operations. Let’s delve into the various types of sensor conveyor belt and understand their specific roles and benefits.
Conveyor Belt Speed Sensor
Conveyor belt sensors can monitor and control various parts of the conveyor belt, including its speed, temperature and position.Conveyor belt speed sensors are designed to accurately monitor the speed of a conveyor belt. These sensors work by detecting the rotational speed of the rollers or by using optical or magnetic encoders to measure the speed of the conveyor belt directly. The primary applications of speed sensors include:
- Ensuring Consistent Product Flow: By monitoring the speed, operators can adjust the conveyor to maintain a steady flow of products.
- Preventing Overloads: Speed sensors help in identifying slowdowns which might indicate overloads or potential jams.
- Energy Efficiency: By optimizing the speed, these sensors contribute to energy savings.
- Safety: Speed sensors can trigger alarms if the conveyor operates outside of the designated speed range, preventing potential accidents.
- Function: The primary function of a conveyor belt speed sensor is to measure the speed at which the conveyor belt operates. This measurement ensures that the conveyor belt runs within the desired speed parameters, maintaining efficient and safe operation.
- Example Products: Popular conveyor belt speed sensors include the Doppler radar-based speed sensors and optical speed sensors. These sensors offer high accuracy and reliability, making them suitable for demanding industrial environments.
Conveyor Belt Zero Speed Sensor
Conveyor belt zero speed sensors play a critical role in detecting the halt or zero movement of a conveyor belt, which is crucial for both safety and maintenance. These sensors are typically used to:
- Prevent Damage: Automatically shut down the system to avoid damage to the goods or the conveyor itself.
- Safety Protocols: Trigger safety mechanisms to protect the workforce in case of unexpected stoppages.
- Maintenance Alerts: Indicate when the conveyor has stopped for maintenance teams to inspect and address any issues.
- Operational Efficiency: Ensure that the conveyor is only active when necessary, saving energy and reducing wear.
- Function: A zero speed sensor detects when the conveyor belt has stopped or is moving at an extremely slow speed. This functionality is crucial for identifying potential issues such as belt jams or motor failures.
- Example Products: Commonly used zero speed sensors include inductive proximity sensors and magnetic proximity sensors. These sensors are designed to be robust and reliable, capable of functioning in harsh industrial conditions.
Conveyor Belt Stop Sensor
Conveyor belt stop sensors are essential safety devices that are integrated into conveyor control systems. They are designed to bring the conveyor to a halt in emergency situations or when a specific condition triggers the need for stopping. The integration of these sensors into conveyor systems ensures:
- Immediate Response: In the event of an emergency, stop sensors can halt the conveyor instantly to prevent accidents.
- Integration with Control Systems: These sensors work seamlessly with conveyor control systems, allowing for automated or manual triggering of the stop function.
- Customizable Activation: Stop sensors can be programmed to activate under specific conditions, enhancing the safety protocols of the conveyor system.
- Versatility: They are suitable for various types of conveyors and can be adapted to different industrial environments.
- Function: Conveyor belt stop sensors detect when the conveyor belt needs to be stopped, often integrated with emergency stop systems. They ensure that the conveyor belt halts immediately in case of an emergency or malfunction.
- Example Products: Common stop sensors include pull-cord switches and emergency stop buttons. These sensors are designed to be easily accessible and reliable, providing a quick response to emergency situations.
Light Sensor on Conveyor Belt (Input or Output)
- Function: Light sensors detect the presence or absence of items on the conveyor belt. They are typically used for sorting, counting, or ensuring that the conveyor system is loaded correctly.
- Applications: Light sensors are widely used in packaging, manufacturing, and logistics to manage product flow. They help automate processes such as sorting and counting, enhancing the efficiency of the conveyor system.
- Input vs. Output: Input light sensors are placed at the entry points of the conveyor to detect incoming items, while output light sensors are positioned at exit points to verify the dispatch of items. Both types of sensors ensure accurate tracking of products through the conveyor system.
Speed Switch Sensor
- Function: A speed switch sensor monitors the conveyor belt speed and detects any deviation from the preset speed range. This sensor ensures consistent operation by triggering alarms or corrective actions if the belt speed goes outside the acceptable range.
- Applications: Speed switch sensors are used to maintain the integrity of conveyor operations in industries like mining, manufacturing, and logistics. By preventing over-speed or under-speed conditions, these sensors help avoid potential damage to the conveyor system and the products being transported.
- Example Products: Different speed switch sensors, such as rotary shaft encoders and magnetic speed sensors, offer various benefits. These sensors provide precise speed monitoring and can be easily integrated into existing conveyor systems.
The implementation of these conveyor belt sensors not only enhances the operational efficiency of conveyor systems but also significantly improves workplace safety. By monitoring speed, detecting stoppages, and enabling emergency stops, these sensors provide a comprehensive solution to many of the challenges faced in conveyor system management.
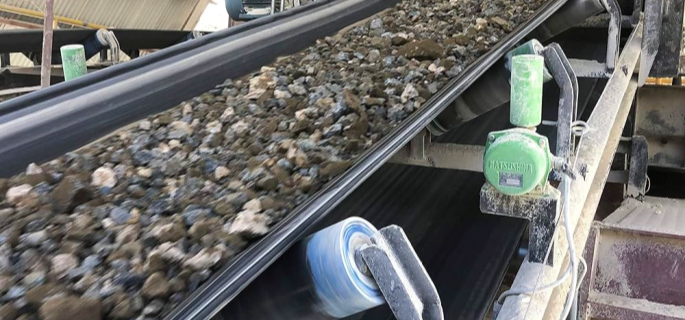
How Conveyor Belt Sensors Enhance Operations
Conveyor belt sensors are essential components that significantly enhance the operational efficiency, safety, and cost-effectiveness of conveyor systems. Here’s a detailed look at how these sensors contribute to improved operations:
Operational Efficiency
Conveyor belt sensors play a crucial role in optimizing the efficiency of conveyor systems by providing real-time data and enabling automated control mechanisms. These sensors continuously monitor various parameters, such as speed, position, and load, ensuring that the conveyor operates within optimal conditions.
- Real-Time Data Monitoring: Sensors such as speed sensors and proximity sensors offer continuous monitoring, allowing operators to keep track of the conveyor’s performance in real-time. This immediate feedback helps in quickly identifying and rectifying any deviations from the desired operational parameters.
- Automated Control: The integration of conveyor belt sensors with control systems facilitates automated adjustments to maintain optimal performance. For instance, if a speed sensor detects that the belt is moving too fast or too slow, the system can automatically adjust the motor speed to correct the discrepancy. This automation minimizes human intervention, reduces errors, and maintains a consistent flow of materials.
- Predictive Maintenance: Conveyor belt sensors can predict potential failures before they occur. For example, vibration sensors can detect unusual vibrations that may indicate bearing wear or misalignment, allowing for timely maintenance and preventing unexpected breakdowns.
Safety
Ensuring workplace safety is one of the primary benefits of using conveyor belt sensors. These sensors are designed to detect hazardous conditions and trigger immediate actions to prevent accidents and protect equipment.
- Accident Prevention: Sensors like zero speed sensors and stop sensors are critical for detecting anomalies that could lead to accidents. Zero speed sensors alert operators when a belt has stopped unexpectedly, while stop sensors enable emergency shutdowns if a potential hazard is detected. This immediate response capability is vital for preventing injuries and ensuring a safe working environment.
- Equipment Protection: By continuously monitoring the operational parameters, conveyor belt sensors help in identifying issues such as belt misalignment, excessive load, or overheating. Addressing these issues promptly prevents damage to the conveyor system and extends the lifespan of the equipment.
- Compliance with Safety Standards: Using conveyor belt sensors helps businesses comply with industry safety regulations. Sensors ensure that safety protocols are adhered to, thereby reducing the risk of legal liabilities and enhancing the overall safety culture within the organization.
Cost Savings
Conveyor belt sensors contribute to significant cost savings by reducing maintenance expenses and minimizing downtime.
- Reduced Maintenance Costs: Sensors provide early warnings of potential issues, allowing for proactive maintenance. This approach helps in addressing minor problems before they escalate into major repairs, thus reducing maintenance costs. For instance, a speed switch sensor can detect variations in belt speed that might indicate wear or tension problems, prompting maintenance actions before extensive damage occurs.
- Minimized Downtime: By ensuring continuous and efficient operation, conveyor belt sensors minimize unplanned downtime. Real-time monitoring and automated adjustments mean that the system can quickly return to optimal performance after a minor issue is detected and resolved. This minimizes production interruptions and maintains high levels of productivity.
- Extended Equipment Life: Regular monitoring and timely maintenance, facilitated by sensors, extend the lifespan of conveyor components. This reduces the frequency of replacements and the associated costs, leading to long-term savings.
Conveyor belt sensors are indispensable for enhancing the operational efficiency, safety, and cost-effectiveness of conveyor systems. By providing real-time data, enabling automated controls, ensuring safety, and facilitating proactive maintenance, these sensors help businesses achieve optimal performance and significant cost savings.
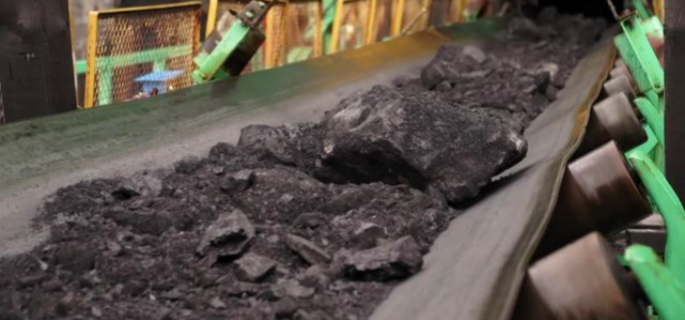
To Enhance Safety with Conveyor Belt Sensors and Devices
In the complex network of conveyor systems that power today’s industrial operations, ensuring the safety of both the machinery and the workforce is paramount. At the heart of this safety net are conveyor belt sensors, sophisticated devices that offer real-time monitoring and control capabilities, significantly bolstering the safety measures in place. When these sensors are seamlessly integrated with specialized safety devices, they create a formidable barrier against operational hazards, safeguarding the smooth functioning of conveyor systems.
Speed Switch Sensor: A Key Conveyor Belt Safety Device
Among the various conveyor belt sensors, speed switch sensors are vital for monitoring the operational speed of a conveyor belt. These sensors excel in identifying speed variations that could signal issues like belt slippage, overloads, or mechanical failures. Recognizing any deviation from established speed parameters enables speed switch sensors to trigger several preventive actions:
- Alarm Activation: Engaging audible or visual alarms to notify operators of speed discrepancies.
- System Shutdown: Automatically stopping the conveyor system to avert damage to both the machinery and the transported products.
- Maintenance Notification: Alerting maintenance teams for prompt inspection and corrective measures.
- Safety Lockout: Implementing a safety lockout to prevent system restart until the issue is fully addressed.
The proactive measures initiated by speed switch sensors play a crucial role in maintaining the conveyor system’s integrity and preventing accidents.
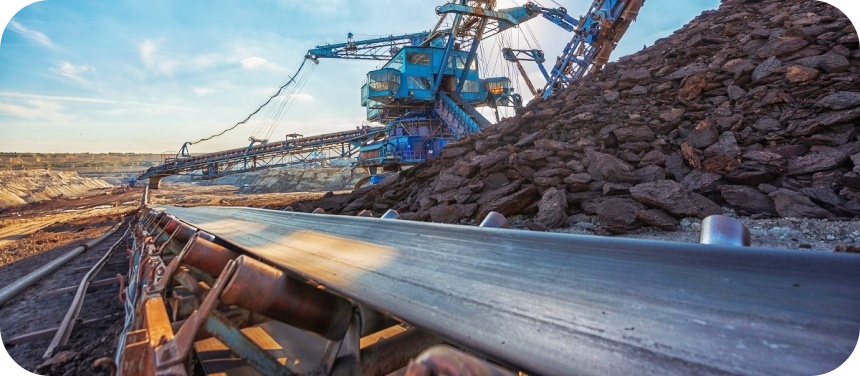
Conveyor Zero Speed Switch: Enhancing Conveyor Belt Safety
The conveyor zero speed switch is another critical component among conveyor belt safety devices, designed to detect when the conveyor belt ceases movement. This capability is essential for avoiding situations where a stationary conveyor belt could cause product pile-ups, system overloads, or mechanical breakdowns. The application of conveyor zero speed switches in conveyor systems contributes significantly to:
- Preventing Equipment Damage: Initiating system shutdown before jams lead to mechanical damage.
- Avoiding Product Loss: Preventing damage to products due to unforeseen stoppages.
- Enhancing Safety Protocols: Triggering emergency stops to protect personnel from potential hazards resulting from system malfunctions.
Illustrative case studies demonstrate the value of zero speed switches in industrial contexts. For example, their deployment in a manufacturing facility successfully averted a fire hazard by detecting and responding to a conveyor belt halt caused by a jammed item, facilitating an immediate system shutdown and hazard removal.
The integration of conveyor belt sensors with safety devices like speed switch sensors and conveyor zero speed switches is fundamental to a holistic approach to conveyor system safety. Leveraging these sensors’ capabilities ensures the uninterrupted, efficient, and secure operation of conveyor systems, thereby safeguarding industrial assets and the workforce from potential dangers.
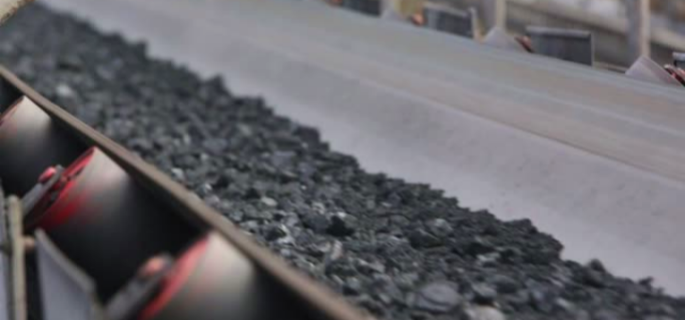
Belt Monitoring System with Conveyor Belt Sensors
The advent of belt monitoring systems equipped with conveyor belt sensors marks a significant advancement in the management and maintenance of conveyor systems. These sophisticated systems integrate various types of sensors to monitor critical aspects of conveyor belt operation, offering a holistic view of performance and potential issues in real-time.
Benefits of Real-Time Monitoring with Conveyor Belt Sensors
- Enhanced Preventative Maintenance: Conveyor belt sensors provide vital data that can predict failures before they occur, allowing for timely maintenance actions that prevent costly downtime and repairs.
- Minimized Downtime: Immediate detection and alerts about issues such as misalignment or abnormal wear enable quick corrective measures, significantly reducing unplanned downtime.
- Improved Safety: Continuous monitoring of conveyor belt conditions with sensors helps identify safety hazards, reducing the risk of accidents and ensuring a safer workplace.
- Increased Operational Efficiency: Real-time data from conveyor belt with sensor enable operators to optimize conveyor belt speed, tension, and load distribution, leading to improved efficiency and productivity.
- Cost Reduction: The combination of preventative maintenance, reduced downtime, and increased efficiency leads to substantial cost savings over the life of the conveyor system.
Electro-Sensors, Inc.: Pioneering Conveyor Belt Sensors for Monitoring
Electro-Sensors, Inc. specializes in providing cutting-edge solutions for conveyor belt monitoring, incorporating conveyor belt with sensor that enhance the safety and efficiency of industrial conveyor systems. Their comprehensive range of sensor-based products is designed to offer accurate, reliable monitoring of conveyor belt parameters, ensuring optimal performance in various industrial settings.
Key offerings include:
- Speed Monitoring Sensors: These sensors ensure that conveyor belts operate within safe and efficient speed parameters, alerting operators to any deviations that could indicate potential issues.
- Belt Alignment Sensors: Critical for preventing premature wear and tear, these sensors detect misalignments early, allowing for adjustments before significant damage occurs.
- Wear Detection Sensors: By monitoring the condition of the conveyor belt, these sensors help predict when maintenance or replacement is necessary, preventing unexpected failures.
Integrating products from Electro-Sensors, Inc. into a belt monitoring system equipped with conveyor belt sensors not only safeguards the conveyor system but also optimizes its operation. This synergy between advanced sensors and monitoring technology represents a comprehensive approach to conveyor system management, ensuring reliability, safety, and efficiency in industrial operations.
How to Implement Conveyor Belt Sensors
The successful implementation of conveyor belt sensors is a critical step towards enhancing the efficiency, safety, and reliability of conveyor systems in industrial settings. These sensors serve as the eyes and ears of the conveyor system, providing vital information that helps in preventing downtime, reducing maintenance costs, and ensuring the safety of both the workforce and the machinery. Here are some guidelines and tips for selecting, installing, and integrating conveyor belt sensors into your conveyor systems.
To Select the Right Type of Conveyor Belt Sensors
The first step in implementing conveyor belt sensors is to identify the specific needs of your conveyor system. Different types of sensors are designed to monitor various aspects of conveyor operation, such as speed, alignment, load, and wear. Consider the following factors when selecting sensors:
- Operational Requirements: Determine what aspects of the conveyor’s operation need monitoring. For instance, speed sensors are crucial for applications where maintaining a specific belt speed is necessary for product quality.
- Environmental Conditions: Assess the operating environment. Harsh conditions such as extreme temperatures, moisture, and dust can affect sensor performance, so choose sensors designed to withstand these conditions.
- Integration Capabilities: Ensure the sensors can be easily integrated with your existing conveyor control systems and automation software for seamless operation.
- Maintenance and Durability: Opt for sensors with a proven track record of reliability and low maintenance requirements to minimize downtime.
Tips for Conveyor Belt Sensors
Once the appropriate conveyor belt sensors have been selected, the next steps involve their installation and integration into the existing conveyor systems. Here are some tips to ensure a smooth process:
- Follow Manufacturer Instructions: Each type of conveyor belt sensor comes with specific installation guidelines provided by the manufacturer. Adhering to these instructions is crucial for optimal sensor performance and longevity.
- Strategic Placement: Position sensors at critical points along the conveyor system where they can best capture the required data. For example, install speed sensors near the drive mechanism and alignment sensors along straight sections of the belt.
- Test Before Full Integration: After installation, conduct thorough testing to ensure the sensors are functioning correctly and accurately capturing data. This step is crucial before fully integrating the sensors with the conveyor’s control system.
- Ensure Proper Calibration: Sensors may require calibration to function accurately within the specific parameters of your conveyor system. Regular calibration checks are essential for maintaining sensor accuracy over time.
- Train Personnel: Educate your maintenance and operational staff on the functions of the newly installed conveyor belt sensors, including how to interpret the data they provide and the actions to take based on that data.
Implementing conveyor belt with sensor with careful consideration to selection, installation, and integration can significantly enhance the operational efficiency and safety of conveyor systems. By following these guidelines, industries can ensure that their conveyor systems are not only more reliable but also provide actionable insights that contribute to smoother, safer, and more cost-effective operations.
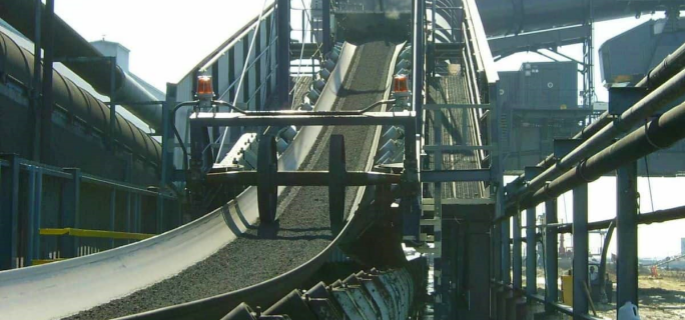
Integration of Conveyor Belt Sensors
Integrating conveyor belt sensors into your existing systems is crucial for maximizing their benefits in terms of efficiency, safety, and cost savings. Here is a detailed look at the steps involved in the installation, calibration, and system integration of conveyor belt sensors.
Installation and Calibration
Proper installation and calibration of conveyor belt sensors are essential to ensure accurate data collection and reliable performance. Here’s a step-by-step guide on how to install and calibrate different types of conveyor belt sensors:
Preparation:
- Safety First: Before starting the installation, ensure that the conveyor system is powered off and locked out to prevent accidental activation.
- Read Manuals: Carefully read the installation manuals provided by the sensor manufacturers. Each sensor type may have specific requirements and procedures.
Installation Steps:
- Positioning: Determine the optimal location for each sensor based on its function. For instance, speed sensors should be placed near the drive pulley, while proximity sensors should be positioned along the belt where items pass.
- Mounting: Securely mount the sensors to the conveyor frame using appropriate brackets and hardware. Ensure that sensors are aligned correctly to avoid inaccurate readings.
- Wiring: Connect the sensors to the control system using the recommended wiring practices. Ensure all connections are secure and protected from environmental factors such as moisture and dust.
Calibration Steps:
- Initial Setup: Power on the conveyor system and the sensors. Follow the manufacturer’s instructions to initialize the sensors.
- Calibration Process:
- Speed Sensors: Run the conveyor at a known speed and calibrate the sensor output to match this speed. Adjust the sensor settings until the readings are accurate.
- Proximity Sensors: Place a test object in the sensor’s detection range and adjust the sensitivity to ensure reliable detection. Repeat the process with different objects to verify consistency.
- Zero Speed Sensors: Simulate a stopped belt condition and calibrate the sensor to recognize this state accurately. Adjust thresholds as necessary to avoid false alarms.
- Testing: After calibration, test the sensors by running the conveyor under normal operating conditions. Verify that the sensors provide accurate and consistent readings.
System Integration
Integrating conveyor belt sensors with your existing conveyor systems and control software can enhance overall system functionality. Here are some tips for successful integration:
Compatibility Check:
- Ensure that the sensors you choose are compatible with your existing control systems and software. Check for matching communication protocols and interface requirements.
Interface Setup:
- Communication Protocols: Configure the sensors to communicate with the control system using standard protocols such as Modbus, Ethernet/IP, or Profibus. This setup ensures seamless data exchange between the sensors and the control system.
- Data Mapping: Map the sensor outputs to the relevant input channels of the control system. This mapping allows the control software to interpret sensor data accurately and trigger appropriate actions.
Software Configuration:
- Parameter Settings: Adjust the control software settings to incorporate the new sensors. Set parameters such as speed thresholds, detection ranges, and alarm conditions based on the sensor specifications.
- Automation Rules: Define automation rules in the control software to utilize sensor data for real-time decision-making. For example, configure the system to automatically adjust conveyor speed based on speed sensor readings or to stop the conveyor if a zero-speed sensor detects a malfunction.
Testing and Validation:
- Functional Testing: Conduct comprehensive testing to ensure that the sensors and control system work together as intended. Simulate different operating conditions and verify that the system responds correctly to sensor inputs.
- Troubleshooting: Address any issues that arise during testing. Common problems include incorrect sensor readings, communication failures, and software configuration errors. Make necessary adjustments and re-test to confirm resolution.
Training and Documentation:
- Operator Training: Train your maintenance and operational staff on how to use and maintain the integrated sensor system. Provide detailed instructions on sensor calibration, troubleshooting, and routine maintenance.
- Documentation: Maintain thorough documentation of the installation, calibration, and integration processes. Include wiring diagrams, calibration records, and software configuration details for future reference.
By following these steps for installation, calibration, and system integration, you can effectively incorporate conveyor belt sensors into your conveyor system, enhancing its operational efficiency, safety, and reliability. Proper integration ensures that the sensors provide accurate data and enable automated controls, leading to optimized performance and reduced downtime.
Need conveyor belts? Contact us for the best options!
Future Trends in Conveyor Belt Sensors Technology
The realm of conveyor belt sensors is witnessing rapid advancements, with emerging technologies poised to revolutionize the efficiency and safety of conveyor systems. These innovations are not just enhancing the functionality of conveyor belts but are also setting new benchmarks for industrial operations. Let’s delve into the future trends in conveyor belt sensor technology and explore how these advancements could significantly improve conveyor system safety and efficiency.
Emerging Technologies and Innovations in Conveyor Belt Sensors
- IoT-Enabled Sensors: The integration of the Internet of Things (IoT) with conveyor belt sensors allows for real-time data exchange and monitoring across the system. This connectivity enables predictive maintenance, immediate anomaly detection, and system-wide optimization.
- AI and Machine Learning: Artificial Intelligence (AI) and machine learning algorithms are being applied to analyze the vast amounts of data collected by sensor conveyor belt. This analysis can predict potential system failures, optimize operational efficiency, and automate decision-making processes.
- Advanced Material Technologies: New sensor materials are being developed to withstand extreme environmental conditions, including high temperatures, corrosive substances, and intense vibrations. These durable sensors extend the lifespan of conveyor systems and reduce maintenance requirements.
- Energy Harvesting Sensors: Future conveyor belt with sensor may utilize energy harvesting technologies, drawing power from environmental sources or the operation of the conveyor itself. This innovation would eliminate the need for external power sources or battery replacements, ensuring continuous operation.
- Flexible and Wearable Sensors: The development of flexible and wearable sensors that can be integrated directly onto the conveyor belt material. These sensors offer enhanced monitoring capabilities, including strain and wear detection, providing insights into the belt’s condition and lifespan.
Predictions on Improvements in Safety and Efficiency
These future trends in conveyor belt sensor technology highlight a shift towards more autonomous, reliable, and efficient conveyor systems. By leveraging IoT connectivity, AI analytics, and innovative materials, conveyor belt sensors are set to offer unprecedented levels of operational control, safety, and efficiency. As these technologies continue to evolve and mature, they will undoubtedly become integral components of modern industrial conveyor systems, driving forward the capabilities and performance of material handling operations worldwide.
FAQs about Conveyor Belt Sensors
Conveyor belts utilize a variety of sensors to ensure efficient and safe operations. These include speed sensors, which monitor the velocity of the conveyor belt to ensure materials are moved at the correct pace. Misalignment sensors detect when the belt deviates from its intended path, helping to prevent wear and tear or potential system damage. Zero speed sensors are crucial for identifying when the conveyor belt has stopped moving, which could indicate a blockage or system failure. Additionally, load sensors measure the weight of the materials on the belt, ensuring the system is not overloaded and operates within safe parameters. These sensors collectively contribute to the optimization of conveyor belt performance, enhancing productivity and safety in industrial settings.
The best way to track a conveyor belt involves regular maintenance and the use of appropriate tracking technologies. Initially, ensure that the conveyor belt is correctly installed and aligned according to the manufacturer’s specifications. Regular inspections can identify potential issues before they lead to misalignment. For ongoing maintenance, tracking sensors and edge guides can be installed to monitor and automatically correct the belt’s path as needed. Laser alignment tools are also effective for ensuring the pulleys and idlers are properly aligned. Implementing a combination of these strategies, along with routine visual inspections and adjustments, represents the most effective approach to maintaining optimal conveyor belt tracking.
Conveyor belt safety devices are designed to protect workers and equipment from accidents and damage. These include emergency stop systems, often referred to as e-stop buttons, which allow workers to immediately halt the conveyor’s operation in case of an emergency. Guardrails and barriers provide physical protection, preventing access to moving parts. Pull cord switches, also known as safety cable pull switches, offer a means to stop the conveyor from any point along its length in case of an issue. Speed switch sensors and zero speed sensors help monitor the conveyor’s operation, triggering alarms or shutdowns if unsafe conditions are detected. Together, these devices form a comprehensive safety system for conveyor belt operations, ensuring both worker protection and equipment integrity.
The speed of a conveyor belt is controlled by a combination of motor type, drive systems, and electronic controllers. AC and DC motors are commonly used, with speed control achieved through variable frequency drives (VFDs) for AC motors or speed controllers for DC motors. These systems allow for precise adjustment of the conveyor belt’s speed to match the requirements of the production process. Programmable Logic Controllers (PLC) can also be integrated to automate speed adjustments based on real-time operational data, enhancing efficiency and adaptability. The choice of control system depends on the specific needs of the conveyor application, including the type of materials being transported, the desired speed range, and the level of automation required.
A conveyor belt tracker is a device used to ensure that a conveyor belt remains aligned along its intended path, preventing misalignment issues that can cause belt damage, spillage, and increased wear and tear. It automatically adjusts the belt’s position by sensing deviations and applying corrective pressure, thereby maintaining smooth and efficient operation. Conveyor belt trackers are essential in various industries, such as mining, manufacturing, and food processing, where they help reduce downtime, extend belt life, enhance safety, and improve overall efficiency by keeping the belt properly aligned.
In island environments, conveyor sensors ensure efficient and safe material handling by detecting the presence and speed of items on conveyor belts, sorting and counting goods, and maintaining proper belt alignment. They enhance safety through emergency stop functions and proximity detection, preventing accidents and equipment damage. By providing real-time data and automated control, these sensors help optimize conveyor operations, reduce downtime, and extend equipment life, which is especially crucial in remote island settings where reliability and efficiency are paramount.
Last Updated on June 19, 2024 by Jordan Smith
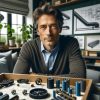
Jordan Smith, a seasoned professional with over 20 years of experience in the conveyor system industry. Jordan’s expertise lies in providing comprehensive solutions for conveyor rollers, belts, and accessories, catering to a wide range of industrial needs. From initial design and configuration to installation and meticulous troubleshooting, Jordan is adept at handling all aspects of conveyor system management. Whether you’re looking to upgrade your production line with efficient conveyor belts, require custom conveyor rollers for specific operations, or need expert advice on selecting the right conveyor accessories for your facility, Jordan is your reliable consultant. For any inquiries or assistance with conveyor system optimization, Jordan is available to share his wealth of knowledge and experience. Feel free to reach out at any time for professional guidance on all matters related to conveyor rollers, belts, and accessories.